The location of mainstream oil field development is shifting from the land to the sea. In the search for rich resources at the bottom of the sea, people are digging wells in the seabed, connecting pipes, and pumping crude oil. This is a story about robots, called AUVs, devoted to working for humans in the dark, cold, dangerous deep-sea oil fields. They are the guardians of the sea bottom.
Thirty Percent of the World’s Crude Oil Comes from the Oceans
Almost seventy percent of the Earth’s surface is covered by ocean water, which humankind has been using as a valuable source of food since ancient times through fishing and salt making. The mother ocean is not simply home to sea creatures. Since becoming aware of the many minerals and energy sources in the ocean, human beings are looking to explore the untouched deep ocean frontier after having relied on resources from relatively small land areas. Full-scale offshore drilling and subsea oil field development started in the 1940s. The first case took place offshore of Louisiana in the United States in 1947.*1
Now, the world depends on oil for 30% of its primary energy. Although natural gas accounts for 20% and a diverse range of energy sources are used, the International Energy Agency (IEA) forecasts that for the period up to 2040, oil will supply 30% of the primary energy. Oil has been and will continue to be an irreplaceable resource for humans.*2
Regardless, trends regarding the locations of access to oil have changed. New oil sites have been developed mainly in the ocean since the 1980s. According to the IEA, subsea oil fields today produce 27 million barrels of oil per day, and 30% of global oil production is from the oceans.
*1: For the descriptions above, see “Offshore Petroleum History,” Oil and Natural Gas History, Education Resources, Museum News, Exhibits and Events, of the American Oil & Gas Historical Society
*2: For the descriptions above, see “Clarifying the Future World Energy in the IEA Report” of the Agency for Natural Resources and Energy, the Ministry of Economy, Trade and Industry
Oil Production Shifting from Shallow Water to the Deep Sea
The first oil field offshore of Louisiana was at a depth of a mere 18 feet (about 6 m). It was shallow enough that one could see the bottom. Then, submarine oil fields were discovered one after another in many parts of the world, and offshore drilling equipment gradually improved, which let people dive to 200 m, 300 m, and even deeper than 400 m.
Estimates indicate that the volume of oil of all subsea oil fields is now 260 billion barrels, or 15% of total global reserves, including onshore oil production. However, this number refers to the proven oil reserves, or the quantity evaluated with reasonable certainty as recoverable with currently existing technology. In brief, the more advanced the engineering, the greater the oil production. Innovations will increase the quantity of available oil.
The oil industry foresees that production from fields at depths of 400 or more meters will increase hereafter because onshore and shallow water oil production is declining in conjunction with the development of technology. Nevertheless, the steady production of crude oil from the dark, cold world of high pressures where deep-sea fish live quietly will obviously require complicated techniques.
What are the workings of offshore oil fields?
The gigantic derricks seen on the ocean are classified roughly into platforms (oil production facilities) and the oil rigs (drilling facilities). Below them are several wells on the seabed, and each wellhead has a controller called a “Christmas tree,” apparently because it looks like a tree with many ornaments (components) attached to its branch ends, to open and close valves and regulate the pressure.
The extracted crude oil is sent through a flowline pipe on the seafloor to a manifold integration device where several flowlines come together, and then the oil is pumped up to the platform through pipes called risers. According to research from UK-based Infield Systems Limited, demand was generated for pipeline inspections of the approximately 220,000 km of pipelines at the end of 2020, having grown 1.6 times in the past decade.
