”Upcycling” means reviving products that were going to be discarded for alternative use. Unlike recycling and reusing, “upcycling” revitalizes products with an emphasis on adding new value. All Nippon Airways (hereafter ANA) and Kawasaki initiated a unique project to take on this very task. The two companies worked as a team to create a variety of goods using aircraft manufacturing technologies. The intent behind this project was to create products that contribute to the environment while bringing excitement to aviation enthusiasts. The project also marked a restart following the COVID-19 pandemic, and contributed to regions and businesses impacted by it.
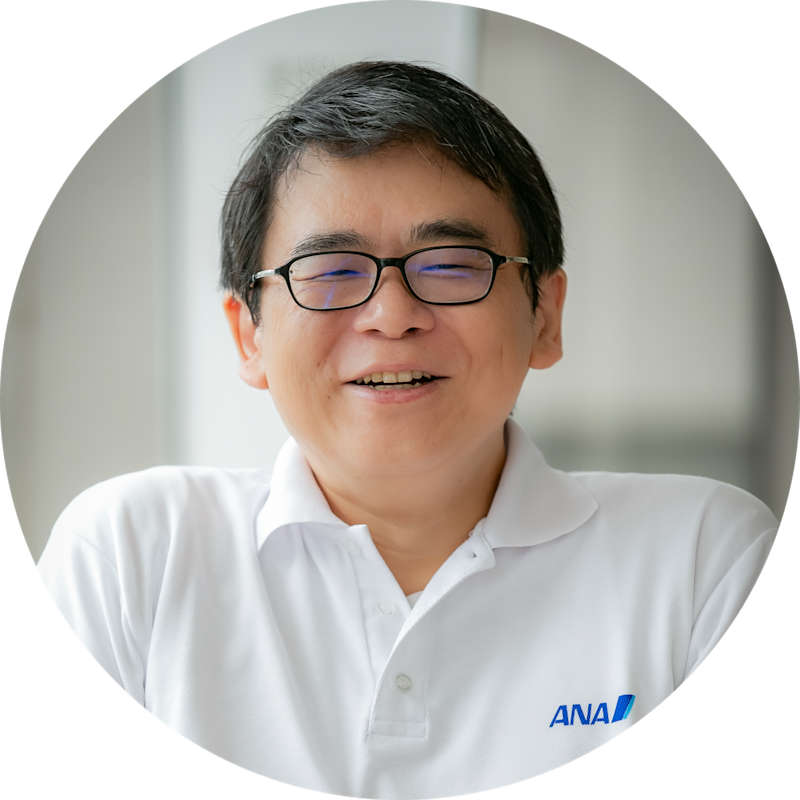
Engineering & Maintenance Center
All Nippon Airways Co., LTD.
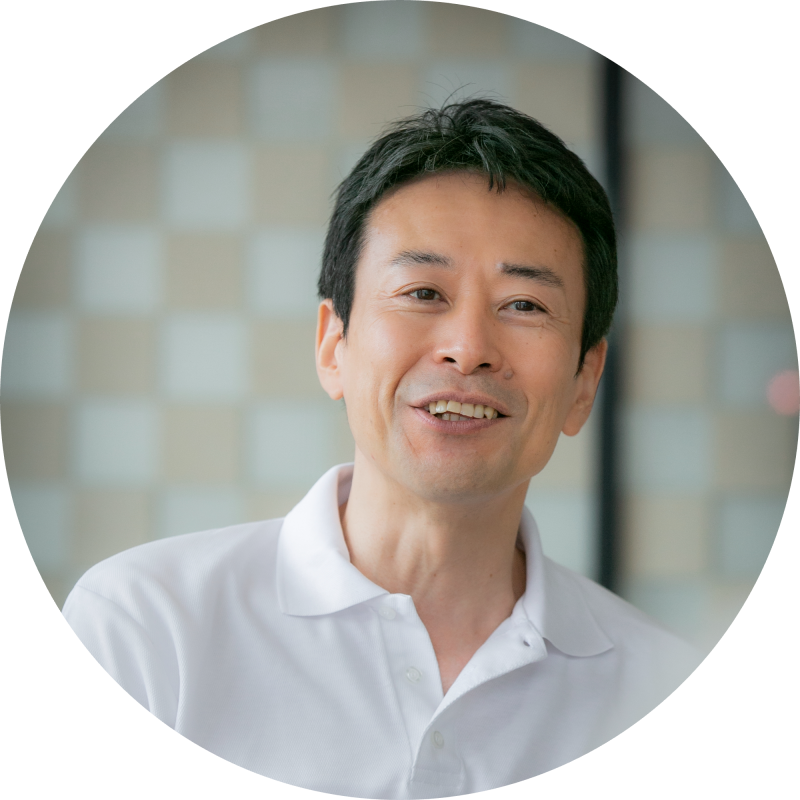
All Nippon Airways Co., LTD.
