地球温暖化や燃料高騰に伴い、航空機の低燃費、低騒音の追求、安全性の向上がますます求められています。航空機業界の新潮流は、エアバス、ボーイングなど欧米の大手メーカーによってけん引されていますが、ギア技術において川崎重工は世界のトップランナーとして技術革新を続けています。次世代ギアなくしては次世代航空機の実現は成し得ません。先進技術でリードする川崎重工の航空機用ギア事業を紹介します。
多くの産業にとって欠かせない「ギアボックス」。航空産業の多彩なギア製品群を誇る川崎重工
歯車装置(ギアボックス)は、歯車を組み合わせて速度やトルク(回転力)を変換させる歯車装置のこと。ギアボックスを使用することで、小さなトルクを増幅したり、遅い回転を速くしたりすることができます。
動力の伝達装置である歯車装置は多くの産業にとって必要不可欠なものであり、自動車の変速装置(トランスミッション)、観覧車の減速機、風力発電の心臓部とも言える増速ユニットなどで活用されています。
航空機においてギアボックスは、エンジンの回転を効率よく速度変換するという基本的な役割と、回転からエネルギーを取り出す発電装置としての役割があります。ギアボックスには、長期間運転しても破損しない高い信頼性と、滑らかな動力伝達による低振動、低騒音が求められます。
そのほか、ギア同士の接触による発熱を少なくする高い伝達効率、軽量で大きな動力を伝達できる高い動力伝達密度も重要です。
航空機用ギアで、川崎重工ほど豊富な製品群をもつメーカーはありません。ラインナップは、「BK117」をはじめとするヘリコプター用トランスミッション、航空機用アクセサリー・ギア・ボックス(AGB)、独自技術の航空機用 発電システム「T-IDG®」など幅広いもの。まさに、世界トップクラスの航空機用ギアボックスメーカーと言えるでしょう。
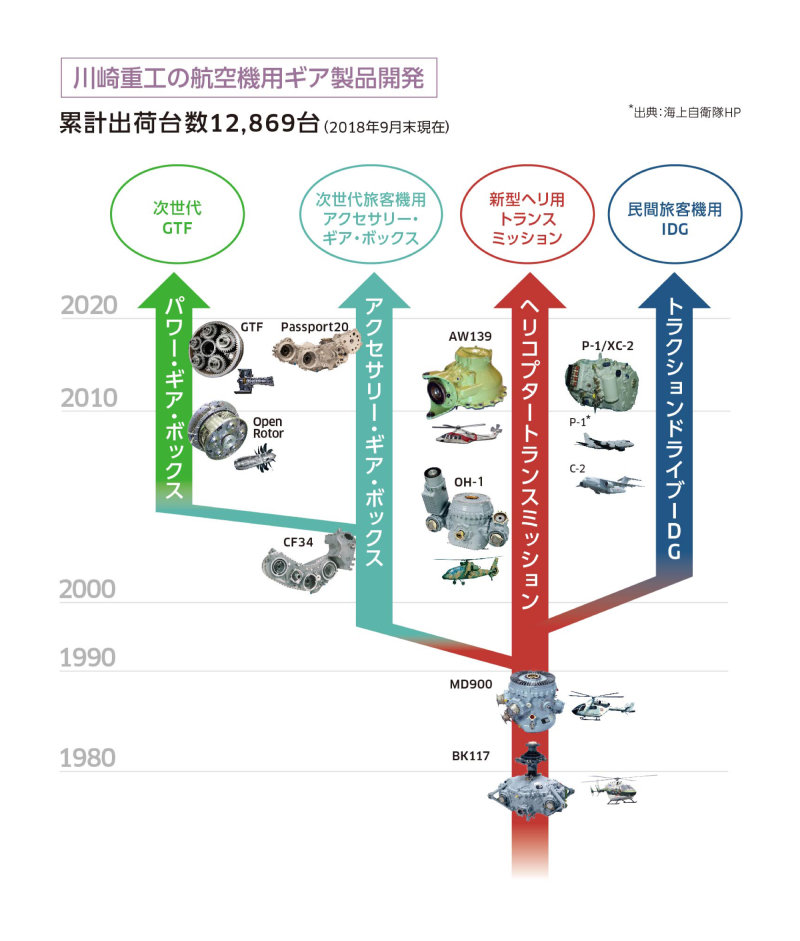
川崎重工の航空機用ギア事業は、ヘリコプター用トランスミッション開発から始まりました。
1960年代の自社開発機計画を手始めとし、1977年から始まったメッサーシュミット・ベルコウ・ブローム社(現エアバス社)との「BK117」の共同開発において、最重要部位であるトランスミッションを担当。優れた運航・安全性能により警察、消防、報道、さらにドクターヘリなどとして活躍しています。その信頼性と耐久性の高さを証明した傑作機を礎として、航空機用ギア事業の拡大に成功しました。
