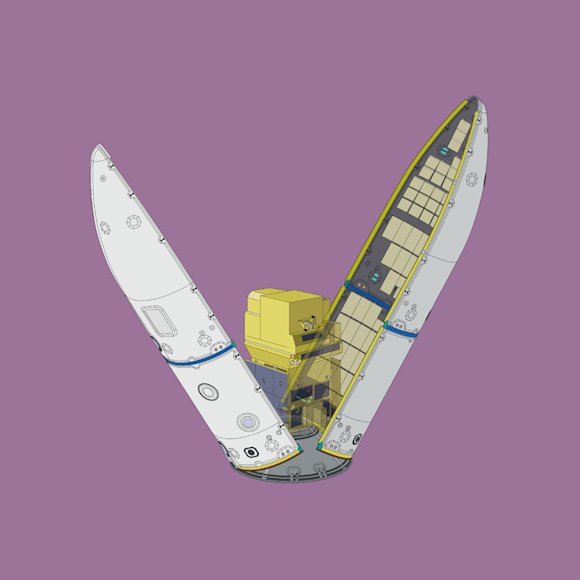
The first test model of the next-generation large -size launch vehicle, the H3, is scheduled for takeoff within fiscal 2021. Kawasaki provides the payload fairing on top of the launch vehicle to protect the satellite inside from large acoustic vibrations when it leaves the ground and from aerodynamic heating during the flight through the atmosphere. Discover the sophisticated technology that plays a part in the evolution of domestically developed rockets in Japan.
Protect satellites for travel into outer space
The first test model of the next-generation large-size launch vehicle, the H3, is scheduled to take off within fiscal year 2021. The H3 is the successor to the H-II A rocket currently in operation and offers three advantageous features: high flexibility, high reliability, and high cost-performance to facilitate carrying satellites.
The payload fairing on the top of the launch vehicle safeguards the satellite inside from large acoustic vibrations when leaving the ground and from the aerodynamic heating of atmospheric flight. Kawasaki was entrusted with the development of payload fairings for the H-II in 1984 by the National Space Development Agency of Japan (the present-day Japan Aerospace Exploration Agency) and successfully produced a made-in-Japan fairing for a large rocket.
Since then, the Company has led the development of rockets and satellite protection in Japan as the sole domestic supplier of fairings for large launch vehicles. The Company is also responsible for the supply of the H3 and will steadily support six liftoffs as expected per year.
The fundamental technological elements of payload fairings include the following: (1) an air-conditioning door to maintain a good environment (temperature and humidity) for the satellite, (2) sound absorbing materials to protect the satellite from large acoustic power and vibrations, (3) thermal insulation to shield the satellite from heat, and (4) separation systems to be jettisoned when the spacecraft reaches outer space and the systems are no longer necessary.
For the H3, wide application of carbon fiber reinforced plastics (CFRP) onto the structural members, the use of components common to both long- and short-type fairings, and other new technologies for flexibility, reliability, and cost reductions have been developed, which allow Kawasaki to have a role in the evolution of domestically produced rockets in Japan.
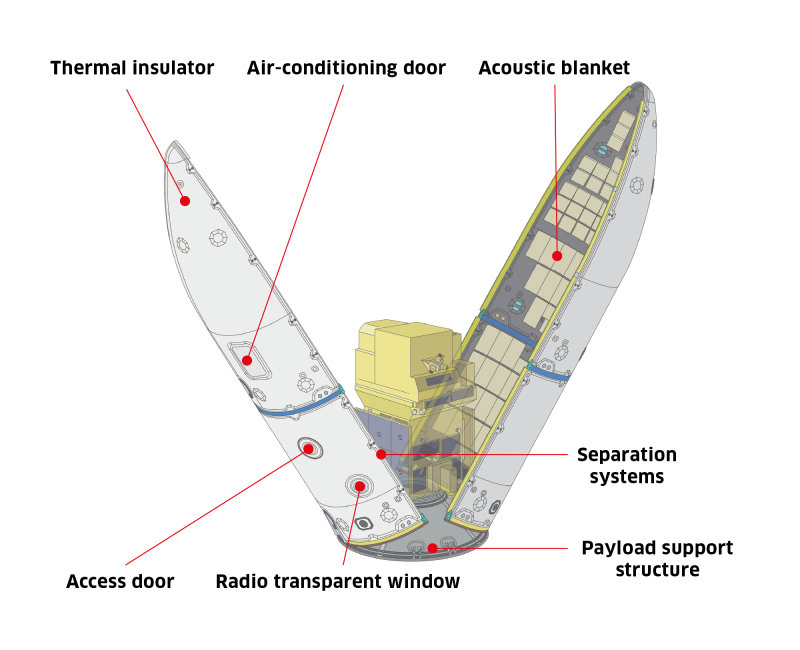
What is the H3 launch vehicle?
