The asteroid explorer Hayabusa2 delivered a capsule packing surface materials from the asteroid Ryugu to the Earth and then left for a journey of deep space exploration on December 6, 2020. The mission took 2,194 days, 13 hours, and 32 minutes from launch with a total flight distance of 5,240 million km. The biggest achievement was sampling and bringing back substances from Ryugu—but do you know what devices were behind the success of the mission? They were the helical springs developed and produced by NIPPI Corporation, a group company of Kawasaki and the only aerospace-specialized manufacturer in Japan. The mission of Hayabusa2 could not have been completed without the great supporting actor that reliably performed sample collection, detachment, and release of the capsule to return.
Pivot of the Three Major Missions
Hayabusa2 succeeded in nine of the world’s first attempts during the mission of exploration to Ryugu, and four of them were related to sampling of surface and underground substances from the asteroid:
(1) The mission successfully retrieved samples from a C-type asteroid, which is considered to have water and organic substances.
(2) The samples contained gas outside the sphere of the Earth.
(3) The mission accessed underground substances of a celestial body outside the sphere of the Earth.
(4) The craft created an artificial crater.
The detailed observation of the course and before and after these operations was a considerable achievement.
Hayabusa2 tried to touch down on the Ryugu surface twice; the successful attempt was spectacular. The second touchdown was on the crater created by the Small Carry-on Impactor (SCI), which enabled sampling of underground materials that had been very difficult to obtain. The appreciation that sampling is Japanese specialty became firm throughout the world.
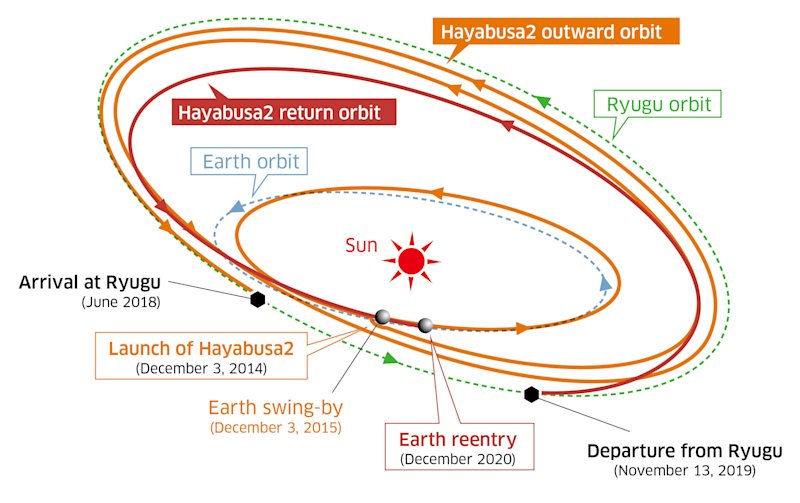
A variety of dedicated devices were required to sample materials from an astral body and return them to Earth: a sampler for collecting objects, the SCI to artificially create a crater, and the reentry capsule to return the capsule containing the samples to Earth. The wonderful supporting actors that helped achieve secure, stable operation of these devices were the special helical springs developed and manufactured by NIPPI.
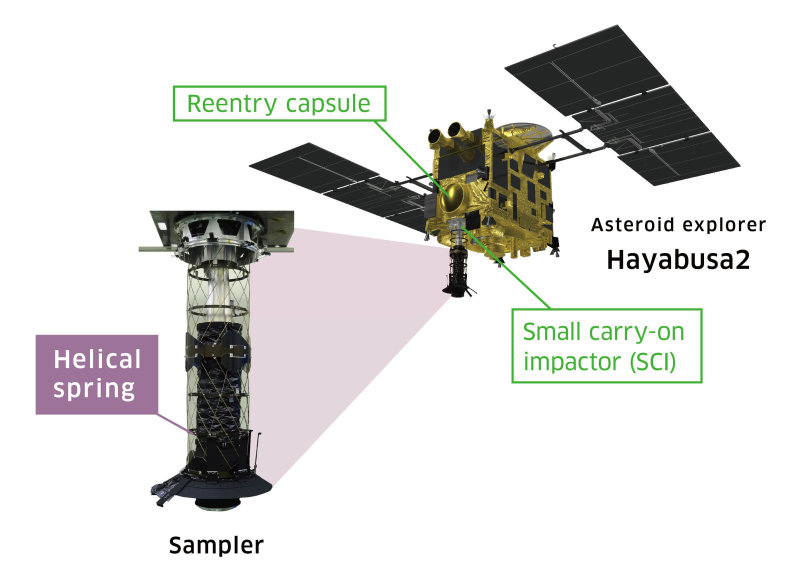
Both the sampler and the SCI, and even the reentry capsule, require execution of extension, detachment, and release, as well as other tasks, with an extremely high degree of precision and accuracy.
