New Approach to Saving Energy by Factory Hydraulic Equipment ―Evolution of ECO SERVO
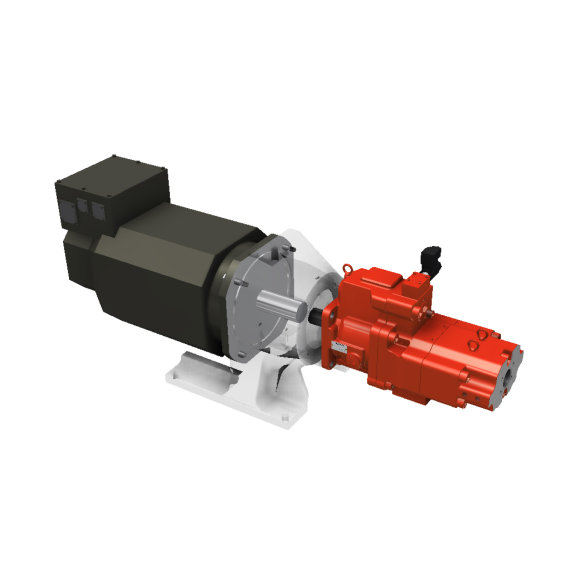
For hydraulic equipment and systems in plants, changes are taking place with regard to energy saving, including lowering power consumption and oil amount. This article explores the evolution of hydraulic equipment and systems by Kawasaki, which has developed the innovative product, ECO SERVO, to control the speed of hydraulic pumps as a leader in the industry.
Speed control of hydraulic pumps is the key to saving energy, reducing the size, and lowering noise
In 1999, more than 20 years ago, the first unit of the epoch-making hydraulic system from Kawasaki, ECO SERVO, was created.
In a conventional hydraulic system, the motor and hydraulic pump are constantly operating and consuming power even when the actuator is not running.
ECO SERVO, on the other hand, performs optimum speed control to limit runtimes to essential operations in response to actuator operation instructions, decreasing unnecessary energy consumption.
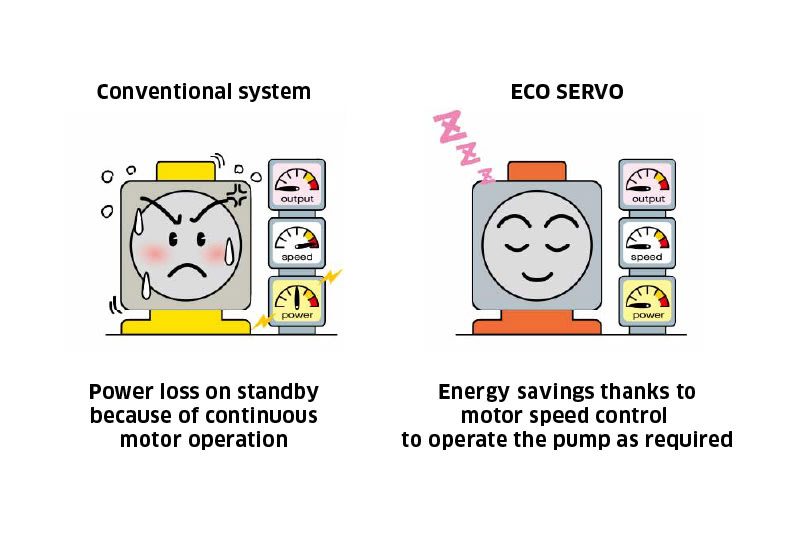