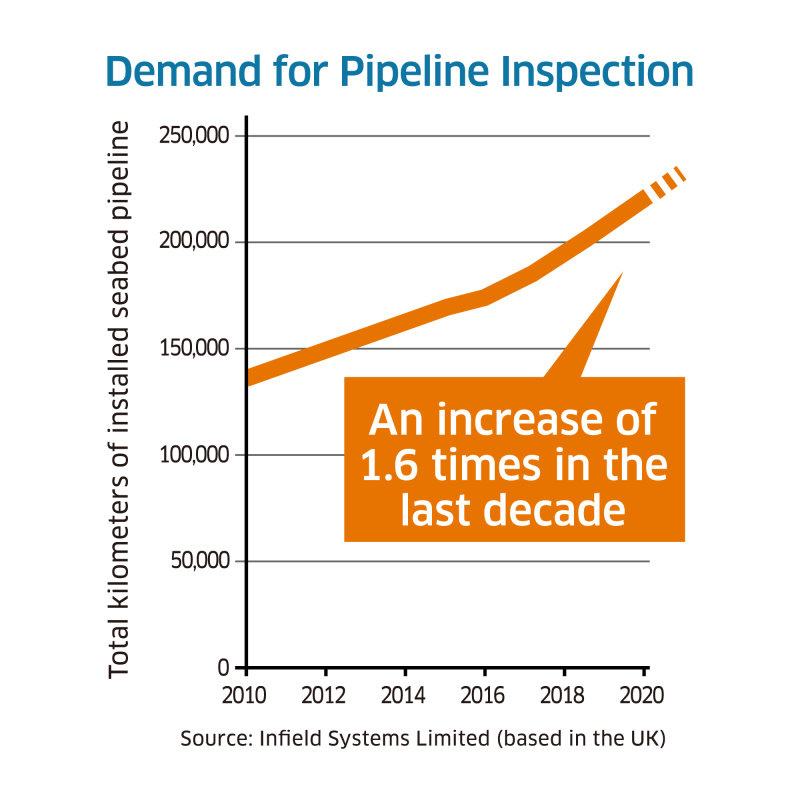
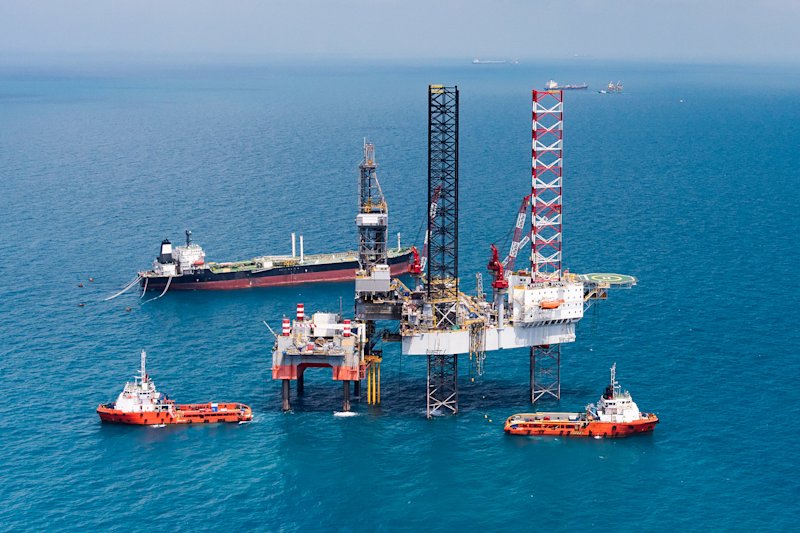
Pipelines—Vital Paths from Offshore Oil Fields
At a subsea oil field, we see huge derricks standing upright in the sea, and most people would think they have very large pipes suspended deep into the sea to draw and swallow crude oil from the deeper parts of the strata. The fixed platform type appears like the Tokyo Tower standing firm in the sea as the legs of the solid truss structure reach to the seabed. This method is advantageous in terms of stability but is limited by the depth.
On the other hand, floating platforms remain on the surface of the water and the pipes extend like the tentacles of an octopus with the ends clinging to the ocean floor. This system can be adapted to drilling deeper parts as the mainstream of ongoing offshore oil field development projects.
The following explains the floating facilities: multiple oil wells on the seafloor drill for the crude oil, which is sent through flowline pipes on the bottom of sea that come together into an integrated manifold device, where the oil is transferred to the above-sea platform derrick via pipes called risers. The oil produced at the platform is ultimately delivered through the export pipelines to the onshore site.
A network of pipelines on the seafloor is exactly equivalent to vital blood vessels for subsea oil fields. Once installed, the pipelines will be in service for several decades. Therefore, exhaustive measures to ensure security are implemented under strict regulations. Exposed to the constant effects of seawater, the pipelines cannot avoid the possibility of corrosion due to the salt and water, metal fatigue from the pressure, and damage and destruction from impacts. In addition, the pipelines are always vulnerable to a variety of risks, including seismic displacement and deformation and subsidence of the seabed. A single break can lead to a reduction in productivity and to severe environmental pollution. For these reasons, the maintenance and inspection of pipelines are important elements of keeping the pipes in good shape.
