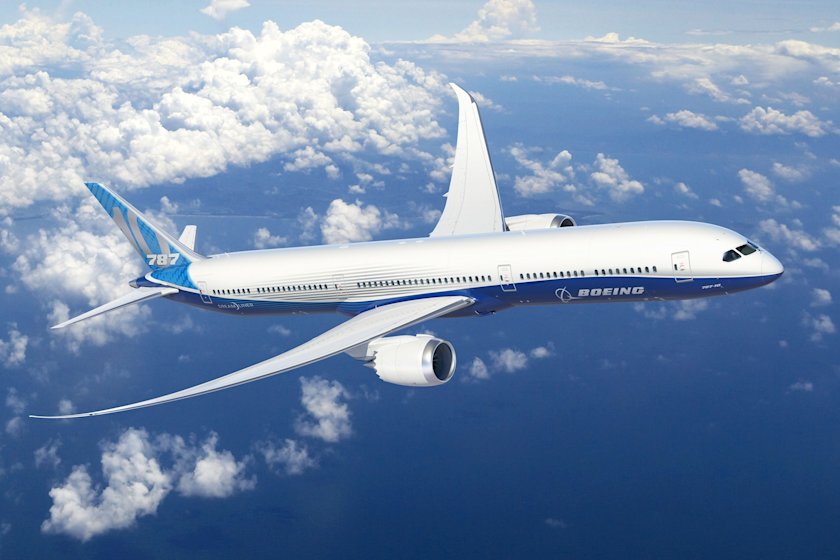
The Boeing 787 Dreamliner is a mid-size aircraft which is capable of accommodating from 200 to 300 passengers, with fuel efficiency representing an improvement of about 20%, and operating cost an improvement of about 30%, compared to the previous model in the same size category, owing to weight savings, advanced aerodynamics and new systems and engines.
Taking Manufacturing to a New Level
The Boeing 787 Dreamliner is a 200- to 300-seat, mid-size airliner featuring advanced aerodynamics as well as new systems and engines. Its lighter frame boosts fuel efficiency by 20% and reduces operating costs by 30% compared to existing airplanes of the same class. This improvement has also dramatically increased the flight range, making the aircraft hugely popular among airlines across the world. The 787 comprises the 787-8, the base model, and the -9 and -10 derivatives which feature an elongated fuselage for increased seating capacity.
According to figures released by Boeing, orders for these three models totaled 1,105 as of the end of March 2015. To ensure the airplanes are delivered on time, Boeing is working with its global partners to boost production capacity.
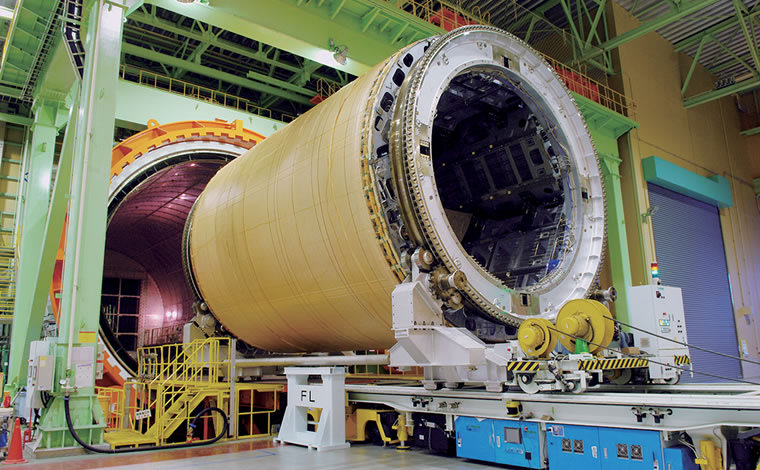
As a partner in the 787 program, Kawasaki manufactures the forward fuselage, wing fixed trailing edge, and main landing gear wheel well. The recently completed East Plant of Nagoya Works 1 is the third facility fully dedicated to the 787 program, following the North and South Plants. The East Plant will produce the forward fuselage of the 787-9 and 787-10. The plant is now getting ready to start production of the 787-10 by introducing state-of-the-art equipment also used in the two other plants. Kawasaki aims to take manufacturing to a new level at the new plant by building on its experience and achievements so far.
