CO2排出量が少なく、都市ガスなどとして利用拡大が進むLNG(液化天然ガス)。その安定供給の基盤となるのがLNG向け極低温タンクです。川崎重工は、設計・製造・施工技術の革新を進め、今また世界最大レベルのタンク建設プロジェクトに取り組んでいます。
世界最大級の地下式タンク保冷壁に投入される技術の粋
名古屋から電車で知多半島を下ること30分。伊勢湾に臨む浜に、都市ガス大手のガス事業者である東邦ガスの知多緑浜工場があります。すでに稼働している2基の地下式LNGタンクの隣に3号タンクが姿を現わしていました。東邦ガスが、都市ガスのさらなる安定供給をめざして建設を進めているタンクで、景観に配慮した地下式タンクなので地上に見えるのはドーム型の屋根だけです。
タンクは厚いコンクリートで造られた円筒形で、内径は約75m、深さは約50mもあります。容量は22万klで世界最大級。この大プロジェクトの屋根や保冷設備などの建設工事を川崎重工が担いました。
2015年6月1日。円筒の底から重さが約1,000トンもある鍋蓋のような屋根が静かに浮かび上がってきました。そのスピードは1分間に20cm。屋根は気密性を確保する精密加工のために円筒の底で製作され、微圧の空気を送り込むことで浮上させる「エアレイジング工法」で地上部に姿を見せたのです。クレーンの補助は一切ない、驚異的な光景です。
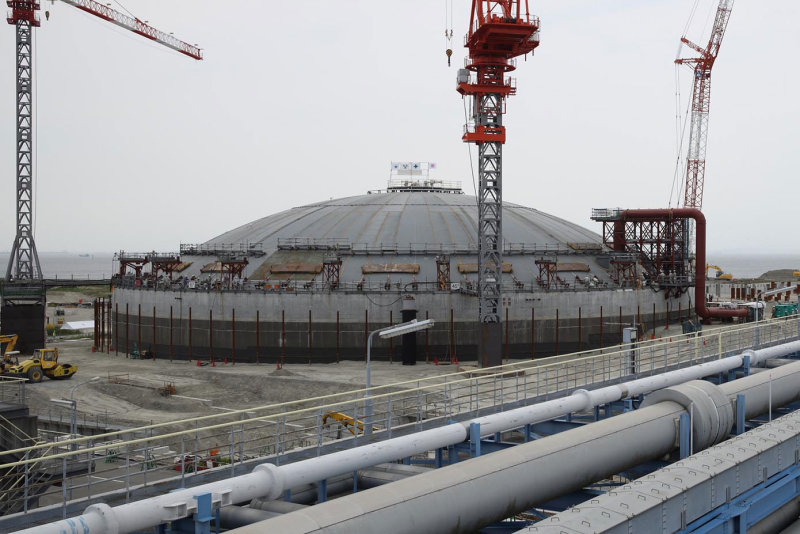
