Kawasaki’s Floor Conversion System: Using Air Technology Supports the Stages of Athletic Victories
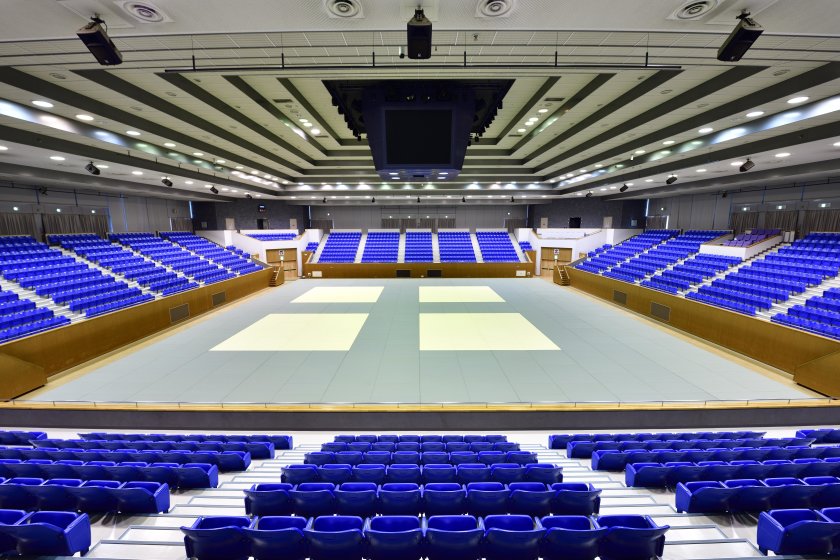
Today, a wide range of people enjoy a variety of sports, and Kawasaki’s “air technology” is facilitating this trend, supporting the operators of sports venues by broadening the uses of their facilities.
Where Japanese Martial Arts Flourish, the World’s First Floor Conversion System Is Applied
Himeji City in Hyogo Prefecture is famous for Himeji Castle, a UNESCO-listed World Cultural Heritage site. It is also reputed to be a place where Japanese martial arts flourish, even more than other cities in the prefecture, which has produced many notable martial arts experts. Himeji-born artists include Mikinosuke Kawaishi, who was entrusted with the mission of popularizing judo in France by Kodokan Judo Founder, Jigoro Kano (Kobe-born), and who later became known as “the Father of French Judo,” and Kyutaro Takahashi, the “Swordsman of the Meiji Era.” And the venerated swordsman of the Edo period, Musashi Miyamoto, had a close association with the head of the Himeji Domain.
Given these connections, it is not surprising that the Hyogo Prefectural Government chose Himeji as the location for its WINK Budokan (Hyogo Prefectural Budokan [Martial Arts Hall]) in 2002.
Of the two dojos (practice halls) in this facility, Dojo No. 1 is equipped with the world’s first automated floor conversion system which lays tatami (straw mats) for judo on top of the Japanese cypress floor used for kendo (Japanese swordsmanship).
Using this system, conversion from a kendo hall to a judo hall with four judo rings, which meets international competition standards, takes just 40 minutes. In the conversion process, a base of 32 tatami mats (each mat being about 1.8 x 0.9 m/5.9 x 3.0 ft), called a “tatami unit,” is brought in on two automated guided vehicles (AGVs), with four tatami units completing one judo ring. Since the venue consists of four rings (16 tatami units), a total of 512 mats are used.
Converting kendo halls to judo halls by laying down tatami mats is a common practice, but it has always been labor-intensive, time-consuming, and costly. It is estimated that converting a regular martial arts hall into a judo hall that meets international competition standards, which require the hall to have a 50 cm high base, takes 10 workers two days, costing five to 10 million yen (about US$46,750–93,300).
For the operators of large public facilities, such as the WINK Budokan, having flexibility in the way the venue is used is key to achieving sustainable operations, and Kawasaki’s floor conversion system provides a solution which contributes greatly to efficiency.
