Capturing CO₂ from the atmosphere and storing it inside concrete. Kawasaki and Kajima working together toward carbon neutrality
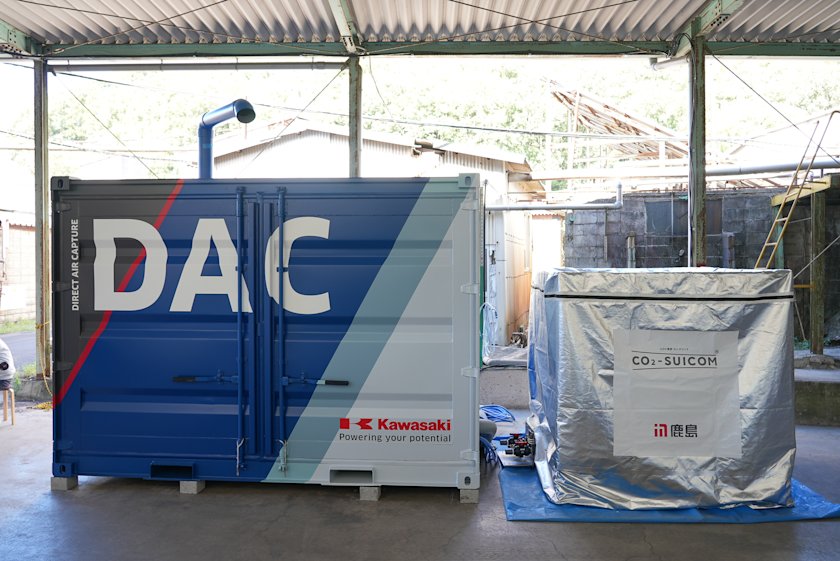
In 2024, Kawasaki and Kajima Corporation launched a joint study on how to capture and utilize CO₂. The goal was to apply Kawasaki's direct air capture (DAC) technology to the manufacturing of CO₂-SUICOM, CO₂-absorbing concrete developed by Kajima in collaboration with other companies. The initiative was a success. The CO2-absorbing concrete manufactured after a series of demonstration tests have been installed at the EXPO 2025 Osaka. In this article, we interviewed Takeshi Okumura of Kawasaki and Takeshi Torichigai of Kajima Corporation, who have been leading this pioneering project. They shared how they conducted their joint research and what they achieved as a result.
[Glossary of terms related to carbon neutrality]
(1) Kawasaki Heavy Industries’ DAC technology
Direct air capture (DAC) is a technology that captures CO2 from the atmosphere. Kawasaki’s unique DAC technology uses solid sorbent shaped like beads and coated with amine, a substance that absorbs CO2.
(2) Kajima Corporation’s CO2-SUICOM
The world’s first CO2-absorbing concrete developed jointly by Kajima Corporation, Chugoku Electric Power Co., Denka Co., and Landes Co., in 2008. One of the main components of concrete is cement, which emits large amounts of CO2 during the manufacturing process. However, CO2-SUICOM, over half the cement is replaced with a more environmentally friendly substitute, allowing us to greatly reduce the amount of CO2 emitted from manufacturing the concrete. Furthermore, when the concrete is being hardened, CO2 is absorbed and stored inside the carbonation curing chamber. As a result, the total CO2 emissions from manufacturing the concrete at net-zero or less, the so-called a carbon-negative effect can be ecpected.
https://www.kajima.co.jp/tech/c_sus_con/technology01/index.html
(3) CCUS
CCUS refers to “carbon dioxide capture, utilization, and storage,” initiatives and technologies to use CO2 that has been separated and stored. This is distinguished from “carbon dioxide capture and storage” (CCS), in which CO2 separated from the atmosphere is captured, injected into deep underground formations, and stored. CCUS, in addition to storing captured CO2, also puts it into effective use. Various technologies and initiatives are being developed and implemented around the world for CCS and CCUS in an effort to achieve carbon neutrality.
