Kawasaki’s Liquefied Natural Gas (LNG) Carriers Packed with Innovations to Accommodate the World’s Energy Supply Needs
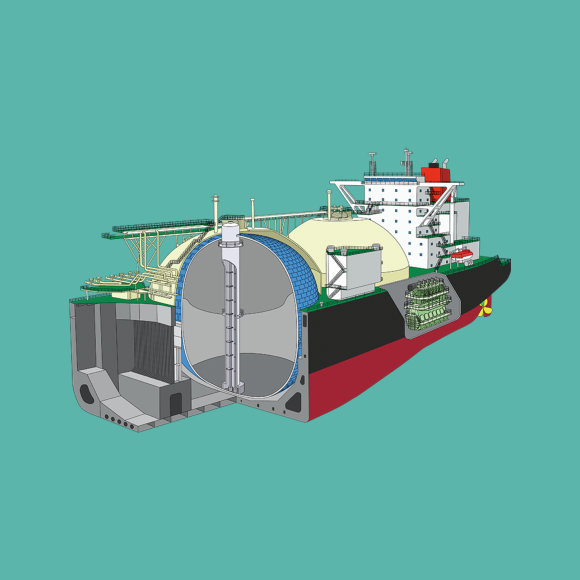
Emitting less CO₂ during combustion than petroleum and coal, liquefied natural gas (LNG) is an essential energy source in a low-carbon society. Kawasaki built Japan’s first LNG carrier in 1981. Presented here is an analysis of the techniques for fast, stable, mass transportation of LNG as it serves energy supply needs worldwide.
A leader in ever-evolving LNG carrier designs
Liquefied natural gas (LNG) carriers are marine vessels designed to transport natural gas liquefied at a cryogenic temperature of -162 ℃ at atmospheric pressure. Kawasaki is the first company to have built domestically-produced LNG carriers in Japan.
These vessels have three technological features:
- High-speed, energy-saving propulsive performance.
- The use of Moss spherical tanks, to achieve both a larger tank capacity and a reduced boil-off rate of LNG.
- Operational performance that achieves improved maneuverability and efficient transport operations.
Shipbuilders achieve good propulsive performance by optimizing the design of the underwater portion of the ship, in order to reduce hydraulic resistance during navigation, and also by improving engine performance. Optimization of ship structure, in particular, calls for time-tested technological expertise in LNG carrier building and ample navigational experience.
The level of such expertise directly affects the design capability of shipbuilders. As the builder of Japan’s first LNG carrier, Kawasaki boasts an unrivaled accumulation of knowledge and expertise in this field.