The helical springs under those circumstances used the spring force to accurately extend the devices or to give the best velocity and rotation for the release of the capsule while stabilizing the devices. Although they seem to be simple, analog tools at first sight, in reality, they are ultra-high-tech components based on an enormous number of experiments, simulations, and material studies so that 100% of the intended functions are executed
What Can Springs Do When They Elongate?
The helical spring looks exactly like a sieve without mesh. Learn how it works by taking the sampler extension mechanism used in the asteroid explorer as an example.
The sampler was folded and stored in the bottom of the body until the launch (Video 1). The device was 20 cm in diameter with a thickness (height) when retracted of 23 cm (only of the helical spring). However, the part stretched to 86.2 cm (ditto) after liftoff (Video 2).
Then, the explorer slowly touched down on the surface of Ryugu and promptly shot a bullet weighing about 5 grams at a velocity of 300 meters per second to pulverize the Ryugu surface. The crushed and lifted surface substances moved upward into the sampler horn and were caught in the sample catcher. A series of tasks was performed in the blink of an eye, and the spacecraft left lifted off after touching down and immediate jumping.
The mechanism is that upon release of the compressed state, the spring extends to guide and form the folded sampler horn. The role of the helical spring is to elongate when freed, which results in extension, detachment, release, or spinning to another device from the force. Therefore, the function for the SCI and the Earth reentry capsule is almost the same and very simple. However, Kazuhiro Abe, who develops and designs helical springs on the Space Structure Design Team, System Design Section, Engineering Department of NIPPI, says proudly that the devices look easy but are, in fact, awesome. Actually, there is a good reason.
Pushed Out and Spun to the Target Point
The helical spring consists of circular aluminum base rings and glass fiber-composite longerons arranged in the longitudinal direction, and the number of longerons is different: 12 pieces in two stages each for the sampler, 12 for the SCI, and 24 for the capsule detachment device.
The longerons are bundled glass fibers impregnated with epoxy resin and cured with a thickness of about 2 mm. Since the fibers run longitudinally, they bend well without breaking. Making use of this property, the helical spring is designed to shrink flexibly when a hold-down force is applied from the top and recover at once upon removal of the force (Video 3). Another important point is that the direction to push, whether clockwise or counterclockwise, does not matter.
Hayabusa2 is equipped with a helical spring 25 cm in diameter for the SCI, a 37.2 cm one for the reentry capsule, and a double 22 cm one for the sampler. The reason for the two-stage structure is explained by Abe.
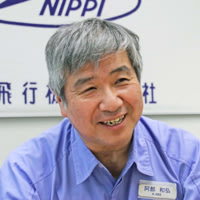
They are foldable in opposite directions to cancel rotation and enable linear elongation.
