Challenges to Sustainable Sewage Plants - Discover the Technological Innovation of Kawasaki
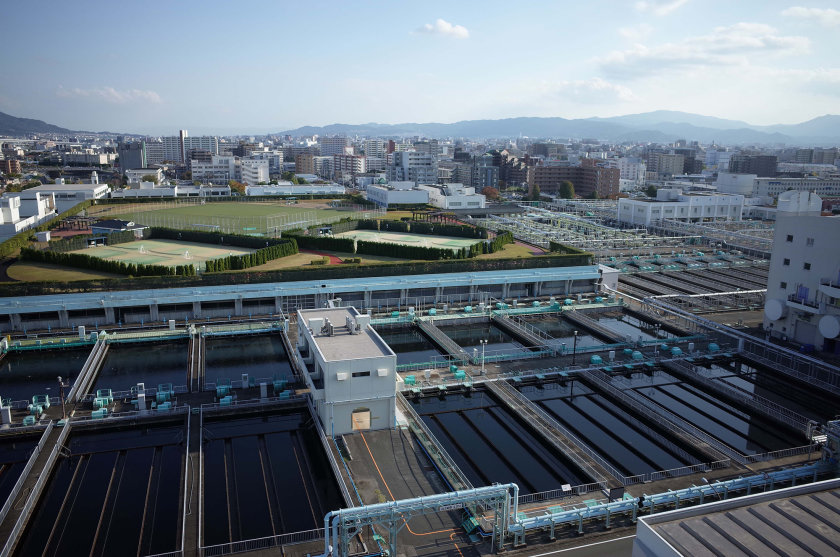
Water resources are essential for people and life. The Sustainable Development Goals (SDGs) of the United Nations also state that the water and energy goals and the actions for energy saving and sustainable water infrastructures have started. One of the keys is wastewater treatment. Kawasaki aims to improve the energy efficiency of sewage facilities throughout the world. The Company pioneers the sustainable future with its original technology, including the MAG Turbo M55.
Great Contribution to Reducing Power Consumption in Wastewater Treatment. Kawasaki Aeration Blower, MAG Turbo
Sewage plants consume as much as about 0.7% of the total electricity in Japan (according to the statistics of FY 2018).
The principal method of sewage treatment in Japan is the conventional activated sludge process, which was first adopted in the United Kingdom in 1914. In this process, sludge containing microorganisms is mixed with wastewater. As the microorganisms digest the organic matter in the wastewater and increase in number, clean water is the result. At a sewage plant, the microorganisms in the biological reaction tanks are activated by air. The aeration blowers play an important role in supplying air to the tanks. However, the blowers account for sixty percent of the electricity used for sewage treatment.
Water Treatment Flowchart
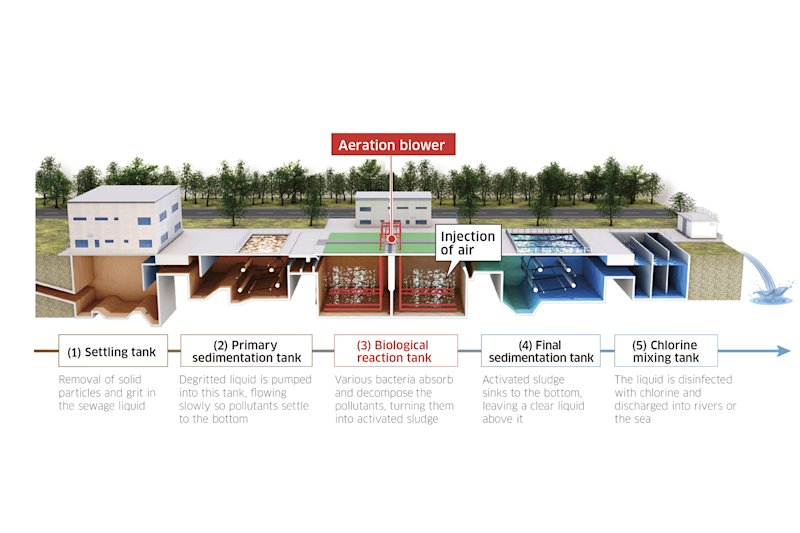
Accompanied by the technological development of the conventional activated sludge process, the blowers’ features also evolved. The advancements included adjustment of the air volume to activate microorganisms based on the volume of sewage and long-term stable operation. However, the problem of large power consumption remained. The solution to this issue was the technical innovation that resulted in the Kawasaki MAG Turbo, the high speed motor driven single stage turbo blower with magnetic bearings.
