For a Carbon-Free Society, Hydrogen Energy Development is Accelerating Worldwide
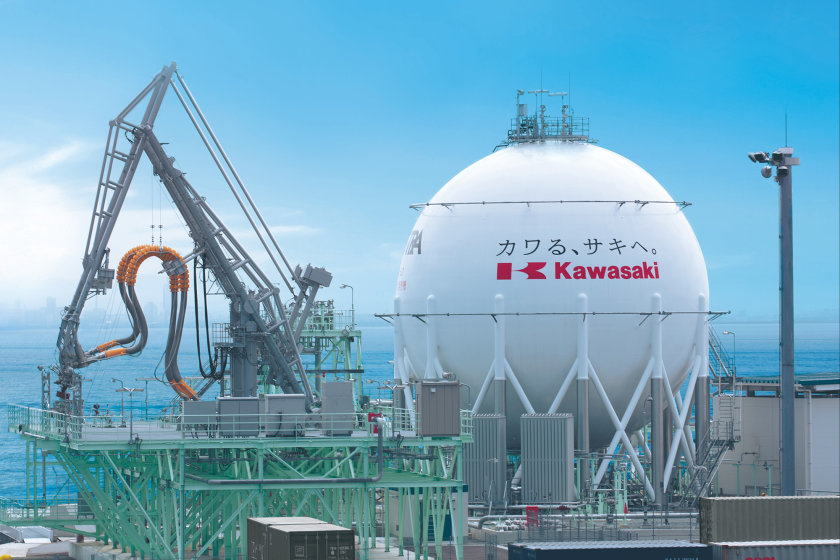
Today, hydrogen energy is gaining popularity as part of the efforts toward the realization of a carbon-free society. Since hydrogen does not emit CO₂ when utilized, it serves to considerably limit global warming. Moreover since, hydrogen is derivable from numerous sources, it is also expected to be used from the perspective of energy security in Japan. Kawasaki promotes the development of its original technologies in the four-phase process of hydrogen: production, transportation, storage, and utilization. Let’s look at its progressive actions with the objective of building a hydrogen energy supply chain.
The Key is to Diffuse the Use of Hydrogen Energy during Production
Since adoption of the Paris Agreement in 2015, the trend for carbon-free and low-carbon practices has been accelerating worldwide. Because the power generation sector specifically calls for CO2 emission reductions, expectations are growing for the application of hydrogen energy, which does not emit CO2 during utilization.
The energy self-sufficiency rate in Japan is only 6% to 7% after the Great East Japan Earthquake, and the majority of fossil fuels for energy depend on imports from the Middle East and other foreign countries. From the viewpoint of energy security, the use of domestic energy, imports of energy from multiple sources, and the use of diverse types of energy are required.
Therefore, hydrogen energy is gaining attention because it can be manufactured in a variety of ways: using electricity to extract hydrogen from water and by processing the different ingredients of oil, natural gas and other fossil fuels, methanol, ethanol, sewage sludge, and waste plastic.
In particular, the supply chain to produce hydrogen from unused or renewable energy resources overseas and to import it by marine transportation will contribute to the energy security of Japan. In addition, the process to convert surplus domestic renewable energy, including solar power, into hydrogen gas for use by vehicles, or “Power to Gas,” is considered an effective use of energy.
Hydrogen energy does not emit CO2 in the utilization phase. The process is expected to promote low-carbon operation in the electric power, industrial, and transportation sectors with large carbon footprints by using hydrogen as fuel for thermal power plants, the home-use fuel cell ENE-FARM, and vehicles.
The hydrogen fuel cell-related market will grow in the future; one estimate suggests that the worldwide use of hydrogen in a low-carbon society could create a 2.5 trillion USD market and jobs for 30 million people globally.
