In recent years, various social challenges, including environmental concerns and a shortage of truck drivers, have been accelerating a modal shift in freight transport. Due to these factors, rail is attracting increasing societal attention. As a leading manufacturer of locomotives and freight cars, Kawasaki is making a steady contribution to promoting this modal shift.
Supporting customers’ logistics strategies that bring about operational improvements
Today, companies are increasingly focused on upgrading their logistics strategies in an attempt to reduce inventory and achieve cost reductions. Another factor behind heightened interest in the transformation of logistics is a serious systematic shortage in the workforce of the trucking industry, which once accounted for 90% of the volume of domestic freight transport.
To cope with the shortage, the Japanese government and the transport industry have been promoting a shift from road transport to other means ― a modal shift ― and rail is top of the list as an absorber of this shift. Japan Freight Railway Company (“JR Freight”), with its nationwide network, happens to be Japan’s sole rail freight entity.
Yasutoshi Ohashi, head of Railway Business Headquarters of JR Freight comments, “Transport volume has been steadily increasing. Two of the driving factors are the enactment in November 2016 of the Paris Agreement on climate change and shippers’ increased use of rail in order to reduce their environmental footprint.” Ohashi says that JR Freight has been receiving business inquiries even from medium-range-transport sector competitors, namely trucking companies and airlines.
Rail offers a unique set of benefits, which includes an impressive volume of goods (the equivalent of 65 10-ton trucks) being transported by a single driver, which is also cost-effective; eco-friendliness, as freight trains emit only one-ninth of the amount of carbon dioxide as do trucks; and one of the world’s top punctuality ratings, achieving an arrival/departure punctuality score of 94%, while traveling the equivalent of five times around the world on a daily basis. Customers rate the company’s services highly, saying that with JR Freight, planning the receipt and dispatch of goods is easy, and because the company offers containers of various sizes, different packaging styles can be accommodated, which helps improve loading efficiency.
The modal shift to rail is becoming an irreversible trend, compelling companies normally competing with each other to share freight space, and forcing mass retailers to combine into one shipment goods from several vendors, in order to utilize rail freight and reduce overall logistics expenses. These developments demonstrate that strikingly unconventional strategies for streamlining logistics are being practiced.
Locomotives and freight cars are integral components of rail freight transport that underpin its safety, high-speed operations, and punctuality. JR Freight operates on a nationwide network of rail lines totaling 7,967.9 km, and owns 430 electric locomotives, 160 diesel locomotives, and 7,243 container cars. It also provides transport services for 1,883 privately-owned freight cars (as of April 1, 2016).
In conjunction with JR Freight, Kawasaki has been developing and manufacturing locomotives and freight trains, including the EF210 and the EF510 (electric locomotives), which operate on the Tokaido Main Line and Sanyo Main Line, Japan’s main railway arteries; the M250 (express container train); and the DF200 (diesel-electric locomotive), which serves in a very cold region of Hokkaido Prefecture. In terms of bogies (trucks), locomotives manufactured by other companies all use Kawasaki-made units.
Kawasaki also manufactures freight cars; the latest model of the Koki 107 freight car, for example, accommodates both compressed air and electric braking systems. Kawasaki is undeniably a leading developer and manufacturer of locomotives and freight cars in Japan.
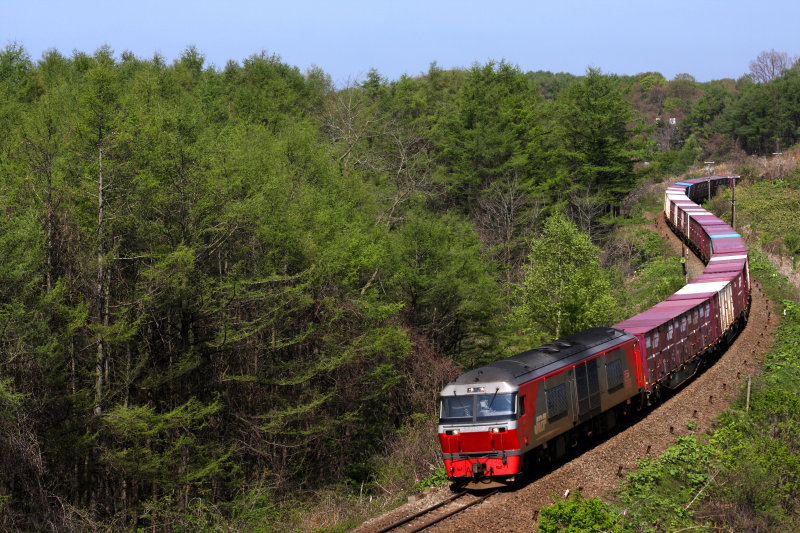
Creating world-class locomotives and freight cars
Naoto Yamamoto, who oversees the locomotives and freight trains, says, “The specifications and standards we expect manufacturers to meet are extremely high.” This is because, as a freight operator, ensuring safe and stable operations is a must. Another reason for these high-level requirements is dictated by JR Freight’s operational style, as it is renting the nation’s network of passenger rail lines for its operation. High-speed capabilities and minimal malfunctions are prerequisites for both locomotives and freight cars if they are to share rail lines with passenger trains operating on very congested schedules, and achieve improved service at the same time. If one of the freight cars connected to a locomotive fails, it brings the entire train to a halt and impacts the network almost to the degree that a disconnected rail line would. Because these trains carry a large volume of goods, as well, such incidents can have a serious impact on society.
