日本政府が発表した「2050年カーボンニュートラル宣言」を機に、いま企業が脱炭素に向けた取り組みを加速しています。川崎重工は自社の事業プロセスにおけるCO₂排出量削減はもちろん、CO₂の分離・回収、次世代エネルギーとして注目されている水素の技術開発およびその活用を推進しています。輸送、エネルギー、産業用機械などの多彩なフィールドにおいて、最前線の取り組みをご紹介いたします。
CO2をゼロにするのではなく、排出量と吸収量の相殺が「カーボンニュートラル」
2020年10月、「2050年までに温室効果ガスの排出を全体としてゼロにする、2050年カーボンニュートラル、脱炭素社会の実現を目指す」と菅総理によって宣言されました。また、2030年度のCO2排出量を2013年度比で46%削減する目標も発表。この高い目標のもとに民間企業の大胆なイノベーションをうながし、新時代に向けた挑戦を支援する「2050年カーボンニュートラルに伴うグリーン成長戦略」も策定されました。これを機に、民間企業において温室効果ガスの排出抑制に向けた新事業の開発や方向転換が進みつつあります。
そもそも「カーボンニュートラル」とはどのような意味でしょうか。直訳すると「カーボン」は炭素、「ニュートラル」は中立という意味です。しかし、ここでは菅総理の「温室効果ガス」というワードに注目してみます。日本政府が目指す「カーボンニュートラル」は、CO2に限らず、メタン、N2O(一酸化二窒素)、フロンガスを含む「温室効果ガス」を対象にしています。また、「排出を全体としてゼロにする」と述べている点も注目です。「全体としてゼロに」とは、「排出量から吸収量と除去量を差し引いた合計をゼロにする」ことを意味します。つまり、温室効果ガスの排出を完全にゼロに抑えることは現実的に難しいため、排出せざるを得なかった分については同じ量を「吸収」または「除去」することで差し引きゼロを目指す、ということになります。これが、日本政府が進める「カーボンニュートラル」なのです。
CO2は元々、大気中、地中や地表、水中にも存在します。炭素は生物の呼吸、有機物の燃焼、腐敗などによってCO2の形で大気に放出されていますが、植物は光合成によってCO2を吸収し、海も大気と接することでCO2を吸収しています。炭素は循環しますが、それぞれの場所で量は安定しているのです。地中には、石油、石炭、天然ガスといった化石燃料があります。人間が掘り出してエネルギーとして利用し大気に放出するため、大気の炭素濃度が上昇して温暖化を引き起こしています。