In consideration of the next 20 years from fiscal year 2021, the large LE-9 liquid rocket engine and other new features have been developed not only to ensure the means of transportation from Japan into space but also to establish a competitive advantage in the commercial satellite launch business.
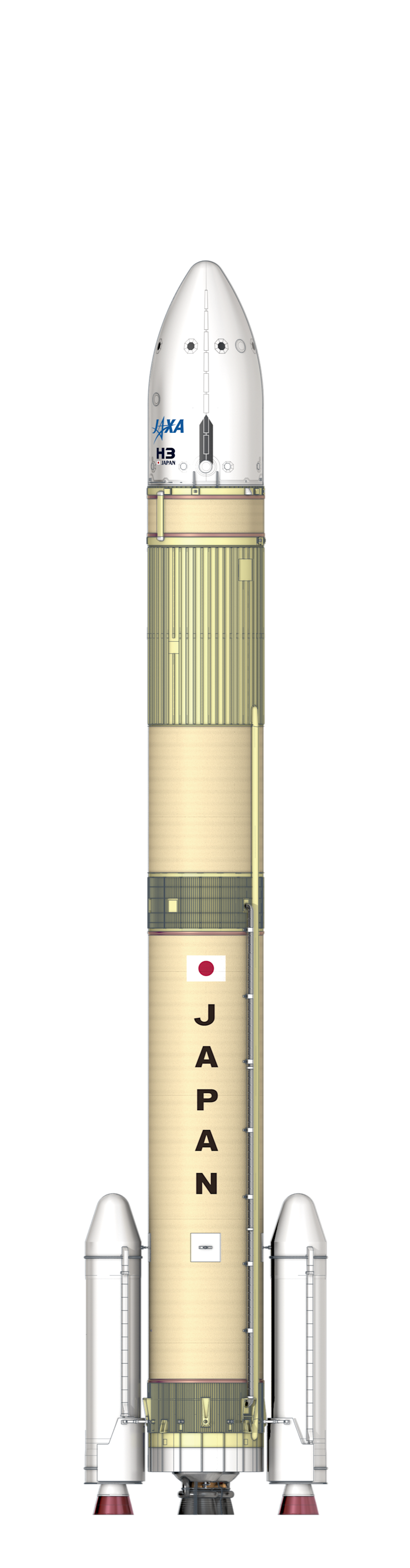
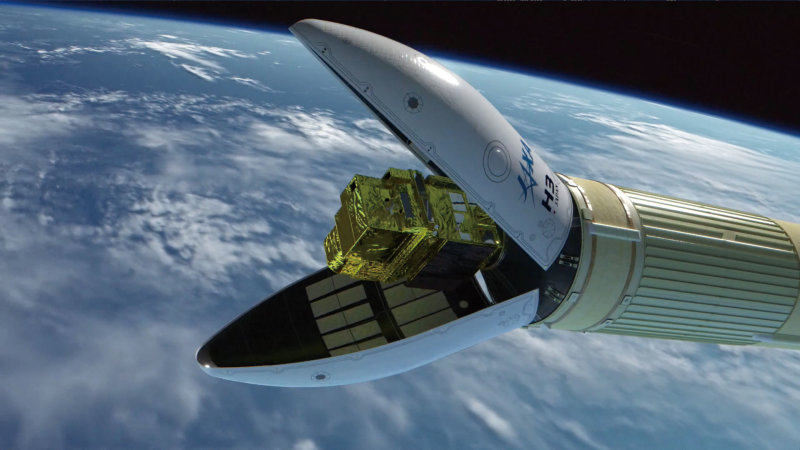
Introduction of Automated Fiber Placement (AFP) and practical use of the OoA adhesive technology
The use of CFRP applies to the double contour shape of the ogive and reduces the cost to produce the structure panels of the fairing, which account for a large portion of the expenditures.