Kyosuke Ogawa from the Systems Engineering Department, Precision Machinery Business Division of Kawasaki describes the background to developing ECO SERVO:
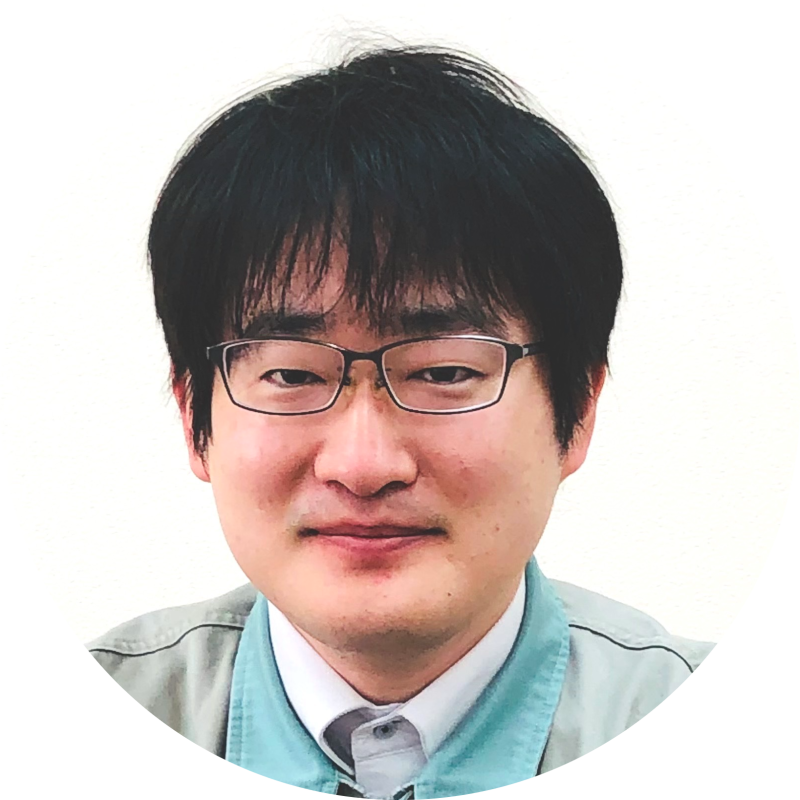
“Kawasaki provided the hydraulic equipment and systems for a variety of machines and devices, including construction, industrial, and marine machinery. The technique where the pump and the motor ran only when the actuator worked was realized by conception of the knowledge of energy savings and control technologies.”
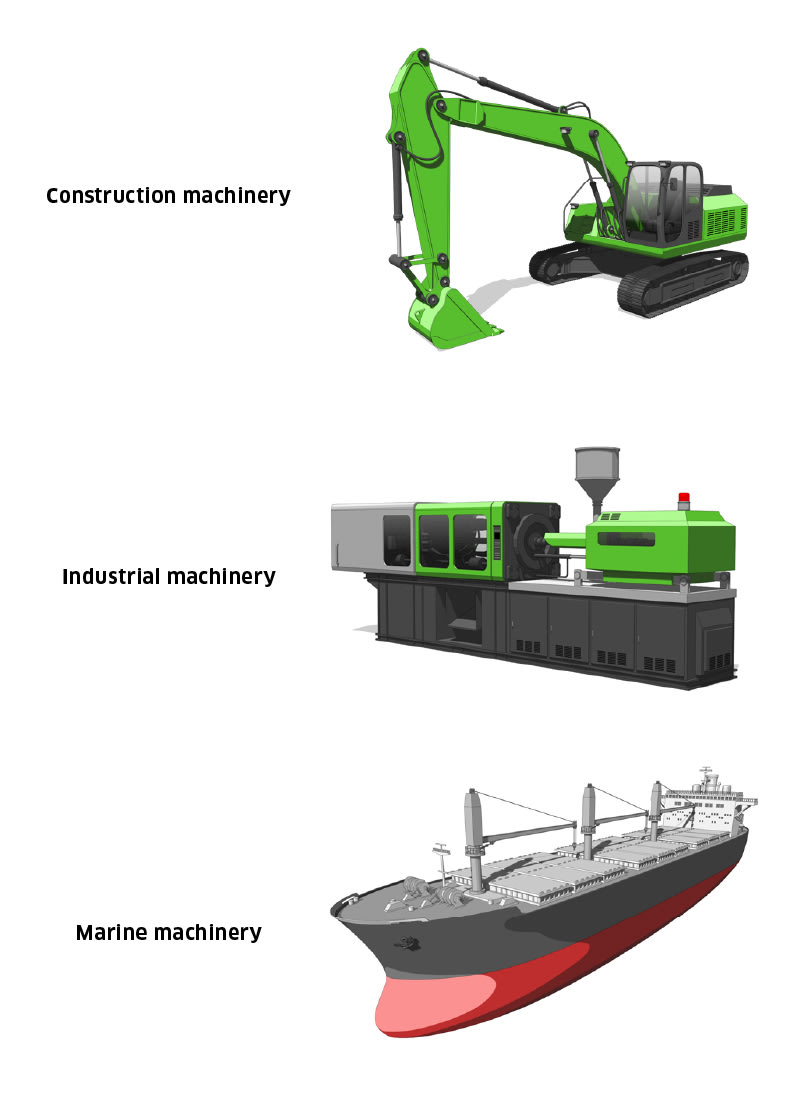
The innovative idea to control the hydraulic pump speed and the accompanying plan to simplify the hydraulic circuit resulted in the following advantages:
● Optimum control of the hydraulic pump and motor
→ Reduction in power consumption by up to about 80% and a significant decrease in operational noise
● Decline in heat generation due to power loss
→ Smaller volume of hydraulic oil and easier maintenance
● Simplified hydraulic circuit
→ Footprint reduced to one-third, and oil tank capacity to one-twentieth in the best case (estimations by Kawasaki)
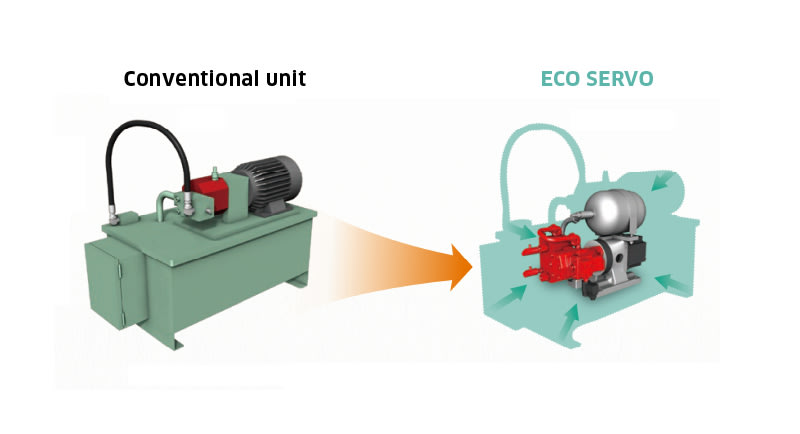