Aircraft must be absolutely safe in order to protect passengers. Every manufacturer involved in the production of aircraft must therefore obtain international certification for its production equipment. The crucial thing is to continually produce the required functionality and quality with precision. The means to achieve this end, however, are not prescribed. There is room for each manufacturer to exercise ingenuity.
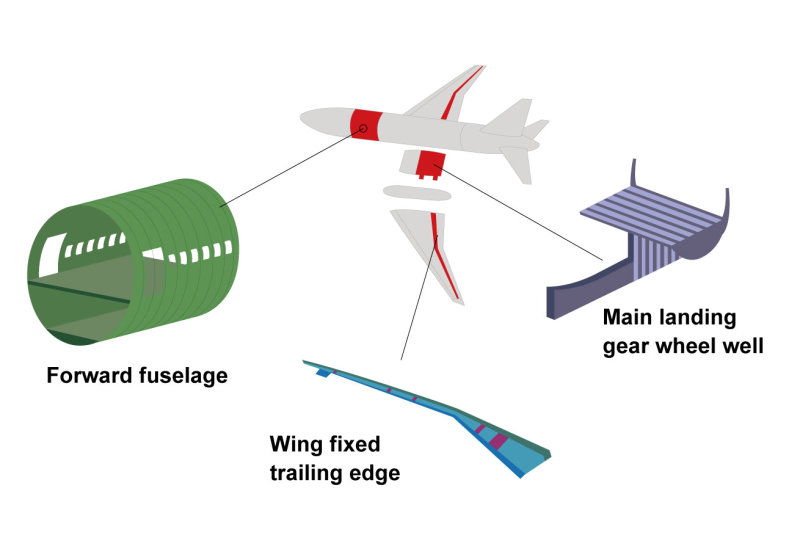
Making One-piece Barrel Fuselage with Carbon Fiber
Akihiro Shiraishi, Deputy General Manager of Manufacturing Division of Kawasaki’s Aerospace Company, sheds light on one of the main challenges faced in aircraft manufacturing. “The most difficult thing,” he says, “is to continue making the exact same thing with absolute precision, every day. Technology to make this possible is an area where advancement is constantly taking place. Kawasaki has produced most of the tools and equipment it uses to maximize efficiency, while ensuring that information is shared across the organization to facilitate technological development.”
The 787 is said to have revolutionized aircraft manufacturing. This is epitomized by the use of carbon fiber composites even in primary structures including the fuselage and wings. While carbon fiber composites offer such benefits as high strength-to-weight ratio, they also bring new challenges. Due to the nature of carbon fiber to change properties during processing, manufacturers are required to guarantee both material properties and geometry through process assurance. This process assurance is said to be the most difficult aspect in the production of the 787.
In particular, the forward fuselage which Kawasaki manufactures uses composites to create a one-piece barrel that is entirely seamless. This was the first time the technology was used in a commercial jetliner, and overcoming the technical challenges involved was where Kawasaki had to prove its merits.
Pursuit of Ultimate Precision
The one-piece barrel structure of the forward fuselage of the 787 is produced in six steps. First, carbon fiber composites are laminated onto a cylindrical mold, after which the composites are cured with heat in a pressure vessel called autoclave. In the third step, holes are made for positioning of parts. After undergoing ultrasonic nondestructive testing, reinforcements are installed inside the fuselage, and in the final step, floors, ducts, and other parts are installed.
Lamination of carbon fiber composites is performed using an automated fiber placement (AFP) device. The device works much as a silkworm spews out thread, depositing a number of carbon fiber tows onto a cylindrical mold.
Syoji Tada, who leads the process engineering team of the 787 Manufacturing Engineering Department, says, “Carbon fiber composites are extremely changeable and must be treated like fresh foods. The challenge was to understand their characteristics and establish a stable method to form composite layups.”