川崎重工のプロジェクトマネージャーであるプラント・環境カンパニー 化学・低温貯槽プラント総括部 低温貯槽プラント部 設計一課の恒川 昌宏 基幹職は、「屋根の重心計算を行い、それに基づいて重りを乗せて浮上させます。今回は屋根の重さの分布が複雑で重心が取りにくく、無事に終了してホッとしています。地上部に出ると楔のような部材で仮止めします」と説明します。
朝8時に始まった浮上作業は、午後1時半に終了。約1,000tの屋根を約50m浮上させる作業をたった5時間半でやりきりました。屋根が乗ったタンク内は、むき出しのコンクリートが圧倒するものの、わずかに差し込む光と照明で緑色の幻想的な雰囲気を醸し出しています。
「屋根に続き、いよいよ本丸工事です」と気を引き締めるのが川崎重工の現場施工の責任者である前田 剛志 東邦ガス知多緑浜工場No.3タンク建設工事所長です。液密と気密性を確保するために、底部と側面に保冷材と「メンブレン」と呼ばれる薄板ステンレスを貼り付ける工事が始まるのです。年が明ける頃には、コンクリートの筒は銀色の光沢を放つ空間へと変わります。このメンブレンの設計・製造、施工方法こそが、川崎重工が満を持して投入する技術でした。
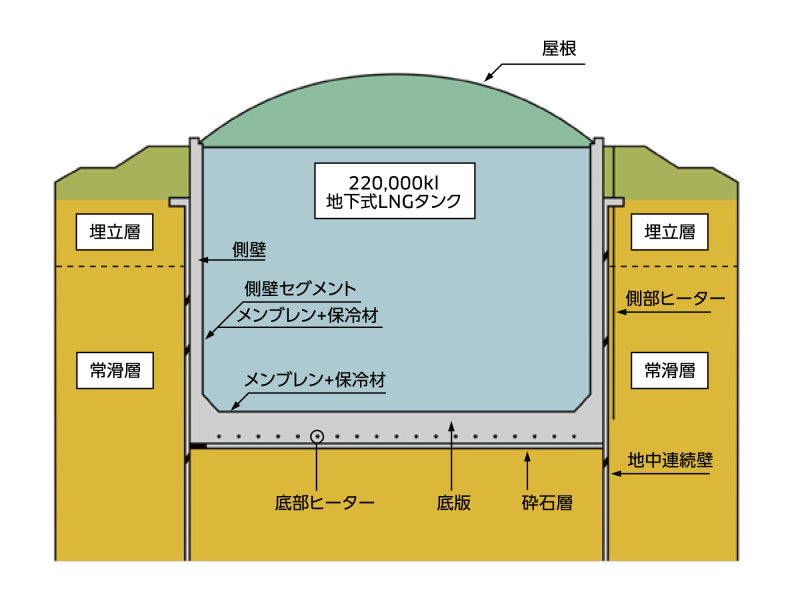
厚さわずか2mmのステンレス板メンブレン。保冷の秘密は波形の加工に