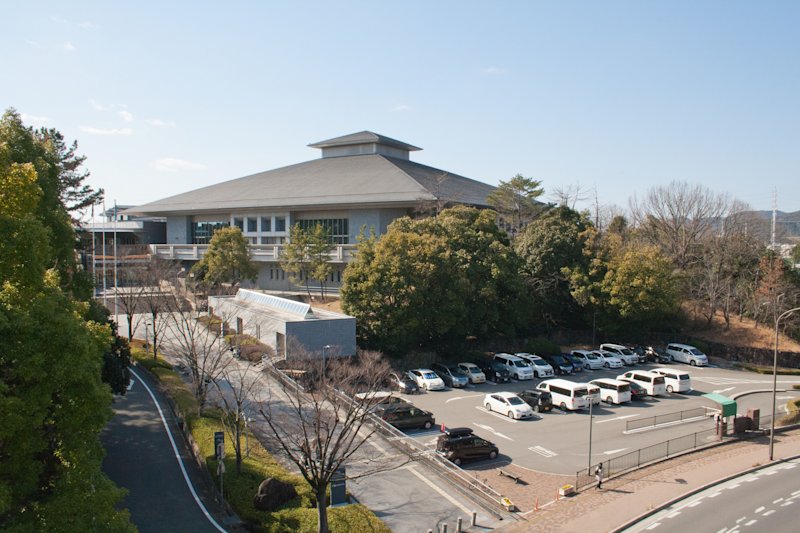
Director of the WINK Budokan, Nijo Kobayashi, comments, “While we were preparing for construction of the Budokan, Kawasaki provided a solution for our need for an automated system which achieves both effective operations and the size and level of facility required for international competitions. When the Budokan opened, people called the conversion system ‘a magic carpet’.”
The power of air is at play in this system. In 2001, Kawasaki delivered a “Hovering Stage” (a movable natural grass football pitch) to Sapporo Dome, which can be moved into and out of the stadium using pneumatic flotation technology for moving heavy objects. This system made the stadium operator’s dream of hosting the 2002 FIFA World Cup come true. Another innovation contributing to this floor conversion system is an “air-raising method” that Kawasaki makes use of, in which the roof structures of liquefied natural gas (LNG) above-ground tanks are assembled at the bottom of the tanks and then raised using air.
Moreover, technology for the Flow Dynamics Conveyor (FDC), a long-lasting, high-speed, long-distance, air-supported belt conveyor, and other air-supported inventions were incorporated in the development of the Budokan’s floor conversion system.
Nearly twenty years after its installation, a six-month project to renew the system began, and was completed in March 2020. Not only its aging parts but also its control system was replaced, as a result of which an improvement in the conversion speed was achieved.
Let’s take a look at Kawasaki’s technology which achieved the world’s first floor conversion system using the power of air.
A Heavy Base Is Elevated and Moved Using AGVs
The floor conversion system is comprised of four components: 1. Tatami units (elevatable bases holding tatami mats), 2. AGVs that move and align the tatami units to create judo rings, 3. Storage lifters for tatami units and AGVs, and 4. Control equipment and panels for these components.
Each tatami unit is about 15 m (W) x 4 m (D) x 0.5 m (H) and weighs about 4.5 t. It is impressive that air can lift such a huge object.
Under the tatami unit, a balloon-like bag (called an “air mat”) with myriads of holes on the bottom is installed, and when air is injected into the bag by a blower, the bag swells and elevates the unit about 40 mm. As the air then escapes through the holes, a layer of air beneath the bag is also created, reducing the friction between the tatami unit and the floor to one thousandth.
Osami Oogushi, who was involved in the development of the system and was in charge of the renewal project, says, “The floor for kendo, which is made of Japanese cypress, is so soft that if a carpenter’s square is dropped, it can stick. We therefore designed the tatami units and the AGVs with utmost care so that they do not damage the cypress floor and that safety is ensured for kendo players who fight barefoot.”
Each tatami unit is moved and aligned by a set of two AGVs, which slide under the unit and insert connecting pins into it so that the unit and the AGVs move together. At the same time, the AGVs provide power to the unit’s blower. The elevated unit is then moved to the desired spot by the AGVs, which have tires that allow both forward/backward and left/right motion.
The layout of the units varies depending on how many judo rings are to be installed. The AGVs run on designated routes, guided by magnetic tracks and stop markers embedded in the floor which send commands to the AGVs, such as “stop in another 5 cm.” This explains why they are officially called “magnetically guided automated vehicles.”