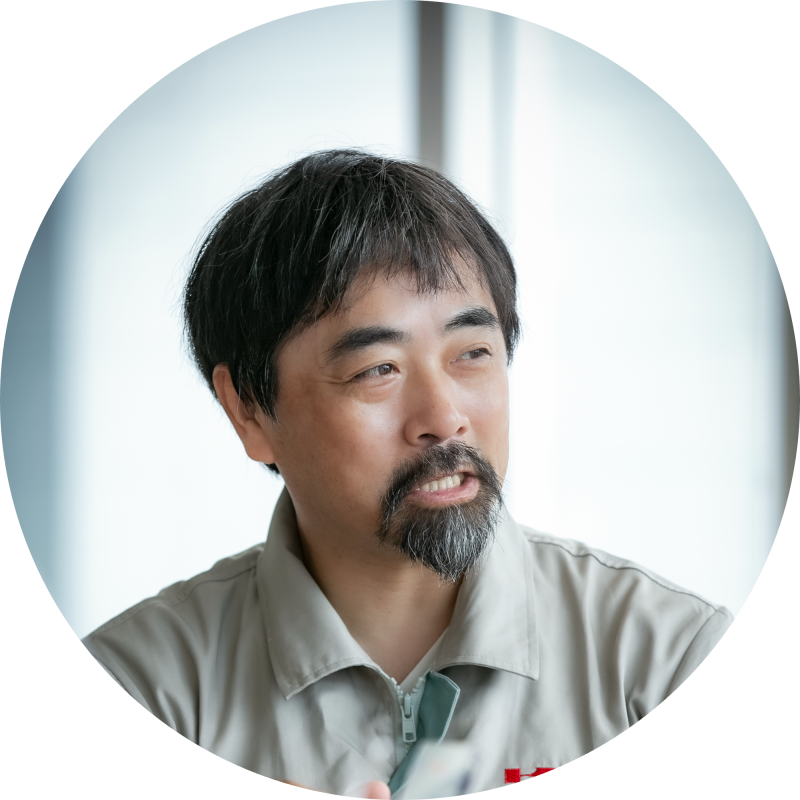
Fabrication Manufacturing Engineering Department
Manufacturing Group
Aerospace Manufacturing Division
Aerospace Systems Company,
Kawasaki Heavy Industries, Ltd.
What can we do to revitalize the aviation industry?
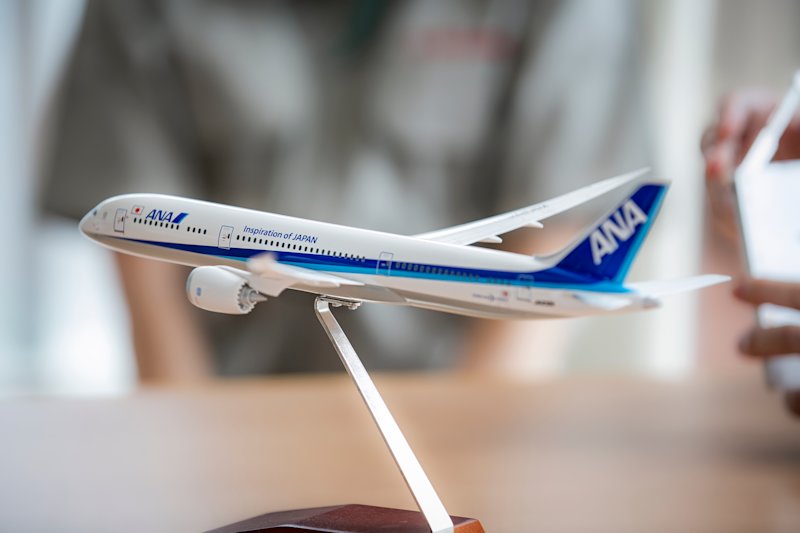
The COVID-19 pandemic, which took hold starting in 2020, had tremendous impact on the aviation industry. This upcycle project was born out of the growing momentum among the people working in the aviation industry in the midst of this unprecedented crisis.
