All Nippon Airways (ANA) and Kawasaki launched a line of upcycled products made from aircraft scrap, offcuts, and excess materials in July 2023. The products attracted particular attention because they were created by the very people who build the aircraft. These innovative aircraft goods could not have been completed without the skills of the experts who support the manufacturing process on a daily basis. What challenges did the craftspeople face in developing these products? We spoke to them to find out.
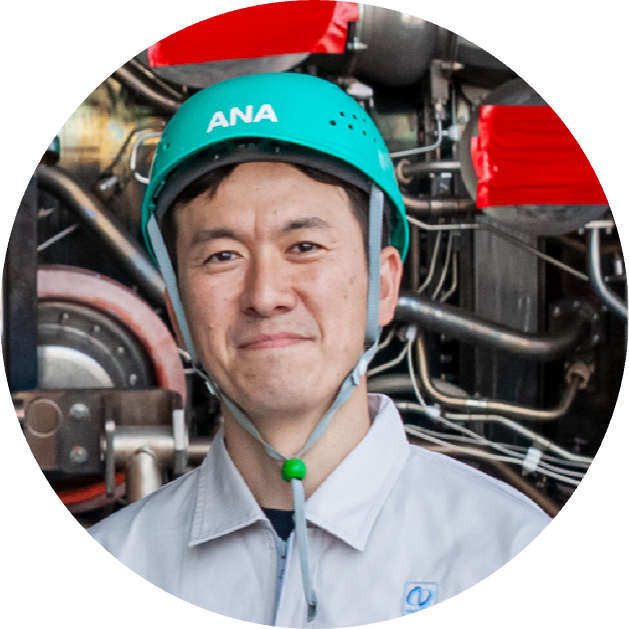
Test Piece Business Section, Test Piece Division,
Industrial Development Department,
Nabeya Manufacturing Co., Ltd.

Production Control Dept.
Tenryu Aero Component Co., Ltd,
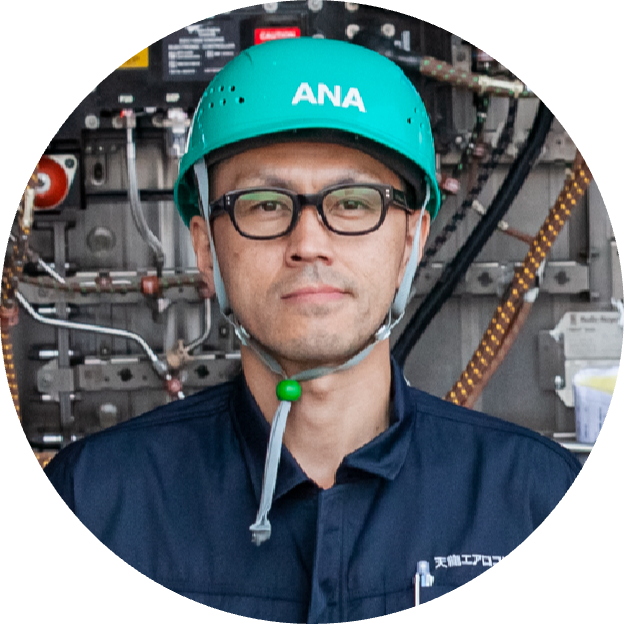
Parts manufacturing Section
Manufacturing Dept.
Tenryu Aero Component Co., Ltd,
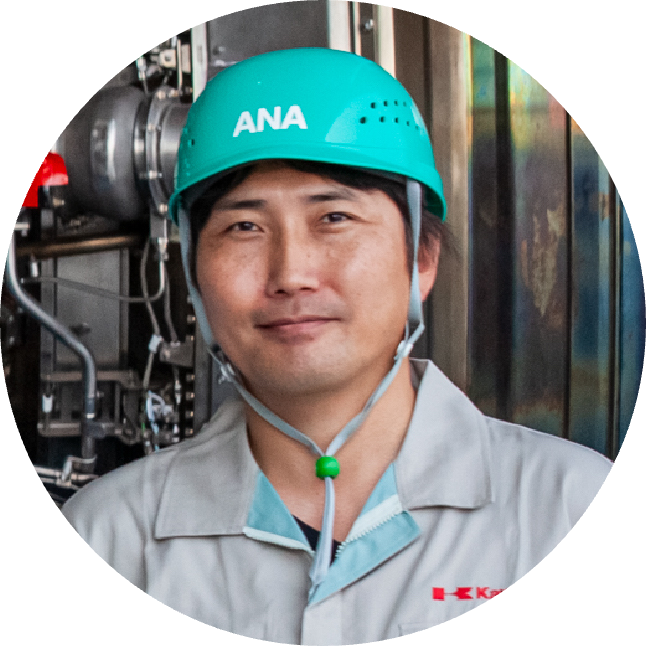
Outsourcing Management Department
Aerospace Procurement Division
Aerospace Systems Company
Kawasaki Heavy Industries, Ltd.
