Becoming the world’s most environmentally friendly paper mill: Decarbonization using gas turbine cogeneration
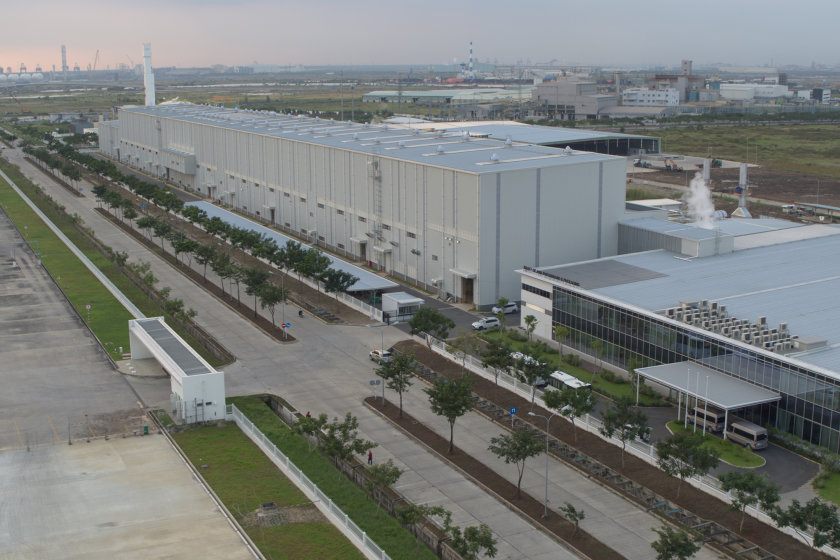
“Becoming the paper mill with the world’s smallest environmental footprint”
It’s summer 2020 and containerboard manufacturing company Kraft of Asia Paperboard & Packaging (KOA) has completed the construction of a new sustainable paper mill in Vietnam in preparation for the decarbonized society. The energy needed to power the mill is produced by a cogeneration system (CGS) that was designed and built by Takasago Thermal Engineering Co., Ltd. (TTE) as an EPC (engineering, procurement, construction) package and that employs a gas turbine manufactured by Kawasaki. The installation of this CGS facility, the first of its kind in Vietnam to run on natural gas, was conceived with a firm eye on the future of the industry.
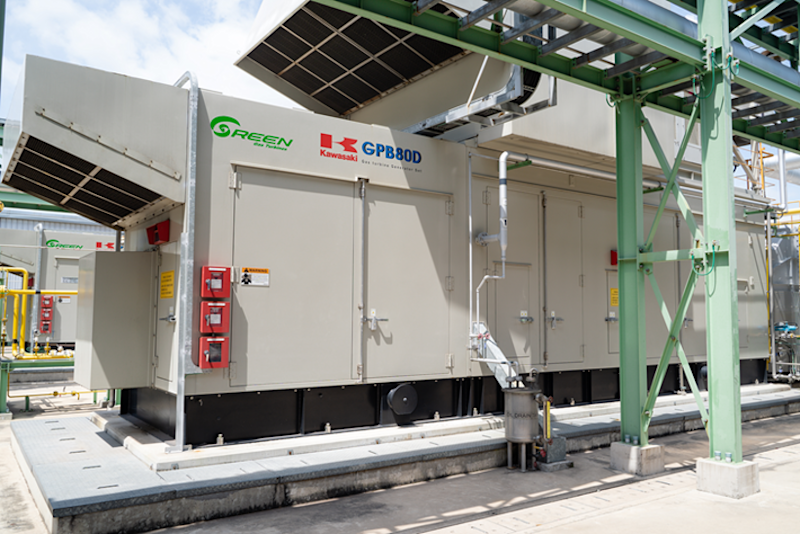
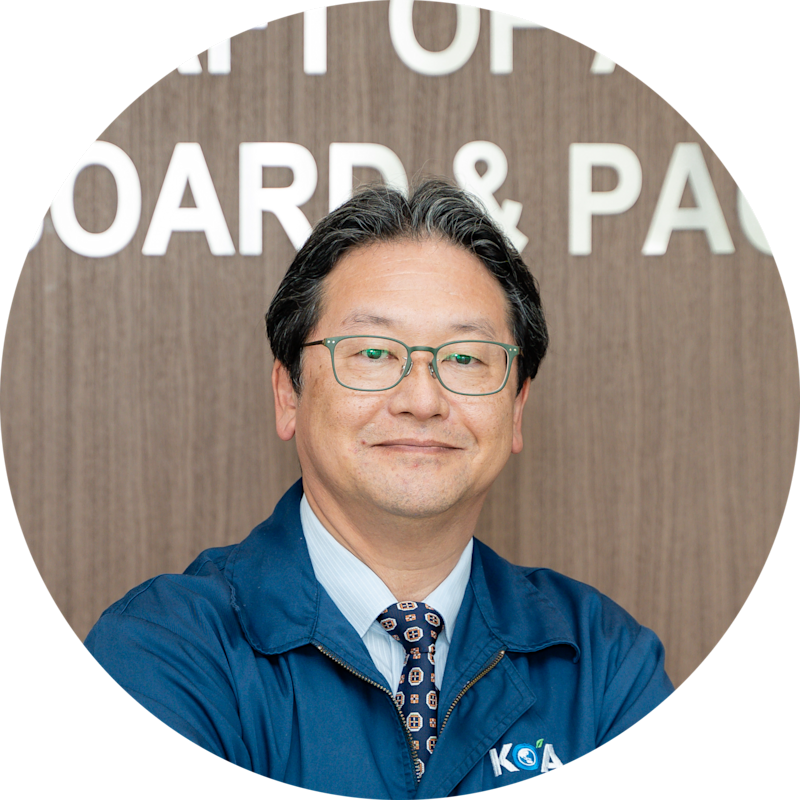
General Director
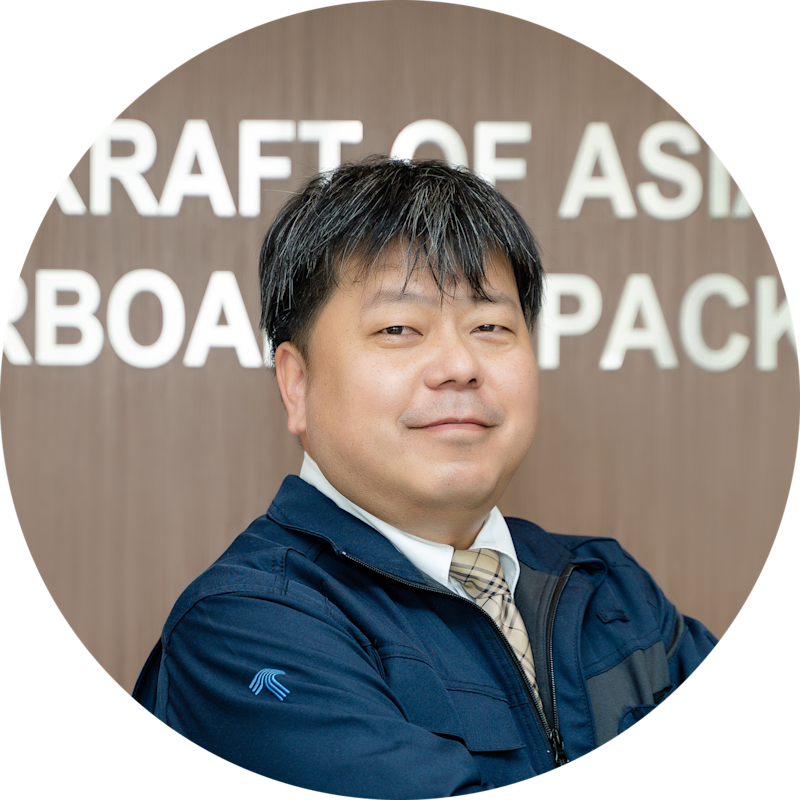
International Business Headquarters
Manager Representative of Carbon Neutral Business
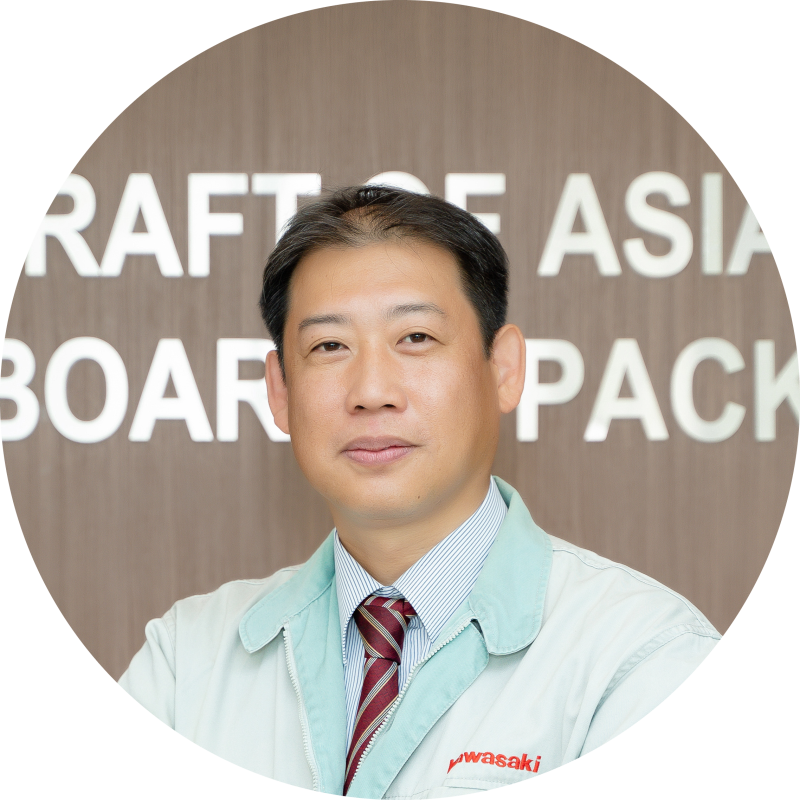
Senior Staff Officer
Project Planning Section 3
Project Management Department
Energy System Group, Energy Solution Business Division
Energy Solution & Marine Engineering Company
Vietnam’s first-ever natural gas-powered CGS
Around one hour’s drive from Ho Chi Minh, Bà Rịa-Vũng Tàu Province is known as the maritime gateway to southeastern Vietnam and is also home to extensive offshore oil and gas fields. This resource-rich region is also the location of Phu My 3 Specialized Industrial Park, which is where KOA, a 100% owned subsidiary of Marubeni Corporation, decided to build its new paper mill featuring Vietnam’s first-ever natural gas-powered CGS. TTE handled the engineering, procurement and construction of the CGS, and selected Kawasaki’s GPB80D gas turbine as its centerpiece.
