「ボーイング787」生産の一翼を担う川崎重工は、名古屋第一工場内に3つ目となる「787専用工場」、東工場を完成させました。最初の工場の完成から9年、新たな東工場にはこの間の経験と知見が凝縮されています。急増する航空機の世界需要とその安全性を担う、川崎重工の最前線を訪ねました。
「787」のものづくりを進化させる新工場
「ボーイング787 ドリームライナー」は座席数が200〜300台の中型機で、先進的な空気力学と新しいシステム・エンジンの採用、また軽量化により、従来の同型機に比べて燃費を約20%、運航コストを約30%向上させました。それに伴い航続距離が飛躍的に延び、世界中の航空会社から圧倒的な支持を獲得。基本型である「8型」の他に、胴体を長くして座席数を増やした「9型」「10型」で「787ファミリー」をなしています。
ボーイング社によれば、2015年3月末までに3機種で総計1,105機を受注しており、世界中の生産パートナーメーカーと増産体制の整備を進めているといいます。
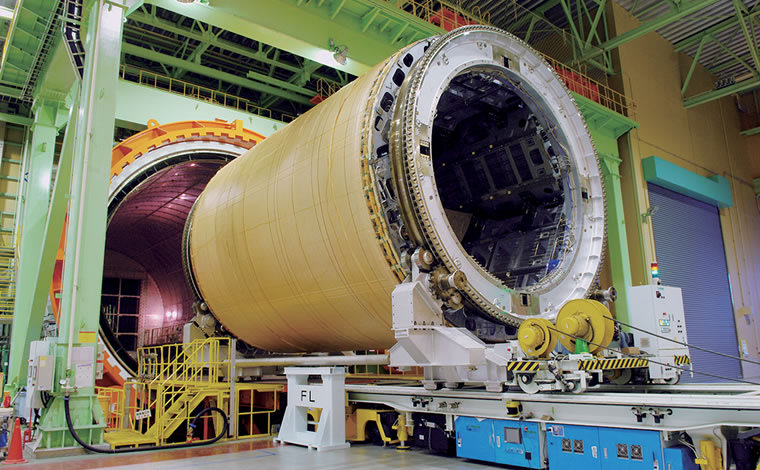
「787」の生産パートナーメーカーである川崎重工では、①前部胴体、②主翼固定後縁、③主脚格納部、の 3つの部位を担っています。今回、名古屋第一工場内に竣工した東工場は、北工場、南工場に続く3つ目の「787専用工場」です。この東工場では「9型」と「10型」の前部胴体を生産。特に「10型」の生産開始に向けて、北・南工場と同様に各種の最新鋭設備を導入するとともに、今までの経験と実績を活かしさらに進化させたものづくりを実現します。
航空機に求められるのは、乗客を守る絶対的な安全性。そのために航空機関連メーカーは、生産設備について国際的な認証を取得しなければなりません。