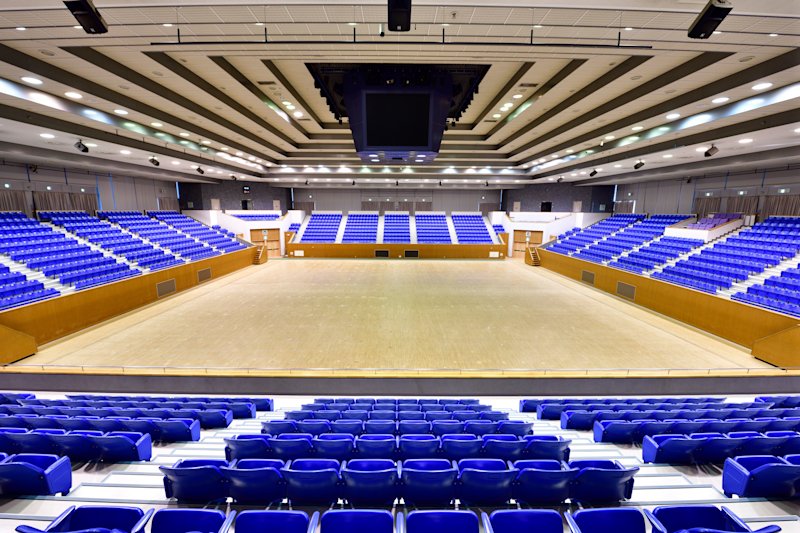
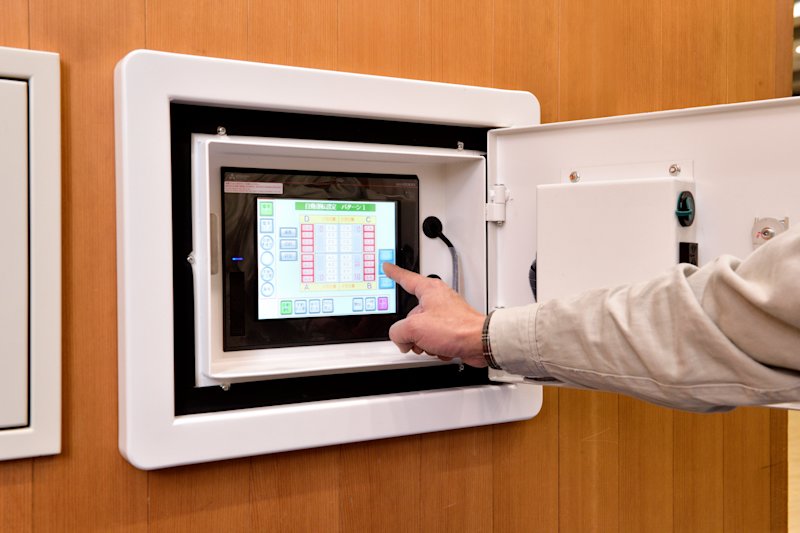
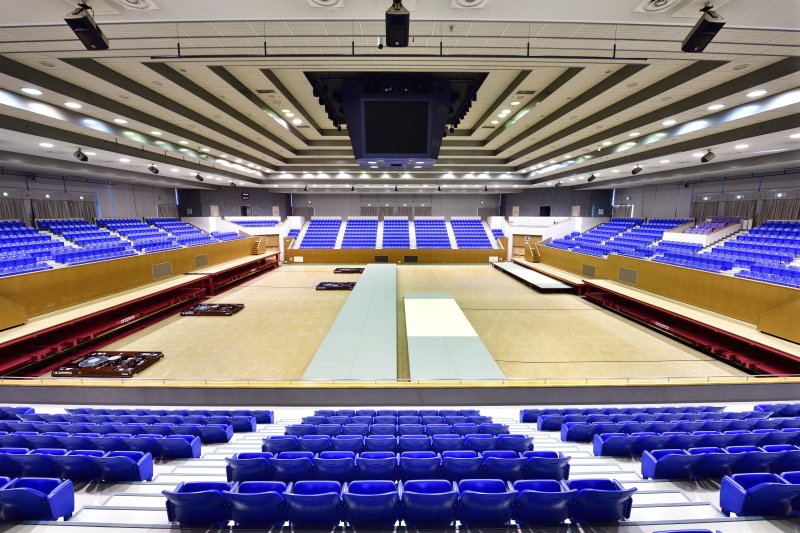
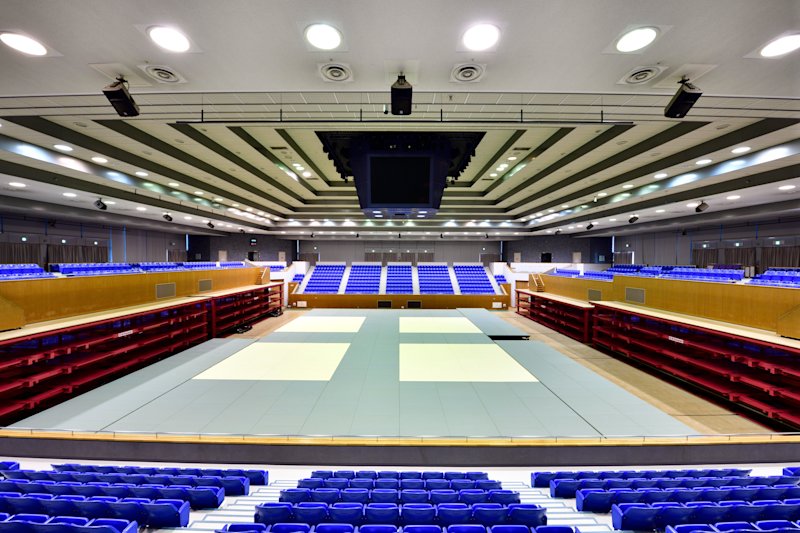
Two AGVs Move in Perfect Coordination
Although the AGVs are guided magnetically, Oogushi says, “The most challenging aspect of using the AGVs in moving and aligning the tatami units is that they have to move in perfect coordination, which we call ‘a-un (harmonious) breathing’.”
