We built a new material management system that embodies thorough elimination of waste—a central idea of the Kawasaki Production System (KPS). As a result, we not only streamlined production, but also succeeded in a great reduction of material storage space.
KPS, the foundation governing Kawasaki in building a quality product
I entered KMM as a welder in 1979. I’m currently overseeing day to day operations of the “consumer products division.”
Kawasaki products are highly competitive in the U.S., owning up to their reputation of high performance, reliability and durability; in other words, I believe our manufacturing philosophy (KPS) is the foundation governing us in building a quality product. KPS is a system, originally developed by Kawasaki Heavy Industries, based on Toyota Motors' Toyota Production System, and its central, inviolable rule is "thorough elimination of waste."
I am one of the employees who are called the “Kawasaki Production System (KPS) first generation” in KMM. We have learned the significance of implementing the KPS, and taken the initiative in spreading the philosophy throughout the company. The fruit of our efforts over many years is the establishment of the Warehouse Management System (WMS), which streamlines material storage management.
The system was put into full operation in 2015. The WMS creates a "First-In First-Out (FIFO)" flow of inventory control for procured materials. It supplies what you need as exactly many as you need, when you need. This has reduced the number of materials stored around the assembly lines, which means more space to work and improved safety.
We replaced the paper-based "kanban system" with "digital kanban," which manage the inventory of all materials as a system. Now, those digital kanban enable even more timely delivery of materials to the production lines. In addition, no matter what materials we put in storage, they are all kept track of in the system. It increases shelf efficiency and perfectly ensures FIFO.
When supplying materials to the production lines, the system takes the oldest stock, that arrived at the warehouse first, out from storage first. The computer shows the order to take out each material to be delivered, and, based on that order, the most efficient route to collect multiple materials. That series of operations is all completed automatically. Furthermore, the system now can monitor the materials kept next to the production lines and the number of materials in transport, in real time.
Previously, seven handling processes were required to get materials from storage to the production lines. The new system has cut the number of processes down to five through a mechanism that automatically determines the order to deliver materials, and through increasing shelf density by the adoption of free location management.
And what is better, the new system allowed us to change the storage method from "designated location" to "free location", and as the result, we could minimize the empty storage cells and reduce the total space by half.
In the days ahead, I hope to pass on the knowledge that we learned and the experiences that we gained to our future employees.
Diverse technical skills, galvanized to enhance product manufacturing
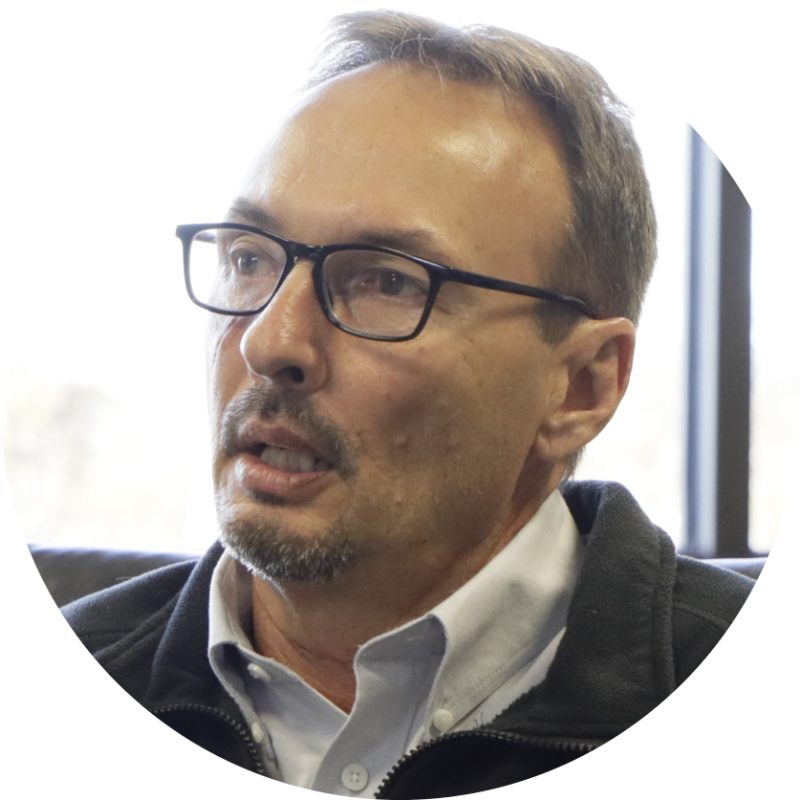
Kawasaki Motors Manufacturing Corp., U.S.A. (KMM)