ヘリコプター用トランスミッションは、キャビンの上部に据えられています。①エンジンの出力をメインローター(翼)とテールローターに減速して伝達、②補機を駆動、③メインローターで発生する揚力を機体に伝え、推力とそれに反する抗力を受け止める、などの役割を担っています。
シリーズ8世代目となる「BK117 D-2型」での検証によれば、1分間に6000回転するエンジンの回転を、380回転まで減らす(減速比は約16)とともに、トルクを1万9600N・mにまで増幅してメインローターを回します。これは長さ1mの棒の先に乗用車2台がぶら下がるほどの巨大な回転力に匹敵するのです。
具体的には、2基のエンジンの動力1000馬力は、トランスミッションのスパイラル・ベベル・ギア(まがりばかさ歯車)で回転軸の向きを垂直に変えると同時に回転数が減らされ、続く2段目のヘリカルギア(はすば歯車)で合成されて減速されます。トランスミッションの中には、さらにコンパクト性を求めるためにプラネタリギア(遊星歯車)を使うものもあり、パワー・ウエイト・レシオ(1馬力あたりの重量)は自動車などのトランスミッションの半分以下になります。
この小型で信頼性の高いギア・ボックスを設計し、天井部分にコンパクトに収めたことで、後方キャビンが広くなり観音開きのドアも実現。緊急時に出動するドクターヘリ、警察、消防用ヘリとして信頼され活躍する一因ともなっているのです。
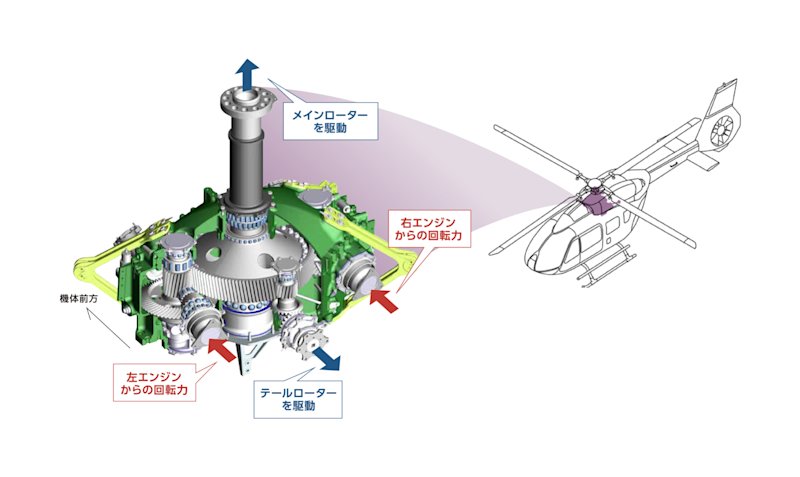
素材加工から最終検査まで。ギアの軽量化を極限まで追求する技術
航空機においてギアの軽量化が常に要求されるなか、薄さと耐久性の両立が極限まで求められています。ギアは薄いものでは2mmほどで、この薄さで巨大な力を伝達します。軽量化のため内側に穴開けされることもあり、必然的に歪みが出やすくなっています。そのうえでギアの歯の形は1000分の1mm(1µm)単位の精度に収めなければならないのです。
川崎重工 航空宇宙システムカンパニー 生産本部 生産技術部の郷橋 昌宏 主事は、「ギアの形状によって加工時の歪み方が異なり、加工工程ごとでも歪み方が変わります。この歪みをいかに抑え、もとに戻し、設計者が理想とした複雑で微妙な形の歯形を実現するかがギア製造の重要なポイントになります」と解説します。
