Hokkaido Shinkansen Completed. What is the Backstory to Shinkansen Development?
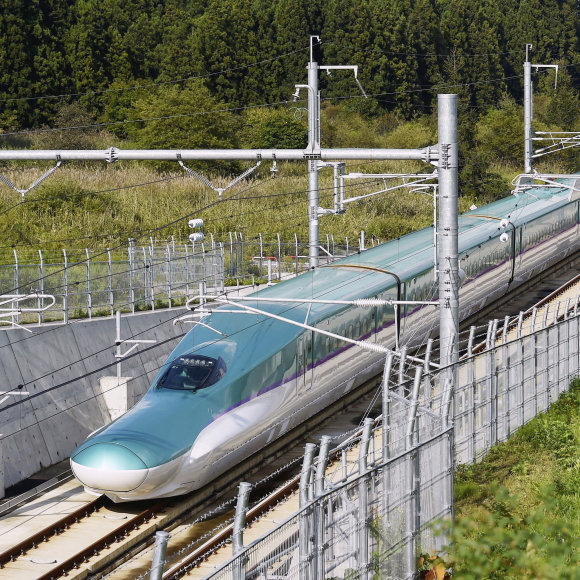
Forty-three years after the decision on the construction plan and eleven years after the start of construction, the Hokkaido Shinkansen entered commercial service on March 26, 2016. The trains that link the main island of Japan, Honshu, to the northernmost island at 200 km/h are called the Series H5, built to order for the Hokkaido Railway Company (JR Hokkaido). Key persons from Kawasaki, who worked on the first set of these trains, talk about the special inside stories.
Hokkaido Enters the Shinkansen Era
Sitting in the berth of a train, which exits the Seikan Tunnel, you see snow before you—have any of you had that experience? The Hokutosei, Twilight Express, the Cassiopeia, the Hakuchō and the Hamanasu—these express and limited express trains, linking Honshu and Hokkaido since the beginning of the Heisei era (1989–2019), completed their mission and left the frontline just before the start of the Reiwa era (2019–). While, on March 26, 2016, Hokkaido finally entered the Shinkansen era.
The Hokkaido Shinkansen had been the earnest desire of the public for a long time. Today it travels the northern land. The project was launched with the expectation to create new demand for tourism through collaboration with the Tohoku region, provide transportation unaffected by bad weather, and increase in the number of tourists and visitors. Transportation by train is a sustainable means with lower impact on the environment than travel by air, which could be one of the reasons why trains have gained in popularity. The Hokkaido Shinkansen was initially launched for the 149 km section between Shin-Aomori Station of the Tohoku Shinkansen and Shin-Hakodate-Hokuto Station. The new trains have a top speed of 260 km/h and travel between Tokyo and Shin-Hakodate-Hokuto in four hours and two minutes at the shortest. Currently, thirteen round-trip services per day are offered: ten between Tokyo and Shin-Hakodate-Hokuto, and one each between either Sendai, Morioka, or Shin-Aomori and Shin-Hakodate-Hokuto.
The Series H5 for the Hokkaido Shinkansen is a special train designed for particular weather conditions. To begin with, the Series H5 features specifications to withstand heavy snowfall based on the Series E5 developed for the JR Tohoku Shinkansen. The train already had a number of design features for cold weather, including covers to protect electrical systems in the underside of the cars from snow and wind, and a snowplow at a nose of the lead car to clear snow from the tracks. What were the specific challenges for the Series H5? Nobuyoshi Takehiro, senior staff officer in the Engineering Department, answered, “The Series H5 required additional improvements in three areas: condensation, snow, and icing.” What is condensation? The hint is in the Seikan Tunnel.
