The helical springs from NIPPI were behind the success of the many important missions of the Hayabusa and Hayabusa2. What made NIPPI, which began as an aircraft manufacturer of seaplanes and training planes for the Japanese Navy in 1934, come to have a presence in the aerospace field? The secret buried in the background is the fusion of analysis technology ensured by knowledge of aircraft design and high-level production in space development where everything is made to order and one of a kind.
Development of the First Rocket Engine-Powered Fighter Plane Made in Japan, Shusui
Many airplane fans will react with excitement to the names Shusui and Akatonbo. Shusui was the first domestic rocket-engine-powered interceptor (1945) while Akatonbo (Type 93 Intermediate Trainer) was the training aircrafts with almost 2,000 units produced from 1939 to 1945.
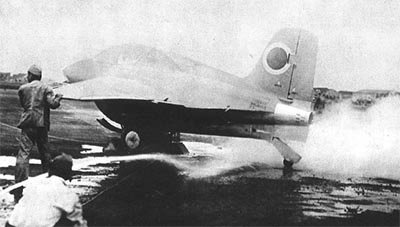
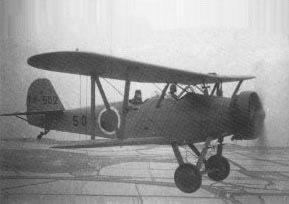
After World War II, Japan was banned from the aircraft business for seven years, but NIPPI managed to keep the company together through automobile repair and service. Afterwards, they made a mock-up of the YS-11 Japanese transport aircraft, and started to produce pylons (pillar-like adapters to equip with missiles under the wings) for the F-15 fighters of the Japan Air Self-Defense Force. In the field of civil aviation, the company manufacturers parts for the Boeing 777 and the Airbus A380 as a group company of Kawasaki, and its high level of carbon fiber-reinforced plastics (CFRP) molding technology is well established. The name NIPPI was originally the nickname of the Japanese corporation Nippon Hikoki, which literally means Japan Aircraft, and the designation NIPPI is familiar in Japan.
NIPPI entered the space business in 1963 when the Institute of Industrial Science, the University of Tokyo, was developing the L (Lambda) series of rockets with NIPPI in charge of the production of the tail section thanks to its high reputation for analysis and production technologies for sheet aluminum structures cultivated in aircraft manufacturing.
While the company was still producing rocket fins and fuselages, a big change occurred in the early 1970s. The engineers frequently went to the University of Tokyo for development meetings, and a researcher asked if NIPPI could make a deployable system called a coilable mast.
The coilable mast extension mechanism can be folded into a compact unit, and once the latch is released, the components automatically extend smoothly. The coilable mast, about which the researcher approached NIPPI, was planned for use on the Akebono, a magnetosphere observation satellite, subsequently making high-level Japanese space technology famous around the world from both the aspects of science (observation) and engineering (satellite development).

Coilable Masts for Elucidation of the Aurora
The magnetosphere observation satellite, Akebono, was a scientific satellite sent into orbit in February 1989 for the main task of clarifying the acceleration mechanism of high-energy electrons in the aurora luminous event. Akebono was equipped with four wire antennas and two magnetometers in order to measure plasma, magnetic and electric fields, and waves in the aurora.
If the magnetic sensors, in particular, were mounted close to the body, then they were affected by the magnetism of the satellite, lowering observational accuracy. Therefore, a plan was studied to attach the sensors on the tip of 5 m and 3 m masts. Those two were the coilable mast extension mechanism that NIPPI was asked to develop. The satellite had four wire antennas 30 m long and two coilable masts 3 m and 5 m long, and it was called the Oiran Kanzashi from the appearance (Oiran were high-class courtesans and used several kanzashi hairpins to look beautiful).
The extension mechanism of the coilable mast consists of a hinge-less structure that allows the folded material to stretch out by an intrinsic force. NIPPI determined the material and developed the folding method in time for the launch in 1989.
Akebono had been operated for a very long time of 26 years until April of 2015, which exceeded the initial assumption, but resulted in the accomplishment of an important discovery and observation, including the finding that the Earth’s magnetosphere controls the aurora phenomena, and the acquisition of demonstrative data of long-term periodic changes in the Van Allen radiation belts captured by the magnet field of the Earth. The coilable masts, which remained exposed to cosmic radiation, also served for long-life studies.
