Hybrid Vessel Realized through Co-creation Project Gas-only Engine and Electric Hybrid Propulsion System for Bulk Carriers
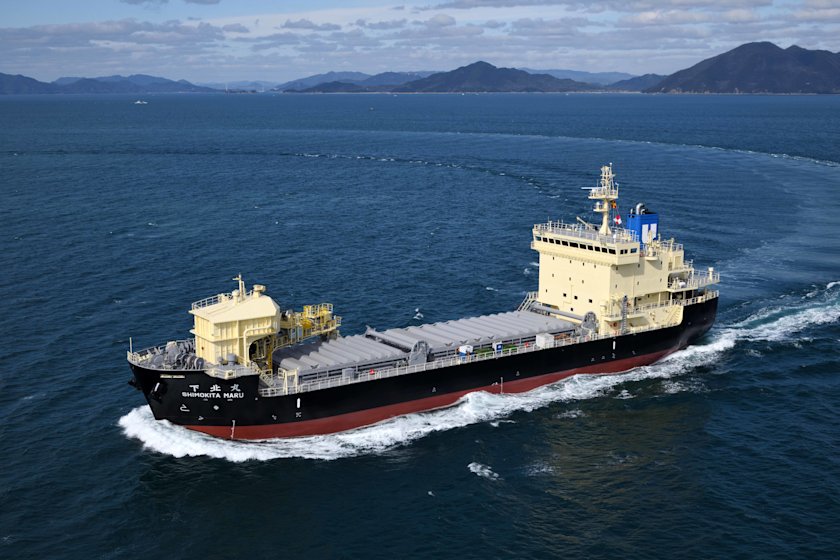
Ships have taken a step along a new evolutionary pathway, with Kawasaki Heavy Industries, Ltd. (“Kawasaki”) delivering a hybrid propulsion system that combines a gas-only engine―an engine that does not use heavy oil at all and is fueled solely by liquified natural gas―with a large-capacity electric battery. The system has been installed in a bulk carrier* operated by NS United Naiko Kaiun Kaisha, Ltd. (“NSU Naiko”) to create the world’s first bulk carrier equipped with a hybrid propulsion system. With the new system running well, the vessel is maintaining stable operations across the Tsugaru Strait, known for its extremely rough winter waters, achieving a nearly 50% reduction in CO2 emissions.
* Bulk carrier: a merchant ship designed to transport large quantities of unpackaged cargoes of amorphous materials, such as minerals and grains
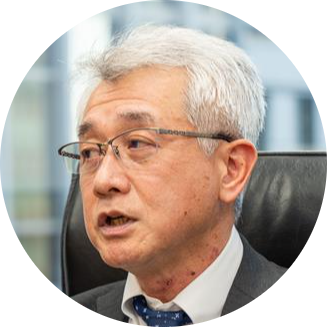
NS United Naiko Kaiun Kaisha, Ltd.
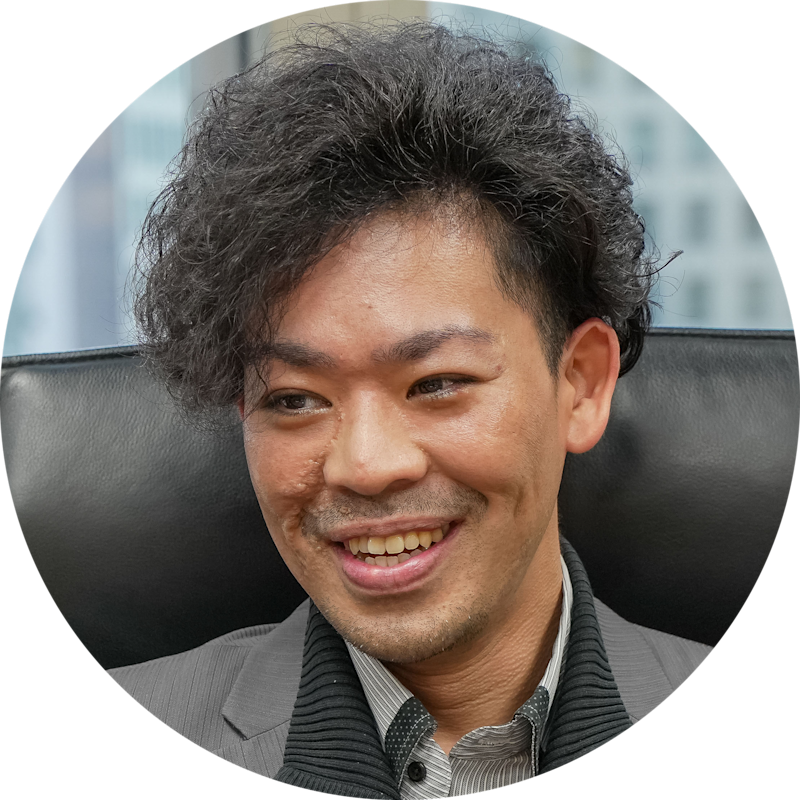
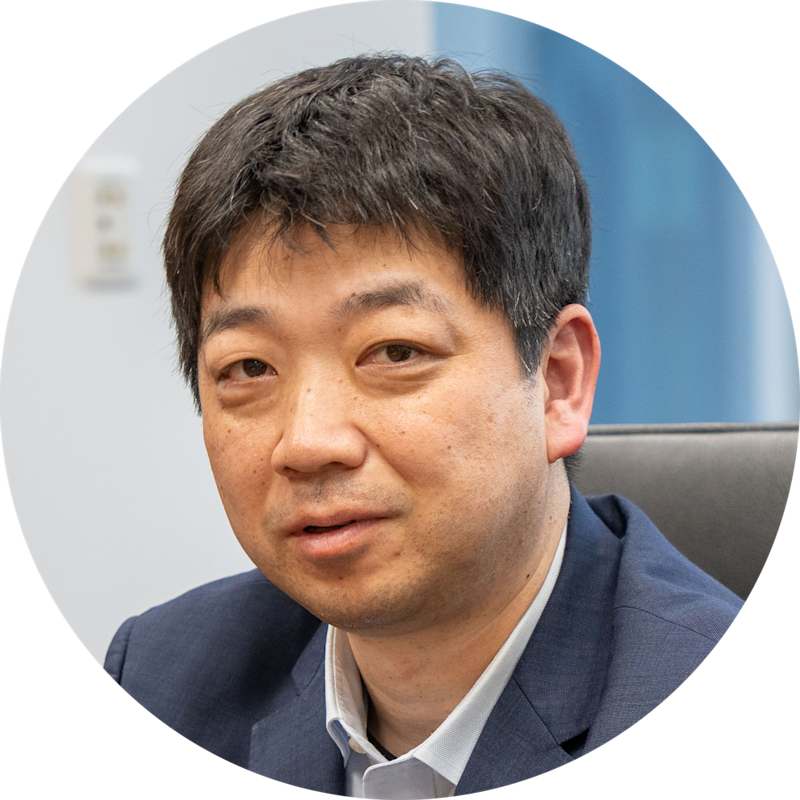
NS United Naiko Kaiun Kaisha, Ltd.