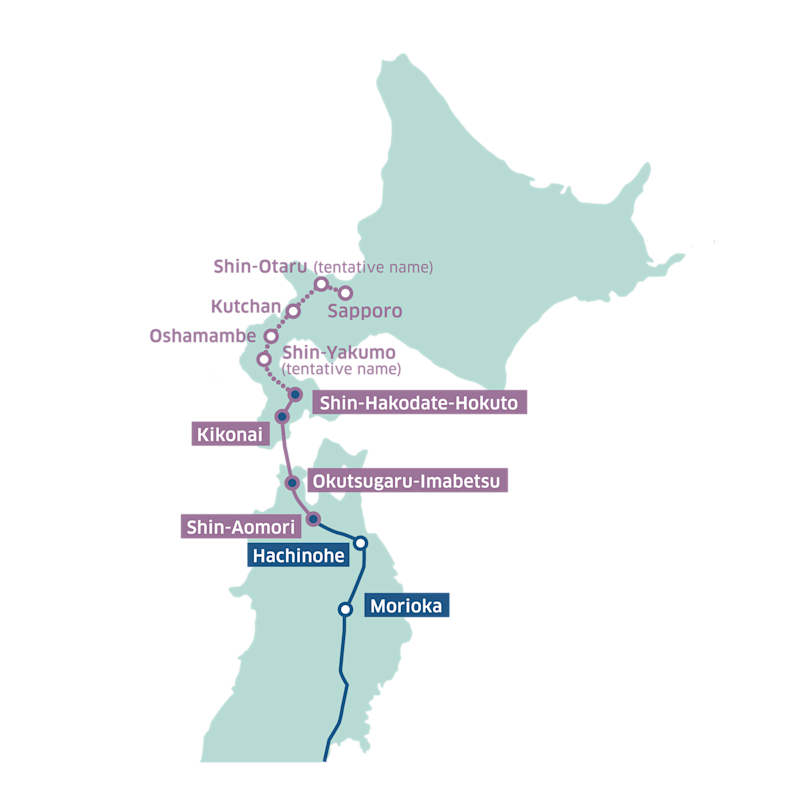
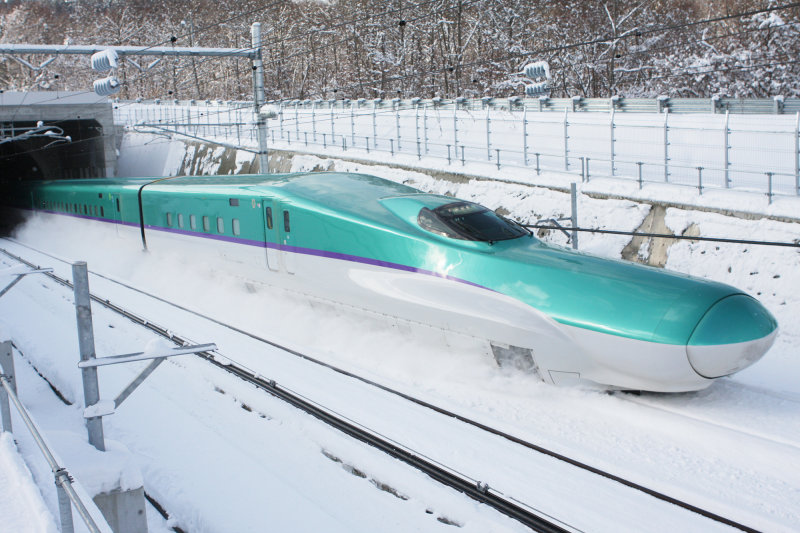
Technologies to fight Temperature Differences of 20 Degrees Celsius
Of the 149 km section where the Hokkaido Shinkansen initially started operation, the Seikan Tunnel accounts for 54 km. The temperature inside the tunnel under the sea is kept at 20°C and the humidity is 80% to 90% all year round. On the other hand, the average temperature in Aomori and Hakodate during the coldest time of the year is 1ºC to 2°C below zero. When a train enters the tunnel at a speed of more than 200 km/h and is exposed to this temperature difference, condensation instantly forms on the cars, and when the train exits the tunnel, the condensation freezes due to the cold air. Even a small amount of snow or ice can be hazardous to the Shinkansen at high speeds. “Sections with exposed metal parts are particularly susceptible to condensation, so they are covered with insulating materials, taking care not to leave any gaps,” said Takehiro.
Plumbing was emphasized as anti-icing measures. Draining is a well-known process that prevents pipes from freezing in cold regions. This process of draining is incorporated into the Series H5 as well. For example, any water remaining in the plumbing pipes, such as in the toilet drainpipe, might result in a failure if it were to freeze during storage of the trains in a depot. To prevent this, the piping is provided with a drain, along with other technologies such as using compressed air to purge the water remaining in the pipes. The Series H5 can purge all water from the plumbing pipes even if the main power supply is shut off. Such invisible efforts into the minutest details are the basis of operational safety.
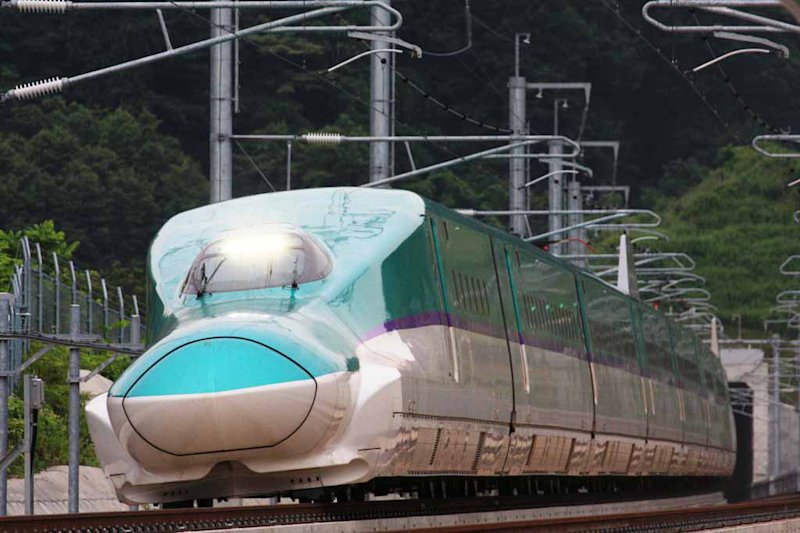
Running a Three-Legged Race with a Railroad Company
A countless number of people, railroad companies, and rolling stock manufacturers were involved in the major project to introduce the new generation Shinkansen. Ryo Tahara closely watched the development of the project as the first trainset of the Hokkaido Shinkansen was delivered. He was the sales representative in charge of the Hokkaido District. Tahara conveyed the questions and requests of the railroad company to Kawasaki’s design department and supported them so that the development moved along smoothly. He found the optimal solution on how Kawasaki’s technologies could fulfill the requests of the client.