「求められる機能や品質を、正確につくり続けられる」ことが重要なのです。ただ、それを実現する手法について制限はありません。そこにメーカーの創意工夫が発揮される余地があります。
「ボーイング787」は、開発段階では「7E7」、つまりEfficiency=効率と冠されていた通り、抜群の燃費の向上と運航コストの低減を実現。川崎重工をはじめとする日本の航空機関連メーカーは、全体の35%の生産を担っています。
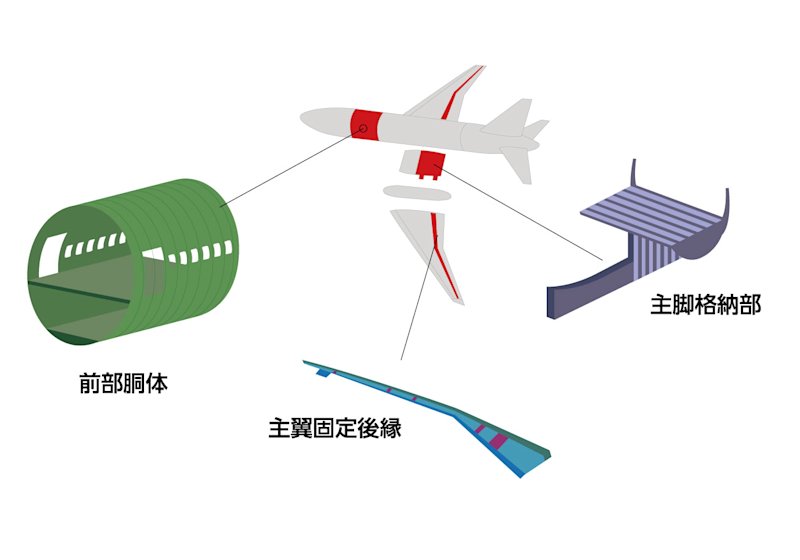
炭素繊維複合材による前部胴体の一体成形
「787」生産の一翼を担う川崎重工 航空宇宙カンパニー 生産本部 の白石 明裕 副本部長は、「毎日、きっちりと同じものをつくり続けることが最も難しい。日進月歩で進化しているのは、同じものをつくり続けるための技術。川崎重工では、治工具類はできるだけ自社製として改善効果を高める一方、徹底的に情報共有してものづくりの力を高めてきました」と語ります。
「787」が航空機づくりに革新をもたらしたと言われる象徴が、胴体や主翼などの一次構造部にまで採用された軽量・高強度の炭素繊維複合素材です。炭素繊維複合材は加工過程で材質が変化するため、生産メーカーは材質と形状の両方を保証する「プロセス保証」の責任を負うことになります。「プロセス保証が787生産の最も難しいところ」と言われるゆえんです。
特に川崎重工が担う前部胴体は、「ワンピースバレル」と呼ばれるつなぎ目が一切ない炭素繊維複合材による一体成形。これは民間航空機で初めて試みられた技術であり、この技術課題の克服こそが川崎重工の真価でした。
貼り、焼き固め、精度を極限まで追究する
「787」の一体成形構造の前部胴体は、①筒状の治具に炭素繊維複合材を積層する、②積層された炭素繊維複合材をオートクレーブという窯で焼き固める、③部品位置決めの孔を開ける、④超音波による非破壊検査、⑤胴体内への補強部品の取り付け、⑥床やダクトなどの取り付け、という6工程を経て完成します。