Japan Railway Companies (operators of the railway network) require trains operating on regular lines to meet a 16.8 ton axle load limit (the weight placed on the rail by all wheels of one axle), in consideration of the strength of tracks and bridges. Some countries outside Japan have axle load limits exceeding 20 tons.
Yamamoto comments, “There is no country in the world other than Japan which operates locomotives that haul freight cars with goods weighing up to 1,300 tons, and freight cars that can withstand such extreme weight, given all the constraints and technological challenges arising from narrow-gauge lines, a topography full of slopes and curves, and a variety of weather conditions. Japanese locomotives and freight cars are world-class.”
Tetsuya Kawahigashi, who is engaged in the development and design of locomotives and freight cars at Kawasaki’s Rolling Stock Company, says, “We aspire to maximize the overall capabilities of locomotives and create the highest quality of freight cars.”
In developing the EF210 locomotive, Kawasaki introduced the concept of “30-minute-rated output”. Rated output is a maximum output in a set period of time, but is usually represented in terms of an hour. The EF210’s one-hour-rated output is 3,390 kW. However, the EF210 achieves a 30-minute-rated output of 3,540 kW, which is higher than its one-hour-rated output.
This improvement enables Kawasaki locomotives to climb steep gradients without the support of auxiliary locomotives, thereby eliminating the need to switch locomotives and making freight transport more flexible in dealing with various operating environments. A variety of technologies support this enhancement, such as VVVF (variable voltage and variable frequency) inverter control and a three-phase AC induction motor, resulting in a significant upgrade in overall performance.
A locomotive bogie is another product that must be fail-proof, and it is therefore packed with advanced mechanical technology to ensure high rigidity, durability, and gear performance. Yamamoto notes that all bogies used for new locomotives at JR Freight are manufactured by Kawasaki because, “They are definitely the epitome of technological expertise backed by time-tested development know-how.”
Manufacturing Processes of the Koki 107 Freight Car
An underframe serves as a platform for the cargo. Welding is used in assembling the cut steel plates and other steel materials comprising the underframe. Robotic welding is used for welding the bolster beams which hold the bogies (trucks).
Wheels, axles, and other basic parts used in making bogies are acquired from steel manufacturers.
Distortion resulting from welding of the cargo platform is measured and then the platform is heated to shape it into a perfect arch, a sophisticated technique derived from Kawasaki’s long-accumulated know-how.
Braking systems and pipes are installed to complete the bogie. This is a process to which utmost attention is paid, as it directly affects safety performance.
Metal connectors for securing containers, couplings, hand brakes, etc. are installed.
The underframe is then mounted on the bogie, completing the car, which has a load weight of 40.7 tons, a dead weight of 18.6 tons, and is capable of traveling at 110 km/h.
Manufacturing focused on enhancing customers’ transport services
With respect to development of new container cars, ingenious ideas are being introduced, including an underframe camber (a slight convexity in the center of the underframe) to absorb the weight of the containers and improve the overall stability of the cars. Unlike box-shaped passenger cars, container cars are structured more “two-dimensionally,” and become less stable without containers, because the container weight works as a stabilizer.
Kawasaki is also giving technological consideration to the stability of container cars being operated with less than full payloads.
The volume of transport service significantly expands when maritime shipping containers can be transferred from ship to rail without unloading and reloading the contents. However, because such containers are tall, when loaded onto container cars, they exceed height regulations. This has been hampering their wider application in the transport network. Yamamoto comments, “Development of container cars with lower floors is very much needed, but there are many technological challenges to resolve, such as redesigning their overall structure. We are currently summoning all our expertise to develop this new design.”