Noise and vibrations generated during the operation of hydraulic equipment in factories place a large burden on workers in the field. ECO SERVO consists of a hydraulic pump, motor, and control device to lower operational noise by governing the motor speed to the bare minimum.
The control device offers precise, energy efficient, highly responsive operation. Furthermore, the system uses a rigid structural part (bracket) and resilient support to alleviate vibrations transmitted from the hydraulic pump and thus reduce operational noise.
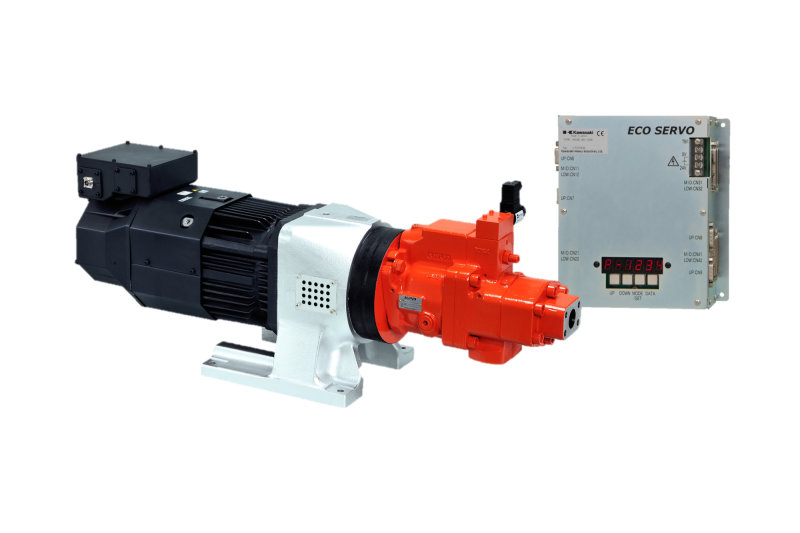
Lineup of a wide range of pump displacement specifications Diverse system configurations available
ECO SERVO has been a popular product since its release, being used in a variety of applications, such as in plants that provide pressing and injection molding. The model with a pump displacement of 500 cm3 appeared in 2018, and the broad product line is featured by coverage from small to large equipment. Another notable attribute is the applicability to hydraulic systems that require high pressure and high capacity thanks to the maximum operating pressure of 32 MPa and the maximum discharge per pump of 600 L/min (pump displacement: 500 cm3).
