Kawasaki’s Century-Old Business Takes on New Fields
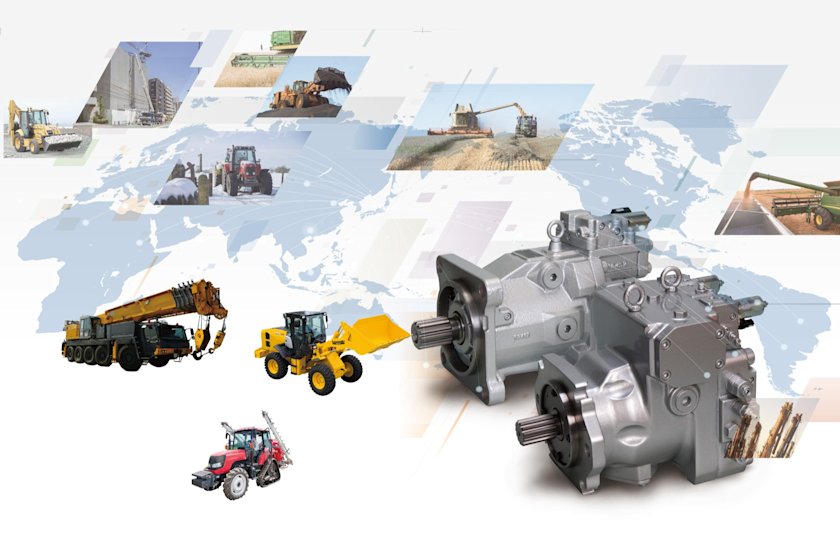
Kawasaki’s hydraulic equipment business has set out toward its next centennial. A global leader in hydraulic equipment for excavators, the company is now seeking to build on its success by making inroads into new fields. A new innovation for work vehicles is just around the corner.
Tackling HST and Other New Fields
Construction machinery such as hydraulic excavators is the quintessential example of a work vehicle. The first hydraulic excavator made entirely in Japan—Hitachi’s (now Hitachi Construction Machinery) UH03—was developed back in 1965.
In developing the UH03, Hitachi commissioned Kawasaki to develop hydraulic motors for the travel and swing devices. After much trial and error, Kawasaki produced and delivered three hydraulic motors—left and right travel motors and a swing motor.
In the half-century since then, Kawasaki has become the world’s leader in hydraulic pumps and motors for excavators and earned the overwhelming support of customers. And this year marks the 100th year since Kawasaki entered into a technological partnership on a radial piston pump for a steering gear at Kawasaki Dockyard Co., Ltd. (now Kawasaki’s Kobe Shipyard) in 1916.
At this milestone, Kawasaki’s hydraulic equipment business has embarked on a challenge in a new eld. For the first time, Kawasaki began supplying products in the eld of industrial vehicles equipped with a hydrostatic transmission (HST). HST uses a closed circuit to continuously change the gear ratio only by controlling the displacement of a hydraulic pump and hydraulic motor. Examples of vehicles that use a closed-circuit hydraulic system include wheel loaders and tractors. The first products to be released in this category are the K8V series of swash plate type HST pumps and the M7V series of swash plate type axial piston motors.
World’s Top-Level Performance, Achieved with a New Method
Hydraulic pumps that provide the energy to drive motors and cylinders through hydraulic pressure come in two types: one for an open circuit, and the other for a closed circuit. While hydraulic excavators employ an open-circuit system, a continuously variable HST consists of a closed-circuit system.
In an open-circuit system, hydraulic fluid leaves the tank and flows through a pump, valve, and motor (cylinder) before it returns to the tank. In a closed-circuit system, on the other hand, hydraulic fluid is circulated between a pump and motor (see Fig. 1). Although a closed circuit is simple in structure, the pump must be fitted with various features, such as a charge pump for replenishing hydraulic fluid.
Structures of Pump and Motor
At this milestone, Kawasaki’s hydraulic equipment business has embarked on a challenge in a new eld. For the first time, Kawasaki began supplying products in the eld of industrial vehicles equipped with a hydrostatic transmission (HST). HST uses a closed circuit to continuously change the gear ratio only by controlling the displacement of a hydraulic pump and hydraulic motor. Examples of vehicles that use a closed-circuit hydraulic system include wheel loaders and tractors. The first products to be released in this category are the K8V series of swash plate type HST pumps and the M7V series of swash plate type axial piston motors.