Because they are transporting a 15 m long unit, even a slight discoordination can result in a major misalignment. To prevent this, Kawasaki developed a control technology that allows the AGVs to recognize each other’s position using optical communication and move in parallel with each other ― the “a-un breathing” technology.
Oogushi adds, “This technology realizes gapless alignment of the tatami mats, thanks to a level of precision which achieves a less than 5 mm difference between the AGVs every time they come to a stop, and a mechanism which ensures that the units are fastened tightly together.”
Another feature contributing to efficient floor conversion is the storage lifter (lifting shelf) used to house the tatami units and AGVs. There are four storage lifters in the hall, with two each installed on opposite sides. This means that 16 units and eight AGVs can be hidden in four locations under the arena floor.
Weighing 40 t, a lifter is a 4-shelf structure that can hold 21 t worth of tatami units and AGVs. Because the height of each shelf of the lifter must align with the cypress floor when the tatami units and AGVs are being loaded/unloaded (around 60 t when the lifter is fully loaded), Kawasaki developed a positioning system to adjust the lifter to the perfect height.
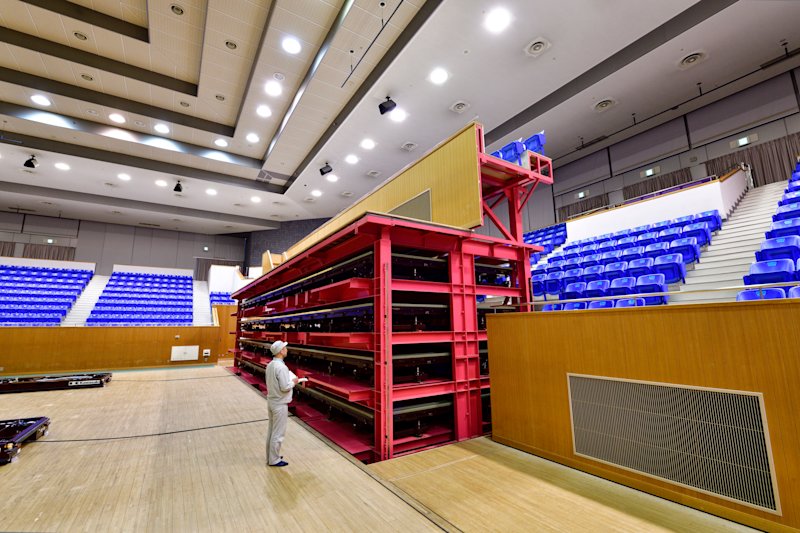
The position and status of the tatami units, AGVs, lifters, and other equipment are controlled in real time via wireless communication, and by moving multiple pieces of equipment simultaneously, the system deploys and stores the tatami units in the shortest time possible.
Oogushi comments, “It was quite meaningful to develop this floor conversion system because it helped us establish technologies for creating heavy structures, elevating them using air, and controlling them to a millimeter level of precision. We can apply the system to transport other heavy objects from place to place, which is a significant labor-saving contribution.”