まず、炭素繊維複合材の積層は、自動積層装置「AFP(Automated Fiber Placement)」が担います。装置は「蚕」のイメージ。蚕が口先から糸を吐くように、装置先端部から複数本の複合材が出て筒状の治具に貼られます。
川崎重工 航空宇宙カンパニー 787生産技術部 787プロセス技術課の多田 章二 主事は、「炭素繊維複合材は、いわば『気分屋の生鮮品』。その性質を見抜き、安定した積層手法を確立することが課題でした」と語ります。
例えば、貼り付きの良し悪しが決まる粘度は、時間の経過により変化します。「複合材を積層するヘッドの構造や貼り方、作業場の湿度など、あらゆる要素の相関について知見を深め、最適な手法の確立に挑んできました。東工場に導入されたAFPは、これまでの787生産のすべての経験と知見を投入してアップグレードしています」(多田主事)
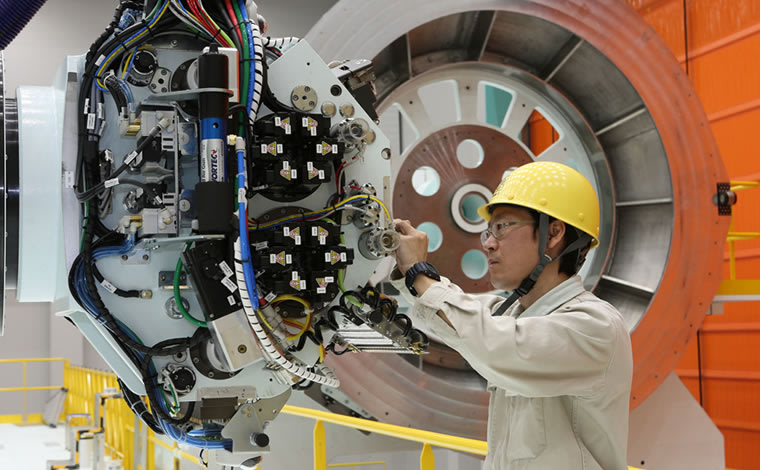
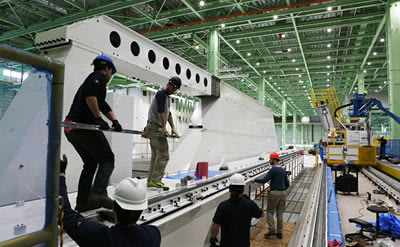
次に、積層された炭素繊維複合材を、オートクレーブと呼ばれる加熱・加圧窯で焼き固めて硬化します。東工場に設置されたオートクレーブは全体の重さが900t、硬化炉の内径が約8m、長さ約19mという巨大なもの。「787」の基本形である「8型」の前部胴体と比較すると、「10型」ではだいぶ長くなります。東工場のオートクレーブは、「10型」にも対応できるように関連会社である川崎エンジニアリングが川崎重工の播磨工場で製作しました。
開発を担う川崎エンジニアリング 産業プラント部の前川 完二 部長は、「オートクレーブのポイントは『炉内温度の均一性能を達成すること』、これに尽きます」と語ります。