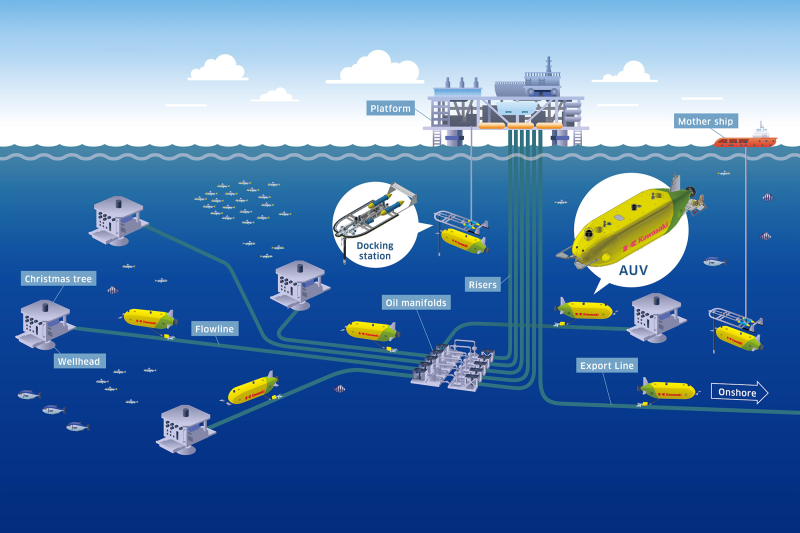
Emergence of Wired and Wireless Underwater Drones
Serious observations are essential for maintenance and inspections. In this area, specialists with a tough spirit, a robust body, and expert skills, called oil rig divers, have traditionally played active roles in subsea oil field development. However, divers can perform visual checks only in relatively shallow water up to 300 m deep; diving deeper is much more dangerous. How are maintenance and inspections conducted safely in the deep sea? The solution is underwater robots or unmanned submersibles.
Presently, remotely operated vehicles (ROVs) connected via cables to the mother ship on the ocean surface provide the maintenance work on the submarine pipelines. ROVs use high-performance cameras and sensors on behalf of human eyes to collect information like the underwater version of drones. However, despite the advantage of direct powering from the mother ship, ROVs have to be operated by skillful dedicated operators on the dangerous ocean, and the range of operations is limited by the length of the cable.
A newfound character to solve the issue is the autonomous underwater vehicle (AUV). Not tethered by a cable but able to perform tasks autonomously even in deep water, AUVs are the next generation guardians of the subsea oil fields as the substitute for ROVs. However, AUVs also have the limitation of operating time because of the absence of a continuous energy supply from the mother ship. Moreover, the new challenges encountered include the necessity of advanced, complex control technology for detailed autonomous work.
Inspecting 20 km of Pipeline on a Single Dive
Kawasaki’s SPICE overcame these technological challenges. Merging the extensive expertise of submersible vessels that Kawasaki accumulated for years and the sophisticated control techniques as a leader in industrial robot technology, the company developed the world's first AUV equipped with a robot arm. SPICE is the acronym for Subsea Precise Inspector with Close Eyes, which means the AUV carries out precise inspections by coming close to the object in the sea.
SPICE, or the commercial AUV developed with the target of release in the market in 2021, is a streamlined vehicle that looks like a small airship at 4 m in length, 1.2 m in width, and 0.9 m in height. The lithium-ion battery mounted in the core enables about eight hours of operation when fully charged. SPICE travels underwater at up to 4 knots (1 knot = 1.852 km/h) and at an average of 2 knots while performing a task. Thus, SPICE is capable of inspecting about 20 km of pipeline on a single dive.
Once SPICE begins navigating, the robot arm with inspection sensors embedded on the tip touches each section of the pipes, detects the condition, and collects data. When SPICE needs recharging, the AUV returns on its own to the docking station suspended from the mother ship, charges itself like a popular robotic vacuum cleaner, and sends the collected inspection data to the mother ship. After about four hours of charging, SPICE leaves again for the task on the seabed. This is the operational flow of SPICE.*3
*3: See the official Kawasaki Group Channel on YouTube.
Changing forward (SPICE ver.) ,and Autonomous Underwater Veh icle SPICE
Use of Technologies from the Creation of Submersible Vessels
While AUVs operate autonomously, cruising-type vehicles have already been used to investigate submarine volcanic activities by measuring the ocean topography, temperature, and salt content. However, a subsea robot that approaches and tracks pipelines, collects detailed data, and carries out monitoring and maintenance of equipment requires the following special features for each issue: (1) a body that can withstand the enormous water pressure of the deep seas, (2) efficient means of charging, (3) elaborate control technology for safe autonomous navigation, and (4) the capability of accurately collecting data for maintenance and management of pipes.