3号タンクの屋根が浮かび上がった頃、兵庫県播磨町の川崎重工播磨工場では、メンブレンのパネルづくりが最終段階を迎えていました。メンブレンは、厚さがわずか2mmのステンレス板。ステンレスは腐食せず、極低温の中でも強度を発揮できるという特長もあります。ただ、メンブレンを見ると不思議な形をしている。丸い凸が一筋や格子状に出ているのです。実は、この「波」のような形状や配置にこそ、LNG用低温タンクを手がけるメーカーの技術の粋があります。
LNGは-162℃で液化しています。タンクでは冷蔵設備などを使わず、そのまま貯蔵されています。保冷材によって温度を維持するのですが、「これだけ低温になるとステンレスは大きく縮み、1mで約3mm、底面の内径が75mあるとすると全体で20cmほど縮みます」(恒川基幹職)。そこで縮みを吸収してメンブレンの液を漏らさない機能を維持するのが波の部分なのです。
川崎重工のメンブレンは「旋回収縮型」と呼ばれるもので、ステンレス板が縮むと周囲の波が開き、波で囲まれた平板が回転を始めます。ステンレス板自体への負荷が少なく、疲労にも強いのです。LNG液の重みにも高い剛性があり、恒川基幹職は「川崎重工のメンブレンならば深さ90mクラスのタンクにも耐えられます」と胸を張ります。35年ほど前、川崎重工がLNGタンク事業に参入した際に、先輩技術者たちが民家の屋根の波板を見て着想したオリジナル技術です。