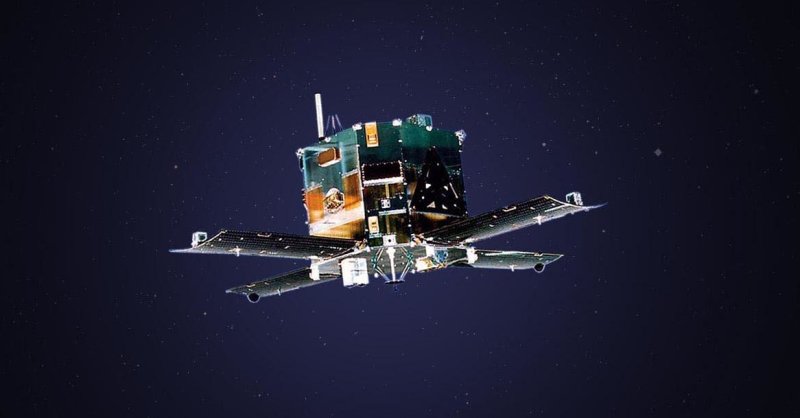
What Technology Enabled Observation with a Radio Telescope?
The capability of NIPPI to create aerospace structures was proven by the coilable masts of Akebono, and the renown finally became substantial when the radio astronomy imaging satellite, HALCA was developed.
Launched in February 1997, the HALCA mission was to establish the technology for Very Long Baseline Interferometry (VLBI), where multiple radio telescopes on Earth and the radio astronomy satellite observed objects collaboratively. For that purpose, HALCA deployed a parabolic antenna with an effective diameter of 8 m in space. The antenna mirror plane consisted of metal mesh and cables and was spread by six extension masts. NIPPI undertook development and production of the extension system.
The deployment and operation of the parabolic antenna were determinant points of HALCA’s mission success. On the antenna mirror plane, triangular cable networks with a side length of about 20 cm supported the reflecting surface of the metal mesh, and the total number of cables was about 6,000. All of them were of the ideal length and had to extend and contract at the same time. Otherwise, each joint would not form the theoretical mirror plane.
In addition, misalignment could be caused by variations in production, alterations in tensile force, and expansion and contraction from temperature changes. To prevent any variations, the cable lengths on the reverse side were adjusted to increase the accuracy of the mirror plane. A stronger spreading force was not always better for ideal opening, and a very complicated trial and error process, in other words, analysis, continued for solutions, including for the method of deployment.
In the early development stage, everyone thought it would not unfurl, which created a hopeless mood. However, the researchers and NIPPI staff added the idea of an autonomic retraction mechanism built for the HALCA and other satellite projects to the extension masts and thus took advantage of the accumulated analytical skills to achieve 100% deployment.
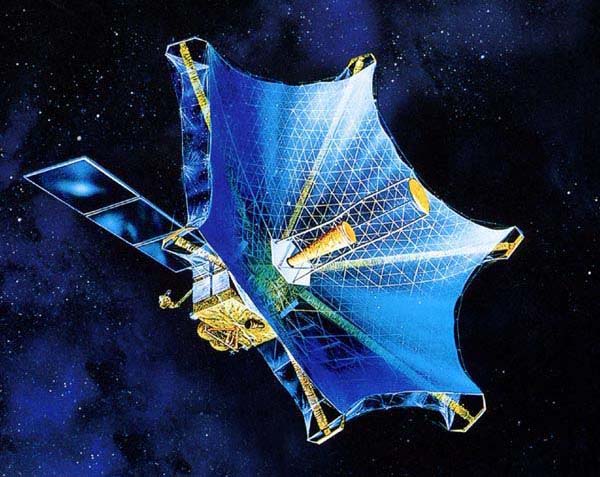
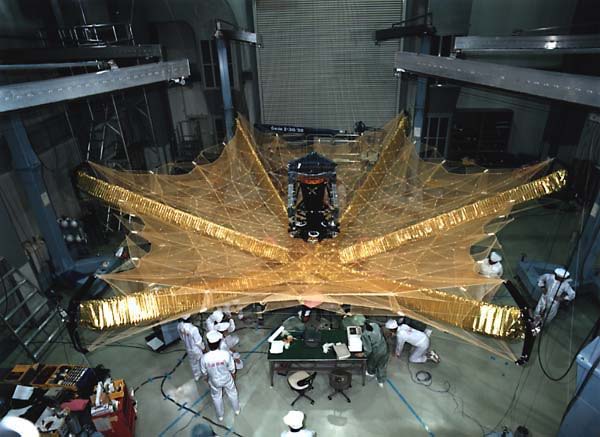
Company Culture of Trying Any Idea!