Inverter control, which regulates rotational speed by altering the frequency and voltage of the power supply to drive the motor, is applied to the MAG Turbo. The unit has an impeller attached to the shaft end of a high-speed motor in which the rotor is levitated by magnetic force and rotates at high speed to produce the compressed air. Since the floating rotor does not make any mechanical contact, the bearings, lubricant, and other auxiliary equipment to protect high-speed rotation are no longer needed.
Minimizing mechanical losses reduced power consumption by 15% to 30%. Since delivery of the first unit in 2004, Kawasaki has received orders for more than 200 units in Japan and achieved approximately a 50% share of the total domestic aeration blower market during the five years until FY 2020. MAG Turbo blowers serve to reduce CO2 for customers by 50,000 tons a year as a rough estimate.
Shedding Light on the Issue of Aging of Facilities, Reducing Power Consumption and Construction Costs
Kawasaki developed the MAG Turbo model M55 (M55), a high speed MW(Mega Wat) motor driven single stage turbo blower with active magnetic bearings, which has the world’s highest output for large-scale sewage plants.
Now, the aging of facilities is an increasingly serious problem both in Japan and overseas. A common global issue is the use of highly efficient equipment to reduce renewal costs and operational expenses. The M55 was developed as one solution to that challenge.
The name MAG Turbo was created from “MAGnetic bearing” and “Turbo Blower”. Whereas the maximum motor output of the largest model of the original MAG Turbo is only 400 kW, the maximum output of the M55 is 1,300 kW, which exceeds 1 megawatt. Accordingly, the discharge air volume and the discharge pressure are also enhanced from 300 to 900 m3 per minute and from 80 to 100 kPa, respectively.
The high-speed motor and the rotor that turn the impeller are heavy; the rotor alone weighs 700 kg, or more than five times the largest MAG Turbo model, and it is levitated by 10 electromagnets installed on three bearings with a shaft vibration displacement of a mere 20 µm.
Soichiro Takemura, assistant manager at the Energy System & Plant Engineering Company, says, “In order to stably levitate such a heavy shaft rotating 11,500 times per minute within a tolerance of 20 µm, we had to improve the electromagnets’ magnetic attraction performance and develop new technologies for the controller and control systems for the magnetic bearings.”
The magnetic bearings maintain the rotor in its reference position as follows: the position sensors installed in several places determine the rotor’s position relative to the X-, Y-, and Z-axes at all times, and the electric current values to the magnetic bearings are controlled. This method is called feedback control, where positional data is received 10,000 times per second. Kawasaki developed the techniques for this method to control such high-speed, high-output motors.
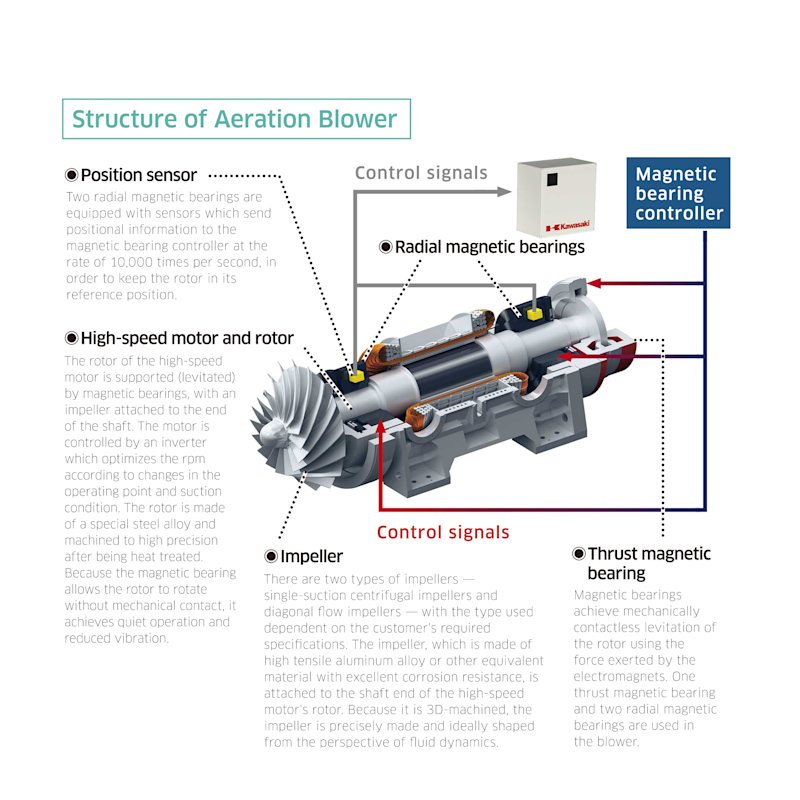
At the same time, an important review of the impeller to compress the air was made. The first impeller was developed internally by Kawasaki half a century ago, and the designs for the shape and the airflow path are always improving with cutting-edge technologies.
