In June 2020, Yasuhiko Hashimoto was appointed the new President and Chief Executive Officer (CEO) of Kawasaki Heavy Industries, Ltd. ANSWER's editorial team interviewed the new president to find out how the manufacturing sector is apt to change in the post-pandemic era and what Kawasaki Group’s strategy for it will be.
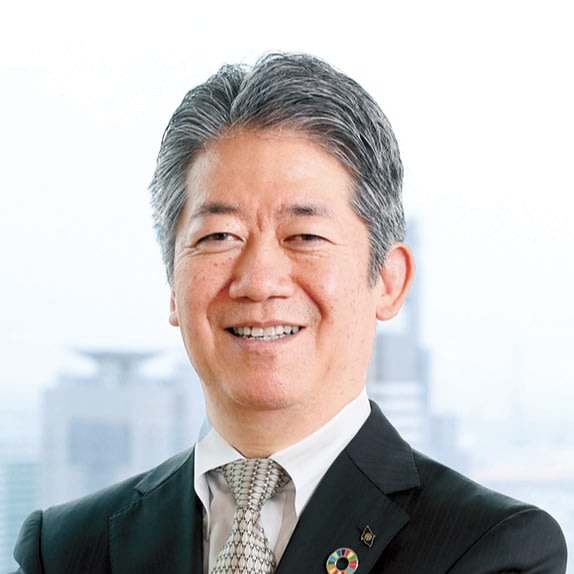
Kawasaki Heavy Industries, Ltd.
Profile
Born in Kobe City in 1957. He graduated from the Faculty of Engineering, University of Tokyo, in 1981, and joined Kawasaki Heavy Industries, Ltd. the same year. He was assigned to robot development projects and launched the semiconductor robotic business at Kawasaki and established Medicaroid Corporation, a developer of robots for the medical sector. In 2018, he became Director and Managing Executive Officer and President of Kawasaki’s Precision Machinery and Robot Company. In June 2020, he took on the post of President and CEO of Kawasaki Heavy Industries, Ltd.
Changes Required in the Manufacturing Sector
In your opinion, what changes are required of the world’s manufacturing sector today?
I think manufacturers are being tested for their ability to quickly accommodate changes and consistently continue upgrading the value they offer their customers. Today, manufacturers are required to improve the quality of the solutions provided by their products and to be capable of developing products more quickly in order to minimize the chance of missed opportunities being encountered by their customers.
For example, the volume of airplane production worldwide was expected to rise, but was instead severely hit by the COVID-19 pandemic, and that sector must now fundamentally change the way it manufactures products. Given this coronavirus calamity, we must think hard about what technologies we are able to offer and how they could be utilized.
The Kawasaki Group must therefore develop products with a shorter turnaround time, offer even more effective solutions, and practice effective sales communications using our long-standing suriawase* (optimal integration) approach in order to keep generating new value. In short, we must commit ourselves to bringing our comprehensive technological capabilities to the world.
Is the Kawasaki Group sufficiently responding to these challenges?
Employees of the Kawasaki Group can be characterized as having integrity. Period. I am proud that they are so committed to offering products that satisfy our customers. The downside is that we sometimes do more than simply fulfill a customer’s request, to the point where we prepare a full-course meal even though the customer is saying, “Instant noodles are fine - I'm hungry right now.” Rather, we must sharpen our senses to discern how the world is changing and what needs are emerging, and increase our ability to respond speedily to those needs.
To achieve this, I consider it imperative to further promote digital transformation (DX), foster a culture where it becomes the norm to produce things in a shorter time frame, and be more selective in which of our businesses we focus on, in order to accelerate the speed of operations. All of our businesses must be reviewed and redefined from the perspective of customers’ and market needs, rather than our own.
* Suriawase (lit. fitting, reconciling): A product-making approach in which any problems arising during both development and manufacturing processes are resolved through optimal integration of different technologies at each stage, beginning with prototype-making, in order to achieve sophisticated features and quality in the end.