What’s a cogeneration system?
In a cogeneration system, a gas turbine is driven by primary energy (fuel), and continuously produces multiple types of secondary energy (e.g., electricity, steam). A gas turbine cogeneration system uses fuel as the primary energy and produces multiple types of energy to enable more effective energy use. Furthermore, the system curbs NOx production and reduces environmental impact by using a gas turbine as the drive source.
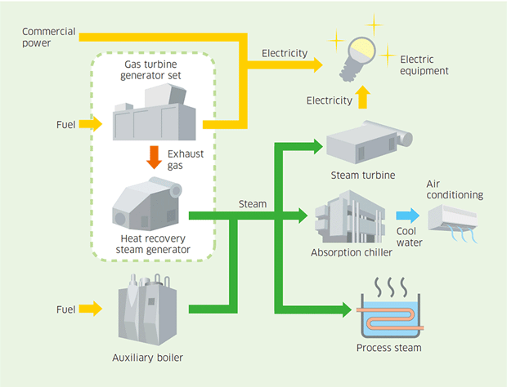
Only about four or five years ago, it was taken for granted that paper mills had to be powered by coal-fired boilers. KOA’s general director, Hiroshi Matsumura, says that companies were disincentivized to use natural gas because it was a more expensive option than coal. Despite this, KOA first considered a project to build a new paper mill in Vietnam back in 2013. Why did Matsumura take a leap of faith and select natural gas as a power source?
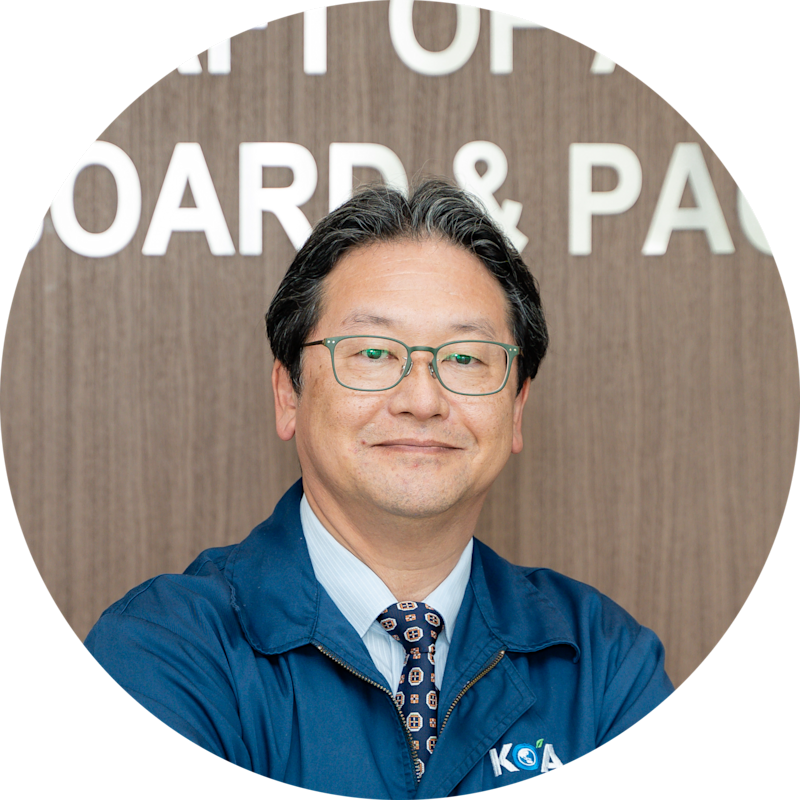
At the start, the consensus was, ‘Costs are critical in the paper mill business, so the power must inevitably come from coal,’ and we therefore obtained approval from the provincial government for a coal-powered CGS. However, looking 10 or 20 years into the future, we couldn’t just ignore the looming issue of global warming. One of my senior colleagues, who has a wealth of experience in the paper mill business, told me, ‘No matter what anyone says, you need to stop using coal.’ That led us to choose natural gas, which has much lower CO2 emissions than coal, to power the new plant. The provincial government was also extremely appreciative of our decision.