川崎重工 エネルギーソリューション&マリンカンパニーの渡辺 達也 プレジデントは語ります。「私たちがめざしているのは、カーボンゼロではなくカーボンニュートラルです。CO2は生物にとってある程度の量は必要です。過剰に排出しすぎていたものを改めること、極端なことを言えば、カーボン自体をリサイクルする取り組みが重要なのです。いま、水素エネルギーが注目を集めていますが、水素エネルギーの製造過程ではCO2が排出されます。このCO2をニュートラルに変えた上での水素利用こそが重要です」。
現在、日本の年間CO2排出量は、12億1,300万トン(2019年度/国立環境研究所調べ)にのぼります。この膨大なCO2排出量をいかに削減するか、私たちがクリアすべき課題は多くあります。※1
※1 EMIRA「『カーボンニュートラル』って何?脱炭素社会に生きるための基礎知識」 および経済産業省 資源エネルギー庁「『カーボンニュートラル』って何ですか?(前編)~いつ、誰が実現するの?」 参照
川崎重工が進める「カーボンニュートラル」。事業プロセスにおけるCO2 FREEの取り組み
鉄道車両、航空機、エネルギー・環境製品、産業機器、モーターサイクルなど幅広いフィールドで事業を展開する川崎重工グループ。その環境経営は、1994年の第1次環境経営活動基本計画の策定から始まりました。1999年には基本理念および行動指針である「環境憲章」を定め、重工業界で初めて「環境報告書」を発行。
そして、地球温暖化の抑制に向けて発効されたパリ協定や、国連により採択された持続可能な開発目標(SDGs)など、世界的に地球温暖化対策の必要性が高まるなか、より高いハードルを課した「Kawasaki地球環境ビジョン2050」を策定。CO2 FREE(低炭素社会の実現)、Waste FREE(循環型社会の実現)、Harm FREE(自然共生社会の実現)につなげる重点施策を設定し、「世界の人々の豊かな生活と地球環境の未来に貢献する『Global Kawasaki』」というグループミッションの実現に向けて、さらなる環境経営を進めています。
