兵庫県神戸市に浮かぶポートアイランドは、日本初の都市機能をもつ人工島として1981年に誕生しました。豊かな大阪湾と古き佳き港町に挟まれたこのウォーターフロント都市には、いかにも清潔そうな白亜の巨大建造物がそびえています。たくさんの緑とふたつの公園に囲まれた謎の建物は、気鋭エンジニアを抱える一流テック企業のオフィスか、はたまた次世代医療の開発拠点か−−じつはこれ、創エネ視点でも大注目の「一度は行ってみたいごみ処理場」なのです。
災害時のエネルギー供給源にも
鉛を金に変えるのが錬金術なら、ごみをエネルギーに変える取り組みはさしずめ、21世紀の“エコ錬金術”といえるかもしれません。ごみを燃やした熱で蒸気を作り、タービンを回して電力を生み出すという、火力や水力発電ならぬ、ごみ発電。このテクノロジーの前では、ごみは単なる廃棄物ではなく、立派な資源なのです。
「ごみ焼却施設」=「エネルギー生産拠点」。神戸市ポートアイランド南東部に建つ港島クリーンセンターは、その考え方を2017年4月1日から本格的に具現しています。白い建物の前面には外壁と躯体が格子模様を描き、おしゃれなデスクトップパソコンを横にしたようにも見えます。これは、「テクノディスプレイ」と名付けられた意匠。ここに設置された3つの焼却炉では1日あたり600t のごみが焼却可能で、ごみを燃やした熱を元に作られる電力は、最大1万5,200kWにのぼります。神戸市長田区の約5万世帯分の電力消費量をカバーできるほどのボリュームです。ごみ発電によるエネルギーは、所内の電力として有効利用するほか、余剰分は電気事業者に売却しています。さらに非常用のガスタービン発電施設も備えており、万一の際のエネルギー供給源としても活躍するなど、災害にも強い施設を目指して建設されました。
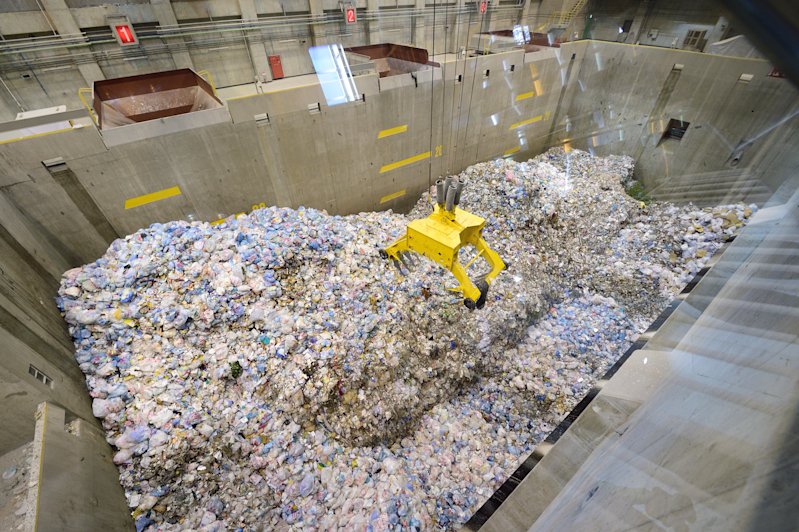
ごみ焼却炉の熱エネルギーを施設の暖房や近隣の温水プールや熱帯植物園などに使う「余熱の利用」は、これまでにも多く行われてきました。一方で、港島クリーンセンターの場合は火力発電と同じように、ごみ焼却時に生じる蒸気を使ってタービンを回し、発電するというもの。生活ごみそのものをリサイクル燃料として電気を得ることができる、いわばサーマルリサイクルの進化形なのです。
ところで、港島クリーンセンターの焼却システムの発電効率はじつに20.8%と、全国のごみ発電設備の平均値13.74%を大きく上回ります。この業界トップクラスの性能を支えているのが、川崎重工の生んだ「カワサキ・アドバンストストーカシステム」。巨大総合エンジニアリングメーカーが、もてる技術の粋を集めて開発した高度なごみ燃焼システムです。