Kawasaki’s submersible technologies fostered for many years have resolved the first issue. Components offering excellent anticorrosion features were selected, and what’s more, the AUV was designed to navigate at depths of up to 3,000 m and withstand the extraordinary high pressure of 30 MPa, or loads of 3,000 tons per square meter applied to the vehicle.
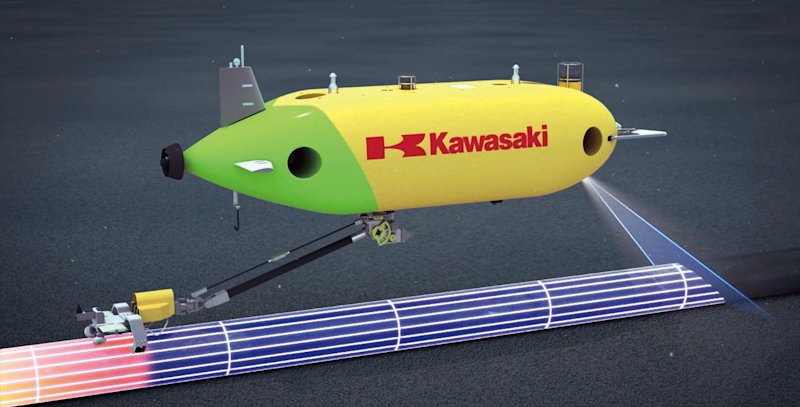
Reasons for Recharging in the Ocean
In order to address the second issue, a first-in-the world docking station method was developed. Noriyuki Okaya, manager of the AUV Department at Kawasaki’s Ship & Offshore Structure Company, says, “The most dangerous phases in the operation of an AUV are when it is launched into the water and when it is recovered.” Kawasaki devised a method for underwater power charging and data transfer to avoid the dangerous operations of repeated recharging.
Advanced control technologies are what counted to address the third issue. The think tank of Kawasaki, the Technology Division, played a vital role in the development of these latest technologies. A method for automatically tracking pipelines was developed in collaboration with Heriot-Watt University of Scotland, which is known for its excellent AUV research. A system for steady navigation was established, which enabled safe tracking in the jungle of pipelines on the bottom of the ocean to avoid any obstacles.
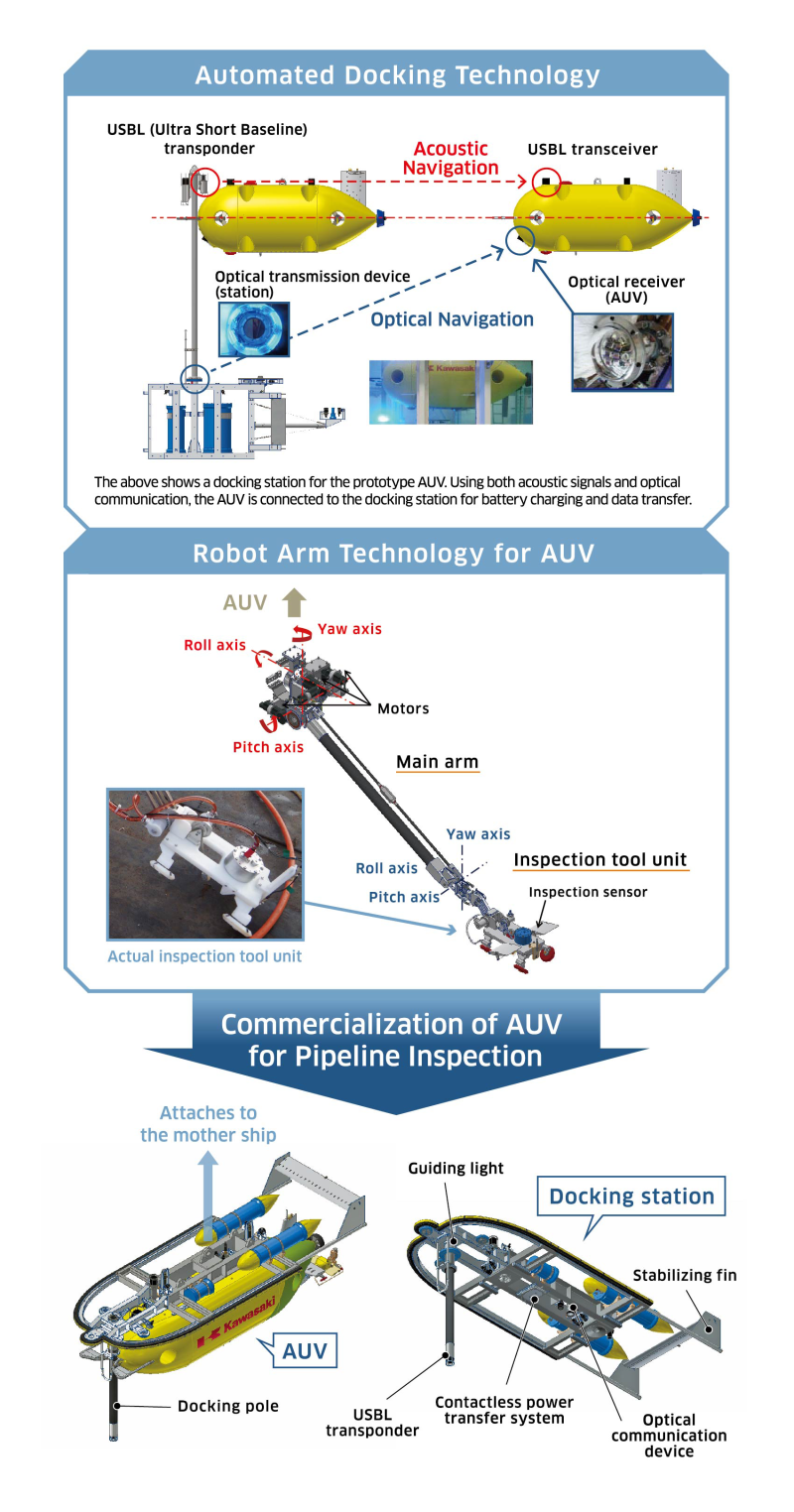
What happens when SPICE needs to recharge its battery?
The docking station is equipped with a transponder (emitter) and SPICE has a transceiver (receiver). When the battery level drops, SPICE locates the docking station using acoustic signals. As it approaches the station, SPICE is guided optically to catch the pole of the docking station using an M-shaped connection device at one end of the body. The vehicle's position is then fine-tuned using optical communication to complete the docking process. Charging is done using a contactless system.
Why was the docking station turned upside down?
