Kobelco Construction Machinery x Kawasaki. Possibility of Future Construction Machinery Expanded by Hydraulic Pumps
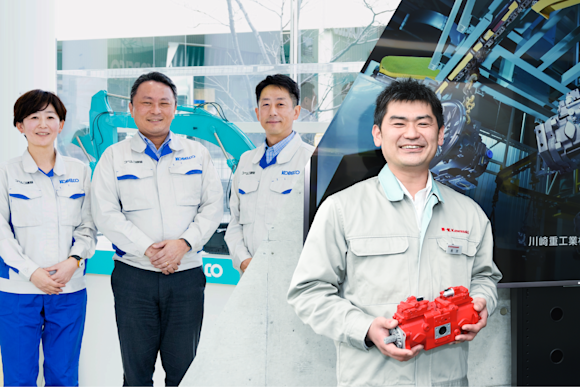
Have you heard about hydraulic equipment? Hydraulic equipment uses a system to convert a small force into a large power based on Pascal's principle (*1). Such a mechanism is always integrated into large artificial objects, including machinery working at construction sites and factories, as well as on ships and aircraft, in order to control motion, and the use covers a broad range in society. Kawasaki has grown the hydraulic equipment business, which started with the release of electro-hydraulic steering gears in 1924. Almost a hundred years have passed since the commencement of the business, and now is the time when solutions to energy consumption and labor shortages are in demand in each industry, and the assumed role of hydraulic systems is increasing. This article describes the roles of these products that operate behind the scenes even now to help solve a variety of social issues and their progress for the future.
Hydraulic Pumps Keep Evolving Over a Long Time
While a hydraulic system actualizes great force with precise control, the component that plays the role of generating power is the hydraulic pump. In 1968, which is about half a century ago, Kawasaki launched the KV Series of hydraulic pump for Japan’s first 100% domestically produced hydraulic excavator. The new models, released in 1981, were called the NV Series. Thanks to modification of piston shape machining, development of a new material for sliding surfaces, and the idea of joining two pumps in a tandem arrangement, the series offered greater pressure and higher speed in a smaller frame and rated pressure*2 that finally reached 32 MPa.
The subsequent K3V Series appeared in 1988. The number of parts was reduced by 30% to make it more price competitive, which gave the made-in-Japan hydraulic excavators the driving force to spread out and dominate the world market. Then, in 2014, the well-prepared latest model, the K7V Series, was launched. The design of major pump components was reviewed thoroughly to achieve the rated pressure of 35 MPa that offered higher efficiency, increased reliability, and a longer service life than the previous K3V Series.
Although the appearance of Kawasaki’s hydraulic pumps has not changed remarkably, they have matured steadily for as long as fifty years.
*1 Blaise Pascal, French philosopher, proved the principle that pressure applied to any part of an enclosed static liquid will be transmitted to all parts of the liquid at the same pressure
*2 Rated pressure indicates the maximum pressure at which the equipment driven by a hydraulic system can be used continuously with a payload applied to it. The larger the numeric value, the higher power it can exert and the more efficiently it works. It also means that the machine is more robust against a load and is less likely to fail
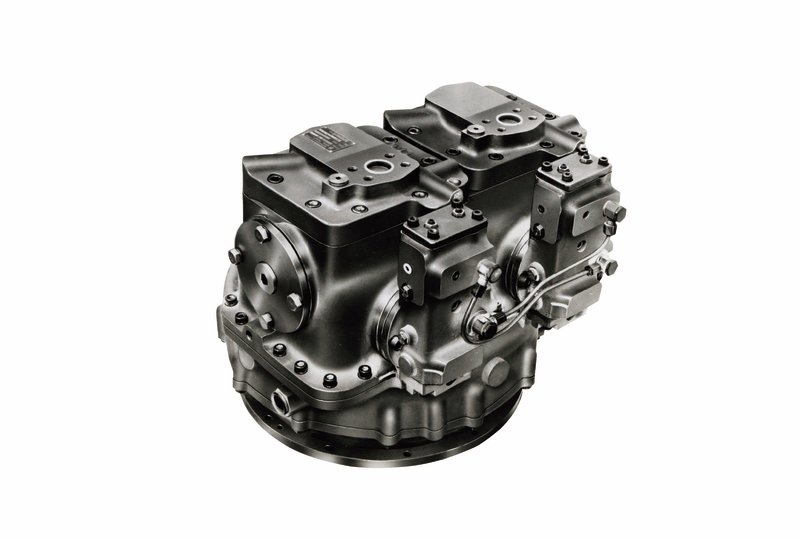
Kawasaki KV Series Mounted on the First Excavator Completely Made in Japan
How was the high-efficiency, long-life hydraulic pump K7V achieved?
Seeking higher efficiency to reduce energy loss has been a crucial subject in hydraulic pump development for a long time. Improved efficiency leads to energy savings and the reduction of CO2 emissions. In addition, the globalized market has increased the occasions where hydraulic excavators are used in harsh environments overseas, which demands higher reliability from hydraulic pumps.