In Vietnam, continued industrialization and population growth has led to a steady increase in CO2 emissions over the last decade1 At COP26, the Vietnamese government announced plans to halt this trend and a commitment to achieving carbon neutrality by 2050. Technologies and related legislation are now being developed at a rapid pace so that the country can make headway in achieving this ambitious goal.
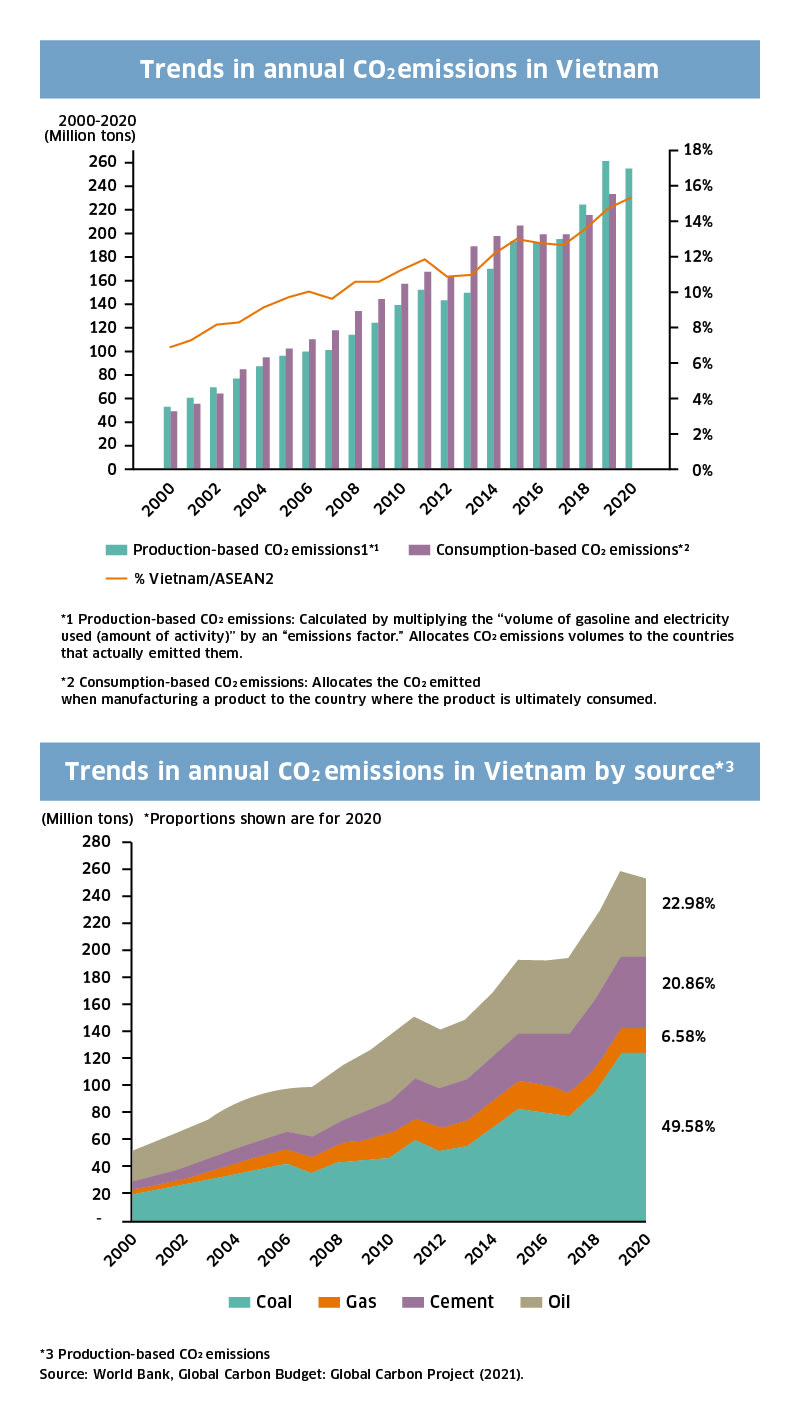
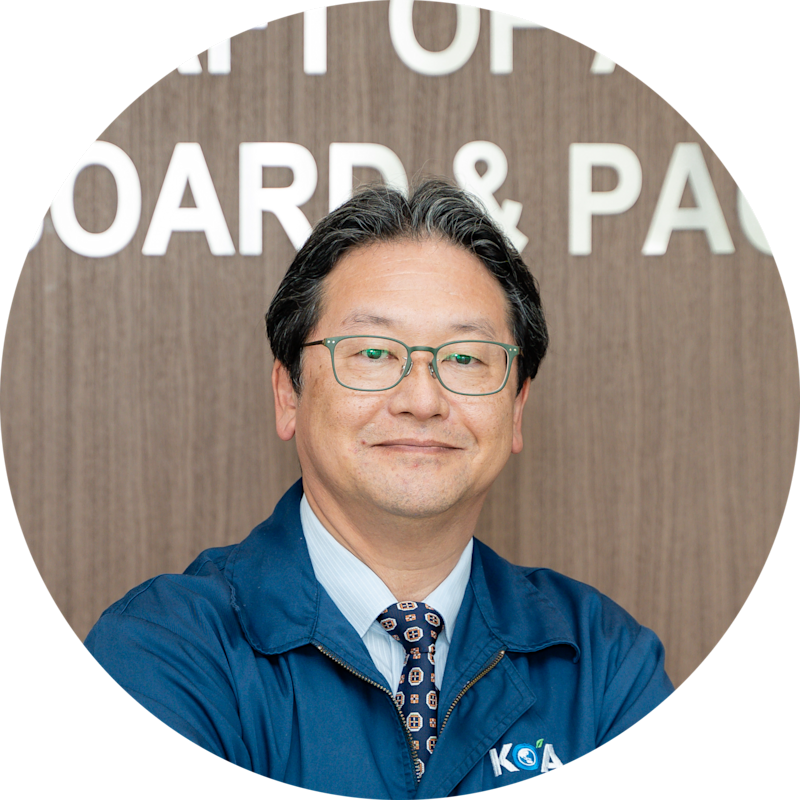
During the past year, decarbonization initiatives have started to take off, mainly among non-Vietnamese companies. This means that the decision we made several years ago to switch to natural gas is now one of our plant’s biggest strengths. By adopting a CGS that creates both power and steam from natural gas, we can roughly halve our CO2 emissions compared to our competitors in the same industry. I can say with confidence that there is no paper mill in Vietnam that is more environmentally friendly than ours.
*1 Excerpt from JETRO Hanoi Office report, Status of initiatives in Vietnam towards realization of carbon neutrality. (Report in Japanese only)
Coal and natural gas energy costs reaching a similar level
Natural gas is generally considered to be a more expensive option than coal. However, Matsumura questions this view.