Each spacecraft is launched in a compact form, spreads solar panels upon reaching orbit in outer space, puts out observation instruments, and starts working. The extension mechanism is an essential tool for satellites, and no matter how advanced the observation equipment, the missions can never be accomplished without the stability and reliability of the mechanical components to set outside and support them.
Subsequent to Akebono, all satellites had extension mechanisms and lifted off in Japan carrying devices made by NIPPI. Such confidence in NIPPI is symbolically seen by adoption of the helical springs to the sampler horn, the SCI, and the reentry capsule release device on Hayabusa2.
Kazuhiro Abe, who helped design the Hayabusa2 components on the Space Structure Design Team, says,
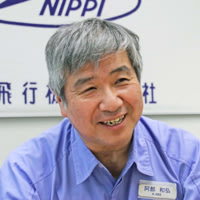
When you have an idea, you should do it anyway. The designers’ team and the production site workers assist in the detailed materialization of a space quality product. Such an atmosphere at NIPPI leads to the creation of profound, unique products that others cannot realize.
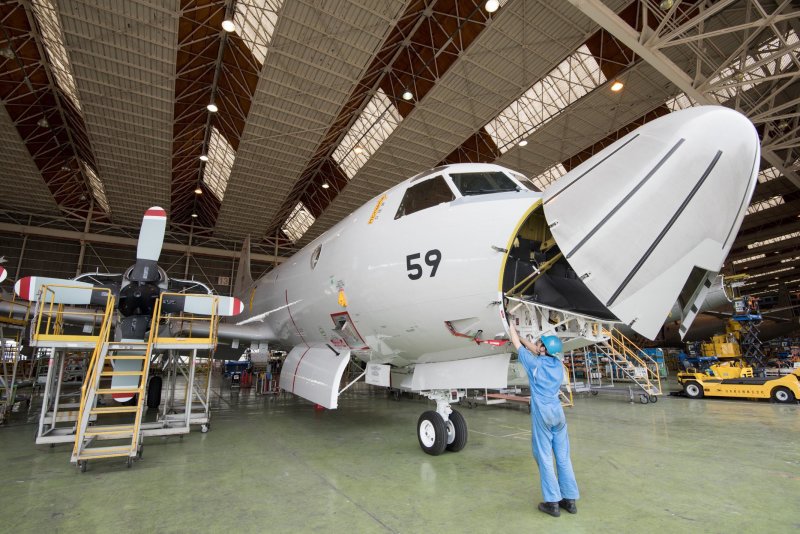
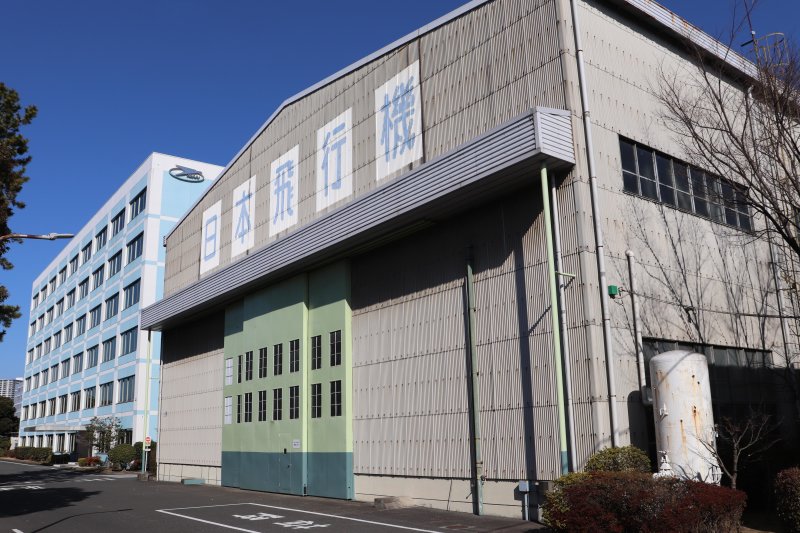
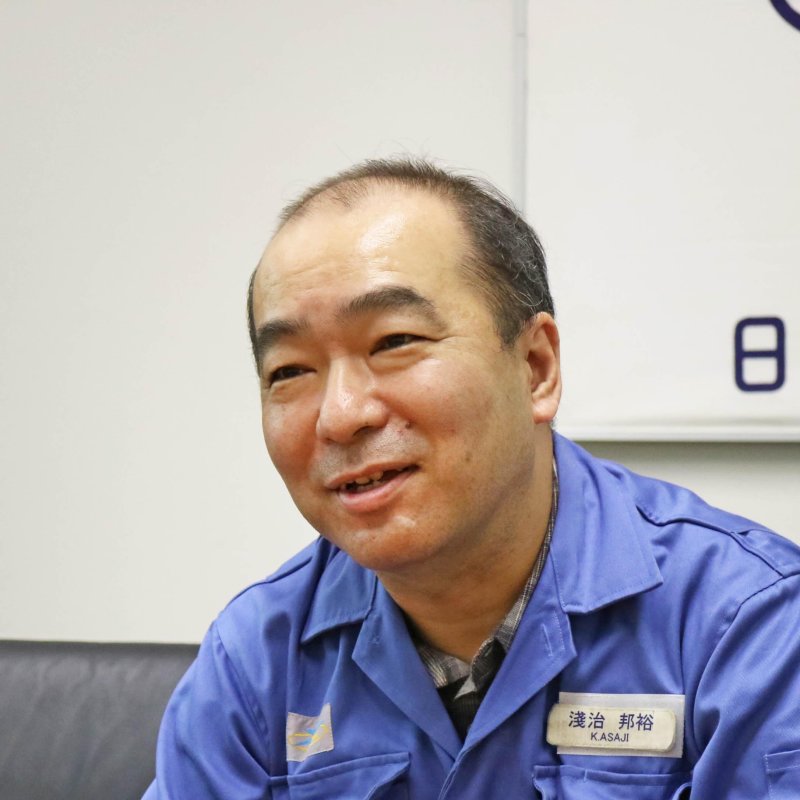
System Design Section
Engineering Department
Engineering / QA Division
NIPPI
Real Ability to Develop Testing Equipment In-house to Meet Demanding Requirements
Since the success of the Hayabusa and Hayabusa2 tends to spotlight helical springs and related items from NIPPI in the aerospace field, the company may be seen as a spring part manufacturer. However, as you can see from the example of the extension masts described above, springs are just some of the products from the company.
In the development of reliable, stable aerospace components, everything is custom-made, and the manner can be called the all-bespoke principle. The skills to develop and produce components are backed by NIPPI’s superior technical capabilities in analysis fostered from aircraft development and manufacturing. Design and production of structures with ultra-low thermal distortion using carbon fiber reinforced plastics (CFRP) have supported the high-precision observation performance of scientific satellites even before the Hayabusa.
The integrated preparation for quick action in design to production, testing, and delivery is a strength of the company, and for aerospace components, original experiment facilities are established at the head office and plant in Yokohama.
It is natural that space-related parts are subject to very rigorous evaluation testing and must satisfy the requirements. In the course of creating the helical springs for the Hayabusa2, NIPPI independently established testing equipment to meet the much higher level of detachment performance than that of Hayabusa and proved that they could pass the criteria. NIPPI is proud of the ability to develop the original evaluation systems and thinks that this should be the evidence of the high level of creation performance.
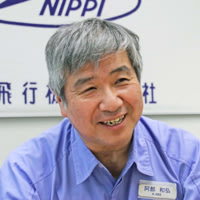
System Design Section
Engineering Department
Engineering / QA Division
Nippi