The Kawasaki Spirit that Extends Beyond National Borders: Manufacturing Advances in the U.S.
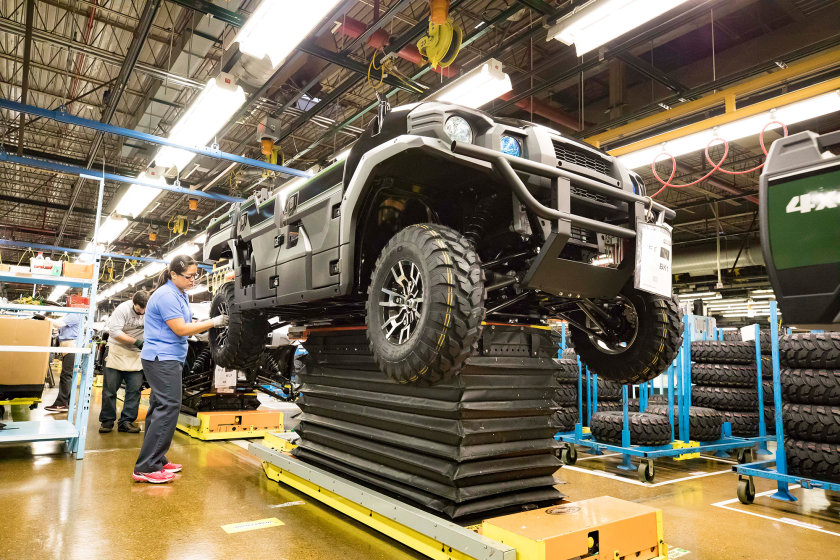
Kawasaki Motors Manufacturing Corp., U.S.A. (KMM) serves as the manufacturing base for Kawasaki in the U.S. and has at the same time been leading our push toward globalization.
At this manufacturing site that operates on the basis of Kawasaki's original production system, you will discover an extraordinary fusion of Japan-U.S. approaches to manufacturing.
Among Japanese manufacturers, Kawasaki was the pioneer in the U.S.
Located at the center of the U.S. is Lincoln, Nebraska. As you approach the airport runway from the northwest, on the left you catch sight of a completed rail car and a huge building emblazoned in red with "Kawasaki." This is the KMM Lincoln Plant.
KMM was established in 1974 as the manufacturing division for Kawasaki's motorcycle business in the U.S., and became independent in 1981, adopting the name KMM. In 1989, the Maryville Plant was established as a branch in Missouri, which is about 210 km away.
Motorcycle manufacturing in KMM was stopped in 2006, and currently four kinds of business are carried out:
(1) the "consumer products business," in which recreation utility vehicles, utility vehicles, etc., are manufactured; (2) the "rail car business," in which subway and commuter rail cars for public transportation systems for U.S. east coast metropolitan areas are manufactured; (3) the "aircraft business," in which cargo doors for Boeing's next flagship civil aircraft, the 777X, are manufactured; and (4) the "general purpose engine business" of the Maryville Plant, in which engines for lawn mowers, etc., are manufactured.
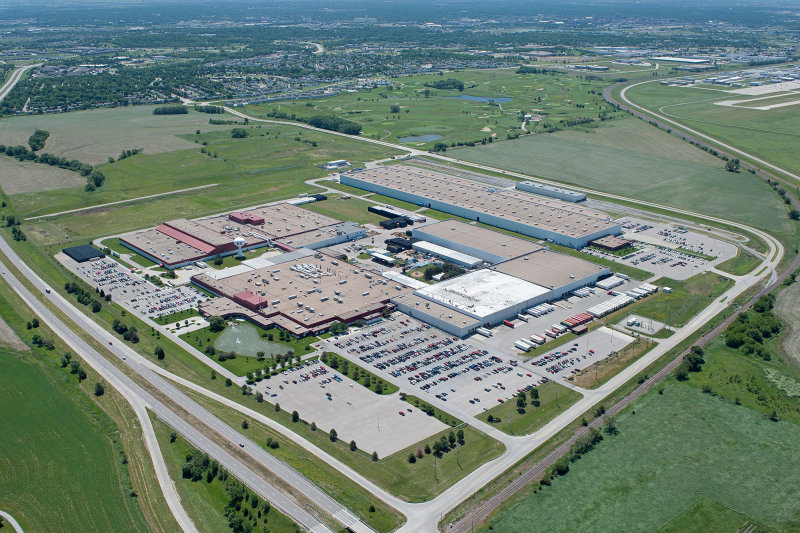
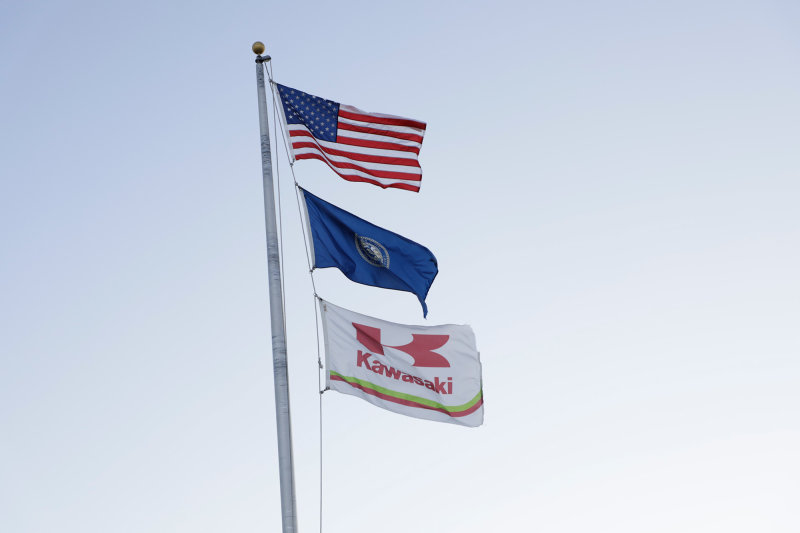
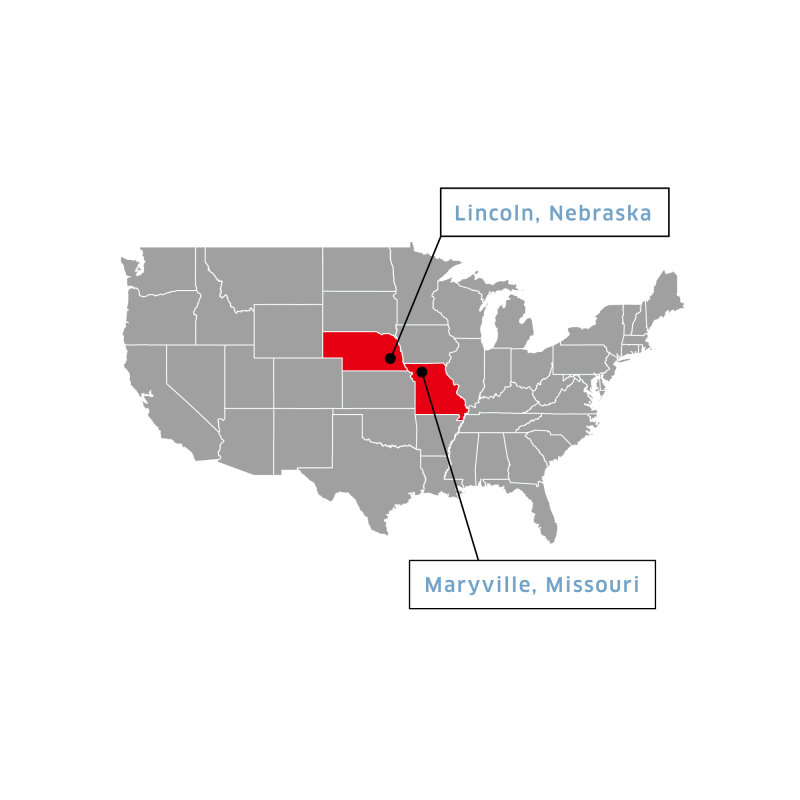
With about 2,000 people working there, including temporary employees, the Lincoln Plant is the largest manufacturing entity in Nebraska. There are also about 1,100 people working at the Maryville Plant. You can understand the significance of the workforce size if you consider that the population of Lincoln is about 280,000, and Maryville about 12,000.
According to Mike Boyle, Senior Vice President and COO of KMM, "Kawasaki and KMM have gained deep respect from the community. This is because we are not only creating employment, but also bringing significant economic benefits as a result of our trading with 250 local companies in areas such as parts manufacturing. There are other contributions that cannot be described in figures, such as technical education of employees and support for the Japanese library 'Kawasaki Reading Room' at the local University of Nebraska. There is nobody in Nebraska who does not know the name 'Kawasaki.'"