ANA had previously created other upcycled products such as stamp books made from wood offcuts and slippers made from the seat covers used in aircraft cabins. Mr. Ikari of ANA, the proposer of these products, now wanted to create products that would further capture the hearts of aviation enthusiasts.
For example, he imagined that products made from parts dismounted from aircrafts as they underwent maintenance would catch their eye. However, this characteristic alone would not make the product unique. This is how he thought to collaborate with a manufacturer who actually creates aircraft parts in order to add unprecedented value.
There have already been upcycled products created from dismantled aircrafts that completed their service after 30 years. If we can use parts that are used in active aircrafts, such as the Boeing 737, 767, and 777, fans may recognize them. In addition, if such parts can be processed by engineers who are involved with aircrafts on a daily basis and have high machining accuracy, not only could product quality be enhanced, but we could also bring more excitement to aircraft enthusiasts, and this would help uplift the mood of the entire industry. This is the thought behind the project.
Incorporating aircraft technology for further impact
The project proposal created by Mr. Ikari highlighted the phrase “Support through buying.” Mr. Kojima of ANA, who led the project together with Mr. Ikari, recalls his reaction to reading the project proposal for the first time:
I initially wondered who would benefit from buying products made of leftover aircraft materials. However, I connected the dots soon after — his intention was to sell products made in a plant in Gifu so as to contribute to reactivating their regional economy.
What was essential to make this project a success was the technology to process aircraft materials to create upcycled products. For this reason, ANA had to collaborate with a company that has expertise in aircraft manufacturing – Kawasaki Heavy Industries.
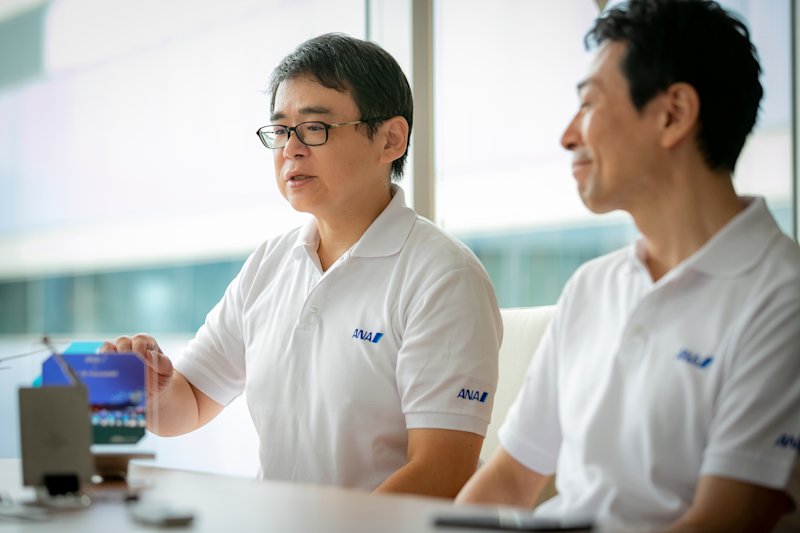
The Aerospace Department of Kawasaki co-manufactures for the Boeing 767, 777, and 787. And in Gifu Prefecture, where the department is located, there are many companies that manufacture aircraft parts along with Kawasaki. If we can gain cooperation from people working on the front line, it becomes possible to introduce their technological capabilities to the public. Our hope was to introduce technologies that the Japanese airline industry is proud of, to as many people as possible.
The driving force behind promoting this project was ANA’s hope of bringing attention to the airline industry, particularly to Gifu Prefecture which is a major hub for the Japanese aerospace and space field industries.
For the Aerospace Department of Kawasaki, which usually manufactures and delivers aircraft parts for manufacturers, creating products for general consumers was a completely new challenge. However, Mr. Fujihara of Kawasaki said that he felt excited rather than anxious when he was consulted on this unprecedented matter.
