The KPS of KMM is a hybrid manufacturing method, which integrates Japanese attention to detail and willingness to persevere with the necessary training, with American creativity and ingenuity, and forms the foundation for all KMM employees' way of thinking.
KPS is the “philosophy” that forms KMM culture
I entered KMM as a manufacturing engineer in 1984. At the Jet Ski manufacturing site, there is a large pressing machine that molds SMC (Sheet Molding Compound) a kind of fiberglass with intense pressure and heat. It is the largest pressing machine in Nebraska, and was actually built by KHI. I was the lead engineer on this project, I am quite proud of this.
KPS (Kawasaki Production System) was introduced into KMM in the early 80s. KPS, which is based on the idea of thoroughly eliminating waste, was the “trump card” to get us through a tough time in management. KMM acquired strong competitive power through the committed implementation of KPS and the employees felt deeply the significance of working on KPS. Now, KPS has become something that we can say is the “philosophy” that forms KMM culture.
With KPS, KMM is never satisfied with the present situation, always working on improving its manufacturing technique. Fellow employees’ open-minded character and flexibility support the implementation of new ideas for manufacturing techniques and methods.
KPS is created through Japan’s manufacturing management scheme and has been developed to a sophisticated level, and KMM’s KPS has evolved into an advanced hybrid manufacturing method, which integrates Japanese attention to detail and willingness to persevere with the necessary training, with American creativity and ingenuity.
Initially, KMM was established as a motorcycle manufacturing base, but that role ended in 2006 owing to changes in the business environment in the U.S.A. At present, it has four manufacturing divisions. They are namely, 1) the “consumer products division,” in which multi-utility four-wheel vehicles, etc. are manufactured; 2) the “rail car division,” in which subway cars and commuter rail cars for public transportation systems in metropolitan areas on the East Coast are manufactured; 3) the “aircraft division,” in which cargo doors for Boeing’s next flagship civil aircraft, the “777X” are manufactured; and 4) the “engine division” of the Maryville Plant, in which general purpose engines for lawnmower equipment manufacturers, etc. are manufactured.
Overcoming differences in the manufacturing methods and culture of these different businesses, and demonstrating a synergistic effect by improving the level of KPS as well: this is the greatest mission of KMM and us at the management level, and is shared deeply with employees. By enforcing the 5S’s (sorting, straightening or setting in order, shining, standardizing, and sustaining), we are going to bring another achievement realized by the synergy of the four different businesses to the simple yet deep world of KPS, which aims to “thoroughly eliminate waste.”
I find it very rewarding to work at a site where these kinds of challenges continue.
I feel great responsibility and at the same time a strong sense of pride for the fact that the community has high expectations for KMM.
With American technology, to American markets
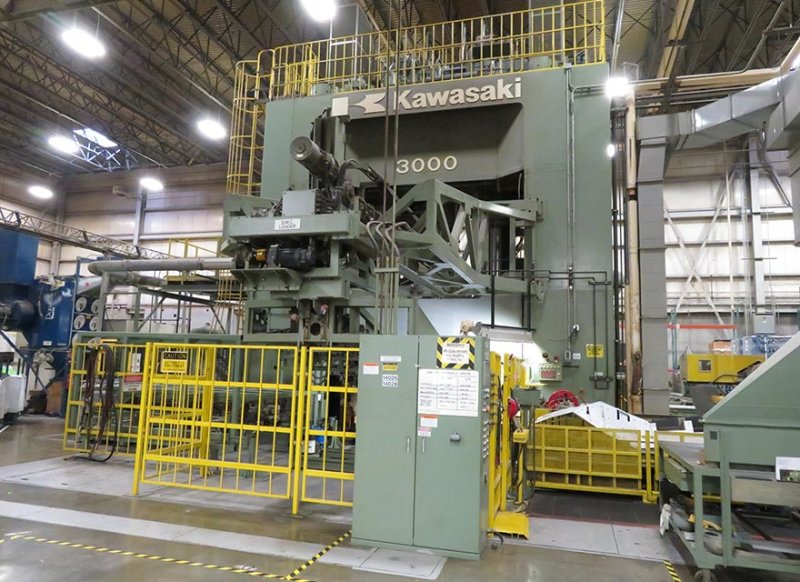
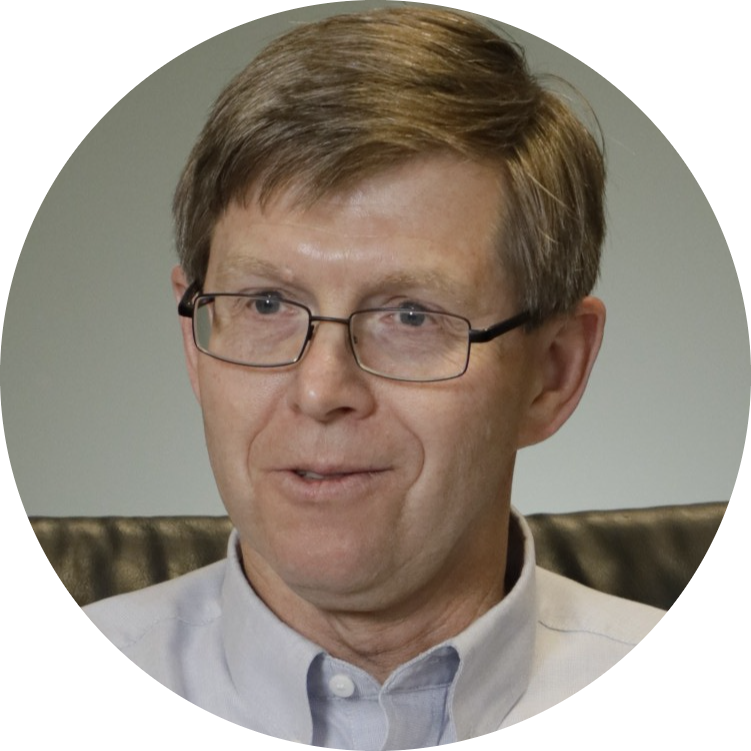
Kawasaki Motors Manufacturing Corp., U.S.A. (KMM)