1枚のメンブレンに加工される波の配置は、例えばタンク内の液表面の上部と下部の温度差など配置場所別に精細に解析されて決まります。今回の東邦ガス知多緑浜工場3号タンクでは、112種類もの形状のメンブレンが用意されました。小さなものは68cm四方で、大きなものは1.7×3mもあります。その総数は7,900枚。波を造る金型は23種類もあります。
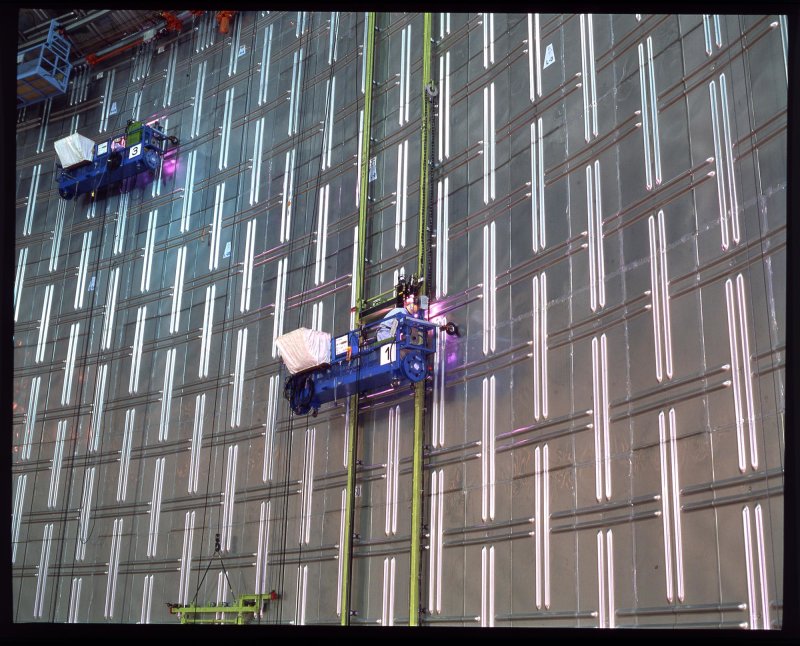
「金型が多いことで、ものづくりのハードルが高くなり、精密な加工技術が必要とされます」と語るのはメンブレンの製造を担う川崎重工 プラント・環境カンパニー 生産本部 生産技術部 生産技術第一課の川端 真治 主事です。
「金型が多くなれば、それだけ波山の形状・精度にバラツキが生じ、つなぎ合わせてパネルに する際にもすき間が出やすくなります。そのため、加工される1枚1枚のパネルに対して後工程のつなぎ合わせを考慮した要求品質を定め、厳しく管理しています」
工期短縮を実現したパネル化。傷の深さは35㎛以内の表面精度
メンブレンは、播磨工場内に新設されたラインで溶接され、大きなパネル(ブロック)になります。最初の肝は、溶接するために複数のメンブレンを仮止め(仮付)する際のすき間管理にあります。計測器を入れながら、すき間が0.3mm以内に収まるように仮付して溶接工程に送る。熟練者の技が発揮される部分です。