ギア製造はまず、専用の工作機械を使い、丸い素材に創り出したい歯形と同じ形の刃を当てて削り出します。次に歯の表面を硬くするために表面に炭素を浸透させる「浸炭焼き入れ」を行い、最後に専用工作機械を駆使して1µm単位の精度で歯の形を研削して仕上げます。
さらに耐久性を上げるため、表面に細かな鉄の球をぶつけて鍛える「ショットピーニング」が施されます。検査工程では、加工時の温度上昇で強度が低下していないかを特殊な薬液で調べる「ナイタルエッチ」や、ギアを磁化して肉眼では発見が難しい微小な傷を検出する磁粉探傷などの非破壊検査が繰り返されます。
「当社の航空機用ギアの最大の特徴は、素材加工から熱処理、最終検査までの一貫した作業を行い、見えない部分での不具合を絶対に見逃さないノウハウを備えていることです。航空機用ギアの分野で、一貫したノウハウをもつのは世界に通用する強みです」と郷橋主事は語ります。
ヘリのドライラン60分の実現へ。トランスミッションの安全性を追求。
トランスミッションの開発には、ギア単体はもちろんユニット部品としての高精度・高能力が求められます。より高回転・大馬力のエンジンの力を受け止めるギアの開発や、軽量で薄肉であるが故に起きやすい振動を防ぐ仕組みづくりな土が必要です。
ヘリコプターの安全性に関するニーズのひとつに,トランスミッションの「ドライラン」性能があります。「ドライラン」とは、ギアやベアリングの潤滑と冷却に用いるオイルが失われ、トランスミッション内の潤滑油が失われても継続的に飛行できる耐久性のこと。
現在、30分間の飛行能力が民間機に義務付けられています。近年、海上の油田掘削基地と陸上を結ぶオフショア運用が増加しており、安全確保のためにさらなる長時間のドライラン能力が求められています。
川崎重工 航空宇宙システムカンパニー 民間エンジンプロジェクト本部 駆動システム技術部の小笠原 健太 主事は、「川崎重工はすでに60〜70分間ほど飛行を可能にする改善技術に見通しを得ており、今年度内にも実証試験に入る予定です」と打ち明けます。