第10次環境経営活動基本計画(2019~2021年度)では、特にCO2 FREEの実現に注力した活動を推進。事業プロセスにおけるCO2排出量のさらなる削減と、CO2排出の少ない製品の提供拡大により、大幅なCO2排出量の削減を目指します。※2
川崎重工では事業活動でのエネルギー使用において、購入電力の占める割合が高いため、自家発電設備の積極活用、太陽光発電による再生可能エネルギーの活用、省エネルギー活動を主に進めています。
川崎重工 環境・エネルギー管理部の安藤 嘉人 部長は語ります。「現在、明石工場、神戸工場、岐阜工場で自家発電設備が稼働中です。明石工場では自社開発のFEMS(Factory Energy Management System)を導入しました。電力使用の経験値をシステムに覚えさせて判断させることで、年間の電力使用の効率化を図っています」。
「EMS(Energy Management System)」とは、ガスタービン、ガスエンジン、ボイラなど多様な機器などで構成される複合エネルギー設備のこと。各エネルギー機器の出力配分や運転パターンを最適化し、運用コストを最小まで低減することができます。その工場向けシステムを「FEMS」と呼ぶのです。

また、川崎重工の西神工場では、「PPA(Power Purchase Agreement)モデル」により太陽光発電を導入しています。「PPA」とは、売電事業者と需要家が直接、電気の売買契約を結ぶことを言います。日本においては「太陽光発電の無償設置」というビジネスモデルを「PPAモデル」と呼ぶことが多くあります。需要家の屋根上に、太陽光発電システムの設備を無償で設置し、発電した電力を需要家が購入する仕組みです。
安藤部長はその効果について語ります。「現在、西神工場で使う電力量全体の3%を太陽光発電で賄っています。工場全体の電力量から見ると少量ではありますが、これらの電力は全てCO2排出量がゼロになります。初期投資も抑えられ、電気料金も安くなるのでコスト的なメリットも大きく、他の工場でも導入を検討中です」。
また省エネルギー活動において、自社開発のエネルギー見える化システム(K-SMILE)を主要工場に導入しています。安藤は「当社では省エネに関してはいち早く取り組んできました。K-SMILEの導入によって、現状把握により設備運用のムダと、ムラを見つけることができます。システム故障の予兆検知も可能です」と解説します。