高効率でクリーン、そしてタフ
ここで改めて、ごみの焼却炉の仕組みについておさらいしましょう。ごみの焼却方法は「ストーカ方式」「流動床方式」「ガス化溶融方式」の3つに大別できます。このうち最も歴史が古く、主流となっているのがストーカ方式であり、数の多さから技術革新も積極的に進められてきました。
ちなみにストーカとは日本語で火格子と呼ばれるもので、ごみを攪拌(かくはん)、搬送する台のこと。下から空気を送り込み、ごみを燃えやすくするため格子状になっています。このストーカを階段状に設置し、①水分を蒸発させる乾燥、②勢いよく燃やす焼却、③最後まで完全に燃やしきる後燃焼と、それぞれのゾーンへごみを移動させながら細かな灰にしていきます。
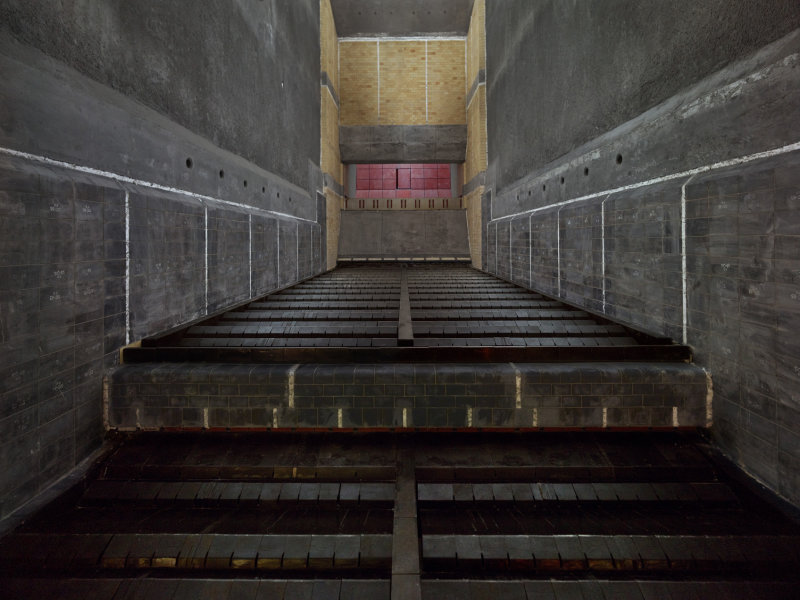
川崎重工が開発したのは“アドバンスト”の名前が付くとおり、旧来のストーカ方式をさらに一歩前進させたシステムです。より少ない空気でごみを完全燃焼し、高温燃焼により焼却灰や排ガスをクリーン化するとともに、熱回収効率をアップ、さらにブレなく安定的に運用できる“タフなメカニズム”を構築しました。
より少ない空気でごみを完全に燃やしきる
ごみがエネルギーに変わるまでの一連を、「カワサキ・アドバンストストーカシステム」の流れに沿って辿ってみましょう。まず、焼却炉の投入口からごみを投入。前後運動しながらごみを送り出していくストーカのうえで、乾燥・燃焼・後燃焼の工程を経て、3時間後、灰になったごみはシュートボックスへと集められます。この燃焼の際に生まれた熱エネルギーは、ボイラで高温・高圧の蒸気に変換され、その蒸気がタービンを回転させ、電気を生み出すという仕組みです。
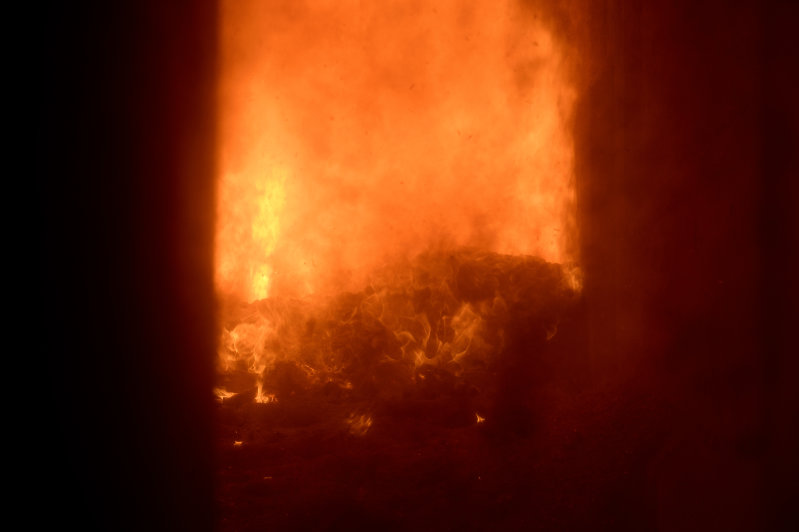
ここでポイントになるのが、いかに少ない空気でごみを安定的に、かつ完全に燃焼させるか。空気を増やせば燃焼の勢いは当然増しますが、その分排ガスが増えてロスが生じてしまいます。そこで川崎重工が採った方策が、「並行流焼却炉」。多くのストーカ炉は、ストーカの真上に口をあけた煙突からごみを燃やした熱や排ガスを“まっすぐ”に排出します。一方、段々下降していくストーカの面と並行するように仕切り天井を設置し、燃焼ガスを後燃焼エリアまで押し込んだうえで、仕切り上に設けた第2エリア=再燃焼域のへ強制的に“反転”させてから送りこむのが川崎流です。
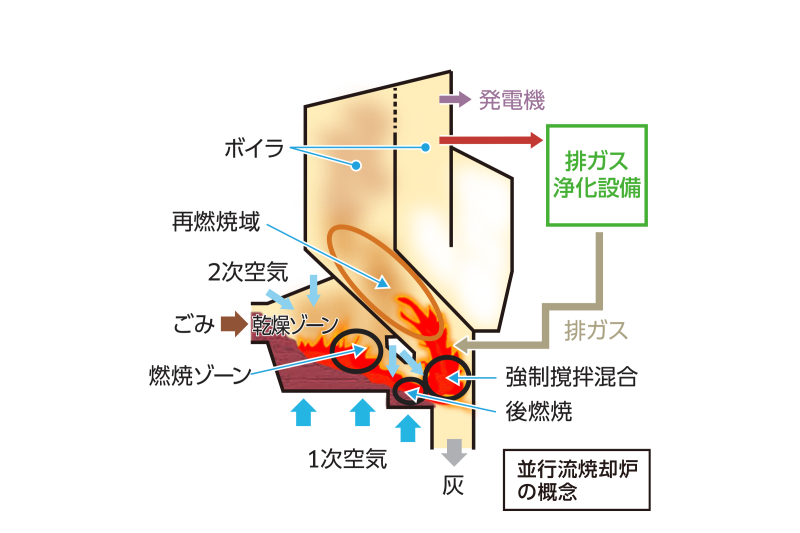