そのカギとなるのが冷却です。潤滑油が失われてもギアやベアリングの温度が上がらない、つまり「焼き付き」を発生しにくくするための配置や構造、素材を追求しています。また、ドライランが発生した際のトランスミッション内における各ギアの温度変化などについて、CFD(熱流体シミュレーション) と伝熱解析を組み合わせたシミュレーション技術を開発。ギア形状やベアリング配置などの最適化を実現しています。
小笠原主事は「将来的には、新しい発想によるトランスミッションの開発につなげたいと考えています」と語ります。※1
※1 上記内容は川崎重工技報・179号「航空機用ギアボックス設計技術の高度化」 参照
軽量、高効率・高耐久性、高度な制御を実現。革新的な発電装置「T-IDG®」を開発
航空機は、エンジン停止時は機内の補助電源装置からの電力を、照明、放送システム、調理器具など各装置に供給しています。エンジン起動後は、エンジンの動力を利用して発電する交流発電装置が作動し、補助電源装置に切り替わるのです。エンジンの回転数は離陸前、離陸中、飛行中で異なりますが、発電装置はエンジンとつながっているため、発電機の回転数も発電周波数も変化してしまい、安定した電力になりません。
そのため、エンジンの回転数が変化しても一定速度に調整して発電機を回す、定速駆動機構(無段変速機)と一体化した発電装置(IDG:Integrated Drive Generator)がエンジンのアクセサリー・ギア・ボックスに据えられている。
アクセサリー・ギア・ボックスとは、発電機、潤滑ポンプ、燃料ポンプ、ハイドロポンプなどを駆動するモジュールであり、駆動力はエンジン本体から供給されます。
川崎重工は独自技術により、航空機の定速駆動機構では世界初となる高速トラクションドライブ無段変速機を用いた航空機用一定周波数発電装置「T-IDG®」を開発しました。この「T-IDG®」では、変動するエンジンからの駆動回転数をトラクションドライブ無段変速機で調速し、発電機を一定速度で回転させることにより、常に一定周波数(400Hz)の交流電力を航空機に供給できるのです。
トラクションドライブとは、油の粘性抵抗を利用して動力を伝える機構のこと。 従来、IDGは油圧式変速機が主流でしたが、「T-IDG®」は特殊なオイルの粘性抵抗を利用して動力を伝達する方式を採用。従来の油圧式よりもロスが少なく、部品同士の接触摩擦がないため耐久性が高くなっています。油圧式に比べて軽量で、高効率・高耐久性と高度な制御を実現させた革新的な無段変速機なのです。