The prototype station had a docking mechanism on the top, which was opposite the current configuration. For the commercial version, Kawasaki completely reversed the concept so that the station was suspended from the mother ship. Now, the AUV can be recovered or launched from the mother ship together with the station. This is a more efficient and safer method because it does not involve divers or boats to deploy or recover the AUV.
Competent Arm of Kawasaki’s AUV
The most unique solution is for the fourth issue. Kosuke Masuda, assistant manager of the AUV Department, Kobe Shipyard, Ship & Offshore Structure Company, comments, “Many of the AUVs developed by other companies inspect pipelines from a distance, which makes it difficult to collect precise data.” As described above, subsea oil field pipelines are like blood vessels, and the health of the “vessels” links directly to the overall performance of oil field facilities. The idea of a robot arm was created in order to achieve the mission of determining the condition of the pipe with greater precision and to avoid overlooking even a tiny abnormality.
The robot arm extending from the bottom of the SPICE body has a wheeled base at the tip with inspection sensors mounted there. The wheels of the base roll on the pipes as the AUV advances to collect the required data.
Even if SPICE sways from tidal currents, the root and tip of the arm have a mechanism to control movement along the X-, Y-, and Z-axes (roll, pitch, and yaw), and displacement is therefore absorbed automatically for continuous and steady inspections. The SPICE robot arm is incredible in that such delicate operations are possible under the harsh conditions of 3,000 m below the surface of the ocean.
Masuda explains, “We applied technologies developed through the design and construction of submersible vessels to the mechanism and structure of the arm dedicated to the AUV,” and adds, “We also received technical support from the Precision Machinery & Robot Company of Kawasaki to incorporate the accuracy and precision of industrial robots.” With the robust body structure derived from submersible vessels and dexterity of industrial robots, the SPICE robot arm is packed with Kawasaki’s cutting-edge technologies.