ごみと燃焼ガスを並行して流すことで完全燃焼を促すとともに、燃焼 ガスを反転させる際に空気と排ガスを強く攪拌することで高温を維持。これで排ガス中に含まれた未燃ガスも燃やしきります。結果、ごみ焼却の課題となっていたダイオキシンや一酸化炭素の発生を抑え込んでいるのです。もちろん、それでも残るわずかな排ガスは、コンパクトな排ガス浄化装置を通して清浄化。しかも、その一部を炉内に戻して、高温下維持のために“リサイクル”活用までしています。
「ごみ焼却ノウハウの塊」が詰まった制御技術
ところで、ストーカ(stoker)の名が「蒸気の釜に石炭をくべる人」を意味する英語に由来するとおり、この方式はヨーロッパから導入されたもの。しかし、ヨーロッパと日本ではごみの質が違います。湿度の高い日本では、ごみに含まれる水分量が多く、燃えにくいのです。そこで、ブレることなく良く燃やすために生み出されたのが前述の「並行流焼却炉」であり、それにくわえて、川崎重工はもうひとつの重要なテクノロジーで強化を図りました。「Smart-ACC(自動燃焼制御)」です。
川崎重工が独自に開発した「Smart-ACC」は、タービンを回すための蒸気量を安定して獲得するための自動燃焼制御技術。安定した蒸気は安定した燃焼から生まれますが、よく燃やすためにはごみと空気との関係性が肝となります。「Smart-ACC」は、ごみの発熱量や質などのデータをもとに、理想的な燃焼状態をキープさせるための高度なコントロール装置です。燃焼状態と蒸気量を適切に制御するこの先進テクノロジーは、「ごみ焼却ノウハウの塊」(川崎重工 プラント・環境カンパニー 環境プラント総括部 環境プラント部 装置技術課 橋元 篤志基幹職)なのです。
ごみ焼却ノウハウの塊、「Smart-ACC(自動燃焼制御)」とAI
ごみが燃焼したときに発生する熱量を把握することは、“良い燃焼”を作るカギ。その発熱量はごみの質によって変わります。しかも、ごみの質は、季節や地域によって多様に変化します。そのため、従来のごみ処理施設では、炉内の状況を人間が監視することで最適な燃焼状態を維持してきました。すなわち、どのような状態のときにごみをどれくらい炉に投入するか、空気や排気ガスをどれくらい投入するかを人間が的確に状況判断し、適切な運転操作を行なう必要があったのです。
その監視と制御業務をアシストするのが「Smart-ACC」。例えばごみをほぐして燃焼用空気との接触を安定させる独自の「揺動」動作を行うストーカや、焼却炉の中にあるごみの量を測定するセンサー、燃焼状況を把握して最適な燃焼用空気を供給するための排ガスセンサーなど、蒸気量の変動を抑えるための様々な仕事をシステム側が司るという先進の装置です。これにより、時間あたりの発電出力も調整しやすくなり、電力需要に応じた発電が可能になっています。さらに、新たに独自のごみクレーン制御やAIと組み合わせることでより精密な制御や予測を実現するなど、「Smart-ACC」はいまも日々進化を続けています。
