Meeting the Stringent Demands of Environmentally Aware Europe-Kawasaki's Cement Plant Waste Heat Recovery Power Generation System-
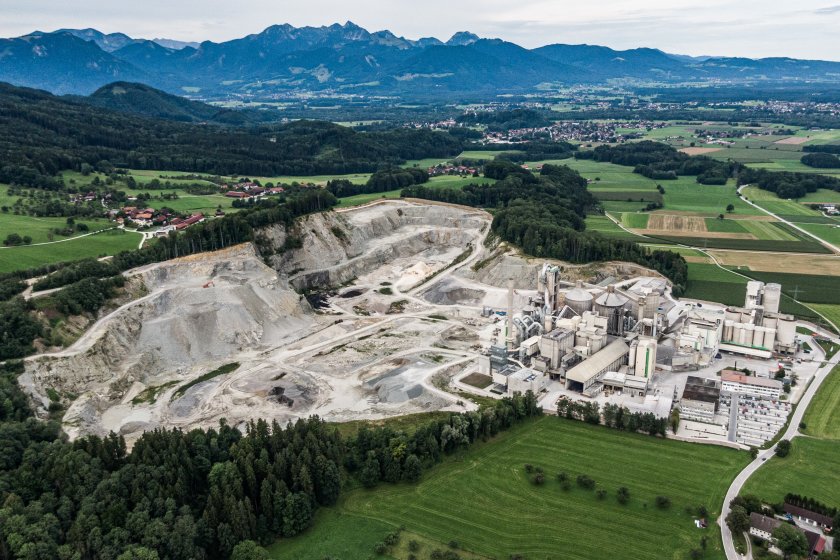
The European Union has always been at the forefront of the world's efforts to tackle climate change. The EU has set a goal of becoming the world's first Climate Neutral continent by 2050, but it now faces a serious dilemma of tackling climate change and securing energy while an energy supply crisis was hitting the world in 2022. Against this backdrop, the introduction of waste heat recovery power generation (WHRPG) systems has been attracting keen attention in the energy-intensive cement industry. The starting point of this attention is in Rohrdorf, Bavaria in southern Germany.
What is the best solution to the energy and climate crisis?
In 2019, the European Union put together the European Green Deal, a blueprint for environmental transformation, declaring that greenhouse gas (GHG) emissions will be net zero (Climate Neutrality) by 2050. As a step toward achieving this goal, the EU has set an ambitious target of reducing GHG emissions by at least 55% (from 1990 levels) by 2030.
However, in order to achieve a 55% reduction in greenhouse gas emissions by 2030 compared to 1990 levels, emissions must be reduced by an average of 130 million tonnes per year from 2021 levels in terms of CO2 equivalent. This is equivalent to double the average annual reduction volume achieved from 1990 to 2020, requiring even greater efforts to reduce emissions. Social conditions are also becoming increasingly severe in order to achieve this goal. The global energy situation changed drastically in 2022, and the energy supply crisis is about to become permanent.
The ”Trends and Projections in Europe 2022“ (Climate Action Progress Report) by the European Environment Agency (EEA) states that short-term measures to secure energy supplies and support the most vulnerable households are necessary and justified.1 While the report accepts a temporary increase in fossil fuel consumption, it nevertheless shows no wavering in the EEA's basic policy that energy saving and the production of renewable energy in Europe are the best solutions to the problems presented by the unfolding energy and climate crisis.
1The European Environment Agency (2022, p. 12), Trends and Projections in Europe 2022. Copenhagen, Denmark. Available at:
https://www.eea.europa.eu/publications/trends-and-projections-in-europe-2022
To begin with, the EU has developed various measures targeting energy-intensive industries such as power generation, steel, cement, and oil refining. Germany is a pioneer in energy saving and energy reuse in the EU cement industry.