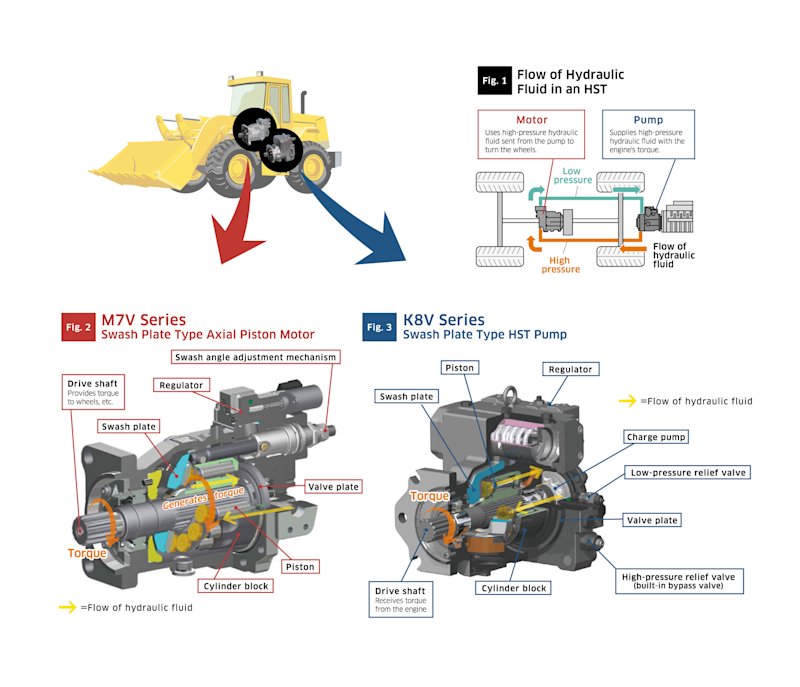
Closed-circuit hydraulic equipment is adopted in various industrial vehicles. The biggest market, however, is industrial vehicles provided with an HST drive system, which include wheel loaders, tractors, and forklifts. As such, motors used in a closed-circuit system require high speed and high torque capabilities, as well as a pump for generating force.
K8V pumps supply hydraulic fluid at a pressure of 40 MPa. They not only boast the world’s top-level pump efficiency, which impacts the vehicle’s fuel efficiency, but also achieve low noise and high reliability, responding to the needs of industrial vehicles.
M7V motors receive the force of hydraulic pressure generated by a K8V pump to produce high speed and high torque. Compared to a motor for hydraulic excavators, which is capable of operating at approximately 2,000 rpm, a motor for HST can run at 5,000 rpm, nearly doubling the power density (power per unit weight).
Closed-circuit hydraulic equipment is adopted in various industrial vehicles. The biggest market, however, is industrial vehicles provided with an HST drive system, which include wheel loaders, tractors, and forklifts. As such, motors used in a closed-circuit system require high speed and high torque capabilities, as well as a pump for generating force.
K8V pumps supply hydraulic fluid at a pressure of 40 MPa. They not only boast the world’s top-level pump efficiency, which impacts the vehicle’s fuel efficiency, but also achieve low noise and high reliability, responding to the needs of industrial vehicles.
M7V motors receive the force of hydraulic pressure generated by a K8V pump to produce high speed and high torque. Compared to a motor for hydraulic excavators, which is capable of operating at approximately 2,000 rpm, a motor for HST can run at 5,000 rpm, nearly doubling the power density (power per unit weight).
The Art of Controlling Oil
As illustrated in Figs. 2 and 3, swash plate type pumps and motors are like twins. Both have common technological challenges as well as their respective challenges.
Common technological challenges include high-speed rotation, high pressure, large swash angle, and weight reduction. These challenges are actually closely related. Masaki Ohnishi, Senior Manager of the Engineering Division of Precision Machinery Company, explains as follows.