川崎重工製品ならではのタフネス
なにより、この焼却システム全体の強力な基盤となっているのが川崎重工の誇るボイラおよびタービン技術です。水深400mで加わる圧に匹敵する4MPaという高圧、かつ400℃という高温に対応するボイラを使い、タービンを回転。安定して燃えているごみが発する“質のよい蒸気”を受けて、タービンも常に安定して回ります。すなわち、常に“質のよい電力”を事業者に供給することが可能になるのです。
もうひとつ、川崎重工が重視しているのが耐久性。高負荷のかかる環境で24時間365日稼働し続けるヘビーデューティーな産業向け製品を作り続けてきた同社だからこそ、いかなる酷使にもヘタれにくい部品開発に関するノウハウを持っています。たとえば燃焼炉に使用するボイラの過熱器には、管の腐食を防ぐために「肉盛溶接」という独自の溶接方法を採用。耐食性能の高い金属を管表面に“肉盛”することで、通常はおよそ10年で交換が必要といわれるところを、30年以上に長寿命化しています。こういった川崎重工製品ならではのタフな設計により、メンテナンス費は大幅にコストダウン。その総額はじつに15億円に達します。
川崎重工の総合力を投じて完成した「港島クリーンセンター」。敷地面積約3万8,900m2、延べ床面積約1万2,600m2の広大な空間で、「カワサキ・アドバンストストーカシステム」は日夜ごみを燃やし、電力を作り出しています。その先進のメカニズムは、10名以上の団体であれば実際に見学することができます(要事前予約)。自分の出すごみがどんな風に“電気”へ姿を変えるのか。百聞は一見にしかず。その壮大なエコシステムに一度、足を踏み入れてみてはいかがでしょうか。
ごみ処理場の役割を再定義する
「ごみは社会を写す鏡である」と言われます。とりわけ多くの人が集まる都市部において、ごみをクリーンに、スピーディに、効率よく処理することは、その街の景観と衛生、ひいては在り方そのものに直結する重要な生命線。日本を代表する港湾都市の神戸市は、国内でも最も早い時期である1963年にごみ焼却施設の第1号を稼働させました。以来、同市はごみ処理に関する多くの経験、そして技術を評価する知見を積み重ねてきました。さしずめごみ処理技術の“目利き”ともいえる自治体が、新しい焼却施設の作り手として選んだのが川崎重工でした。