For instance, viscosity, which determines the adhesive strength of carbon fibers, changes with time. “We worked to deepen our understanding about the correlation between the various elements,” explains Tada. “That includes everything from the structure of the composite placement head and the method of placement to the humidity of the shop floor. Through these efforts, we sought to establish the optimal method. The AFP machine we have installed at the East Plant incorporates all the experience and knowledge we have gained through the project so far.”
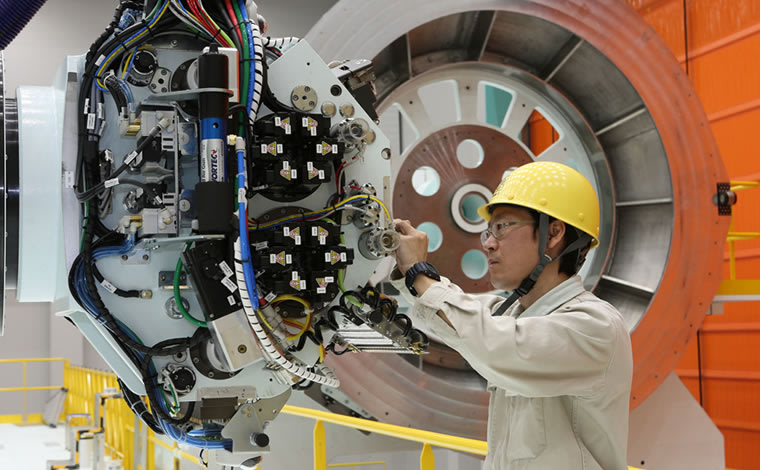
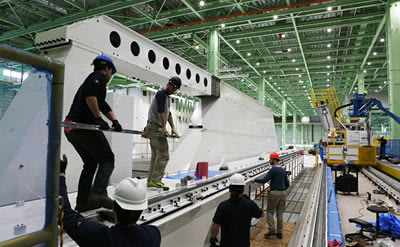
he composite layups will then be cured in an autoclave. The autoclave installed at the East Plant is an enormous structure, weighing 900 tons overall, and measuring 8 meters in diameter inside the curing oven and 19 meters in length. Compared to the base model 787-8, the 787-10 will have a significantly longer forward fuselage. The autoclave at the East Plant was manufactured at Kawasaki’s Harima Works by the group company Kawasaki Engineering, and it is designed to handle production of the 787-10.
Kanji Maekawa, General Manager, Industrial Plant Department of Kawasaki Engineering Co. Ltd., says that “the key point with autoclaves is achieving an ability to maintain an even temperature inside the vessel. That’s the most crucial thing.”
In order to maintain the strength and performance of carbon fiber composites, they must be cured evenly throughout the entire construct. The ability of the autoclave to maintain an even temperature inside the vessel leads directly to meeting deadlines and even improving turnaround. Achieving this ability was more important than anything else for the autoclave at the East Plant, which has the world’s largest-class diameter and will be used to cure elongated fuselages. Maekawa explains that various simulations were repeatedly performed to analyze the temperature distribution inside the vessel, using the thermal analysis technology developed mainly by Kawasaki’s Corporate Technology Division and the group company Kawasaki Technology.
“We managed to create an autoclave that works like a precision machine by combining Kawasaki’s entire manufacturing know-how cultivated through the development of plants and boiler equipment.”
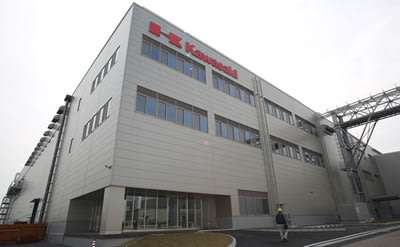
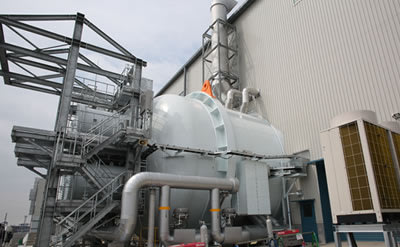
Automated Riveter, Guided with the Five Senses
Once cured, the carbon fiber composites command an imposing presence as a large one-piece barrel fuselage. The ultrasonic nondestructive testing device used for inspection is a world first developed by Kawasaki.