What was the trigger for the joint research between Kawasaki and Kajima?
Please tell us how the two companies came to to collaborate and conduct joint research.
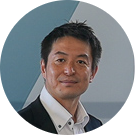
I happened to be seated next to (Torichigai-san) at a reception hosted by the U.S.-Japan CCUS/Carbon Recycling Working Group.* The meeting was held in August 2023 in Pittsburgh and co-sponsored by the Ministry of Economy, Trade and Industry. CCUS stands for “carbon dioxide capture, utilization, and storage.” It refers to initiatives and technologies for the capture, utilization, and storage of CO2. The meeting provided a platform for Japanese and U.S. companies with various CO2 capture and utilization technologies to gather and exchange information. There, I learned about the details of CO2-SUICOM from Torichigai-san for the first time.
*The meeting was co-sponsored by the Ministry of Economy, Trade and Industry, the U.S. Department of Energy, the National Energy Technology Laboratory (NETL), and the New Energy and Industrial Technology Development Organization (NEDO). This was one of the areas of cooperation pursued in accordance with the Japan-U.S. Clean Energy and Energy Security Initiative (CEESI), which was launched in May 2022 following an agreement between the Japanese and U.S. governments.
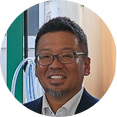
I told Okumura-san that there were some challenges involving CO2-SUICOM, such as ensuring a steady supply of CO2. He then suggested that we use DAC to capture CO2 from the air. I thought that was an interesting idea. We were purchasing CO2 at the time, but it was difficult to find a supplier that could provide the right amount of CO2 for CO2-SUICOM. Kawasaki Heavy Industries’ DAC would let us design a system for the right amount of CO2. I thought this might be an excellent combination.
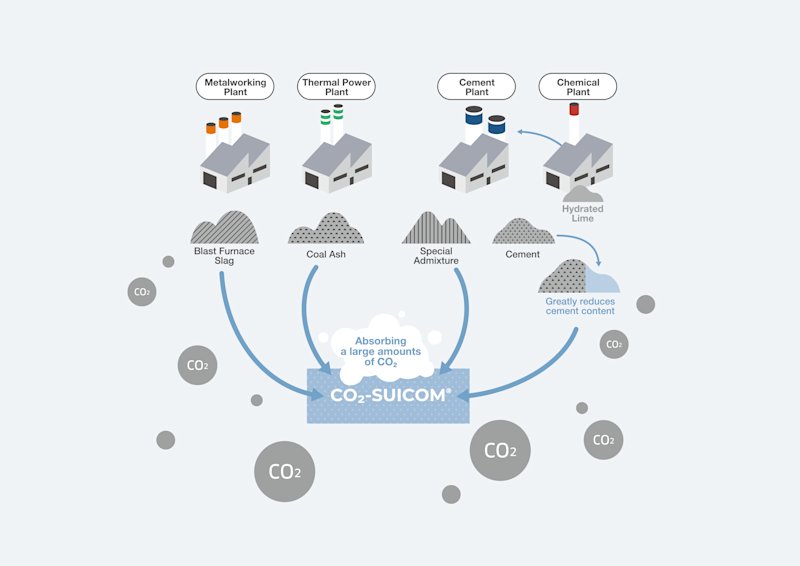
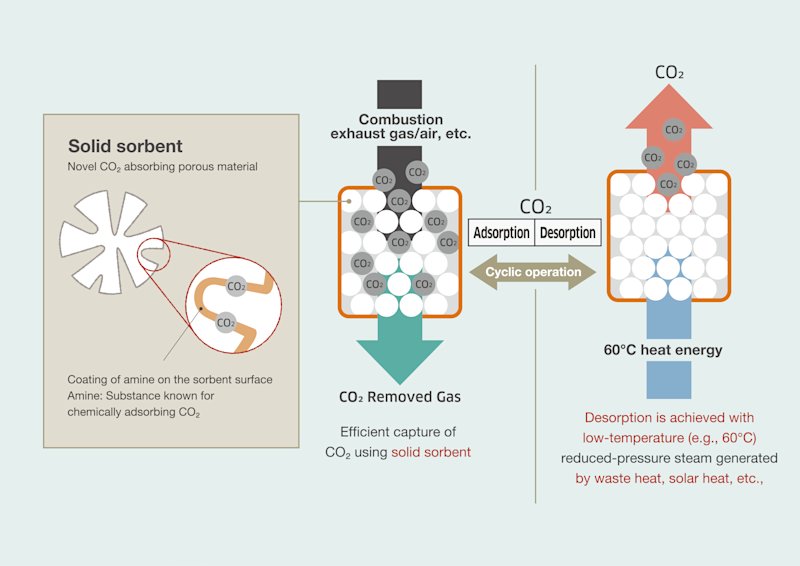
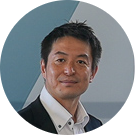