炭素繊維複合材の強度・性能を確保するには、全体を均一に硬化しなければなりません。また炉内温度の均一性能は、納期の順守や短期化にも直結します。特に東工場のオートクレーブは世界最大級の胴径を有し、長い胴体の硬化を行うため、均一性能の達成は何より重要な課題なのです。この課題解決のために、技術開発本部や関連会社の川重テクノロジーなどが培ってきた熱解析技術を活用し、炉内の温度分布についてさまざまなシミュレーションを繰り返したと言います。
「プラントやボイラ設備で培ったものづくりの総合力によって、精密品レベルのオートクレーブを実現できました」(前川部長)
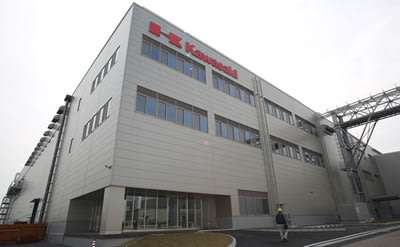
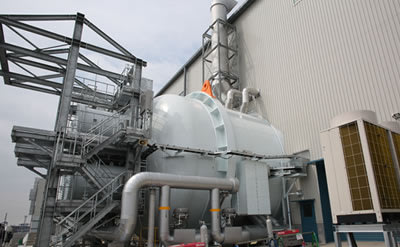
自動リベッターに「人の五感」を添えて
焼き固められた炭素繊維複合材は、大型の一体成形胴体としての威容を見せます。この検査工程で使われる超音波非破壊検査装置は、川崎重工が世界で初めて開発したものです。
非破壊検査が終わると、胴体に補強用のフレームを取り付ける作業へと進みます。ここで活躍するのが「パネルリベッター」。胴体とそれに仮り付けされたフレームに同時に孔を明け、ボルトを締めるという一連の作業を自動で行います。
長いレールが胴体を外側と内側から挟み込み、その上を機械が移動していくイメージです。具体的には外側の機械で孔を明けてボルトを入れ、それに内側の機械が同期して打鋲していきます。
パネルリベッターの導入を担う川崎重工 航空宇宙カンパニー 787生産技術部 787組立技術一課 の三輪 和彦 基幹職は、「孔を明けてボルトを入れると言っても、前部胴体は長さがかなりあるので正確な位置決めや機械同士の同期など、精度確保が大きな課題です」と説明します。