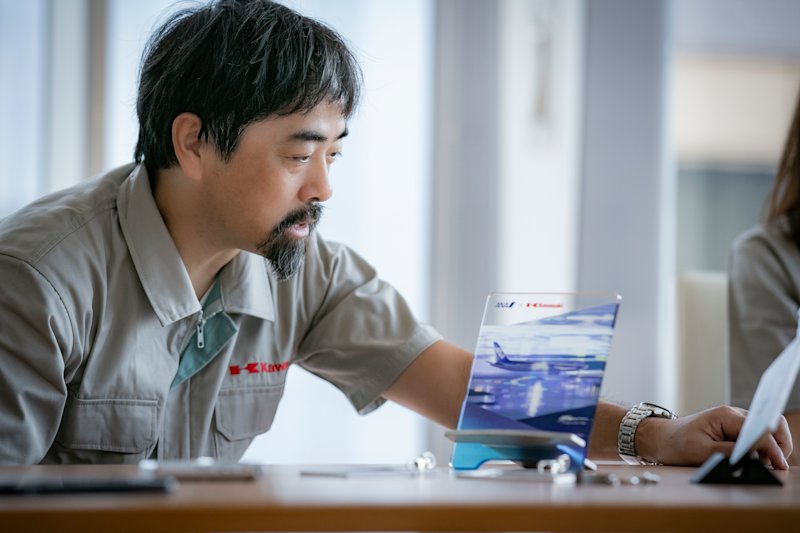
In our day-to-day work, our main role is to manufacture parts according to customers’ drawings. And so, it was a fresh, new challenge for us to conceptualize and realize a product from scratch for general customers.
The similarity between ANA and Kawasaki is that both use internal and external resources flexibly to create innovative objects of value, a process known as “open innovation.” This upcycle project started smoothly because both had similar approaches to the creation process. Mr. Kojima explains:
ANA outsources the manufacturing and repair of various aircraft parts to domestic and foreign companies. Among them, ANA contacts Kawasaki on a daily basis because we outsource the repair of some parts for dismantled engines, and often experience Kawasaki’s culture of creating new value firsthand. We thought there were many similarities to our aim of realizing a world filled with excitement.
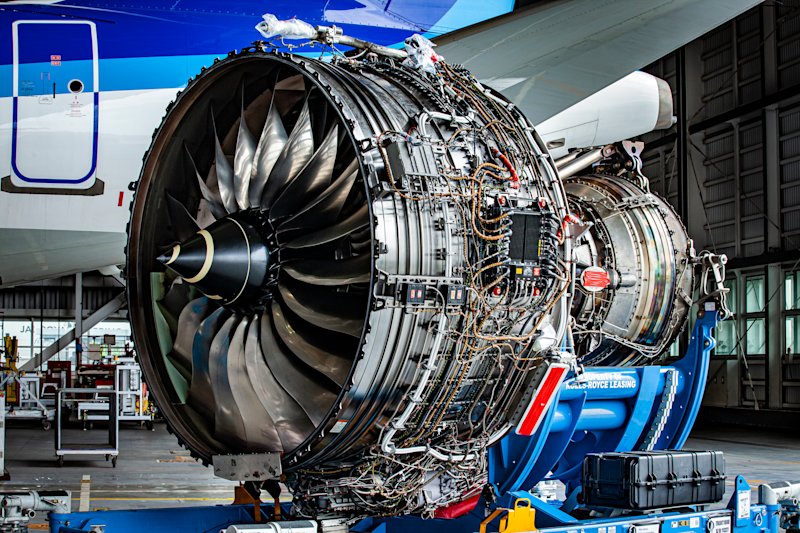
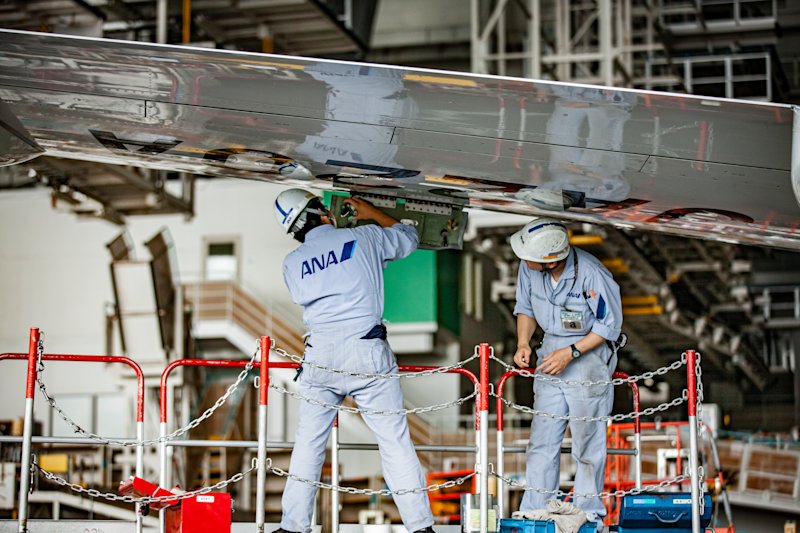
A new project was finally underway for aviation fans, for the airline industry recovering from COVID-19, as well as for local regions and many people involved in the industry.