Kawasaki developed computer programs to predictively calculate the minute energy lost inside a pump at high accuracy and obtained the point of maximum efficiency under the constraint of part interference and strength. As for extending the service life, if the housing to support the pump structure is made thicker and more solid, then the pump body becomes bigger and cannot fit into the construction equipment. How is pump performance increased in this trade-off relationship? This is the place where hydraulic pump designers to show their ability. They make full use of simulation tools and advance the development of hydraulic pumps for the optimum balance between size and performance.
Another concern for achieving a longer service life is the design of the moving parts, including the piston in the cylinder block and the shaft. The piston-cylinder geometry has micrometers of recesses on the contact parts so that the load is spread out over an area and the risk of breakage is decreased. In addition, the thicker shaft reduces the deformation due to the centrifugal force and stabilizes the posture of the internal parts, contributing to endurance.
Since Kawasaki has taken many years and many actions to improve the efficiency of hydraulic pumps, little room remains—it’s as if you tried wring water from a dry towel. The energy efficiency of the K3V released in 1988 was around 91% and that of the K7V, which became commercially available 26 years later, was 93% to 94%. These numbers simply show that improvement was only two to three percent in almost three decades. However, this small difference is valuable to users and significant in terms of reducing the environmental burden of construction machinery and the enhancement of operability.
There is a concentration of the predecessors’ wisdom accumulated so far. The K7V developed in this way is certified and registered as part of Kawasaki Ecological Frontiers, superior products in terms of whether the products evidence improved environmental performance and whether the associated manufacturing processes demonstrate a reduced environmental impact, by Kawasaki stating the goal to realize carbon neutrality by 2030.
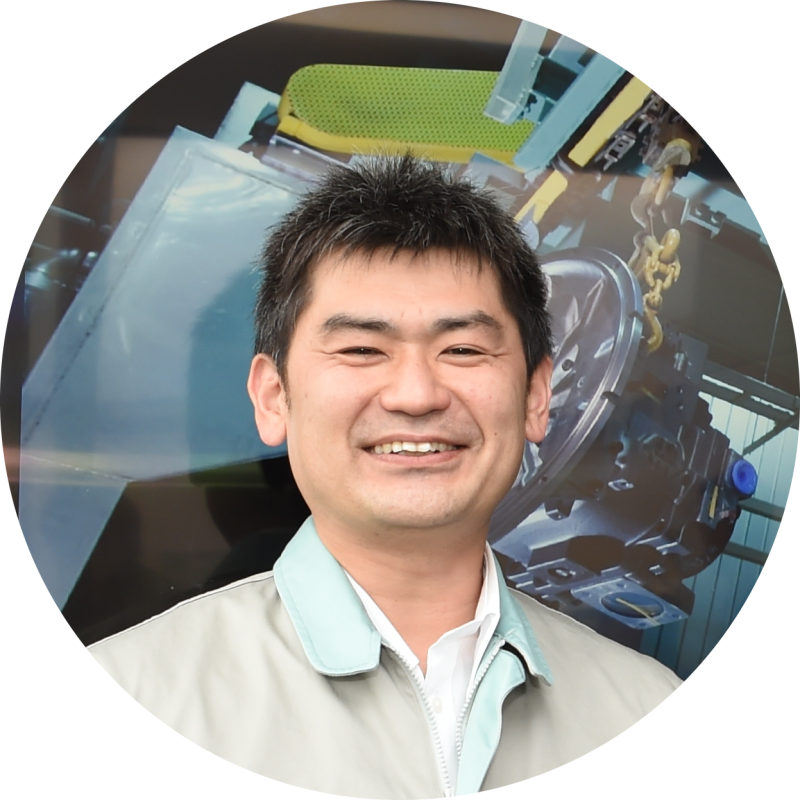
It always seems to me that while I am involved in the development of the K7V from the initial stage up to now product development is not like individual competition but team competition. Not only the design division but also all personnel from manufacturing to sales think together of ways to produce better products, and we sometimes have conflicts of opinions. However, every member has the same determination to make good products and to please the customers with them. I am interested in and motivated by the process of accomplishment by a team with a feeling of unity of the company.
Firm Partnership Creating Excellent Products
A hydraulic pump does not serve any purpose when it is alone, but it functions once the pump is allocated as a part of a system. In this sense, the relationship with construction machinery manufacturers is of critical importance.
The partner in the joint development of the K7V was Kobelco Construction Machinery, which has been an essential partner to Kawasaki since the era of the first hydraulic pump, the KV Series, released in 1968, and a strong relationship has been formed by working on different products for more than half a century. The main role of Kawasaki is to develop hydraulic pumps as a component and to fine-adjust the specifications for integration into the final products, while Kobelco Construction Machinery deals with the optimum design of the excavator system and the execution of a performance evaluation of the excavator with the hydraulic pump mounted. The issues revealed through the tests are resolved using the technologies of both companies.
The experiments on a hydraulic pump installed in an actual excavator discloses any hidden problems when the pump is tested as a single unit. The most challenging subject in this collaborative work was the elimination of the phenomenon called hunting, which is the unstable and fluctuating condition of the position and the velocity around the target values. Two patterns of unstable excavator motion, which occurred at low and high temperatures, were identified during trial operation of the excavator in actuality.