“By increasing speed and torque, the amount of heat generated will inevitably increase as well, which means that sliding components where parts rub against each other must use materials with greater heat resistance. So our job begins with choosing the right materials, enhancing the dimensional accuracy of parts, and increasing surface hardness. We also need to adjust the balance of hydraulic pressure to ensure the shaft remains steady when rotary components such as pistons and a cylinder block rotate. Although we can increase the power density by increasing the swash angle of the swash plate, that presents another challenge in constructing the internal structure.”
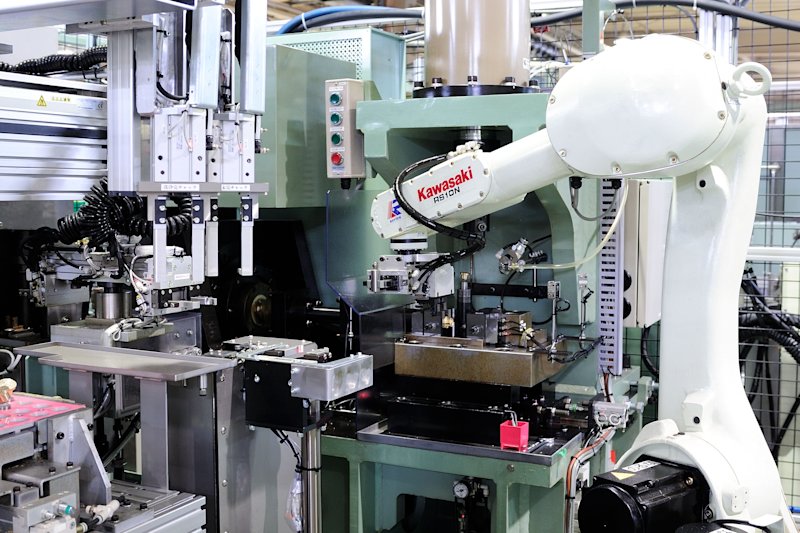
Despite these challenges, the K8V series achieves the world’s highest pump efficiency and low noise. To increase efficiency, both the clearance between the cylinder block and pistons and frictional force were minimized. By using highly heat-resistant piston materials to reduce the clearance, the amount of hydraulic fuluid leaking from the clearance can be reduced. This will enable the pump to supply hydraulic fluid more efficiently, and high power can be ensured even when the pump is reduced in size.
To reduce noise, the shape of the valve plates that control the timing at which pistons take in and discharge oil was re-examined. Noise is generated as a result of the pressure change that occurs inside the piston chambers. Thanks to the newly redesigned valve plates, the timing in which hydraulic fluid is taken in and discharged was optimized.
Ryosuke Kusumoto, who was responsible for the development of K8V pumps, says, “To enhance reliability, a system called a slide bearing is used for the swash plate’s support structure. This system is notable for its ability to absorb strong shock, and because it is supported by the oil film pressure of the fluid, theoretically it can operate semi-permanently. It is one of the main features of K8V that we take special pride in.”
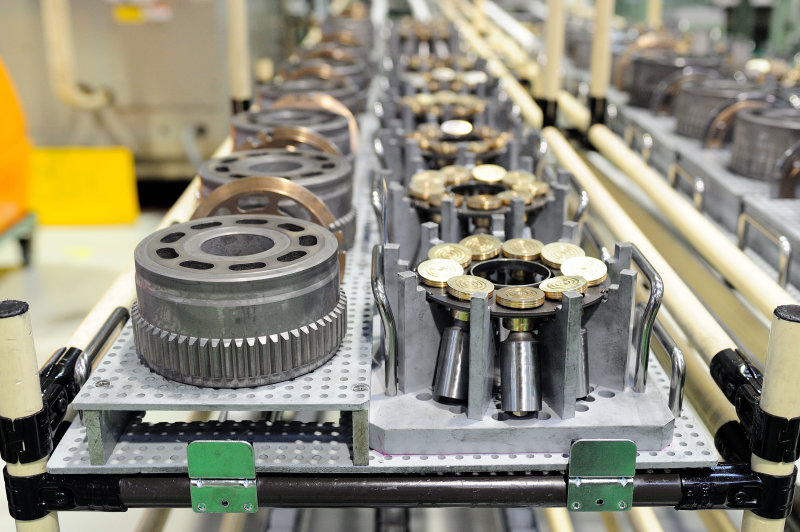
Development Supported by Advanced Measurement & Analysis Technologies
In the development of M7V motors as well, there were technological challenges to overcome in realizing a high-speed and high-torque swash plate type motor. Kouichi Komada, who was in charge of development, says, “Because HST travels at 40 to 50 km/h, 5,000 rpm was a prerequisite. But the significance of this challenge was in achieving this with a swash plate type motor.”