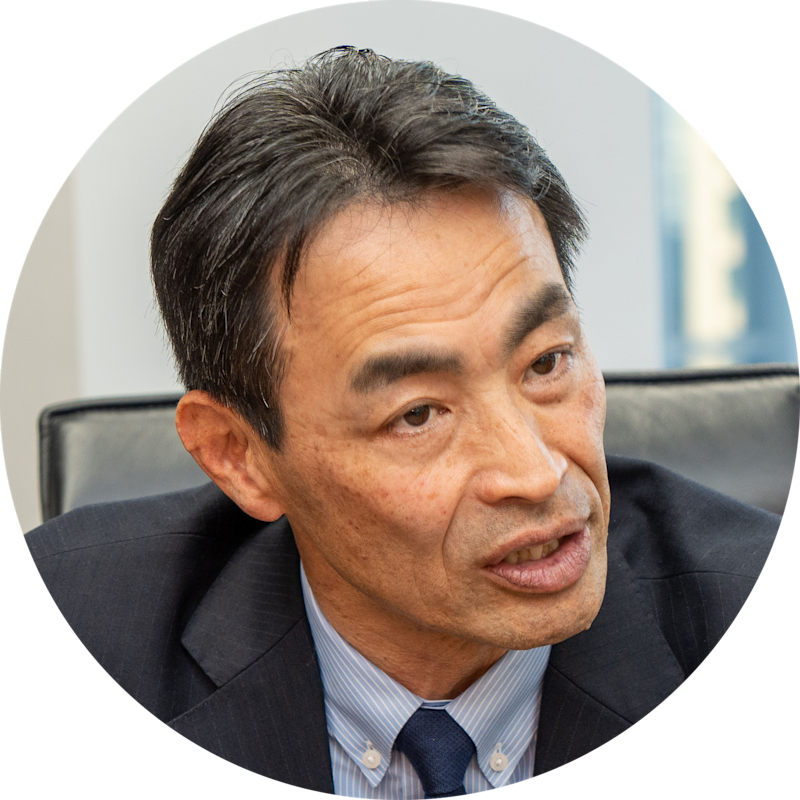
Marine Machinery Sales Department
Marketing & Sales Division
Energy Solution & Marine Engineering Company
Kawasaki Heavy Industries, Ltd.
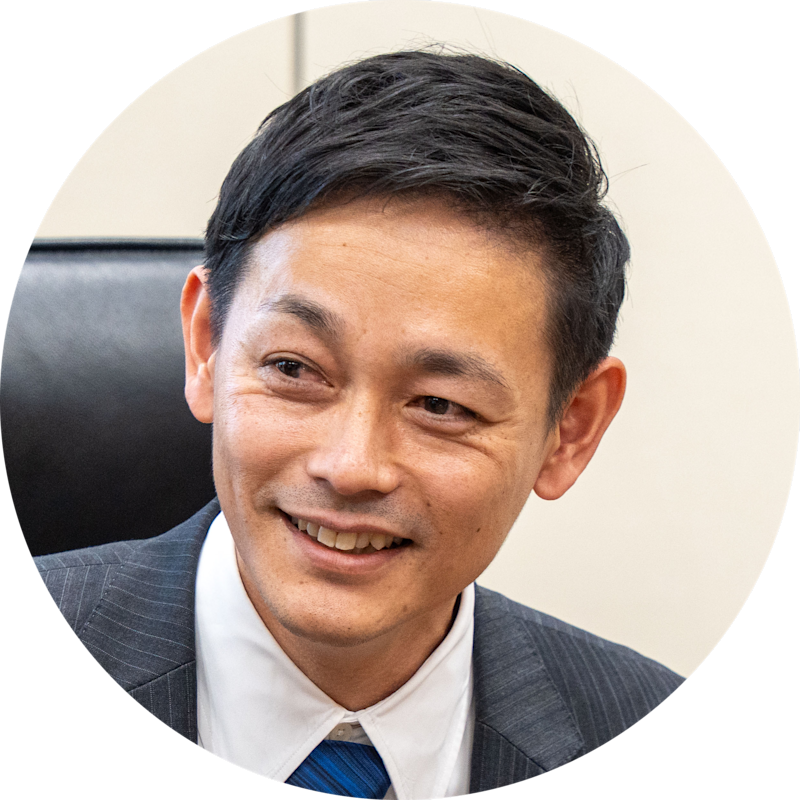
Systems Engineering Department
Marine Machinery Systems Group
Marine Machinery Business Division
Energy Solution & Marine Engineering Company
Kawasaki Heavy Industries, Ltd.
High performance demonstrated by halving of CO2 emissions on rough waters of the Tsugaru Strait
Named the Shimokita Maru, this bulk carrier moves limestone from Shiriyamisaki Port to the iron mill in Muroran, Hokkaido, making the roughly 110-kilometer journey across the Tsugaru Strait on a daily basis. Shiriyamisaki Port is an industrial port located near the limestone mine site, which is situated close to the northeastern edge of the Shimokita Peninsula in Aomori Prefecture (at the northern end of Japan’s Honshu island). The surrounding sea is known for its formidable meteorological and hydrographic phenomena, including most notably the six- to eight-meter-high waves during winter. Despite such harsh conditions, the Shimokita Maru and its operator, NSU Naiko, have been providing reliable transport services for many years, earning solid trust from shippers.
Since going into service in March 2024, the new Shimokita Maru has achieved a significant reduction in greenhouse gas (GHG) emissions. It has achieved particularly remarkable feats in terms of the following: near-zero emissions of sulfur oxides (SOx); satisfying the latest Tier III standards for nitrogen oxides (NOx) established by the International Maritime Organization (IMO); and attaining quickly the initial target of reducing CO2 emissions by 26.35% compared to the previous Shimokita Maru, which started operation in the 2000s, and even hitting phenomenal figures of 46 to 47% in some months.