Koichiro Kawai
Made in the heart of the Japanese aerospace industry
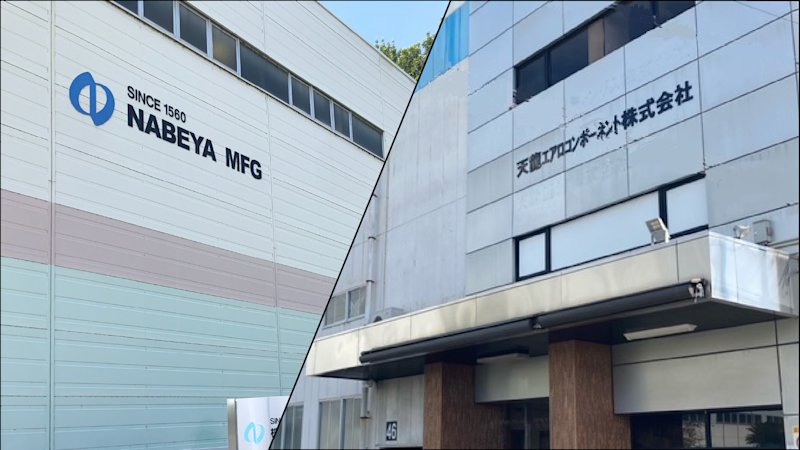
The manufacturing of upcycled products by the ANA-Kawasaki partnership was entrusted to two companies: Nabeya Manufacturing and Tenryu Aero Component. Both companies are located in Kakamigahara City in Gifu Prefecture, which is known as the heart of the Japanese aerospace industry. Both companies possess high expertise in aircraft manufacturing.
Nabeya Manufacturing engages in three main business areas: aerospace, which includes tool manufacturing, regular inspection and parts processing; 3D laser measurement and scanning; and industrial machinery, including cast metal processing. The company has expertise in the challenging fields of metal fabrication and precision measurement. Mr. Tsuchida of the company's Industrial Development Department commented as follows:
In our daily work, we cut test metal and resin specimens, which are used to evaluate the mechanical properties and strength of materials, components, and products. In that sense, cutting and fabricating various shapes and rare materials are some of our daily tasks.
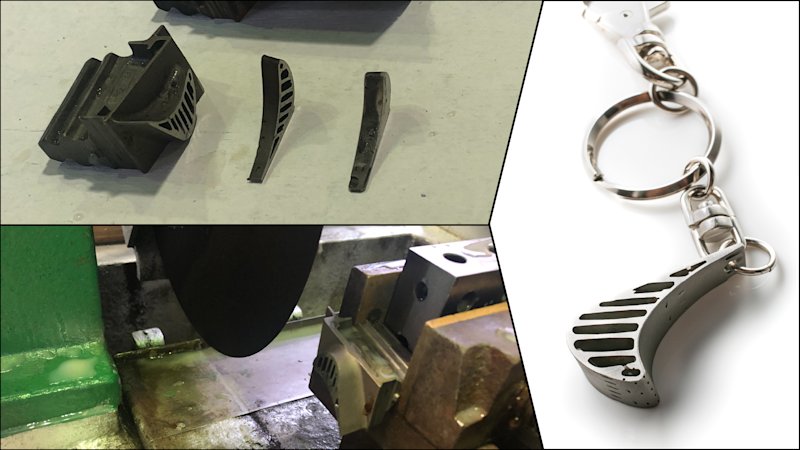
Bottom left: Cutting the HPT blade of the CFM56 engine
Right: Key chain
Nabeya Manufacturing was responsible for the manufacturing of a key chain made from the HPT blade of a CFM56 engine used in Boeing's B737-800 aircraft. The key chain weighs just 20 grams, but when you hold it in the palm of your hand, it has a satisfying weight and a unique mechanical beauty. Turbine blades are exposed to temperatures of over 1,000 degrees Celsius and spin at ultra-high speeds. They must be highly heat-resistant and strong. Because they are designed to withstand extreme loads, they are also difficult to machine. Nabeya Manufacturing's expertise in cutting was put to good use in the processing of this complex, three-dimensional material.
