Once-Through Boiler WILLHEAT
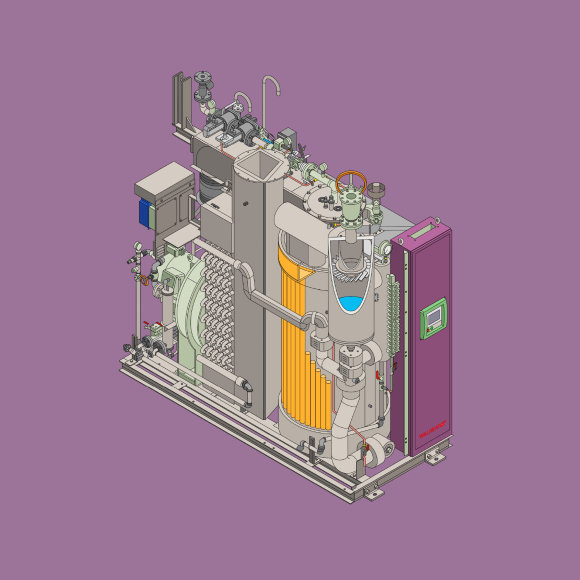
In 2019, Kawasaki Thermal Engineering developed and sold the once-through boiler WILLHEAT, proving to the world that significant technological advances were still possible for boilers, which were considered products from mature technology whose performance indices were hard to improve even by 1%. The ceaseless pursuit of user benefits from development culminated in technology that realized a greater than 1% performance improvement. The expertise and uncompromising attitude in the background are discussed in this report.
Customer-Centricity Drives Our Pursuit of Technological Innovation
In 2019, Kawasaki Thermal Engineering Co., Ltd. (KTE) developed and sold the once-through boiler WILLHEAT, proving to the world that significant technological advancement is still possible for boilers, which are considered products with mature technology whose performance indices are hard to improve even by 1%.
WILLHEAT now boasts a 99% efficiency rate (the percentage of the total absorption heating value of outlet steam in the total supply heating value), an increase from 98%, achieving the highest rate in the boiler industry. This accomplishment is attributable to a newly-designed economizer, which preheats feed water using waste heat, and the adoption of PID (proportional-integral-derivative) control, which controls the boiler’s combustion and water feeding.
Many boilers have a turndown ratio*1 of 5:1 (i.e., 20%). The WILLHEAT, however, achieves an even higher ratio of 7:1, or the lowest combustion rate being about 14%.
A boiler can be run at a lower cost if the combustion for steam production is continuous and the temperature of the boiler proper is maintained, compared to repeatedly cycling on and off. In that way, CO2 generation can also be curbed, which makes the improved turndown ratio a significant benefit for industrial facilities using boilers.
KTEʼs proprietary “Steam-Water Separator” results in a greater than 99.5% steam dryness, which indicates a high quality of energy, since the higher the steam dryness, the greater the amount of heat energy. Therefore, achieving a higher steam dryness can significantly improve the production efficiency of industrial facilities using steam.
This is one of the fruits of our ceaseless pursuit of user benefits, which culminates in technology that realizes a “greater than 1% performance improvement.”