Tahara said that the most nerve-racking moments for him came during the in-process inspection of checking whether the train cars were being manufactured with precision during the middle of the process and the final acceptance inspection before delivery. “Even a small chip remaining on machined parts, for instance, could cause a malfunction in the future,” explained Tahara. “For this reason, we made the utmost effort to ensure that our inspections were thorough. This is part of our commitment to the safety of passengers using our trains.” Tahara continues to be involved even after the trains had been delivered. Elaborate maintenance is essential to ensure that the trains are safe to operate. It is necessary for Tahara to continue to watch the trains and maintain close relations with the client. The railroad company and the rolling stock company move forward together like participants in a three-legged race.
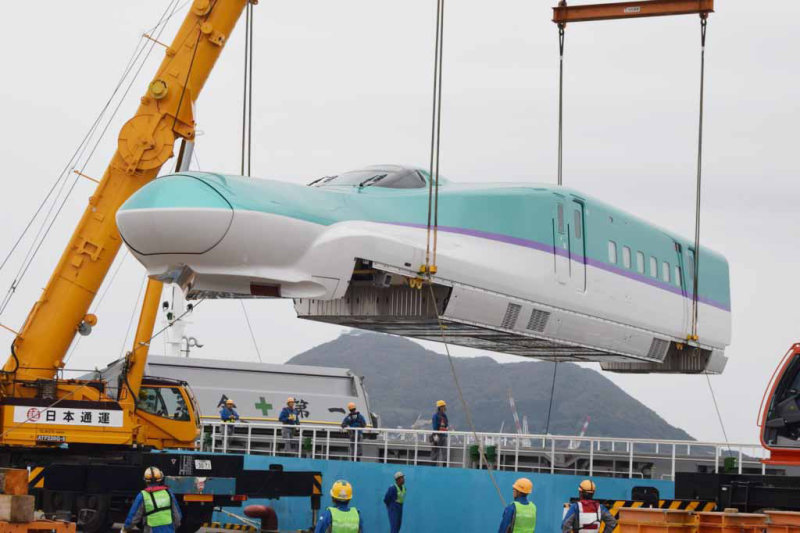
Major Mission to Transport Cars to Hakodate Port as Planned
The Shinkansen is manufactured by each railroad company. For example, Kawasaki manufactures train cars at the Hyogo Works located along the Hyogo Canal, ten minutes’ drive south from JR Hyogo Station. The direct distance from Hyogo Works to Hakodate as the delivery destination is about 1,000 km. The newly completed train cars will be shipped from Kobe Port to the far north along the Pacific coast of Japan, which takes three days. Transportation is a major mission, though it is only part of the project. Tsutomu Maeda, the manager responsible for transportation work in this project said, “A single completed car weighs several tens of tons, so these cars must be transported with utmost care. They must be handed over to the client free of the slightest imperfection—not even a single scratch is permitted.”
The ten memorable cars of the first Hokkaido Shinkansen trainset were shipped from the Works in October 2014. The shipment was scheduled to arrive at Hakodate Port in time for an unloading and welcoming ceremony on October 13. “We faced an unexpected problem,” said Maeda.
Transportation of the train cars by sea from the Hyogo Works to Hakodate Port takes three days. Therefore, with a few days to spare, work began on the 8th to load the cars onto barges at the Works. However, Typhoon Vongfong, which formed near the Marshall Islands on October 3, was approaching Japan and developing into the most powerful typhoon of the year. A typhoon course map indicated that the typhoon might pass through the Japanese Archipelago along Kyushu, Kobe, and the Pacific coast. In addition, a probability circle for Typhoon Vongfong covered the transportation route of the Series H5 cars.
“The cars were transferred to a transport vessel at Kobe Port, but the vessel might have been hit by the typhoon if it had sailed up the Pacific coast,” recalled Maeda. Therefore, at the last moment, the route was changed to sail up the coast of the Sea of Japan through the Kanmon Straits from the Seto Inland Sea. Maeda added, “We were very anxious about whether we would make it by the ceremony on the 13th, and were very nervous.”
On October 13, seven hours before the welcoming ceremony, the ship carrying the completed cars finally reached Hakodate Port where the parties involved were waiting impatiently. The work to unload the cars was carried out carefully with occasional gusts of wind from the approaching typhoon. First, the lead car, weighing 31 tons, was successfully unloaded without a single scratch. “I was so relieved that I felt completely worn out,” said Maeda with a laugh.
The cars continued their journey even after being unloaded. They were transported by road to the Hakodate General Rolling Stock Depo*1 in Nanae-cho. Test runs began on December 1 and were repeated until the opening day to ensure that the trains were safe to operate.