To cut a workpiece accurately, we need to understand its material and shape, secure it firmly so that it does not move, and select the optimal cutting method. Precision measurement and tool manufacturing are our strengths. First, we scanned the 3D shape of the blade, converted it into a 3D model using CAD (Computer Aided Design), and then derived the optimal cutting process.
Even though they were able to apply their expertise in high-precision measurement technology to find the optimal method, it was still not an easy process, he admitted.
We tried wire cutting (wire electrical discharge machining, a method of cutting a workpiece while melting it by passing an electric current through a wire such as brass), which we use when cutting super-hard materials. At first, the electricity would not flow as we hoped and we could not cut it. When we looked into it, we found that there was a coating around the workpiece. After peeling it off, we were able to cut it, but even if the outside was fine, the wire would stop at the hollow part inside. In the past 20 years or so that I have been involved in machining, I have rarely been unable to cut something, so I thought maybe this time I had really met my match.
Mr. Kawai, one of the leaders of the upcycling project team at Kawasaki, shared his thoughts.
When we received the blade from ANA, we did not know the material, nor how it was structured inside. Nabeya Manufacturing is a group of experts who can measure anything, from large facilities such as plants to small parts. We immediately consulted with Nabeya Manufacturing, knowing that if we had something challenging, they would be able to advise.
The two companies that participated in the project are partners that have worked together with Kawasaki on a daily basis. Kawasaki has built a deep relationship of trust with these companies, which is why Kawasaki turned to them in this new challenge of upcycling aircraft scrap and surplus materials.
Nabeya Manufacturing is involved in the machining and subassembly of parts, as well as the manufacture, modification, and repair of tools. We have been asking them to manufacture parts and tools for all types of civilian and defense aircraft. They are also strong in high-precision measurement, such as product measurement and regular inspection using 3D laser measurement. I think you can feel the spirit of Nabeya Manufacturing's machining technology and pursuit of precision from the products we have created.
Making products with a focus on how they will feel to maneuver
Tenryu Aero Component handled the fabrication of the card case, business card holder, and tablet stand for this project. A major feature is that they have an organization in place to carry out all processes in-house, from product and process design to material procurement, component fabrication, and assembly. They have accumulated know-how in a variety of specialized manufacturing, including welding, heat treatment, surface treatment, and adhesive bonding and forming of composite materials.
For this product, we used the same equipment to fabricate sheet metal as we do for manufacturing aircraft parts, and we implemented assembly using the same assembly technology as for aircraft. Thanks to Tenryu Aero Component's technical capabilities, the product conveys the manufacturing technology of aircraft from the aspects of both aircraft parts and the assembly process.
Ms. Arano of Tenryu Aero Components reflected on her impressions of the proposal for this project.
Our company is mainly responsible for the manufacturing of components that become part of the aircraft, which are usually not visible. I was very interested in this project, because it was intended to create products that users can see and touch for themselves. It was a new field for us, but I think we were able to make use of our high-quality manufacturing skills in aircraft manufacturing and the technical capabilities that we have fostered at our company. I hope that people will experience and appreciate these products, each of which were created with the same technology as real aircraft manufacturing.
For example, the rivet parts of the card case and business card holder employ high technology that has been honed in the field of aircraft manufacturing. The height of the rivet head and the surface of the base material are perfectly smooth, so there is no sense of protrusion. When you trace it with your finger, it feels like you are touching a single flat metal plate that is endless.
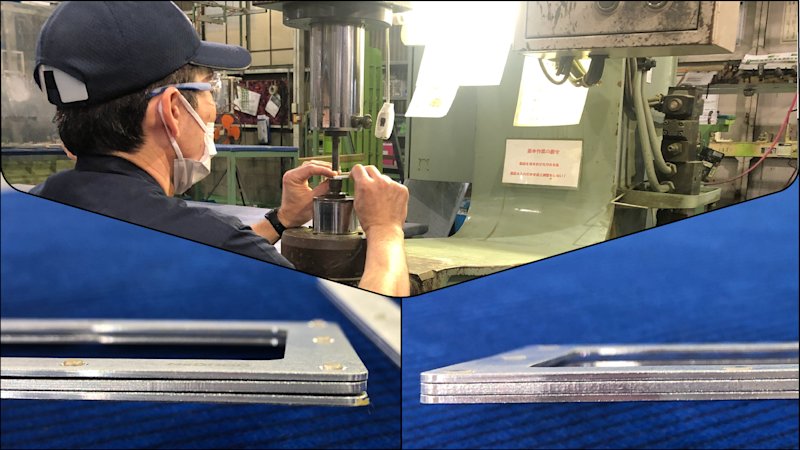
Left: Rivets before fitting
Right: Rivets fit snugly and smoothly
The business card holder's lid also demonstrates Tenryu Aero Component's attention to detail. The lid is movable and is designed to look like the landing gear control lever in the cockpit. The initial order was simply to make it openable, but Tenryu Aero Component proposed adding a touch of refinement to how it feels to open and close it.