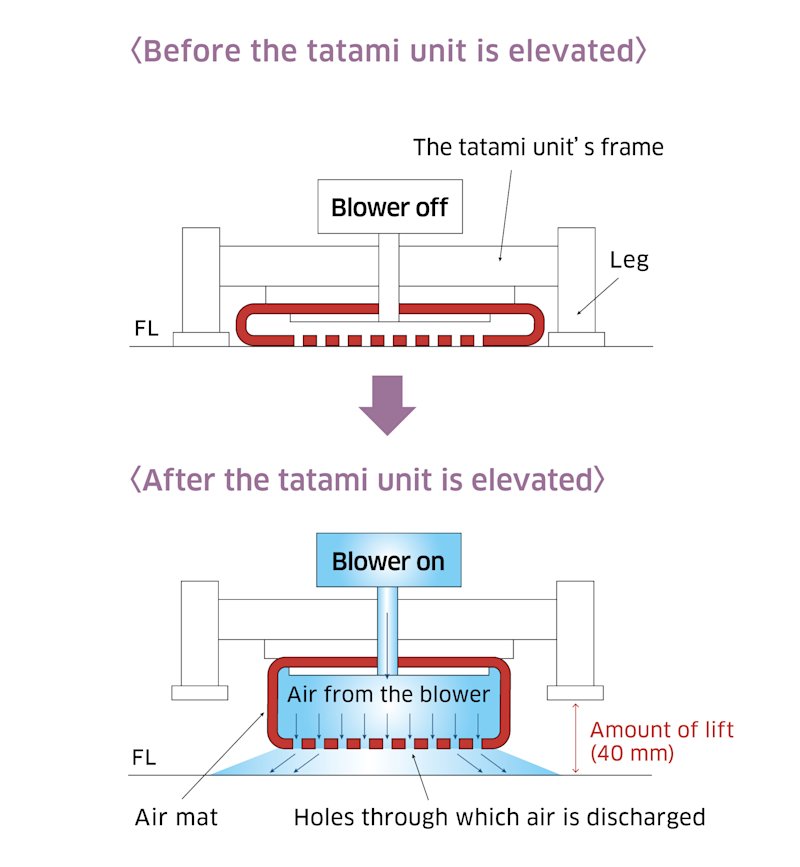
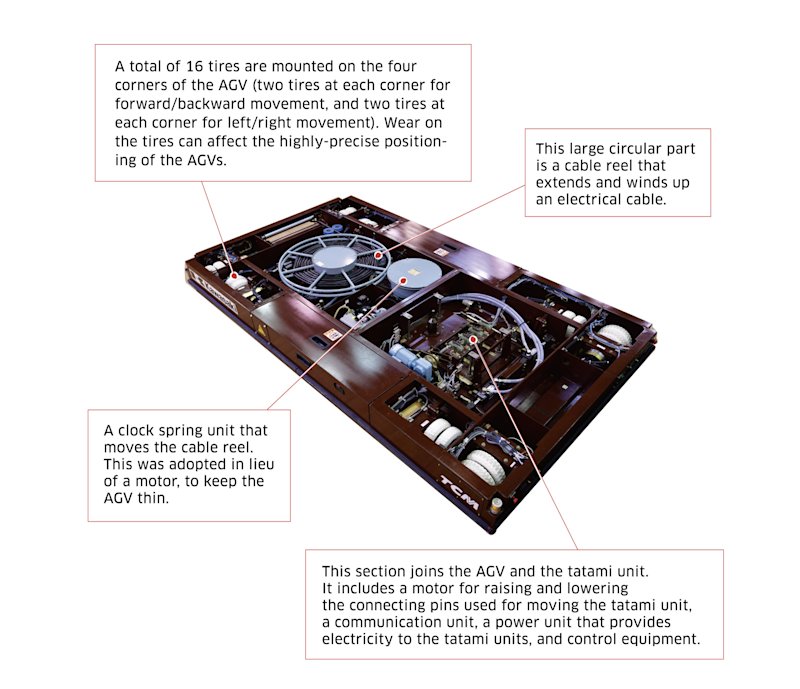
A System that Accommodates Diverse Sports Requirements
Kawasaki has been making efforts to develop new customers for this floor conversion system, as some of the 48 public martial arts halls in Japan opened more than 40 years ago and are failing to meet the wide range of local sports needs.
Yoshitaka Honda, from the sales department in charge of marketing air technology products at Kawasaki, says, “Considering the scale of floor conversion systems, incorporating one requires Kawasaki to be involved in the project even before the designing process begins. Despite such a requirement, some public entities are already showing interest in the system.”
Emphasizing the value of the technology in enabling facility operators to effectively increase the availability of sports for local residents, Honda says, “The use of technologies which utilize the power of air, such as the floor conversion system, greatly enhances a facility’s operating rate and saves a significant amount of labor. It therefore contributes to the effective management of the facility.”
Kawasaki’s air technology is supporting the “stage of victory” for athletes in a city closely associated with Japanese martial arts. It is also meeting the desires of facility operators to enrich people’s lives through sports, and to support athletes in winning victories.
Kawasaki’s Pneumatic Flotation Technology Supports Centers for Sports Promotion in Snowy Regions
The Sapporo Dome, which is located in snowy Hokkaido Prefecture, is an all-weather, multipurpose facility used for professional baseball games, J.League football matches, concerts, motor shows, etc. Launched in 2001, the stadium is equipped with a natural grass football field called the “Hovering Stage,” which can be moved using Kawasaki’s pneumatic flotation system.
The football field ("stage"), which normally resides in the outside arena (right photo), is transferred to the inside arena when such events as home matches of the professional football club, Hokkaido Consadole Sapporo, are held. In regard to the baseball field, the stands behind center field can be moved and the wall opened to bring the stage into the inside arena (photo above). The stage is then rotated 90 degrees so that the stands behind the backstop, where the number of spectator seats is the largest, become the grandstand.