*1:The current official name is Hakodate Shinkansen General Vehicle Station
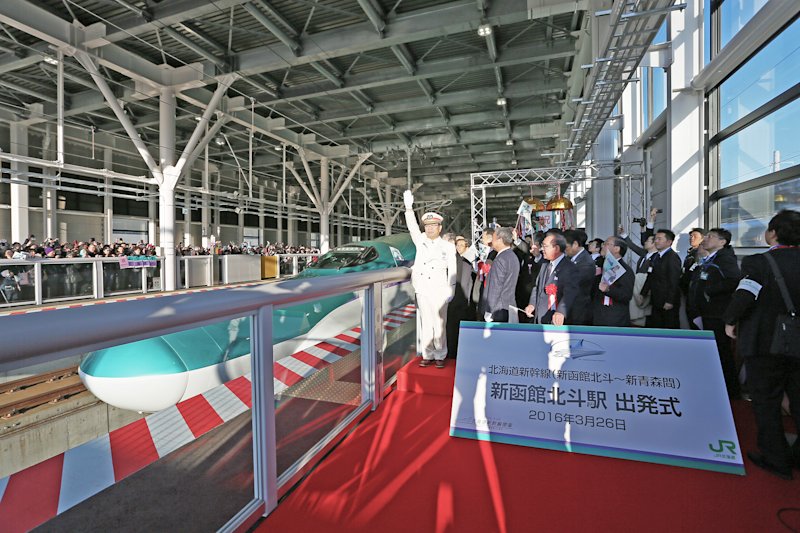
Future When Sapporo in Hokkaido and Kagoshima in Kyushu are Linked by the Shinkansen
Vivid three-color paint applied to the upper, middle, and bottom of the car body is characteristic of the Hokkaido Shinkansen. This color arrangement, coming up with the key phrase “Prologue of the North Experience,” is a reminder of a prologue to the journey to Hokkaido. The colors are Joban green, the same color as the Series E5, on the upper part of the car body, Ayaka purple for the waist of the cars from the image of lilac, lupine, and lavender flowers of Hokkaido, and an elegant Hiun white on the lower part of the body. In addition, the side of cars 1, 3, 5, 7, and 10 features a logo created in the motif of a gyrfalcon flying to Hokkaido and the magnificent northern island. In various places of the inside of the cars are designs inspired by icons typical of Hokkaido, such as the patterns on Jomon earthenware, Ainu patterns, snowflakes, and drift ice.
“At 6:35 a.m. on schedule, the first train with a capacity of 731 passengers departed Shin-Hakodate-Hokuto Station when Tadashi Narumi, stationmaster of Shin-Hakodate-Hokuto Station, signaled its departure. The train started to run smoothly for Tokyo.” (Cited from the electronic edition of the Nihon Keizai Shimbun dated March 26, 2016)*2
The early morning of March 26, 2016, it was sunny but the temperature was below freezing. The platform of Shin-Hakodate-Hokuto Station was filled with people holding flags. The children’s breaths could be seen, and their eyes were gleaming. Everyone there looked bright and happy. The shiny train cars painted in three colors started moving without a sound, when voices calling “Moving!” and “Wow” were heard here and there. Sent off by the crowd to cheers and applause, the car bodies glittered in the morning sun in winter went out of sight in the blink of an eye like a falcon soaring through the air.
Thanks to the Hokkaido Shinkansen, the distance between Tohoku and Hokkaido is now closer. However, the project is ongoing. Work is already under way to extend the Hokkaido Shinkansen line from Shin-Hakodate-Hokuto to Sapporo with the 212 km section slated to begin operation by the end of fiscal 2030 if the work goes as scheduled. In the future not too far from now, the final network of Shinkansen lines will be completed and will span the entire length of Japan from Sapporo in Hokkaido all the way to Kagoshima at the southern tip of Kyushu. Kawasaki’s technologies are connected to that dream come true.
*2: For the details, please refer to the article “The Opening of Hokkaido Shinkansen / The First Train Bound for Tokyo Departures” in the electronic edition of the Nihon Keizai Shimbun of March 26, 2016
The Hokkaido Shinkansen opened as the main artery of Hokkaido linked directly to the Kanto and Tohoku areas. The train has to travel at high speeds under the harsh weather conditions of snow and cold in Tsugaru and Hokkaido. In addition, the train operates under the special circumstances of traveling through the Seikan Tunnel underneath the ocean—conditions that are different from other Shinkansen lines. Therefore, thorough measures have been implemented from aspects of structure and train cars. Kawasaki supports the safety of train cars from the technological aspect. The company makes sure that the professionals in each department work closely with the client from the processes of development and manufacturing to delivery and long-lasting maintenance by which Kawasaki protects the safety of the Shinkansen every day.