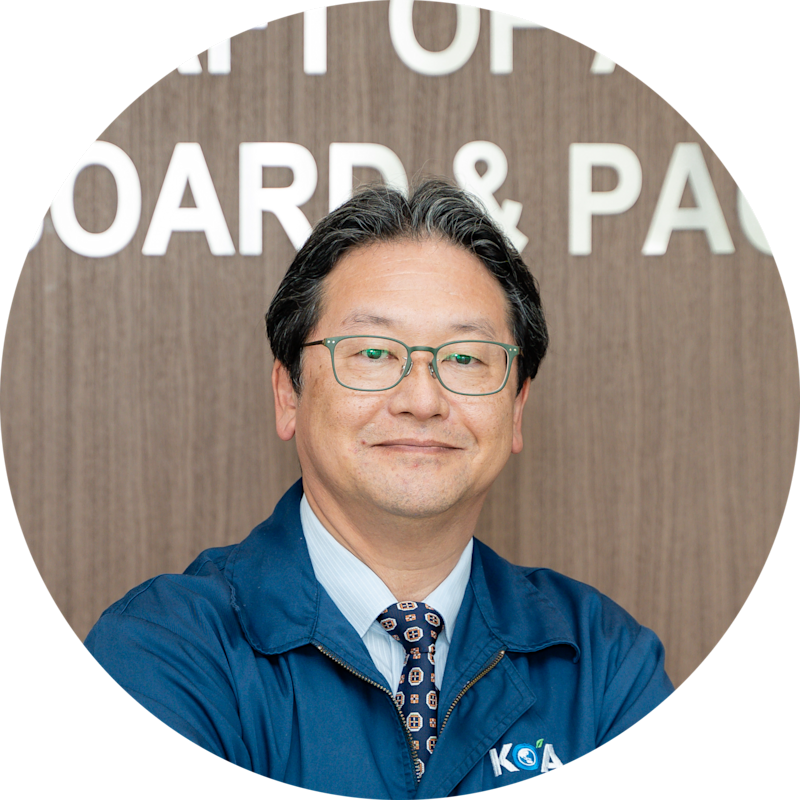
Marubeni owns two paper mills in Japan that have introduced coal and natural gas-powered generation systems respectively. Looking at the state of the fuel market at the time the project was being considered, the energy costs to produce one ton of paper were actually not much different between the two mills.
Matsumura also adds that a CGS that uses natural gas has the advantages of 1) ease of operability, 2) outstanding responsiveness to load fluctuations,*2 3) quick start-up/shutdown times,*3 and 4) excellent safety. Another strength is that initial investment costs can be controlled.
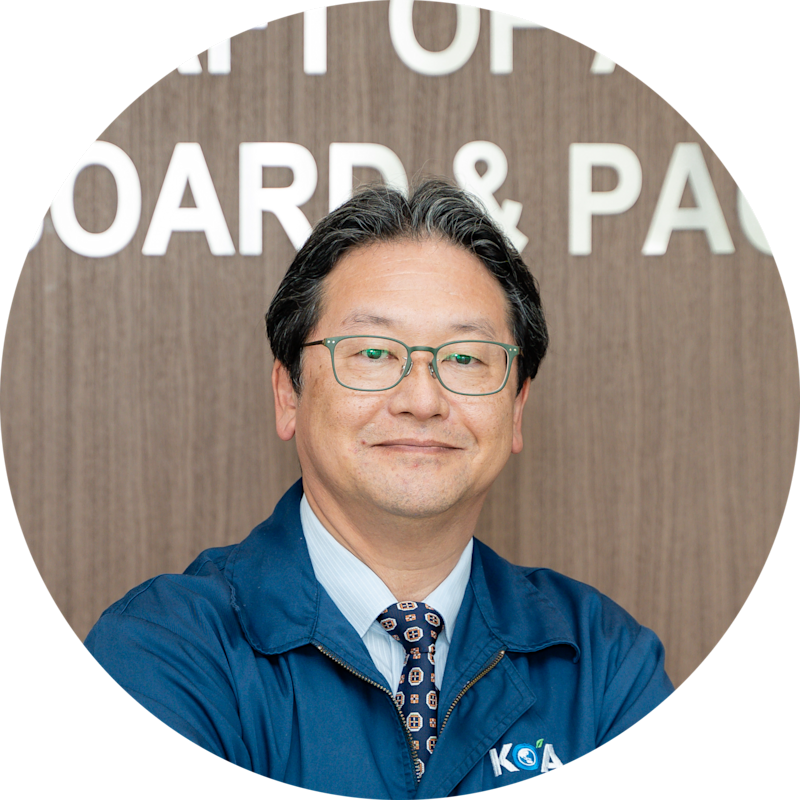
With a coal-fired system, you need a great deal of space, because the boilers are very large and you also need space to store the coal as well as the waste ash. All in all, you need about four times more space than for a natural gas CGS. We already knew, to a certain extent, about the various advantages of a natural gas CGS, based on the performance of the Japanese plant.
In addition, the fact that the gas turbines can be quickly switched on or off has reduced weekly maintenance times. Using gas means that there is also no need to build a coal storage facility, which brings with it the risk of fires. Even so, this was going to be the first-ever natural gas-powered CGS in Vietnam and there were also various challenges specific to paper mills that needed to be overcome.
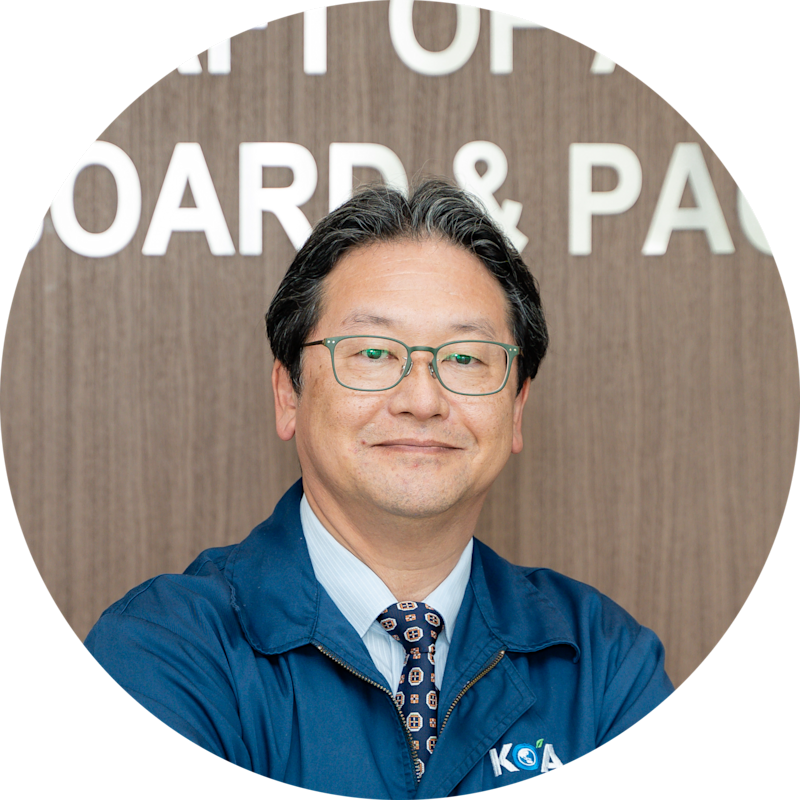
Paper is so thin that it often rips or tears inside the machine during production. This ripped paper falls from under the machine into a device that melts wastepaper. That means that when the paper rips, the motor of the melting device whirrs into action, causing electricity usage to jump. The challenge for us was how to respond to such changes in energy demand in the production process. It was TTE that came up with a solution.”
Hidechika Koga from TTE, the engineering company involved in the project, notes that for paper mills in particular, a natural gas-powered CGS offers a number of advantages.