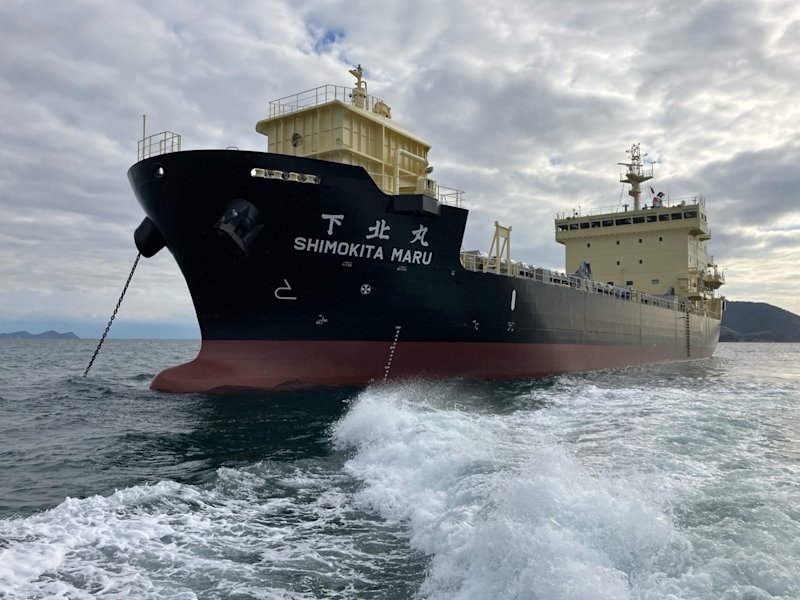
The vessel sails across the Tsugaru Strait, with its engine power output unaffected by the surrounding rough sea. This eliminates the need for additional fuel consumption and enables stable operation at scheduled speeds.
The distinctive performance as described above has been made possible by the hybrid propulsion system that combines the Kawasaki Green Gas Engine (gas-only engine) with a large-capacity lithium-ion battery (electricity). The system was delivered by Kawasaki and is the first in the world to be installed in a bulk carrier.
Basic configuration of the hybrid propulsion system
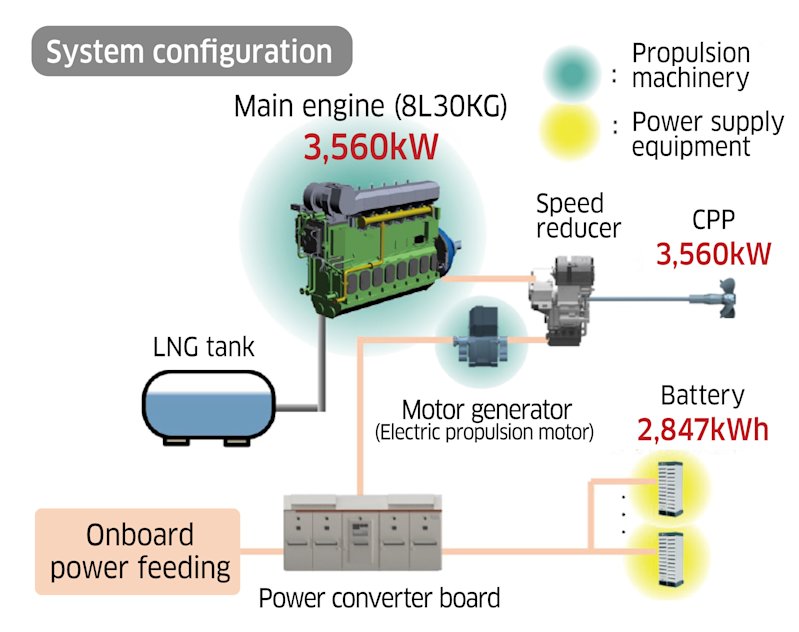
Employed as the main engine of the system, the 8L30KG Kawasaki Green Gas Engine has a rated output of 3,560 kW, constituting its primary ability to propel the 5,646-deadweight-ton vessel. Engine performance is assisted by a motor generator that doubles as an electric propulsion motor, generating electricity to power onboard functions as well as to be stored by the large-capacity battery system, which has a total capacity of 2,847 kWh (enough to charge approximately 280 standard EVs).
By implementing the above configuration, the system has established a battery-powered electric propulsion capability, thus securing sufficient redundancy to ensure continued operations. In addition, when entering and exiting ports, vessel operations can be powered by the electric propulsion motor alone, achieving zero emissions from staying within the port including while at anchor. This configuration also contributes to a highly reliable propulsion system.
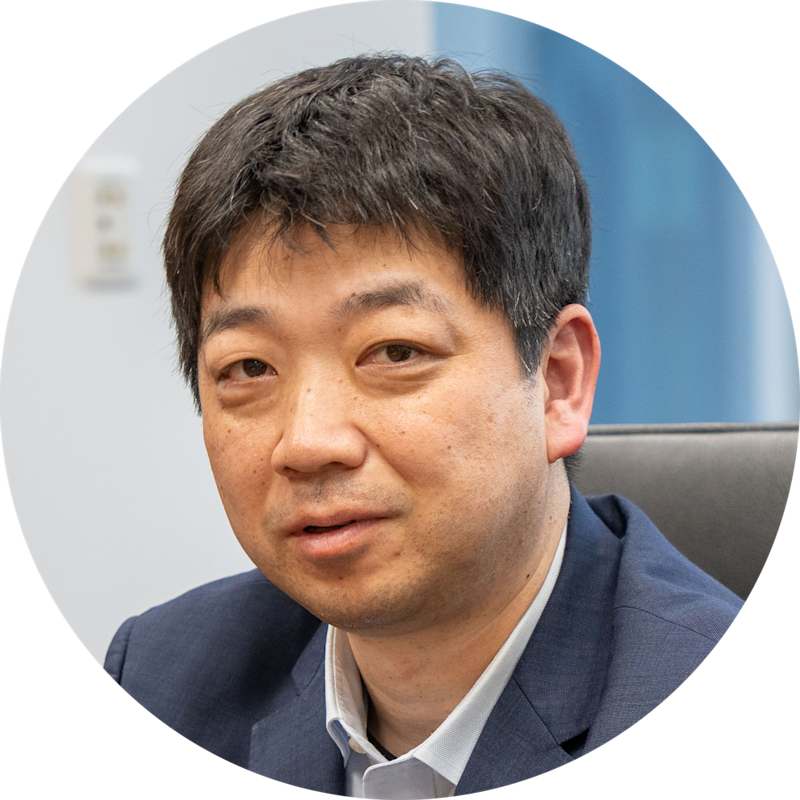
This hybrid system allows for an easy, automatic switch between the gas engine and electric prolusion modes, and offers a smooth and stable process of changing the engine operation status. Moreover, the noise and vibrations are remarkably low, which has improved crew comfort in the living quarters located above the engine room.