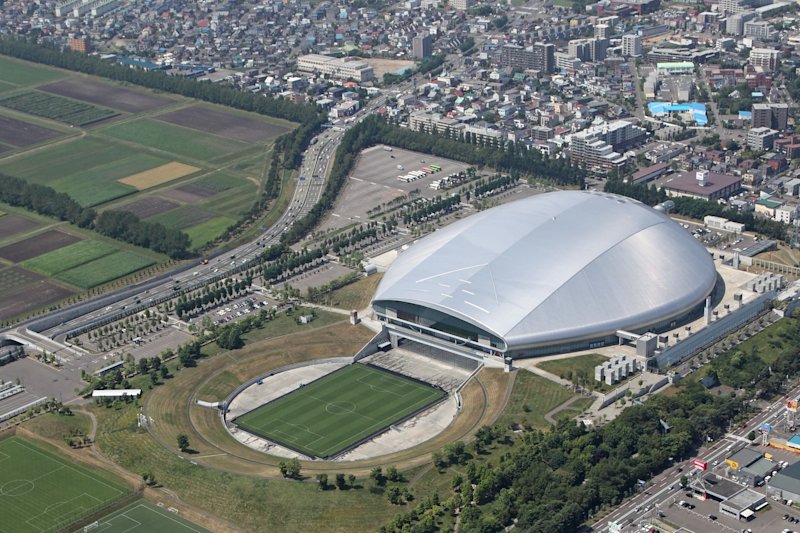

Pneumatic pressure is at play when moving the stage. Pressurized air is pumped into the space directly below the stage and, at the same time, tubular bags (bug seals) which are installed under the four edges of the stage are inflated, trapping the air and creating upward pressure (see illustration below). This pneumatic pressure lifts the 8,300 t, 120 m x 85 m stage, reducing its dead weight to one-tenth.
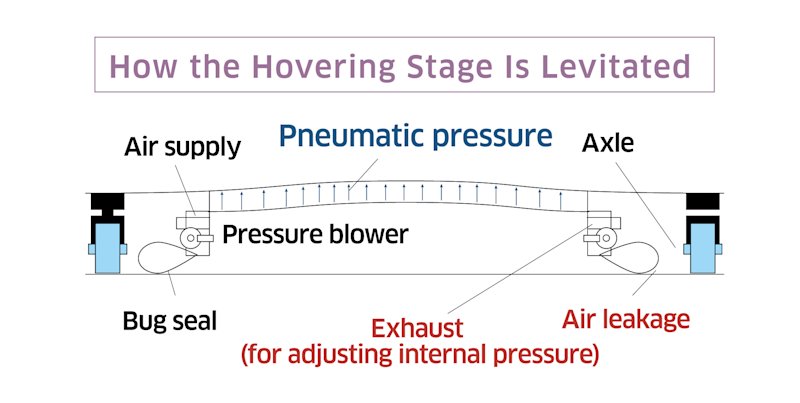
Next, 34 wheels around the outer periphery of the stage are hydraulically extended down to the ground, and the stage is carried straight into the inside arena, guided by the same magnetic guidance system as that used in the WINK Budokan. The amount of air leaking from minute gaps between the bug seal and the ground varies according to the unevenness of the ground, but this exhaust air is controlled in order to maintain a consistent pneumatic pressure. It takes about two hours to move and rotate the Hovering Stage.
Tatsuo Tomono, Senior Staff Officer of the Plant Engineering Business Division, who developed the Hovering Stage, comments, “The Hovering Stage was used for both the 2002 FIFA World Cup at Sapporo Dome, which was co-hosted by Japan and South Korea, and the Rugby World Cup 2019. I’m sure it will be a stage for many more sports events. Hokkaido residents are very happy that Sapporo Dome is allowing them to enjoy indoor sports even during the winter, making the stadium a symbol of sports promotion in Hokkaido. I feel very proud that Kawasaki’s technologies are supporting the operation of the stadium.”