Torichigai-san expressed an interest in Kawasaki Heavy Industries’ DAC technology. So, when I returned to Japan, I worked very hard to make it happen. Our DAC technology uses solid sorbent coated with amine, which absorbs CO2 to directly capture CO2 from the atmosphere. At the time, we had already conducted demonstration tests with other companies using factory exhaust with high CO2 concentrations. However, when it came to capturing CO2 from the surrounding air, we had only conducted tests in-house. We had never disclosed this technology before. So, we made rapid preparations for the joint research.
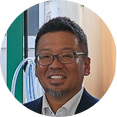
One of the main reasons we wanted to use Kawasaki Heavy Industries’ DAC technology was that it would be able to capture CO2 on the spot. As I said earlier, one of the major challenges involving the development of CO2-SUICOM was obtaining the right amount of CO2 and supplying it to the concrete factory. We hoped to achieve “local production for local consumption” of CO2 through this joint research. We would capture CO2 and use it right there.
Everything is new... The summer demonstration test begins.
The joint research finally began in July 2024. How did you go about conducting demonstration tests?
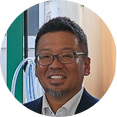
CO2-SUICOM uses a “carbonation curing chamber.” It enables concrete to absorb and store CO2. We have created a system to combine this chamber with Kawasaki’s DAC unit. We installed it inside a concrete factory in Kagawa Prefecture, which became our test venue.
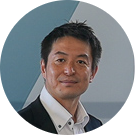
This was the first time that we took the DAC unit outside. So, we prepared a container, put the unit in the container, and transported it to the test venue. The unit was able to capture at least 5 kg of CO2 per day at a concentration of 99% or higher. We carefully checked to make sure that it was not damaged while being transported and installed it at the test site. We used the unit to capture CO2 from the atmosphere at the site and sent it to Kajima Corporation’s carbonation curing tank. The concrete absorbed CO2 and trapped it in that tank.
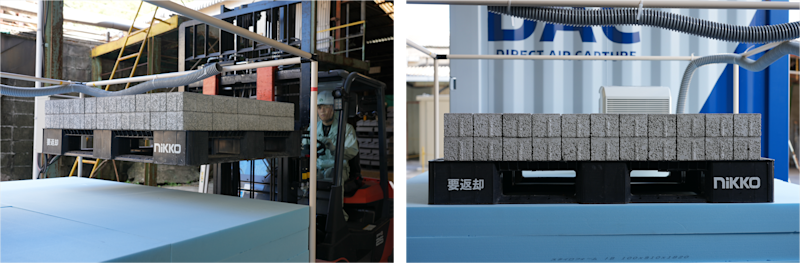
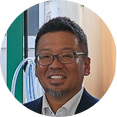
The test was conducted in the heat of summer. The temperature was really high, and we were directly hit by a typhoon. We were worried that the system might break. So, we went through all kinds of hardships (laughs).