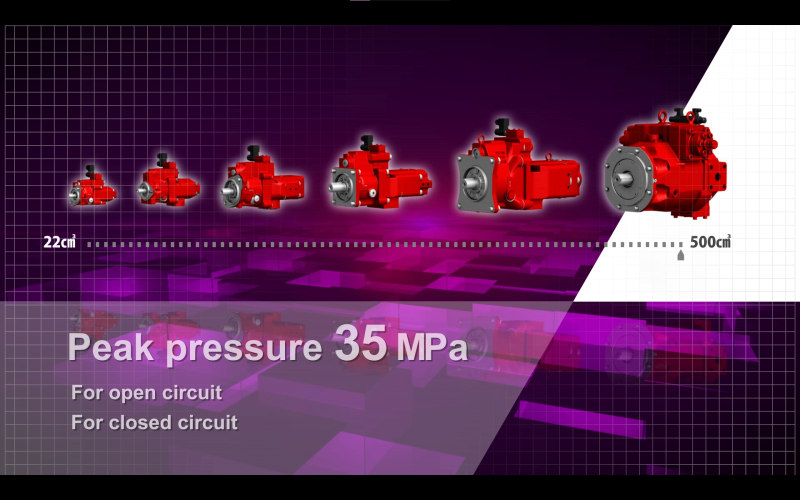
In addition, different systems can be configured by combining the options of an open circuit to control actuator speed and output power by motor speed, a closed circuit where the rotational direction and speed of the motor also determine the operational direction and position of the actuator, a servo motor drive that offers excellent control performance, and an inverter motor drive with good cost effectiveness. Thus, the best system to meet your field needs can be selected.
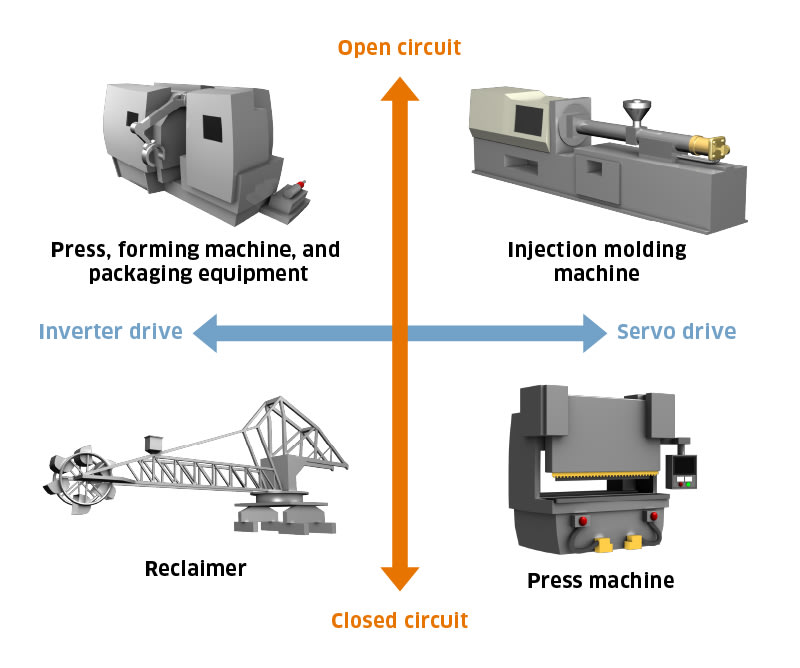
To further facilitate the introduction of an energy-saving hydraulic package unit—arrival of the ECO SERVO Light and ECO SERVO Avant
The energy saving hydraulic package units of ECO SERVO emerged in 2015. A sealed pressurized tank and oil cooler are integrated into a compact body, which facilitates the introduction of the energy-saving hydraulic unit.