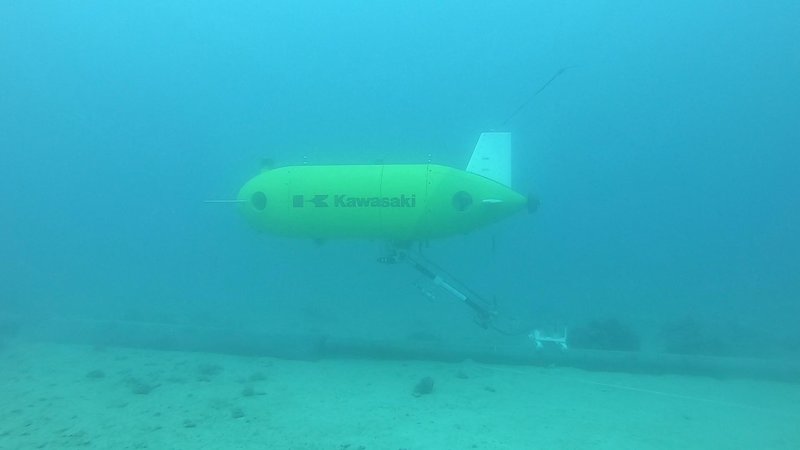
Long-Sought First Order Reception
A prototype (test model) of the commercial AUV, SPICE, from Kawasaki was completed in 2017. Since FY 2018, when the company started verification tests combined with a robot arm that had been developed concurrently, the shape and performance have been repeatedly modified to evolve into the arm in use today. Using the previous generation prototype, a public demonstration was conducted in Scotland in November 2017 for business operators associated with the subsea oil industry.
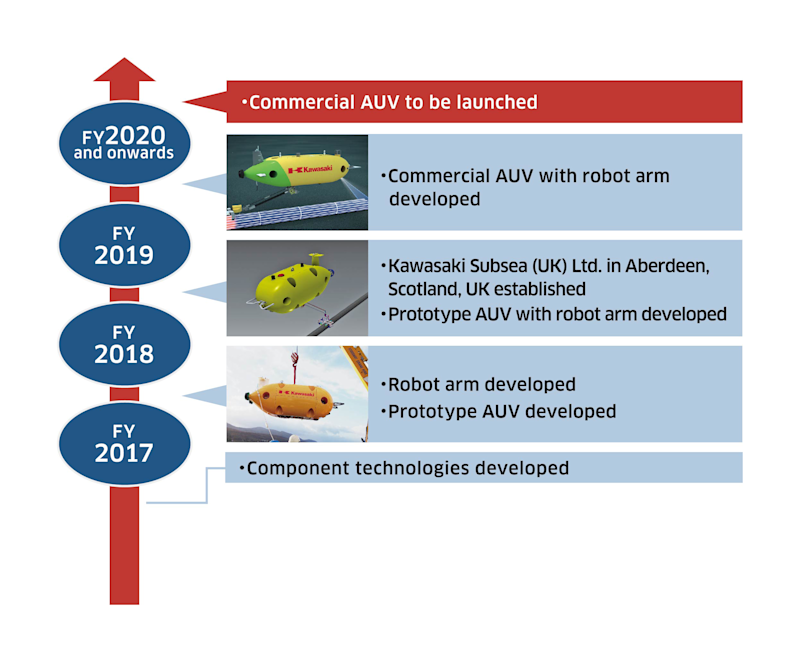
The positive comments of the guests who saw the demonstration stated, “I was impressed by the high hovering performance of maintaining its position in a 1 knot-class fast tidal current,” “I found the system compact, considering that its contactless underwater power transfer system was in the 5 kW class,” and “It’s important for AUVs to have more applications, such as inspection systems. I’d like to talk to Kawasaki more specifically about them.”
On May 18, 2021, Kawasaki received its first order for SPICE from an offshore maintenance service provider in the UK. They planned to acquire two SPICE units from Kawasaki with the first one delivered within the same year and used for operations to monitor submarine pipelines in the North Sea and other sea areas around the world. Kawasaki has indeed realized commercialization within FY 2021 as scheduled.
Nonetheless, Kawasaki is looking ahead to tomorrow. Okaya comments, “Speaking of the future of subsea oil field maintenance, we expect that the roles of ROVs and AUVs will be more clearly divided: ROVs will be used for heavy-duty projects, such as pipe replacements, and AUVs will perform inspections and other less heavy-duty missions.”
Imagine a huge platform in the vast ocean with humans on the surface and robots in the deep sea helping each other produce energy to support everyday life. Such an ideal workplace can be realized in the near future.
Subsea oil field pipelines correspond to blood vessels. Every one of the long pipes extended deep in the ocean is constantly subject to the risks of corrosion, deformation, and damage. In order to carry out the crucial task of inspecting these pipes more efficiently and safely, Kawasaki developed autonomous underwater vehicles (AUVs) with robot arms to maintain the healthy state of such pipelines. Traveling along the bottom of the ocean without a cable connection, Kawasaki’s AUVs carry high-performance cameras and sensors on behalf of human eyes. Furthermore, they have sensors installed on the robot arms to inspect the condition of the pipe sections and are equipped with a function to return to the docking station for recharging. Kawasaki has fostered the technologies for submersible vessels and industrial robots over many years, and the fusion of the two perfected the state-of-the-art guardian of subsea oil fields. Finally commercialized in 2021, AUVs will expand the fields of service worldwide.