今後はS+3E(Safety, Energy Security, Economic Efficiency, Environment)を踏まえて、安全性を担保したうえでエネルギー調達先の最適化も進めていくといいます。
川崎重工は2021年7月より、神戸本社で使用する電気をCO2フリー電気に切り替えました。この電力は、グループ会社であるカワサキグリーンエナジー株式会社から神戸本社が入居する神戸クリスタルタワー向けに供給されます。
使用する電力は、実質的に全量を再生可能エネルギー由来としたRE100※3対応の電力となります。これにより、神戸クリスタルタワーの電力使用に伴うCO2排出量は実質ゼロとなり、年間約2,000トンの削減が見込まれるといいます。
また、エネルギーの最適化を工場単位で考える時代から、複数工場で最適化を図るMEMS(Multisite Energy Management System)を推進。さらに、省エネ設備導入により減少したCO2排出量に価格を付けて評価を行う「ICP(Internal Carbon Pricing(社内炭素価格)」の構築も検討しています。これは、省エネ設備への投資が、生産に直結する設備に比べて優先順位が低くなる傾向を解消するためのものです。
安藤部長は環境保全活動への想いについて語ります。「自然は祖先からの“贈り物”ではなく、子孫への“預かり物”であるというアメリカンネイティブの言葉があります。未来の子どもたちのために、“地球防衛軍”のような意気込みで環境を守る活動を進めています」。
※2 川崎重工プレスリリース「『Kawasaki地球環境ビジョン2050』を策定~3つのフリー(CO2・廃棄物・有害化学物質)へ挑戦~」 2017年8月9日付 参照
※3 企業が事業で用いる電気を100%再エネで賄うことを目指す国際的な取り組み。「Renewable Energy 100%」の頭文字。
製品貢献によるCO2排出量削減へ。独自基準を満たす製品を社内表彰で評価
川崎重工は脱炭素社会の実現のために、使用時のCO2排出量が少ない製品の提供も目指しています。安藤部長は「当社製品の運用時におけるCO2排出量は、事業活動における排出量の100倍以上となります。排出量の小さい製品を世の中に送り出すことも私たちの重要な責務です」と語ります。