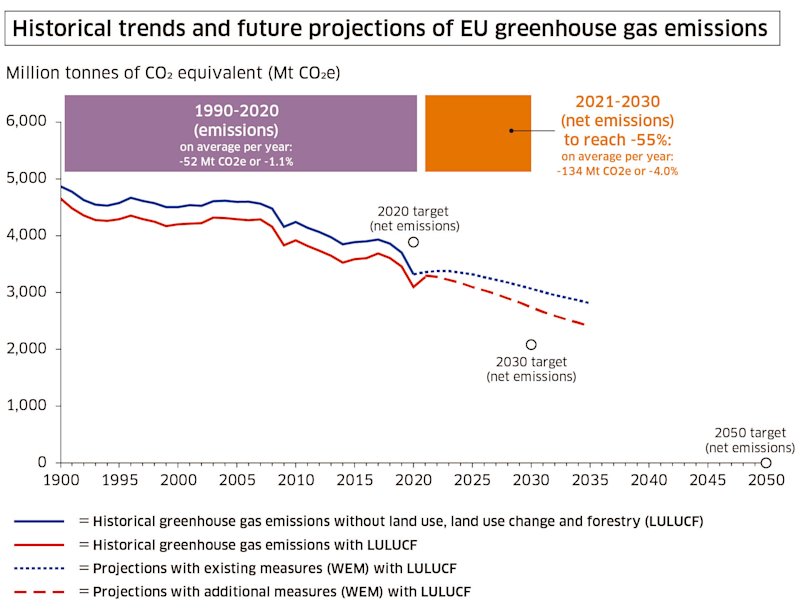
Background of German Rohrdorfer Cement's foresight and confidence
In Rohrdorf, Bavaria in southern Germany, here is Rohrdorfer Cement headquartered, a major cement manufacturer with more than 150 locations in Germany, Austria, Italy and Hungary. The manufacturer produces and markets not only cement but also ready-mixed concrete and precast concrete products, etc.
On September 24, 2022, the "Plant Open Day" was attended by approximately 3,000 local residents. Many of the residents were the most interested in learning about concrete measures to achieve the company's goal of "zero GHG emissions from the plant by 2038.” One of the factors that deeply convinced them of the achievement of the goal was the "Cement Plant Waste Heat Recovery Power Generation System" which has been operating without a single major problem in the 10 years since its installation.
WHRPG system generates electricity by using heat generated in factories and other plants that is not being otherwise utilized to produce high-temperature steam, which is then fed into a steam turbine. The "cement plant WHRPG system" uses "waste heat generated in the cement manufacturing process" to generate electricity. Rohrdorfer cement is a large-scale plant that produces up to 3,600 tons of clinker per day, Clinker is an intermediate product of cement (see below for details), every day. This system was installed ahead of other European customers in 2012 based on the company’s corporate philosophy, “Emphasize Sustainability,” and has a guaranteed output of approximately 6,800 kW.