Hashimoto, Senior Staff Officer at the Energy System & Plant Engineering Company, reveals the secret: “For the development of the M55, we used an analytic method called genetic algorithms to determine the optimal shape, achieving both high pressure and high efficiency at a relatively low rpm.” In addition, a special aluminum alloy is adopted to ensure impeller strength under high temperatures due to compression heat as the discharge pressure approaches 100 kPa.
The fan-shaped inlet guide vanes in front of the impeller at the suction port open and close to cause the air to swirl. In addition to this adjustment, the inverter exerts optimum rotation control so that the airflow volume is regulated efficiently for a wide range of outputs. Thanks to this feature, the blower demonstrates excellent partial-load efficiency even when not operating at full capacity.
For example, the operation record indicates that the cost of electricity for the M55 to raise the pressure of a unit volume (1 m3) of air to 60 kPa was 20% lower than for a conventional large-capacity blower. The M55 requires about a half the electricity when comparing the installation footprint to produce the same amount of compressed air from a conventional unit. This means that the M55 is a large-scale model with energy- and space-saving advantages.
Hashimoto adds, “The principle of levitating the rotor utilizing magnetic bearings is the same for all MAG Turbo models. However, in order to apply it to a motor with an output that far exceeded what we had been producing, our machinery and electrical engineering departments had to, putting their heads together, entirely modify the model. We also couldn’t let the price get too high, or it wouldn’t sell, so we pursued both enlarged scale and reduced cost by reviewing the design and the production method of the magnetic bearings.”