そこで、製品自体の環境性能向上と、生産過程での環境負荷低減を図る取り組みとして、独自に定めた基準を満たす製品を「Kawasakiグリーン製品」「Kawasaki スーパーグリーン製品」として評価し、ISO14021に準拠して社内外に発信しています。さらに、「Kawasakiスーパーグリーン製品」の全登録製品の中から環境に関連する社外評価を受け、かつ、対象期間において事業経営への貢献が大きかった製品を「Kawasaki環境大賞」として特別表彰しています。2020年は5MW級で世界最高の発電効率と環境性能を達成した「M5A-01Dガスタービン」が受賞しました。
製品貢献によるCO2排出量の削減効果の独自の算定ルールも設定し、その結果、川崎重工が2019年度に販売した製品によるCO2削減効果は約2,314万t- CO2にも達しました。
Kawasakiグリーン製品 2020年登録製品(一例)
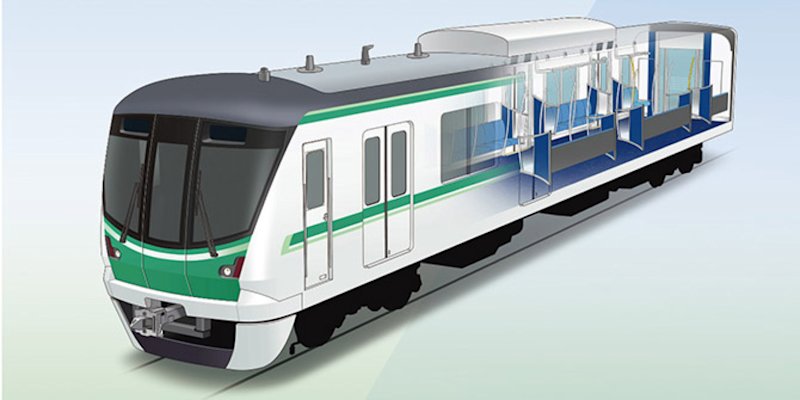
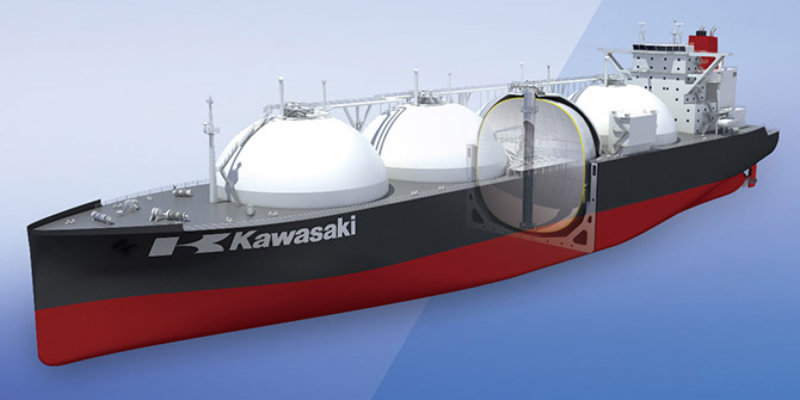
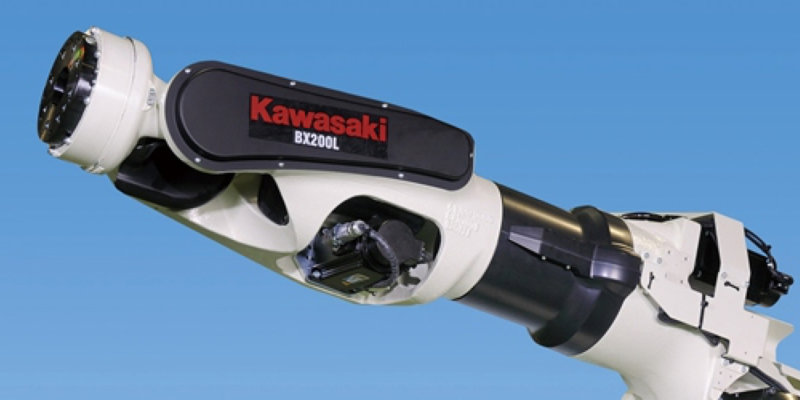
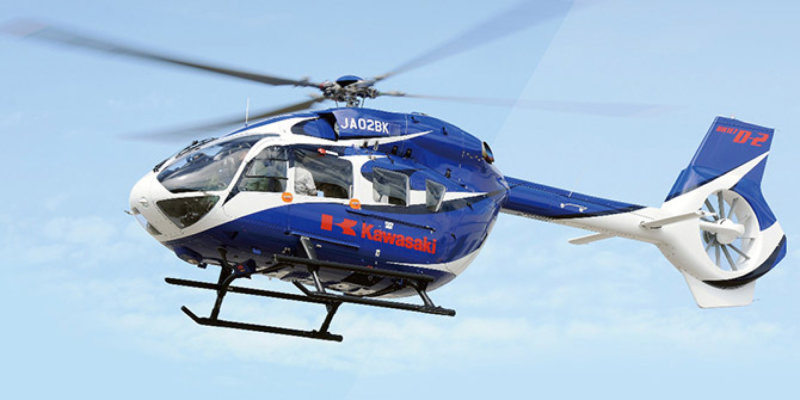
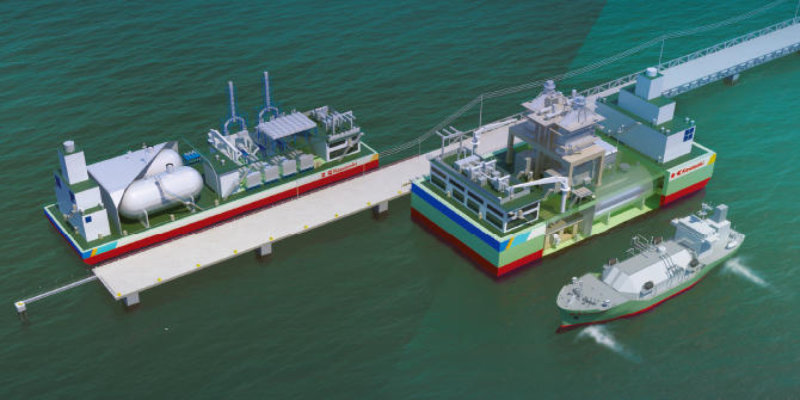
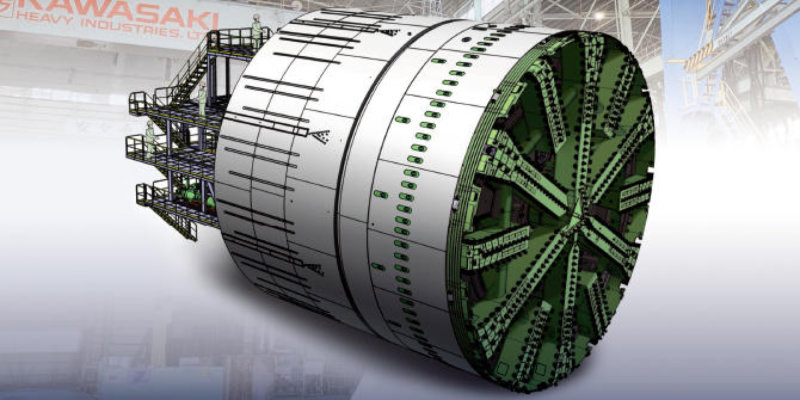
究極のエネルギー「水素」を活用するトップランナーとしての先進技術
現在、脱炭素社会実現のエネルギーとして「水素」が大きな注目を集めています。川崎重工は水素エネルギー技術におけるトップランナー企業として技術革新を推進しています。
渡辺プレジデントは語ります。「石油、石炭、太陽光や風力など従来の多くの一次エネルギーは、二次エネルギーに変えて保管・保存することができません。水素は余った電力を使って水を電気分解する『Power to Gas』により蓄えることで、時間と空間を移動できます。また、水素はエネルギー源のガスにして利用した後は水になります。石油や石炭は燃やしてしまえば CO2と他のガス体になってしまい、それを変換する方法がありません。水素は水になり循環できる、この点において究極のエネルギーと言えます」。