Take up new challenges and break away from conventional thinking to propose attractive and innovative technical approaches
The new Shimokita Maru is the fourth vessel operated under that name. Its build plan was decided in the summer of 2018 with the aim of providing a successor to the third vessel, which was due to reach its 30th year in 2024. The plan was formed in response to the emphatic request of shippers to create an environmentally friendly and inspirational new-concept ship based on their commitment to reducing GHG emissions stemming from marine transportation as a top priority issue.
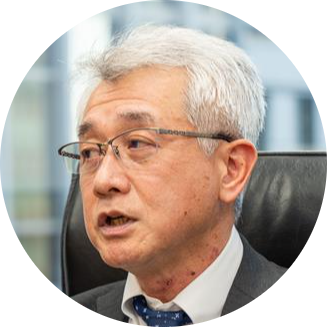
We had a host of issues to deal with, such as technical studies on new energy and propulsion systems that could contribute to carbon neutrality, and strict requirements, including the inability to change the dimension of the hull due to the need to accommodate the water depth of the quay at Shiriyamisaki Port and the request not to decrease DWT from the previous level. With all these conditions considered and discussed, it took three years to work out an outline for the new shipbuilding plan.
As a result of considerations undertaken from various perspectives, Kawasaki’s hybrid propulsion system was selected as the best possible candidate.
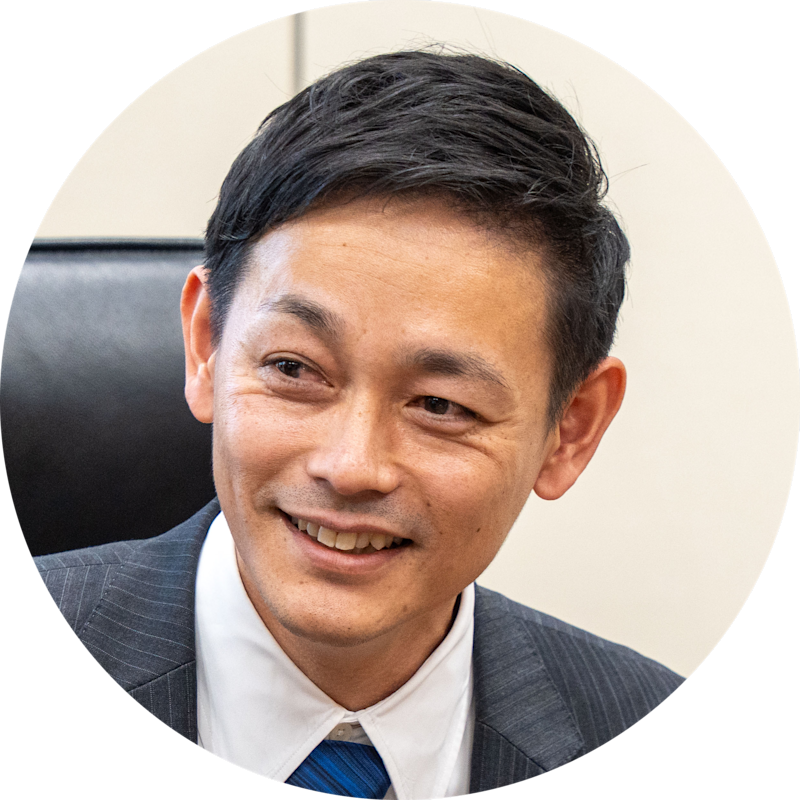
We thought that our proposal to adopt Kawasaki’s latest system would pique the interest of the highly environmentally conscious shippers, our customers. With strong eagerness, we persisted in conveying to them the appeal of the proposal.
It should be noted, however, that the marine transport industry is very hesitant to adopt the latest technologies because of the risks involved.
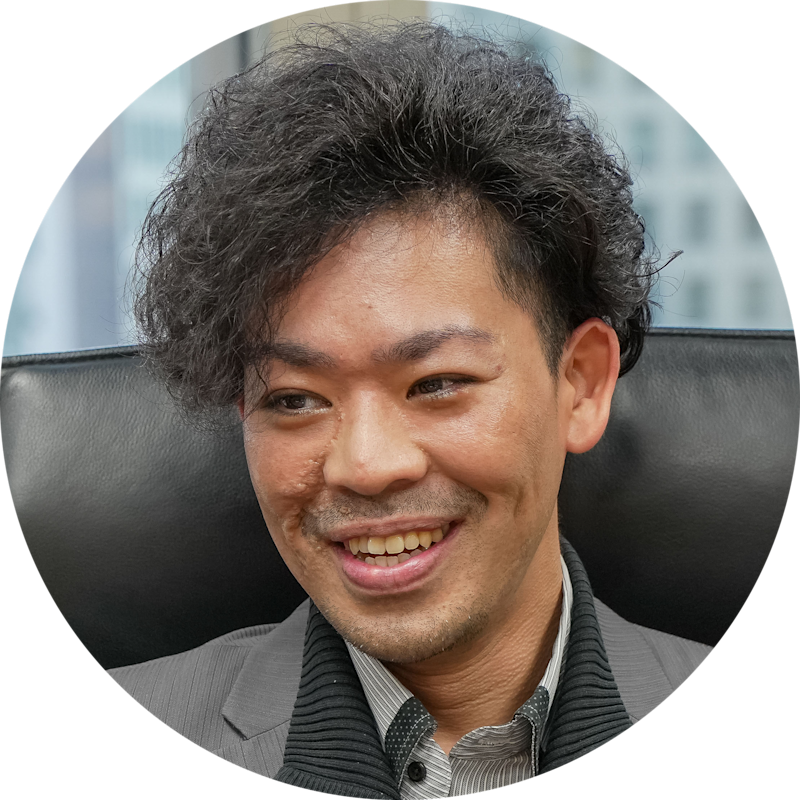
When I first heard about the proposal, I thought it was too unrealistic, to be honest.
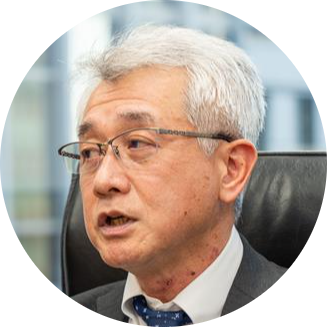
I thought it would be very difficult but never doubted the possibility of success. We were strongly inspired by Kawasaki’s passionate approach in inviting us to join forces to take up new challenges. We began to move forward together and cooperated to resolve the issues one by one, with our confidence increasing by degrees.
Working together to identify and assess every potential risk while sharing the thrill of developing new techniques
The implementation of the new system involved a slew of challenges to overcome, perplexing the client into thinking the plan was “too unrealistic.