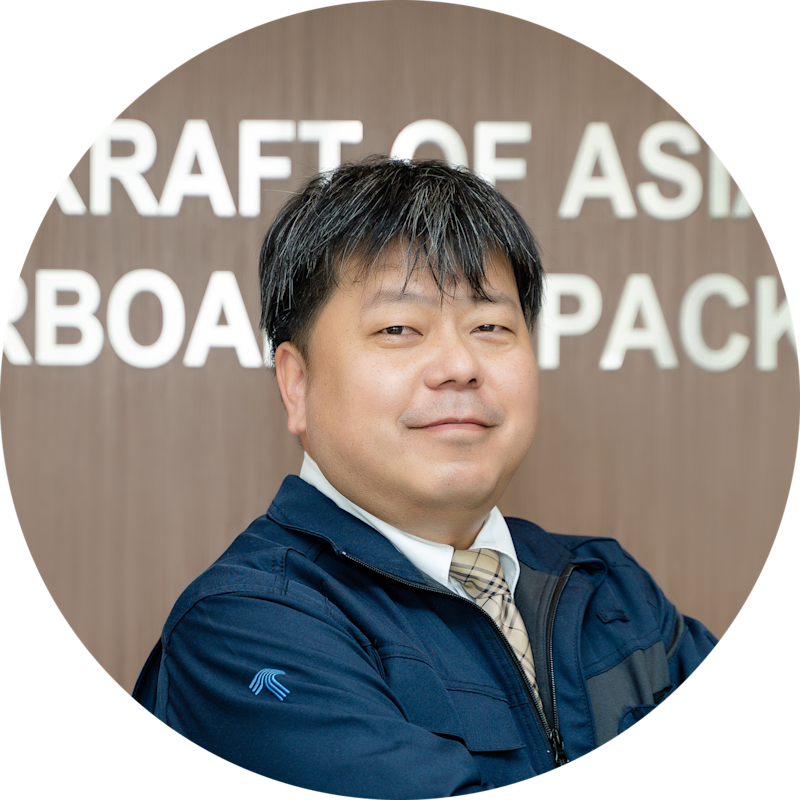
Having listened to KOA’s experiences and issues, we decided that a system centered on a gas turbine, which boasts excellent responsiveness to load fluctuations coupled with relatively small space requirements, would be the best option for the paper mill. Among the various manufacturers, we chose Kawasaki, as it has a maintenance plant for gas turbines in nearby Malaysia, meaning that it could provide support for operations in Vietnam.
*2 Gas turbines continuously rotate at high speed through the mixing of fuel and air, compression, and ignition and combustion. This continuous state of combustion is able to withstand load fluctuations with minimal impact.
*3 The gaseous state of natural gas allows the fuel to be pressurized, which enables ignition in a way that is not possible with coal and that reduces startup times.
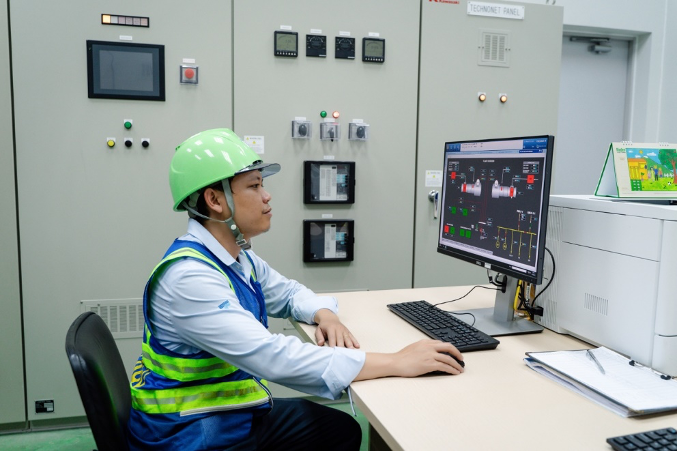
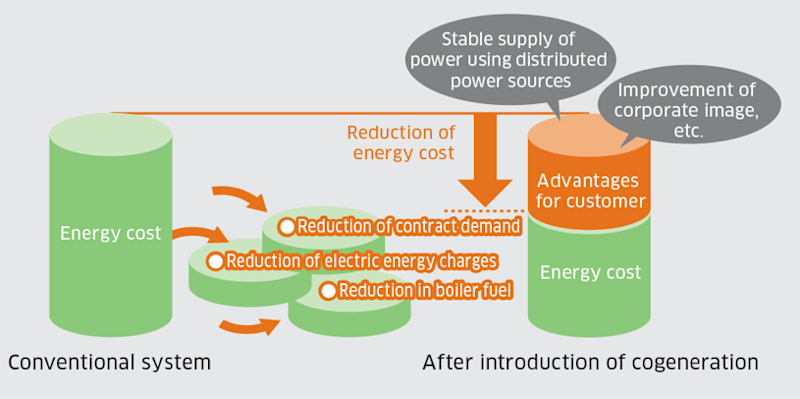
Next up, switching to hydrogen
The natural gas CGS installed at the paper mill in Vietnam is Kawasaki’s 7MW-class GPB80D. Tsuyoshi Torii, who was involved in the project planning from Kawasaki, says that one of the factors behind the project’s success is that it was possible to propose the most appropriate system for KOA’s paper mill.
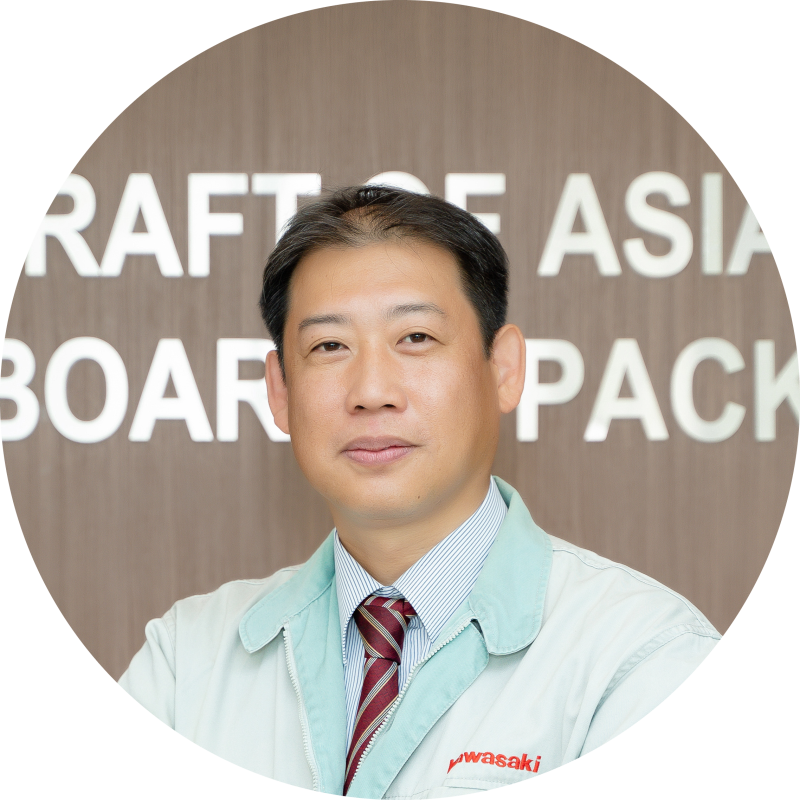
Given that the average outside temperature in Vietnam is 28 degrees, it’s possible to generate 6.7MW of power with each turbine, so that’s 13.4MW in total for the two turbines in this project. It’s possible to supply approximately 80 tons of steam per hour overall. A key feature of the system is its ability to balance the supply of electricity and steam required by the paper mill. In verification tests we ran together with TTE at the plant, we were able to achieve over 90% efficiency for both electricity and steam.