KMM was the first among Japanese two- and four-wheel vehicle manufacturers to start production in the U.S., and as a pioneer, has introduced and fostered the Japanese manufacturing culture. At the same time, as a result of its production scale, KMM has led Kawasaki's push toward global manufacturing.
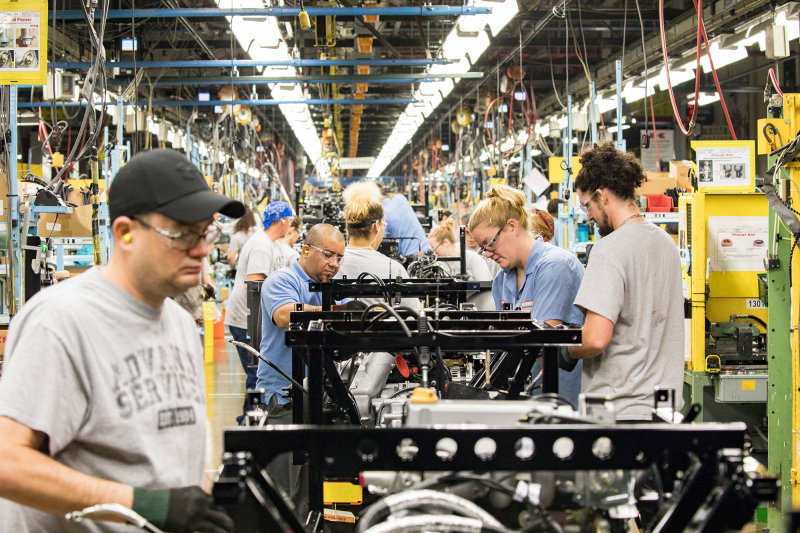
KPS: the driving force that worked to overcome tough times
As you can see in products such as recreation utility vehicles, utility vehicles, personal watercraft, rail cars, and general purpose engines, KMM has promoted manufacturing by Americans of products that have a large market in the U.S. In the 43 years of history since its establishment, KMM has witnessed a number of historic moments in its development, such as the establishment of the Maryville Plant, the passing of the 30-year mark since the production start-up of MULE utility vehicles, the shipment of 2,000 rail cars, and the establishment of a consumer products R&D base in the U.S. All of these moments have been driven by Kawasaki's power of manufacturing.
KMM has a significant characteristic – that manufacturing divisions of different Kawasaki companies coexist within the same plant. Consumer products and general purpose engines are part of the Motorcycle and Engine Company, rail cars are part of the Rolling Stock Company, and cargo doors for aircraft are part of the Aerospace Systems Company.
By overcoming cultural differences among the companies and optimizing manufacturing techniques for each of the four businesses, KMM achieves maximum manufacturing synergy by selecting the best from each. This idea is shared as the mission of KMM.
Richard Small, manager of the Production Department, Consumer Products Division, notes that KMM has a policy that allows employees to transfer between divisions to gain multiple skills and knowledge that benefit both employee and KMM, and says, “The people of Nebraska are honest and hardworking. The integration of these characteristics together with Kawasaki's management guidance creates a 'can-do’ attitude. The KMM management staff have learned and embraced Kawasaki’s original production system, KPS (Kawasaki Production System).”