One major problem was related to the inability to upsize the hull, which posed difficulties in terms of having to house the LNG fuel tank within the dimensions of the former hull while also meeting other conditions, including the requirement for the cargo hold to have the same level of capacity as the former vessel and the unavailability of deck space due to the presence of numerous structures.
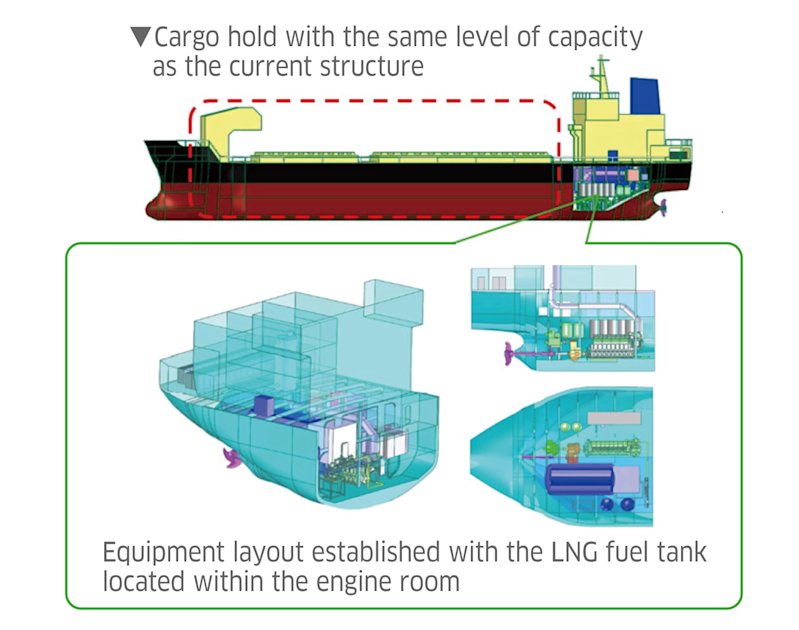
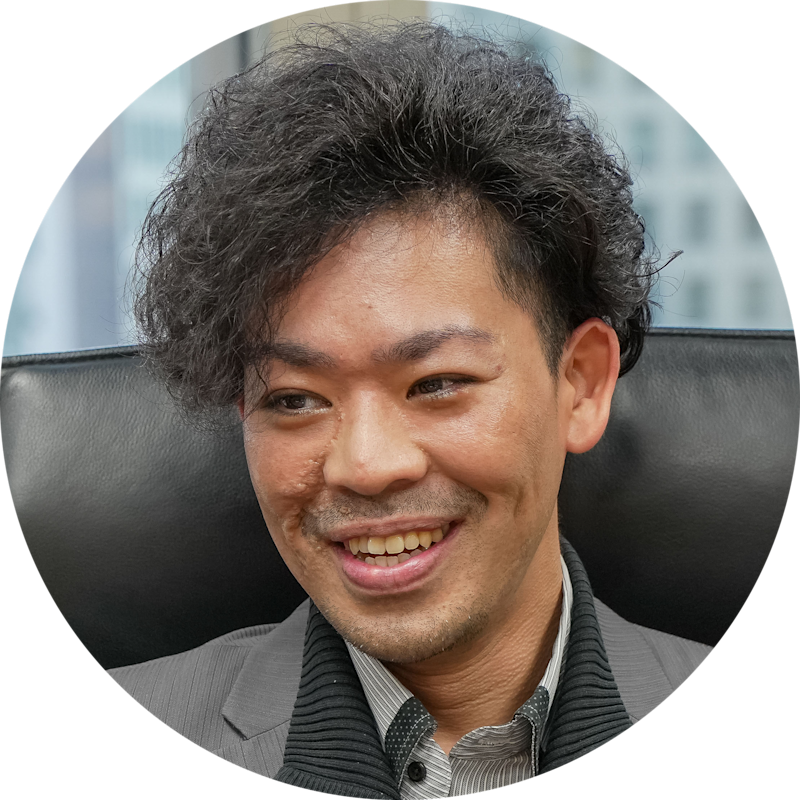
Receiving cooperation from the designer at the shipyard, we worked out special layout arrangements—chiefly by considering the geometry design of the cargo hold—to be able to locate the LNG fuel tank within the engine room while maintaining the same level of cargo capacity.
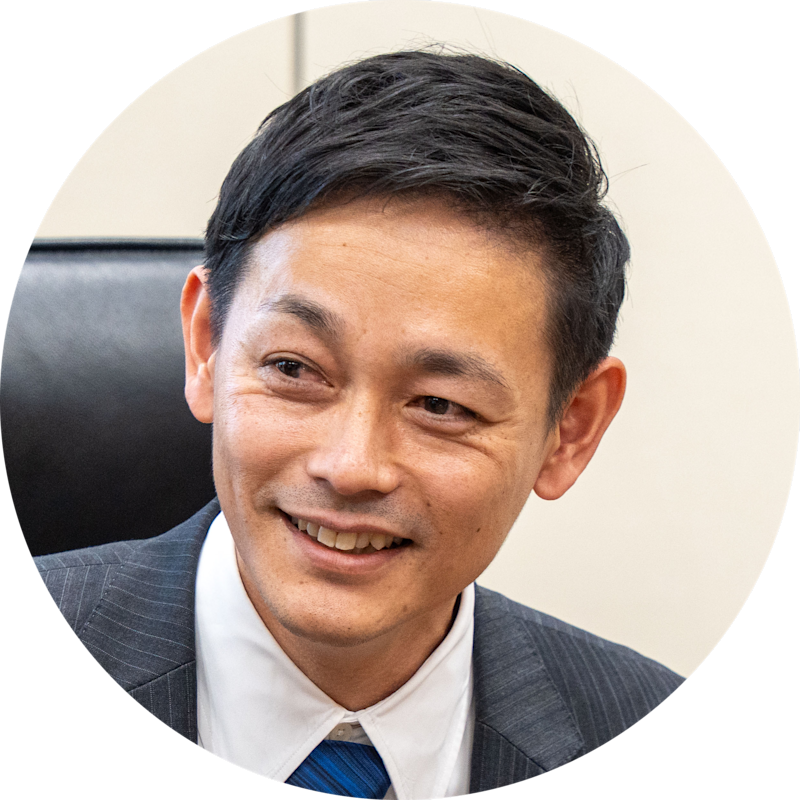
While promoting the pioneering project, we had to address a number of new issues without having any established models or standards to draw on. For example, we needed to consider the risks posed by the proximal placement of the LNG and a large-capacity battery, which could cause a disastrous accident in the event of thermal runaway in the battery. We therefore identified and assessed every potential risk and took control measures in cooperation with the shipowner and the shipyard, receiving guidance from ClassNK, a ship classification society.
