Toward a decarbonized society from factories—the power of evolving energy-saving hydraulic equipment
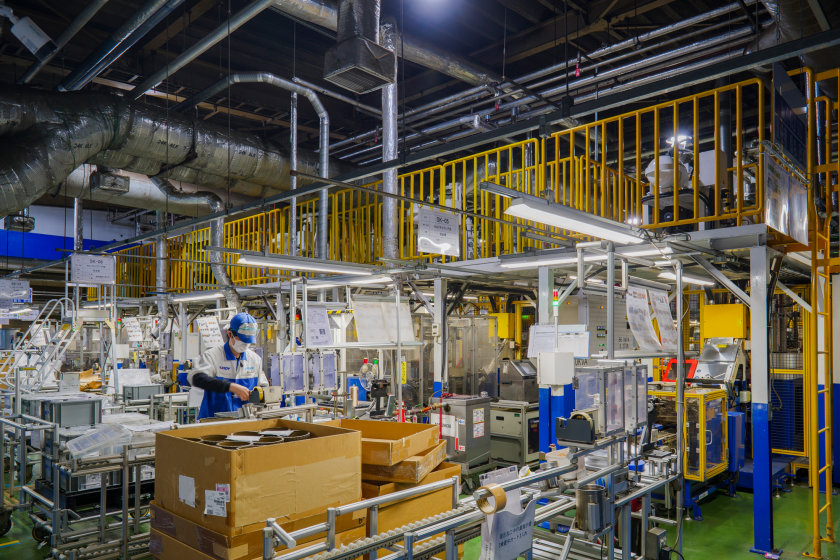
Manufacturing sites are now required to save energy, but, in some cases, the obstacles are equipment installation costs and labor. A review of the hydraulic equipment used in factories will lead to effective energy-saving measures. Kawasaki, which supplies hydraulic equipment and systems throughout the world, proposes new solutions for the realization of a decarbonized society.
Energy saving is an important social issue for factories. Focusing attention on the control of production equipment and stopping when unnecessary
As the momentum for carbon neutrality increases worldwide, the 2050 Carbon Neutral Declaration announced by the Japanese government in 2020 targets the realization of a decarbonized society by 2050 and a reduction in greenhouse gas emissions to virtually zero. Industry sectors of manufacturing, construction, mining, agriculture, forestry, and fisheries emit the second largest amounts of CO2 emission by power plants. Among those industry sectors, the industrial machinery used in the social infrastructure and factories has a long life cycle and consumes more energy during use than during manufacture; therefore, energy-saving measures are an important social issue.*1
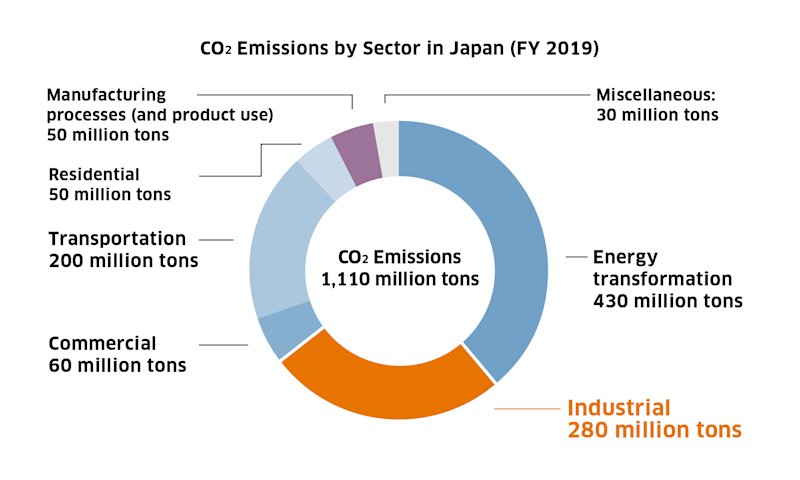
With regard to environmental measures in the factories of the manufacturing industry, the first step toward saving energy tends to be the low technical hurdles presented by lighting and air conditioning. In order to further promote energy savings, improving production and other facilities is effective as shown in the figure below. Power consumption can be significantly reduced (energy saving) through rotation speed control and stopping or shortening unnecessary operating times. Currently, most electrical power is supplied by fossil fuels, so reducing power consumption leads to reduction in CO2 emissions that contribute to the realization of carbon neutrality in the industry sector.