As with the pump, a high-speed, high-pressure motor is subject to high heat. For this reason, materials with high resistance to heat and pressure were chosen, and the surface of the materials was heat-treated.
The key to realizing high speed and high torque was stabilizing the cylinder block. When pistons are pushed out by hydraulic pressure and come into contact with the swash plate, they slide along its slanted surface. This motion generates torque. Accordingly, the positions of the cylinder block in which pistons are lined up must be stabilized in order to achieve high-speed rotation and high torque.
Komada explains, “To optimize hydraulic pressure balance, we fully redesigned the pistons, cylinder block, and other rotary components, and thoroughly reexamined the shape and other aspects down to the smallest detail.”
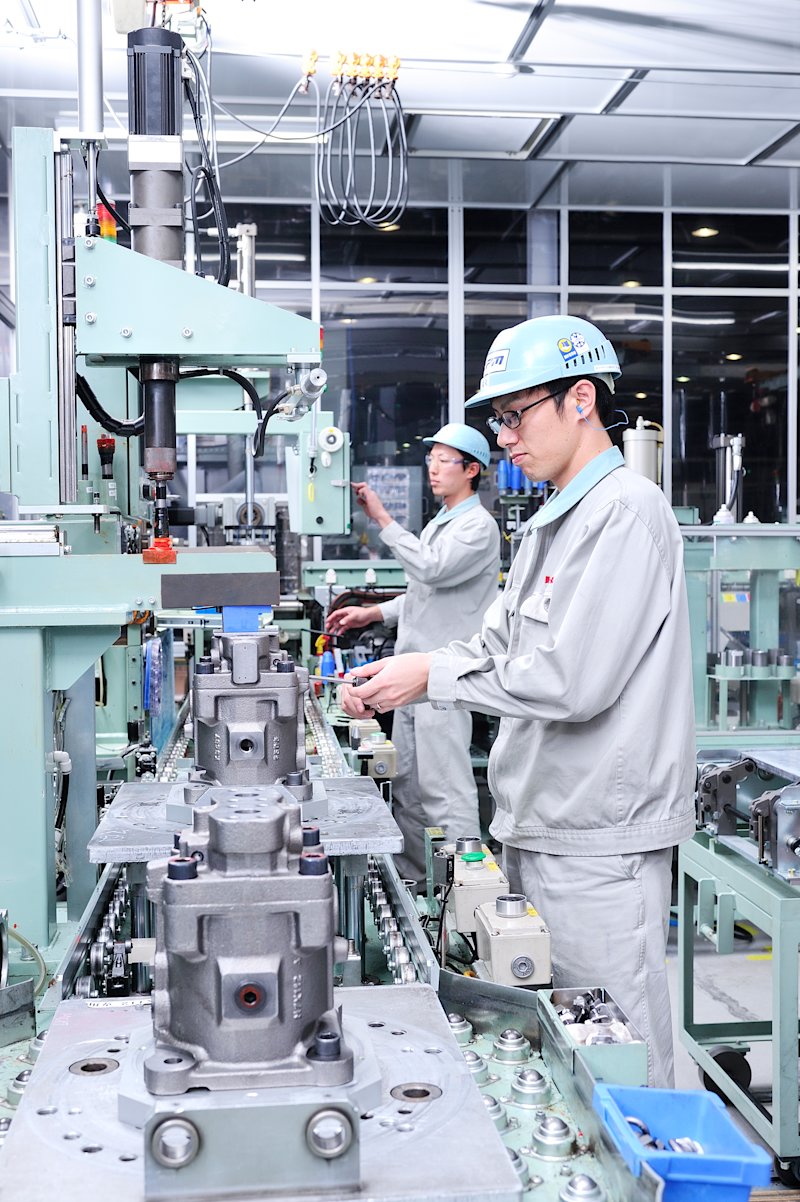
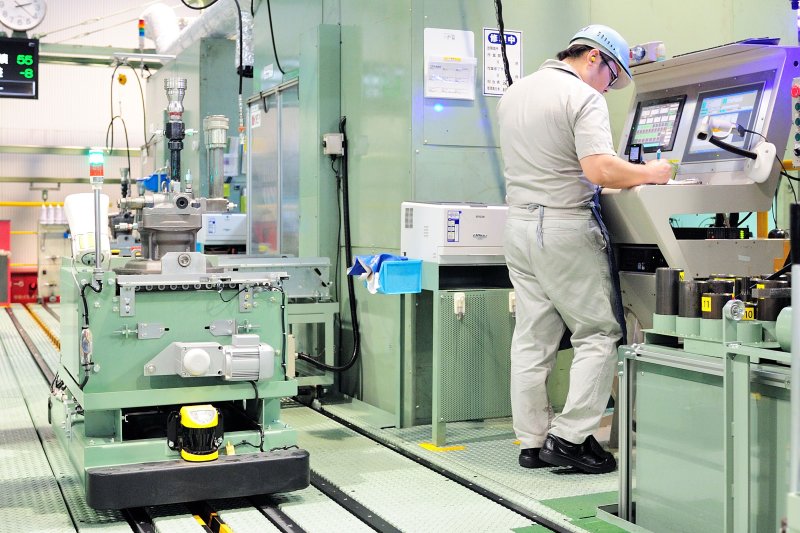
In developing pumps and motors, measurement and analysis technologies play a crucial role. In the case of pumps, for example, their efficiency is determined by volumetric efficiency multiplied by mechanical efficiency. Volumetric efficiency takes account of