Furthermore, the spread of CO2-free hydrogen technology, which does not emit CO2 even during production, will play an extraordinary role in the realization of zero-emission energy systems.*1
*1:For the descriptions above, see the website of the Agency for Natural Resources and Energy of the Ministry of Economy, Trade and Industry
Kawasaki and Three Other Companies Offer the World’s First Demonstration Project for the Establishment of a Hydrogen Energy Supply Chain for Commercial Use
The development of the technology to use hydrogen energy is moving forward around the world. A first-of-its-kind demonstration project was started to establish a hydrogen energy supply chain and produce hydrogen from inexpensive brown coal (relatively low in quality), which is abundant in Australia, for export to Japan.
In February 2016, the consortium of Kawasaki, Electric Power Development (J-Power), Iwatani, and Shell Japan (later, Marubeni, Eneos, and Kawasaki Kisen joined) formed the CO2-free Hydrogen Energy Supply-Chain Technology Research Association (HySTRA) with the objective of launching a commercial-use hydrogen supply chain by 2030 to serve as the platform to produce, transport, store, and use hydrogen.
HySTRA is the implementation body for a pilot project subsidized by the New Energy and Industrial Technology Development Organization (NEDO) to build a hydrogen supply chain.
The four companies of HySTRA assume different responsibilities: (1) J-Power develops hydrogen production technology using the brown coal mined in Victoria, Australia; (2) Kawasaki and Shell Japan (Shell Group) build liquefied hydrogen (LH2) carriers and establish the technology for the transportation of LH2; and (3) Kawasaki and Iwatani construct LH2 handling terminals and establish technologies for operations. Kawasaki also leads the technological development for coordination with the Australian government.
In January 2017, the Hydrogen Council was formed as a global initiative to foster hydrogen energy transition. The Council currently consists of Kawasaki, Toyota, Honda, Iwatani, and other Japanese companies, as well as Air Liquide (France), Anglo American (U.K.), BMW Group (Germany), Royal Dutch Shell (U.K., the Netherlands), and other multinationals.
Turning our eyes to Japan, the government formulated the Basic Hydrogen Strategy in December 2017, which positioned hydrogen as the energy of the future that is as effective as renewable energy resources, and set forth the targets to be achieved, including an increase in the number of fuel cell vehicles and hydrogen stations and procurement of around 10 million tons of hydrogen fuel per year.*2
*2: For the descriptions above, see the website of the Agency for Natural Resources and Energy
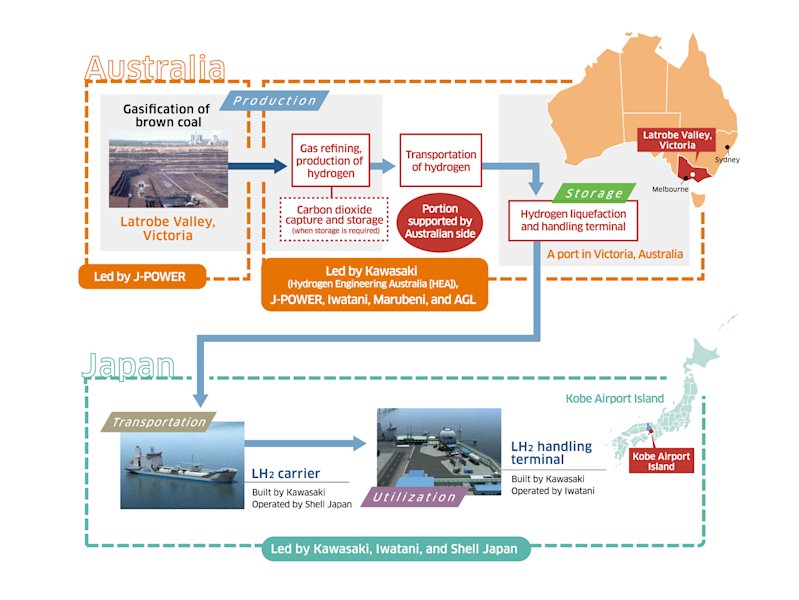
Hydrogen Energy Production is Addressed Collaboratively with the Australian Government.Technology Demonstration Testing Aimed at the Establishment of the World’s First Hydrogen Supply Chain is Scheduled
The Latrobe Valley is located 150 km east of Melbourne, Australia, which has brown coal seams, and the total amount of energy stored is estimated to be equivalent to 240 years of gross power generation in Japan.