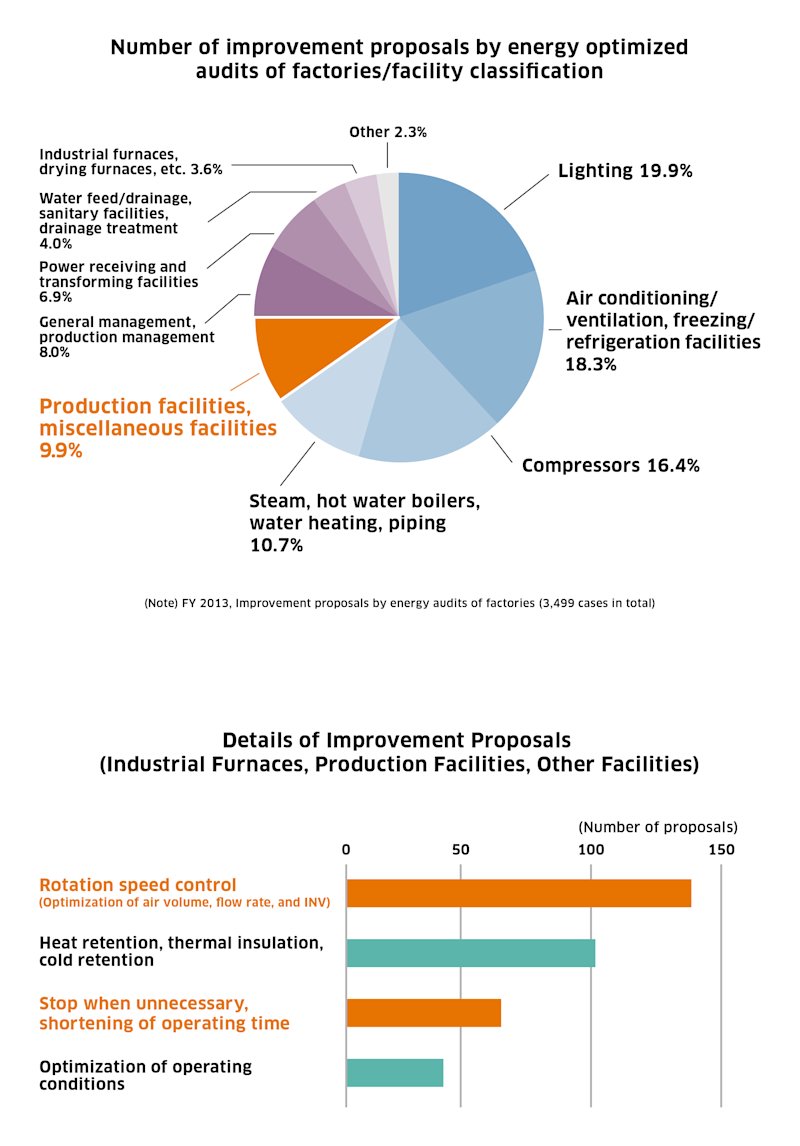
Source: Prepared by Kawasaki Heavy Industries from p. 13 of the Energy Conservation Guidebook for Factories by the Energy Cons ervation Center, Japan
Then, what should we do when actually implementing rotation speed control and stopping or shortening unnecessary operating times for hydraulic equipment?
Kawasaki’s ECO SERVO is one of the options that can be expected to have a great effect.
*1:Refer to FY 2020 Annual Report on Energy (Energy White Paper 2021) by the Agency of Natural Resources and Energy, Ministry of Economy, Trade and Industry
Kawasaki’s ECO SERVO controls the rotation speed of a motor to save energy. Package units and subscriptions meet the needs
Kawasaki’s ECO SERVO, released in 1999, is an epoch-making system born from the unprecedented idea of controlling the rotation speeds of hydraulic pumps and motors according to actuator operation to reduce wasteful energy. ECO SERVO offers the following advantages.
- Reduction of power consumption by up to 80%
- Significant reduction in noise during operation
- Reduction in the amount of hydraulic oil by downsizing the oil tank (to 1/20)*2
- Space saving due to the above (up to 1/3 of the installation area)*2
- Facilitation of maintenance
*2:According to estimations by Kawasaki Heavy Industries
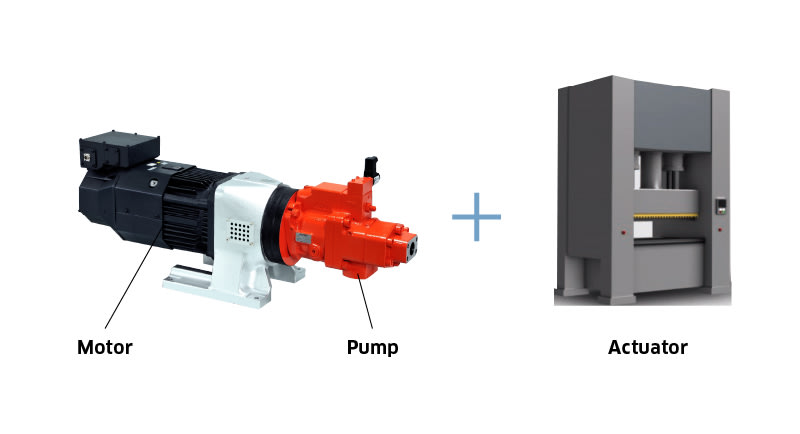
An energy-saving hydraulic package unit is an option to more readily introduce ECO SERVO. The compact integration of a sealed pressurized tank and an oil cooler prevent the entry of foreign matter and allow the stable suction of hydraulic oil.
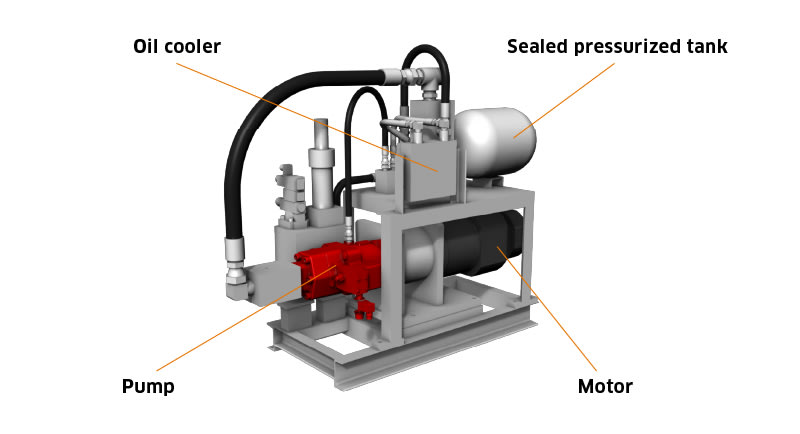
Furthermore, in August 2021, Kawasaki released ECO SERVO Light and ECO SERVO Avant standardized by function according to customer needs.