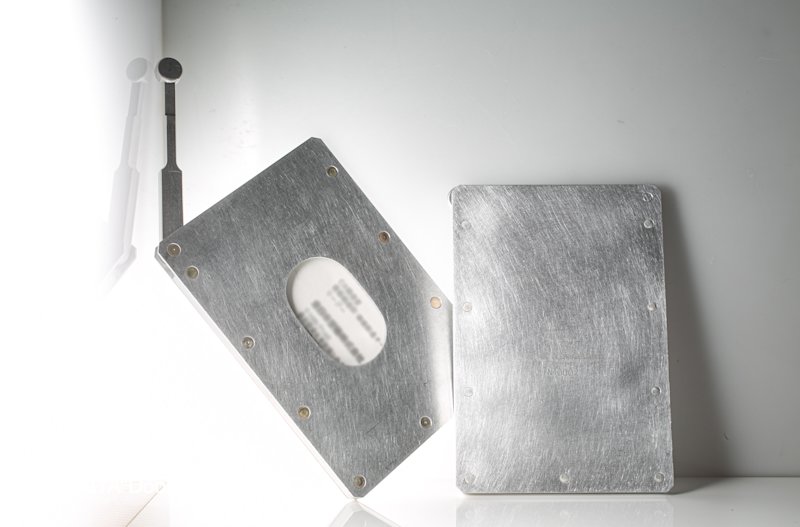
In fact, when you open and close the lid of the business card holder, it has a unique feeling of drag, almost like cutting warm butter with a knife. To achieve this feeling, careful improvements were made, such as inserting a washer at the joint. Mr. Shimizu of Tenryu Aero Component shared the highlights of this product, made with such care, from the craftsperson’s unique perspective.
The material used for this product is typically hidden by paint. However, in this product, we were able to capture a moment in the material's journey to becoming an aircraft. The product would never be good if it were rough cut, but neither would it be good if it were over-finished. I hope you can feel this kind of exquisite care we took during the manufacturing process. Also, the surface was originally shiny, but we deliberately ran it through a deburring machine and matted it, considering that users would invariably scratch it over time. This kind of machining results in different expressions for each piece.
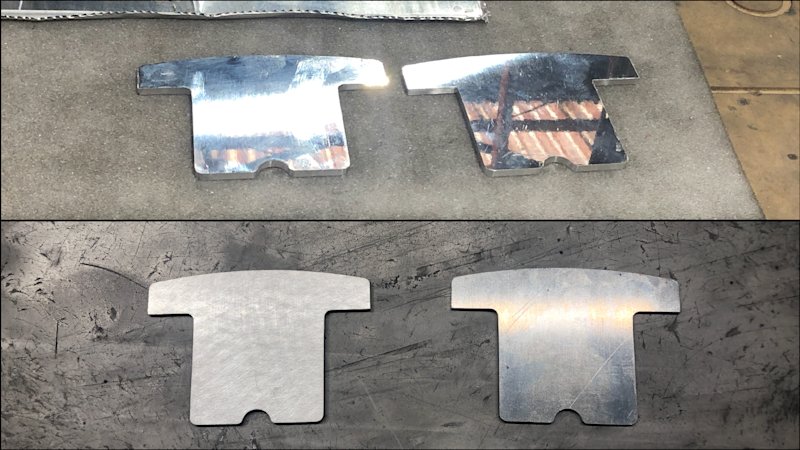
Left: After matting; Right: Back side of material
The collaboration between ANA and Kawasaki not only yielded unique products; it changed the perspectives of people involved with the project.