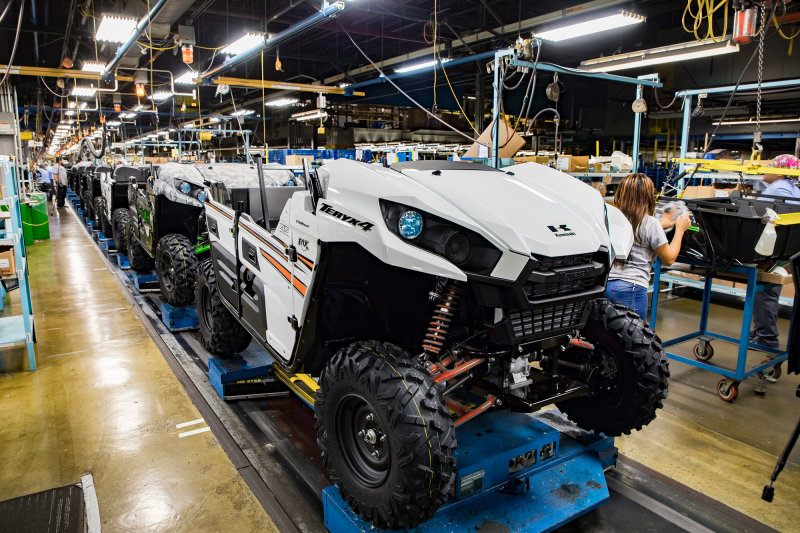
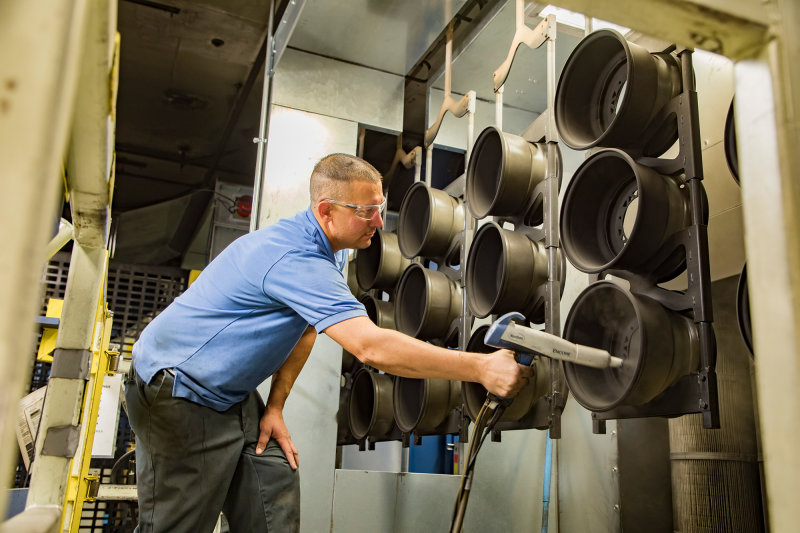
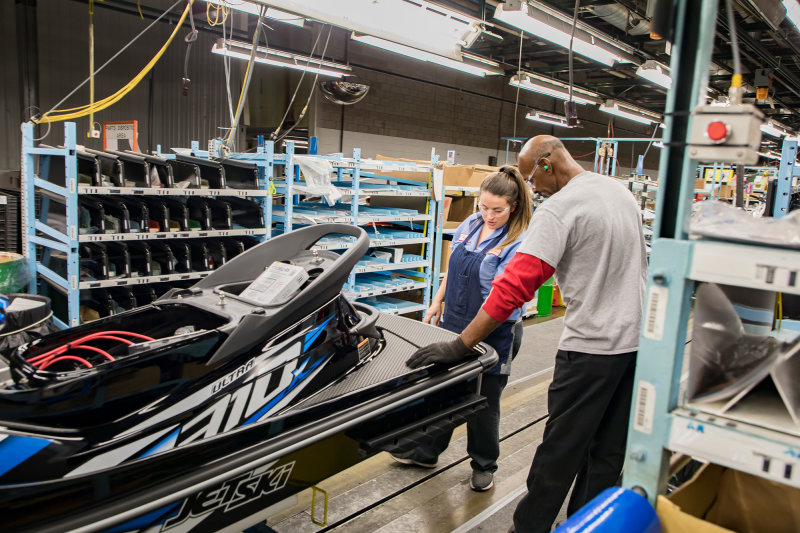
KPS is a system originally developed by Kawasaki on the basis of Toyota Motor Corporation's "Toyota Production System." Its universal iron rule is "thorough elimination of waste."
In fact, KMM was forced into a period of unprofitability immediately after becoming independent, as a result of being drawn into an underselling battle caused by other motorcycles companies. The system that brought the company back to life from this adversity was KPS, which was introduced at the same time that KMM became independent.
Delton Stauffer, manager of the Production Department, Rail Car Division, who joined the company in 1984, three years after KMM became independent, looked back on that time and said, “Senior colleagues told us that, ‘If you work with KPS, you will definitely see the benefits.’ In fact, I, too, received a thorough grounding in KPS.”
“For example, manufacturing people are trained to improve quality, and that is done by thoroughly implementing 5S (sorting, straightening or setting in order, shining, standardizing, and sustaining).
The thing that was emphasized the most was that everything starts with cleanliness! Cleanliness is the first step to order, order builds quality, and quality produces great products! Thoroughly implementing the 5S makes it possible to see that reality at the manufacturing site. 5S enables you to see waste and what should be improved.
When I started using this simple system to eliminate non-value-added activities, I came to realize we should make everyone share this common awareness with regards to the various sorts of situations and statuses we have in our plant, such as where to place things and how standardized work should be carried out. Now, I cannot imagine KMM without KPS."