The two parties investigated the causes by, for example, attempting to reproduce a phenomenon that happened to the excavator on an independent pump and then discussing the countermeasures together to reach a solution in each case of low and high temperatures. Mr. Terauchi and Mr. Ueda from Kobelco Construction Machinery recall the days of this development and commented that success was owed to the close partnership of both the machine and the system designers.
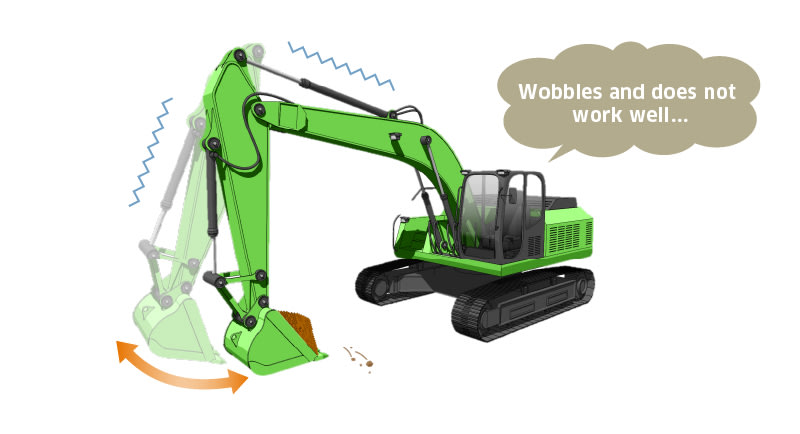
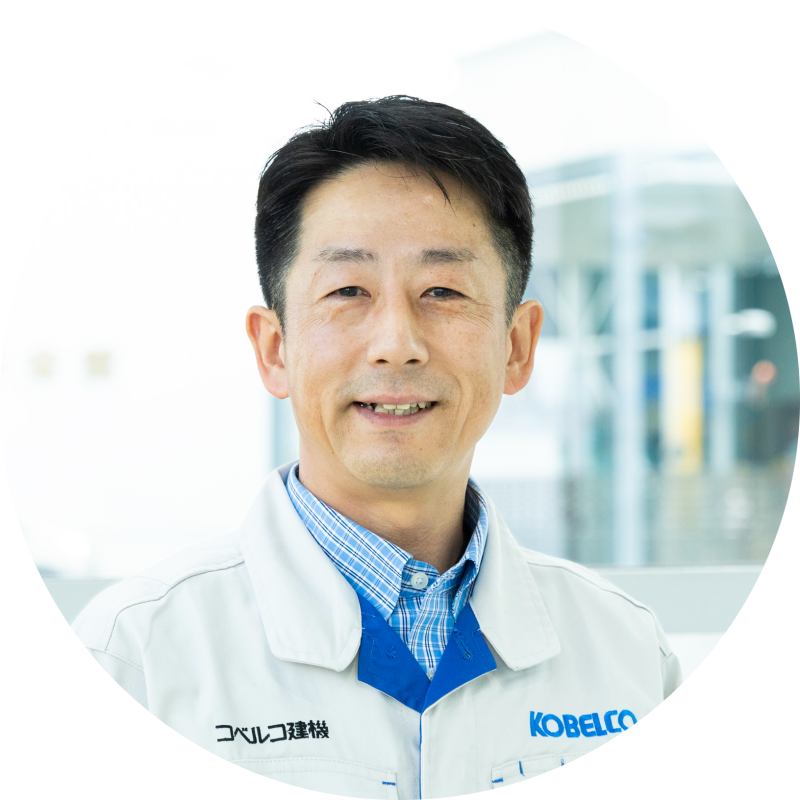
The strong selling point of our products is their energy saving performance, and the key to realizing that performance is the hydraulic pump, the heart of an excavator. The measures to elevate efficiency incurs a variety of disadvantages, and the superiority of the product depends on how many trade-offs were compensated within the development period. We requested many improvements this time, as well, and Kawasaki was very reliable because of the speedy, proper adjustment to our products.
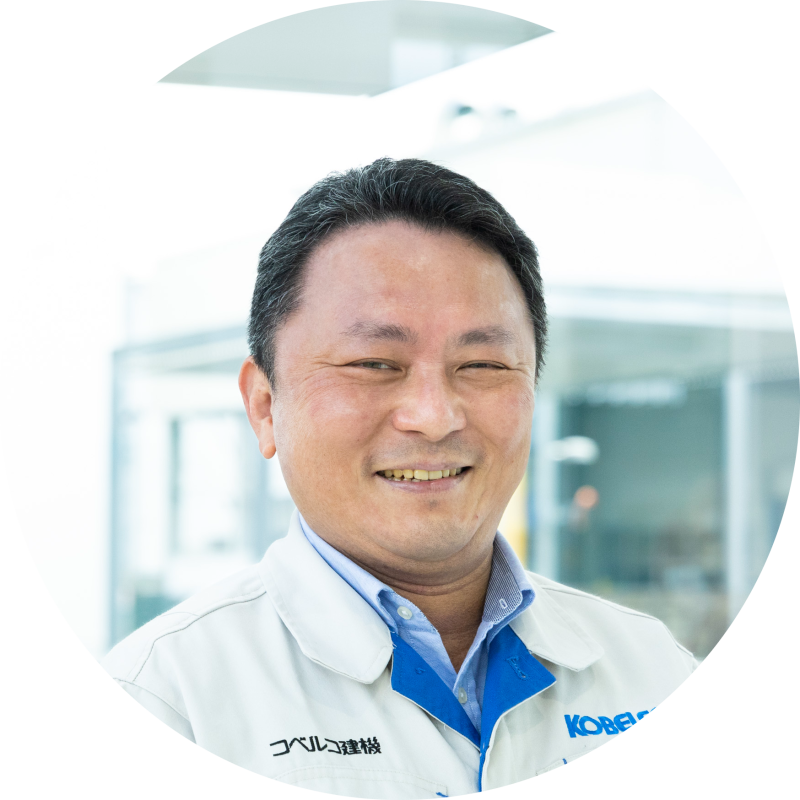
This development was particularly demanding for Kawasaki in terms of durability. The pump is the heart of the excavator. If the pump breaks, the machine is out of order even if the engine is running; moreover, fragments can enter the fluid, damaging components at the same time. For this reason, the pump can become the most troublesome part if it fails, and the degree of toughness affects the market evaluation. We, therefore, set a higher target for durability than previous models every time a new product is planned. Right now, no other vendor of hydraulic pumps materializes permanence, low cost, and fine performance at such a high level, and Kawasaki is a major supplier for us as a result.