This system provides approximately one third of the electricity required by the cement plant itself. The WHRPG system saves approximately 12,000 tons of fossil fuels per year. In addition, annual CO2 emissions are reduced by approximately 30,000 tons.
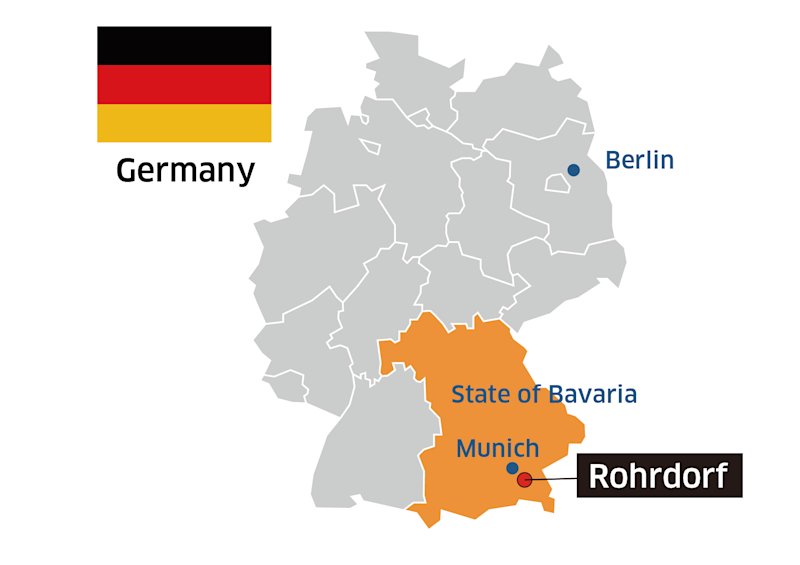
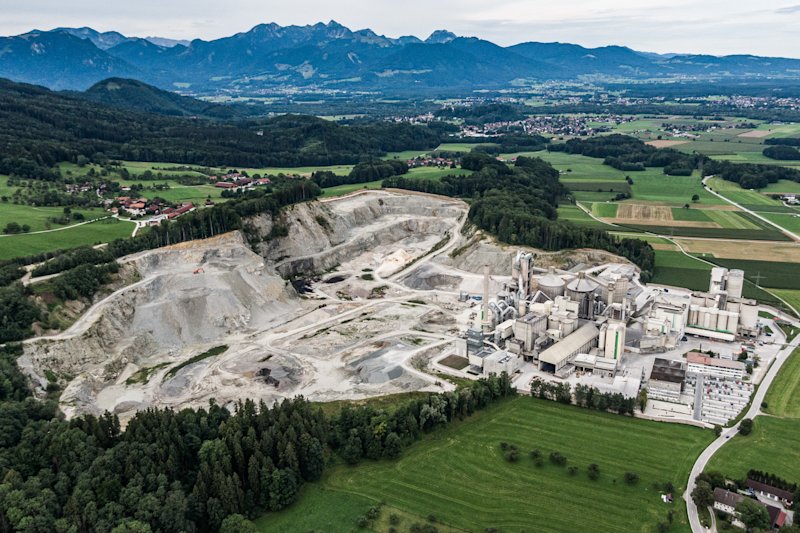
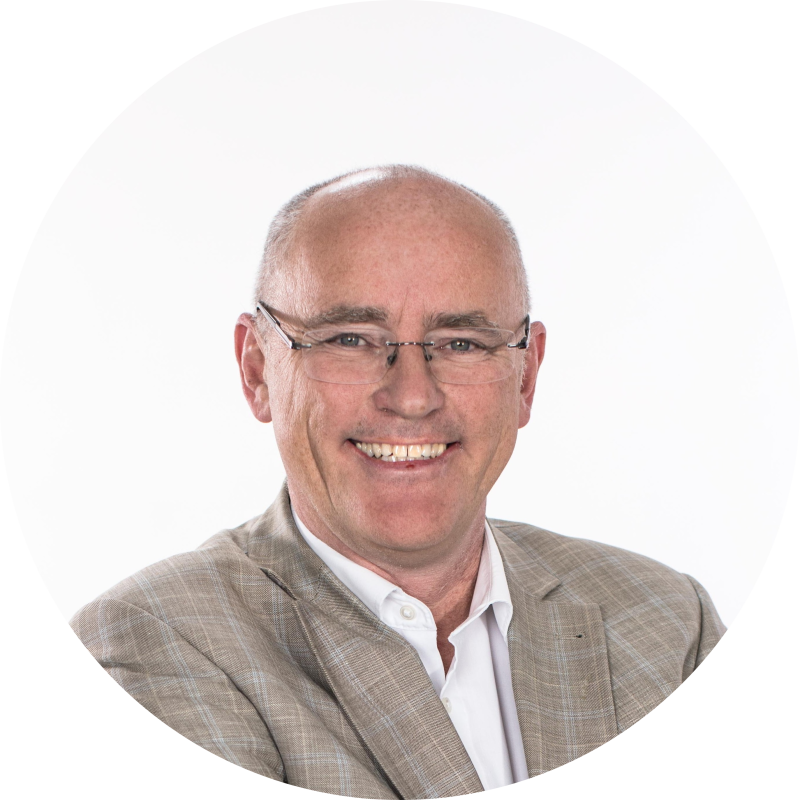
the decision to install a cement plant WHRPG system was "a business decision made in line with our corporate philosophy.” ”Our corporate philosophy is not to focus on short-term returns, but to think long-term and sustainability. This naturally includes using energy as efficiently as possible. That’s why the construction of the system was initiated ten years ago. This courageous step at that time was honored by DENA (German Energy Agency) with the “Energy Efficiency Award.”
Rohrdorfer Cement was the first German cement plant to install a CO2 recovery plant and the first in Europe to install a full-scale WHRPG system. In other words, Rohrdorfer Cement is a pioneer in Climate Neutrality in the German building materials industry.
”The shareholders and the management of Rohrdorfer Cement are always aware of their social responsibility towards people and nature, and our outstanding projects have been ahead of the legislation. We also select our partners and service providers according to these criteria" (Dr. Geller)
“Kawasaki was the supplier with the best competencies and a very good cost-performance ratio for the job," said Dr. Geller, citing the reason Rohrdorfer adopted Kawasaki's proposal. WHRPG system at Rohrdorfer Cement was proposed by Kawasaki with confidence as a way to embody Rohrdorfer's management philosophy.