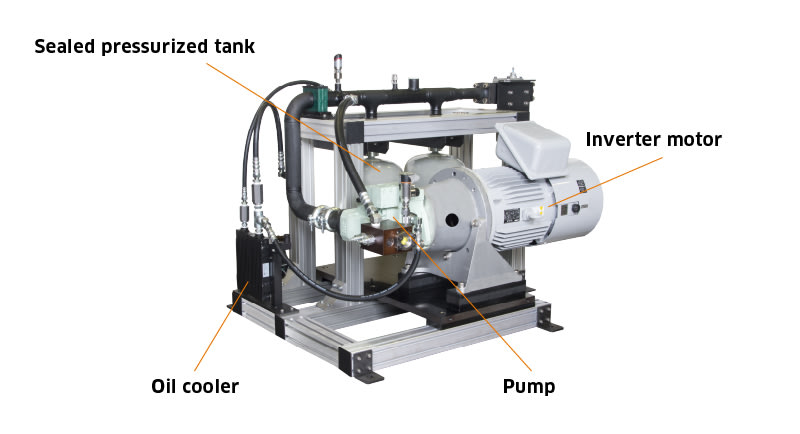
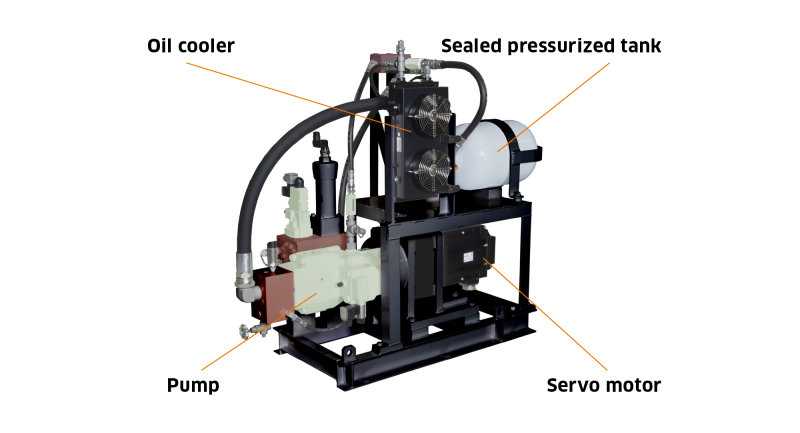
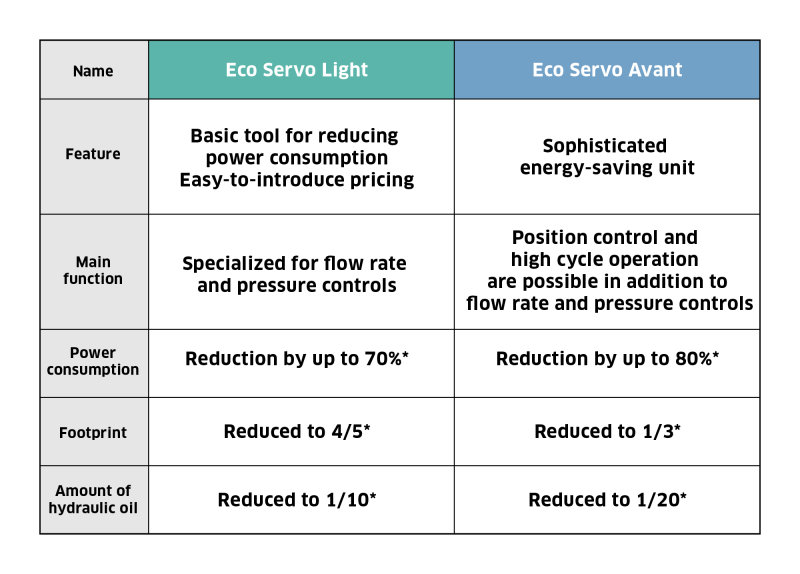
Dynax boasts the top market share in automotive clutch discs. Promoting energy saving by introducing ECO SERVO.
What changes will be generated by introducing ECO SERVO?
Surrounded by the magnificent nature of Hokkaido, Dynax Corporation is headquartered in a highly convenient location about 20 minutes by car from the New Chitose Airport. The company introduced ECO SERVO in 2015 and has realized energy savings since that time.
Dynax was founded in 1973 and has grown into a company known both at home and abroad as a specialized manufacturer of drivetrains for automobiles, construction machinery, and agricultural vehicles. In particular, the company built unique technologies for clutch discs and now boasts the number one market share in Japan and is number two in the world (46%). By continuing to meet the diverse needs of world-renowned automobile manufactures and industrial machinery manufacturers, the company is expanding its manufacturing and sales network to China, the United States, Mexico, and Hungary, in addition to Chitose City and Tomakomai City in Japan.