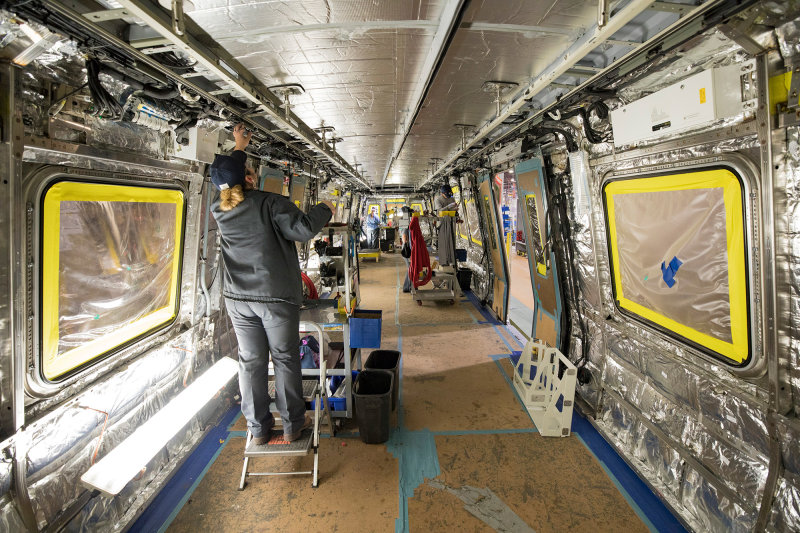
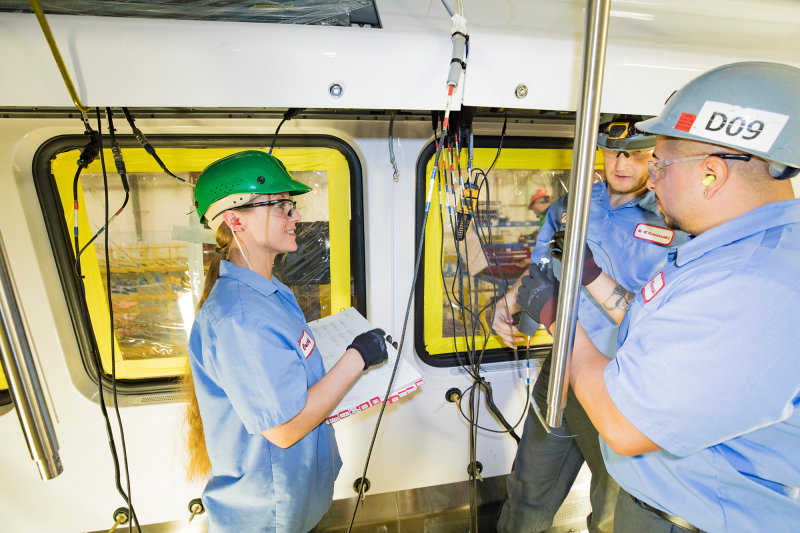
Creating quality from the bottom-up
People with knowledge of the time when KPS was introduced recount how volunteers formed improvement teams and started to get to work at the manufacturing sites. The key was found in the improvement proposals that came from the manufacturing sites. At first, there was confusion and people asked, "Why KPS?" but as the improvements took shape, the work became more accurate, and product quality improved. Recognition of this fact was the driving force behind the proposals.
For example, in the manufacturing line for utility vehicles, the products are conveyed down the line via a work station incorporating a lift mechanism, which goes up and down in coordination with changes in the operator's working posture. When the distance the lift is moved up/down and its position relative to the jigs are appropriate, there is less strain (waste) placed on the body and the work is carried out correctly, insuring quality. In other words, quality can be created by the manufacturing line. These improvements were made by the operators themselves.
Using material cards and identifying labels attached to parts in storage to check whether the supplied part is what should be used for the work is a method for preventing errors from being fed into the next stage of the process. The tag style was digitized in the "Kanban system," the system whereby the necessary quantity of the necessary parts is taken from the preceding stage of the process so that that preceding stage does not produce too many unnecessary parts.
Recently, a parts supply system called "Warehouse Management System” (WMS) has been under construction. By switching to a system whereby computers are used to trace parts from business partners to the warehouse stock location to the manufacturing lines, processes have been shortened. Furthermore, by changing the storage space for received parts from a fixed to a non-fixed style, empty spaces for parts that are not frequently used can be reduced.
The efficiency of supplying parts to manufacturing lines has improved, making it possible to reduce parts stocked beside the lines. Because there are no unnecessary parts, the areas around the lines have become safer, and it has also become possible to respond more flexibly to mixed production, in which different products are manufactured on the same line, and to single-piece flow production. It is said that now, only half the space is necessary for the parts stocked in the warehouse.
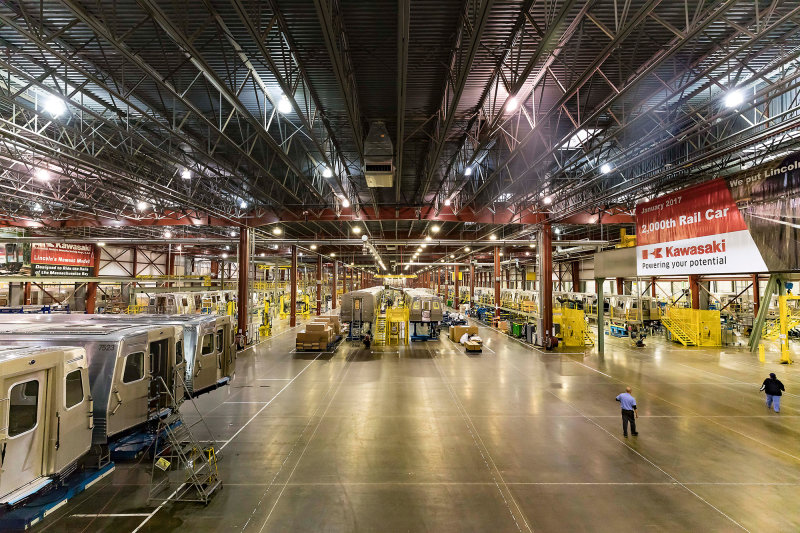
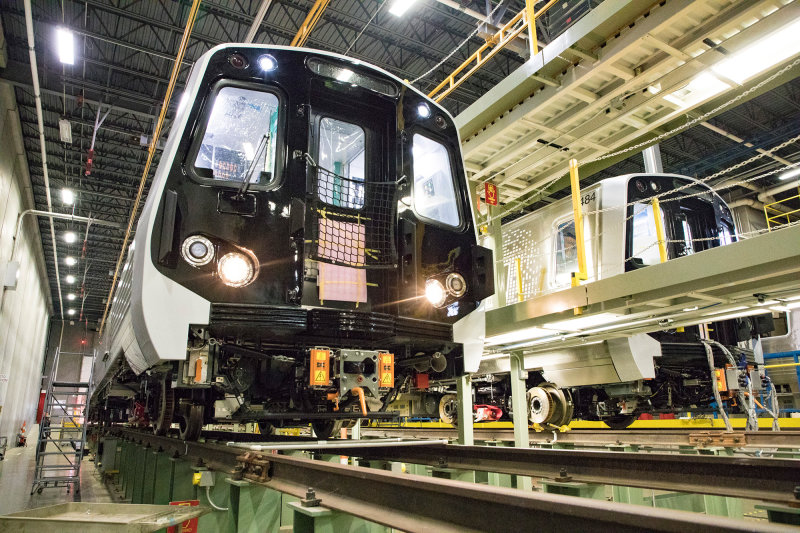
Every year at KMM, many people who need it participate in stratified KPS training and apply it in their manufacturing sites to carry out improvement projects in each business division. Three hundred projects are implemented annually, achieving constant cost reduction.