自動溶接ロボットは、今回のプロジェクトのために本社の技術開発本部や播磨工場の生産本部などと共同開発したものです。メンブレン同士の接着状況を確認して適切な溶接位置をレーザー光で決める工夫が施されています。
タンクは円筒形ではありますが、側壁と底部が接合する部分は垂直ではなく斜めになっています。タンクの強度を増すための手だてですが、それだけメンブレンの形状も複雑になります。タンクの側壁は、完全な円ではなく折れ角4.5度の80角形になっており、設計通りの精度を確保するにはロボットの高精度な溶接技術が必要でした。
溶接が終わった後もさらに、メンブレンには大きな関門が待っています。表面精度の確認です。もしメンブレンの表面に傷があると液の出し入れによる温度や圧力の変化などにより傷が拡大して漏れにつながります。そのため表面の傷の大きさは35㎛(マイクロメートル 0.035mm)以内と決められており、それ以上ならば傷の補修を行うことになります。
「品質保証部の協力を得て、カメラで傷の深さを測る新型の検査機器を導入しました。溶接の自動化、表面傷の計測方法と深さの数値化は、今回のプロジェクトで絶対に実現したい技術テーマでした」
そこまでメンブレンのパネル化にこだわったのは、施工期間の短縮と現場施工で安定した品質を確保するという新たな挑戦があったからです。前田所長は、「現場で発生する思わぬ不良など不確定要素を排除し、良いものを早く完成させる。そうすることで施主様は、より早く設備を稼働でき、より早く安定供給体制を構築できるのです」と説明します。