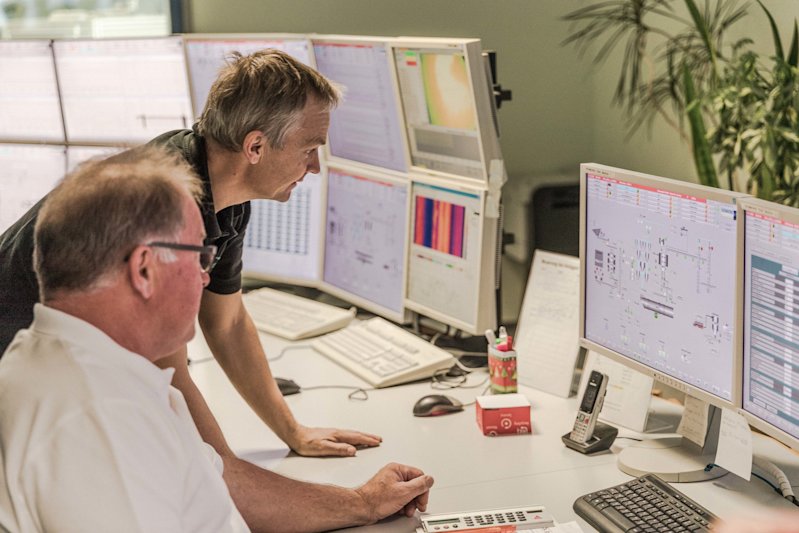
”Cement Waste Heat Recovery Power Generation System" for further energy saving measures in cement plants
Let us briefly explain cement production.
Cement is the most widespread of all building materials, and plays the most important role. There are three major processes in its production: “the raw material process,” “the calcination process,” and “the finishing and shipping process.”
In the "raw material process," limestone and clay are mixed in a specified ratio, dried, and ground. Ingredient adjustment (mixing) is the key to producing high-quality cement. The "calcination process" involves preheating the dried and ground raw materials and then calcining them in a furnace called a "rotary kiln.“ Through this process, the raw materials are transformed into “clinker,” a material with hydraulicity (hardens when mixed with water). The "finishing and shipping process" involves adding an appropriate amount of gypsum to the clinker and grinding it, which produces the so-called "cement.“
Cement production is "energy intensive," consuming large amounts of energy. According to the European Commission (2010), it takes between 3,000 and 6,500 megajoules (MJ) of energy to produce one tonne of clinker, depending on the size and performance of the kiln.2 Thereby, it is said that GHG emissions from the cement industry account for 2% of the total in Europe.
According to The Japan Cement Association, technologies such as adding a preheating device to a rotary kiln to increase the energy saving effect have already been established, and those technologies are mature enough that more energy savings cannot be expected from changes in the manufacturing method.3 A further energy saving effect is expected from the introduction of equipment that generates electricity using waste heat generated in the cement production process.
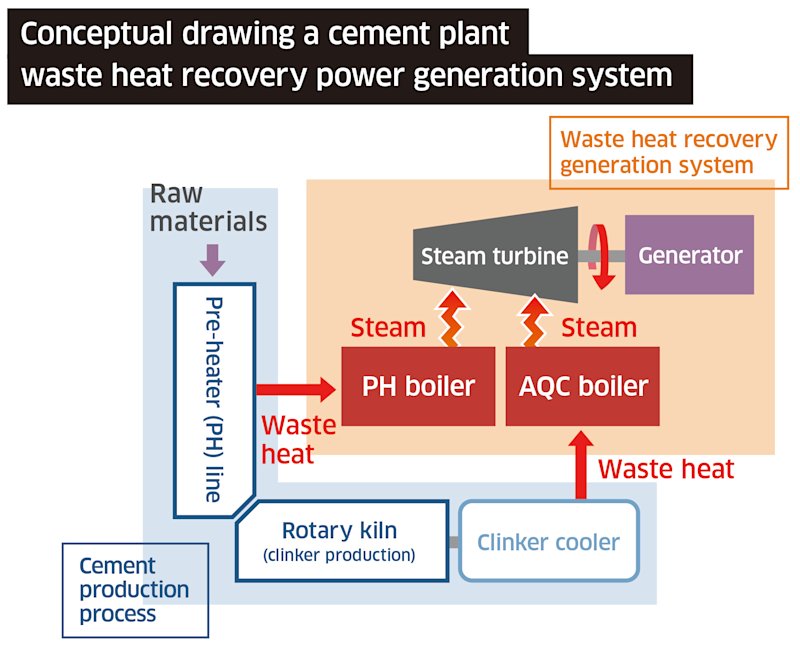
New technological innovations by maximizing the benefits of the SRC
The "Steam Rankine Cycle (SRC)" is adopted in Kawasaki’s cement WHRPG system, and mainly consists of a boiler, steam turbine, and generator.