Manufacturing Processes of the Series H5
01 Production and assembly of body shells
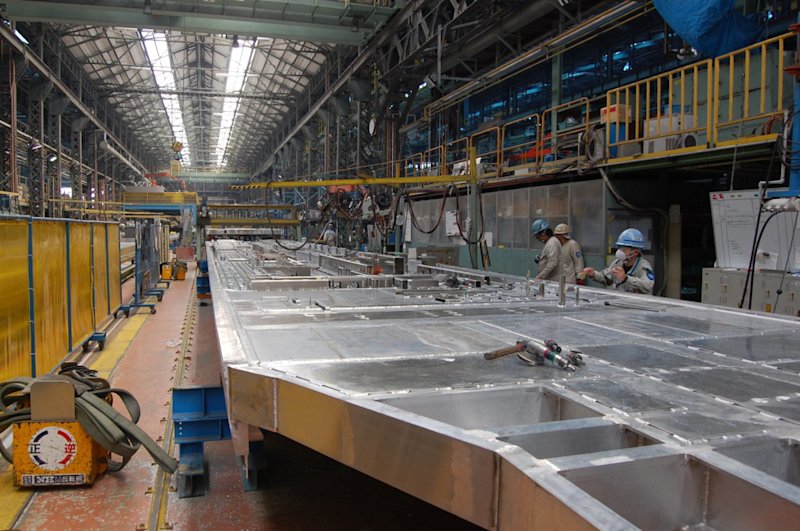
02 Painting
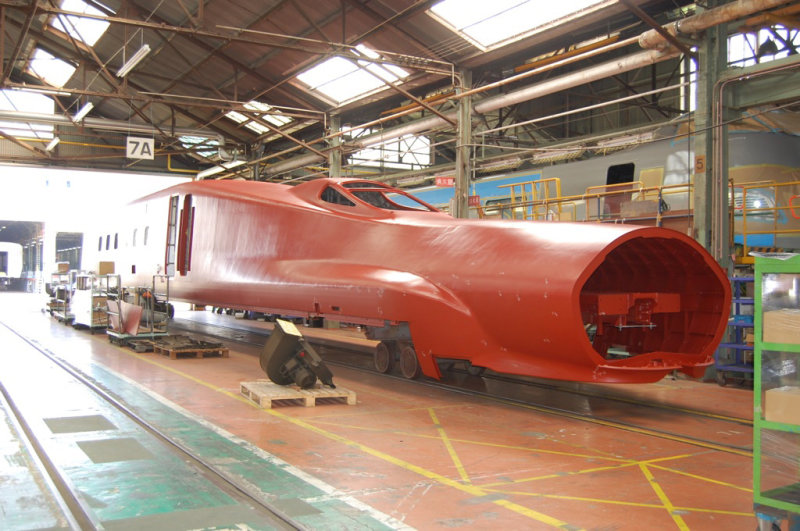
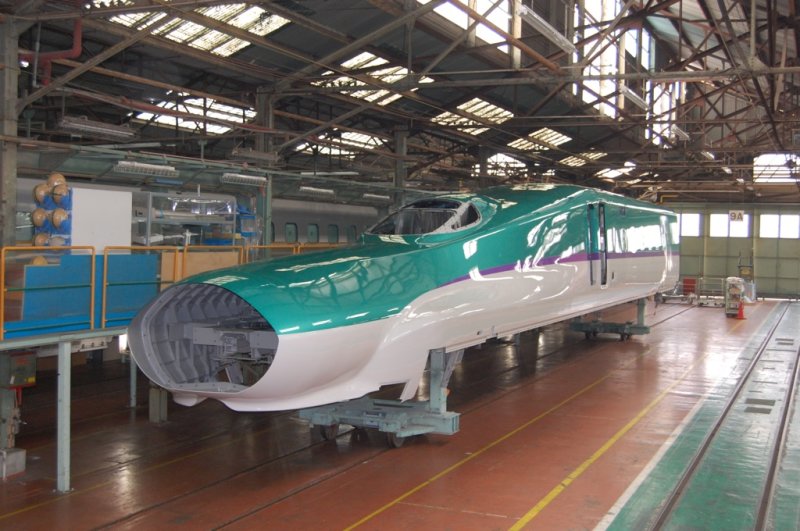
03 Outfitting
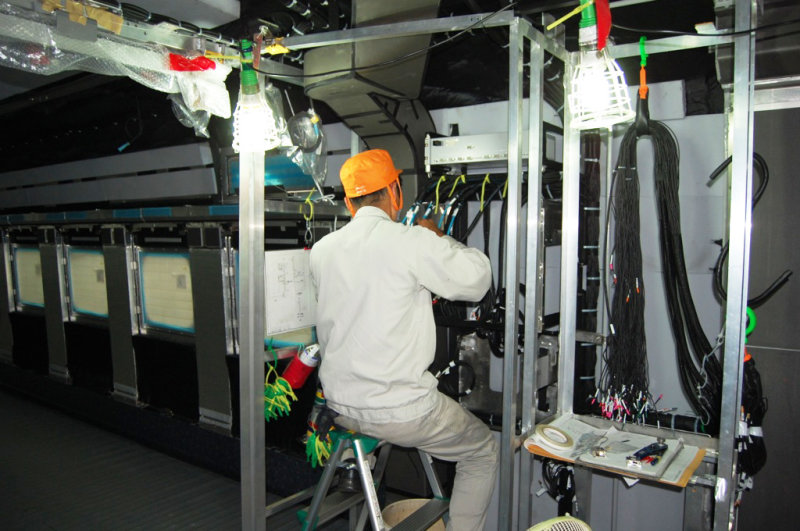
04 Bogie installation
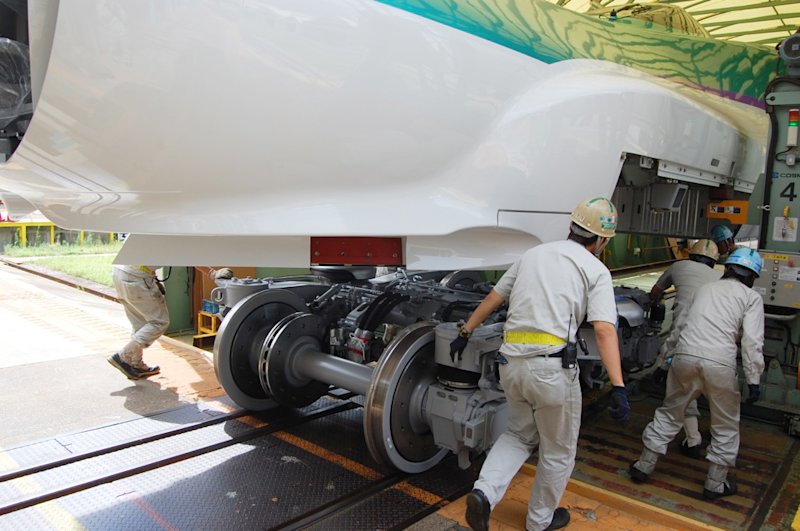
05 Final inspection
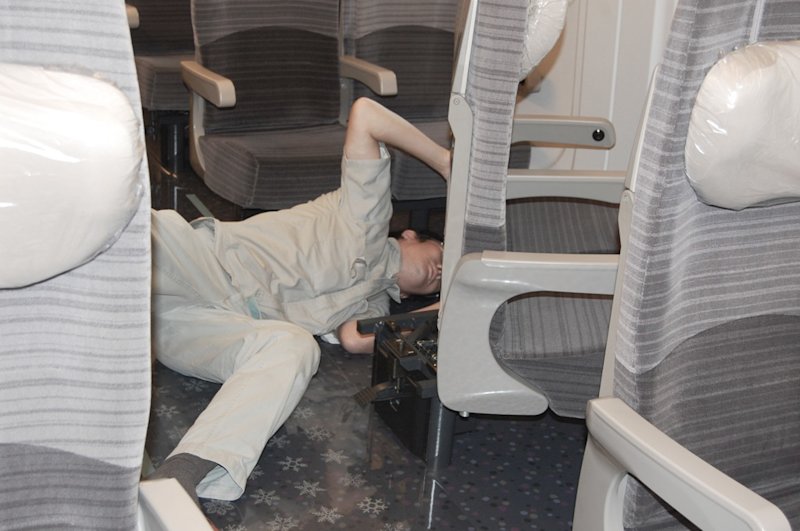
06 Functional tests and on-premise test run
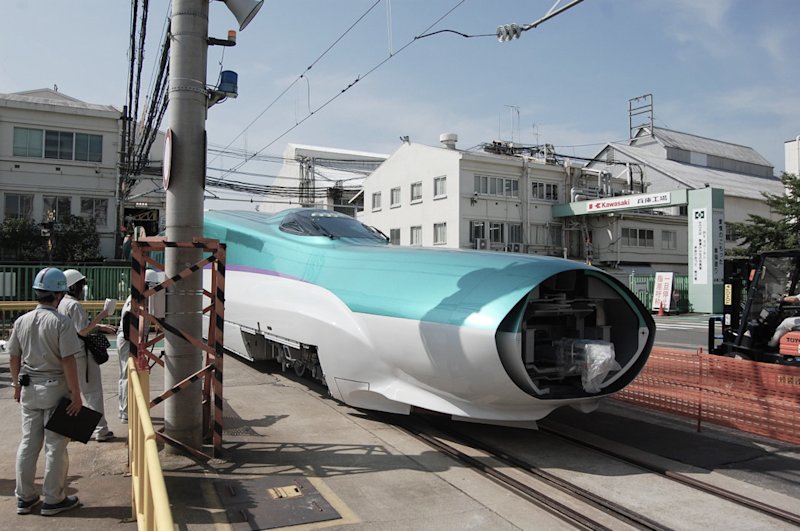
Environmentally and Economically Friendly Shinkansen
Christian Wolmar, a journalist from Britain specializing in traffic and transportation, states in his book Blood, Iron and Gold as a quote from an economist,
“Japan’s high speed railway plays a major role in reducing transportation costs and controlling the amount of import of crude oil. According to the International Association for Applied Systems Analysis, compared to an airplane which flies the same route, the Shinkansen has almost three times the productivity of an airplane in terms of labor efficiency, and five times the efficiency of the latter in terms of capital investment, and eight times in terms of energy consumption.”
Furthermore, the Hokkaido Branch of the Development Bank of Japan points out, “Compared to the conventional line era, the number of visitors to Hokkaido has significantly increased since the Hokkaido Shinkansen began operation, which is boosting the strong demand for tourism.” This branch, before the opening of the Hokkaido Shinkansen, had estimated the economic ripple effect to Hokkaido to be about 13.6 billion yen per year. However, the bank calculated that in the first year of opening the direct effect (economic effect caused by tourism consumption from in-coming visitors from other regions) would be 20.4 billion yen, that the primary indirect effect (effect the production within Hokkaido is triggered in accordance with direct effect) would be 9 billion yen, while the secondary indirect effect (effect triggered by the increase of compensation of employees) would be 5.6 billion yen. Thus, it demonstrates numbers much higher than the preliminary calculation, concluding that the total economic ripple effect generated through the opening of the Hokkaido Shinkansen is 35 billion yen.