2017年から稼働をスタートした港島クリーンセンターは、神戸市にとって11番目のごみ処理施設建設プロジェクトにあたります。都市部から目と鼻の先に位置する新しい拠点として、高い処理能力とクリーンな環境を備えること、そして、より効率の良いエネルギーセンターとなることが期待されました。川崎重工のテクノロジーとノウハウを注入した結果、港島クリーンセンターは完成以降、エネルギー回収率(ごみ処理量当たりの発電電力量)で全国トップ10の常連に。令和1年度(2019年度)には3位にラインクインしています。
川崎重工 プラント・環境カンパニー 環境プラント営業部 西部営業課 市江 和彦 担当 課長はこう語ります。「川崎重工は、各種プラントを手掛けてきた実績からごみ焼却施設でも発電、環境負荷の低減など、総合的なシステム提案ができます」。
川崎重工は、1964年に第1号のごみ焼却施設を愛知県一宮市に納入。さらに、1980年には4,000kWの大型発電施設を併設する京都市東部クリーンセンターを受注しています。それ以来、ごみ焼却施設を、「廃棄するだけの場所」から「エネルギーを生み出す拠点」として定義し直すべく技術を追求してきました。
「ごみ焼却施設が、地域のエネルギーネットワークの中心となり、かつ大都市では複数の焼却施設を抱えることで安定的な電力供給事業者になろうとしている現状から、プラント事業者は的確な提案力が求められています」(市江担当課長)。 そして1996年、ごみ焼却量1,500t、発電量2万7,000kWという国内最大級の施設が名古屋市・南陽工場に完成しました。30年超におよぶ研究開発が、大スケールの設備となって具現したのです。
港島クリーンセンターの「コンセプト」とは
先進のごみ処理場を神戸市ポートアイランドに建設するという一大プロジェクトにあたり、川崎重工は最初に3つのコンセプトを設定しました。まず「地域に貢献して、市民が自由に訪れたくなる施設」、2つ目が「環境に配慮した安全・安心な施設」、そして「経済性が高く、安定・継続したごみ処理ができる施設」であるということです。
神戸の中心地から目と鼻の先、観光地としても有名なエリアに設置する“ 都市型ごみ処理場”は、かくしてハイテクかつクリーンなエネルギー拠点として誕生しました。緑豊かな公園を隣接し、積極的に見学を受け付けているのもそれが理由です。
より豊かな巣づくりに貢献するテクノロジー
いま、日本のごみ排出量は年々減り続け、ごみ処理場は在り方そのものが転換期を迎えています。市江はこう話します。「リサイクルやリユースの浸透により、排出されるごみの量は減り、だからこそ地方自治体はごみ焼却施設をコストセンターではなく、プロフィットセンターに転換させようとしています。このニーズに応える社会的な意義は極めて大きいのです」。