Speaking on Kawasaki’s approach to accommodating such customer needs, Kawahigashi says, “Locomotives and freight cars that rarely break down and require only simple and infrequent maintenance can render reliable performance for long periods of time. Such high-quality conveyances promote the expansion of customers’ transport services, and that's why we make the full understanding of customer requirements a high priority.”
Motokatsu Yoshizawa, who is in charge of Kawasaki’s sales activities for JR Freight, says, “Building locomotives and freight cars that last for 30 or 40 years and remain efficient in harsh operating environments has been achieved only through the ongoing, united efforts between JR Freight and Kawasaki. I’d like to make the value of such partnerships more widely known.”
Commenting on Kawasaki’s role in supporting railway transport as social infrastructure, Yoshizawa says, “We are committed to building a solid relationship of trust with our customers and dedicating ourselves to ensuring that our work is of the highest caliber. As a manufacturer offering an extensive lineup of transport products ― from locomotives, freight cars, and shinkansen cars, to transportation systems covering land, sea, and air ― I think it is our duty to utilize our extensive line-up of products and services in an integrated manner.
Offering a Variety of Services Using a Widespread Network
With the addition of the following three services as primary offerings, Japan Freight Railway Company has been expanding its portfolio of rail transport services, including international freight services, by collaborating with overseas shipping and freight transport entities.
- Maritime shipping container direct transport service
A rail transport service for 20-foot and 40-foot ISO import/export containers, using the Tohoku Express trains operating daily between Tokyo and Morioka, as well as other freight trains.
- “Sea & Rail” service
A door-to-door, integrated transport service connecting rail lines and high-speed ferries in order to transport 12-foot JR Freight containers, linking Busan and Seoul in Korea and Suzhou in China with Japanese cities nationwide. This service aims to achieve “transport that is faster than by sea and cheaper than by air.”
- Cross docking services
At freight sheds located next to Tokyo Station, Yokohama Station, and stations serving other major ports, cargo from ships is unloaded and immediately reloaded onto 12-foot rail containers. This cross-docking enables customers to import bulk goods using maritime shipping containers and reload them into 12-foot containers for nationwide distribution, achieving streamlined logistics.
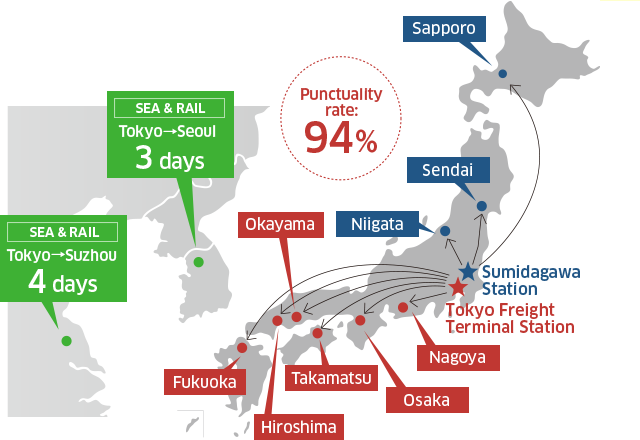
Rail Freight System
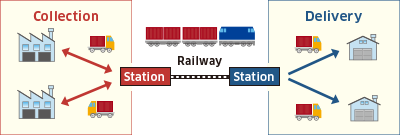
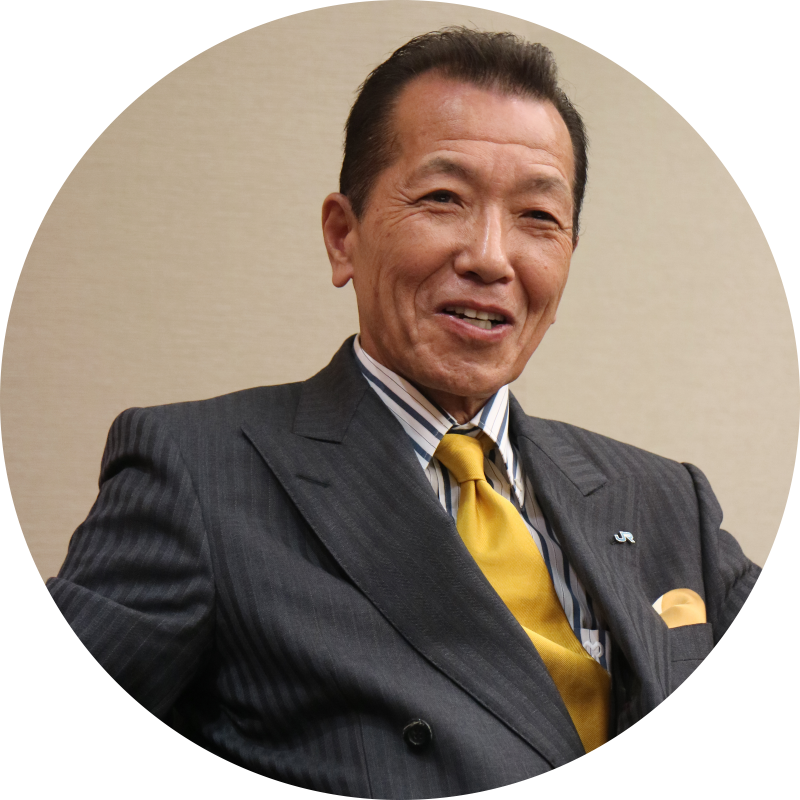
Chief Safety Management Officer
Railway Business Headquarters
Japan Freight Railway Company
Taking Modal Shift to the Next Level High Expectations for Kawasaki as Our Key Partner
We consider expediting modal shift to be a vital initiative for companies to pursue in addressing environmental and energy issues, beyond considerations for private gain.