In the Maryville Plant, initiatives in order to complete 250 improvement items are being carried out themed around the concept of "Aiming for 250."
Scott McGinness, manager of the Maintenance/Facilities & Lean Department, General Purpose Engine Division, says, "We are focusing on our improvement activities and this allows our employees to get more involved in making their job easier. We also have taken initiatives to standardize the work and improve Process Control, by defining the critical features and control points of each process. This will help reduce waste, eliminate errors, and solve problems one by one. For example, if you use the same standard to set up Machine Cutting Tools, it will be easier for the operator to understand and control similar processes, and there will be no need to control the differences of each type of cutting tool. This simple way of thinking, "elimination of waste," is versatile, and on the basis of this idea, we are promoting quality and cost improvements, by training people to understand the function of each process characteristic."
COO Mike Boyle reflects on how KPS has established its position as the foundation of manufacturing at KMM:
"In Japan, people are more concerned about how to improve the negatives, but at KMM, we focus more on the positives and make full use of it to solve negatives, so as to keep the motivation high. KPS at KMM has developed to fit the American culture."
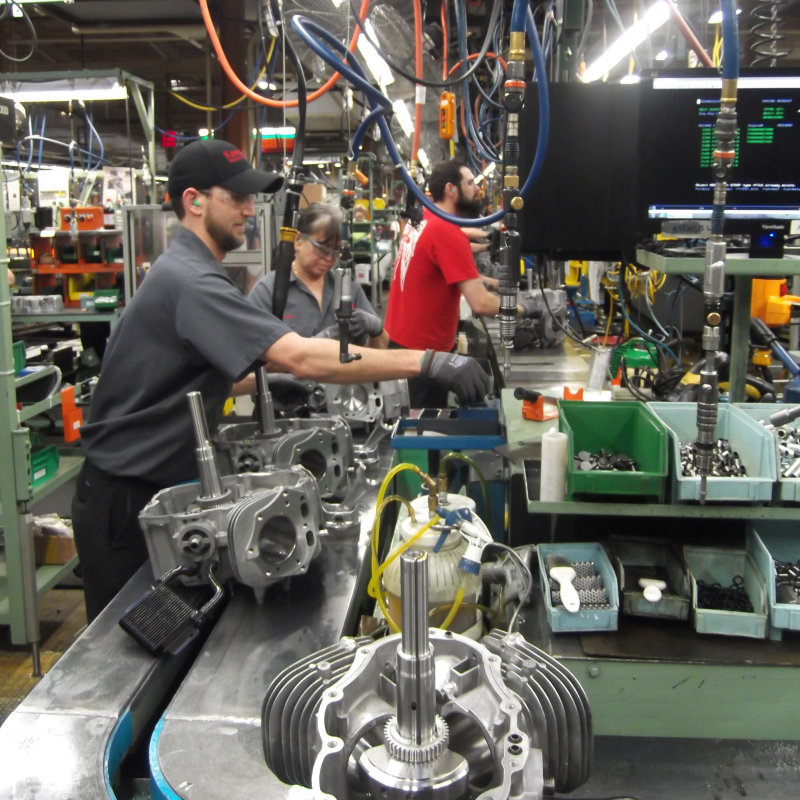
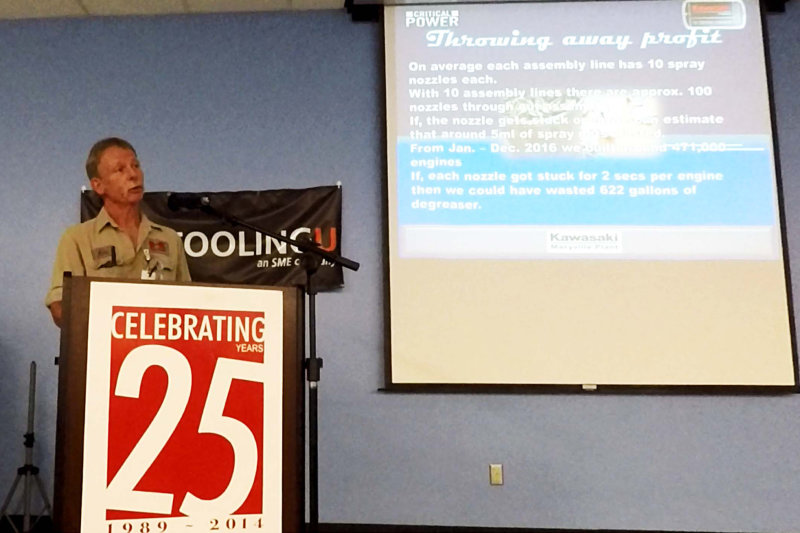
Starting aircraft component production in the U.S. : the first among Japanese manufacturers
Because KPS is being upgraded and optimized throughout the workplace at KMM, the latest KPS techniques are deployed here.
For example, in the rail car division plant, the vast plant floor with a total length of 450 m is made entirely of smooth concrete; there are no rails for moving the vehicles. Vehicles are conveyed on a cushion of compressed air on air pallets in a U-shape line. With this arrangement, it is possible to flexibly change the line layout, making it possible to structure a highly efficient, flexible manufacturing system that can cope with manufacturing a variety of vehicles with differing work loads.