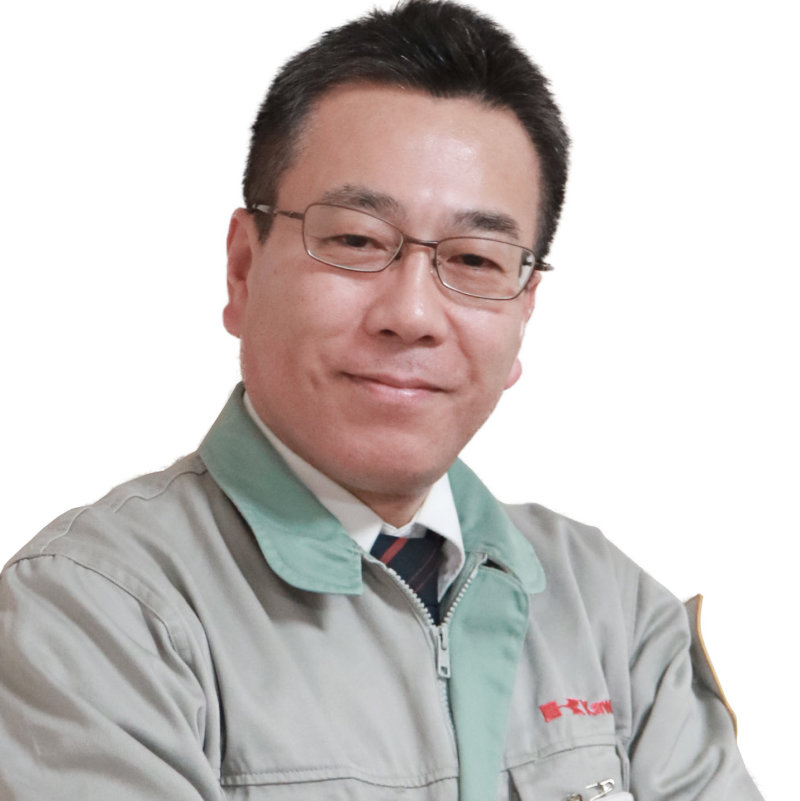
General Manager
Engineering Division
Rolling Stock Company
Kawasaki Heavy Industries, Ltd.
Joint Creation Approach by Manufacturers and Customers is Highly Acclaimed by Railroad Companies around the World
In the United States and Europe, railroad manufacturers are sellers, while railroad companies are purchasers, but in Japan, railroad companies and manufacturers traditionally work closely together from the design and development stage to firm up the details of the specifications and jointly conduct technical verifications. In other words, rolling stock in Japan is a joint creation of the manufacturers and customers. There is a joke that says when trains delivered have problems, an engineer moves in first and foremost from a Japanese manufacturer, while a lawyer moves in first from manufacturers in the United States and Europe. That indicates that train car manufacturers of Japan are customer oriented.
The Series H5 for the Hokkaido Shinkansen was developed jointly by Kawasaki and JR Hokkaido, including the future extension to Sapporo and the challenges that are likely to arise. In the United States, Kawasaki has received numerous orders for rolling stock from major transportation authorities in New York, Washington, and Boston. In Asia, major contracts have been awarded in Taiwan and Singapore. This track record of accomplishments attests to the solid reputation overseas of Kawasaki’s joint development approach that has been honed through rolling stock manufacturing in Japan.
The technologies behind rolling stock and high-speed trains are reaching new levels. Some trains already operate at 320 km/h, and to achieve even higher speeds, state-of-the-art knowledge is required in the development of the motors and brakes, as well as the shape of the leading end and car bodies. Accordingly, we will work together with the Corporate Technology Division—Kawasaki’s think tank—to attain technological synergies within the company in aerodynamic analysis technologies cultivated through aircraft development, thus leveraging our strengths as a rolling stock manufacturer within a comprehensive heavy manufacturing company. We also plan to utilize the supercomputer K, which is located in Kobe, for development. Through this and other measures, we will differentiate ourselves from other rolling stock manufacturers.
