A staggering number of commercial aircraft travel the skies in our current era of mass air transport, and Kawasaki has played an essential role in the development of the engines that power these planes.
V2500 International Joint Development Project
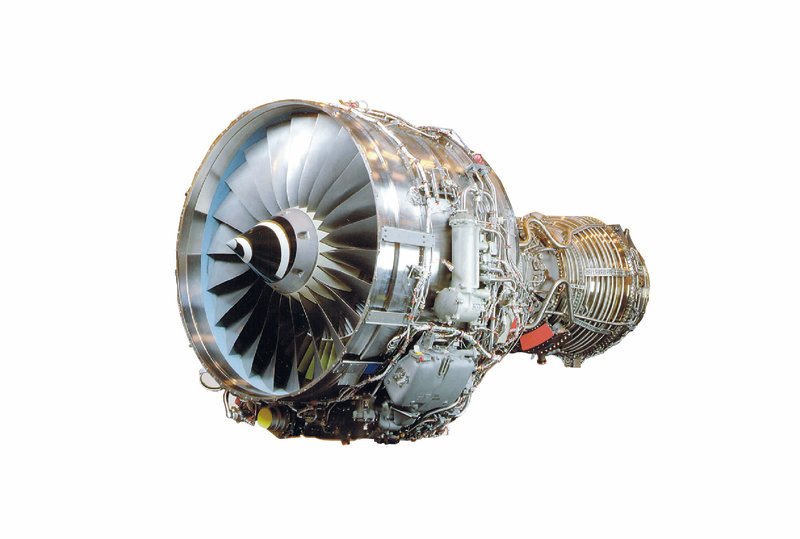
The V2500 was realized through a joint development project involving organizations from five countries, including Japan, the United States and several in Europe. Kawasaki took part as a member of Japan's project representative organization, the Japanese Aero Engines Corporation (JAEC), handling the design and production of fan casing, the low-pressure compressor (LPC), accessories and equipment piping parts. This engine has been installed on the Airbus A320 among other aircraft.
PW4000 Kawasaki's First Project as an RRSP
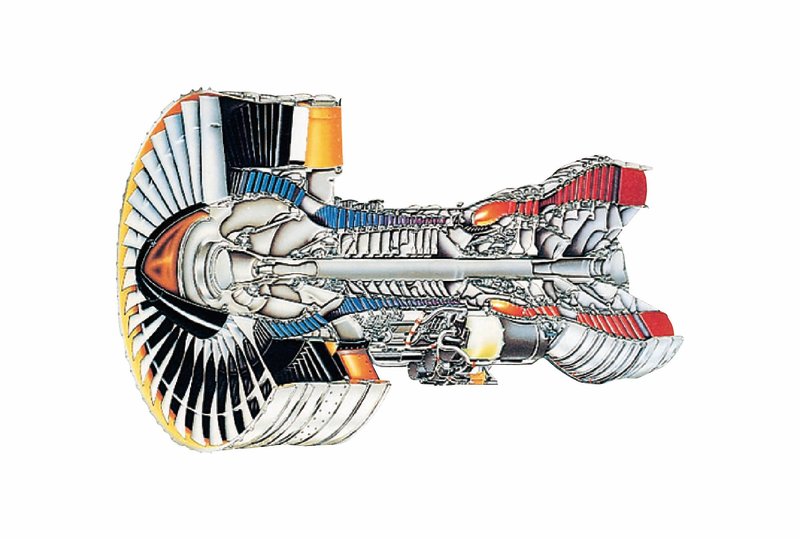
Kawasaki took part as an RRSP* for the first time in this joint development and production project with American company Pratt & Whitney (P&W), creating the casing, shafts, seal rings (to minimize leakage of air, high-temperature gas and so forth), vanes (stator vanes) and other parts. The PW4000 has been installed on the Boeing 747, 767 and 777; the Airbus A300, A310 and A330; and other aircraft.
*RRSP: Risk and revenue sharing partner. A partner that takes on a certain share of the project's risk in terms of development costs, production costs and so forth, and then receives a share of the revenues equivalent to the proportion of the risk borne.
Trent 1000 RRSP for IPC Module Development
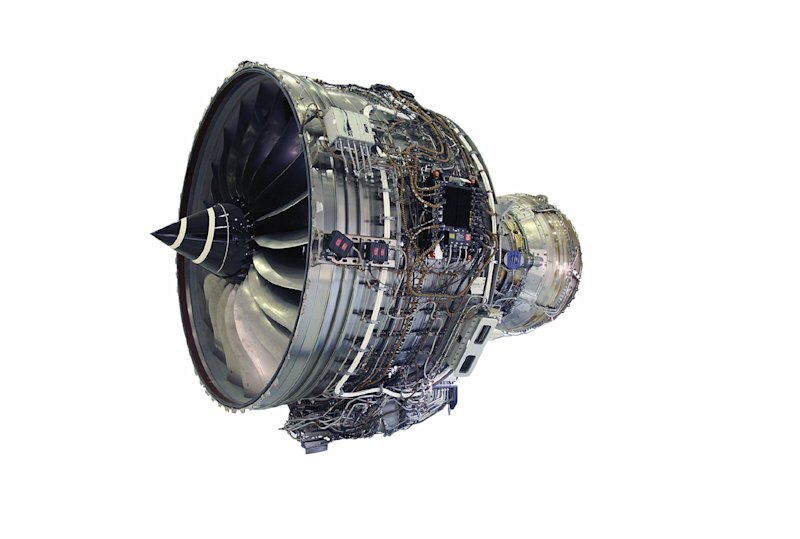
Kawasaki joined as an RRSP in this joint development and production project with British company Rolls-Royce Limited, this time taking part in the project from the design phase onward as a developer of the engine's intermediate pressure compressor (IPC) module. The IPC module is an important section of the engine located between the fan and the high-pressure compressor (HPC), where it further compresses by seven times the pressurized air sent in via the fan. In addition to helping with design, production and assembly, Kawasaki participated in a portion of the engine testing operations carried out as part of the development program. The Trent 1000 is used on Boeing 787 aircraft.