Through this project, we have developed a new perspective. It is a wonderful thing that materials that would normally be discarded can be reused in this way to create new products. We have also started to look for ideas for new products even for things that, up until now, have mostly gone unnoticed by asking ourselves, “What kind of product could we make this material into?”
I work in this industry because I love manufacturing. I am very proud that our technology was used in this product. In the past, we mainly focused on accurately processing products according to the drawings we received. However, this time, we were able to participate in the product development, too, which was a great experience. I believe that this project will also lead to an increase in employee motivation. In addition, by using scrap and surplus materials, we have added value to what would otherwise be discarded, which is also a contribution to our Sustainable Development Goals. I am proud to be a part of such a project.
Handing down the technology of aircraft manufacturing to the next generation
Today, aircraft is constantly carrying people around the world. Modern aircraft is the culmination of all kinds of manufacturing technologies and skills, such as precise and delicate metalworking techniques, advanced and cutting-edge scanning techniques, assembly, welding, painting, and inspection. It is here in Japan’s Chubu region that the three companies—Nabeya Manufacturing, Tenryu Aero Component, and Kawasaki—are in daily contact with these technologies. They have put their skills, which are the pride of Japan's aircraft industry, into upcycled products.
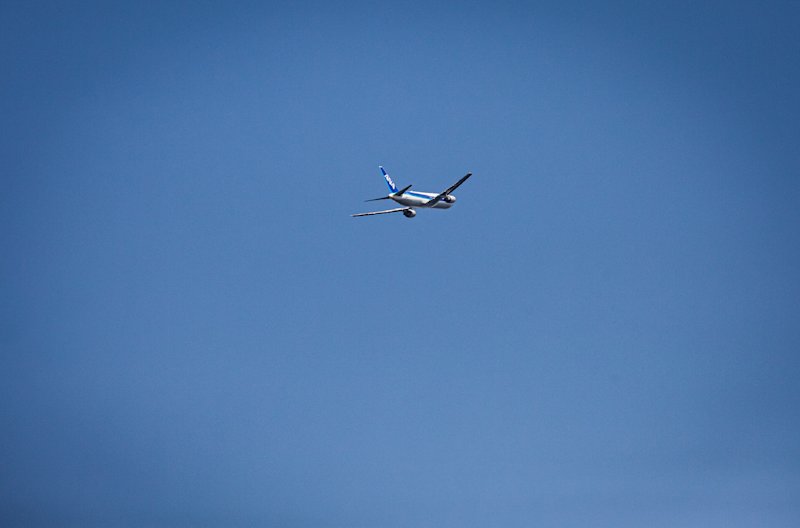
It is rare for the general public to be able to experience the technology of an aircraft directly, so as a craftsperson, I worked even more carefully and with all my heart, envisioning the person who will be using this object, and how they will receive what I was creating. In addition, I learned about technologies that I did not know in my interaction with Nabeya Manufacturing, so I would like to stay in touch with them. This time, we mainly dealt with aluminum alloys, but if we were to make another product, I would like to take on the challenge of using different materials, as well.
I would be happy if people from all walks of life would become more interested in aircraft by encountering a product born from aircraft manufacturing technology. Now that we have passed through the COVID-19 pandemic, it is time to strengthen employment and technology. We are working together as a team to see how efficiently we can make high-quality products in a short period of time. We will continue to explore how to hand down our high manufacturing technology to the next generation.
I think the unique appeal of this industry is the immense scale of an aircraft, which you can sense even in the manufacturing of tools. It is also a world of digital technologies such as the 3D measurement tools that we used with the engine blade key chain. In that sense, as well, I think people will find our work quite intriguing.
The making of aircraft involves complex issues such as how to create more efficiently, how to ensure the process flows better, and how to increase productivity in small-lot, high-variety manufacturing. We are working with Kawasaki and other partners to address and solve these complex issues. I believe we have an environment where people can enjoy manufacturing through their interactions with various people. When people experience firsthand the upcycled products we make with aircraft manufacturing technology and aviation materials (scrap and surplus materials), which they do not usually have the opportunity to touch, it will increase their interest in aircraft manufacturing, which, in turn, will help the aircraft industry to thrive.
The manufacture of huge aircraft involves many companies as partners, and each company has its own unique technology to be proud of. The upcycled products made in this project will allow people to feel a part of this technology and will play a role in bringing people and aircraft a little closer than before. We hope our products will help foster future engineers who dream of building airplanes. Propelled by this wish, our upcycling project has just started down the runway, and will soon soar into the sky.