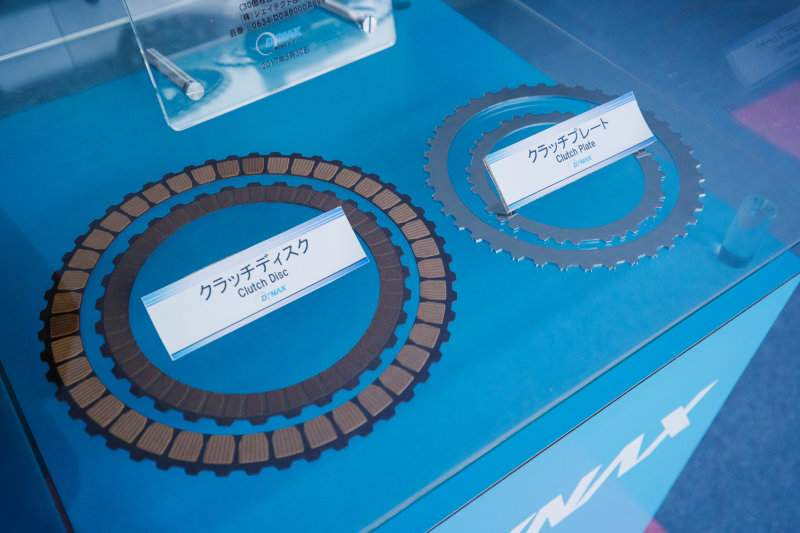
With the desire to contribute to local society, Dynax was one of the first to tackle environmental problems, such as removing asbestos from the friction materials that have been indispensable for the clutch discs of automatic transmission vehicles since the 1980s.
Mr. Kiyoto Goto, General Manager, Equipment Maintenance Department, Manufacturing Headquarters, Dynax, talks about the reason for introducing ECO SERVO as follows: “Conventional hydraulic equipment used a large amount of oil, and there was a lot of waste when changing oil, so we wanted to prevent the inside of the factory from getting dirty from the oil. While reviewing the hydraulic equipment to reduce the amount of oil, we decided to introduce ECO SERVO because it uses far less oil than other products and has the additional effect of reducing electricity costs. It is used in the press process to finish product plate thickness after bonding the friction material to the clutch disc and, at the same time, to finish the flat surface smoothly, which is our core technology. Plate thickness quality is an important process that affects clutch performance. Since we installed many press machines, a high energy-saving effect was obtained by deploying the same equipment to all of them.”