航空業界においては、地球温暖化が問題視される以前から、機体の軽量化とエンジンの高効率化が求められてきました。また、新たな都市間モビリティとして「空飛ぶクルマ」と呼ばれる電動の垂直離着陸(eVTOL)機も現実となりつつあり、エンジン、装備品の両面から航空機の電動化技術の開発が進められています。
次世代航空機において、装備品の電動化(MEA=More Electric Aircraft)と大容量化対応の発電システムが求められています。今後は「T-IDG®」のさらなる大容量化を加速させ、民間市場への投入をめざしています。
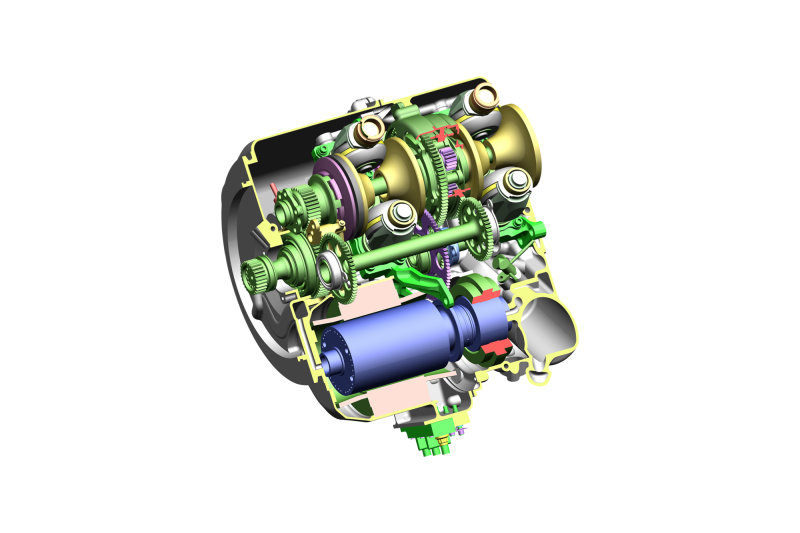
●交流発電機(出力:90kW)1分間に2万4,000回転で発電し、周波数の安定した電力を機内の各装置に供給し、安全な飛行をかけて支えている。
※発電装置はエンジン1基につき1台設置されており、 万一の発電装置自体の不具合、あるいはエンジントラブル時にも他の発電装置がバックアップとなるので、航空機への電力供給には支障ない。
●出力ターミナル ここから電力を出力する。
出典 Kawasaki News162 「航 空機に周波数の安定した電力を供給する、新開発の発電装置『T-IDG®』のしくみ」
新型エンジンの"肝"となる「FDGS」。低燃費、低騒音、CO2・NOx削減へ
川崎重工はP&W(プラット・アンド・ホイットニー)社と組み、先進エンジン開発にも貢献しています。
現代の航空機エンジンは「ジェットエンジン」が主流です。ジェット機は、機体の前方から空気を吸い込み、圧縮機によって圧縮。それを燃焼室に送って高温・高圧にし、排気口から吹き出すという構造が採用されています。
ジェットエンジンのメカニズムは、この「吸気、圧縮、燃焼、排気」の四つに集約されます。また、ジェットエンジンは、戦闘機に使われる「ターボジェットエンジン」と、主に旅客機で採用される「ターボファンエンジン」の2種類に分けられます。
「ターボジェット」は、燃焼室を通った圧縮空気のみを吐き出すエンジンです。これに対して「ターボファン」は燃費を向上させるため、燃焼室から出た圧縮空気のほかに、「ファン」を回して吸い込んだ空気も機体後方に送り出して推力を生み出します。この空気は燃焼室を通らないという意味で「バイパス」空気と呼ばれます。※2