There are two types of boilers: a pre heater (PH) boiler, which is installed in the raw material preheating line, and an air quenching cooler (AQC) boiler, which is installed in the clinker cooler to cool clinker produced by calcination. Kawasaki's WHRPG system can generate electricity by efficiently recovering waste heat that has not been effectively utilized in the cement production process. In other words, it can generate electricity without fuel.
In terms of "no fuel required," electricity thus generated is "CO2-free power" just like solar power, wind power, and other renewable energies. Unlike such renewable energies, Kawasaki’s WHRPG system is not affected by weather conditions and can provide a stable supply of electricity continuously 24 hours a day.
In addition, since 20-40% of the cement plant's electricity consumption can be covered, the cost of electricity purchased from outside sources, such as power companies, can be reduced. Furthermore, it can contribute to the reduction of CO2 emission by a cut in the usage of fossil fuels equivalent to the reduced electricity.
”The SRC also has the great advantage of operating safely and stably over the long term,"
”The SRC method uses water as a heat exchange medium,” says Yamamoto. ”This method is the most suitable for the temperature range of waste heat gas from cement plants and it can generate power more efficiently than other methods. There are other methods that use heat transfer media different from water, but these media are flammable or harmful to the human body, and thus there is a concern in case of leakage due to equipment deterioration. On the other hand, if the SRC is adopted, such problems can be safely and easily repaired with little impact on the other equipment.”
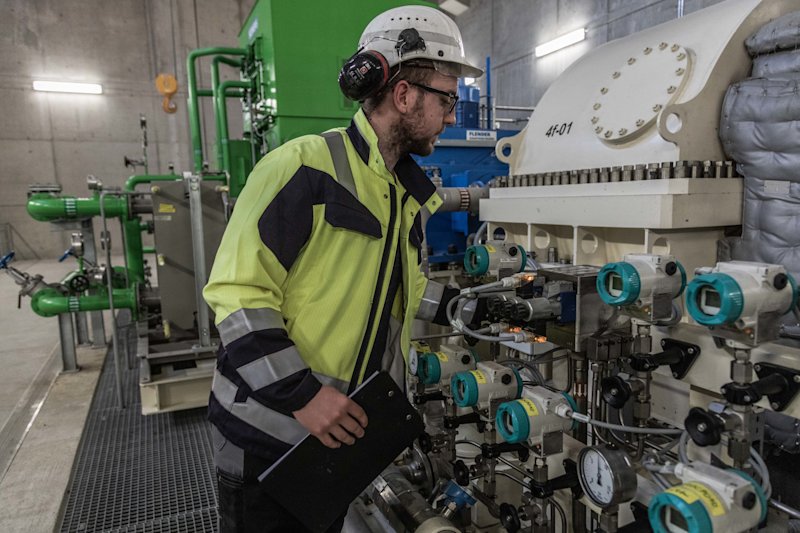
Kawasaki Heavy Industries' development of a cement plant WHRPG system was driven by the Japanese cement industry's aggressive efforts to contribute to saving the environment. Having achieved technological innovations such as energy saving kilns, Kawasaki was looking to the system as its next target.
Kawasaki delivered the world's first cement plant WHRPG system in 1980. The manufacturer also began demonstration tests of PH boilers and has accumulated design data on gas flow direction, heat transfer tube arrangement, dust removal devices, and so on.
”We have more than 40 years of experience in this field, and all of the systems we have delivered to date have continued to operate stably. In light of the current situation where large amounts of alternative fuels and materials such as wood chips, waste plastic, sludge, incineration ash from sewage sludge and municipal waste are used in cement production, we have developed the new PH boiler ‘VEGA®4‘, and we are continuously developing new technologies to meet the needs of the times.”