無くす施設から、生み出す施設へ。「自分の巣を汚す鳥は繁栄できない」という格言にならうなら、「カワサキ・アドバンストストーカシステム」は巣の汚れを取り除くだけでなく、より豊かな巣づくりに貢献するテクノロジーとして、21世紀の社会を支える土台となるはずです。
川崎重工は1日の処理量が300t超という大規模施設を中心に焼却プラントを各地に納入しており、手掛けた78施設全体での1日の総処理量は約1万8,400tにのぼり、発電能力は500MWに達しています。いまや川崎重工製の焼却プラントは、地方自治体の環境問題、財政負担の解決の一助を担っているといえるでしょう。
さらに、同社は中国企業と合弁企業を設立し、ストーカ式ごみ発電施設をすで に10基受注。今後ごみ焼却施設の建設が増加するといわれるマレーシア、シンガポール、タイ、インドネシアといった市場も控えています。世界で最もごみ焼却施設の多い国、日本のすぐれた技術を世界に広めることは、「縮みゆく地球」を再び大きく豊かな星へと押し広げる一歩につながっていきます。
年々減り続ける日本のごみ
温室効果ガスの削減が世界中で叫ばれるなか、企業や人々の意識は大きく変化しています。日本のごみ排出量は2000年代半ばからずっと減り続けてきました。環境省が公開している2019年度のデータによれば、かつて1kg超えも珍しくなかった一人1日あたりのごみ排出量は3桁台の918gまで減少しています。それに従い、旧式のごみ焼却施設も徐々に数を減らしていますが、一方で、発電機能を有する施設数は全体の35%まで増加しています。ごみ焼却施設における総発電電力量は9,553GW、およそ321万世帯分の年間電力使用量に相当するエネルギーを生み出しているといいます。「ごみの再資源化(リサイクル)」は、物質として回収するだけでなく、エネルギーとして回収する方法も各方面で積極的に模索・推進されているのです。
有史以来、人類はいつもごみの処理に頭を悩ませてきました。人が生きていく以上、ごみ問題は避けては通れないテーマであり、その解決はより良い未来につながるカギといえるでしょう。そして21世紀、ついに人々はイノベーションによって「ごみ=エネルギー」という思想にたどり着きました。「埋める」「移動する」といった廃棄物を自分の生活空間以外から追いやるというネガティブ思考ではなく、ごみをひとつのエネルギー資源として捉え直すプラス思考へ。この発想の転換を、川崎重工は高効率の「カワサキ・アドバンストストーカシステム」として具現しました。世界に誇れる日本の「ごみ発電」テクノロジーは、地球環境時代に新しい地平を切り拓いていきます。