In the case of the payload fairings for the H3 launch vehicle, the automated method to lay-up CFRP on aluminum honeycomb cores was adopted.
Moreover, the vertical joining of panels is not achieved with nuts and bolts; a new technology has been developed to use CFRP sheets and adhesive to combine them, which is called the Out of Autoclave (OoA) method because no autoclave molding of CFRP is performed.
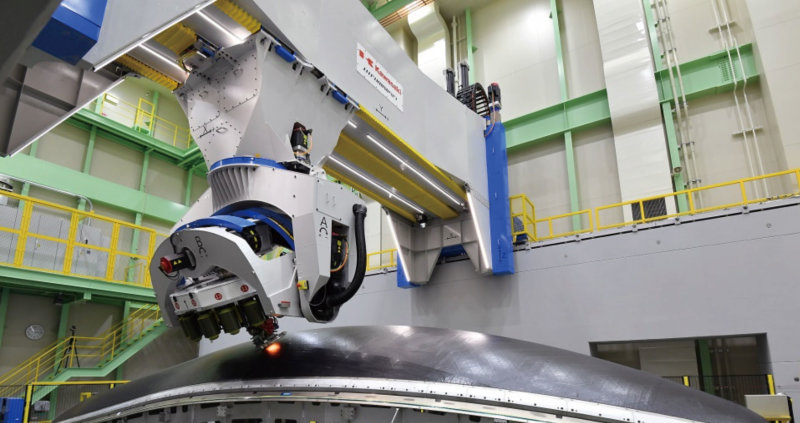
Use of common components compatible with both large and small satellites
In the same manner as the H-IIA launch vehicle, the H3 must have the flexibility to put satellites with different measurements into individual orbits. To cope with this issue, Kawasaki proposed fairings in two different sizes. The bottom part of the long (standard) form can be removed to become the short form. Thus, common components are used in production, and development costs are held down. For your information, the bottom part is about 6 m high.
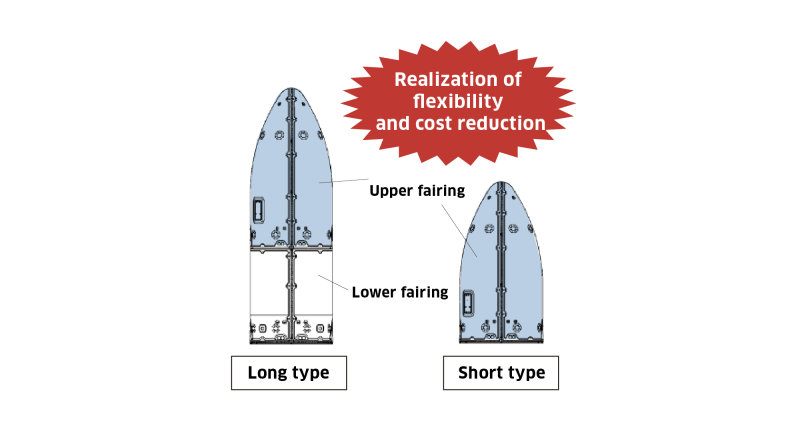
Separation systems at the heart of technology
Separation systems are the most technically difficult devices on the payload fairing. Because they are structural elements that combine the structure panels, the systems must be strong enough to withstand the aerodynamic loads, yet not so strong that they fail to reduce the shock to the satellite during separation (to decrease the energy required for separation). These mutually contradictory requirements must be balanced.
Kawasaki developed a unique Japanese separation mechanism based on the notched bolt (frangible bolt) method, which was used in the canopy (transparent cockpit cover) emergency release system on fighter aircraft. This highly reliable separation system can be applied to new models of fairings even today.