Cement manufacturers have placed their trust in Kawasaki. In Japan, a total of 21 cement plants have installed WHRPG systems, 14 of which were supplied by Kawasaki. Overseas, 237 plants in 14 countries, including South Korea, Turkey, and Rohrdorfer Cement in Germany, have installed Kawasaki systems (as of November 2022).
4 VEGA is a registered trademark of Kawasaki Heavy Industries, Ltd. and Anhui Conch Kawasaki Engineering Co., Ltd. in Japan, U.S.A., European Union, China and Korea.
In Europe and the U.S., the movement to adopt waste heat recovery power generation systems is taking place concurrently
The recent energy supply crisis is about to change the situation in Europe. Electricity prices, which used to be around 100 euros per megawatt (about 14,500 yen), have skyrocketed, with the one-year futures price for German electricity on the European Energy Exchange reaching a historic high of 1,000 euros per megawatt (about 140,000 yen) at the end of August 2022. The price has since been lowered to the 300-400 euro range, but still remains high.
Kazuki Ao of Kawasaki, who is responsible for developing the global market for cement plant WHRPG systems, says, "Until recently, electricity prices were so low that even environmentally conscious Europeans were not interested in the systems. From the perspective of waste-free energy utilization, however, more efforts are desired, and that is why we find Rohrdorfer Cement’s leading-energy-saving initiatives in Europe forward looking.
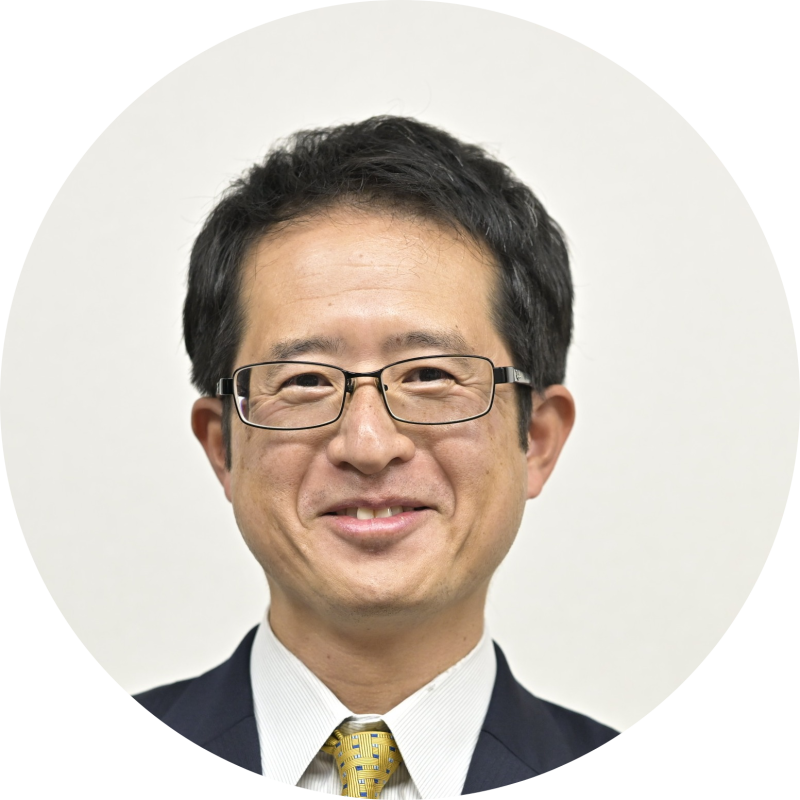
With approximately 250 cement plants, Europe is an advanced area of the cement industry and a promising market for cement plant WHRPG systems because there are 36 cement plants with more than 4,000t/d dry kilns, which is one of the indicators in terms of investment profitability.
“More cement plants are likely to consider installing WHRPG systems, focusing on the superior merits of the SRC. WHRPG system of the SRC is already an established technology with proven economic benefits. Kawasaki’s system does not require a large surface area and can be installed in the limited space of an existing cement plant, which allows it to be introduced immediately. Power generation with this system is not affected by sunlight or wind conditions. And it is an excellent energy saving system that effectively utilizes surplus heat to generate electricity without consuming additional fuel, as long as the cement plant continues to operate.