Also, the sequence can be changed easily, even when a situation arises where pilot vehicles are assembled prior to mass production. Furthermore, on both sides of the straight car body manufacturing line that starts with underframe fabrication, there are parallel subassembly lines for fabricating structures such as sides, roofs, and end structures, in order to synchronize the manufacturing. Depending on the progress of the work, operators can support work that is behind, so that the manufacturing speed can be normalized.
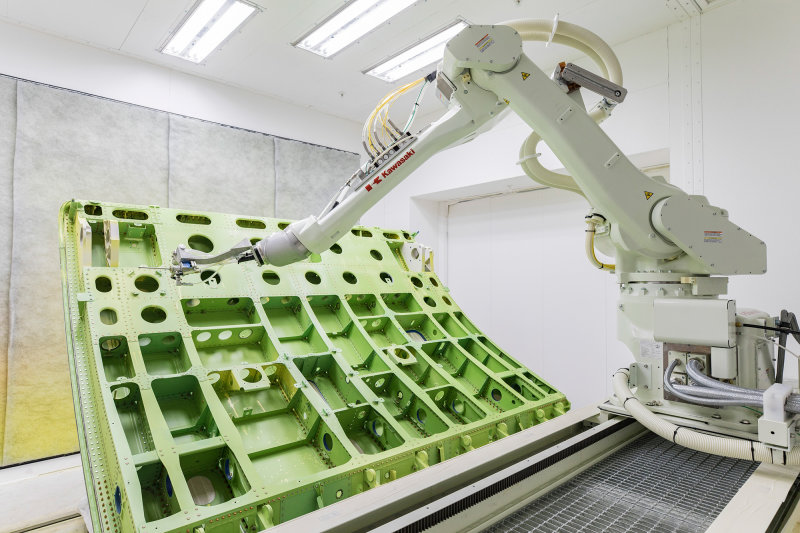
The establishment of our aircraft components manufacturing line in the U.S. - the first among Japanese manufacturers - is also the result of the accumulation of KPS practices; the work space was created by WMS. This line manufactures the cargo door for Boeing’s 777X, and proficiency training is currently being carried out, in preparation for the first shipment. All twelve employees were selected through open recruitment from other divisions in KMM.
Matt Huber, assistant manager of the Engineering Department, Aerospace Division, emphasizes that, "There is nothing more challenging than this. We are endeavoring to achieve a kind of production engineering that no one has ever accomplished before, even at the Gifu Works, which is the center of our aircraft business. When manufacturing aircraft components, we have to achieve precision to a few micrometers, by repeating work on the same part many times over. In order to achieve this, we try to divide a process into small sections as far as possible, clarify the quality requirements that should be achieved, and eliminate unnecessary movement. In any case, since the operators are a team who have learned Kawasaki's manufacturing techniques through KPS and have grown together, and since the organization is geared toward achieving success, we will succeed."
KMM: a company that embodies Kawasaki’s manufacturing ethos. Its potential to grow is limitless.
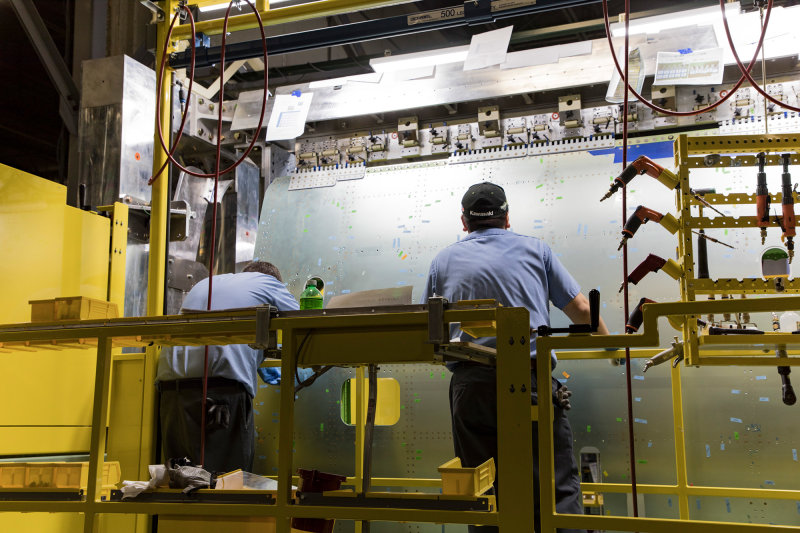
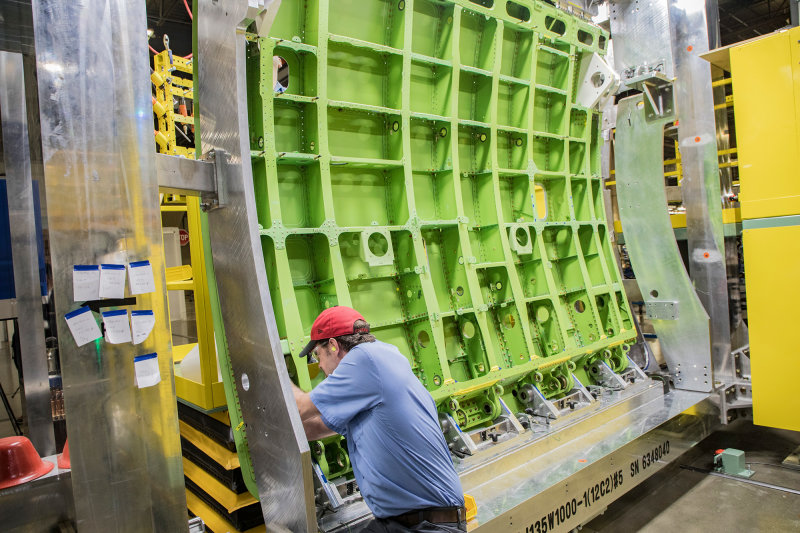
Leader’s Voice
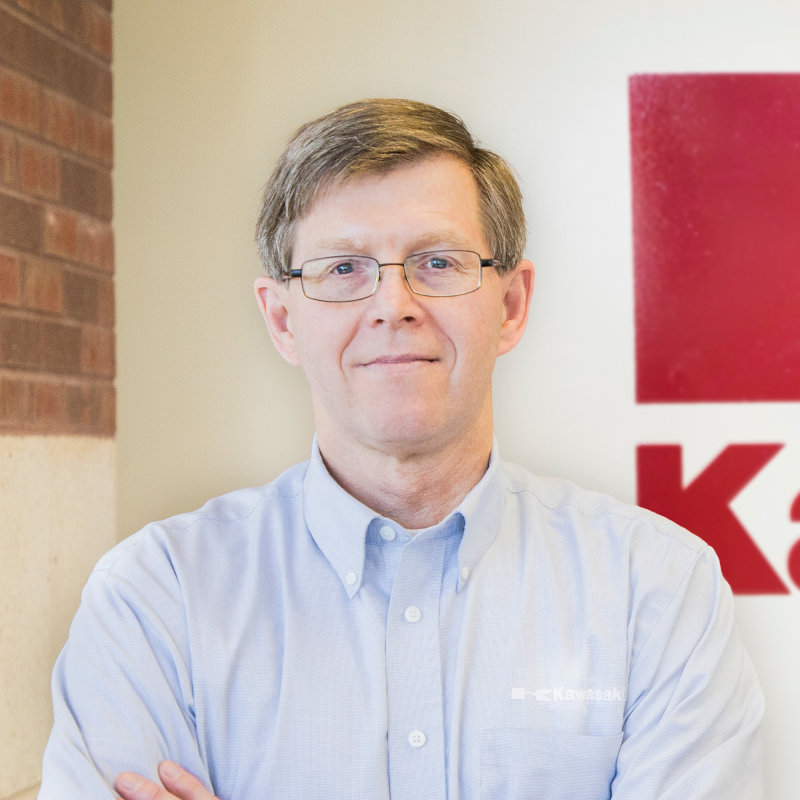
Kawasaki Motors Manufacturing Corp., U.S.A.