One invention that epitomizes this expertise is successful development of a proprietary propulsion system, powered by an electronically-controlled gas injection marine diesel (ME-GI) engine, which is capable of using boiled-off gas as fuel and re-liquefying the excess gas. This system results in the world’s lowest boil-off rate. Moreover, Kawasaki has developed a new non-spherical tank that allows for a ship design that enables it to maintain the required size to access major LNG terminals in the world and pass through the expanded Panama Canal, and, at the same time, achieves a larger carrying capacity of 180,000 m3. This advantage makes the tank suited to marine vessel application.
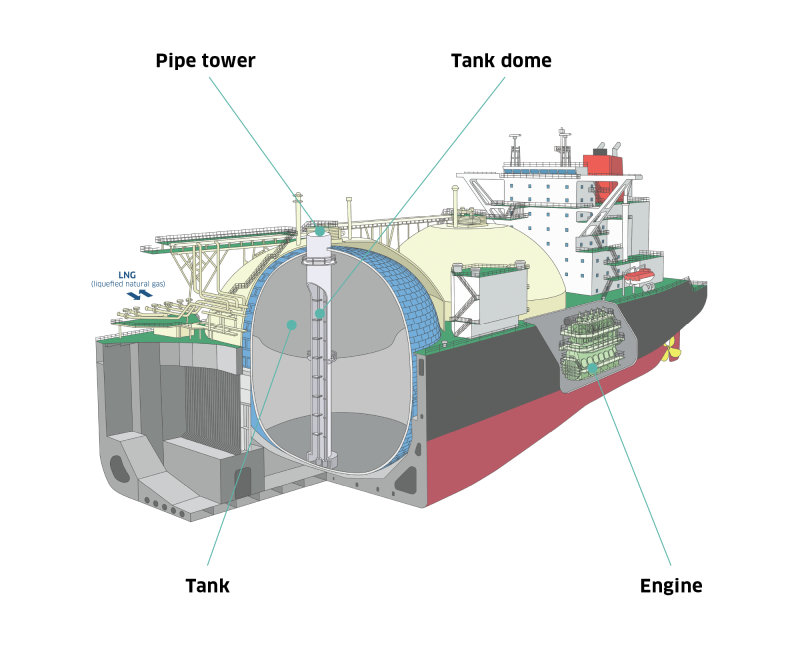
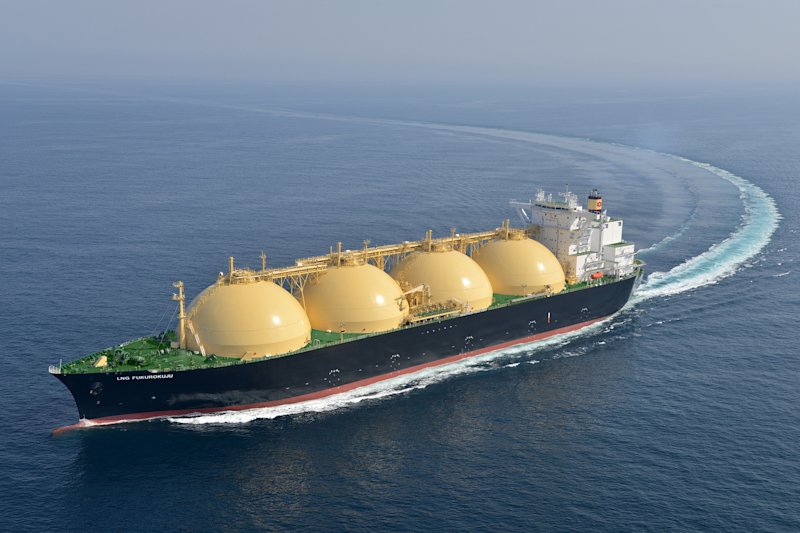
A cutting-edge, energy-saving engine that achieves the world’s lowest boil-off rate
Dual-fuel, slow-speed, gas injection marine diesel (ME-GI) engines are becoming mainstream for LNG carriers. The use of both boil-off gas (BOG) boiled off from the LNG in the cargo tank and marine fuel oil, combined with the ship’s unique structure, results in a significant improvement in fuel-efficiency. Moreover, by adding Kawasaki’s own BOG partial reliquefaction system to the propulsion plant, the company has achieved the world’s lowest boil-off rate at 0.05% per day, an impressive improvement from the 0.075% achieved by the tank's insulation performance alone. The system is designed to reliquefy BOG that was not used as fuel, so the system can be defined as one which completely eliminates waste.
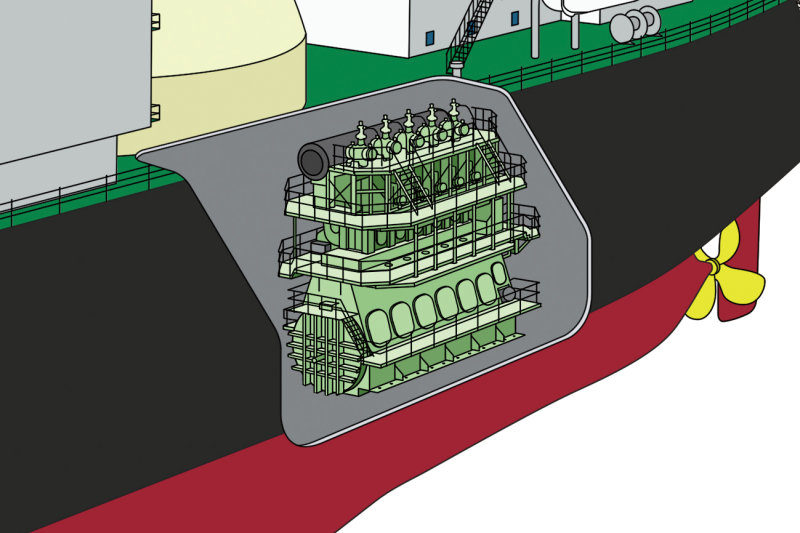
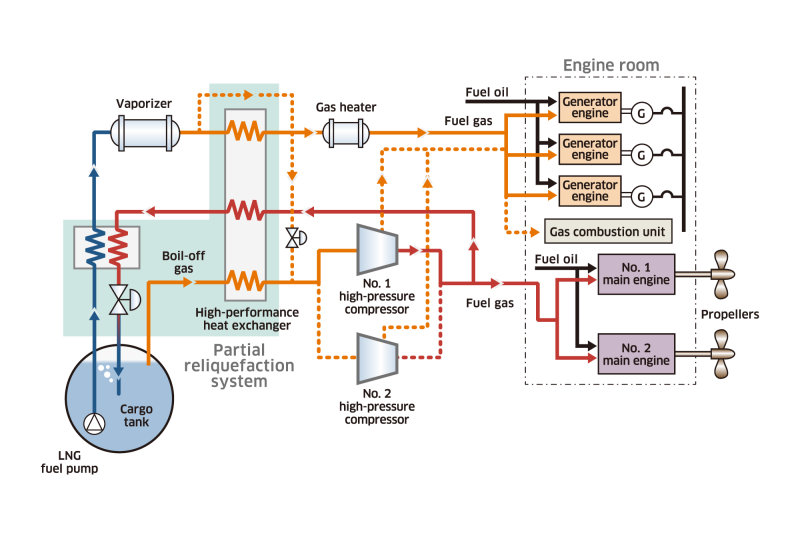
Reshaped tanks for use in a 180,000 m3 LNG carrier that meets the New Panamax requirements
Achieving a 15% increase in capacity compared to a conventional spherical tank of the same diameter and height, this newly-developed tank can be installed on ships that meet the breadth requirements (i.e., the “New Panamax”) to pass through the renovated Panama Canal. The combined volume of four of these tanks is 180,000 m3, an increase in capacity of 25,000 m3. The tank has been awarded Approval in Principle (AiP) from major ship classification societies.