前部胴体では、多数のボルトの孔明けと打鋲を行います。その孔位置の誤差は0.3㎜以内でなければなりません。作業時は全自動ですが、「必ず人の五感を添えることが、精度の向上と品質の確保につながります」と三輪基幹職は言います。
安定した作業を続けるためにはドリルの摩耗具合を感知する熟練の作業員が不可欠で、作業前と作業後には必ずテストピースをつくり、自動作業の精度を人の目で確認するのが必須になっています。
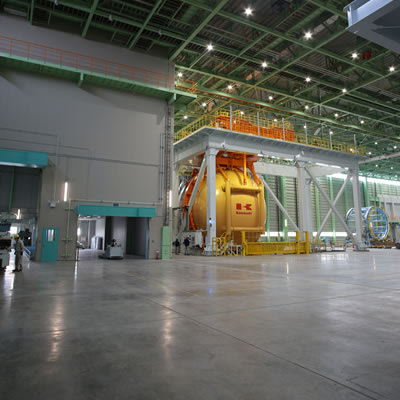
この工程では、川崎重工の独自技術も導入されています。打鋲作業のために胴体が回転するのです。リベッターの位置は同じで、胴体側が回転して次の打鋲に入ります。こうすることで内側にいる作業者は一定の姿勢で作業ができます。
「正確な打鋲を実現するために、現場の人が作業しやすい機械を創造しました。胴体の回転角度や速度なども含め、絶え間なくプログラムや機器類の見直しを続けています」(三輪基幹職)。
「QSKY」が育てる世界で最も効率の良い工場
東工場の竣工で、川崎重工の生産体制は従来の月間10機から14機に増える見込みです。そもそも「787」の生産は、大型機の量産という経験のないものづくりへの挑戦でした。航空宇宙カンパニーでは、ボーイング社の量産手法や川崎重工独自の生産改革手法「KPS(Kawasaki Production System)」の源流である二輪車事業などからもそのノウハウを学んでいます。
それは「愚直な実行」を基本とし、さらに「QSKY(Quality・Safety・危険予知)」という標語に集約された「品質安全と安全作業は同じもの」という考え方だ。このポリシーによって作業の改善内容は広く共有され、良い事例はどんどん真似することが奨励されました。