Once the testing is done, the fuselage moves to the next stage: installing a reinforcement frame. This will be performed using a machine called the panel riveter. It performs the full operation automatically, from drilling holes simultaneously through the fuselage and frame, then tightening bolts.
Long rails extend both inside and outside the fuselage, on which the machines move. Specifically, a machine on the outside opens a hole through which it inserts a bolt, then a machine on the inside rivets it down.
Kazuhiko Miwa, Senior Officer of 787 Assembly Manufacturing Engineering Section 1,787 Manufacturing Engineering Department, who oversees the introduction of the panel riveter, explains the difficulty inherent in this process. “Opening a hole and inserting a bolt may sound easy enough. But we’re talking about a forward fuselage of an aircraft, which has considerable length. Positioning and synchronizing machines pose a huge challenge in terms of accuracy.”
The forward fuselage requires numerous holes and riveting. The margin of error allowed for the positioning of each hole is 0.3 mm. Although the operation is fully automated, Miwa points out that “using our five senses is essential to improving accuracy and securing quality.”
To ensure the operation can be continued with consistency, the experience of a skilled operator is needed to assess the wear of a drill. Before and after each operation, a test piece is made to check the accuracy of automated work with human eyes.
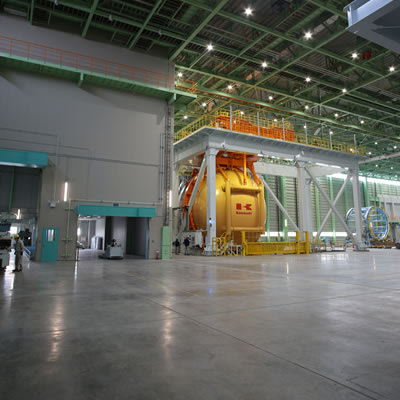
The 787 is said to have revolutionized aircraft manufacturing. This is epitomized by the use of carbon fiber composites even in primary structures including the fuselage and wings. While carbon fiber composites offer such benefits as high strength-to-weight ratio, they also bring new challenges. Due to the nature of carbon fiber to change properties during processing, manufacturers are required to guarantee both material properties and geometry through process assurance. This process assurance is said to be the most difficult aspect in the production of the 787.
In particular, the forward fuselage which Kawasaki manufactures uses composites to create a one-piece barrel that is entirely seamless. This was the first time the technology was used in a commercial jetliner, and overcoming the technical challenges involved was where Kawasaki had to prove its merits.
World’s Most Efficient Factory Built on Quality and Safety
With the East Plant now ready for operation, Kawasaki’s production capacity is expected to increase from 10 to 14 planes a month. For Kawasaki, mass production of large aircraft brought some new challenges. The Aerospace Company learned the method of mass production from Boeing, and also looked to its own motorcycle business, where the Kawasaki Production System (KPS) originated, for its valuable know-how.
It is based on persistent execution, and the idea that “safe operation is synonymous with quality.” This policy promoted widely sharing operational improvements and emulating good practices.
For instance, while an airplane is symmetrical, its parts slightly differ from one another, so improvements were made to jigs to avoid installing the wrong parts at the wrong places. In addition, the operators’ movement in each process was filmed to analyze and streamline their movement, which resulted in shorter process time.
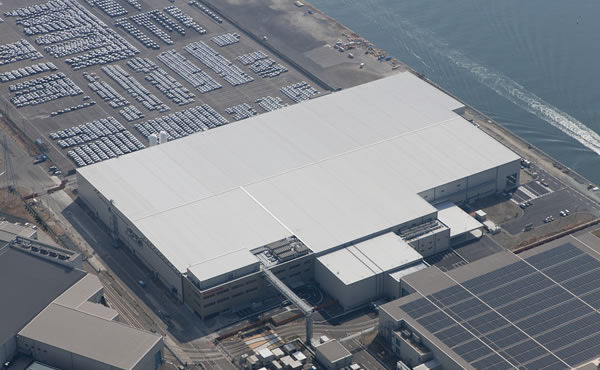
Thanks to such efforts, the site received the honor of being named the most efficient factory in the world by Boeing. Kawasaki’s passion for manufacturing has done more that winning it the Supplier of the Year Award and other accolades: it is contributing to the safety of the skies.