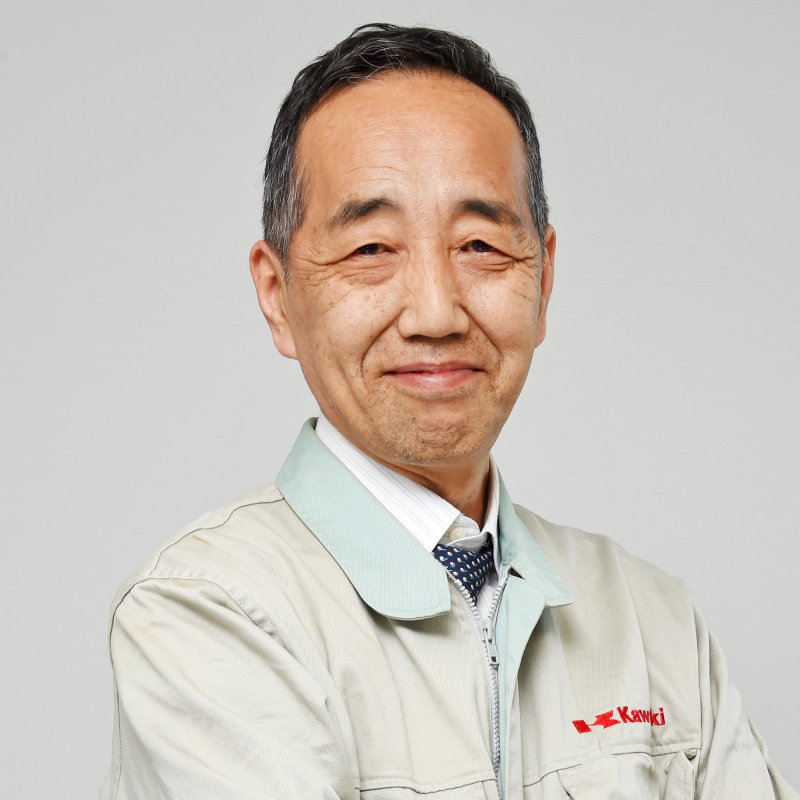
AUV Department
Kobe Shipyard
Ship & Offshore Structure Company
Kawasaki Heavy Industries, Ltd.
Innovative Technology Quietly Supporting Global Energy
For decades, Kawasaki has been building Soryu-class submarine vessels, deep submergence rescue vehicles (DSRVs), and other submersibles. We have thereby accumulated a wealth of technologies for underwater operations over the years. Actually, before we completed the Marine Bird AUV in 2003, we had already established the basic technologies for automated docking and the contactless supply of energy.
For the development of this commercial AUV, and in continuation of our R&D efforts, we again verified the component technology to resolve the different challenges, including the supply of energy, autonomous navigation control, and underwater communications. Fortunately, Japan enacted the Basic Act on Ocean Policy in 2007 to promote the protection of maritime rights and decided to support the development of such technologies. As a result, our development program for AUVs was subsidized, allowing us to continue our research and overcome the unresolved challenges.
This program supported our development of automated docking and contactless power transfer technologies, as well as the measurements to be carried out by the robot arm and autonomous navigation control algorithms—both achievements that were world firsts. We intend to collaborate with customers to upgrade the inspection unit at the tip of the robot arm. We also plan to use the robot arm for applications beyond the maintenance and inspection of subsea pipelines and would like to see it used with umbilicals for power transfer and control signal transmission, and offshore wind-farm cables for transferring power to onshore facilities.
In 2019, we established Kawasaki Subsea (UK) Ltd. (KSUK) in Aberdeen, Scotland, the UK, which is a hub city for North Sea oil firms, to focus on the sale of AUVs and to reinforce our ability to collect information on customer needs regarding AUV features. Based on the knowledge gained, we plan to launch the first commercial AUV into global markets in 2021.
Because the world’s demand for oil as an energy source remains strong, the trend to go deeper under the ocean to extract oil will accelerate. This means that the length of subsea pipelines will be extended, and various types of control equipment will have to function under harsher operational conditions. I am proud that we can deliver AUVs to the world in order to support global energy demand quietly from the bottom of the sea.