Clutch disc-bonding process
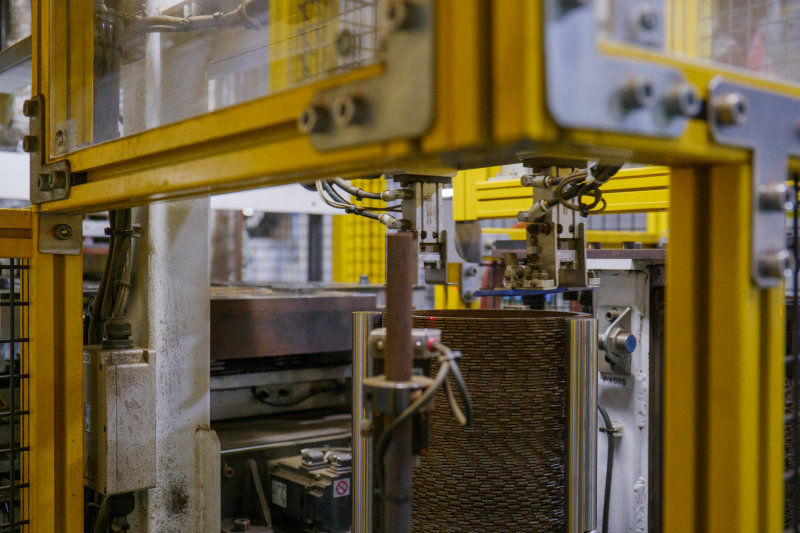
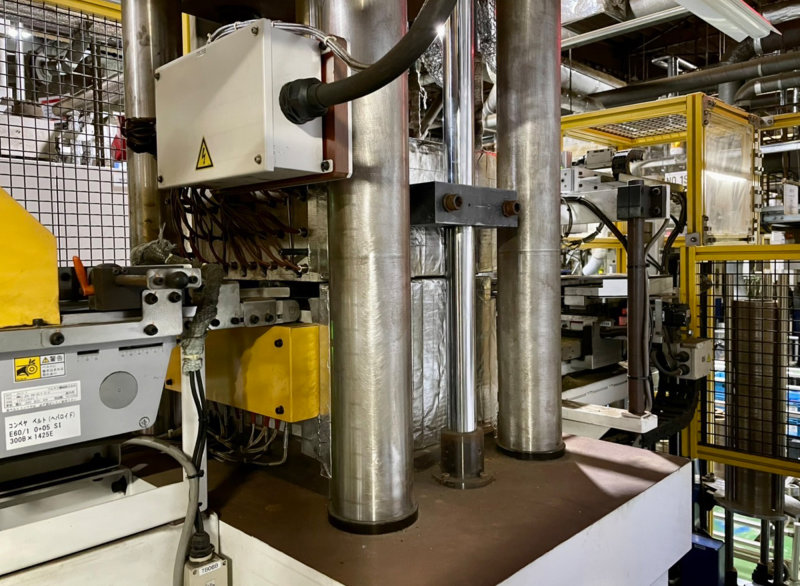
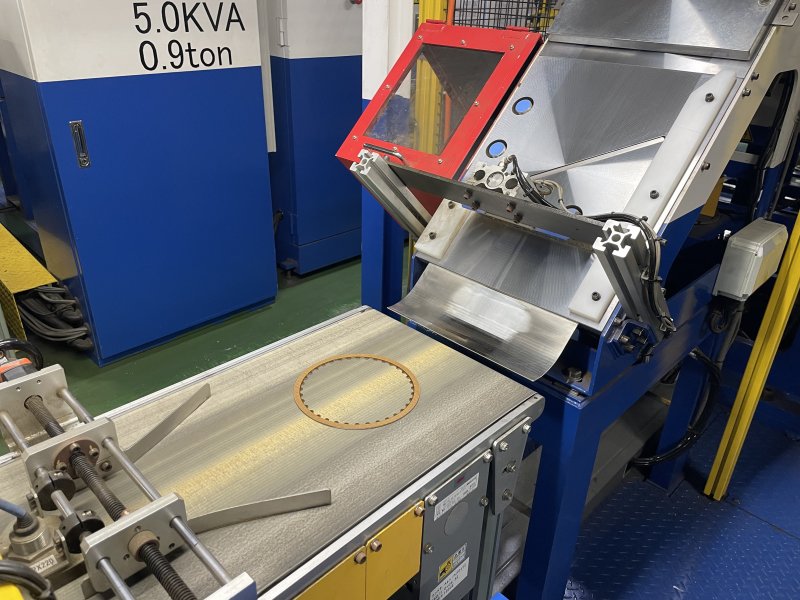
Currently, Dynax introduced seven ECO SERVOs into the Chitose factory, fifteen at the Tomakomai factory, fifteen at the factory in the United States, nine at the factory in Hungary, and two at the factory in China.
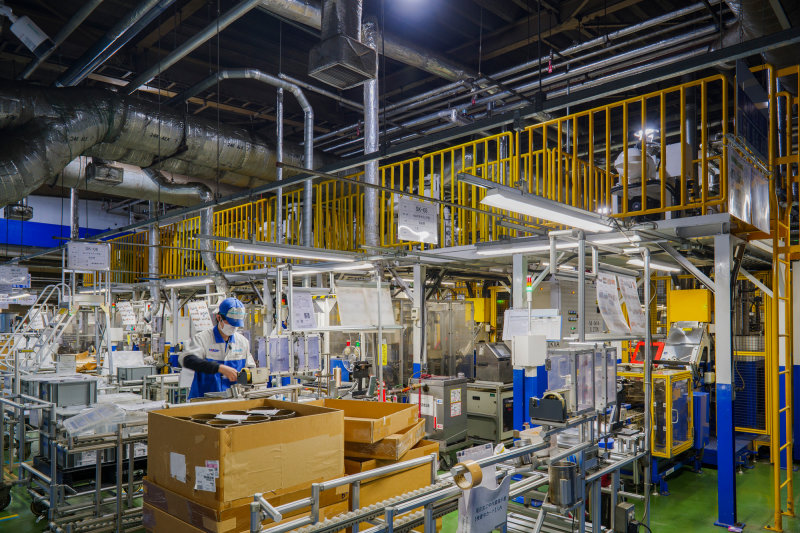
Mr. Goto talks about the concrete energy-saving effect of ECO SERVO as follows: “The effect of reducing power consumption was extremely high, and the power consumption by the equipment alone was reduced by 86% compared to conventional hydraulic equipment. The wonderful performance leads to reductions in CO2 emissions. In general, energy-saving equipment has a high hurdle for introduction due to the high initial cost, but reductions in the costs of electricity can be a great advantage in the long term.
In addition, the Chitose factory used a large amount of oil and replaced it every year, but it is now possible to reduce the amount by about 2,000 L per year with the introduction of ECO SERVO.”