To that end, JR Freight has developed a 31-foot container loadable onto 10-ton trucks, increased the frequency of operations on high-volume transport lines, and formulated strategies to promote the use of rail transport by customers desiring to transform their logistics by finding more efficient ways to transport low- to medium-volume goods. We also improved cargo collection systems, constructed a large transport hub at the Tokyo Freight Terminal Station, and took various other measures to enhance our services.
What our customers expect of us is to see their cargo transported safely, without fail, expeditiously, and inexpensively. The development of new models of locomotives and freight cars is one of our key initiatives to meet those expectations. Our freight trains have already achieved their maximum speed of 110 km/h on main lines, thanks to our collaborative efforts with Kawasaki.
Of course, there are yet many challenges to resolve, including improvement of high-speed locomotives, development of AC/DC dual‐current locomotives that can operate nationwide in a unified, standard manner, and safer and more driver-friendly locomotives utilizing IT. Therefore, we expect much from Kawasaki.
Kawasaki is always innovative in designing new freight trains and, at the same time, honest in dealing with problems when they arise and conscientious in the way they remedy them. Such an approach provides strong support for our business.
In the future, JR Freight will be collaborating with Kawasaki in building an overseas freight transport network. We would like Kawasaki, as our key partner, to work with us in developing locomotives and freight cars that best meet local requirements.
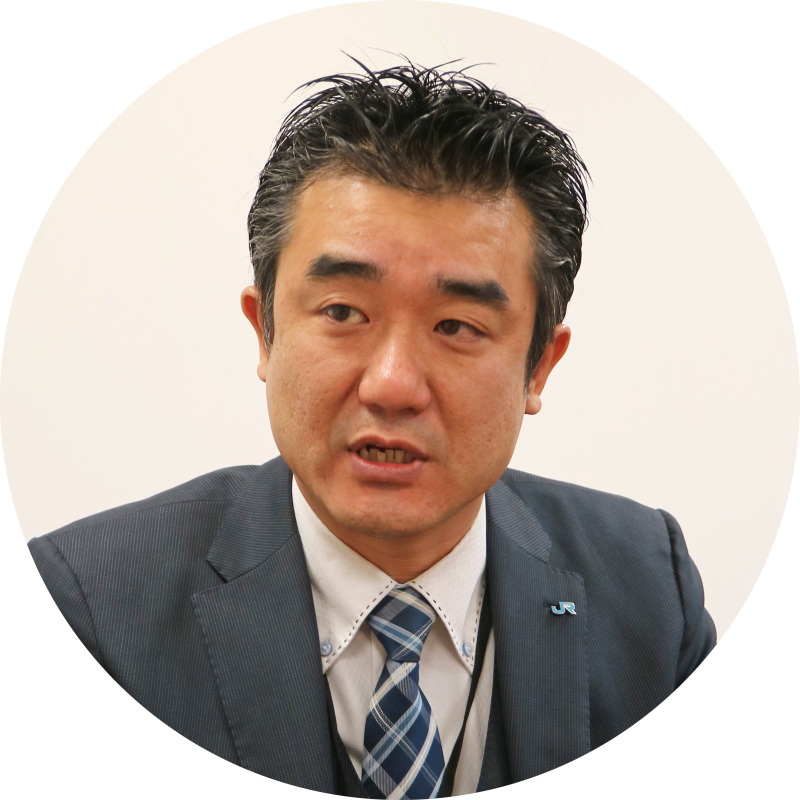
Rolling Stock Dept.