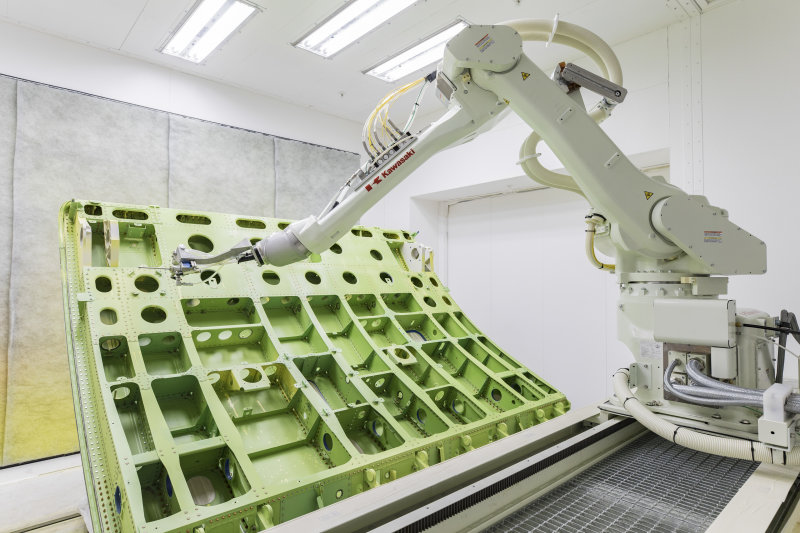
Responding Flexibly to Rapid Change
What measures has the pandemic compelled Kawasaki to take?
It has compelled us to accommodate changes rapidly as a company and at the same time demands mindset transformation on all our parts individually. This means that “KAWA-ru, SAKI-e Changing forward” - the motto that former president Kanehana advocated - must accelerate at once. We must first change our personal mindset and then that of the people around us.
For example, the popularization of teleworking due to the pandemic made us keenly aware that there is value in not always being on the move. However, Kawasaki manufactures airplanes, rolling stock, and many other products that support the value obtained by going from one place to another.
In terms of our products which aren’t “on the move,” such as industrial plants and robots, it is important to provide more IoT-based solutions. In regard to our products whose value is intrinsically tied to movement, such as airplanes and rolling stock, valuable new features, such as a mechanism to prevent infections from spreading from one passenger to another, must be explored in addition to general safety and comfort. I’d like to work on building a mindset among employees that flexibly accommodates expeditious change.
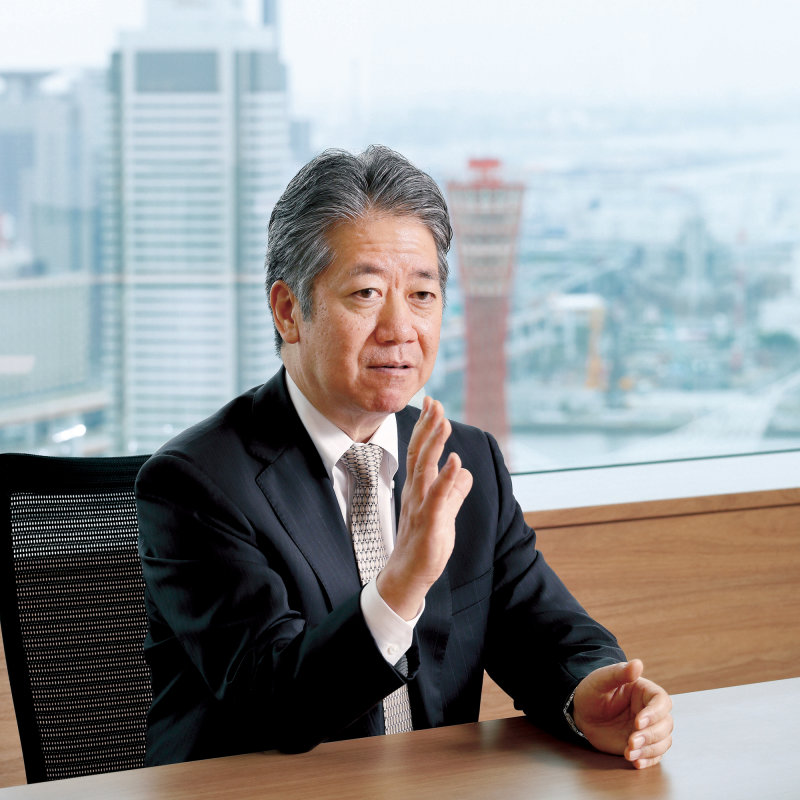
Trustworthy Solutions for the Future
May we ask why you wished to become a robot engineer?
“Astro Boy” and “Iron Man No. 28” were my childhood passion, and I was a boy who was always doodling structural designs of robots in the margins of my textbooks. In my university days, I had opportunities to serve as a volunteer for persons with muscular dystrophy, and I heard one mother saying, “Ever since my child was born, I haven’t slept for more than two hours at a time because I needed to roll the child over every two hours.” It was then that I determined to make a robot useful to the medical and nursing sectors.
The Kawasaki Group has long been manufacturing products that sustain society, and starting in spring of next year, we will begin building a hydrogen-energy-based society. I believe that technological innovation is born out of product developers’ and providers’ passion for wanting to contribute to society. I think, therefore, that offering to the world “Trustworthy Solutions for the Future” is what we should commit to as the Kawasaki Group.