In this area, J-Power leads the gasification of brown coal as part of a NEDO pilot project (“NEDO portion”). Separate from the NEDO portion, the construction of a pilot plant subsidized by the Australian government and the Victoria State government began (“Australian portion”). The plant has the facilities required for the post-processing of hydrogen gas, such as hydrogen gas refining, LH2 production, storage, and handling (loading/unloading).
The Australian portion is led by a consortium of six companies: Kawasaki, Iwatani, J-Power, Marubeni, Sumitomo Corporation, and AGL, a leading energy firm in Australia.
The state of Victoria welcomed this project, stating that this first-of-its-kind project could lead the way to a hydrogen-based society and that a few hundred jobs were expected to be created as a result. Meanwhile, because of the very high environmental awareness of the Australian population, people are paying close attention to the environmental effects of using brown coal, a fossil fuel, and how the CO2 generated during the production phase of hydrogen will be treated.
Brown coal (lignite) is geologically young with high moisture content (50 to 60%) and can catch fire naturally when it dries. This makes it difficult to export, so it has been used solely for local power generation. However, a value judgment was made that the use of brown coal as a raw material for hydrogen energy could offset these shortcomings and the project could create added economic value from the unused resource of brown coal.
With regard to the CO2 generated during hydrogen production using brown coal, Kawasaki is coordinating with the Carbon (CO2) Capture and Storage (CCS) Project, or CarbonNet, led by the Australian Government, and keeping an eye on commercialization.
For the Australian portion, Kawasaki’s role is to build a handling terminal and evaluate its operation. The demonstration testing for building the world’s first international LH2 supply chain, scheduled for the second half of this fiscal year, will verify the series of necessary technologies as follows: hydrogen is produced from the brown coal mined in the Latrobe Valley in the state of Victoria; the hydrogen is liquefied and loaded onto carriers at the port of Hastings and transported to the Kobe LH2 handling pilot terminal Hy touch Kobe in Japan.
By devoting efforts to create infrastructure facilities and foster the engineers essential for the development of the hydrogen industry, Kawasaki is aiming to launch a commercial-use hydrogen supply chain and realize a sustainable society with CO2 emission controls.
World's First LH2 Carrier. Also Leads to Establishment of International Standards for Safe LH2 Transport
As a member of HySTRA, Kawasaki built the LH2 carrier (pilot vessel) Suiso Frontier, and Shell will operate the vessel. The first voyage between Australia and Japan is scheduled for the second half of this fiscal year.
When the temperature of hydrogen is lowered to -253°C, it liquefies, and the volume is reduced to approximately one eight-hundredth of the gaseous state, which makes storage and transportation more efficient and enables a much greater distribution of hydrogen.
Kawasaki provided the liquefied natural gas (LNG: at -162°C) carriers, storage tanks, receiving terminals, and cryogenic LH2 storage tanks. By assembling its many years of shipbuilding experience and LH2 cryogenic technologies, the Company constructed the first-of-its-kind LH2 carrier. Australia is about 9,000 km from Japan. An LH2 tank with a capacity of 1,250 m3 will be installed on the vessel. The tank is designed with a double-hulled, thermos-like structure, and its design pressure is on the order of five times the standard atmospheric pressure.
Kenjiro Shindo, deputy senior manager of the Hydrogen Project Development Center under the Corporate Technology Division, comments, “The LH2 tanks must have thermal insulation performance ten times greater than that for LNG, and Kawasaki is using expertise gained from manufacturing LNG transport tanks and LH2 tanks at the Tanegashima Space Center.”
He adds, “Because it will be installed on the world's first LH2 carrier, we are carefully considering safety performance, and we have been incorporating safety assessments associated with emergency hydrogen release as part of the development of transport tank-related technologies. LH2 is more evaporable than LNG, and because its molecules are smaller, it leaks more easily. To accommodate such characteristics, we are leveraging the manufacturing expertise gained through LNG tank production, as well as from many other technologies developed for products used everywhere from underground to outer space.”