「つくる」「はこぶ・ためる」「つかう」のプロセスにおいて、水素エネルギーの技術開発を進める川崎重工。オーストラリアに存在する褐炭から水素を製造し日本へ運ぶ世界初の液化水素運搬船の実証試験、市街地でのガスタービンによる純水素を燃料とした熱と電気の同時供給、純水素に対応するガスタービンの燃焼試験、水素燃料航空機用の燃焼器の研究開発など、先進的な取り組みで世界をけん引しています。
そして2021年5月、液化石油ガス(LPG)とアンモニアを運ぶ兼用運搬船を開発しました。アンモニアは燃やしてもCO2が出ないことからエネルギー分野での需要増加が見込まれています。
渡辺プレジデントは解説します。「水素を効率的に貯蔵・運搬するキャリアとしては、液化水素、アンモニア、有機ハイドライドがあげられます。将来的には、この3つは使い分けされるのではないでしょうか。アンモニアは畑の肥料のほか工業用アンモニアとして利用され、運搬技術が確立されています。今後、水素キャリアとしての技術開発も急速に進むかもしれません」。
さらに、渡辺プレジデントはものづくりの未来についてこう語ります。「IT技術などがどれほど急速に発達しても、ものづくりの根幹は変わらないと考えます。例えば、液体水素を-253℃でキープする、大量に運ぶ船やタンクなど、技術の大切さは変わりません。変わるのは、情報活用による生産性の効率アップ、ほしい人に届けるスピードなどです。今後は、私たちにしかできないものづくりの技術はしっかりキープしながら、それ以外は他社と協力しアライアンスを進めていく必要があります。全てを自分たちでやろうとすると、国際競争力を失い国内市場をも奪われてしまい、ガラパゴス化されてしまいます。これからはますます、グローバルな視点での戦略が重要となるでしょう」。※4
※4 日本経済新聞「川崎重工業、アンモニア運搬船に参入 LPGと兼用可能」2021年5月31日付 参照
CO2の分離・回収、有効利用、貯留に向けた取り組み。固体吸収材を活用し大幅なエネルギー削減へ
いま、工場などから排出されるCO2を分離・回収、有効利用、貯留する「CCUS(Carbon dioxide Capture, Utilization and Storage)」のシステム確立も求められています。