P&W社は、従来のターボファンエンジンを発展させ、ファンを減速して駆動するために遊星歯車機構を採用した「ギアード・ターボファン・エンジン(GTF)」を開発。
一般にターボファンエンジンは、ファンの直径をより大きくする、すなわちバイパス比を大きくすることで燃費を改善することができます。しかし、ファンの回転数とファンを駆動するタービンやコンプレッサが理想とする回転数は異なるため、性能向上には限界がありました。
これを打破するのがファンとタービンの間にギアを噛ませ、それぞれの最適な回転数を両立させた「GTF」なのです。
※2 ニュースイッチ「【連載】基礎からわかる!MRJ(3)『GTFエンジン』」参照
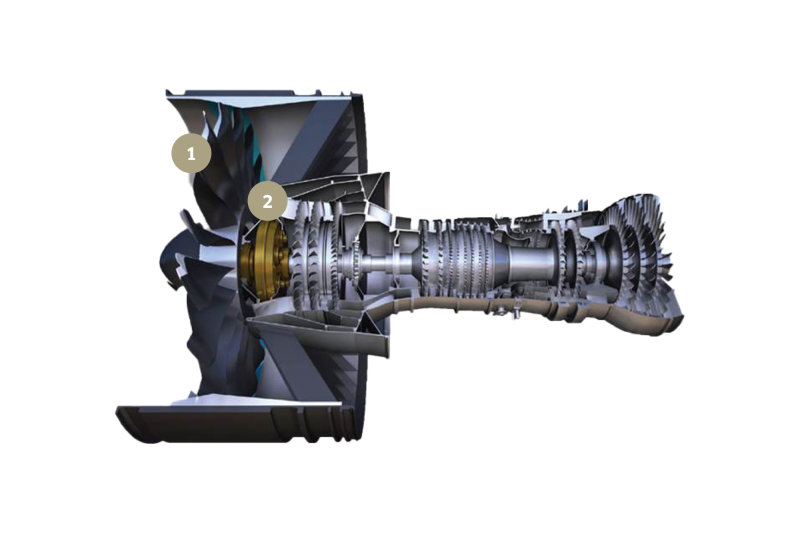
出典:川崎重工技報・179号「新製品紹介 リージョナルジェット機用エンジン『PW1500G』/『PW1900G』」
川崎重工は、P&W社の次期リージョナルジェット機(短距離輸送用ターボファンエンジン搭載航空機)用エンジンである「PW1500G」および「PW1900G」の開発・生産プログラムに参画。この革新的なエンジンの中核となる燃焼器と、「ファンドライブギアシステム(FDGS)」を担当。
FDGSには、入出力が同軸駆動であるため、また小型軽量化のために遊星歯車装置が使われています。エンジンの伝達動力は2万馬力でヘリコプターをはるかに上回ります。3万時間以上の信頼性も要求されるのです。
開発を進める川崎重工 航空宇宙システムカンパニー 民間エンジンプロジェクト本部 駆動システム技術部の佐藤 桂匡 主事補は語ります。
「これほどの馬力になると、わずか1%のエネルギー損失でも約200馬力、つまり150kWを熱に変えてしまうことになります。肝心の燃費を損なうばかりでなく、熱を冷やすためのオイルや熱交換器などの重量やサイズも大きな課題になってしまいます」。
そのため、軽量・コンパクトであるだけでなく、ギアの摩擦やオイルのかき混ぜなどによる損失を低減するための工夫も重要になります。