For the handling terminal that will receive the LH2 from Australia, Kawasaki is building a plant system on Kobe Airport Island to be operated by Iwatani. As with the tanks on the carrier, the key to safety is the insulation and sealing performance of the facilities for unloading LH2 from the carrier into storage tanks. “We developed a technique using double-walled flexible hoses with high insulation and sealing performance compared to conventional steel handling systems used for LNG in order to secure the connection between the swaying LH2 carrier and the onshore storage tank. This will be the world's first pilot test of this innovative approach,” explains Shindo.
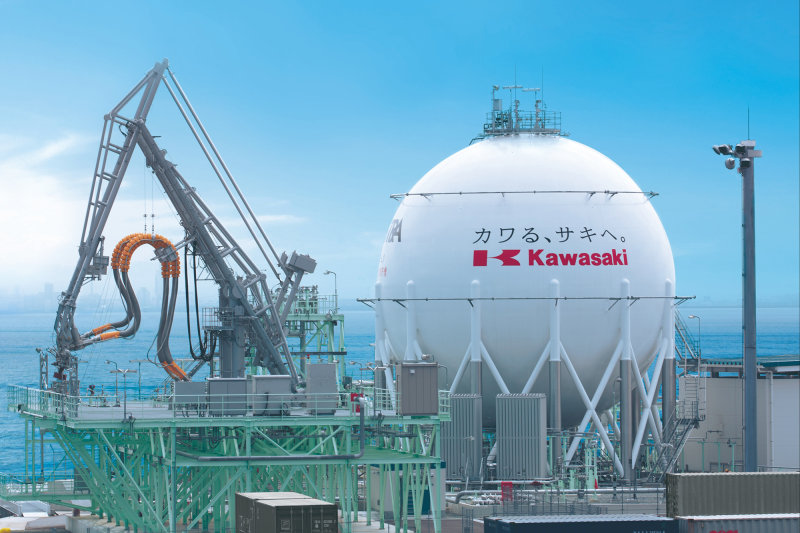
Because mass marine transport of LH2 has never been carried out before, a set of new regulations had to be formulated to ensure safe transport. After many discussions based on proposals from Japan, the International Maritime Organization (IMO) officially approved the safety requirements in 2016 as proposed by Japan.
This means that the building of this pilot vessel, or the first LH2 carrier in the world, will make a technological contribution to the industry and serve to validate the international standards for safe LH2 transport, as well as lead to further establishment of such standards.
“Because the actual carrier is not yet completed, the IMO requirements are interim recommendations. When the pilot vessel is approved as the world's first LH2 carrier and we gain experience operating it, the knowledge will be channeled into the establishment of international rules,” Shindo comments.
On verifying the first of such technologies, HySTRA aspires to achieving commercialized LH2 transport in a manner of safety-first and solid implementation.
Success in Large-scale Hydrogen Power Generation in Urban Areas Demonstrated Plant Capacity and Safe Operation
On April 19 and 20 in 2018, the world's first verification test using a gas turbine fueled by 100% hydrogen was successfully completed for providing both heat and power to urban areas on Kobe's Port Island.
In December 2017, Kawasaki completed the demonstration plant of a 1 MW gas turbine fueled by hydrogen and natural gas, the Hydrogen Cogeneration System (Hydrogen CGS),3 and started its trial run, followed by stand-alone testing of the gas turbine generator using a mixture of hydrogen and natural gas or only hydrogen, as well as verification of providing heat and power using natural gas.
Eventually, the plant successfully supplied electricity and heat (steam and high-temperature water) to four nearby facilities using a cogeneration system (CGS) fueled by 100% hydrogen.
The Kobe City Medical Center General Hospital and Port Island Sports Center were supplied with 2,800 kW of heat while 1,100 kW of electric power was provided to the Kobe International Exhibition Hall and Port Island Sewage Treatment Plant in addition to these two for four facilities in total. At the sports center, hot water was used for the swimming pool, hot-water supply, and heating, while at the hospital, steam was used to supply hot water, heat rooms, and sterilize medical equipment and utensils.