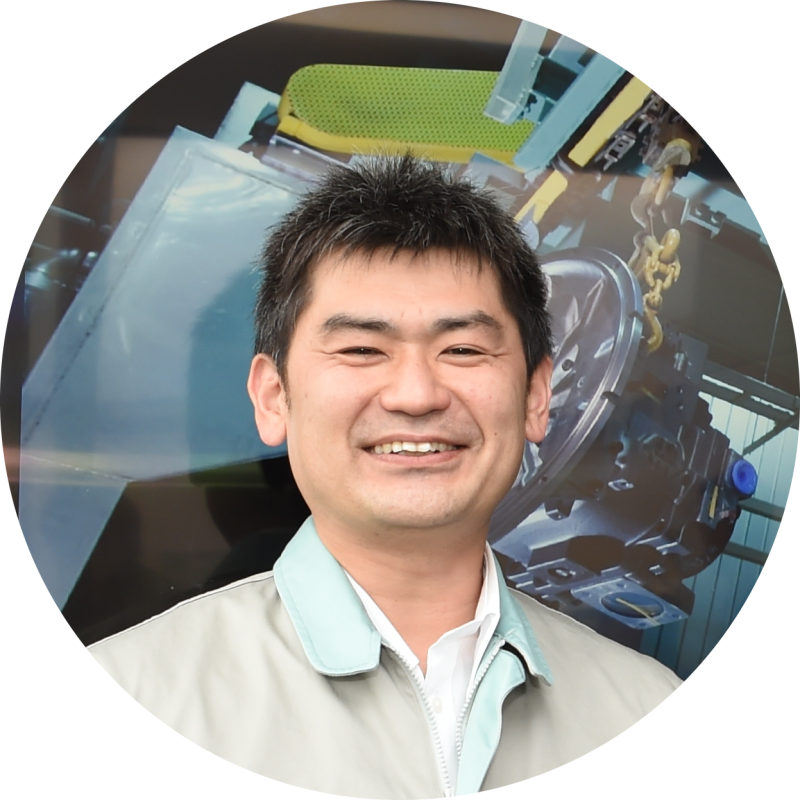
I am strongly impressed by the customer-first attitude of Kobelco Construction Machinery for manufacturing, which is the wish to make their desire come true. The company always sees matters from the standpoint of users and clearly indicates to us how things are supposed to be during the development of the K7V as well. In the course of these tasks, I reviewed and acknowledged our products as a part of a system, recognized what was hardly visible during the ordinary work of an engineer, and learned again how important it was to satisfy customers.
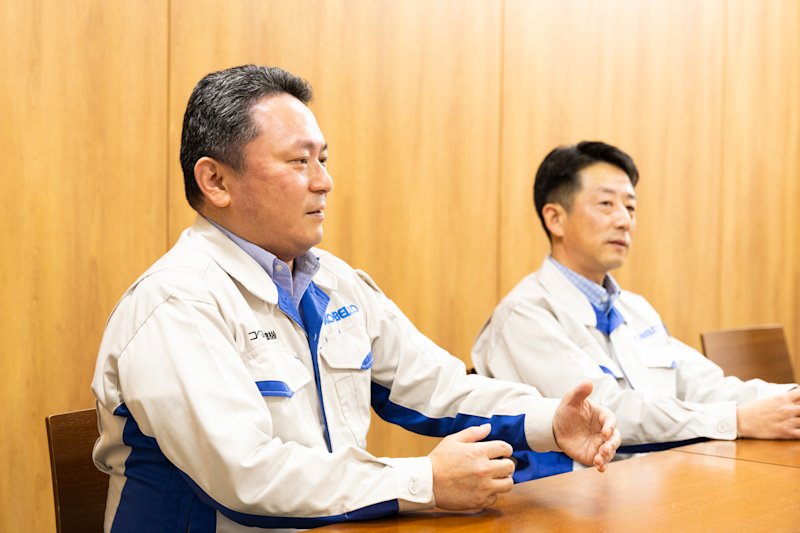
Solutions for the Future Via Construction Machinery and Hydraulic Equipment
The present civil engineering and construction industry of Japan faces many issues. The primary issue is the response to environmental concerns. Construction machines are responsible for 1.4% of CO2 emissions in the domestic industrial sector and account for 0.5% of the entire amount in Japan. It is necessary to create construction machines with enhanced performance toward the realization of carbon neutrality by 2050. Kobelco Construction Machinery and Kawasaki not only develop hydraulic machines but their systems are capable of functionality enhancements so they can promote activities with an eye on electrification, the use of hydrogen, and the fusion of different novel technologies.