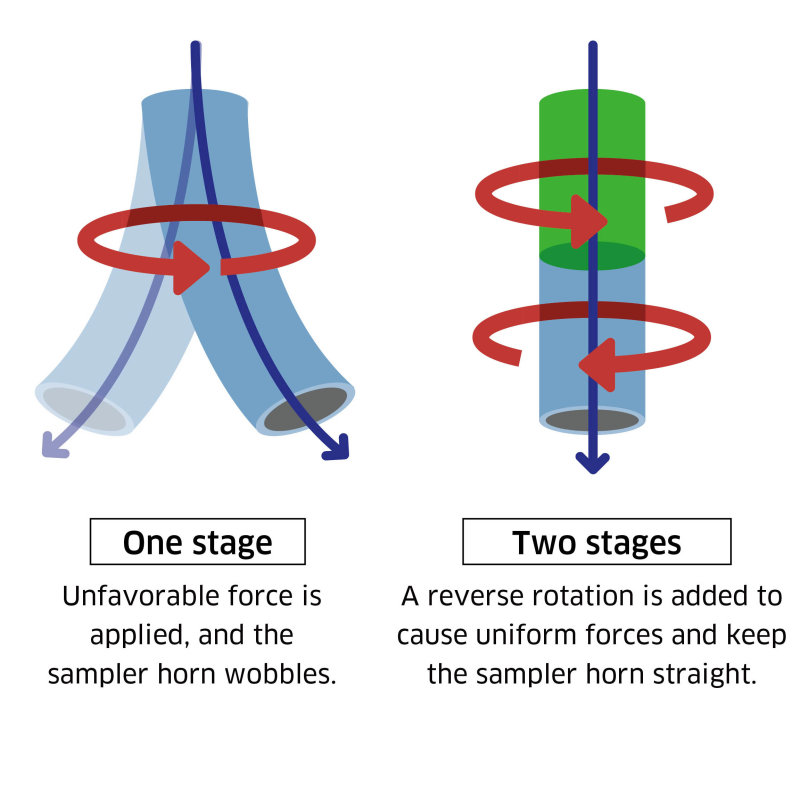
Now, you may have doubts. If the role is to push something out using the spring force, then do metal coil springs work the same? Abe answers as follows:
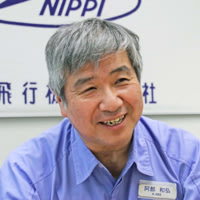
Glass fibers are lighter in weight than metal and allow stretching and compressing the spring a lot. The inner space of the spring is efficiently available. The biggest advantage is the stability to reliably elongate the spring so that devices can be extended, detached, or released accurately.
If coil springs are employed, more than one piece should be installed and compressed. Therefore, to detach or release a device, every spring must be released at the same time. Otherwise, balance is lost, and the object is not released accurately. In the case of the helical springs, the entire ring extrudes without tilting, resulting in a straight release.
Another reason is spin torque. Different from the sampler horn, the SCI and the reentry capsule must rotate. Spinning stabilizes the posture of the device, leading to accurate arrival at the target location. On the other hand, installation of several coil springs does not generate the same rotational force.
For example, when the metal bullet from the SCI exploded, it created a perfectly hollow crater in the ground, and the plane of departure needed to face the surface of Ryugu. However, if the pushing force for detachment or release inclines, the device would tilt in the direction of the strongest force or rotate out of control. Therefore, the SCI was designed to turn (rotate) like a top for stability so that the plane of departure always looked towards the surface of Ryugu (Video 4).
Detachment and release of the reentry capsule were also considered mission critical. Hayabusa2 entered the trajectory to drop the capsule toward the desert in Australia, and after several corrections, detached and released the capsule at 2:30 p.m. on December 5, 2020 (Japan time) at an altitude of 220,000 km. When it reached the atmospheric interface at an altitude of 200 km, the flight speed was 12 km per second, and the reentry angle was 12 degrees with the tiny tolerance of 0.2 degrees.
If the capsule had not detached and released in the planned direction at the predetermined angle according to the scheduled sequence at the expected time, it would have flown to a place different from the target point. This is why it is necessary to push out an object precisely and give it torque.