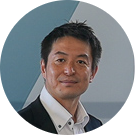
It was a difficult summer in so many ways (laughs). We worked hard to get through this challenge. We were determined to send the right amount of CO2 into the tank, no matter what. When the test began, the tank swelled up with the CO2 from the DAC unit. But it shrank the next morning. I was so excited to see that CO2 had been absorbed into the concrete. I was actually so relieved.
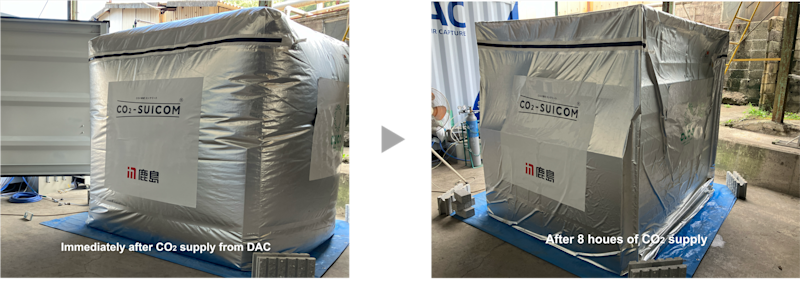
The CO2-SUICOM paving block has been be used at the 2025 EXPO Osaka.
I understand that the CO2-SUICOM paving block that you produced has been used at the 2025 EXPO Osaka.
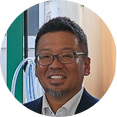
In the demonstration tests, it was confirmed that the amount of CO2 absorption quality of concrete are acceptal. Based on this outcome, we used a similar system to manufacture the CUCO-SUICOM block.* It will be used for part of the entrance to the CUCO-SUICOM Dome (aka Sustainability Dome) at the 2025 EXPO Osaka.
*The paving block was manufactured as part of the Development of Technology for Producing Concrete and Cement Using CO2 project sponsored by the Green Innovation Fund of NEDO (New Energy and Industrial Technology Development Organization).
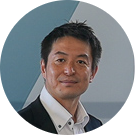
The CO2 captured with Kawasaki’s DAC technology is used in the manufacturing of concrete, and this concrete is used at the 2025 EXPO Osaka. Nothing makes me happier. We hope that people will experience this technology at the EXPO and become more interested in CO2 capture and utilization. This may energize Japan’s CCUS initiatives.
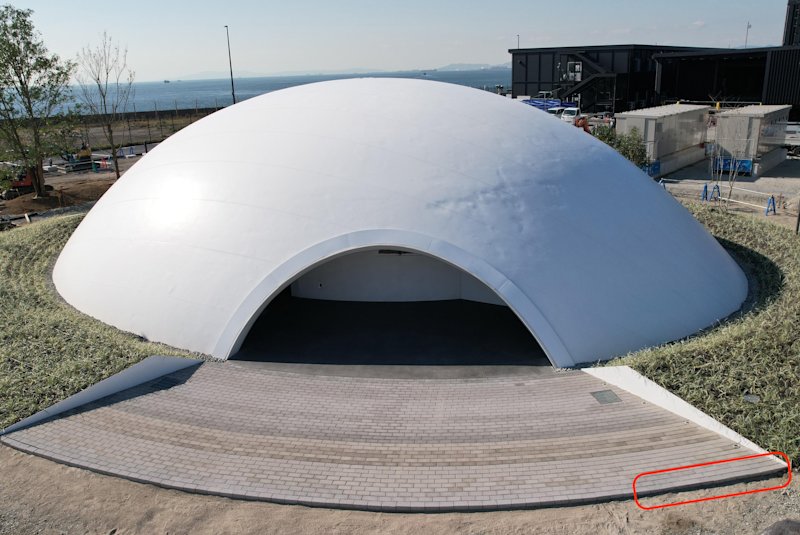
From now on, We want to lead carbon management in Japan.
How do you think this initiative will evolve in the future? Please share your outlook, both of you.