So, using a natural gas CGS, KOA’s paper mill has been able to achieve high-efficiency energy use. The next target is to realize totally clean plant operations by switching to hydrogen, an energy source completely free of CO2 emissions. Discussions around the feasibility of using Kawasaki’s gas turbines, which are also compatible with hydrogen fuel, are proceeding steadily. Kawasaki’s development of hydrogen gas turbines started from a small gas turbine that enabled the mixed combustion of hydrogen and natural gas, and today Kawasaki has realized a combustion system capable of running on 100% hydrogen. Kawasaki is now in the process of gradually expanding application to larger gas turbines and has reached the stage of being able to supply products to customers. Torii has the following to say about the combustion method, which posed the biggest challenge during development.
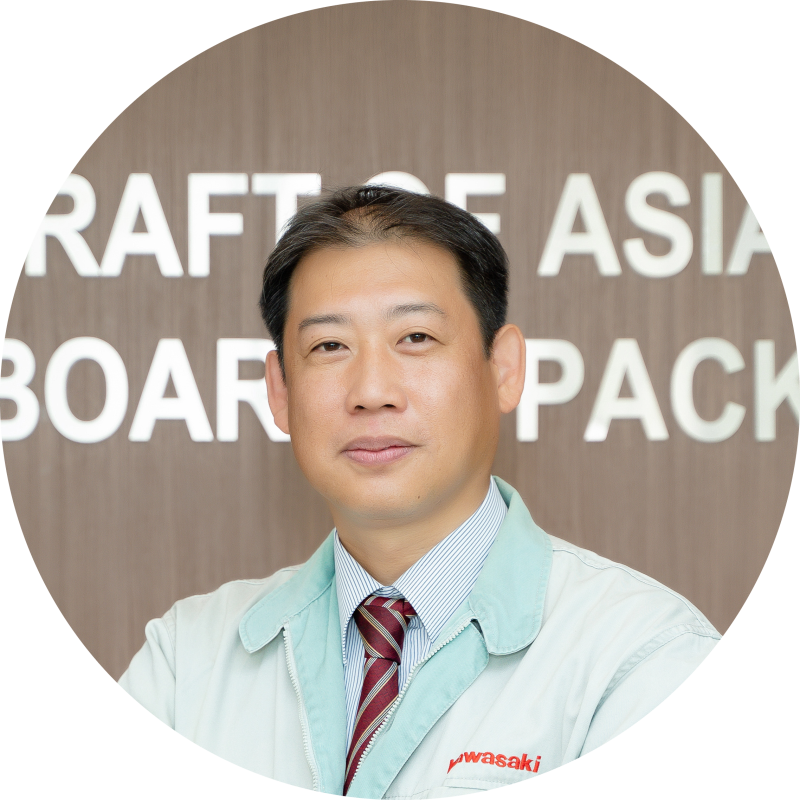
Hydrogen is a light, fast-burning gas that is easy to ignite. We focused on developing combustors that would enable stable combustion, and worked to build a gas turbine power generation system suited to using hydrogen as a fuel source. We think we will also need to put together proposal packages with varying hydrogen volumes, which will make it easier for customers to transition from natural gas to hydrogen.
For example, Kawasaki plans to offer a mixed combustion system for customers who may find it challenging to secure the large volumes of hydrogen they would need to power a 100% hydrogen-fired system. In this way, Kawasaki would offer a range of options based on the available supply of hydrogen.
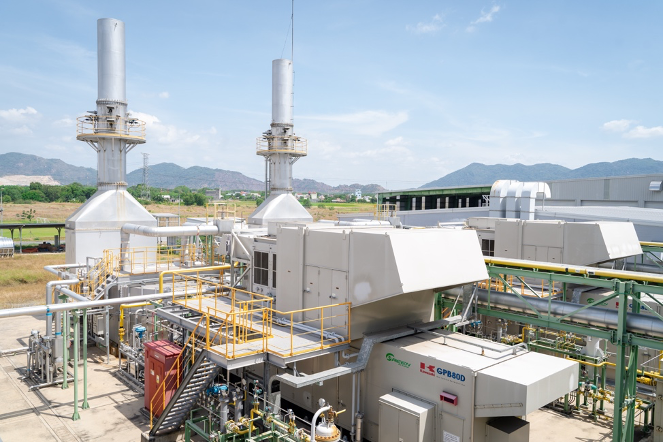
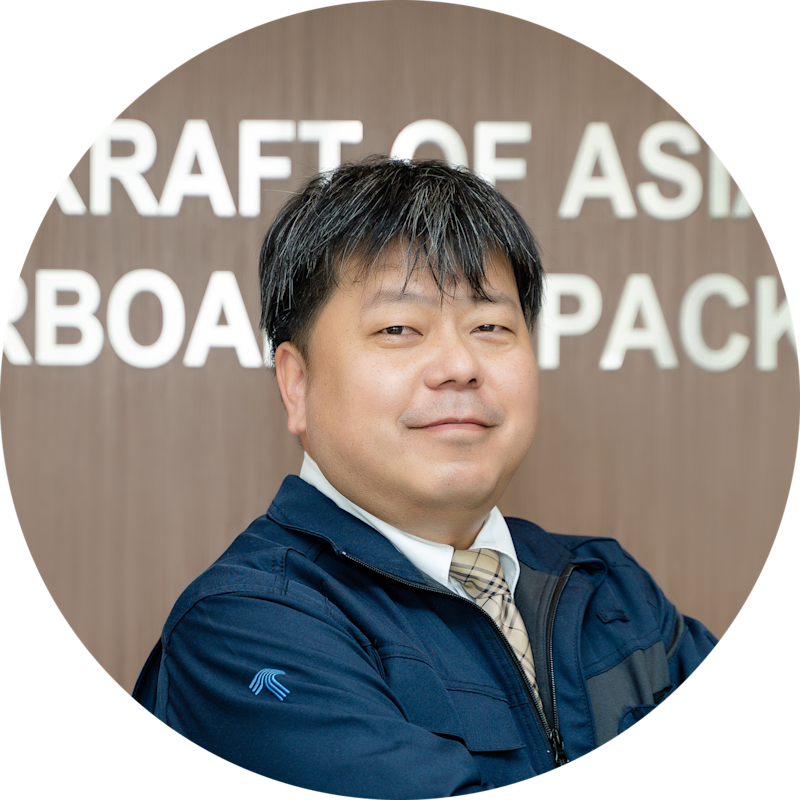
In Vietnam, the legal and regulatory systems for hydrogen utilization are not yet fully developed. One example is that government-mandated rules on prevention of fires, etc., are unclear, which means that, more than usual, we have to confirm each and every item as we proceed. It’s something without precedent in Vietnam, so you face the difficulty of having to create rules from zero. We will continue to build facilities that can provide stable energy while meeting all the required specifications.”
Matsumura is already thinking about the future and the switch to a cogeneration system powered by hydrogen.