In addition, there are the challenges of a decreasing workforce and the aging of skilled operators in the said industry, and the means required to solve them is implementation of smart technologies for such machinery, in other words, actualization of excavators working at construction sites remotely or automatically without anyone in the operator’s seat.
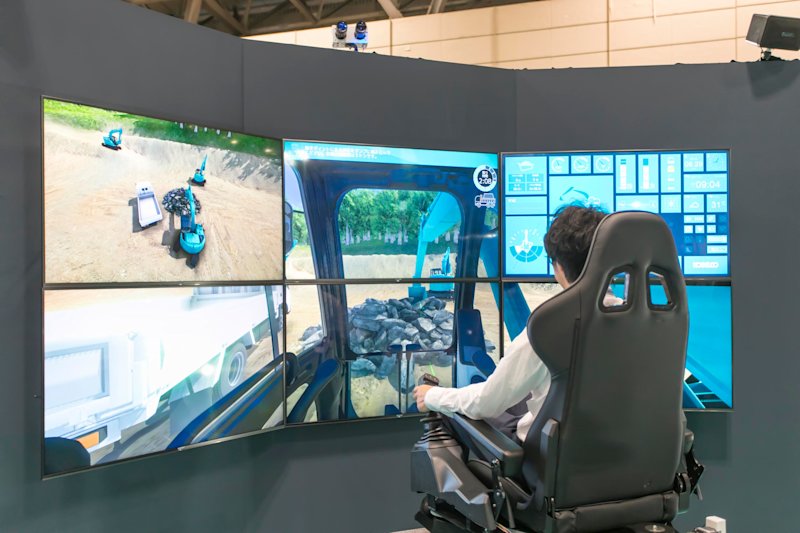
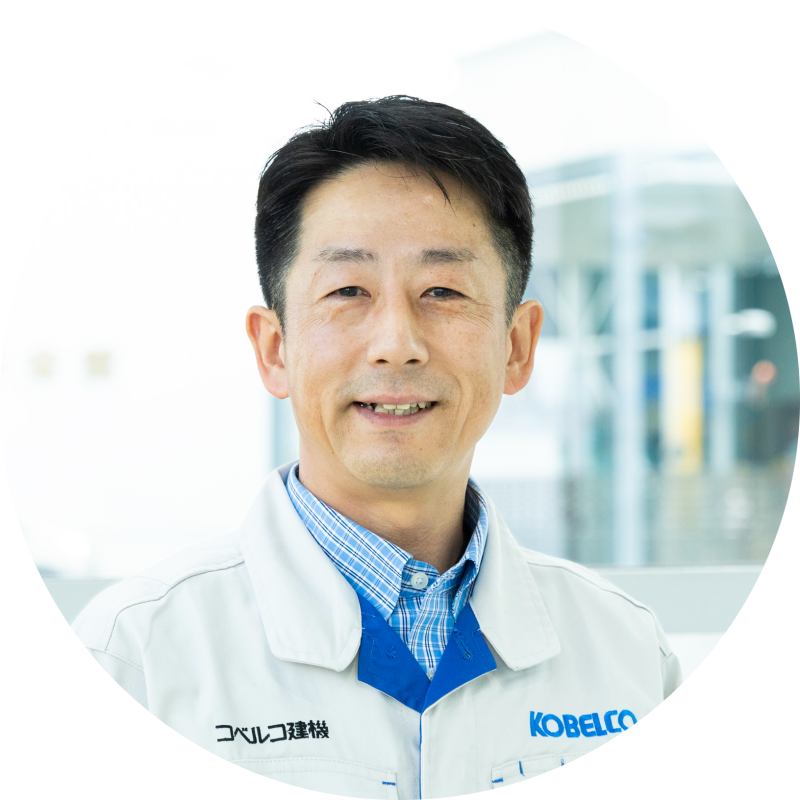
Concerning the excavator business, Kobelco Construction Machinery emphasizes the development of K-DIVE, the system for convenient remote operation with ICT incorporated positively. When construction using ICT and remote technology becomes available, unproductive work is reduced, construction at a distant or poorly accessible location is enabled without the necessity of going to the actual job site; thus, the possibility of the construction industry should be expanded substantially. We think the development of the technology will be a solution to the various problems in the construction domain, including environmental issues and the shortage of manpower.
Ms. Kubo from Kobelco Construction Machinery stated that the spread of K-DIVE allows more human resources to be engaged in the construction business from the viewpoint of a woman.