“Cementing the European Green deal” issued by the European Cement Association indicates the goal that, toward Climate Neutrality by 2050, it is desirable that CO2 emissions will be reduced by about 35% from 2017 levels.5 For this, WHR and improvements in kiln efficiency accounts for about 10%. And we have already received many inquiries from customers, including Europeans due to the recent increases in electricity costs. The same is true in the U.S., where WHRPG systems have not been widely used due to low electricity prices. We expect that the introduction of the systems will increase simultaneously around the world in the near future. We hope to meet our customers’ expectations and contribute to the realization of a decarbonized society using Kawasaki’s technological capabilities.”
5 Calculated by Kawasaki Heavy Industries based on:
The European Cement Association (2020, p.15), Cementing the European Green Deal-Reaching climate neutrality along the cement and concrete value chain by 2050. Brussels, Belgium. Available at:
https://cembureau.eu/media/kuxd32gi/cembureau-2050-roadmap_final-version_web.pdf
Cement plant WHRPG system is not only helping Europe to achieve both energy savings and environmental protection, but they have also come to play an important role in energy security.
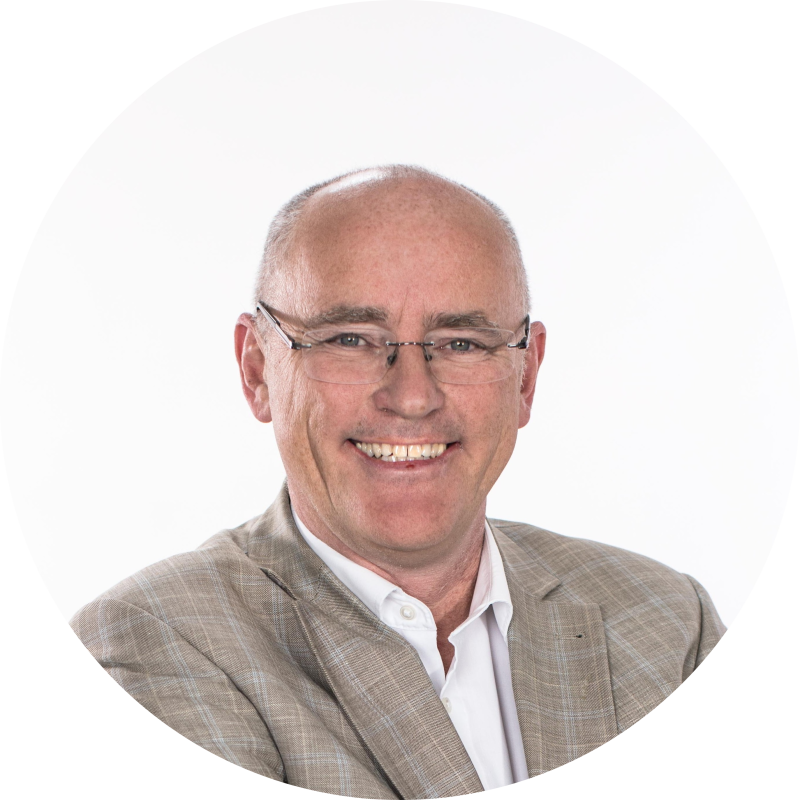
Ten years after installation, we have yet to require Kawasaki to repair our WHRPG system
Ten years ago, we introduced a cement waste heat recovery power generation system from Kawasaki Heavy Industries. The waste heat recovery power generation system itself was the first of its kind in Europe. In the 10 years since then, we have had only minor problems that our engineers have been able to solve in the workshops, and we have never had to call on Kawasaki for help.
The local residents have taken a keen interest in our system, and we have seen a noticeable increase in requests for tours from people in the industry. They seem to be particularly interested in the performance of the system, the steam temperature, and the conditions of the operation and maintenance, including costs.
Rohrdorfer Cement plans to use low-pressure steam from WHRPG system for our newly built pilot plant for CO2 recovery. The use of waste heat recovery power generation without the use of fossil fuels will be an essential technology for cement manufacturers to achieve Climate Neutrality by 2050.
Image: Courtesy of Rohrdorfer Group, Germany
※All photos related to Rohrdorfer Cement are copyrighted by Rohrdorfer Group, Germany.