Railway & Business Headquarters
Japan Freight Railway Company
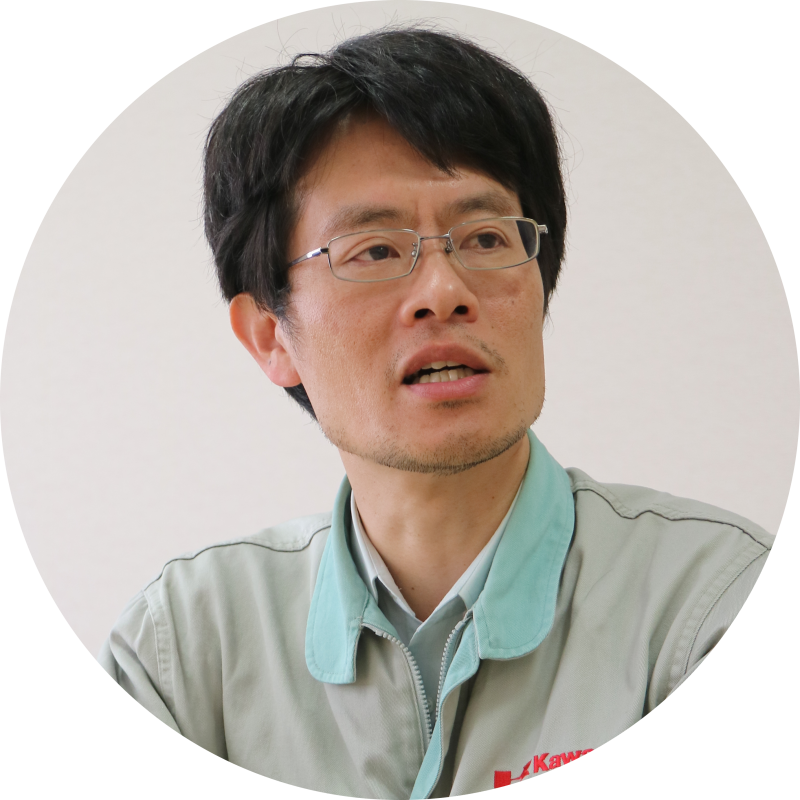
Domestic Engineering Section 3
Domestic Engineering Department
Domestic Project Division
Rolling Stock Company
Kawasaki Heavy Industries, Ltd.
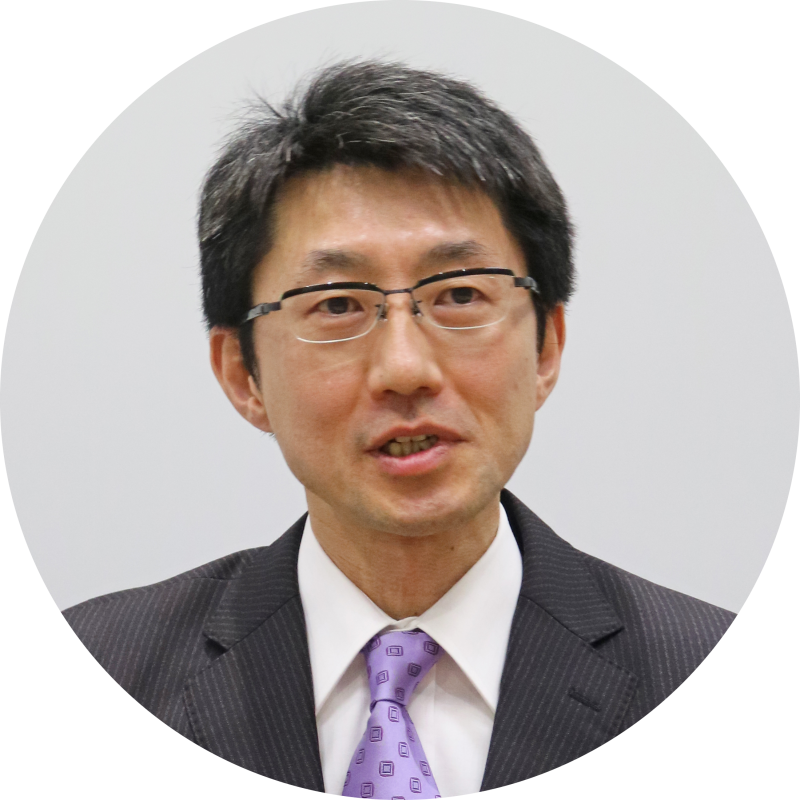
Eastern Region Marketing Dept.
Domestic Project Division
Rolling Stock Company
Kawasaki Heavy Industries, Ltd.