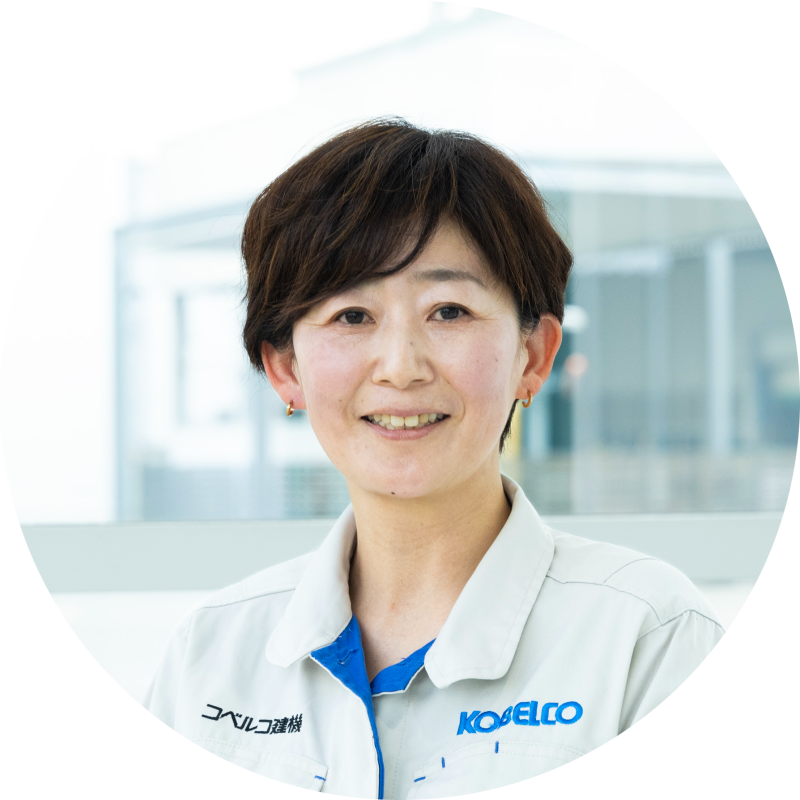
K-DIVE is bringing about the evolution of Kobelco Construction Machinery’s business from dealing with the tangible to the intangible, more specifically, not just supplying products but solving problems by means of its products. While the working population is declining today, fulfillment of the technology to operate construction equipment without attendance at the site will allow ladies and a more diverse range of people to be active in the field of construction.
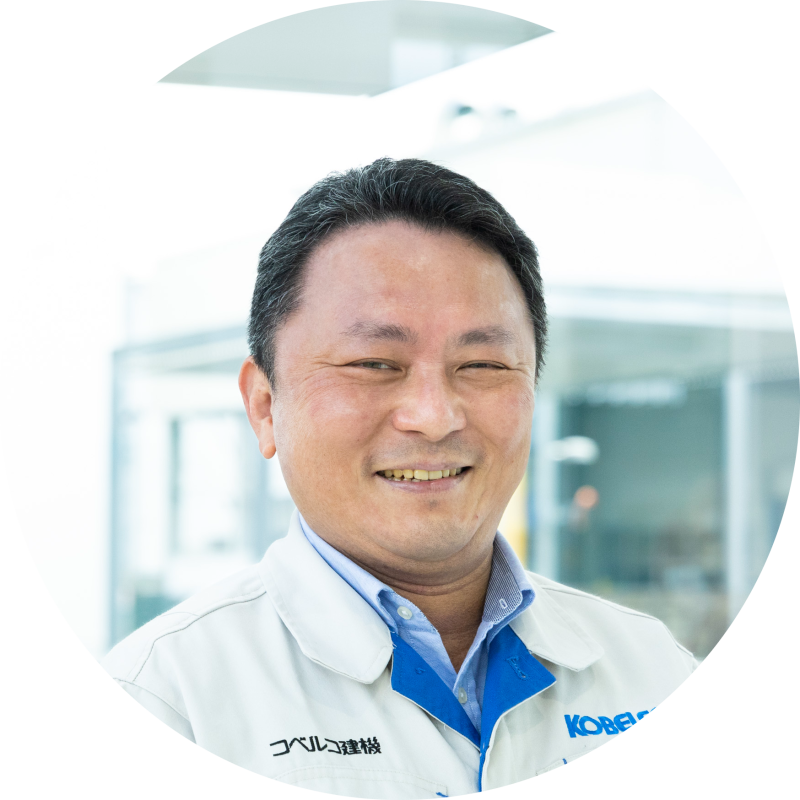
When you think about realizing remote operation, the hydraulic devices must be more reliable than ever before. Moreover, for improvement in work accuracy, it is ideal to control hydraulic machines for the output as ordered. In order to accomplish the targeted goals of ICT construction, we have enormous expectations for the hydraulic equipment from Kawasaki, which is proud of its excellent technology in the area of robots.
The automation and unmanned operation of construction machinery and the fusion with ICT and IoT technology is required in the near future. When it comes true, you will command a view of the construction industry of the time ahead. The core part will be the next generation of hydraulic equipment that has evolved from the comprehensive capabilities of the multifaceted enterprise that is Kawasaki.