川崎重工はCO2の分離・回収システムの研究開発を進めています。固体吸収材を用いた川崎重工のKCC(Kawasaki CO2 Capture)移動層システムを開発・改良することで、CO2分離・回収の性能向上を推進。この取り組みは、2015年度から経済産業省の委託事業「二酸化炭素回収技術実用化研究事業」として公益財団法人地球環境産業技術研究機構(RITE)と共同で行い、2018年度からNEDOの委託事業に移管されて実施されています。
明石工場で実証されたシステムをスケールアップし、関西電力株式会社の協力を得て舞鶴発電所内にパイロットスケール試験設備を建設。2022年度より石炭火力発電所から排出される燃焼排ガス中のCO2分離・回収試験を開始します。
川崎重工 技術開発本部 技術研究所 熱システム研究部の柏原 宏行 部長は解説します。「CO2の分離・回収技術は昔からあり、化学プラントなどで利用されています。私たちが開発を進めているのは省エネと低コストを実現するシステムです。従来はアミン水溶液がよく利用されていましたが、CO2を吐き出す際に120〜130℃の熱が必要でした。これは水の沸点より高い温度のため多くのエネルギーが必要になります。固体吸収材は水を含まないため60℃の熱を利用でき、これまでは捨てていた低い温度の熱エネルギーを有効利用できるのです。従来に比べて、この個体吸収方式では40%以上のエネルギー削減が期待できます」。
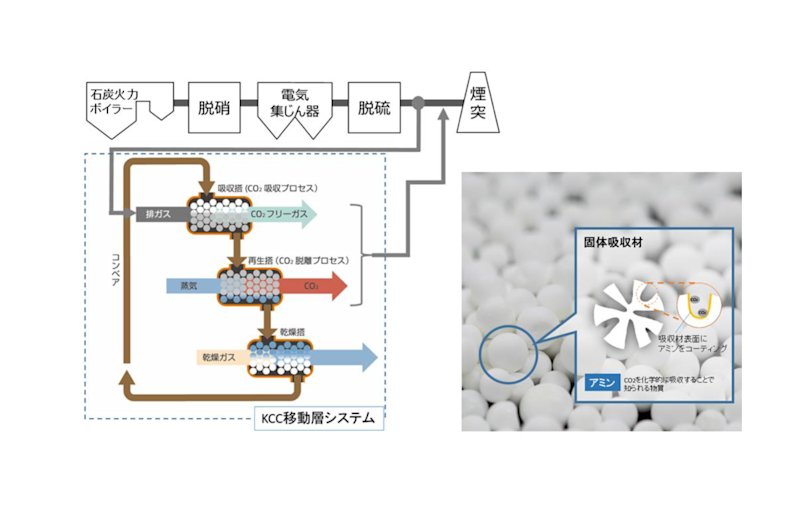
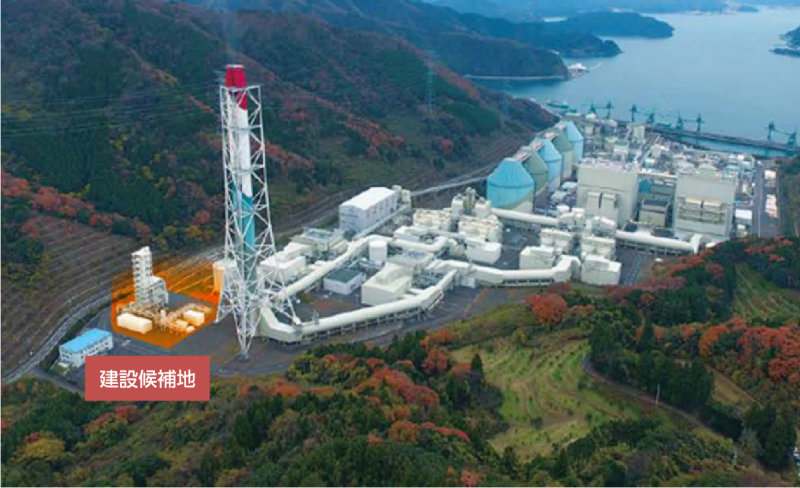
「カーボンニュートラル」「脱炭素社会」の実現に向けて、技術開発や取り組みが加速しています。温暖化への対応を経済成長の制約と考える時代は終わり、長期的な視野のもと、企業成長の機会ととらえる時代に変わりつつあります。
CO2排出量を、事業プロセスや製品の利用時において削減し、CO2の分離・回収技術の開発に取り組む川崎重工。脱炭素社会の実現をめざして環境問題を解決するとともに経済活性化にも貢献し、豊かな未来を切り開いていきます。
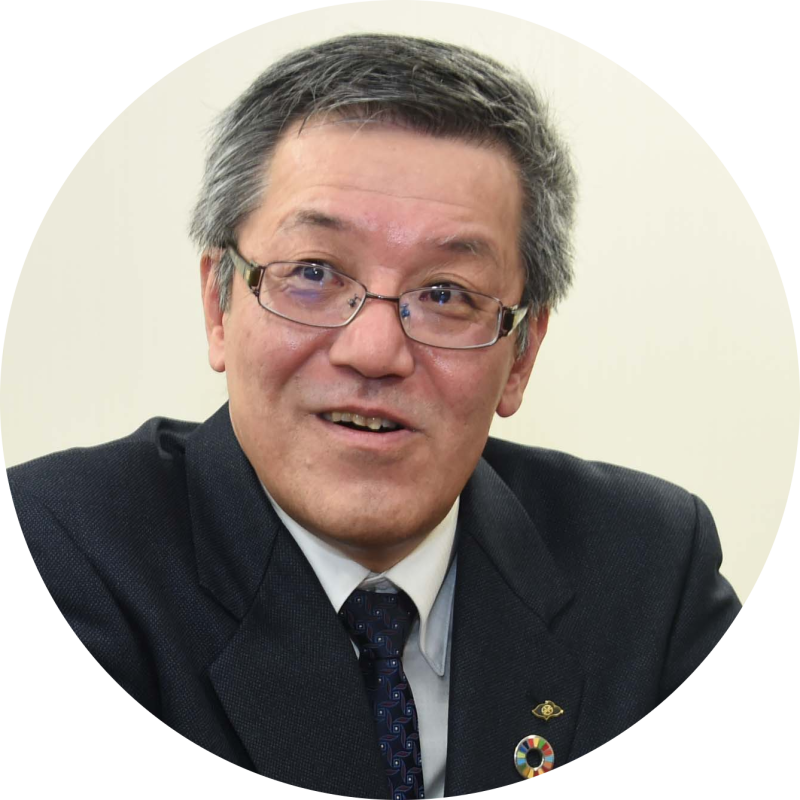
エネルギーソリューション&マリンカンパニー
プレジデント
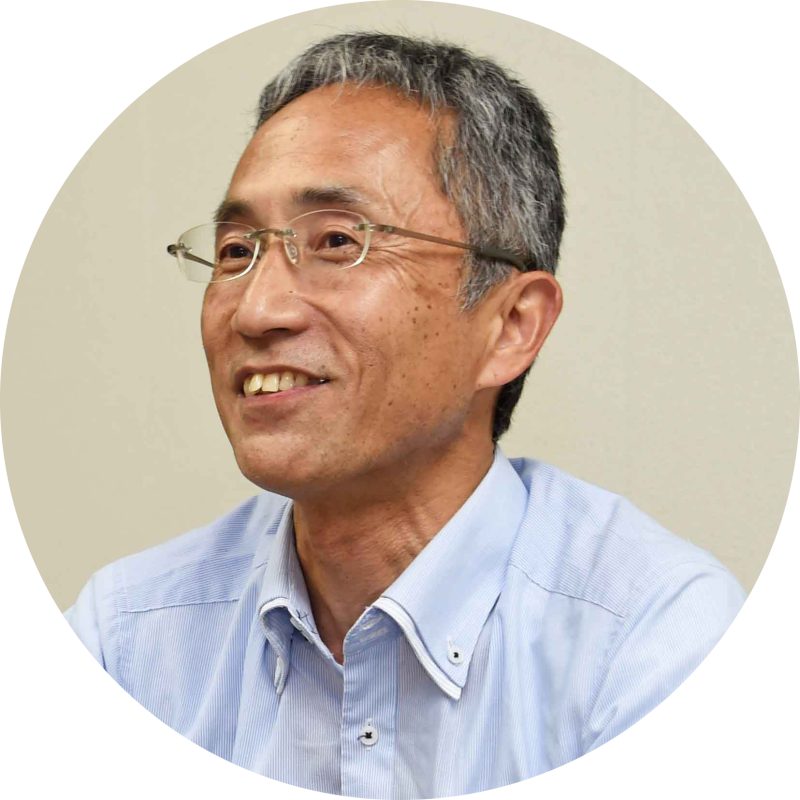
総務本部
環境・エネルギー管理部
部長
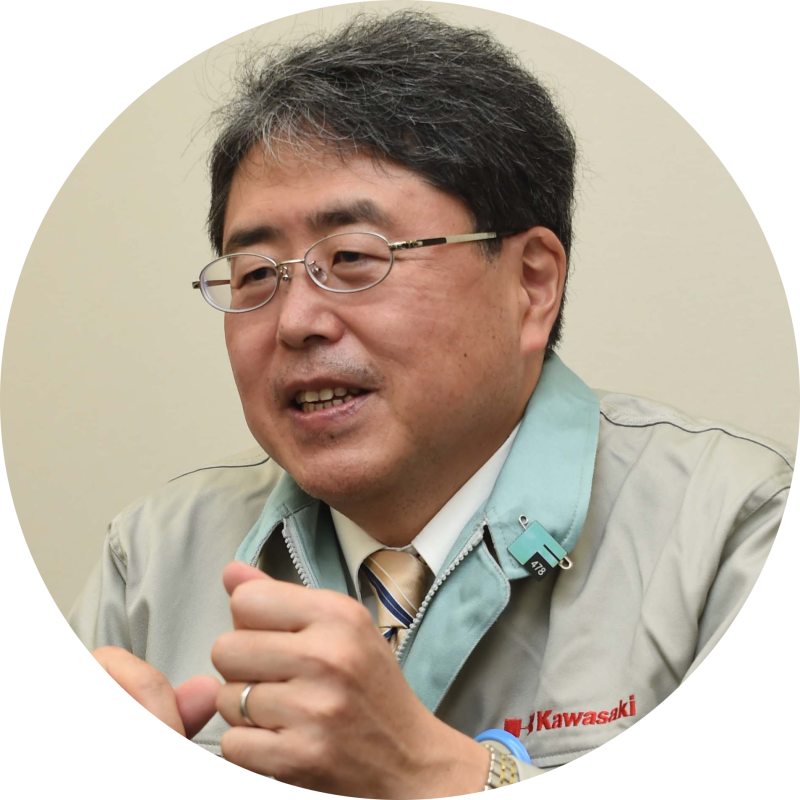
技術開発本部 技術研究所
熱システム研究部
部長