メンブレンパネルの製造工程
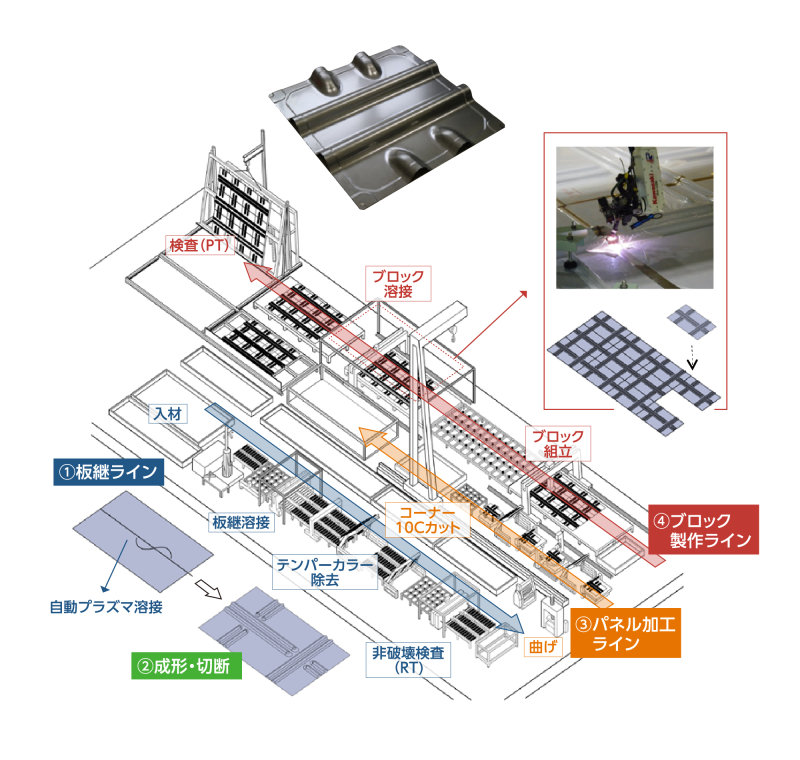
貼り付ける場所に応じて、厚さ2mmの形の異なるメンブレン(写真A)を複数枚つなげてパネル化します。仮付して(写真B)、自動溶接機で溶接(写真C)、仕上げの磨き(写真D)、 そして傷が無いかを独自に開発した検査機器で調べます(写真E)。
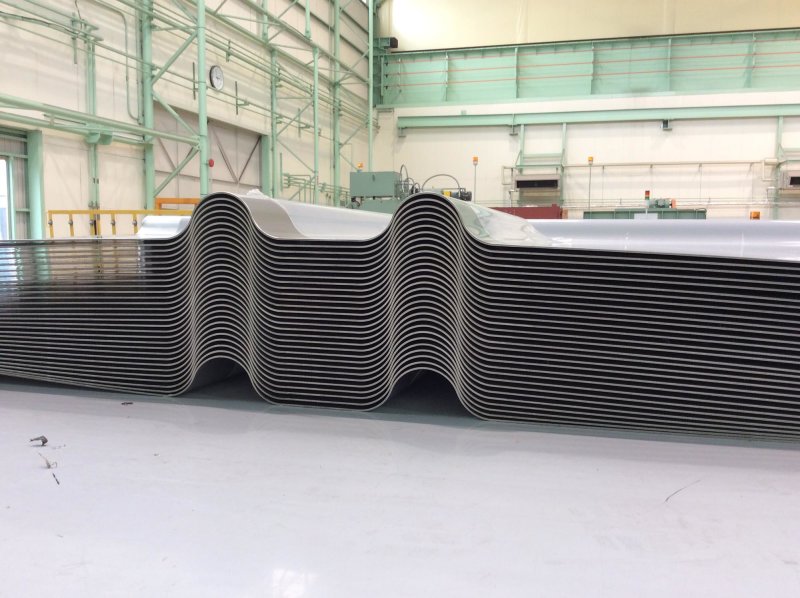

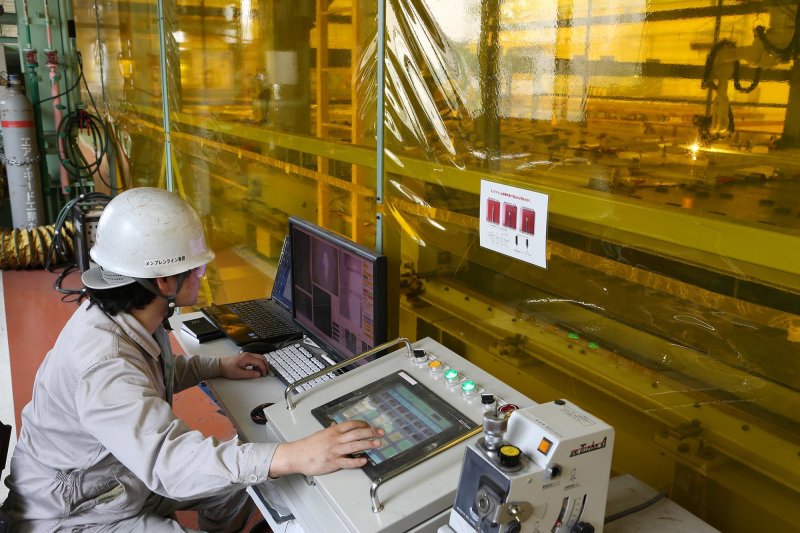
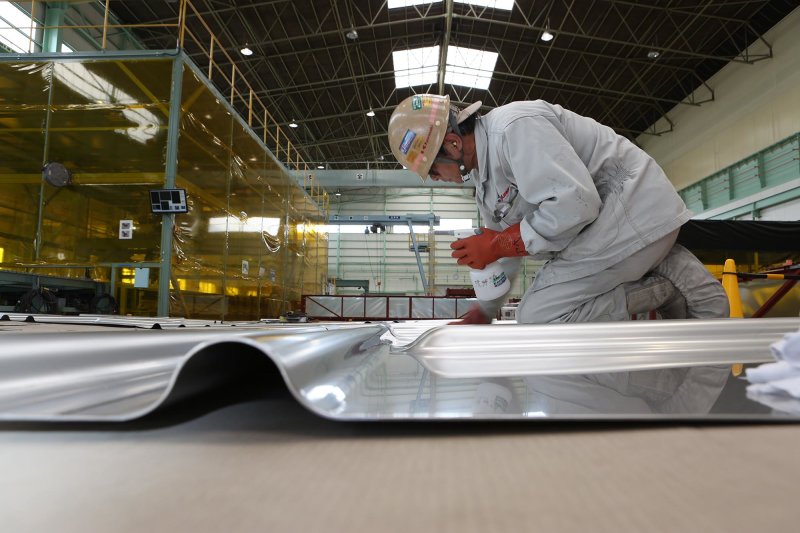
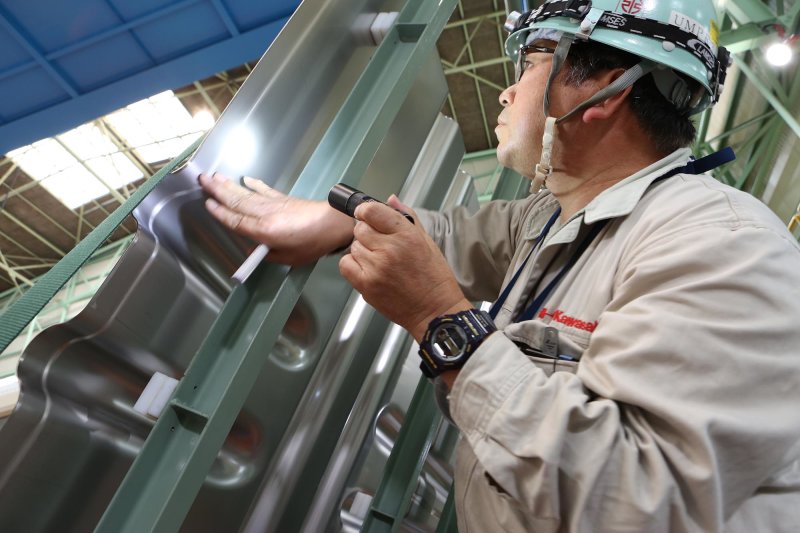
オール・Kawasakiで新型溶接機も開発
目を再び建設現場に転じれば、タンクの側壁には、新たに開発した自動溶接機を搭載した2人乗りのゴンドラが30台も吊り下げられ、播磨工場でパネルになったメンブレンが運び込まれて貼り付け作業が進みます。側壁が終わると底部に移り、2016年の年明けからは溶接部分の検査が始まります。「アンモニアリーク」と呼ばれる漏れがないかのチェック、表面精度のチェック等々。