East Plant Revealed to the Public at Completion Ceremony
On March 13, 2015, Kawasaki held a ceremony to celebrate the completion of the East Plant, newly built at Nagoya Works 1 (Yatomi City, Aichi Prefecture). Press members were also invited to tour the inside of the plant.
Construction of the East Plant, which has a total floor space of 60,000 m2, began in December 2013. Representatives from Boeing and Governor Omura of Aichi Prefecture attended the ceremony to celebrate this new step forward for the aerospace industry of the Chubu region.
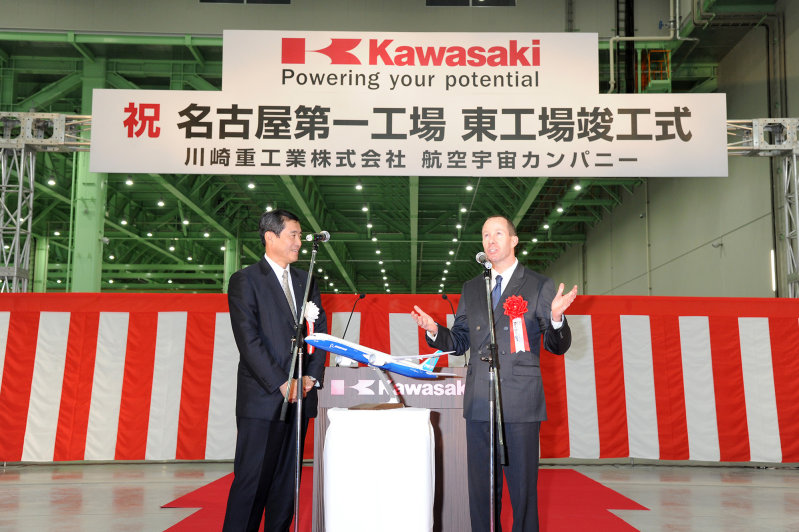
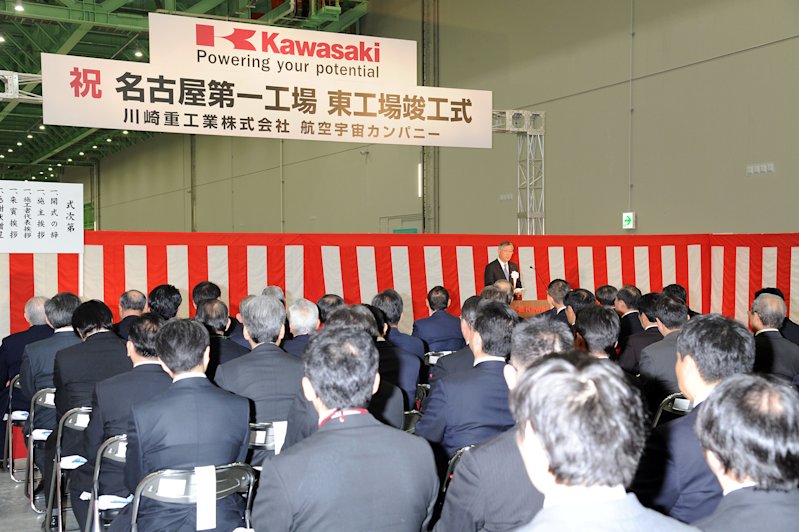
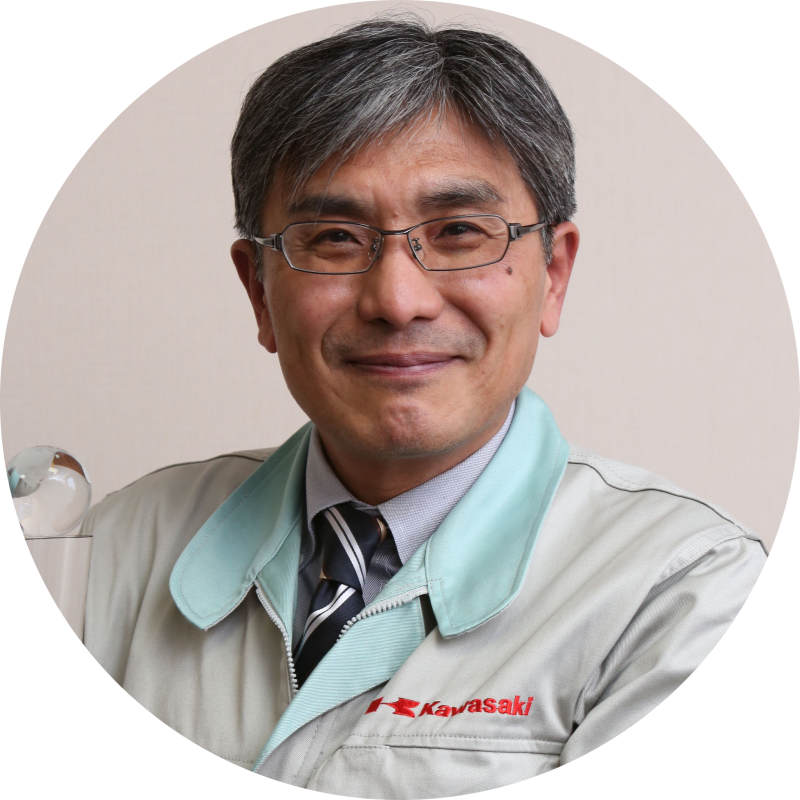
Manufacturing Division
Aerospace Company & Director,
Nagoya Production Department.
Kawasaki Heavy Industries, Ltd.
Developing a Solid Production System to Work Together with Partners Around the World
The 787 is produced with the participation of many companies across the world. Under the slogan of “Working Together,” Boeing specifically called for the adoption of the Boeing Production System (BPS) on the shop floor. As a result, partners around the world collaborated much like an orchestra, in an attempt to create a smooth flow of manufacturing. This was a new approach for creating safe aircraft.
While BPS has its roots in Toyota’s Kaizen activities, Kawasaki’s own Kaizen activities, KPS, were also derived from Toyota. As such, BPS and KPS have close affinity. Efforts toward mutual learning and improvement are producing excellent results, including consistent quality, zero delays, and no missing parts, which are raising Kawasaki’s profile.
In building the East Plant, which will produce the -9 and -10 variants of the 787 family, ensuring enough capacity to be able to accommodate future ramp-ups was a crucial challenge. Procurement of parts and the production lines have to be in synchronized, an area where special know-how unique to aircraft manufacturing is exercised.
Constant efforts are made to develop that know-how, with the help of Kawasaki’s Corporate Technology Division and group companies. These efforts have already led to the development of tools for cutting composites, an analytical method using an ultrasonic nondestructive testing device, and more. In building the East Plant, simulations were performed to optimize production management by linking the activities of the three plants, including the handling of work in process and delivery schedule. The collective effort of Kawasaki is directed toward the creation of safe aircraft.