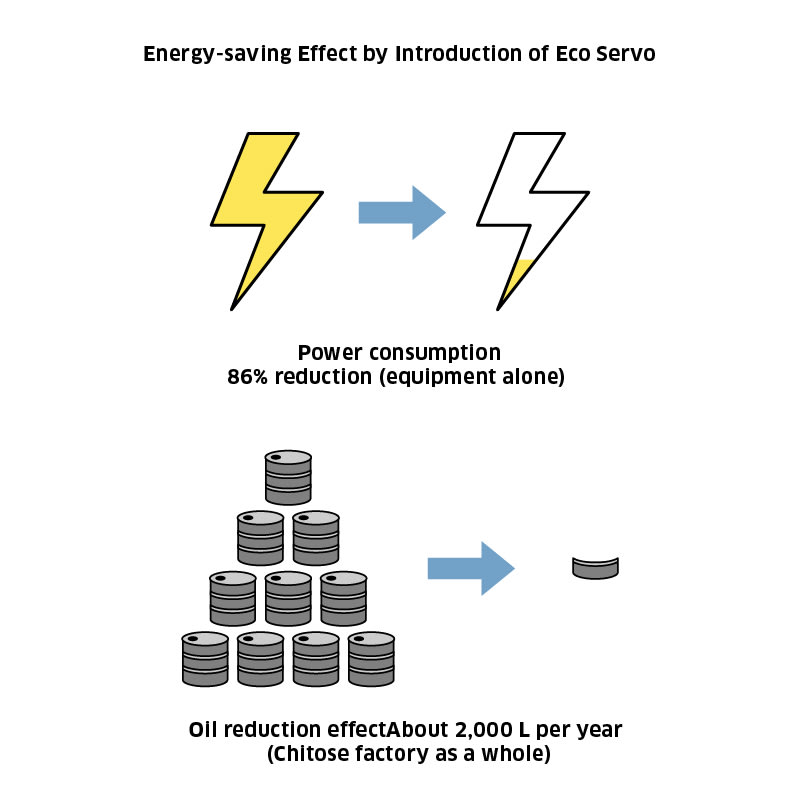
ECO SERVO offers many attractive features, including improved maintainability and low noise
Mr. Yoshihiro Abe, Team Leader, Chitose Equipment Maintenance Team, Equipment Maintenance Department, Manufacturing Headquarters, Dynax, explains as follows: “For conventional hydraulic equipment, the motor was always operating at maximum load, so the problem was that the oil tended to deteriorate because of temperature changes and other reasons. Since ECO SERVO operates only when necessary by controlling rotation speed, the amount of oil circulating is small, and the amount of oil to be put into the tank can also be kept to the minimum in the first place. In addition, the oil deteriorates from contact with oxygen and contamination with dust, but the sealed pressurized tank of the ECO SERVO package unit prevents that deterioration and contamination. ECO SERVO does not stain the equipment with oil, is hard to break, and requires almost no maintenance once adjusted, which is especially helpful for overseas factories where frequent visit is difficult.”
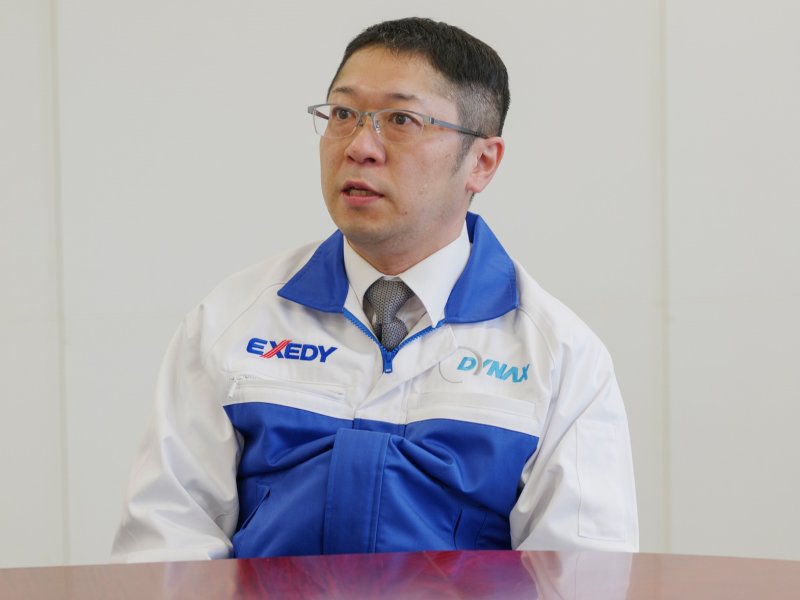
According to Mr. Goto, “The ECO SERVO hydraulic equipment is friendly not only to the global environment and cost but also to workers. As you can see from actual experience, the operating noise is quieter than conventional hydraulic equipment, so that you may doubt that is it really operating.
Low noise, low heat generation, and improved working environment are important for employees as well.”
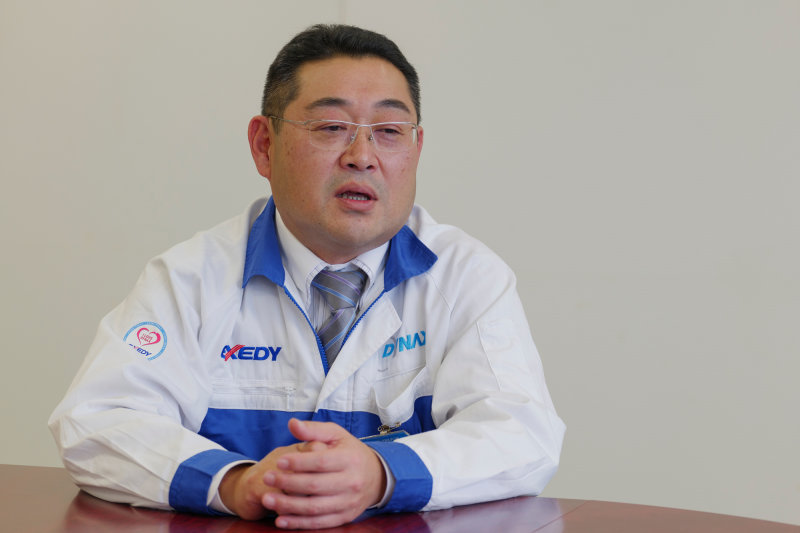
Currently, Dynax has set up a carbon neutral committee and is promoting a variety of different efforts. In addition to the development of electrification technology, which is accelerating throughout the automobile industry, Dynax is making progress toward the realization of a decarbonized society by promoting the introduction of cogeneration systems that use the waste heat of exhaust gas when generating electricity with gas and the introduction of biomass power generation into its factories.
