High-Efficiency Cone Crusher ZI Cone Crusher
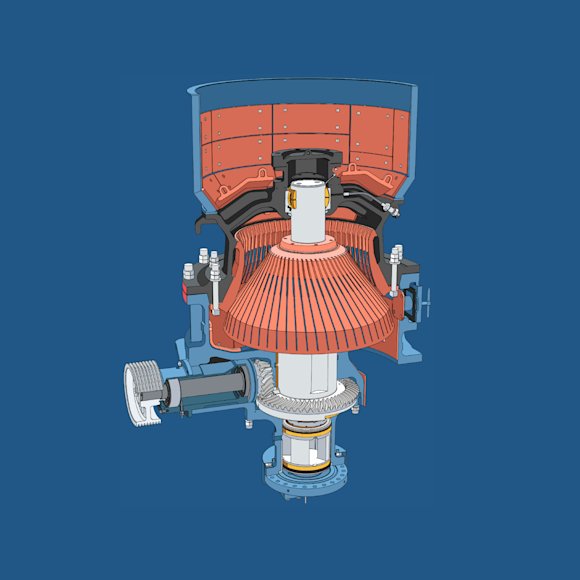
EARTHTECHNICA, a Kawasaki Group company that manufactures crushing and grinding equipment, has an extensive range of products for the crushing and screening field and holds the leading position and largest market share in the Japanese market. The ZI Cone Crusher, launched in 2012 as a strategic model for overseas markets, was developed to meet the market demand for high efficiency as well as compact design and high throughput capacity, and has been well received in the most demanding mining industries.
Crushes Meter-size Rocks Down to Millimeter-size Rocks
Aggregate quarries and mining operations use several types of crushers, with primary crushers handling raw materials that are 1-2 meters in size, and secondary and tertiary crushers reducing the material size down to 10-20 mm to achieve finer gradations.
Each crusher is designed to work with a certain size of feed material and the ZI Cone Crusher is dedicated to secondary and tertiary crushing applications.
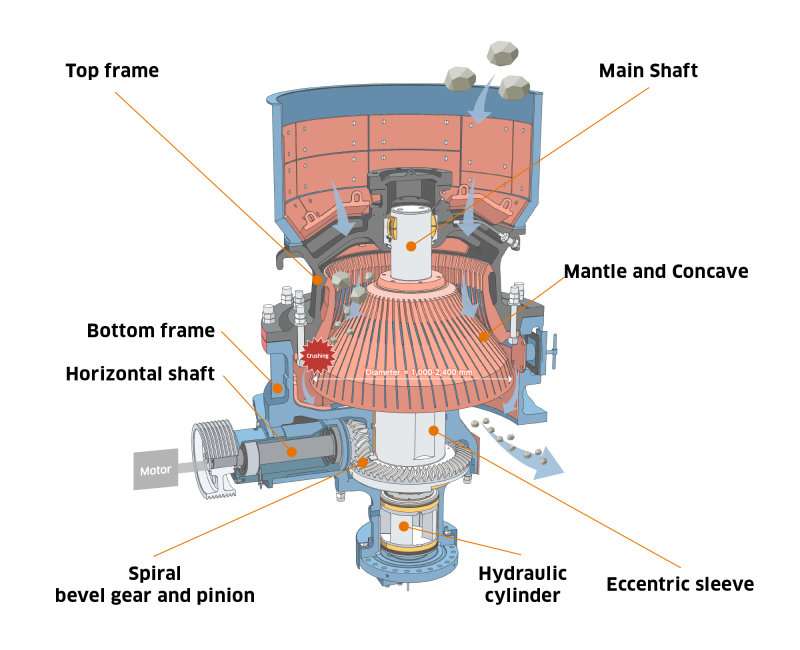
Boosting Productivity with Special Crushing Technology That Does Not Crush Diamonds
Since the introduction to the market, more than 20 units of the ZI Cone Crusher have already been ordered and delivered, all of which are for overseas customers. Especially, the ZI Cone Crusher has been used extensively in the liberation of diamonds in diamond mines across Southern Africa with excellent results.
The reason the ZI Cone Crusher is successfully adapted for diamond liberation is a special crushing technology that does not crush diamonds. Diamonds are concealed in a rock called kimberlite. Accordingly, kimberlite must be crushed by crushers to liberate the diamonds. However, diamonds must not be crushed with kimberlite during the crushing process; if a diamond is damaged, its market value will drop drastically.
The solution which EARTHTECHNICA is able to offer its customers for this conflicting requirement is the mild steel inserted (MSI) type crushing chamber of the ZI Cone Crusher. Mild steel plates are cast in manganese steel castings to form shallow grooves on the surface of mantle and concave and maintain until the liner is worn out. The shallow grooves are very important for liberating diamonds without damage (See Fig. 1).Originally, the MSI technology was developed to maintain high performance crushing. However, it was found through repeated crushing tests that the MSI technology works very well to liberate diamonds without damage.