Moreover, the sealed pressurized tank offers considerably improved maintainability. In the case of conventional oil tanks, the oil can contact the atmosphere via the air breather, which means dust can enter and contaminate the hydraulic oil, depending on the installation environment. The sealed pressurized tank shields the hydraulic oil from exposure to the atmosphere and keeps it clean. As a result, operational failures of the hydraulic equipment caused by foreign matter have been remarkably reduced.
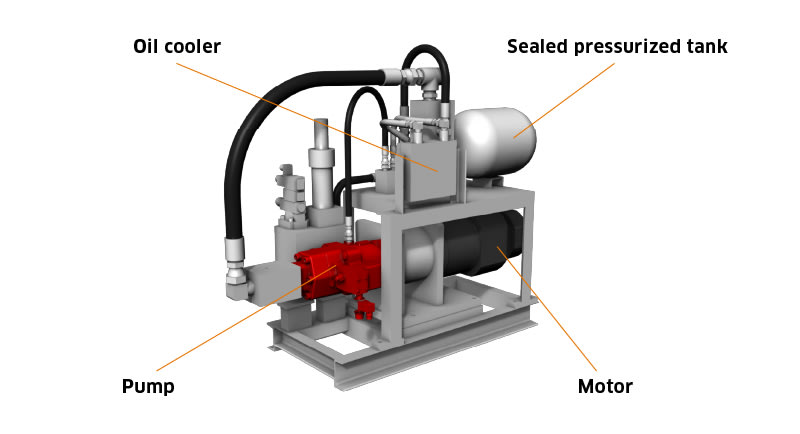
Subsequently, in August 2021, ECO SERVO Light and ECO SERVO Avant were launched. These model types are standardized by function to provide a selection that can meet different user needs.
Ogawa explains the background to this release:
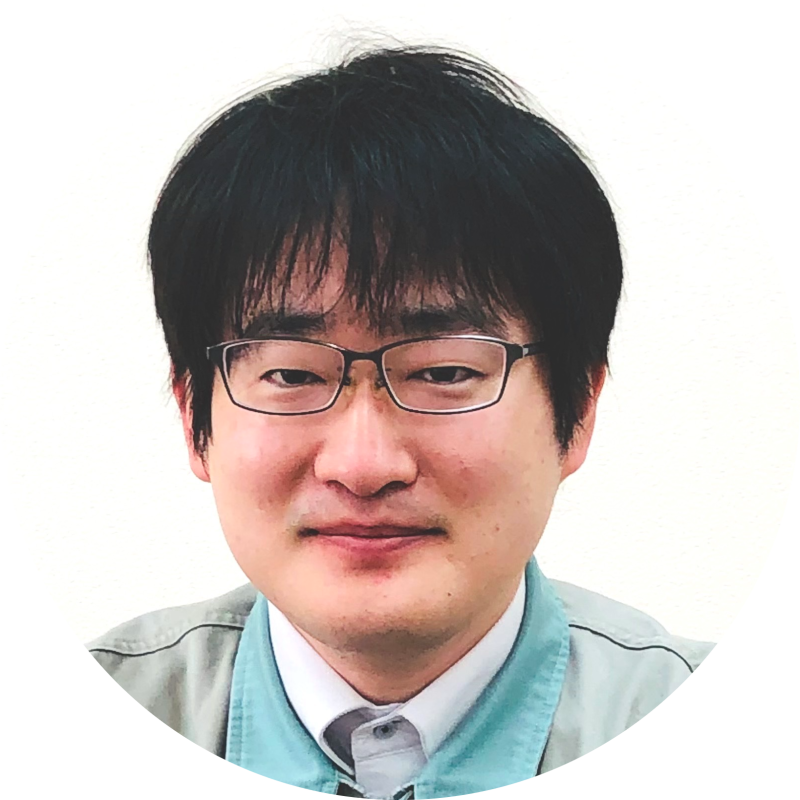
“The technical needs for energy savings and CO2 emission reduction are expected to grow more and more. In order for customers to facilitate implementation of energy savings, depending on the necessary equipment functions, we decided to add standardized, function-specific, energy saving hydraulic package units to the product line.”