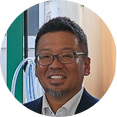
Efforts are underway to achieve a carbon-neutral society. In Japan, technologies for capturing CO2 and technologies for utilizing CO2 are both being developed, but they are being developed independently of each other. There have been very few attempts to bring these initiatives together. However, according to the Ministry of Economy, Trade and Industry, it will become more important in the future to capture and use CO2, in addition to reducing emissions. This is where CCUS, or carbon management, plays an important role. It will become increasingly necessary to combine these two initiatives.
This project is an example of carbon management in action. I believe that we have set an example for others to follow. Looking ahead, we would like to lead Japan’s CCUS and carbon management initiatives though our endeavor.
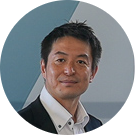
He is absolutely right. Kajima Corporation’s CO2-SUICOM has already been put into practical use. We should combine this technology with Kawasaki Heavy Industries’ DAC. This will make it possible to achieve “local production for local consumption” of CO2, as Torichigai-san mentioned earlier. Our tests show that Kawasaki Heavy Industries’ DAC technology is capable of concentrating rarefied CO2 of 400 ppm, allowing for the capture of high-purity CO2, at around 99%. We will continue to conduct demonstration tests at various locations using this technology. We hope to contribute to the realization of carbon neutrality and carbon management.
Let me share my personal view as an individual researcher. I have been involved in CO2 research for a long time. But this is the first time that I have created something that I can actually touch and see. I can leave something tangible behind. I am very happy about this. I would like to continue working with my teammates and promote the wider use of DAC technology.
Interviewee bios
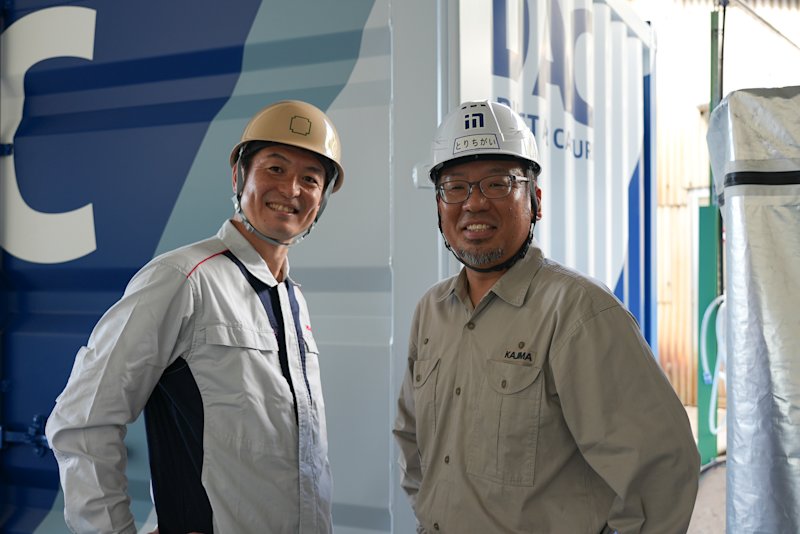
Kawasaki Heavy Industries
Corporate Technology Division, Technical Institute,
Energy Systems Research Department
Takeshi Okumura
Okumura is responsible for the development of CO2 capture technology, conducting various tests as part of a process development project using solid sorbent and sorbent that absorb CO2. He also dedicates himself to the practical application and promotion of this technology. His recent assignments include demonstration tests at a U.S. thermal power plant, a project commissioned by the Ministry of the Environment.
Kajima Corporation
Cheif Research Engineer, Concrete and Construction Materials Group,
Kajima Technical Research Institute
Takeshi Torichigai
Decarbonization has been his passion from the moment he joined the company. Assigned to the CO2-SUICOM project in his fourth year, Torichigai has been leading various research and development projects and deployment initiatives related to this technology. He is instrumental in promoting the practical application of CO2-SUICOM through research and development of the CUCO-SUICOM block, a project sponsored by the NEDO Green Innovation Fund.
*Departments and titles were current as of the time of the interview.