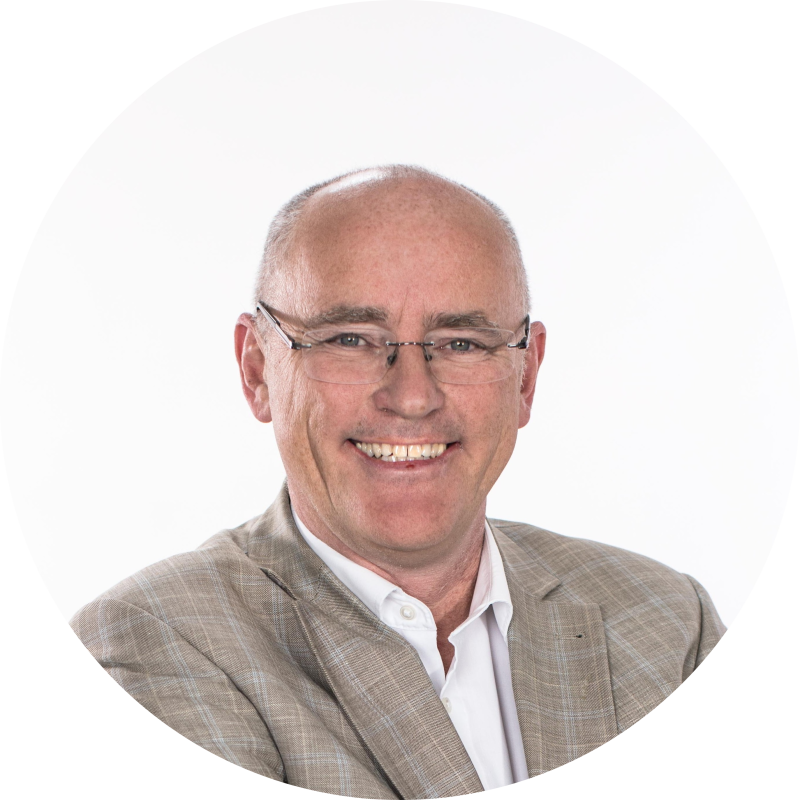
Rohrdorfer Cement Plant
Engineering Section 1
Boiler Plant Department
Power Plant Engineering Group
Energy Solution Business Division
Energy Solution & Marine Engineering Company
Kawasaki Heavy Industries, Ltd.
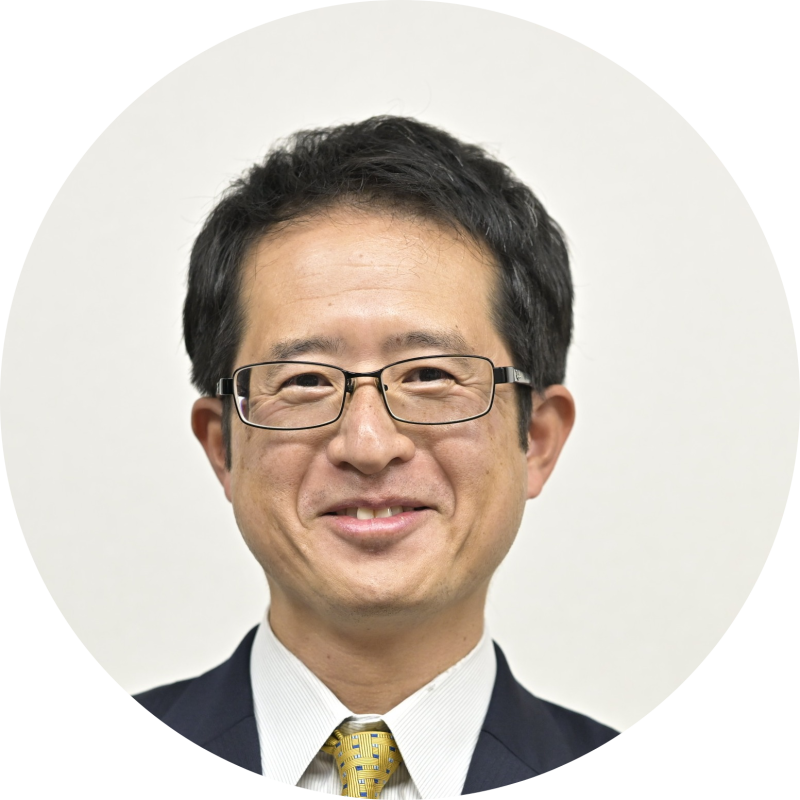
Power Plant Sales Department
Marketing & Sales Division
Energy Solution & Marine Engineer Company
Kawasaki Heavy Industries, Ltd.