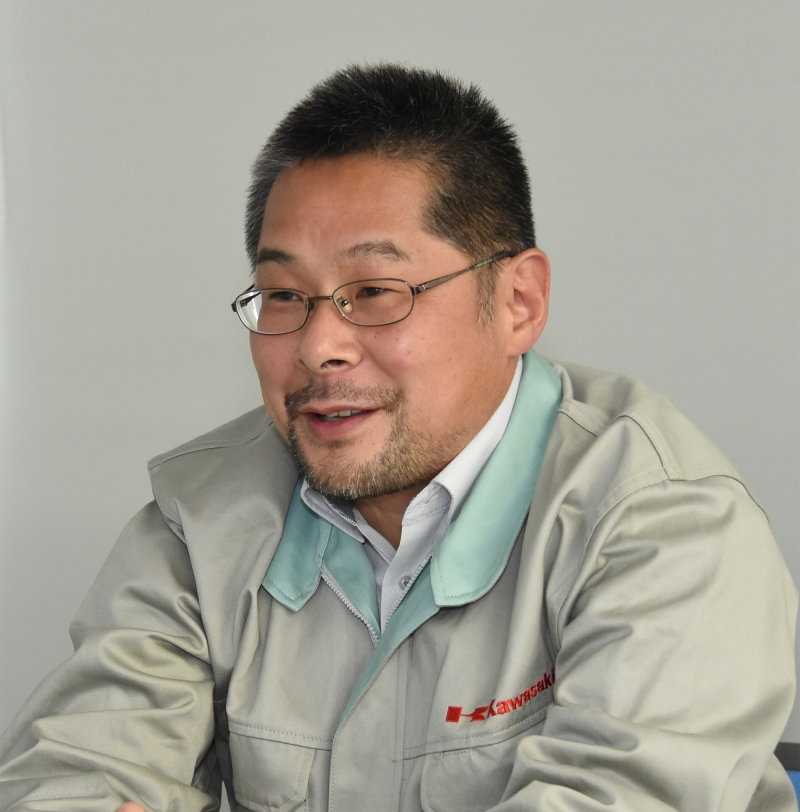
AUV Department
Kobe Shipyard
Ship & Offshore Structure Company
Kawasaki Heavy Industries, Ltd.
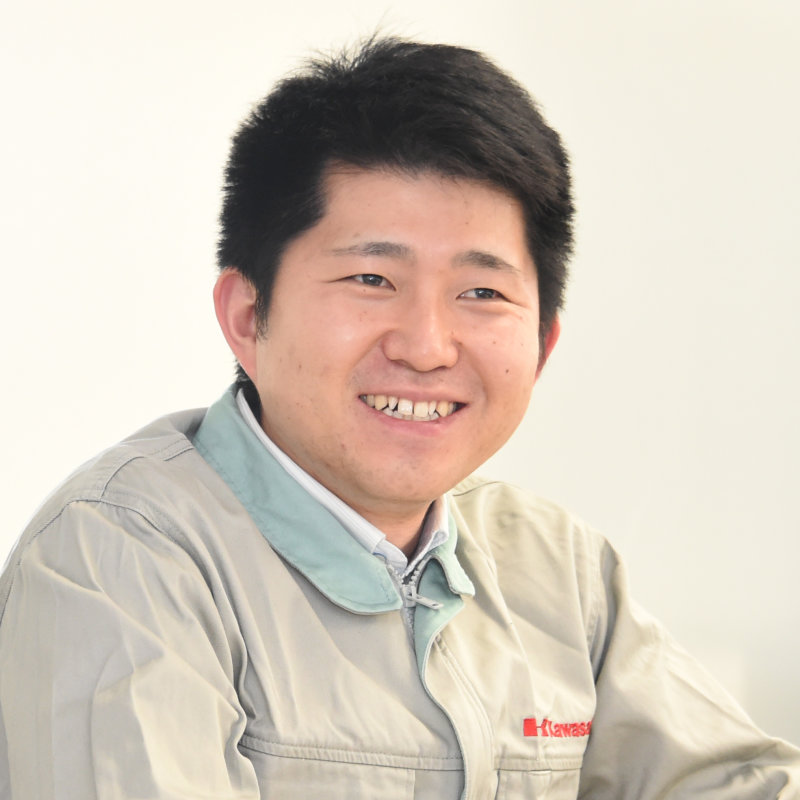
AUV Department
Kobe Shipyard
Ship & Offshore Structure Company
Kawasaki Heavy Industries, Ltd.
Note: The numerical values and job titles stated herein are based on information as of July 2020.