Achieving Highly Competitive Manufacturing that Integrates the Cultures of Japan and the U.S.
As the COO of KMM, I am involved in the daily running of the business with our Japanese President. With regard to management, I focus on three things.
The first is to clarify the goals in a variety of areas such as performance and production results, by reconciling Kawasaki and customer requirements, and developing the pathways to achieve these goals.
The second is the improvement of employee skills. The products that we manufacture and the processes required have become more and more advanced and complicated. In order to deal with them, you need high-level technical skills and it is one of my major responsibilities to develop a plan to improve employees' technical skills and to put it into practice.
The third point is to maximize the synergy between the four kinds of businesses that KMM owns. To achieve this, we have to find practical examples and techniques that we can use from across the whole Kawasaki Group. In any case, we have to share what we learn by overcoming the barriers between businesses.
KPS was a truly innovative method for KMM. We introduced KPS and were able to deliver good results. Because of this, we were able to gain employees' confidence and spread the method throughout. In other words, KPS has become a consistent core for collaboration among workers at KMM and the basis of their way of thinking. It has enhanced their motivation for skill development and is actually leading to skill improvement. There is nobody who doesn't grasp the vast, deep meaning behind the simple idea, "thorough elimination of waste."
At KMM, Japanese attention to detail and willingness to persevere with the necessary training are integrated with American creativity and ingenuity.
We go about our business in the "right way": we are honest and open, and we treat our employees and people in society with respect and dignity. I feel great responsibility and at the same time a huge sense of pride for such feelings of respect that are addressed to KMM.
Persons
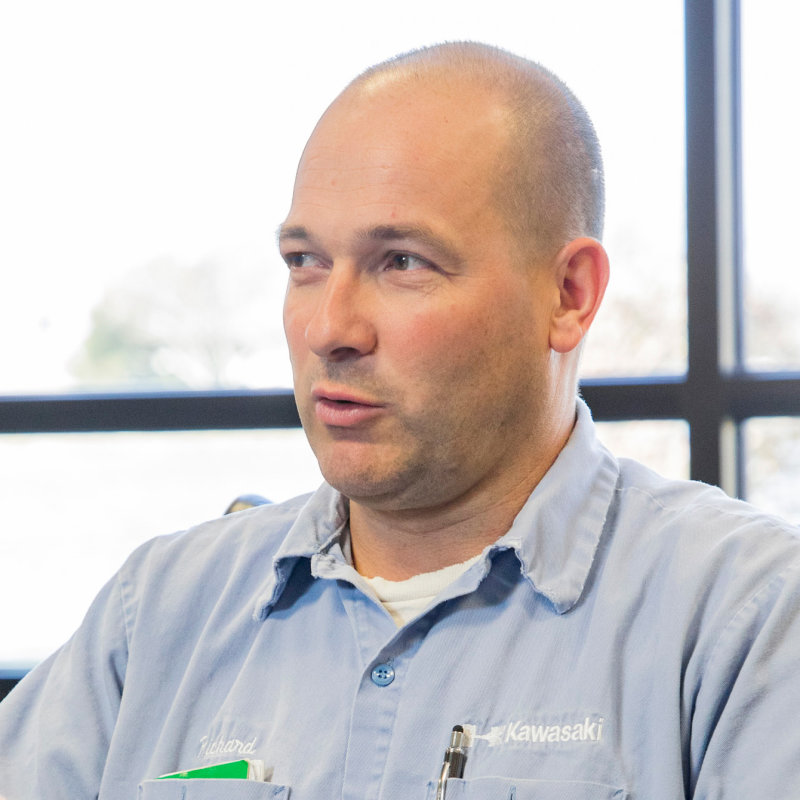
Production Department
Consumer Products Division
Kawasaki Motors Manufacturing Corp., U.S.A.