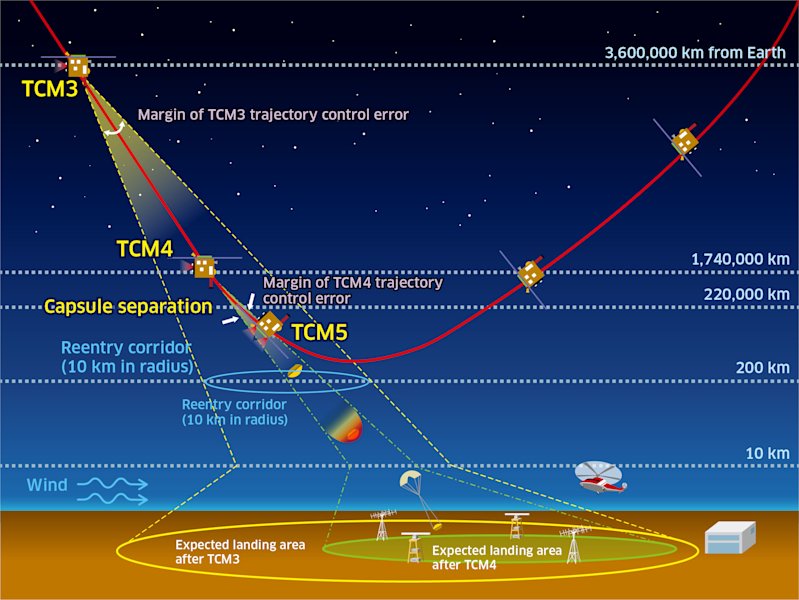
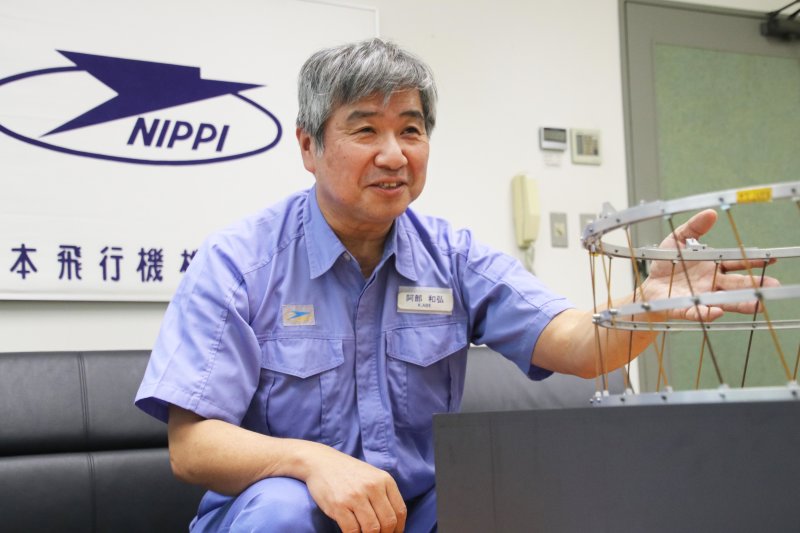
Profound Work together with Identical Brothers
The velocity and rotational speed generated by the helical spring were precisely determined for each device. In the case of the reentry capsule, velocity and rotational speed should be 20 cm per second and 10 rotations per minute. Abe says,
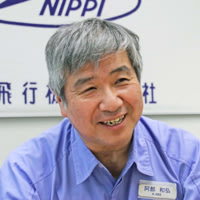
Then, how large should the helical spring diameter be and how long should the longerons be? How much rotational force would be generated from the configuration? And how much would the device body wobble upon detachment and release? These elements had to be considered in the design phase. The fruits of the enormous number of experiments and simulations established the space standard on the Hayabusa2.
As a matter of fact, the helical springs integrated into the Hayabusa2 have duplicates that were on the journey as well. These helical springs were delivered at the same time for long-term storage testing and used for inspections as a permanent set of springs preliminarily on the Earth before the real work. For example, the one for the reentry capsule had been checked for as long as six years. NIPPI developed the helical springs for reentry capsules jointly with JAXA, since the one for the former spacecraft Hayabusa.
Abe comments,
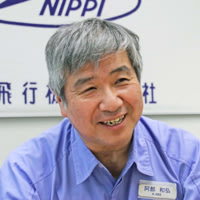
We have knowledge about the degree of permanent set compared with the condition at completion in the case of Hayabusa and it was used in this Hayabusa2 project.
The helical springs are simple but multifunctional and play a profound role indeed. It makes sense that Abe calls them awesome.
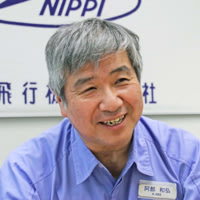
System Design Section
Engineering Department
Engineering / QA Division
Nippi