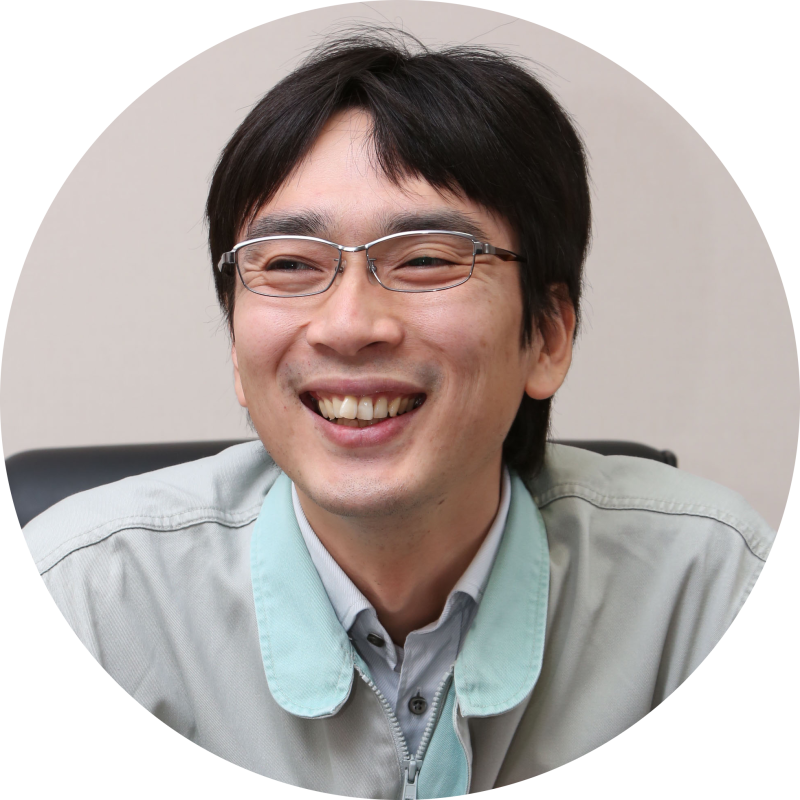
787 Manufacturing Engineering Department
Kawasaki Heavy Industries, Ltd.
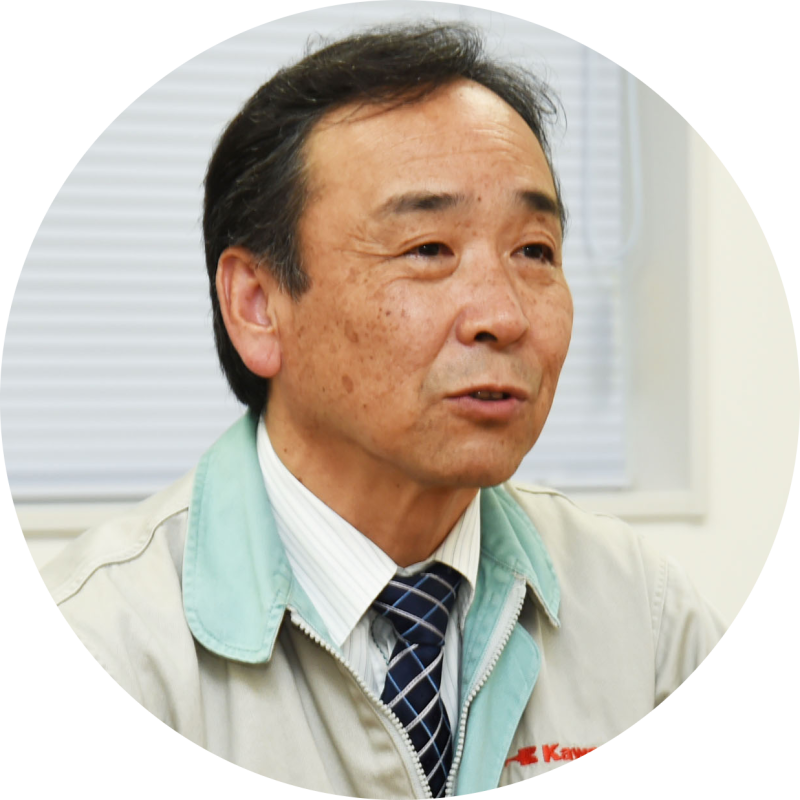
Industrial Plant Department
Kawasaki Engineering.
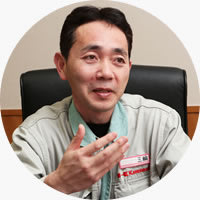
787 Manufacturing Engineering Department
Kawasaki Heavy Industries, Ltd.