最終場面では、ゴンドラに乗った作業員が、鏡を磨いているような風景が出現するはずです。そして、そこにあるのは、LNGタンクに求められる厳しい蒸発率基準を実現した姿。 タンクを満タンにした場合、蒸発して空になるのに3年もかかるという断熱性です。
前田所長は、「今回のプロジェクトは、設計から製造、施工、そして研究開発部門が本当に力を合わせて取り組んだものでした。私はこれまで5つのLNGタンク建設プロジェクトに関わってきましたが、今回ほどオール・Kawasakiの力が発揮されたプロジェクトはありません」と語ります。
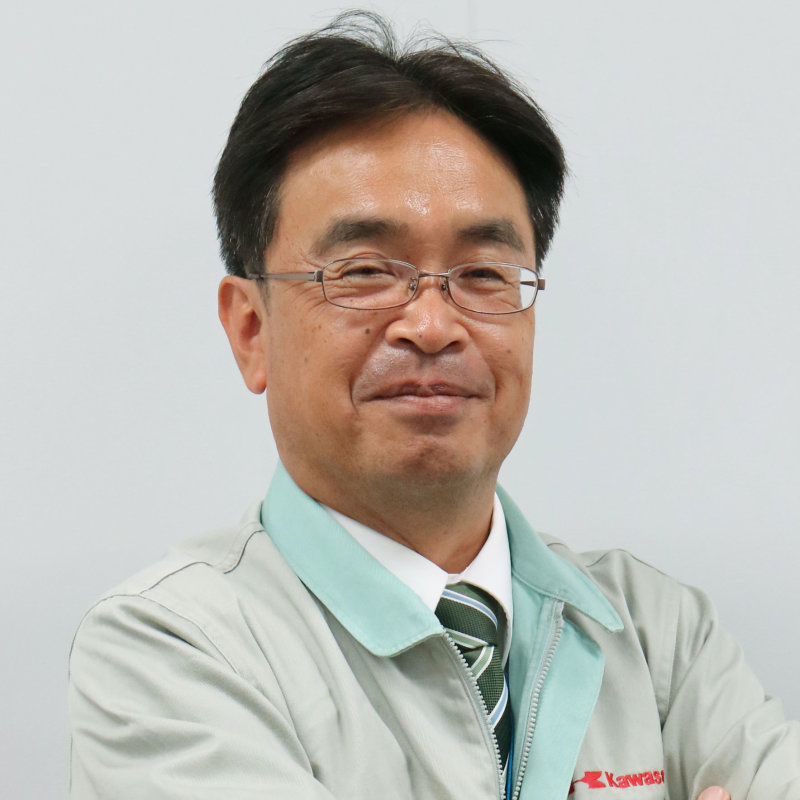
プラント・環境カンパニー
化学・低温貯槽プラント総括部
低温貯槽プラント部
部長
設計・製造・現場が「三位一体」で実現した技術革新
石炭や石油よりもCO2排出量の少ないLNGは、日本では1969年の初輸入より本格的に導入、利用されてきたエネルギーです。川崎重工は1980年代にLNGタンク事業に参入し、後発組でしたが着実に実績を重ね、これまで国内で地上式21基、地下式7基の製造・施工実績があります。近年LNG受入基地の新設・増設によるタンク建設が進み、川崎重工は先行メーカーに伍する受注を獲得しています。
東邦ガス知多緑浜工場3号タンク建設は、川崎重工のLNGタンク事業にも画期的なものになりました。技術の継承が進められただけでなく、設計・製造・現場施工の3部門が「三位一体」となって革新的な技術開発を実現できたからです。例えば、現場の施工問題を播磨 工場でも研究してパネルの大型化を実現して施工期間の短縮を図りました。精度の高い製造技術の実現は設計部門による新たな挑戦を可能にしていきます。