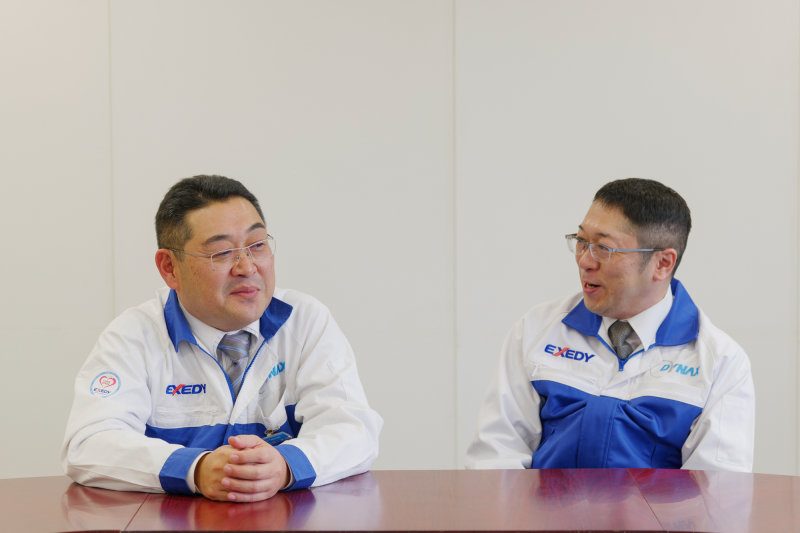
Kawasaki has a wide variety of expertise and a record of achievements in hydraulic equipment and systems in many fields, and it will provide customers with the value of energy savings from its hydraulic equipment, further noise reduction, and improved maintainability. The company will continue to contribute to the realization of a decarbonized society and the sustainable development of industries while responding to a wide range of needs.
Hydraulic equipment is active in all fields from familiar elevators to construction, engineering, agriculture, and ships
Hydraulic pressure is a mechanism that uses Pascal’s principle to generate oil pressure and transmit power to a remote location. Pascal’s principle is that the pressure applied to a part of a stationary liquid in a closed container is transmitted to all parts of the liquid equally. As shown in the figure below, two pistons with different cross-sectional areas are connected by a pipe and confine oil. When the small piston is pushed with a constant force, pressure is generated on the confined liquid and a force proportional to the cross-sectional area of the large piston is obtained. Therefore, a large force can be obtained with a small force.