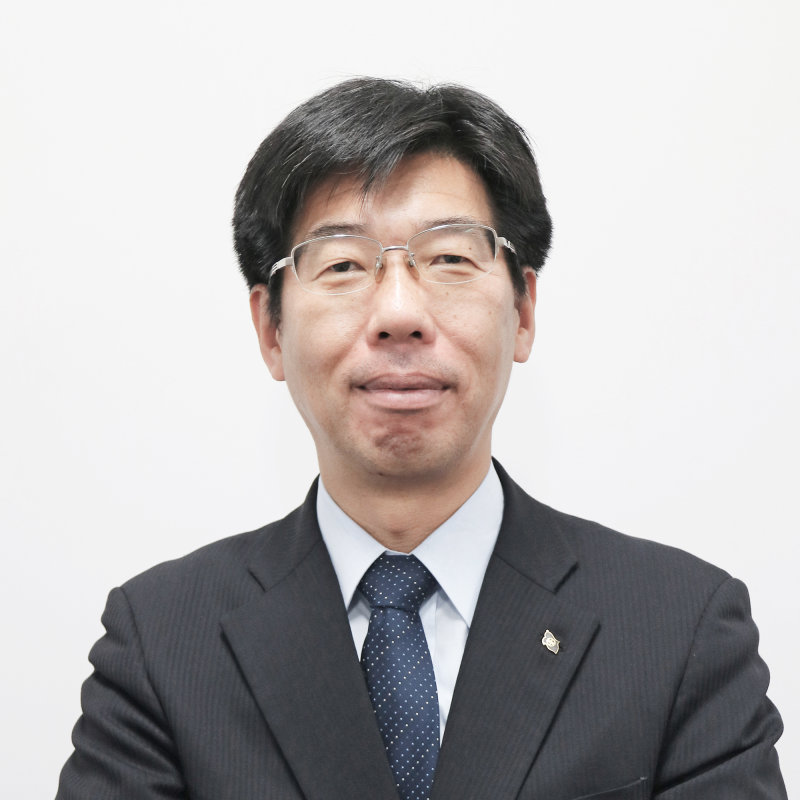
プラント・環境カンパニー
環境プラント総括部
総括部長
日本の先進技術を、グローバルアジェンダの解消につなげる。
日本では、高度成長期が始まった1960年代当初からごみ焼却施設が造られるようになり、設備はおよそ30年で更新されてきました。現在、年間4,000t規模の新炉発注がありますが、そのほとんどが90年代初頭に造られたごみ処理施設の更新です。環境問題を背景に取り組まれ始めた「ごみをエネルギー資源に」は、今や当たり前の取り組みとなり、新炉の建設では安定した燃焼と高い経済効率を両立させる技術提案が、地方自治体の財政負担の軽減にもつながっています。
川崎重工は、64年に第1号のごみ焼却プラントを納入して以来、現在国内で稼働している施設は78施設、建設実績は海外を含めて納入は178施設あります。80年代以降は、エネルギー拠点としてのごみ焼却施設のシステムのあり方を探求し、並行流焼却炉の開発や構造部品の長寿命化など独自の技術で高い評価をいただいてきました。特に大型炉や大型の発電設備を備える大規模施設分野では他社を圧倒する実績を誇っています。大規模施設だけに安全性や安定性、経済性などシステム全体の能力バランスが厳しく求められ、川崎重工は総合力で応えてきたのです。
ごみ処理は、まず埋め立て(ランドフィル)から始まり、国民1人当たりのGDPが5,000ドルを超えると焼却のごみ処理費用を出せるようになると言われ、ごみ焼却施設の建設が始まります。現在、この段階にあるのが中国やマレーシア、シンガポールなどです。その後にタイやインドネシアが控えています。
川崎重工は、中国企業と合弁企業を設立し、ストーカ式ごみ発電の施設をすでに10基受注しています。中国では、ごみをガス化し残った灰をセメント材料として活用するCKKシステムも普及させています。日本の優れたごみ焼却技術を世界に広めることで、世界の環境問題に積極的に貢献していく。この事業は、グローバルアジェンダの解消につながる極めて意義深いものだと考えています。
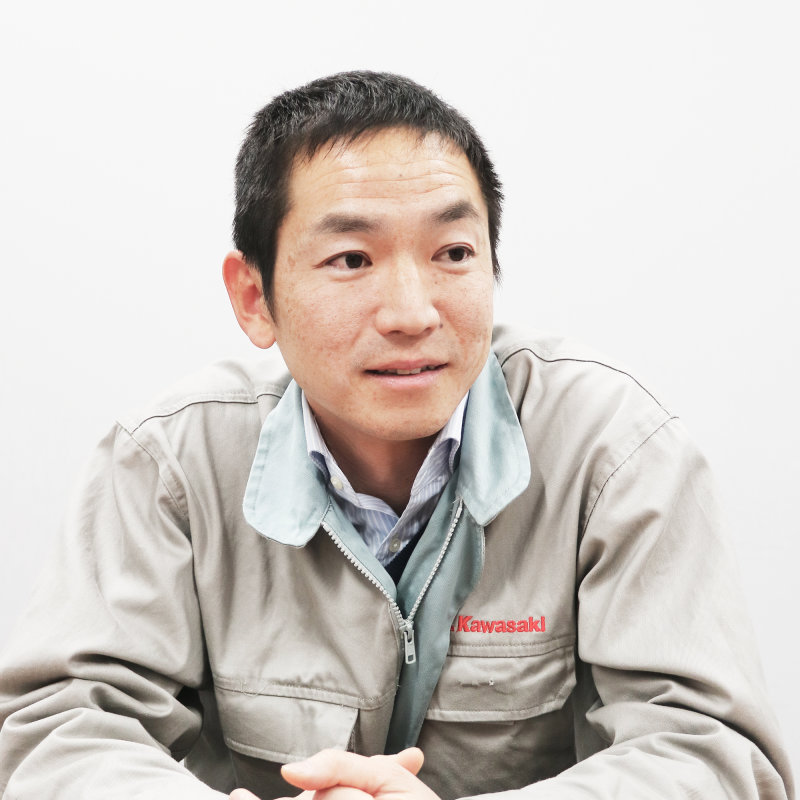
プラント・環境カンパニー
環境プラント総括部 環境プラント部
装置技術課
基幹職
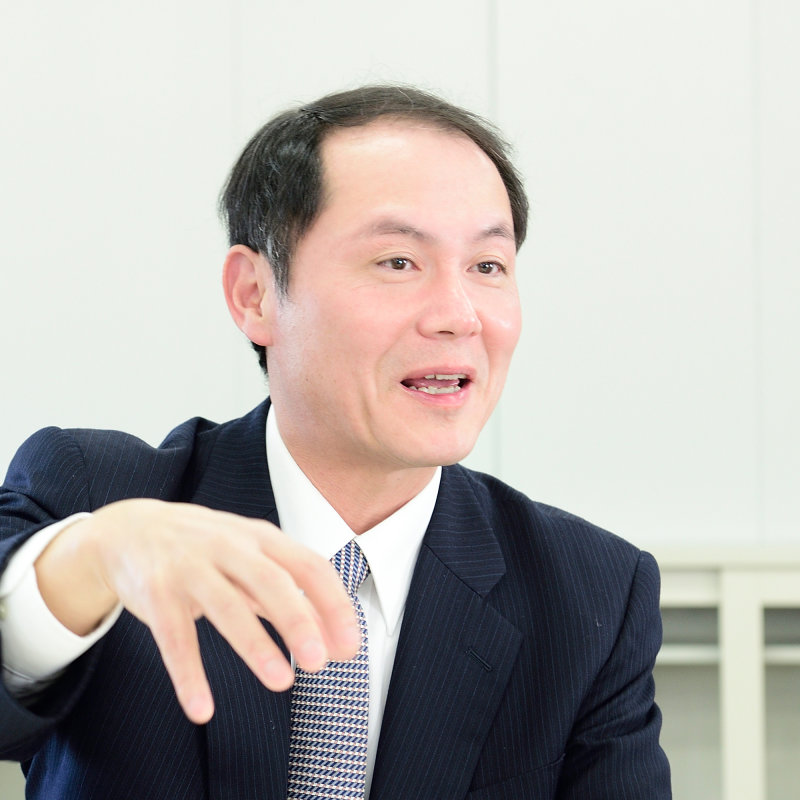
プラント・環境カンパニー
環境プラント営業部
西部営業課
担当課長
※文中に登場する数値・所属などは2017年5月の情報です。