The large-capacity battery system is housed in a dedicated room in a section separate from the engine room, where it is placed under strict temperature control to maintain good performance during the operating lifetime. Fire doors and firefighting equipment have been installed in the room to prevent the spread of fire in the event of the battery catching alight. Furthermore, for LNG fuel supply piping, a double-tube structure has been adopted to provide a system to detect a gas leak and sound an alarm if a crack appears in the inner tube.
The new shipbuilding project was given momentum by the earnest and inventive efforts of all related parties to resolve the mounting issues. Such eagerness was particularly apparent in the Kawasaki engineers, who took the extraordinary step of sailing across the Tsugaru Strait onboard the Shimokita Maru many times to study the navigation environment firsthand and identify clues for improvement.
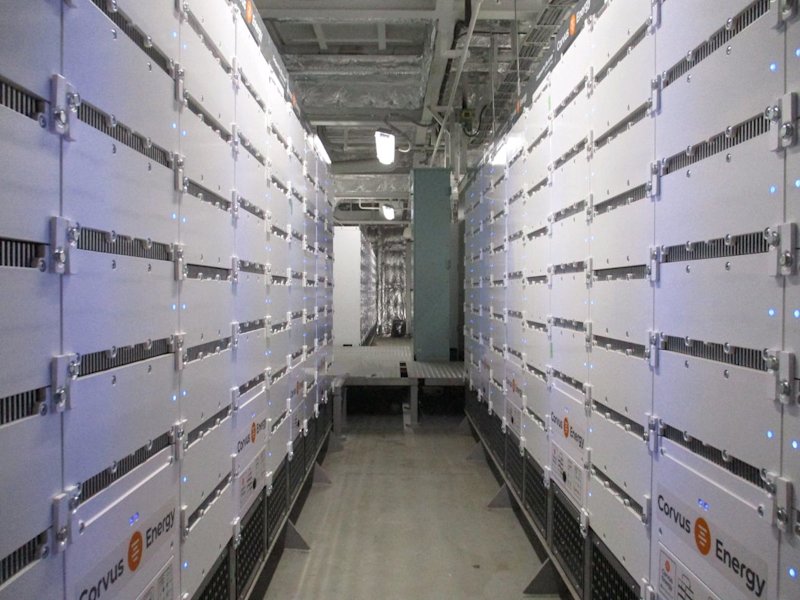
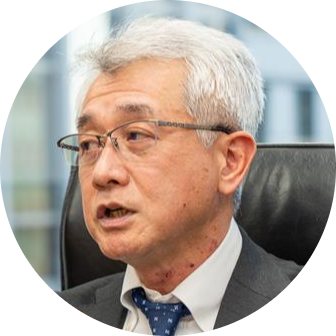
When we talked to specialists to verify new techniques, they expressed amazement about our strong commitment to undertake what seemed to them to be a ‘too adventurous’ challenge. And we did actually have huge difficulties implementing the techniques. We also had to summon additional ‘hustle’ to respond to the eager, almost monthly, requests from Kawasaki to allow engineers to come aboard the ship to perform studies, in addition to reporting on methods for solving issues. At the same time, however, we all shared the genuine thrill of witnessing a significant innovation and evolution of ship technology.
Fluctuation load on the main engine reduced, demonstrating the potential of the hybrid system
The new Shimokita Maru was delivered in March 2024 and immediately started service between Shiriyamisaki Port and Muroran. Since then, the vessel has made around 200 voyages over 10 months to deliver a total 1.01 million tons of limestone.
While supporting the stable performance of the vessel as described above, the hybrid system has made a substantial contribution to reduced GHG emissions, as mentioned at the beginning of this article. In addition, the system is also uniquely characterized by the low-level load fluctuation of its main engine, another advantage that is emphasized by Chief Engineer Kurotobi and Superintendent Yoshioka.
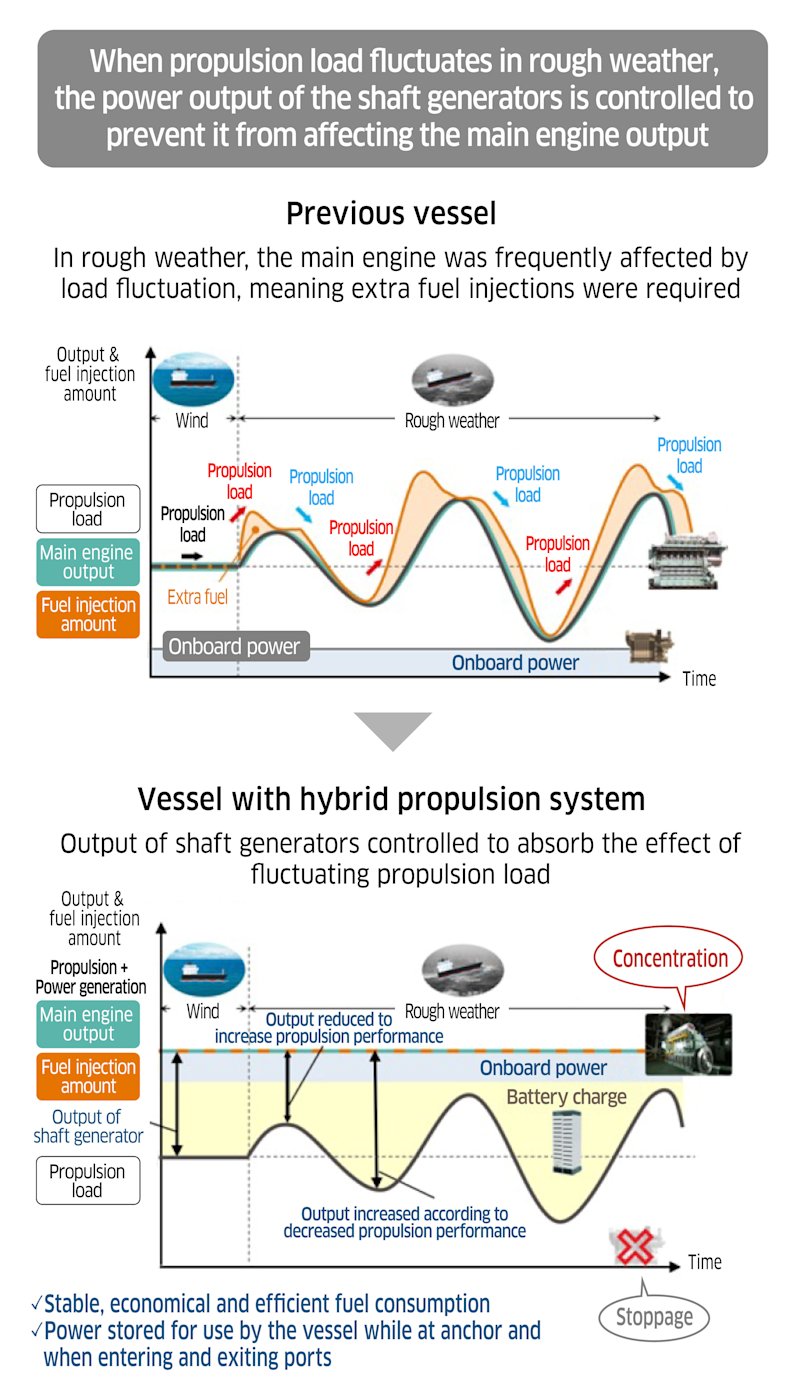
During rough weather, vessels at sea are normally susceptible to large fluctuations in engine output as a result of large waves. This can mean changes in the amount of fuel injected and often leads to extra fuel consumption. With the hybrid system, this issue can be addressed by controlling the output of the electric motor according to fluctuations in the propulsion load so as to absorb their effects. This is an example of the good hybrid coordination functionality that exists between the LNG engine and the electric system.