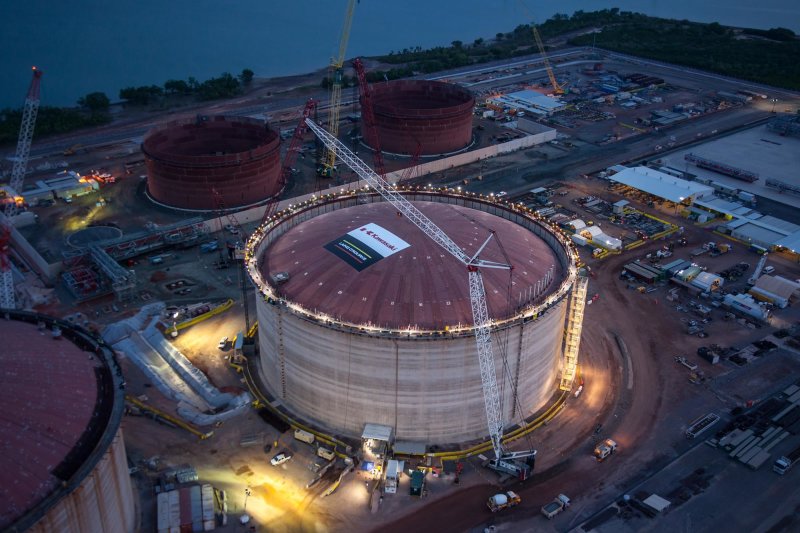
国内では、更なるタンク増設や老朽タンクのリプレイスなどが予想されます。また、海外ではアジアを中心にLNG利用が増えています。川崎重工はこれまで技術供与方式で韓国や中国、欧州、南米などで実績を積み、豪州、台湾においてタンク建設のEPC(設計・調達・建設)も遂行中です。これらの経験を踏まえ、「三位一体」での技術革新とプロジェクトマネジメント能力向上により海外展開を本格化させたいと考えています。また来るべき水素社会でも、種子島宇宙センター向けタンクの実績、本格始動した液化水素基地プロジェクトなどの経験を活かし、川崎重工の低温貯槽技術を世の中にお届けする決意です。
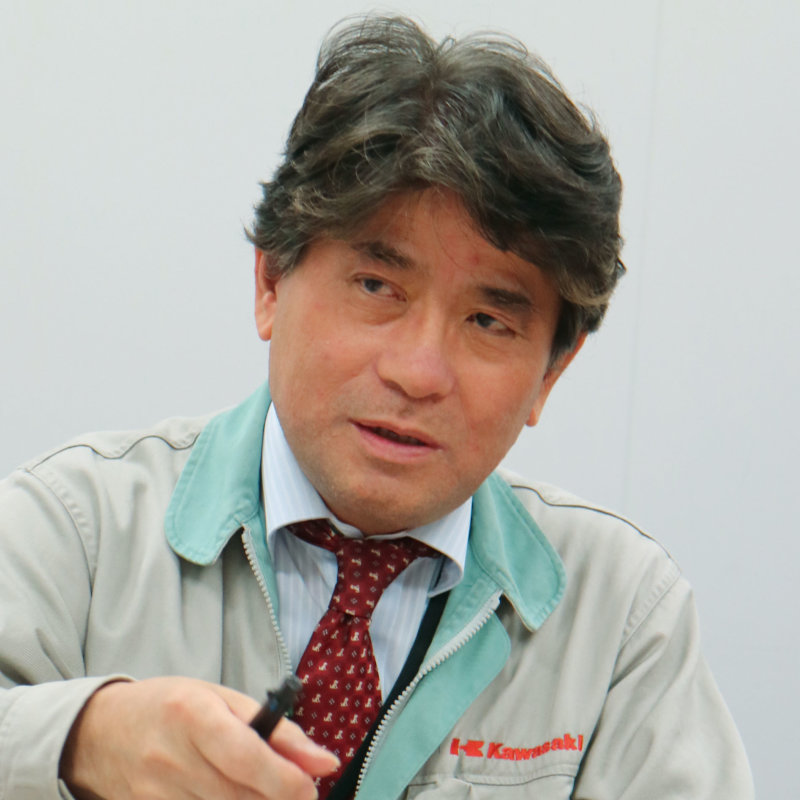
プラント・環境カンパニー
化学・低温貯槽プラント総括部
低温貯槽プラント部
設計一課
基幹職
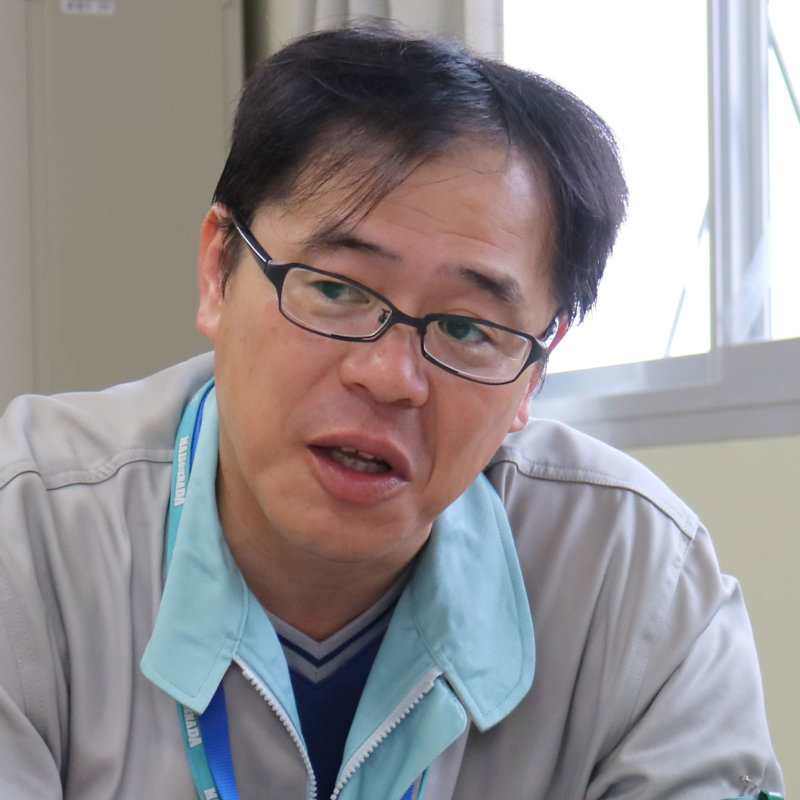
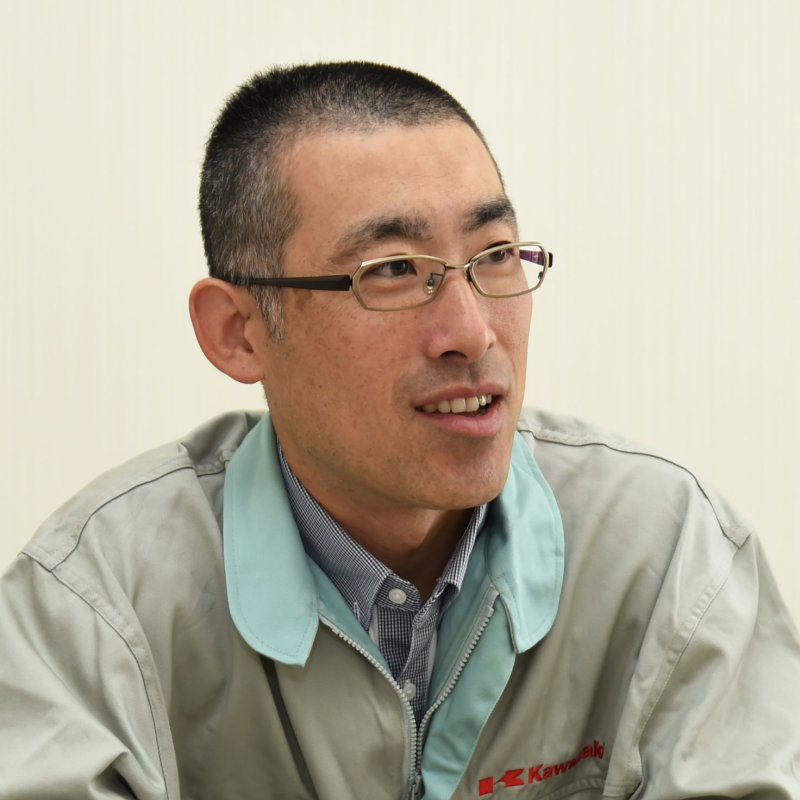
プラント・環境カンパニー
生産本部 生産技術部
生産技術第一課
主事