例えば航空機は左右対称ですが、使われる部品は微妙に異なっているため、取付け部品を間違わないように治具を改善。また、各工程での作業員の動きをビデオで撮影して動線を分析し、ムダのないスムーズな動きを探ることで、工程時間の短縮を実現しています。
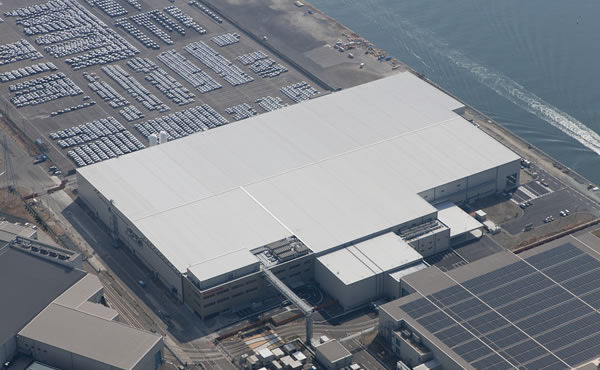
こうした地道な活動が、ボーイング社から「世界で最も効率の良い工場」と賞賛される成果を生み出しました。「サプライヤー・オブ・ザ・イヤー」などのさまざまな表彰につながるだけでなく、川崎重工のものづくりは大空の安全に貢献しているのです。
竣工式で、東工場の全容を関係者に公開
川崎重工は、2015年3月13日に愛知県弥富市の名古屋第一工場内に新設された東工場の竣工式を開き、内部を報道関係者にも公開しました。
東工場は延床面積が約6万m3で、2013年12月から建設を開始していました。竣工式にはボーイング社の関係者や愛知県の大村知事が出席、中部地区の航空宇宙産業の新たな一歩を祝いました。
ボーイング787の生産能力を増強するとともに、高品質の製品提供を通じて本プロジェクトに貢献し、さらには民間航空機事業の拡大を目指していきます。
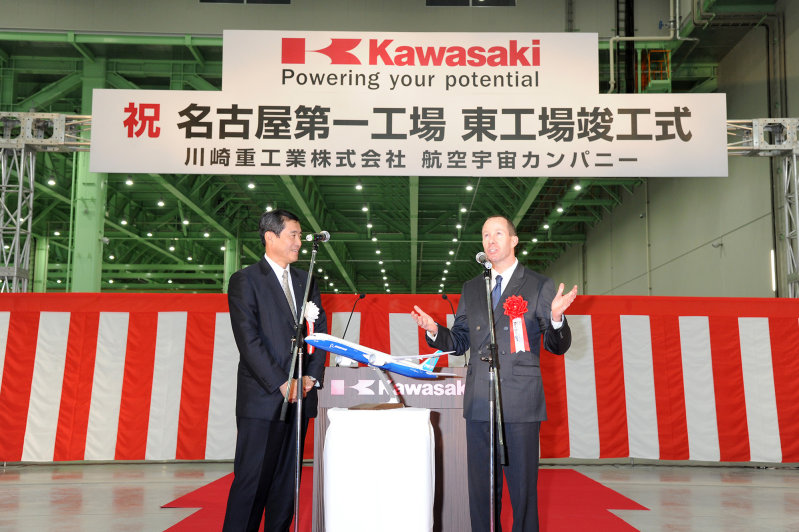
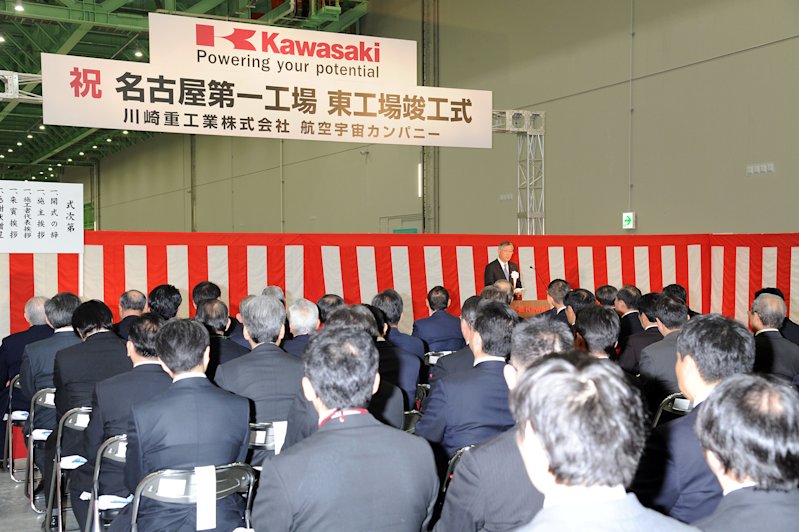
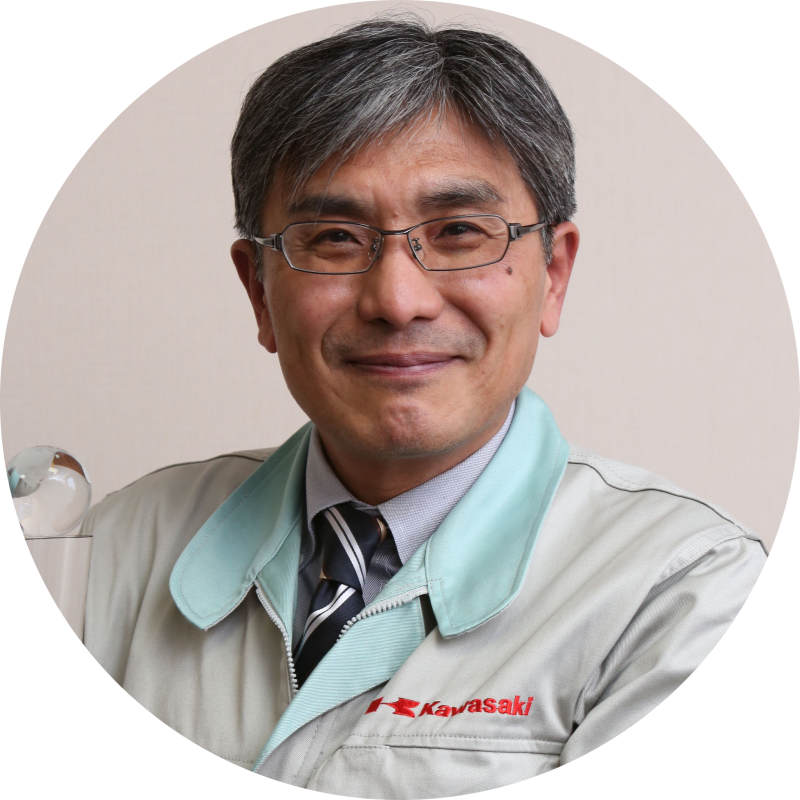
航空宇宙カンパニー
生産本部
副本部長(理事)
Working Togetherに賛同し、確固たる生産体制を整える