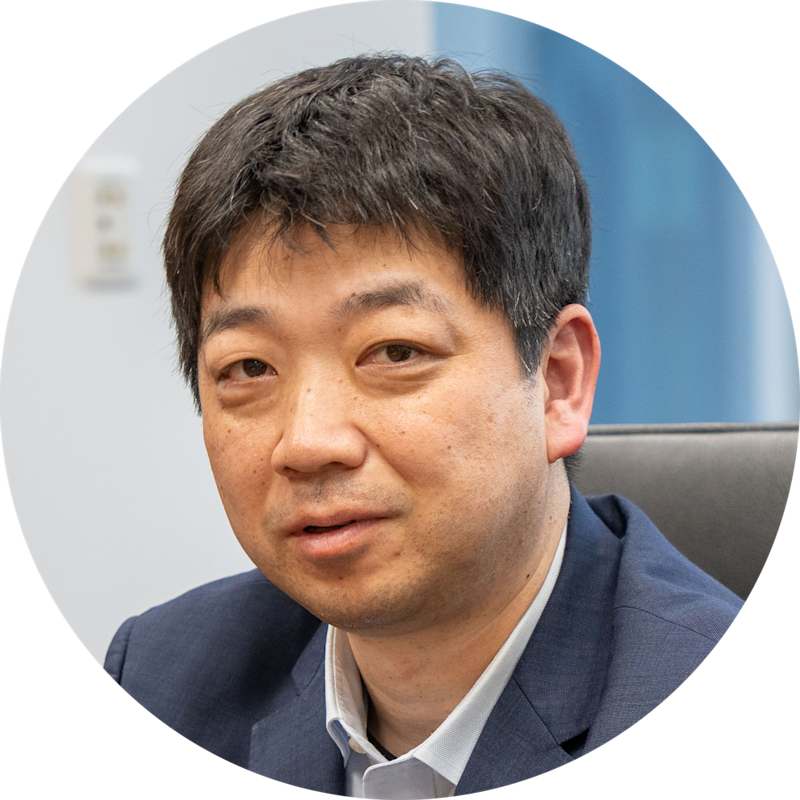
The Shimokita Maru has a rated speed of 12 knots and is capable of sailing at 10 knots even under rough weather conditions. Compared to propulsion load fluctuations that range from 5 to 10% on conventional heavy fuel oil ships, the hybrid propulsion system of the Shimokita Maru keeps them below 1%, which translates to stable and robust sailing performance. This is a significant benefit of adopting the hybrid propulsion system and thus provides support to the plan to introduce the system to various other types of vessels.
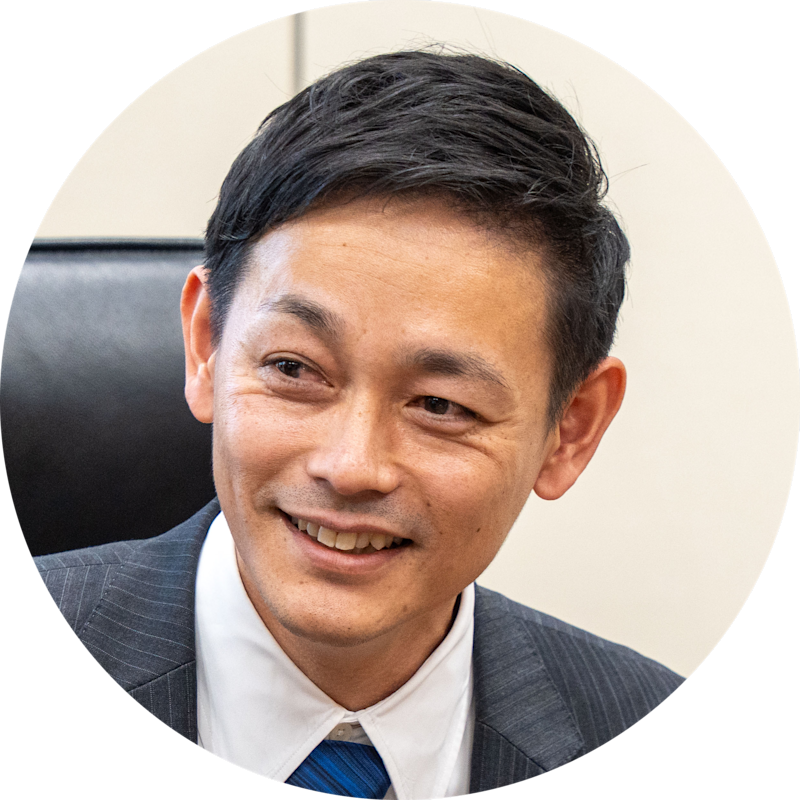
This is the feature that our control personnel worked hardest to achieve, ensuring efficient and stable operation even in the rough condition of the Tsugaru Strait. As a system integrator, we thoroughly understood the performance and characteristics of each device, repeatedly conducting simulations and validation tests using actual equipment, and finally arrived at optimal control.