佐藤主事補は「システム内のオイルは液体と気体が混じった複雑な流れになっており、これをコンピュータでシミュレーションする世界一の技術を川崎重工は保有しています。さらには流れを最適化するだけでなく、潤滑と冷却の効果を最大化するなどの独自技術も編み出すことで、エネルギー効率は99.6%を達成しています」と解説します。
FDGSの採用により、P&W社のGTF「PW1500G」「PW1900G」は高バイパス比を実現。従来機に対し16%の燃費改善と50%の騒音を低減するとともに、CO2・NOxの排出も大幅に削減しました。今後はエアバス社、エンブラエル社のリージョナルジェット機に搭載され量産を開始する予定です。
佐藤主事補はさらに語ります。「川崎重工の独自技術は、現在のGTFのさらに先の2030年以降に登場すると考えられるオープン・ローター・エンジン用ギアシステムの研究プロジェクトにおいて技術開発本部と共に開発しました。これをもとにさらに技術を磨いてイノベーションを提案していく計画です」。※3
※3 川崎重工プレスリリース「Pratt & Whitney社のリージョナルジェット機用エンジン『PW1500G』向けファンドライブギアシステムを初出荷」 および川崎重工技報・179号「新製品紹介 リージョナルジェット機用エンジン『PW1500G』/『PW1900G』」 参照
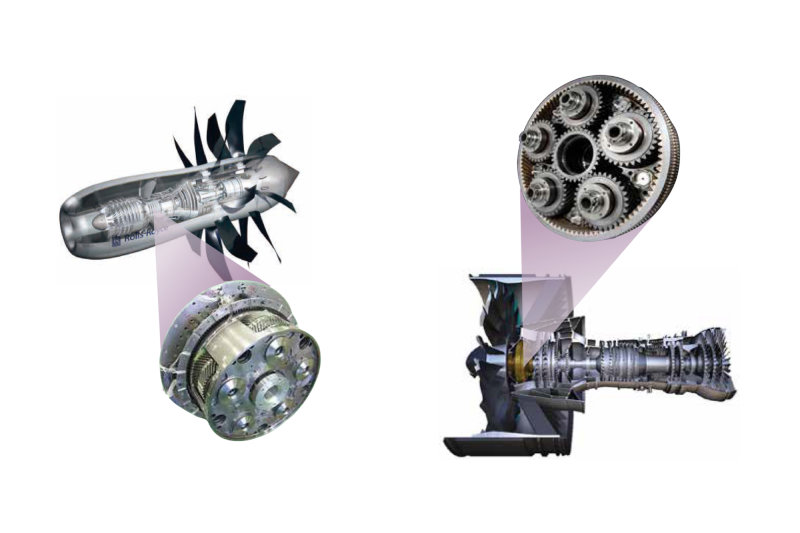
トランスミッションやFDGSなど、航空機に欠かせないギア技術はエンジンと比べて目立たぬ存在。しかし、優れたギアなくして航空機の低燃費の追求、安全性の向上はあり得ません。
次世代航空機の実現には、革新的なギア技術が不可欠であり、まさにギアが全ての核心を握っていると言えるでしょう。多彩な航空機用ギアを開発・製造し、世界をリードする川崎重工の技術革新が、新時代の潮流をけん引していきます。
航空機用ギアで世界制覇をめざします
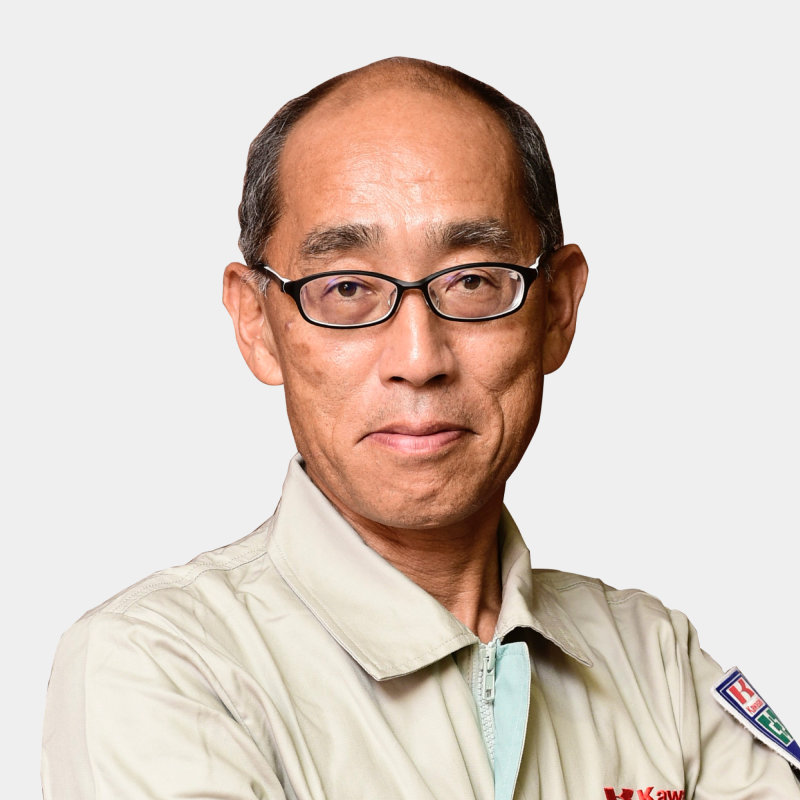
航空宇宙システムカンパニー
フェロー ギアシステム
技術担当
そもそもギアは、エネルギーの効率的な伝達のために活用され、一層の効率化を図ろうとすればするほどギアが果たすべき役割は高まり、大きな技術革新の可能性を秘めている部品です。
川崎重工の航空機用ギア事業は、ヘリコプターのトランスミッションのライセンス生産から始まり、その後は技術開発本部と共にチャレンジを重ね、自社技術で類まれな性能と信頼性を創造しました。