the loss of hydraulic fluid that leaks from clearances between parts, etc. Mechanical efficiency takes account of the loss of power caused by the sliding movement of parts and the agitation of hydraulic fluid inside the device. To improve the efficiency of both, technologies to measure the amount of losses accurately and analytical technologies to theoretically explain why the losses have occurred are needed.
These technologies were supplied by Kawasaki’s Technical Institute, Corporate Technology Division. K8V pumps and M7V motors were developed using the uid analysis technology Kawasaki cultivated through the development of aircraft and rolling stock.
Ohnishi says, “Rotary components such as pistons and cylinder blocks are the core elements of pumps and motors. The ability to accurately achieve the optimum shape obtained through measurement and analysis shows the manufacturing capabilities of the Nishi-Kobe Works. This is truly a technological innovation accomplished through the collective strengths of Kawasaki.”
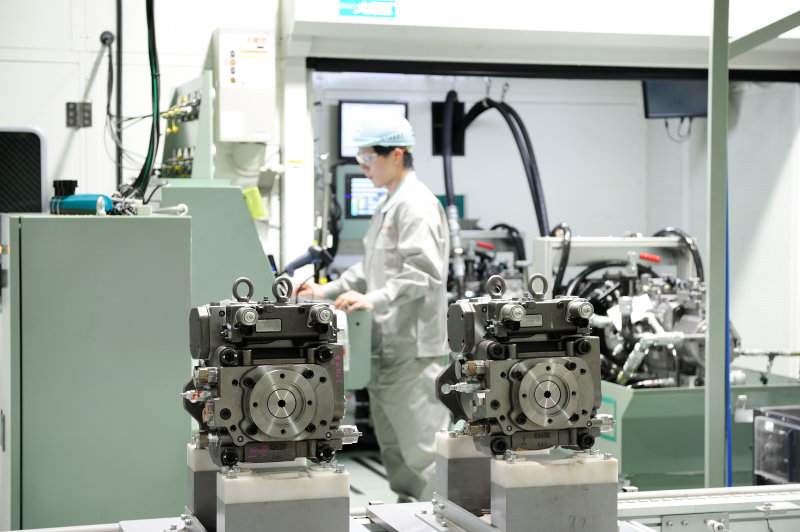

General Manager
Engineering Division
Precision Machinery Company
Kawasaki Heavy Industries, Ltd.