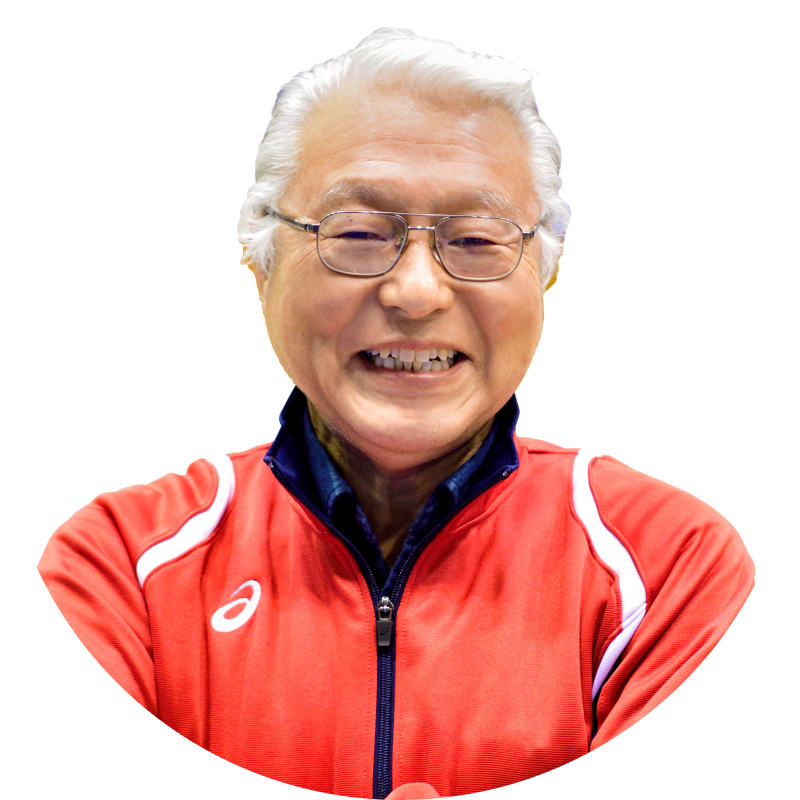
WINK Budokan
Flexible Conversion of Sports Halls Provides Facility Operators with Managerial Efficiency and Competitive Advantages
Opened in 2002, the WINK Budokan has been serving as a center for promoting and developing martial arts, the wellness and fitness of prefectural residents, and a life-long involvement in sports.
It is used mainly for 11 types of martial arts, including judo, karate, and naginata (glaive fighting). Our dojo halls are two of the largest in Japan that meet international competition standards. We enjoy a high operating rate, with various competitions held on weekends and mainly martial arts classes on weekdays.
For effective facility management, it is vital that martial arts halls be designed for multipurpose use. The floor conversion system in Dojo No.1, in particular, is a major contributor to the highly efficient running of the facility. Because conversion from the regular floor to the tatami-covered version and vice versa takes only 40 minutes, we have flexibility in planning our event schedule. Ever since I assumed the post of the Budokan’s eighth director in 2018, I have been committed to using this superior resource to our advantage in facility management.
During the renewal project, I observed Kawasaki engineers’ painstaking attention to their work, indicating a passion for their technology, while rigorous self-discipline is practiced in meeting the timeline. I feel that such an approach fits harmoniously with our desire to foster self-control through martial arts.
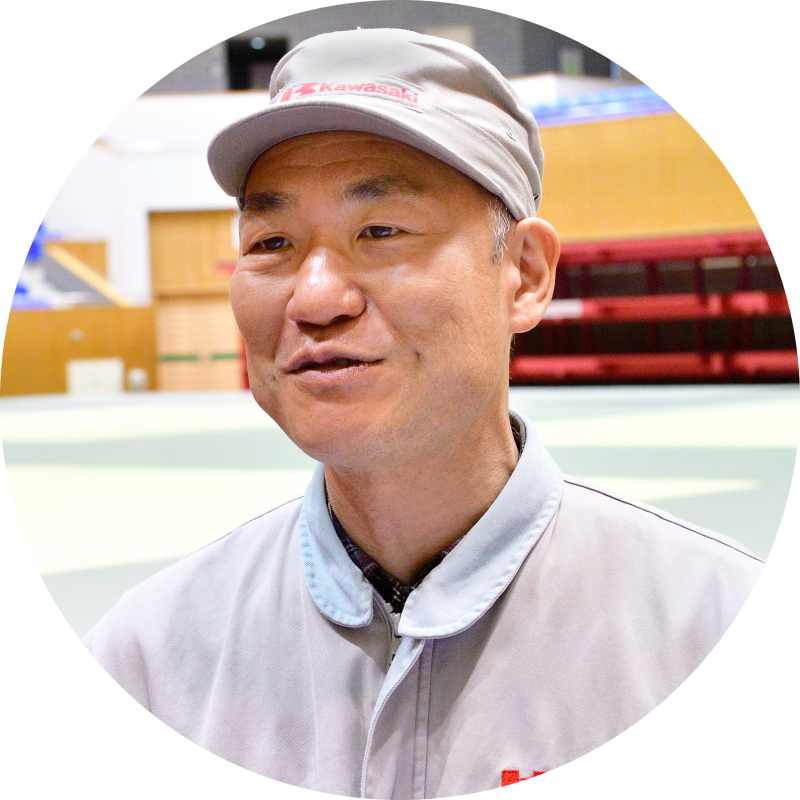
Engineering Section 1
Materials Handling Dept.