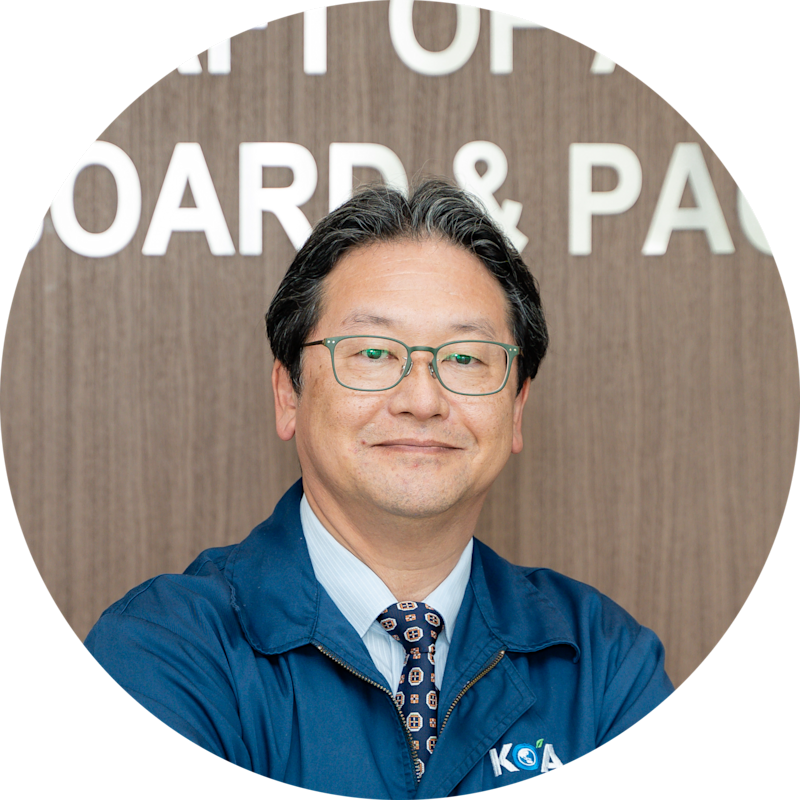
There are many chemical plants here in Phu My 3 Specialized Industrial Park, some of which are actually disposing of hydrogen created in production processes as a waste product. We found out that the volume of this hydrogen would be equivalent to the volume needed to operate our gas turbine, so we are looking into how we can source our hydrogen from these nearby plants.
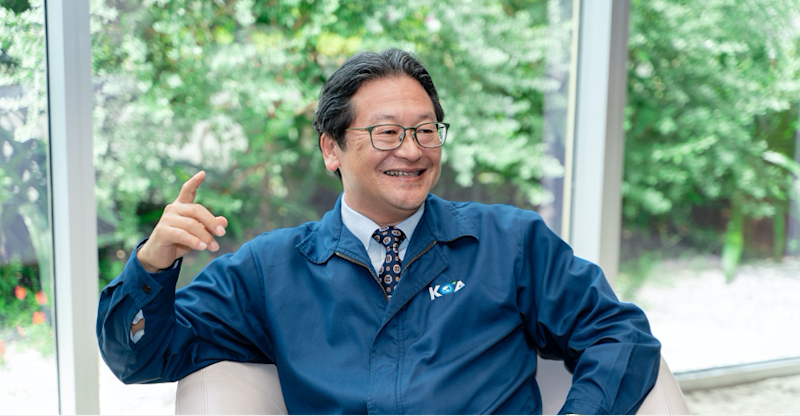
KOA is specifically thinking about converting at least one of the two turbines to hydrogen power during the next major overhaul planned for 2025. If that plan is realized, the plant could become either the world’s first, or at the very least Southeast Asia’s first plant to introduce a hydrogen-powered gas turbine CGS.
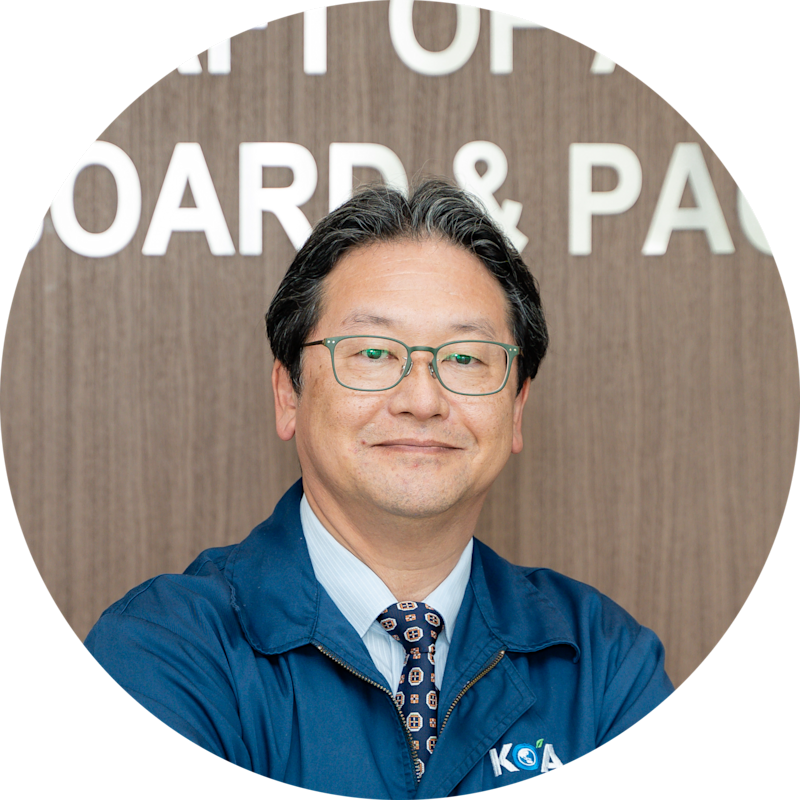
We have already announced to our customers that we plan on moving to hydrogen CGS, as part of our aim to become the paper mill with the lowest emissions worldwide. We must end the industrial practice of running plants on power that generates vast quantities of CO2. KOA wants to be at the forefront of that movement.
A forerunner and trendsetter for decarbonization
As they move onto their next big project of switching from natural gas to hydrogen, how do KOA, TTE and Kawasaki view the future?
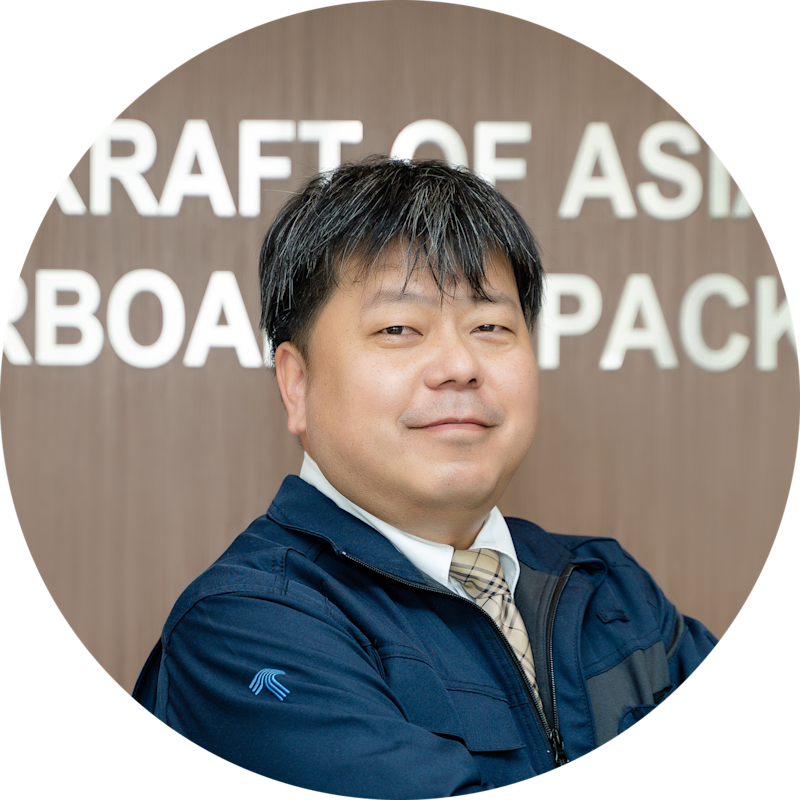
The exciting thing about doing something no one else has done before is that although you face unique challenges, if you’re successful then you get to make the rules. I hope we can continue to partner with KOA and Kawasaki on our next challenge, making the switch to hydrogen. I want us to make preparations ahead of anyone else and share information frequently with customers so that they feel motivated to take this step. By doing so, I hope we can quickly get a system up and running that demonstrates we are ready and able to do this.