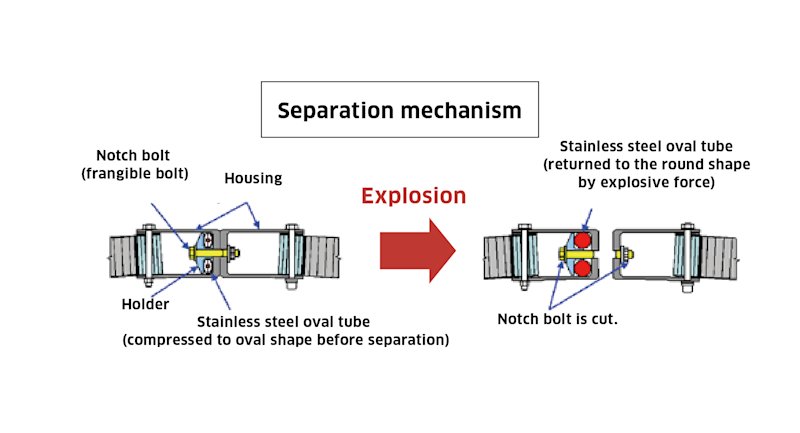
Acoustic blanket
In order to reduce the acoustic vibrations caused by the engines and interference with the atmosphere, the inner surfaces of the payload fairings are covered with acoustic blankets (sound absorbing materials) made of glass wool and resin foam. They are packed in filter-equipped covers to guarantee cleanness in the satellite compartment.
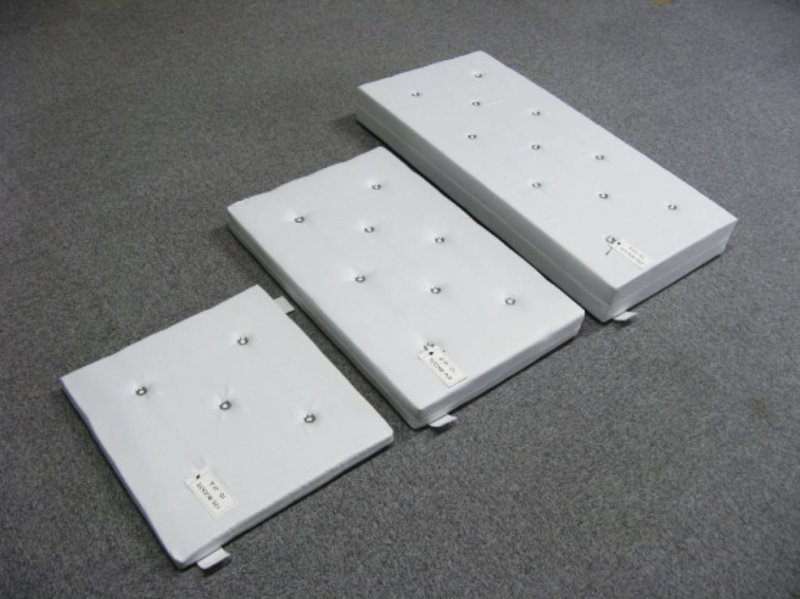
Thermal insulator
To prevent increases in the temperature of the body structures due to aerodynamic heating and to maintain the appropriate temperatures around the payload, insulators are placed on the exterior of the fairings. Lightweight silicone foam, which is good insulation, is used to protect the satellite from the severe atmospheric conditions where fairing surfaces can exceed 300°C.
Radio transparent window
Opening fitted with an RF-transparent material through which the satellite communicates with the facility on the ground.
Payload support structure
Equipment to fix the payload.
Air-conditioning door
To take in clean air from the ground facility to the inside of the fairing until the launch.
Access door
To be used by the satellite crew for service and maintenance.