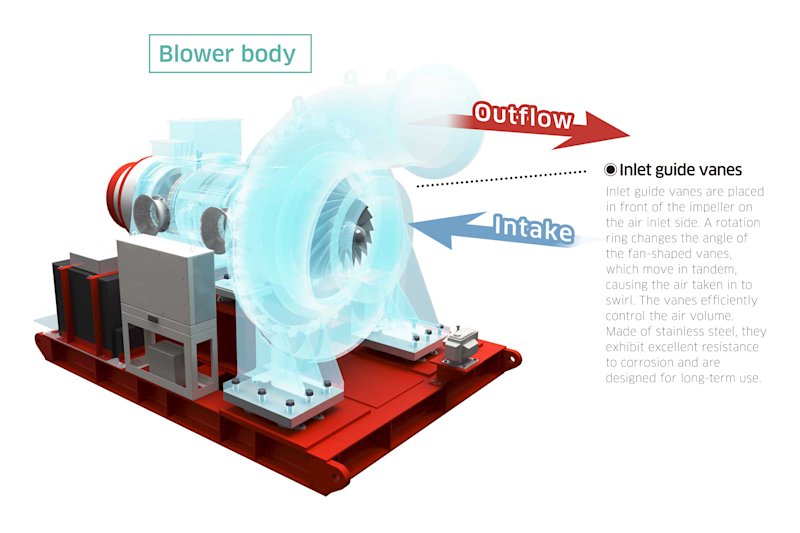
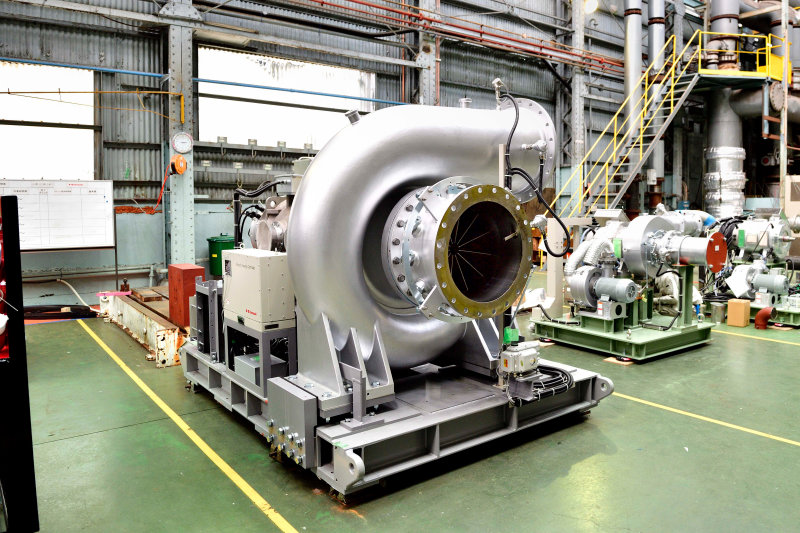
An actual load test of the M55 began in November 2019 at the Mikasagawa Sewage Plant in Fukuoka Prefecture. This facility is one of the largest sewage plants in Kyushu region and processes up to 300,000 m3 of wastewater per day. The M55 replaced two medium-sized blowers and, operating under actual load conditions, reduced power consumption. The construction cost was also lower than that of previous equipment because of the smaller installation footprint.
In addition, a unit of the M55 was delivered to a large sewage plant in Russia in May 2021. One of the largest in Europe, the plant can treat 3 million m3 of wastewater per day. (In Tokyo, the largest plant is the Morigasaki Water Reclamation Center, which treats 1.14 million m3 per day.) Total eight units of the M55 are scheduled to start operation in September 2021.
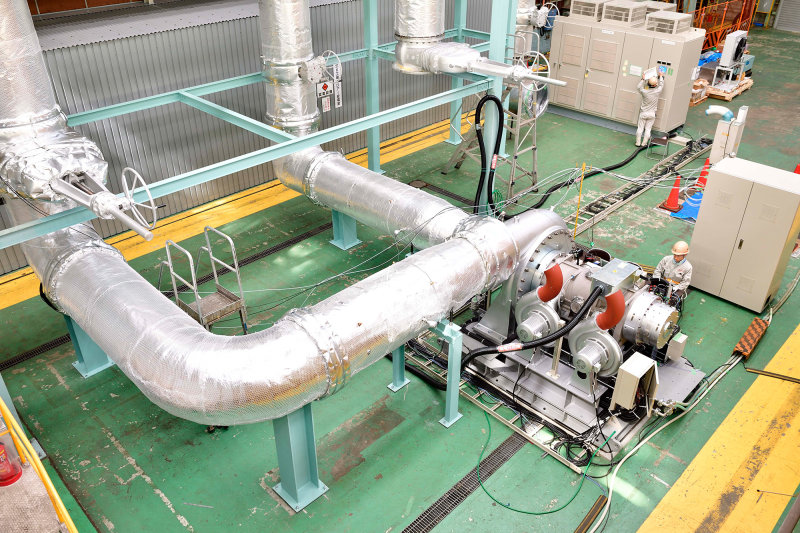
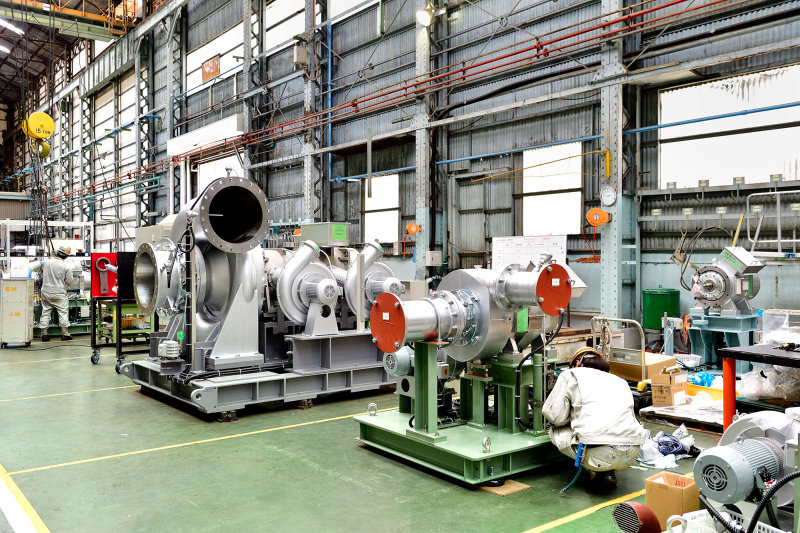
The evolution of the M55 is ongoing. Together with the New Energy and Industrial Technology Development Organization (NEDO) of Japan, Kawasaki has launched an international demonstration study on a sewage cogeneration system involving the M55. The sewage sludge from the wastewater treatment process has great potential as fuel and fertilizer. For example, the clean natural gas and biogas harvested from sewage treatment facilities can be used as a fuel for a gas turbine power generator. The electricity generated by the gas turbine can be used to power the blower, while the heat generated can be used to dry the sludge. In summary, Kawasaki can build an ecosystem that provides electricity, heat, and air.