The new tank’s design is based on the conventional spherical Moss tank, but viewed in vertical cross section, it is shaped more like a square rather than a circle. As a result, the space between the tank and the hull is reduced, allowing for excellent anti-sloshing performance (a prominent feature of the Moss tank), ease of inspection, and improved volumetric efficiency. The tank’s reduced height gives ships improved visibility from the navigation bridge, as well as increased stability.
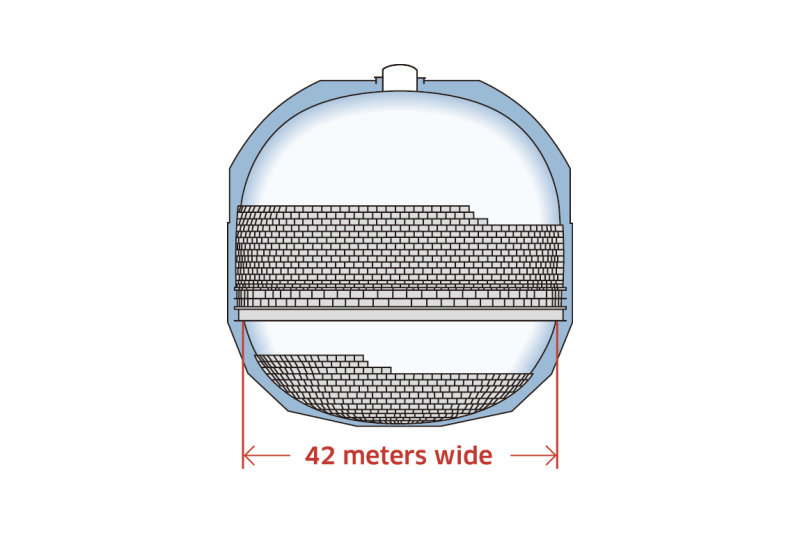
Cargo tank insulation system
The tanks are covered with thermal insulation panels based on Kawasaki’s proprietary panel system technology (“Kawasaki Panel System”). Each multilayer panel is composed of phenolic resin foam on the tank side, polyurethane foam in the middle, and an aluminum-plastic sheet on the exterior. The insulation panel is between 200 and 360 mm thick, achieving an excellent boil-off rate (thermal insulation performance) of less than 0.075% per day. Because of this performance superiority, the panel is being adopted widely by LNG carrier builders other than Kawasaki.
Tank dome
Located at the tank’s top, it holds various pipes housed in the tank and the service entryway.
Tank contraction
The tank contracts about 150 mm in diameter when it is loaded with LNG at approximately -162°C. However, this deformation is absorbed naturally by the upper part of the “skirt” that holds the tank, which also contracts as a result of being cooled.
Pipe tower
A tower placed vertically in the center of the tank, housing pipes for loading/unloading the LNG, cargo pumps to discharge the LNG to onshore facilities, a stairwell, and instrumentation. The cargo pumps are located at the bottom of the pipe tower to improve discharge performance.
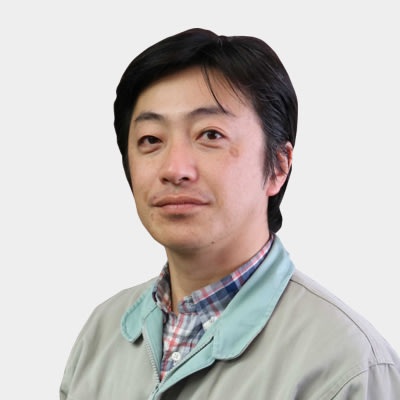
Initial Planning Section 2
Initial Design Department
Engineering Division
Ship & Offshore Structure Company
Kawasaki Heavy Industries, Ltd.
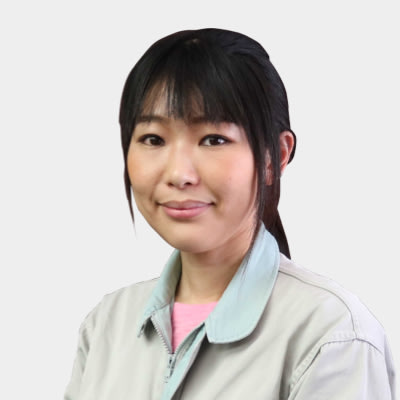
Initial Planning Section 2
Initial Design Department
Engineering Division
Ship & Offshore Structure Company
Kawasaki Heavy Industries, Ltd.