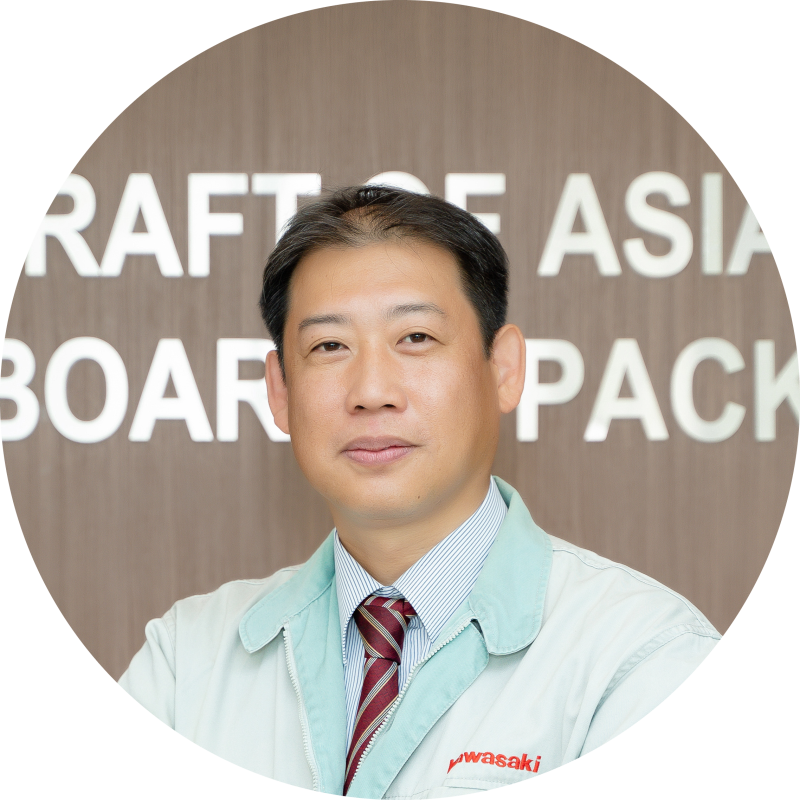
Electricity companies in Vietnam are in a tough situation financially, and are unable to invest in equipment to ensure a stable supply of electricity or in expansion to increase power supply capabilities. That’s why KOA’s investment, as a private sector company, in the creation of distributed power generation will ultimately contribute to alleviating Vietnam’s power deficit. What’s more, if those power generation systems are CO2-free, it will be all the better for Vietnam as a whole.
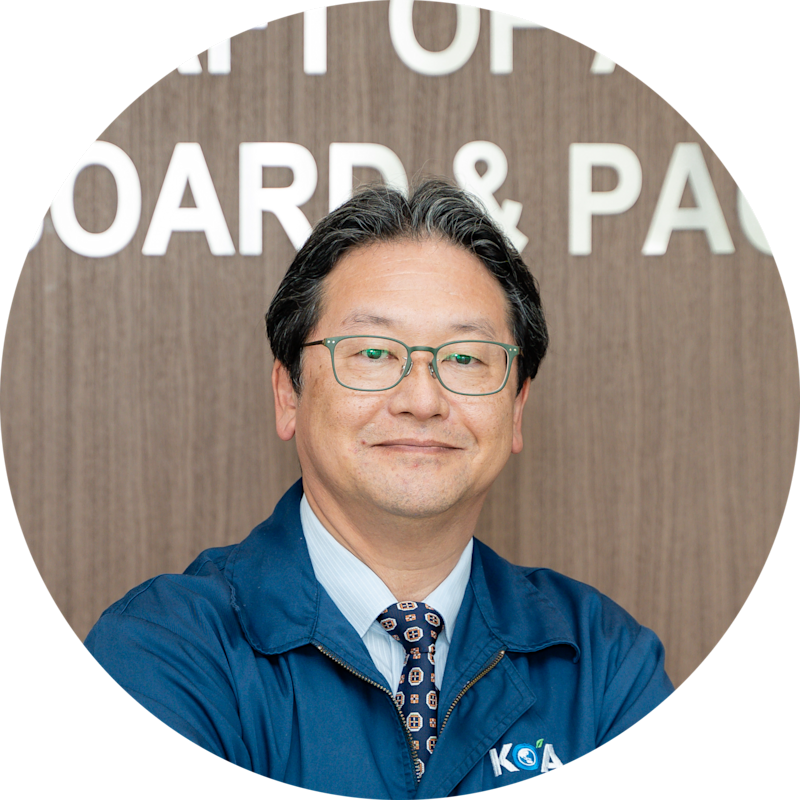
One of the Vietnamese government’s pledges is to realize zero emissions of greenhouse gases by 2050 and that is something to which we are also committed. Hydrogen-powered gas turbines will be a vitally important part of realizing that commitment. If one company starts doing it, then others may also follow. If we can instigate such a trend, then we will, in a broad sense, be contributing to Vietnamese society as a whole.
Vietnam’s first-ever natural gas turbine CGS is already in the process of evolving into the world’s first hydrogen gas turbine CGS. With an eye firmly on the future of the industry, KOA, TTE and Kawasaki are taking pioneering steps into the unknown and paving the way to a decarbonized future.
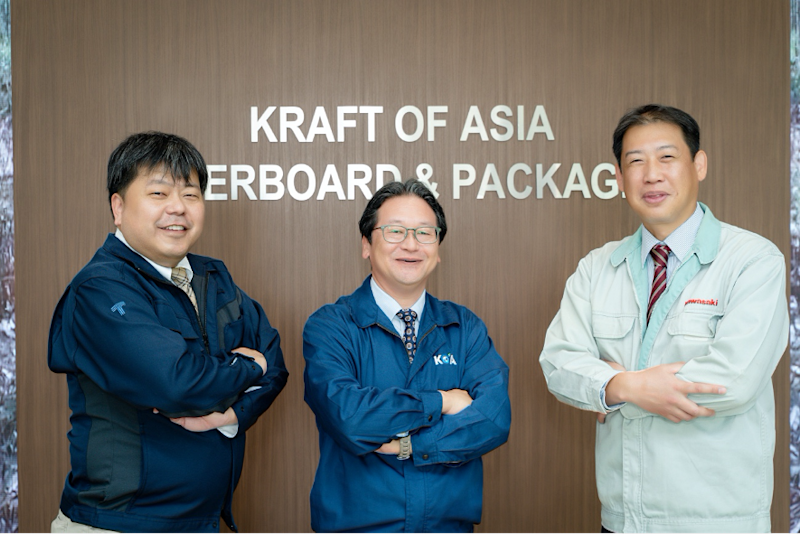