Machinery and equipment use hydraulic equipment to perform work by rotating a hydraulic pump with an electric motor or engine to move an actuator (hydraulic motor, hydraulic cylinder, etc.) with the hydraulic oil discharged by the hydraulic pump. There are many situations where hydraulic equipment is used. For example, the equipment is used as a drive source for the following items.
- Elevators, multilevel parking towers
- Construction machinery (hydraulic excavators etc.)
- Industrial vehicles (forklifts etc.)
- Agricultural machinery (tractors etc.)
- General industrial machinery (steelmaking machines, press machines, injection molding machines, etc.)
- Power generation facilities and marine machinery (steering gears and deck machinery)
Kawasaki is a hydraulic equipment manufacturer that provides hydraulic equipment and systems for machinery and equipment. In particular, the company is proud of its world-class achievements in the manufacturing of hydraulic pumps and hydraulic motors for hydraulic excavators and has won overwhelming support from customers.
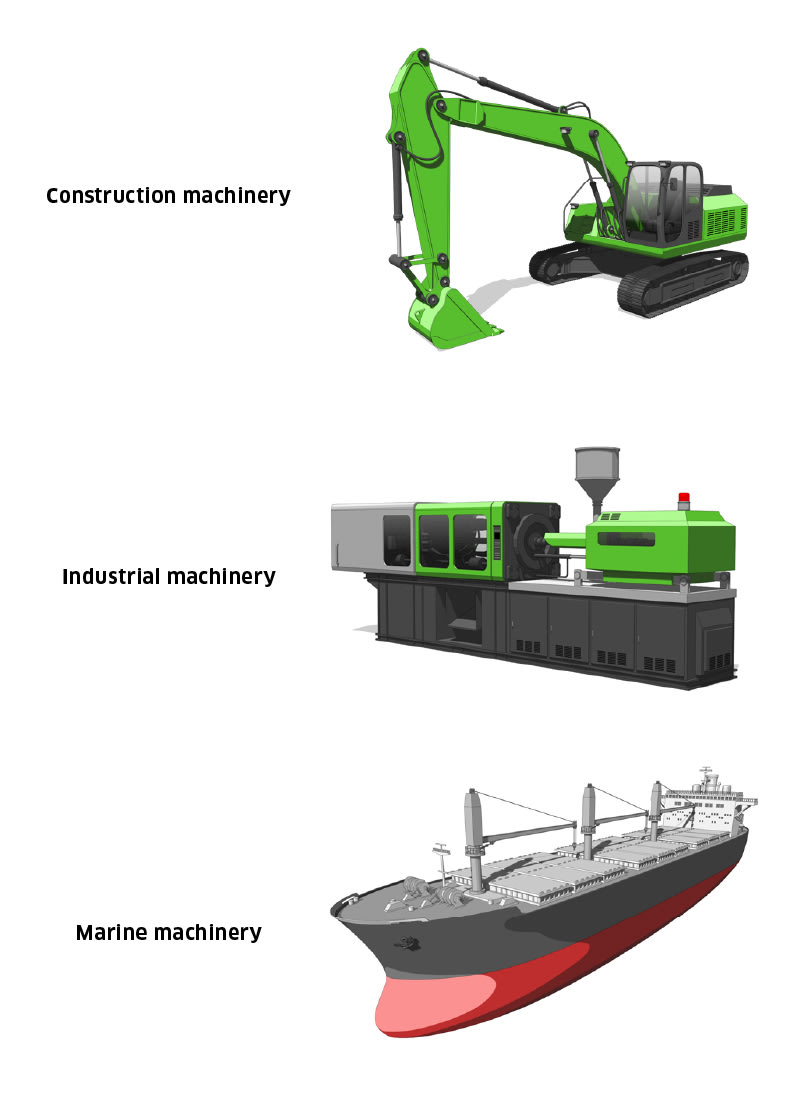
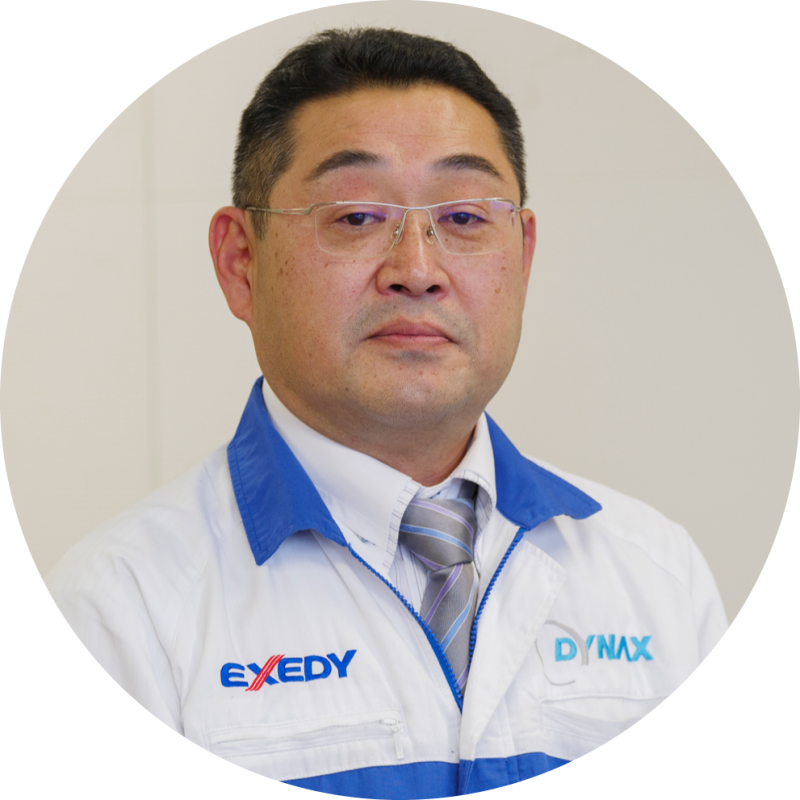
Equipment Maintenance Department
Manufacturing Headquarters
Dynax Corporation
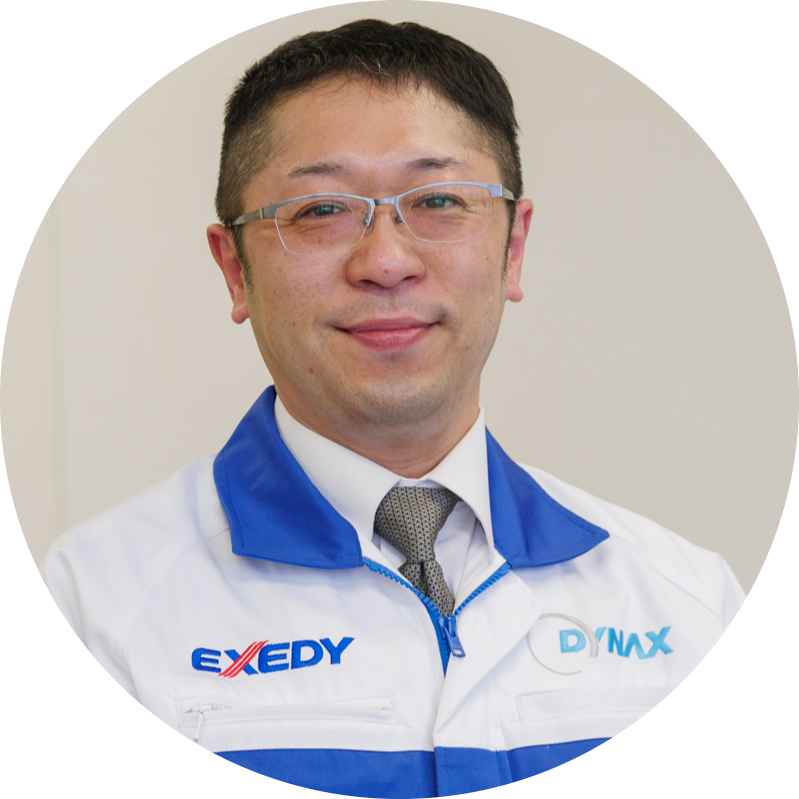
Chitose Equipment Maintenance Department
Equipment Maintenance Department
Manufacturing Headquarters
Dynax Corporation