ECO SERVO Light is an energy saving unit specifically designed for flow and pressure control, and an open-circuit-type pump and inverter drive are adopted for improved operation. Because this is the basic tool to lower power consumption, this product helps to conveniently save energy.
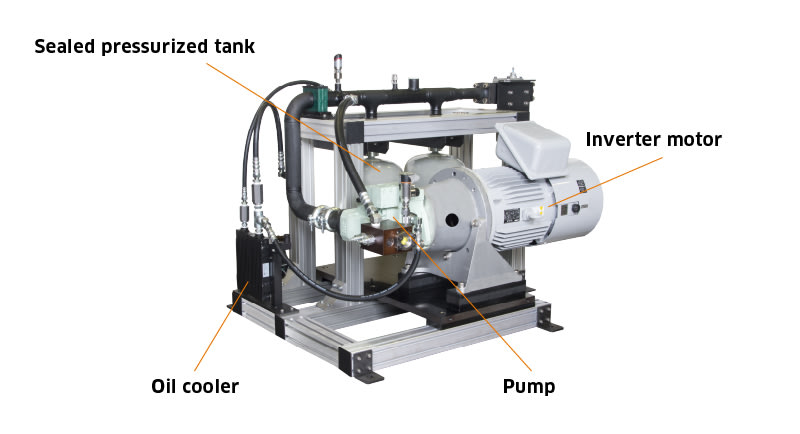
On the other hand, ECO SERVO Avant models are high performance energy-saving units capable of positioning control and high-cycle operation, in addition to the features of the Light models. A closed-circuit-type pump is employed, and the orientation of actuator operation is directly controlled by switching the motor rotation between clockwise and counterclockwise, which further reduces power loss and offers higher efficiency with smaller dimensions. The use of a servo drive enables precise control with high responsivity.