「787」は、世界中のメーカーが協力して生産するパートナー比率の高い航空機です。このためボーイング社は「Working Together」を掲げ、具体的には生産現場における「Boeing Production System(BPS)」への同調を求めました。世界中の生産パートナーメーカーが、あたかもオーケストラの演奏の如く協和し、スムーズなものづくりの流れを生み出そうとしたのです。これは安全な航空機を創造するための新たな取り組みでした。
BPSはトヨタ自動車の改善運動に学んだものですが、川崎重工の改善運動である「KPS」もまた同社が源流で、両者は高い親和性を備えています。互いに学び改善する活動は、安定品質や「納期遅れ/欠品率ゼロ」などの輝かしい成果につながり、川崎重工のプレゼンスを高めています。
新工場の東工場では、「787」の派生機である「9型」「10型」を生産しますが、階段状に増加する生産機数を見越し、増産に対応できる工場として立ち上げることも重要な課題でした。部品調達や生産ラインの同期をスムーズに実現しなければならず、こうした点にも航空機づくりの知られざるノウハウが発揮されます。
そのノウハウを確立するために、技術開発本部や関連企業の協力も得ています。これまでも複合材の切削用刃具や超音波非破壊検査装置の分析手法などが開発され、東工場の建設に際しては仕掛品や搬送スケジュールなど、3工場体制の最適な生産管理シミュレーションもなされています。「ALL KAWASAKI」の力が、安全な航空機を造るために投入されているのです。
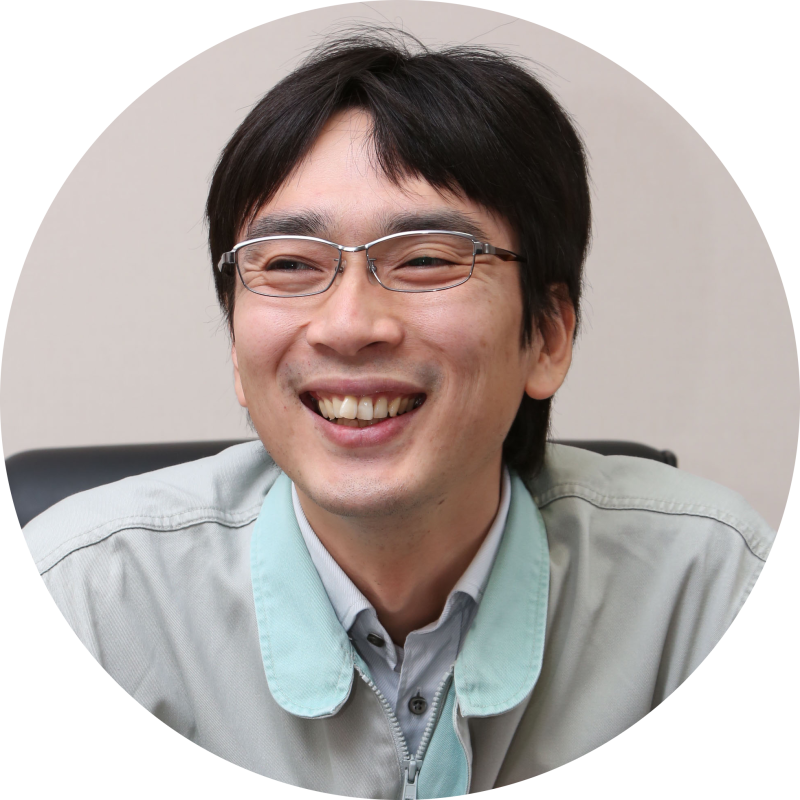
航空宇宙カンパニー
787生産技術部
787プロセス技術課
主事
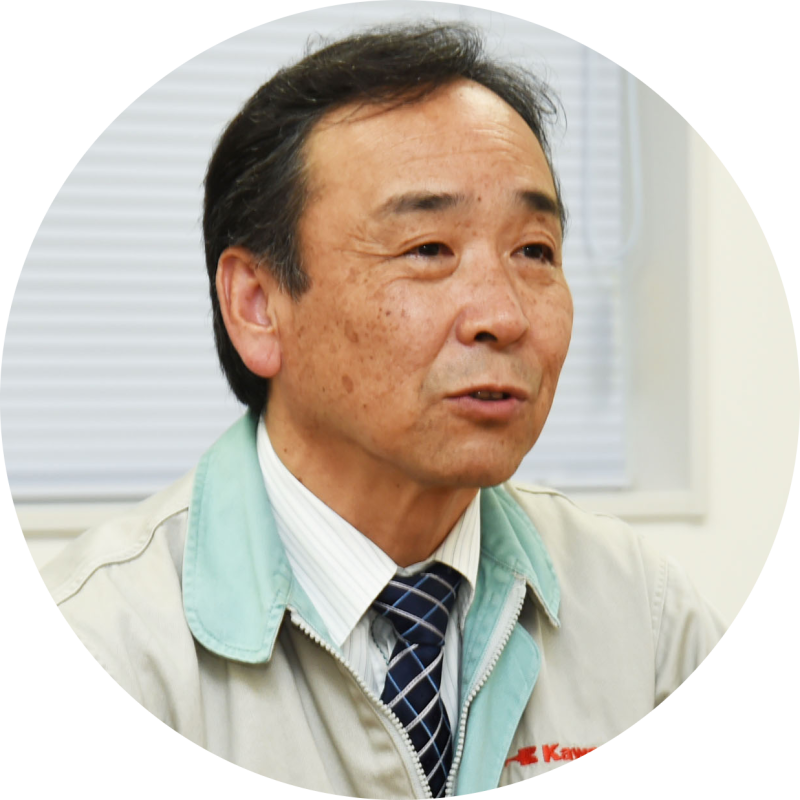
産業プラント部
部長
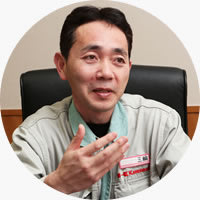
航空宇宙カンパニー
787生産技術部
787組立技術一課
基幹職