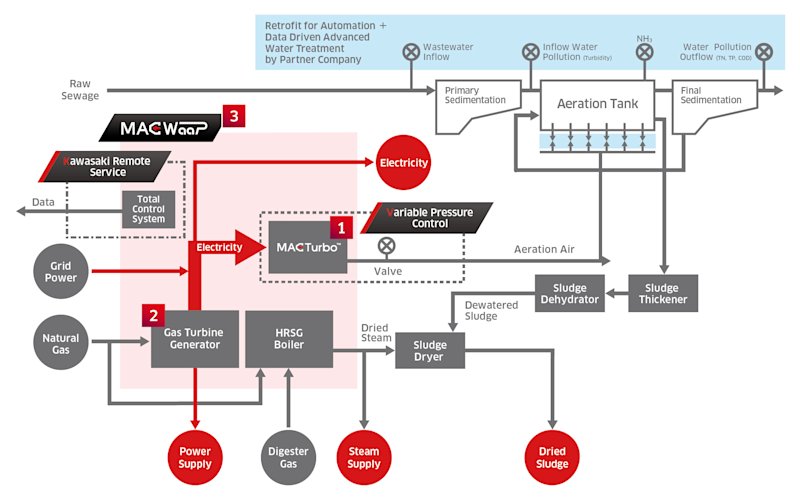
Transfer of Wastewater Treatment Expertise from Osaka City to Historic City of St. Petersburg
Having a long history of operating sewage plants and time-tested expertise in the field, Osaka City intends to expand the use of this internationally. St. Petersburg in Russia is a sister city, and they signed a Memorandum of Understanding (MOU) in 2015 for a technical exchange of expertise for water and sewage systems. Every year since then, Osaka City has provided support through improvement and modernization projects for St. Petersburg’s water and sewer services via technical exchanges. Kawasaki is part of this program in the area of wastewater treatment and is gaining a high reputation. Observing Kawasaki’’ efforts, an Osaka City official is quoted as saying, “The Company’s sophisticated technology and passion for market development strongly support our technical exchanges. I was very impressed that the person in charge of field operations in St. Petersburg was still asking questions of Kawasaki after the allotted time had ended.”
Goal 6 of the Sustainable Development Goals (SDGs) endorsed by the United Nations is to “ensure availability and sustainable management of water and sanitation for all,” and Goal 7 is to “ensure access to affordable, reliable, sustainable and modern energy.” The technologies of Kawasaki for the promotion of energy saving at wastewater treatment plants, the use of sewage sludge as energy, and supplying clean water are the drivers that move forward the fulfillment of the water and energy goals of the SDGs. Continuing technological innovation and solving the issues of customers and society, Kawasaki contributes to the establishment of sustainable water infrastructures.