For the crushing process (especially mineral processing), EARTHTECHNCIA has drawn on its extensive knowledge and years of field experience to design a the crushing chamber that meets the customer’s requirements. Thanks to a newly developed crushing chamber design, the throughput capacity is improved approximately 20-25% compared to the previous model.
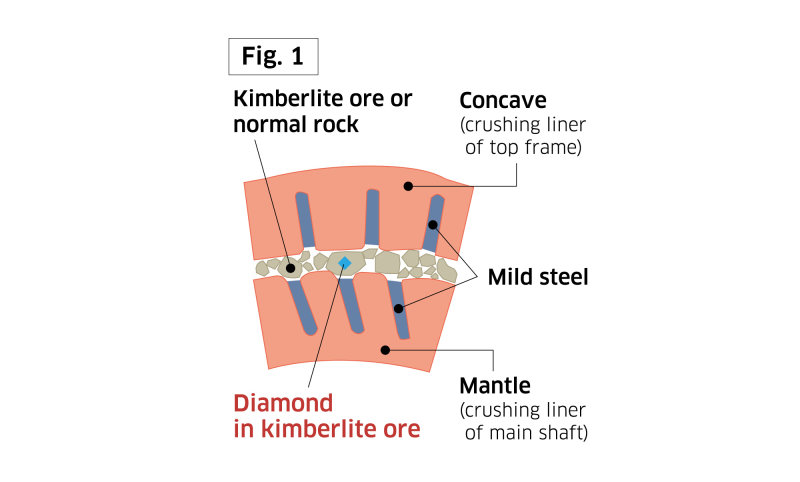
Manufacturing Technology of Special Liners
The crushing liners for crushing materials with various characteristics efficiently are manufactured at EARTHTECHNICA’s own foundry, which is one of the largest factories for steel casting in Japan.
The special crushing liners of the ZI Cone Crusher are realized by the company’s special manufacturing technology.
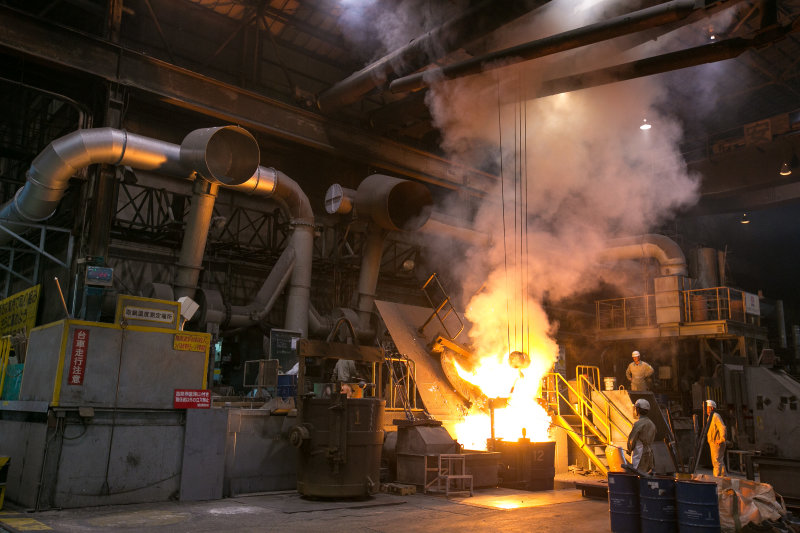
First Machine in Stable Operation in Malaysia
The first unit of the ZI Cone Crusher is currently operated in the state of Sarawak in Malaysia as the main machine in an aggregate production plant for the development of Malaysian domestic infrastructure.
Special Crushing Technology for Supporting Diamond Mines
Southern Africa is one of the largest diamond producing areas in the world, and 14 units of the ZI Cone Crusher have been installed and are in operation in Botswana, South Africa, Namibia and Lesotho.
Kimberlite ore, which contains diamonds, has special characteristics. If the kimberlite ore contains a lot of water inside, it will slip in the crushing chamber (between the mantle and concave), making it difficult to be crushed. As a result, the throughput capacity will drop dramatically. To prevent this phenomenon, a special crushing chamber design, developed based on our years of experience and extensive crushing tests, is adopted.
EARTHTECHNICA is highly reputed for its customized crushing chamber design and for developing mining and minerals processing solutions.
Mantle and Concave
The most important parts that determine crusher performance.
The space between the crushing liners, the concave of the top frame and the mantle of the main shaft, is called the crushing chamber. Materials to be fed into the crushing chamber are crushed down gradually to the required product size through compression, shearing and bending forces, then discharged from the crushing chamber as a product. The product size can be adjusted by changing the minimum gap size at the lowest part of the crushing chamber.