The availability of open- and closed-circuit-type pumps, according to the target equipment, is achieved by the abundant technologies and expertise in hydraulic pumps that Kawasaki has accumulated over many years.
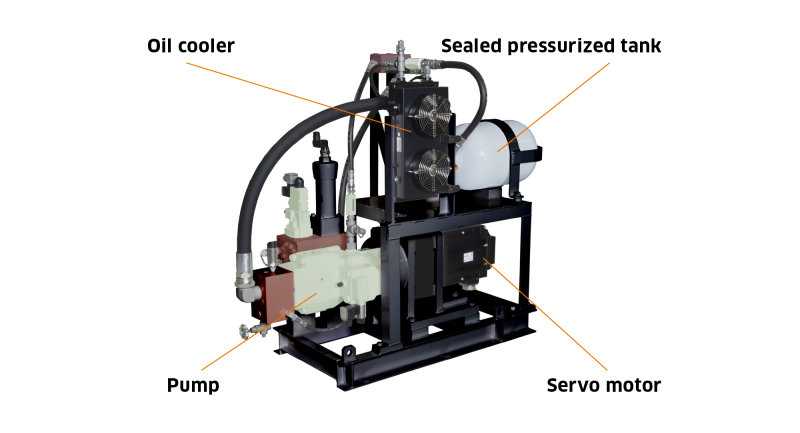
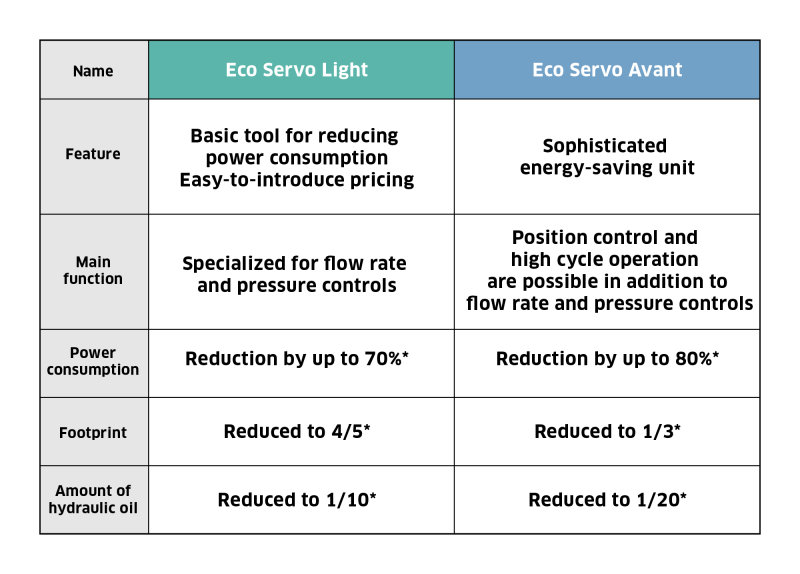
While actions for carbon neutrality are in progress, energy-saving measures for factory equipment are also required. Adopting energy-saving hydraulic equipment and systems will realize the many advantages that include reductions in electricity expenses, oil volumes, noise, and size. From a flexible point of view, Kawasaki continues to accelerate innovation in technology and services while resolving social issues and responding to customer needs.
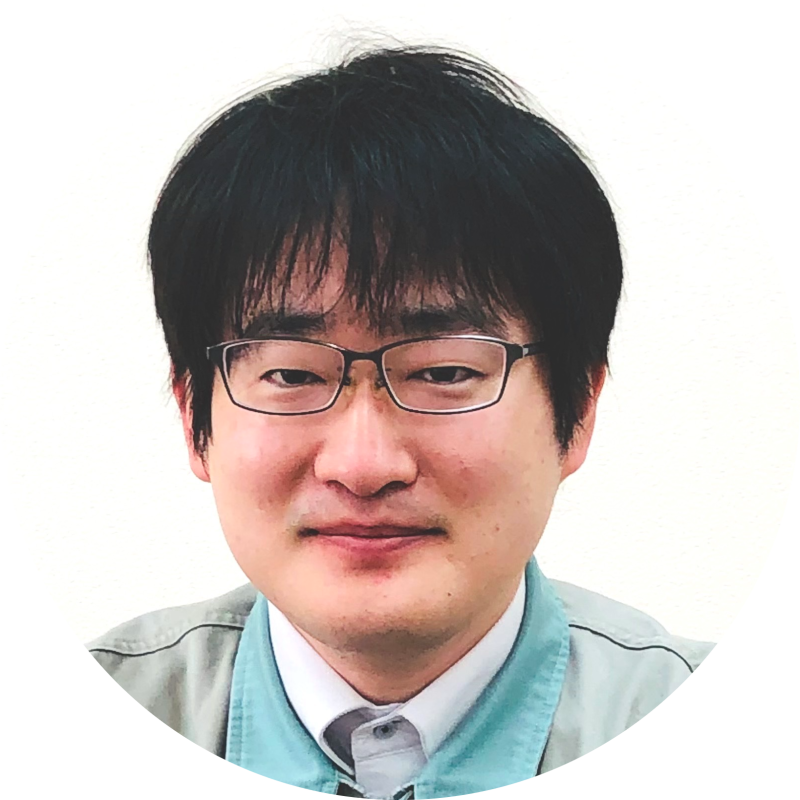
Industrial Machinery Section, Systems Engineering Department
Engineering Group, Precision Machinery Business Division
Precision Machinery & Robot Company
Kawasaki Heavy Industries, Ltd.