PW1100G-JM Joint Development of the V2500's Successor
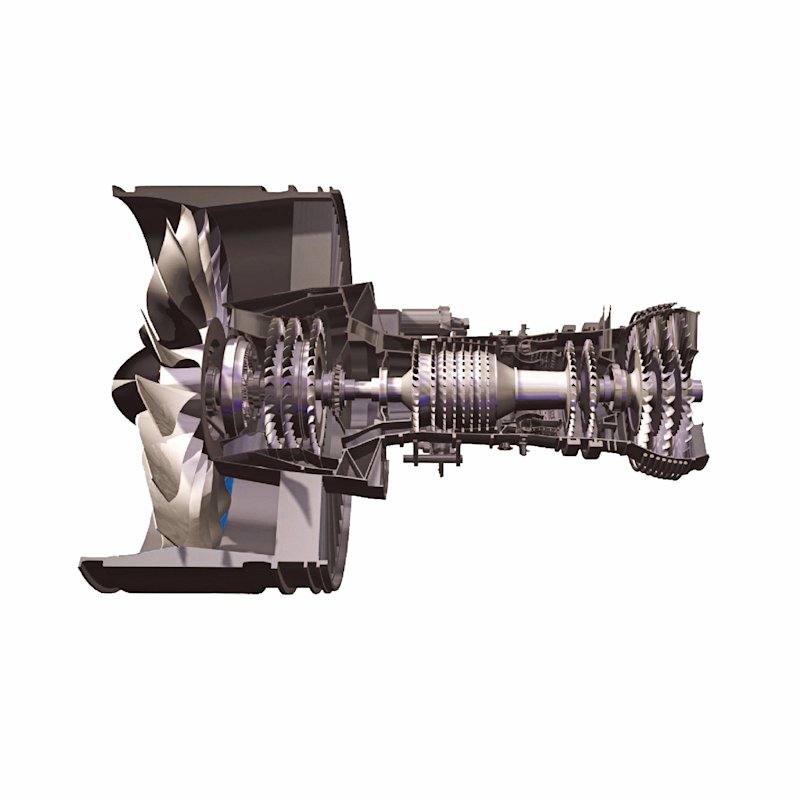
Kawasaki is responsible for the development, production and maintenance of the fan, low-pressure compressor (LPC) and other primary components for this engine, which is used in the A320neo, Airbus SAS's cutting-edge passenger jet. The PW1100G-JM is a geared turbofan engine utilizing an advanced gear system that rotates the fan at slower speeds than the LPC and low-pressure turbines. The advantages of employing leading-edge materials and component technologies include greater combustion efficiency, reduced exhaust gas emissions and quieter operation.
Kawasaki has refined its techniques and technologies over the years through numerous international joint development projects, and the Company is now widely considered to be an essential partner in the development of new engines for civil aircraft.
In 1971, research and development for aircraft jet engines was begun under the initiative of the Agency of Industrial Science and Technology--forerunner to the current National Institute of Advanced Industrial Science and Technology--under the then Japanese Ministry of International Trade and Industry. The FJR710 engine, developed with the participation of Kawasaki and others, was installed on the short takeoff and landing (STOL) aircraft Asuka, earning praise from around the world for its performance.This effort led to an international joint research project in 1983 to develop the V2500 engine for 150-seat aircraft, and later Kawasaki participated as an RRSP in international joint development projects with P&W and Rolls-Royce.
Later, Kawasaki went on to join other projects, helping to create the Trent 1000 engine for the Boeing 787 aircraft, the Trent XWB for the Airbus A350 XWB, the PW1100G-JM for the Airbus A320neo, the PW1500G and PW1900G for regional jet aircraft, and the Trent 7000 for the Airbus A330neo.
Kawasaki has played an important role in developing engines for many of the world's major aircraft that travel the skies today.
In the area of production technologies for engine parts, the Company has achieved a flexible manufacturing system (FMS) that integrates production and control systems throughout all phases of the production process. Kawasaki's FMS was developed jointly by the Jet Engine Division and Factory Automation and Robotics Division, and embodies the essence of the "All Kawasaki" approach.