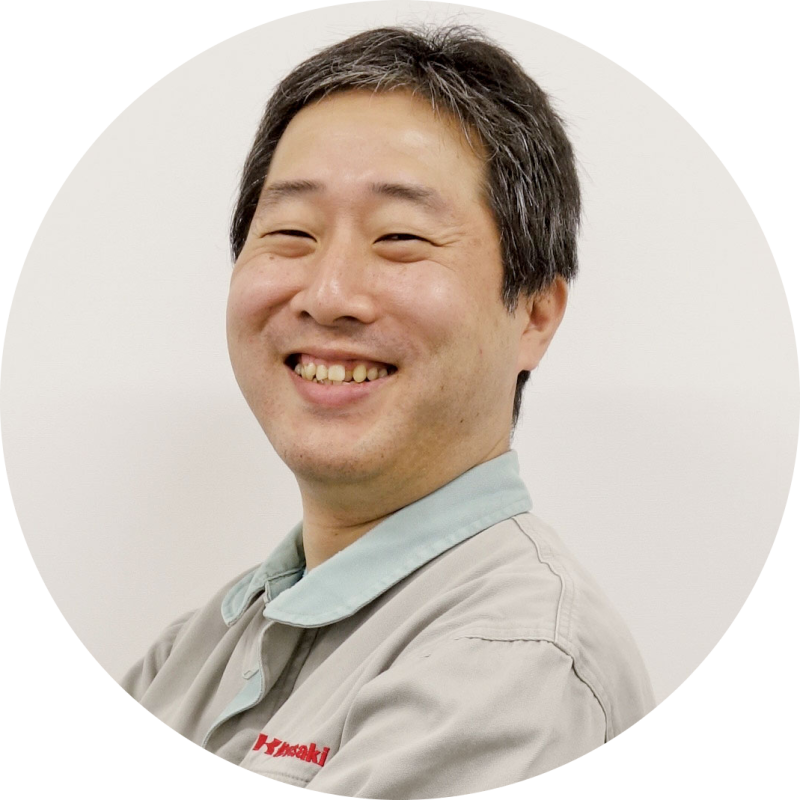
Space Transportation Systems Section
Space Systems Engineering Department
Defense and Aerospace Project Group
Aerospace Business Division
Aerospace Systems Company
Kawasaki Heavy Industries, Ltd.
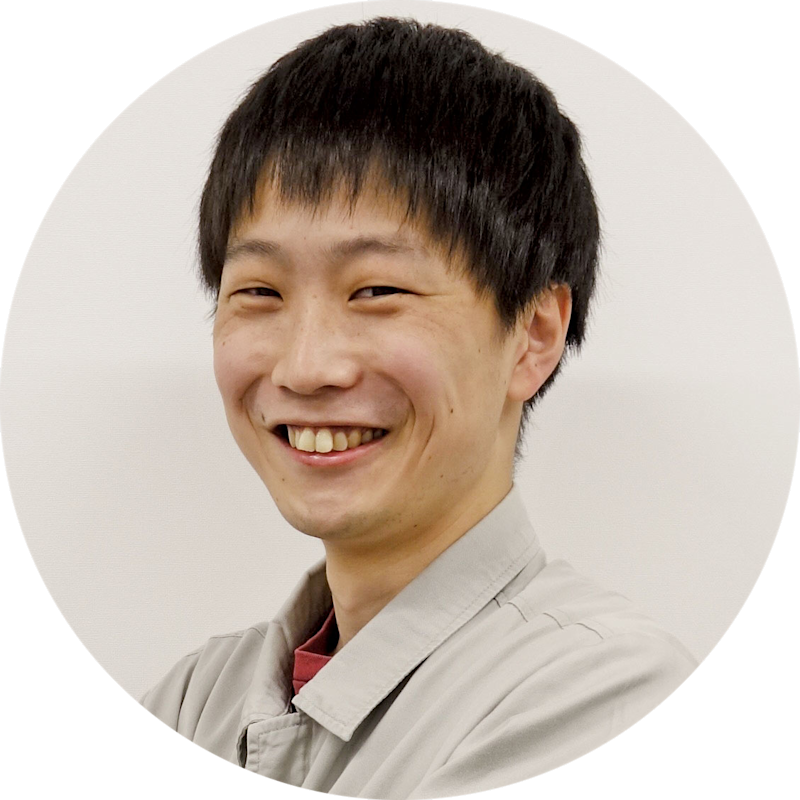
Space Systems Engineering Department
Defense and Aerospace Project Group
Aerospace Business Division
Aerospace Systems Company
Kawasaki Heavy Industries, Ltd.