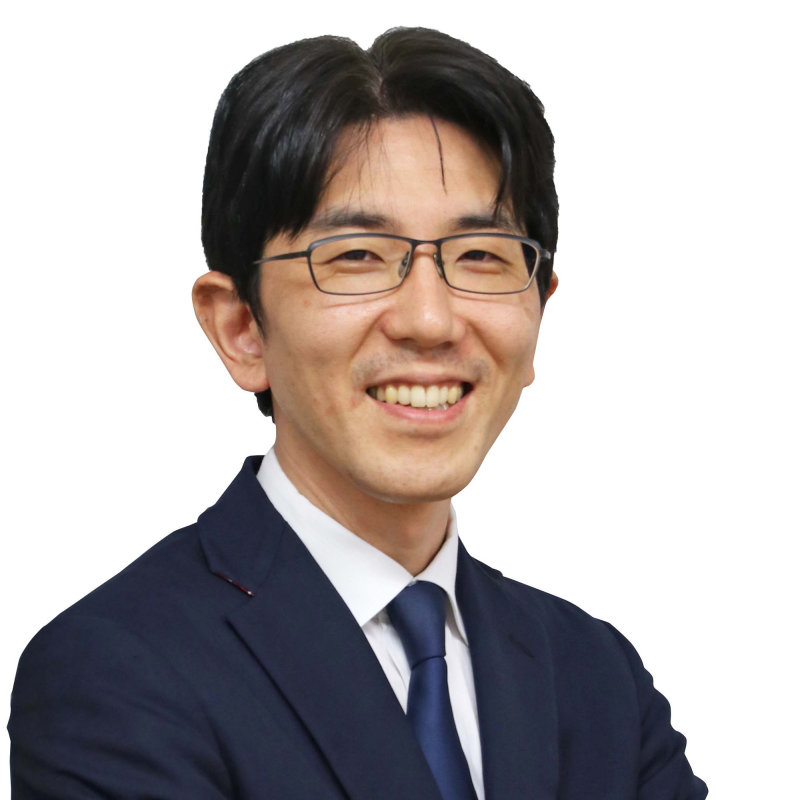
International Affairs Office and Office for Promotion of International Project
Infrastructure System and Water Industry
Manufacturing Industries Bureau
Ministry of Economy, Trade and Industry
High-Quality Water Infrastructure for the World: Strategy for Selling the First MAG Turbo in North America in FY 2021
In 2013, the Japanese government formulated the Export Strategy for Infrastructure Systems with the goal of winning approximately 30 trillion-yen worth of orders for overseas infrastructure systems in 2020. The strategy’s four pillars for meeting this goal were to (1) strengthen competitiveness through collaborative efforts between public and private sectors, (2) implement strategic initiatives for winning orders, (3) promote high-quality infrastructure, and (4) expand the range of infrastructure to be developed. Through measures to improve and enhance support, the strategy yielded results, such as orders totaling 25 trillion yen in 2018.
To further improve recognition of its sophisticated technologies among Japan’s trading partners, the Ministry of Economy, Trade and Industry (METI) has been actively implementing policy tools, including top-to-top sales meetings, intergovernmental negotiations, feasibility studies, and human resource development.
As one such endeavor, METI has been conducting a series of studies called the Project on Feasibility Study Toward Overseas Expansion of High Quality Energy Infrastructures, and in FY 2019 and FY 2020, it made Kawasaki Heavy Industries’ high-output MAG Turbo with magnetic bearings subject to this study, focused on entry into the US market. Specifically, the study provides marketing analyses, a select list of local after-sales service partners, and plans for actual operation of the blowers in North America under the presumption that more than 100 wastewater treatment plants are potential Kawasaki Heavy Industry customers. In short, the study provides an infrastructure export strategy for Kawasaki to close deals in FY 2021 and onwards.
Although Japanese companies’ share in the water business market in North America (valued at 18 trillion yen in 2016), the second largest after Europe, is 0.1%* and still limited, we think market entry opportunities are expanding because the number of renewal projects for aging sewage plants is rising, and the need for reclaimed water for drinking due to water resource shortages is increasing.
To promote market entry, METI will continue its efforts to increase the presence of Japanese companies using the results of the feasibility studies and by broadly communicating the technological prowess at international events and other opportunities in cooperation with the private sector.
Today, with the global spread of COVID-19, new strategies are necessary to meet the infrastructure needs that previously did not exist. At this time when social paradigm shifts, including digitization, are accelerating more than ever, strategies for water infrastructure must focus on improvements in fundamental public sanitation and the spread of new technologies that allow for contactless, remote monitoring and services. METI plans to proactively support Japanese companies in expanding business opportunities and improving competitiveness in these new segments.
We hope to win our first order for the MAG Turbo in the North American market in FY 2021 and become one of the icons of infrastructure exports in the new era.
*Source: “Overseas Development Strategy of Water Industry” released by METI in July 2018
Note: The numerical values and job titles stated herein are based on information as of October 2020.