Ability to Propose a Total Hydraulic System Solution Holds the Key to the Next 100 Years
The year 2016 marks the 100th anniversary of the start of Kawasaki’s hydraulic equipment business. Taking this opportunity, we have decided to expand our business into the new fields of closed-circuit systems and HST, using our technological capabilities built up through the development of hydraulic equipment for excavators and our customers’ trust as a foundation.
The global market for hydraulic-related businesses is estimated to be in the order of 3.3 trillion yen. Kawasaki, which mainly manufactures hydraulic pumps and motors for construction machinery, is one of eight major players in this area.
As we make inroads into new fields, we must make sure our hydraulic equipment delivers unique value and is offered as a system. We must also have a decisive edge over our competitors in our ability to develop and manufacture high quality hydraulic equipment. Our expertise in hydraulic circuits and electric control circuits that are required for making machines work should also be leveraged in offering solutions to our customers. Our strength lies in our ability to offer superior equipment combined with a system that makes the most of it.
The field of HST, including wheel loaders and tractors, is a huge market, but it is also extremely competitive. That is all the more reason to focus on proposing a system solution for our customers’ machinery. Our hydraulic equipment offers world-class efficiency and performance backed by technologies developed over many years. I believe this, combined with our system solution, will enable us to compete in the closed-circuit market as well.
Kawasaki is the global leader in hydraulic equipment for excavators, but our entry into the closed-circuit market and the HST field in general, which are far from our traditional areas of operation, has met with amazement among our competitors and is turning heads. For us, this was a natural choice as we seek to evolve along the way toward the next 100 years of our hydraulic equipment business. It is also a challenge to motivate ourselves for this journey.
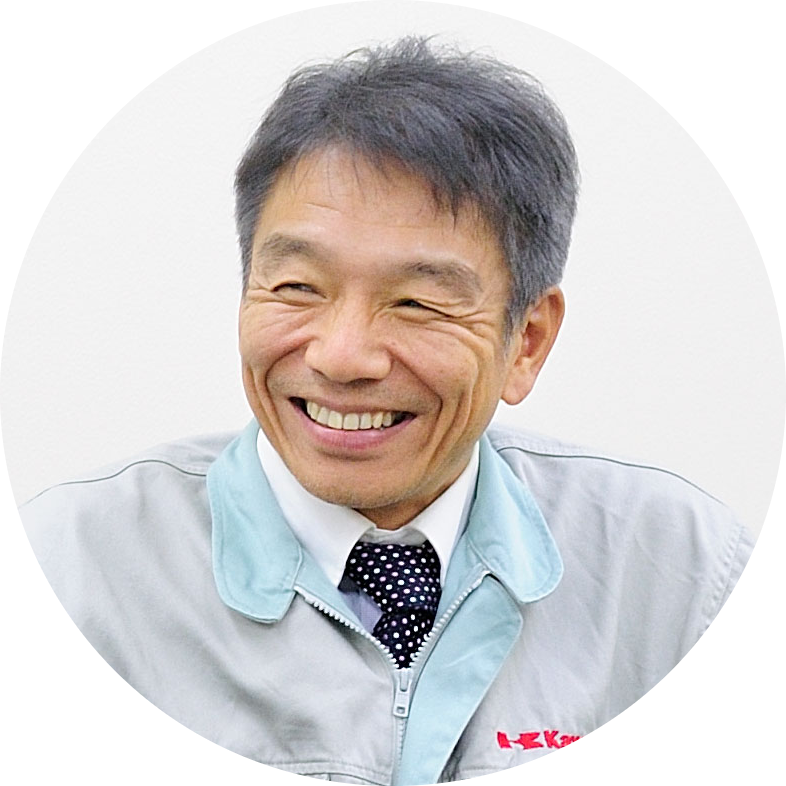
Engineering Division
Precision Machinery Company
Kawasaki Heavy Industries, Ltd.