それを可能にしたのは、開発から製造までの一貫した体制を整えて工程間の課題を擦り合わせるものづくりの体制と、技術者たちのさまざまな挑戦を支援する闊達な風土でした。
その結果、トランスミッションの技術は、補機類を稼働させるアクセサリー・ギア・ボックスや航空機用発電装置「T-IDG®」へと発展し、今は「FDGS」という未来技術に裾野を広げようとしています。
いずれもが航空機には欠かせない技術であり、今後の航空機産業の伸びやエンジンの“Geared”化※3の進展を考えれば、私たちの事業拡大の伸び代は大きく、航空宇宙システムカンパニーの事業の柱の一つとして大いに期待されています。
航空機業界では、より低燃費、低エミッションへの飽くなき追求がなされています。従ってこれからは、さらに進化したGTFあるいはオープンローターといった次世代エンジンでなければ認められないような新潮流が始まるでしょう。
そこでも核心的な部品となるのがギアであり、ギアなくしては次世代エンジンは成り立たないと言えます。
航空機業界の新潮流は、確かに欧米の大手メーカーによってけん引されていますが、それを実現するために必要なギア技術、言い換えれば核となり発展のポテンシャルの高いギア技術については、川崎重工は世界トップランナーです。むしろ私たちの技術革新が新しい潮流をけん引すると言っても過言ではないと自負しています。
まさに「ギアを制すものは世界を制す」と言えましょう。
※3 “Geared”化=ファンを駆動する ためにギアを用いること
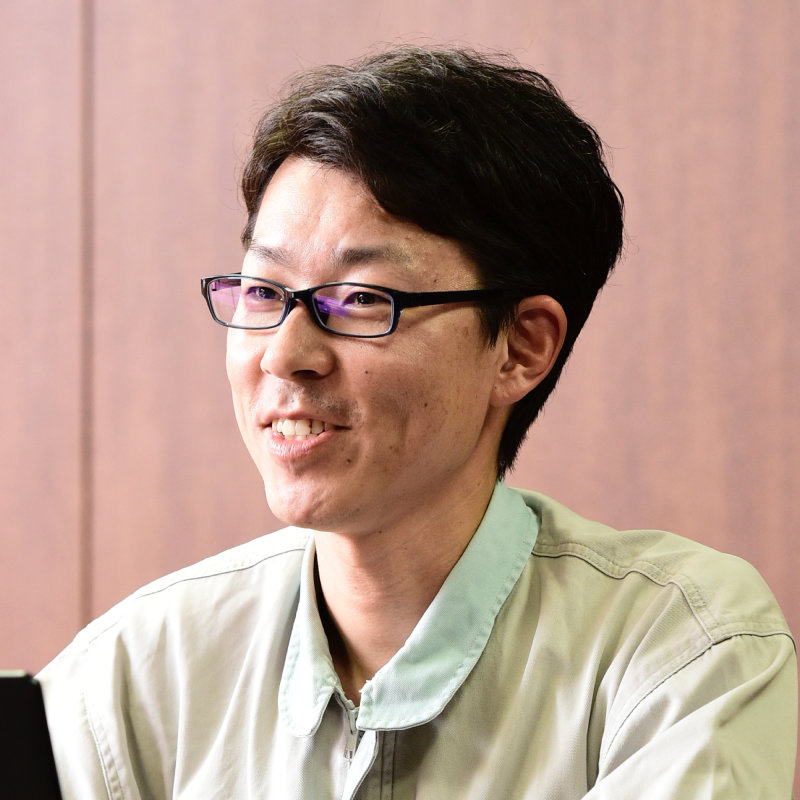
航空宇宙システムカンパニー
生産本部 エンジン生産技術部
エンジン生産技術一課
主事
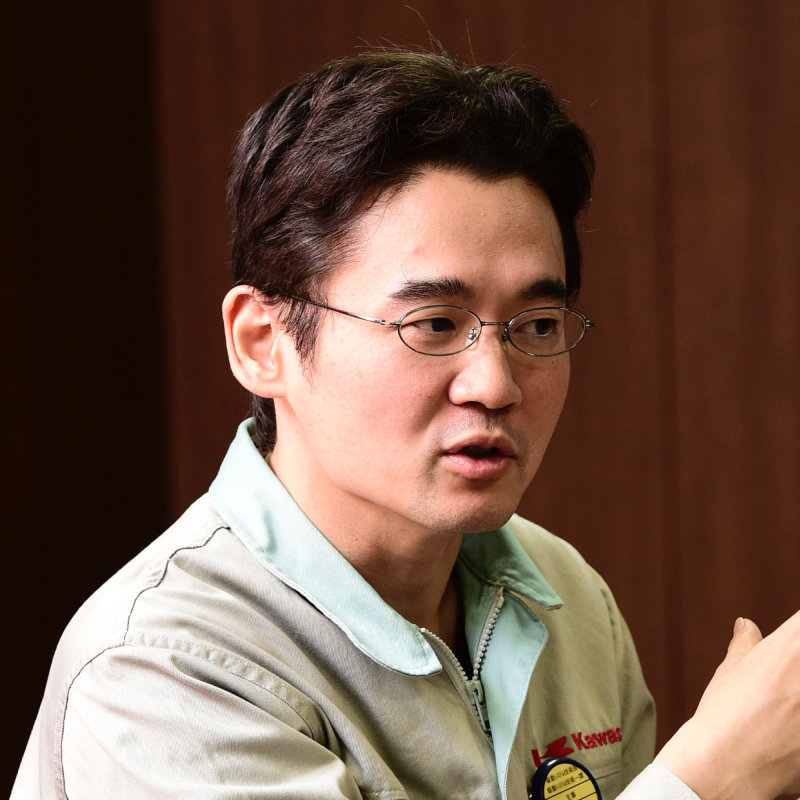
航空宇宙システムカンパニー
民間エンジンプロジェクト本部
駆動システム技術部 駆動システム技術一課
主事
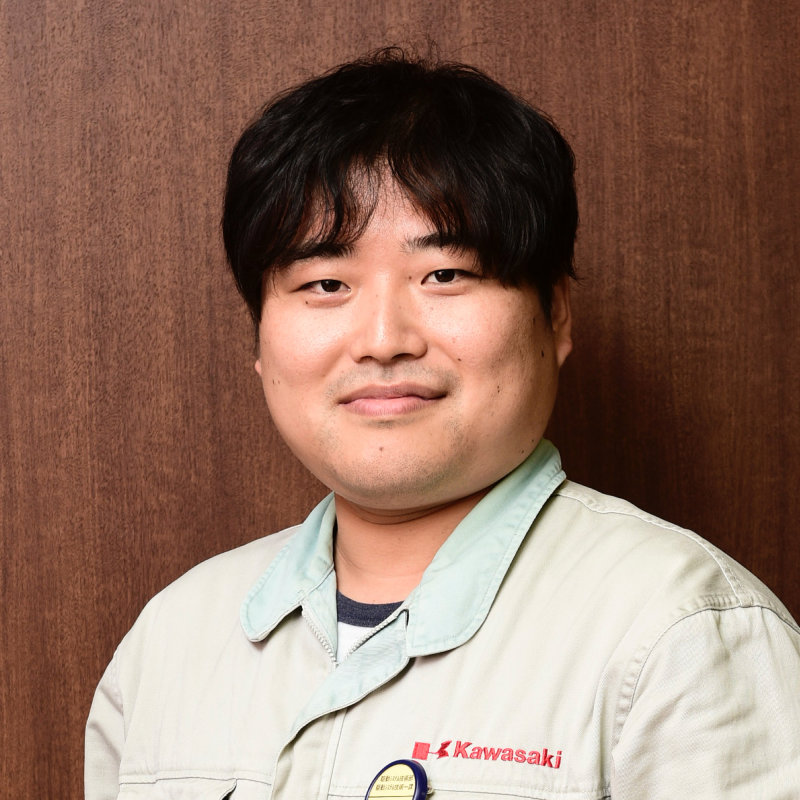
航空宇宙システムカンパニー
民間エンジンプロジェクト本部
駆動システム技術部 駆動システム技術一課
主事補
※文中に登場する数値・所属などは2018年10月の情報です。