Named the Smart Community Technology Development Project Utilizing Hydrogen Cogeneration Systems, this project to generate heat and power using a hydrogen-fueled gas turbine was implemented as part of NEDO's Technology Development for the Realization of a Hydrogen Society program. The aim was to develop and verify an energy management system (integrated EMS) that enabled optimal and efficient use of electricity, heat, and hydrogen energies by users in the community.
This project, in which Kawasaki is responsible for providing a gas turbine, a power generator, and a boiler, and Obayashi Corporation developed the integrated EMS, was followed by a series of similar supply tests.
Mitsugu Ashikaga, deputy senior manager of the Project Control Department for the Hydrogen Project Development Center under Kawasaki's Corporate Technology Division, comments, “The mission of the test was to collect data associated with gas turbine performance, which changes seasonally due to variable demand, and to establish control techniques for the integrated EMS. The collected data and its analyses are essential in gaining sophisticated and practical expertise.”
Kawasaki developed the gas turbine used for the project, which allows the use of either hydrogen or natural gas alone, as well as flexible adjustment of any hydrogen/natural gas combustion ratio.
When only hydrogen is used, the temperature of the flame is high and the flame is easily spread out, which results in burner damage and emissions of nitrogen oxide (NOx). Kawasaki resolved these problems by developing a fuel injection valve with a novel shape and adopting a method through which water and fuel are injected together. Ashikaga says, “The most significant achievement of the verification test was that we were able to verify that hydrogen energy could be used safely in a community setting.” Robust design and construction methods are applied not only to the gas turbine but also to the entire plant, which assures that at both plant capacity and operational safety levels, practical power generation for large-scale facilities using hydrogen is possible.
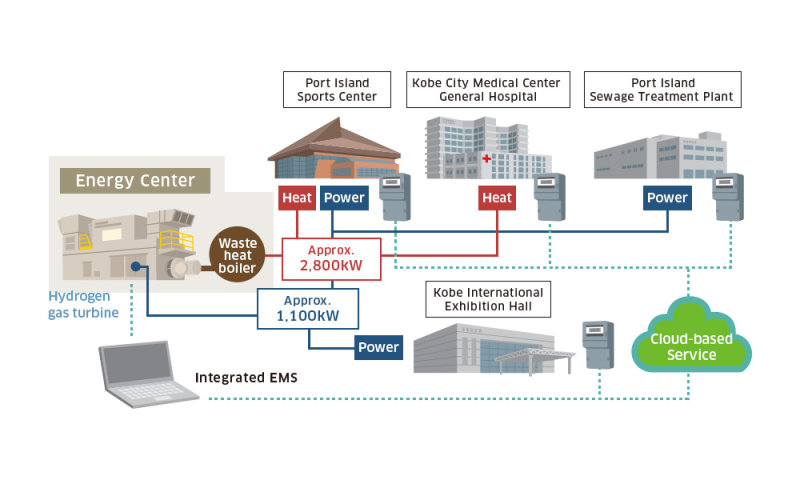
Kawasaki aims to build a hydrogen energy supply chain in four phases: utilization, transportation, storage, and production. Not only development of its own company but also advancement of technological innovations by involving many players, including other firms, governments, and specialized agencies in Japan and overseas, enables a carbon-free and low-carbon society and continued economic growth at the same time, which is exactly the appeal of hydrogen energy. Realization of a carbon-free society, energy security in Japan, and compatibility with the environmentーsuch a safe, fruitful future may be just around the corner.