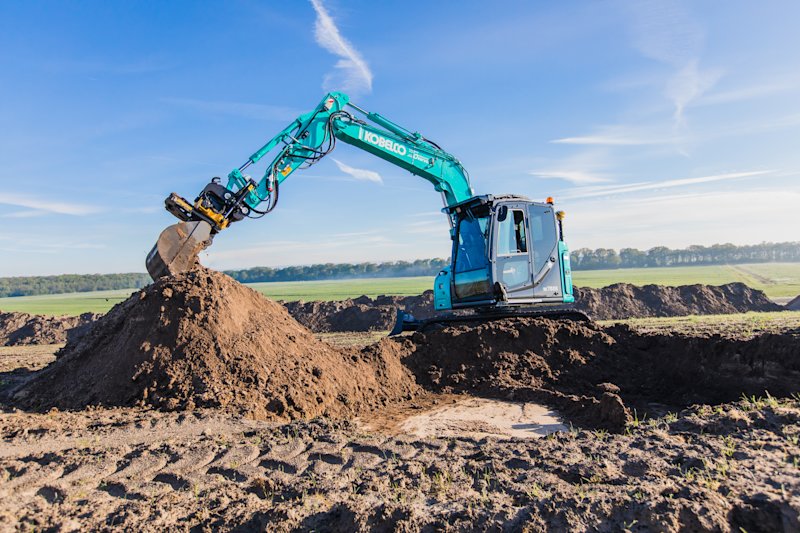
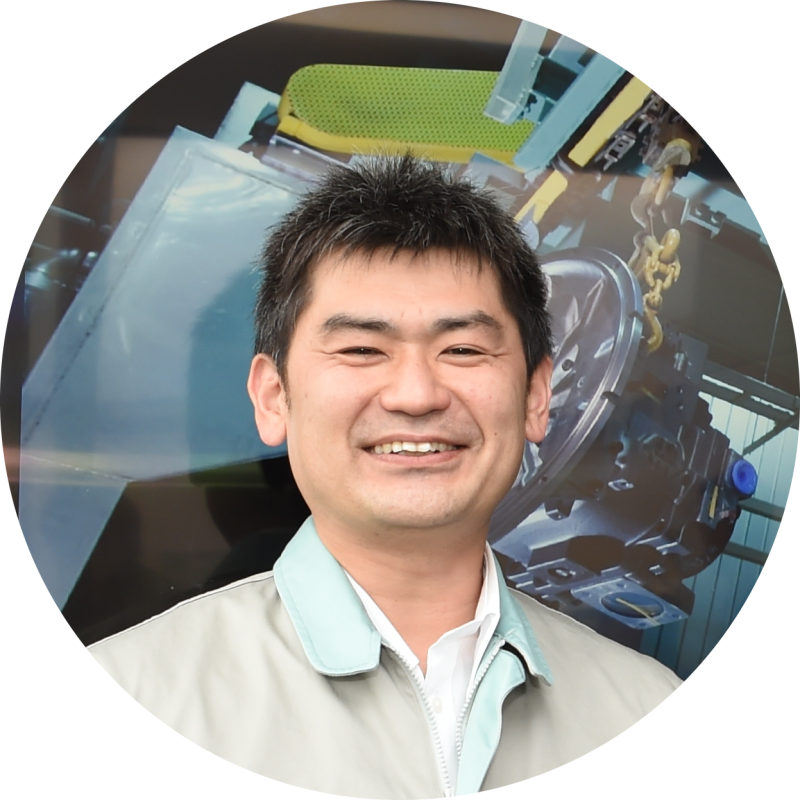
Control System Development Department
ICT Utilized Development Group
Precision Machinery Business Division
Precision Machinery & Robot Company
Kawasaki Heavy Industries, Ltd.
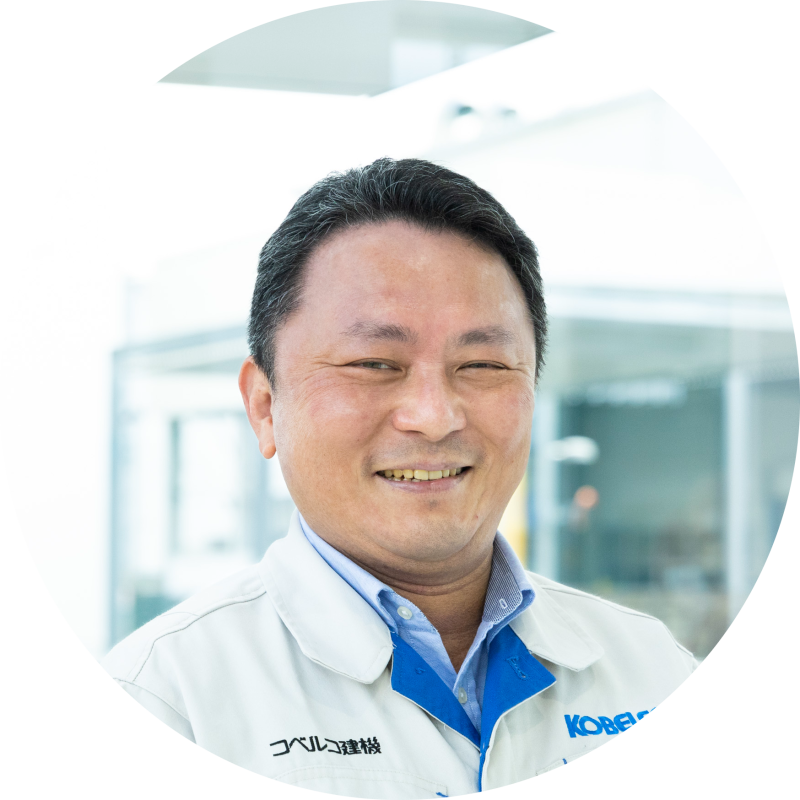
Zero Emission Engineering Department
Product Development Engineering Division
Visiting Professor of Toyohashi University Of Technology
Kobelco Construction Machinery Co., Ltd.