The plan to adopt the hybrid system for the new Shimokita Maru vessel was backed by a number of favorable factors, such as the fixed service route and availability of LNG bunkering functions. Yet this does not necessarily mean a smooth expansion of the possibility of introducing similar advanced systems to the coastal shipping sector, where many service routes involve various types of ports characterized by different specific conditions and many difficulties will be posed by restrictions on vessel types and the limited availability of fuel supply infrastructure. The recent project represented a special case made possible largely thanks to suitable geographical conditions surrounding the service route, including for the size of the gas-only engine and fuel supply functions.
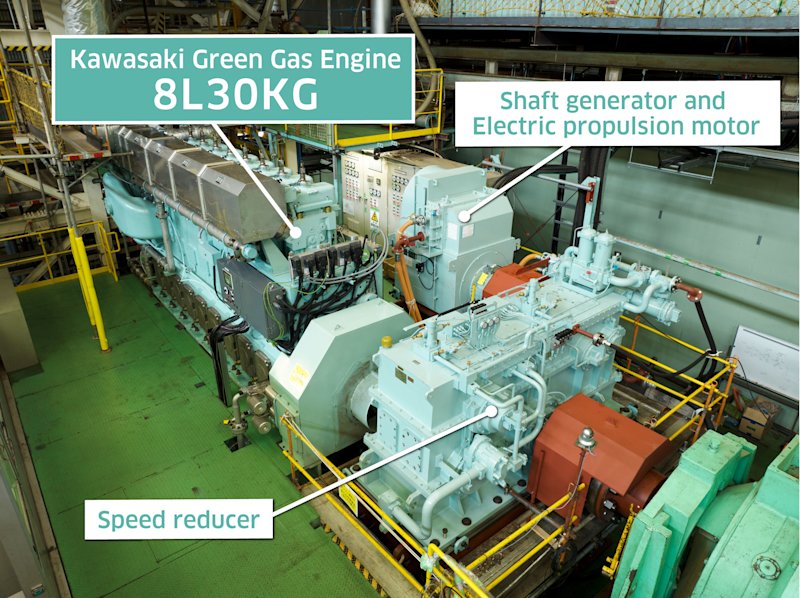
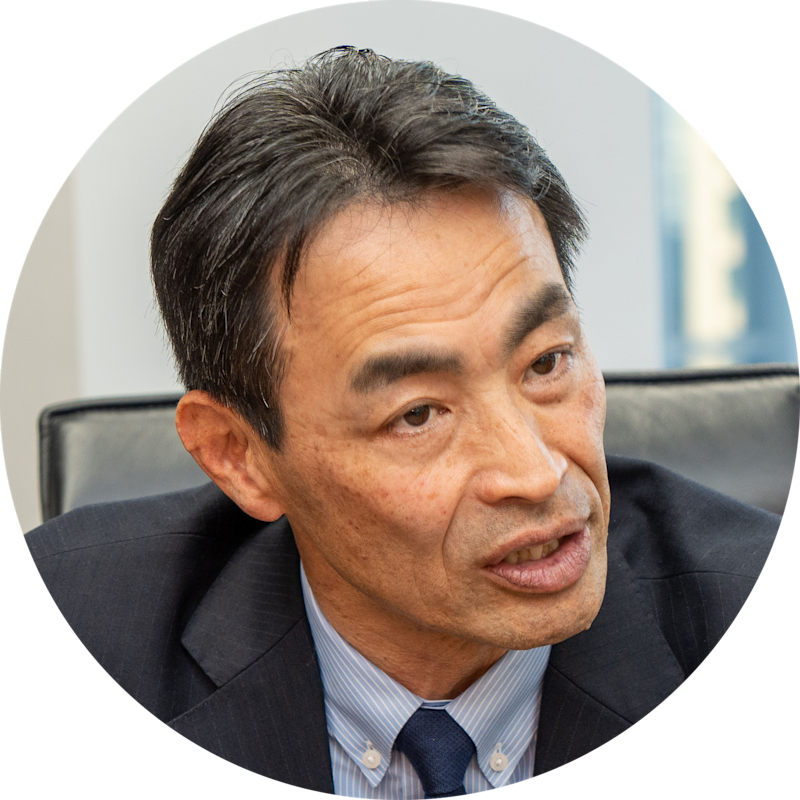
The successful performance of the new system demonstrated by the new Shimokita Maru has given momentum to efforts to promote the utilization of new energy sources such as hydrogen in pursuing this heading. In the recent project, the shipowner and shippers, our customers, worked with us to build systems for joint development, which we deeply appreciated, understanding the importance of promoting co-creation efforts for the purpose of implementing new technologies.
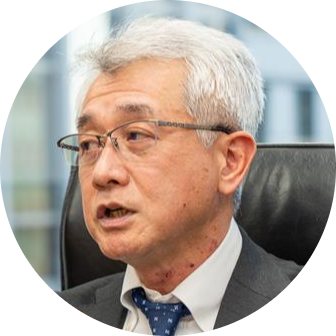
The hybrid system employed in the recent project is composed of the gas-only main engine and auxiliary battery system. I think it will be possible to develop a system in which the position of the two elements is switched. We should be open to adapting a diverse range of technologies to respond to user needs and offer optimal solutions. To this end, it is crucially important to receive cooperation from the user side. This recent project has solidified my understanding in this regard.
The successful delivery of the recent hybrid system project, a result of effective co-creation activities, has opened up a new path in ship technology.
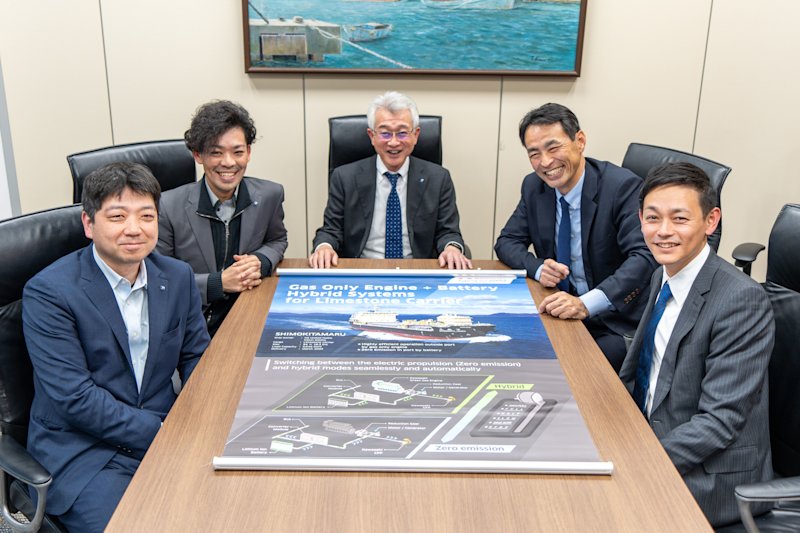