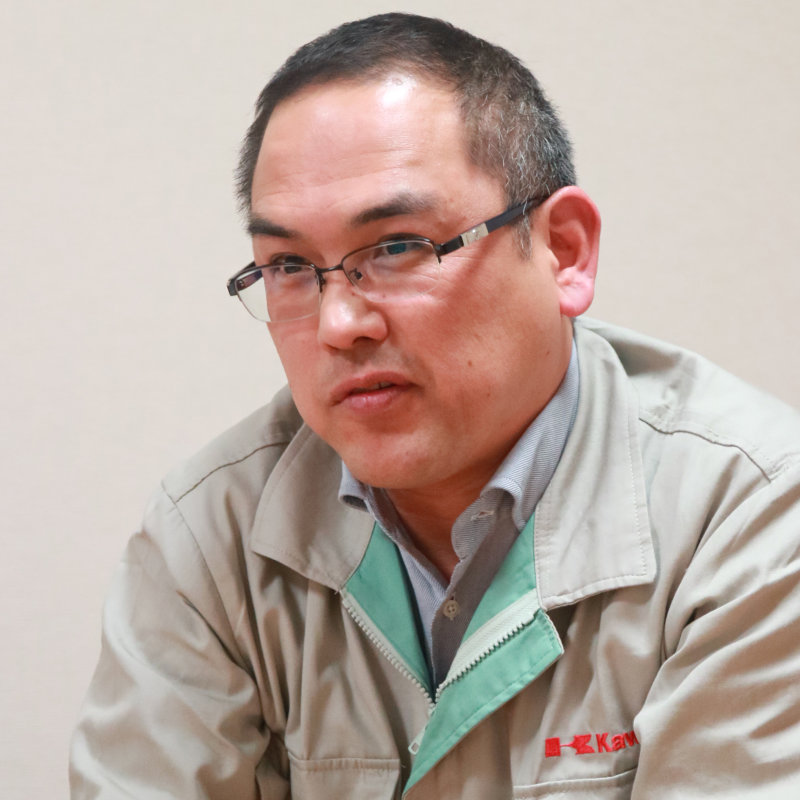
Engineering Section 1
Engineering Department
Engineering Division
Rolling Stock Company
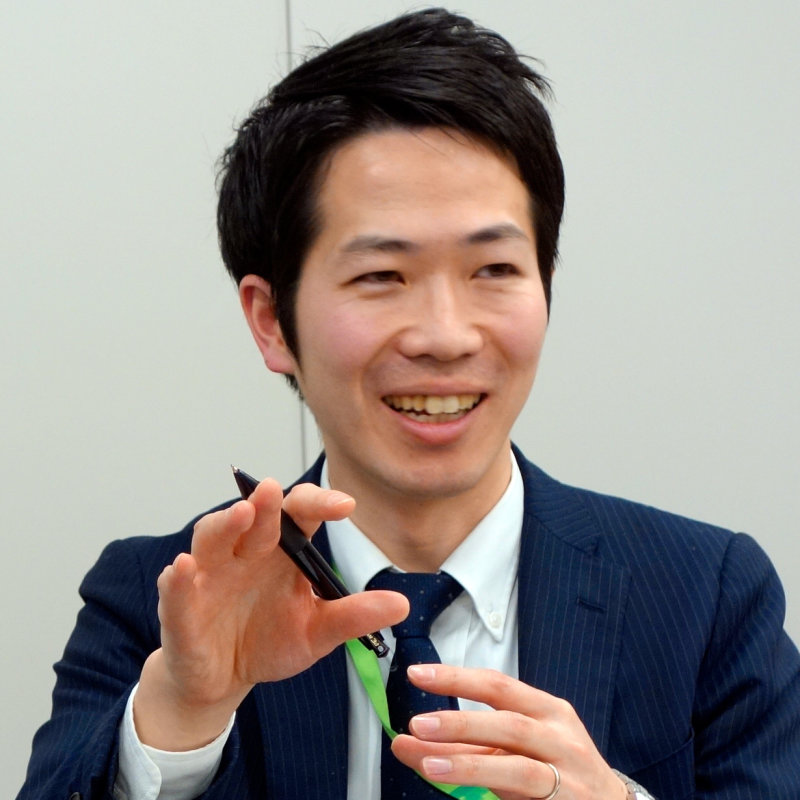
Marketing & Sales Division
Rolling Stock Company
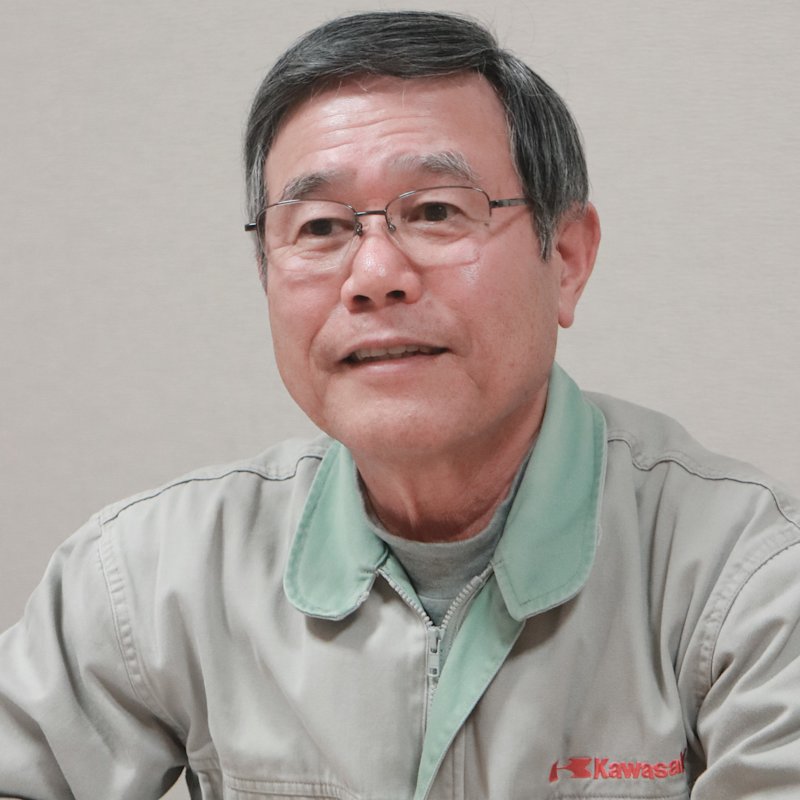
Transportation Section
Transportation Department
Kawasaki Rolling Stock Component Co., Ltd.
Note: The numerical values and job titles stated herein are based on information as of April 2016