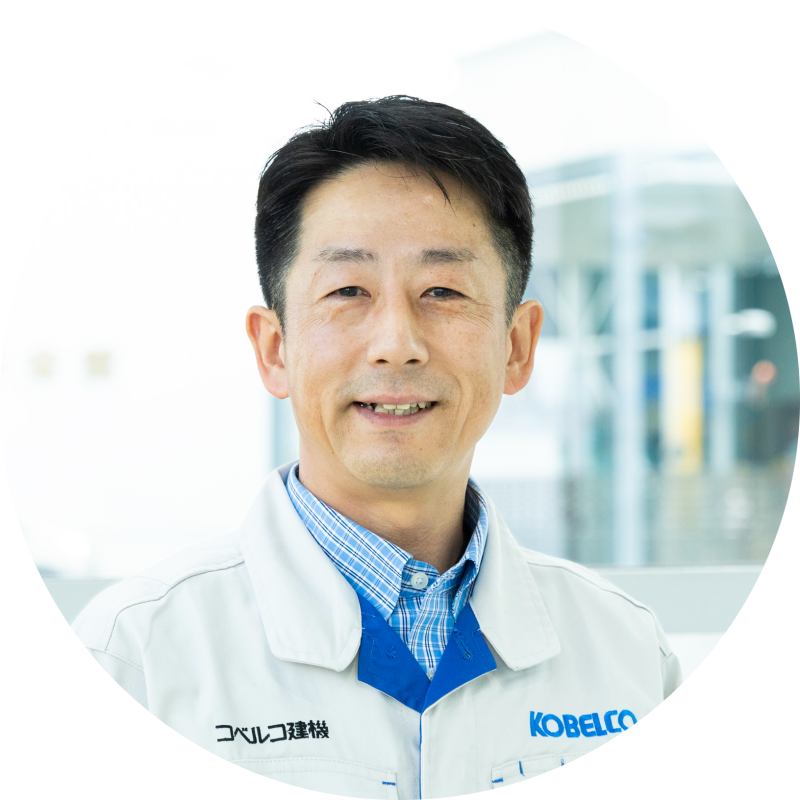
System & Component Department
Product Development Engineering Division
Kobelco Construction Machinery Co., Ltd.
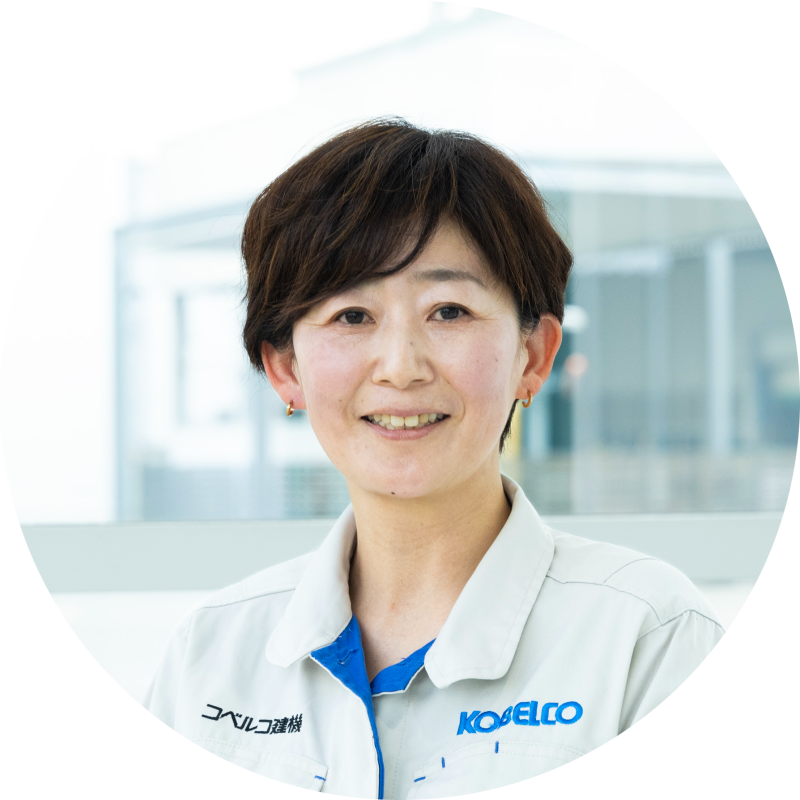
Global Production Control Department
Production Division
Kobelco Construction Machinery Co., Ltd.
*The numerical values, job titles, and other information contained in the article are current at the time of the interviews