Industrial Machinery Group
Plant Engineering Business Division
Energy System & Plant Engineering Company
Kawasaki Heavy Industries, Ltd.
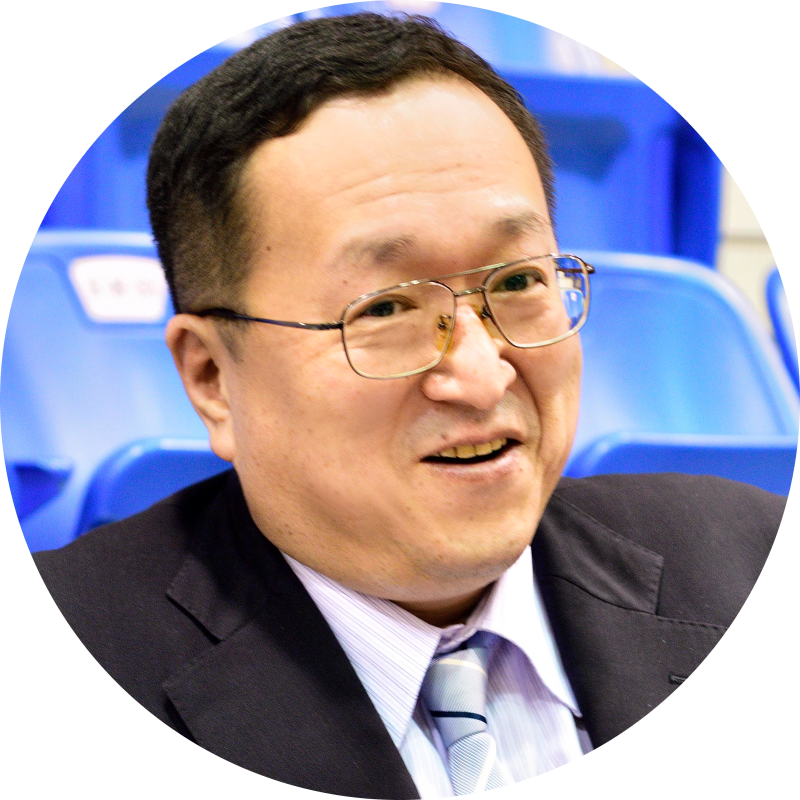
Domestic Plant Sales Dept.
Marketing & Sales Division
Energy System & Plant Engineering Company
Kawasaki Heavy Industries, Ltd.
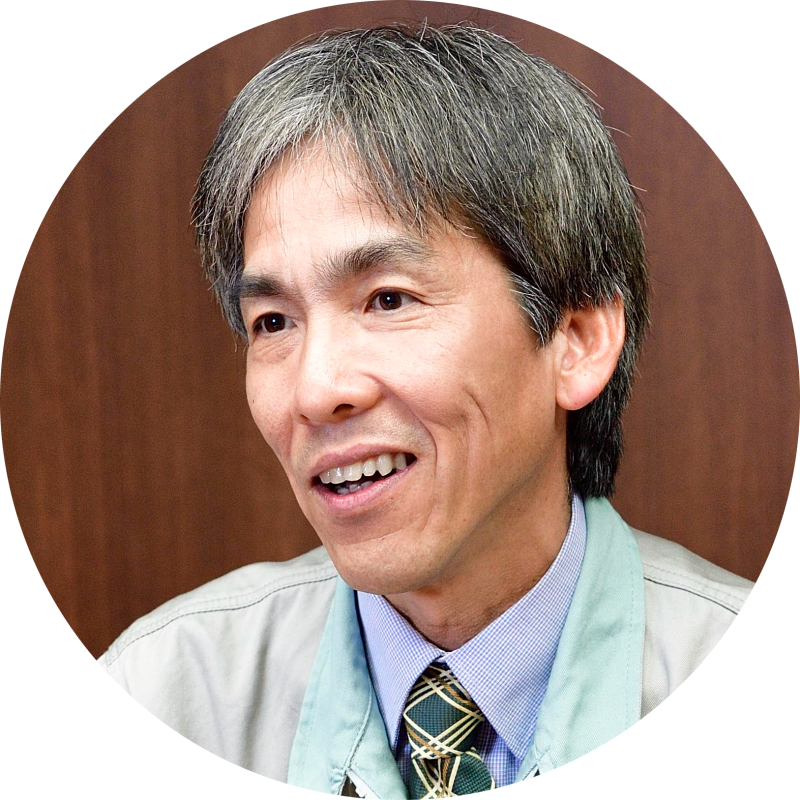
Engineering Section 1
Materials Handling Dept.
Industrial Machinery Group
Plant Engineering Business Division
Energy System & Plant Engineering Company
Kawasaki Heavy Industries, Ltd.