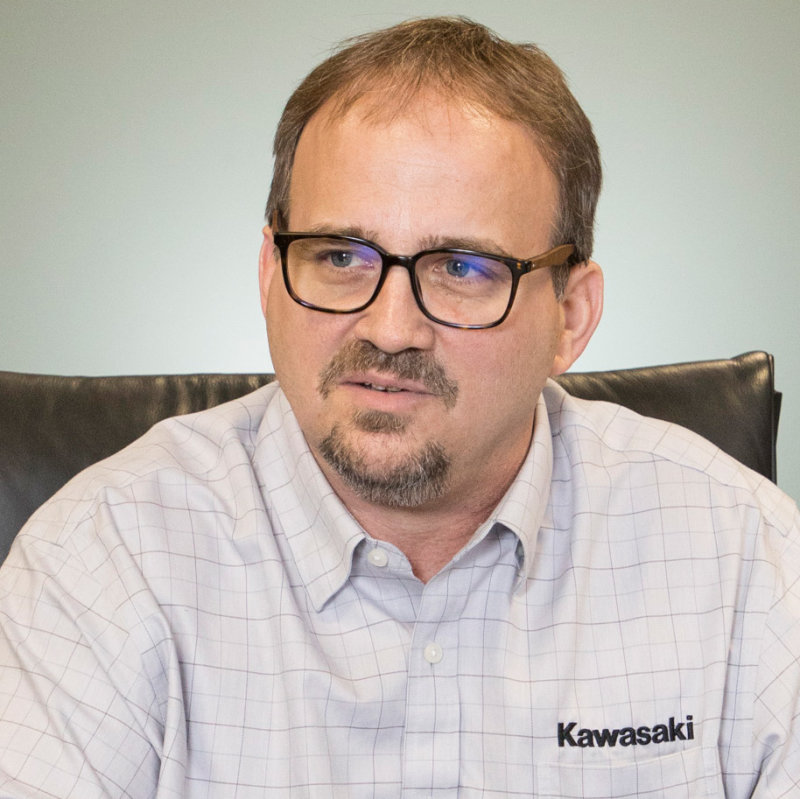
Production Department
Rail Car Division
Kawasaki Motors Manufacturing Corp., U.S.A.
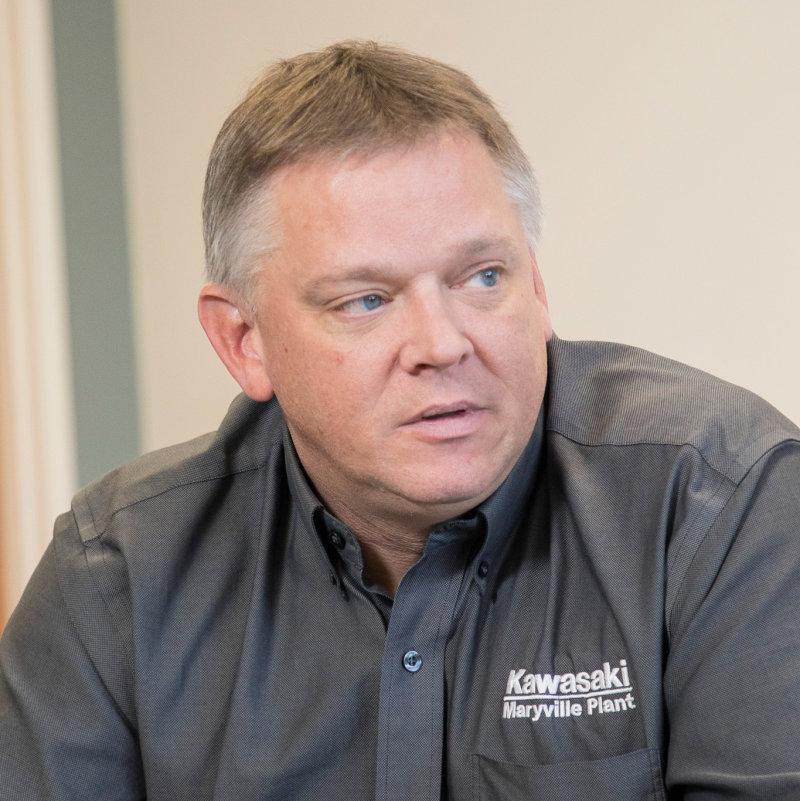
Maintenance/Facilities & Lean Department
General Purpose Engine Division
Kawasaki Motors Manufacturing Corp., U.S.A.
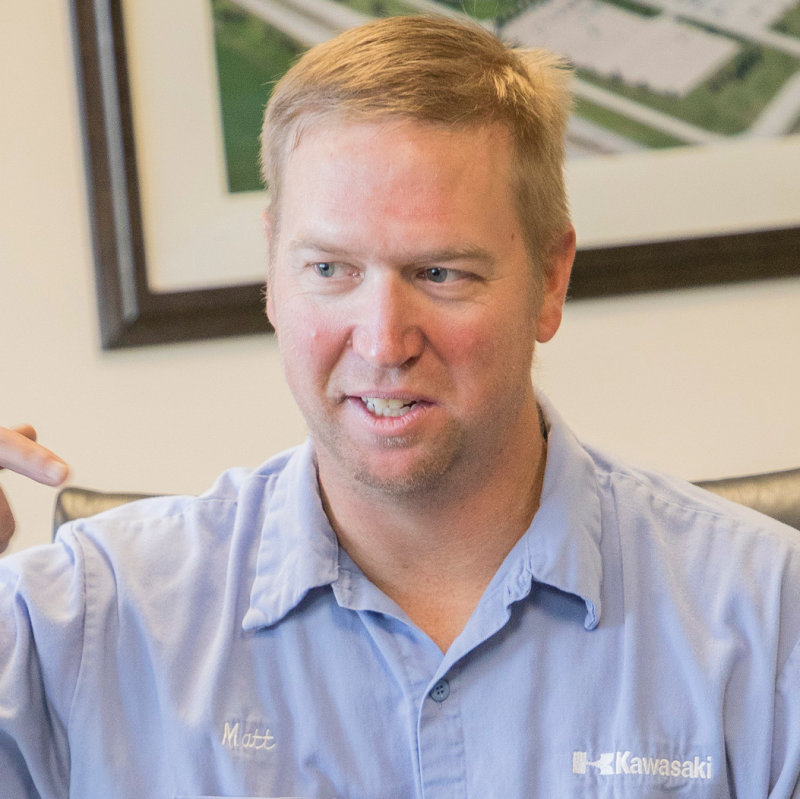
Engineering Department
Aerospace Division
Kawasaki Motors Manufacturing Corp., U.S.A.