Top view of crushing chamber
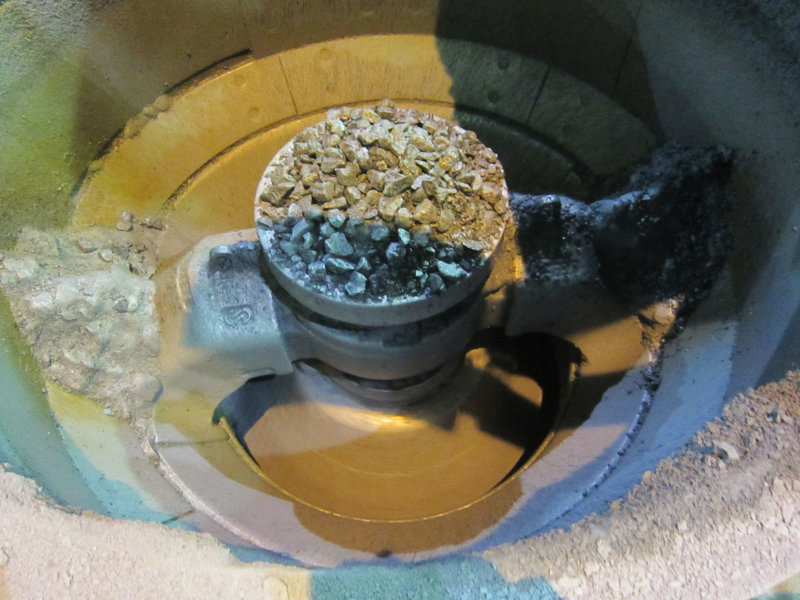
Main shaft
Supported by two bearings (the upper bearing of the top frame and the lower bearing of the bottom frame). The feed materials are crushed by the eccentric motion of the main shaft.
Top Frame
The concave (crushing liner) is assembled inside. It is one of the main wear parts and is replaced during maintenance work if worn-out.
Horizontal shaft
Motor power is transmitted to the crusher.
Eccentric sleeve
A special sleeve is used for journal bearing to transmit motor power to the main shaft. The inside of the sleeve is eccentric and produces the gyratory movement of the main shaft.
Hydraulic cylinder
A Heavy-duty hydraulic cylinder adjusts the discharge setting between the mantle and concave by moving the ram position. It is also used as a protection system by lowering the main shaft position if un-crushable foreign materials are fed into the crushing chamber.
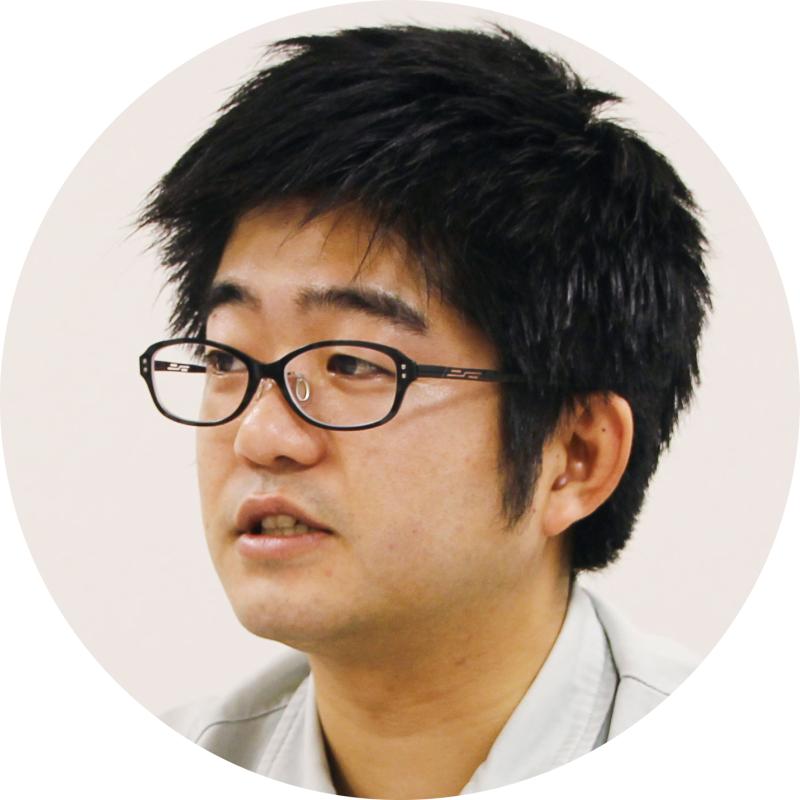
Engineering Department
EARTHTECHNICA Co., Ltd.