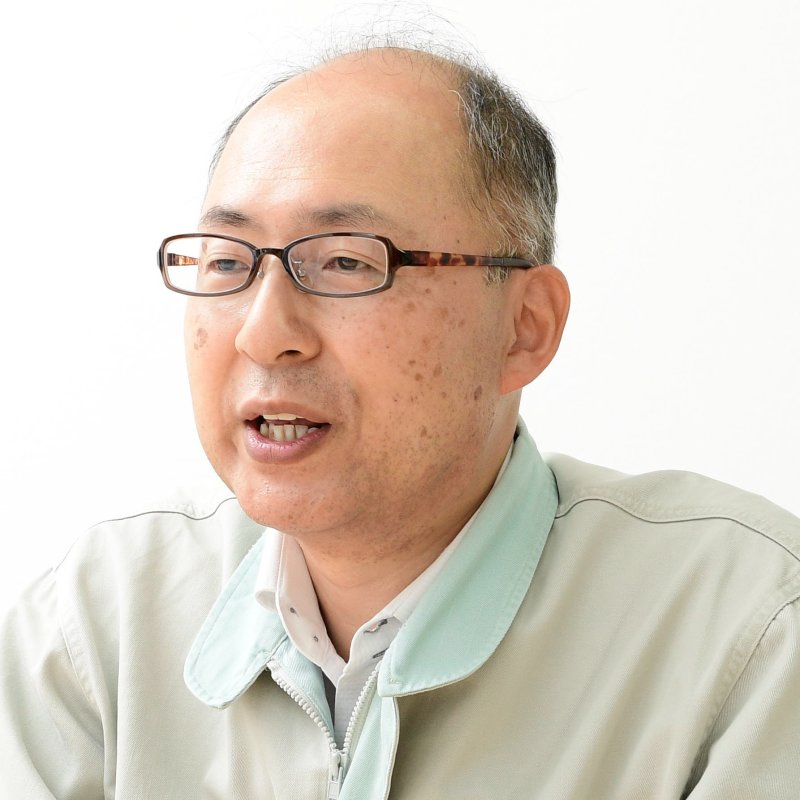
Project Promotion Department
Hydrogen Project Development Center
Corporate Technology Division
Kawasaki Heavy Industries, Ltd.
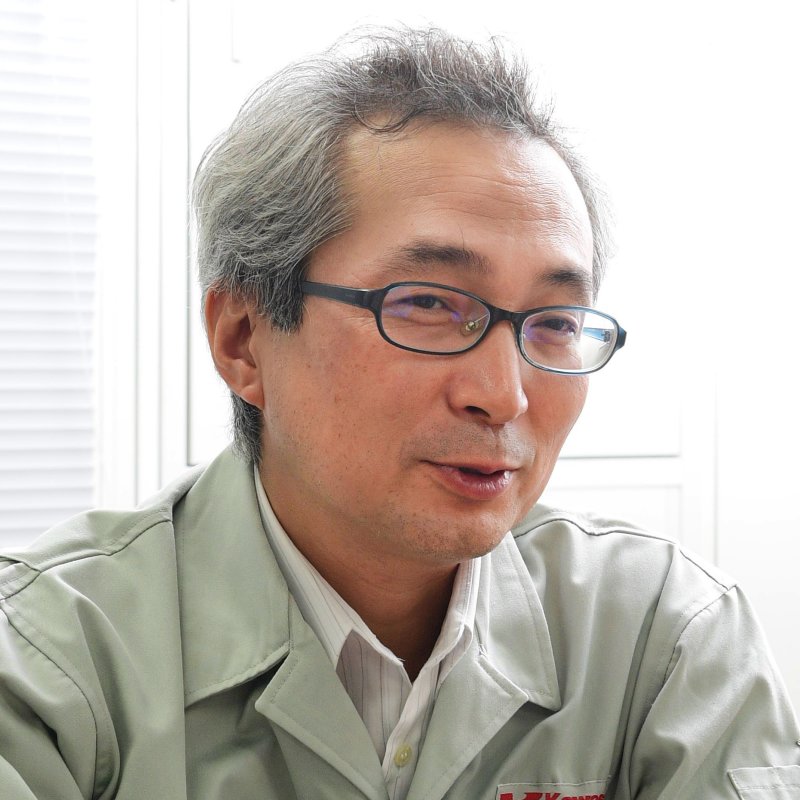
Project Control Department
Hydrogen Project Development Center
Corporate Technology Division
Kawasaki Heavy Industries, Ltd.
Note: The numerical values and job titles stated herein are based on information as of July 2018