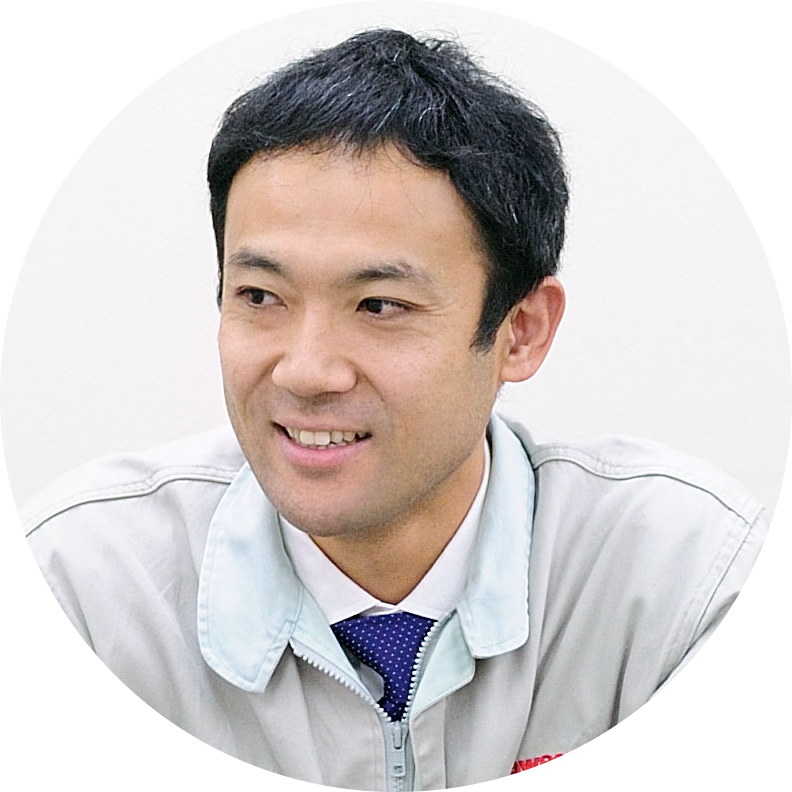
Engineering Division
Precision Machinery Company
Kawasaki Heavy Industries, Ltd.
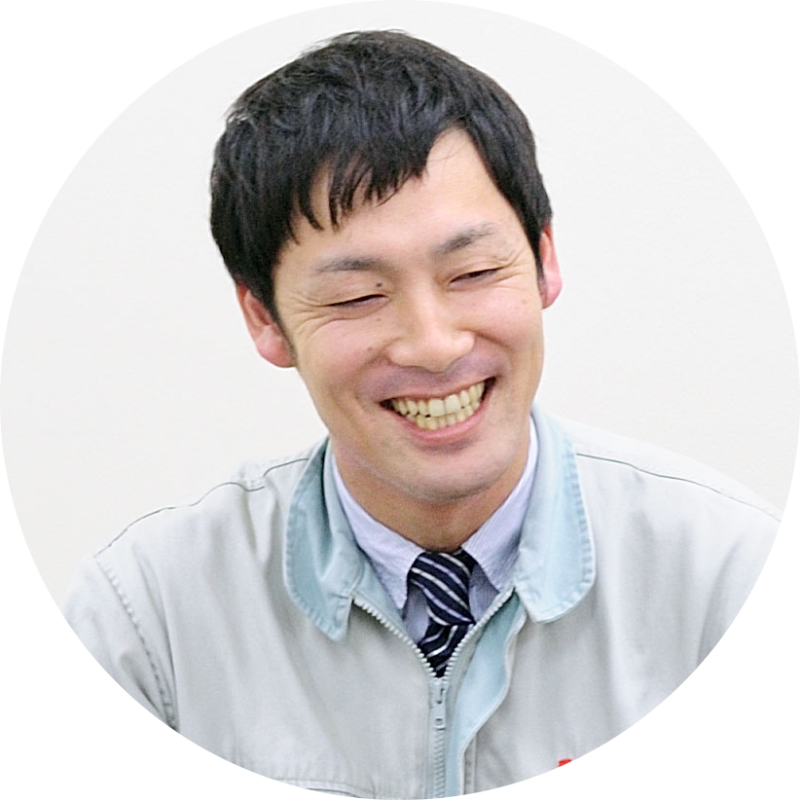
Engineering Division
Precision Machinery Company
Kawasaki Heavy Industries, Ltd.