*1 The turndown ratio refers to the ratio of the largest combustion amount and the least combustion amount
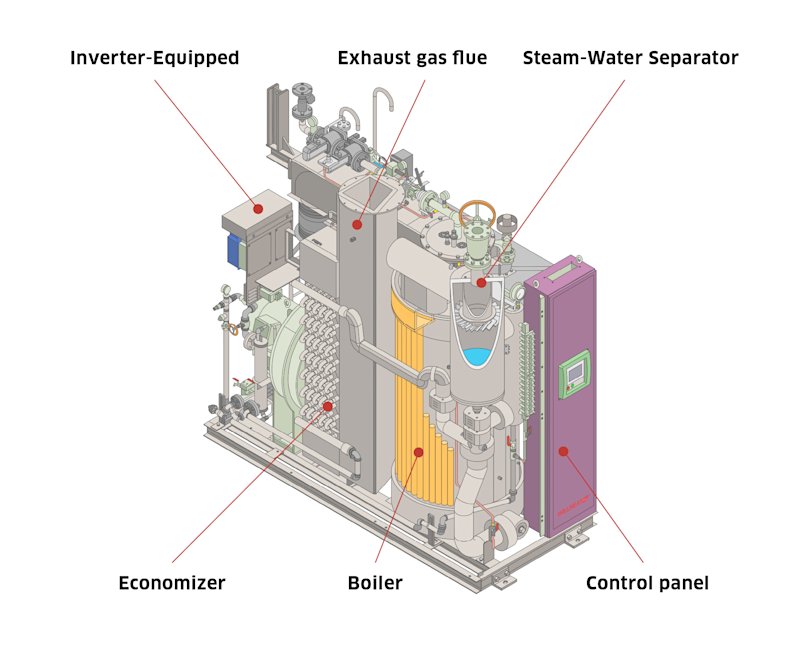
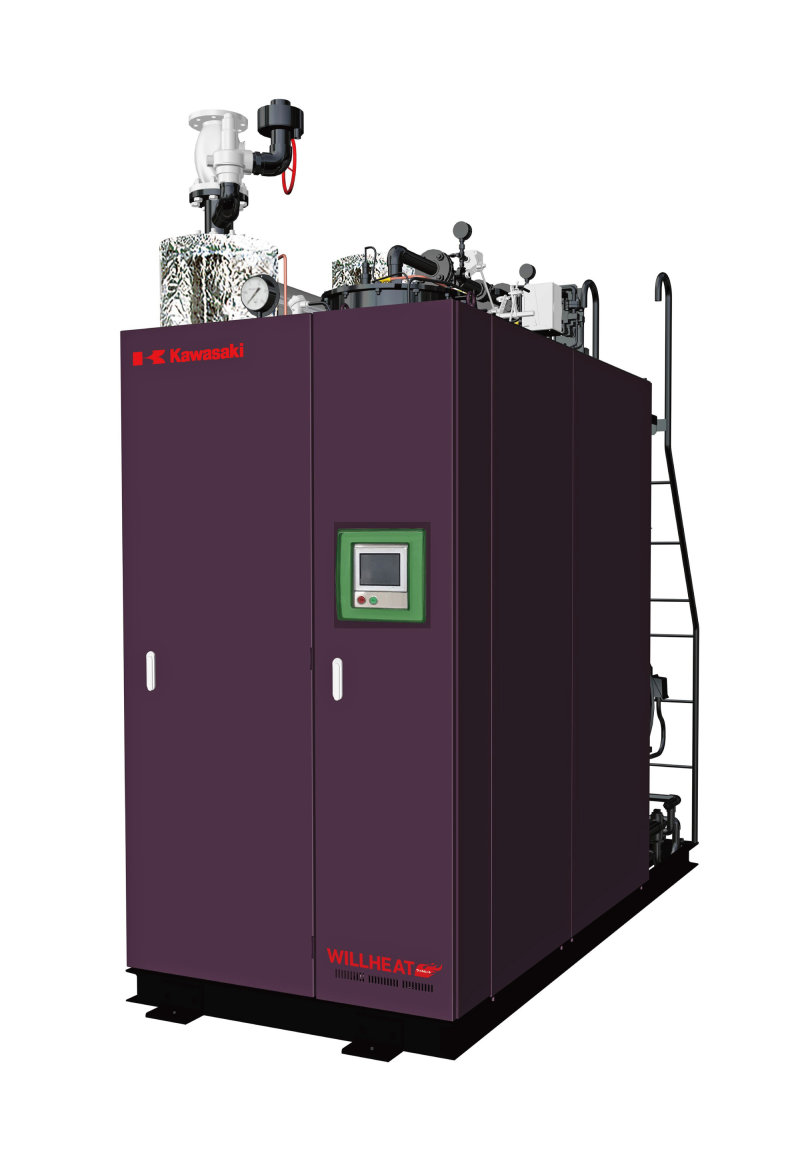
How a Once-Through Boiler Works
A once-through boiler is composed of water tubes, into which water is fed from one end and steam is output from the other end. Small type once-through boilers with compact configuration typically hold less water than normal sized versions and offer a shorter steam generation reaction time, as well as smaller footprints. The economizer preheats the feed water using waste heat, and this heated water is fed into the boiler’s water tube, which produces steam following additional heating by residual heat inside the Steam-Water Separator. KTEʼs product portfolio includes both the compact “WILLHEAT” and the large-sized “Ifrit,” which can produce 6t of steam per hour.
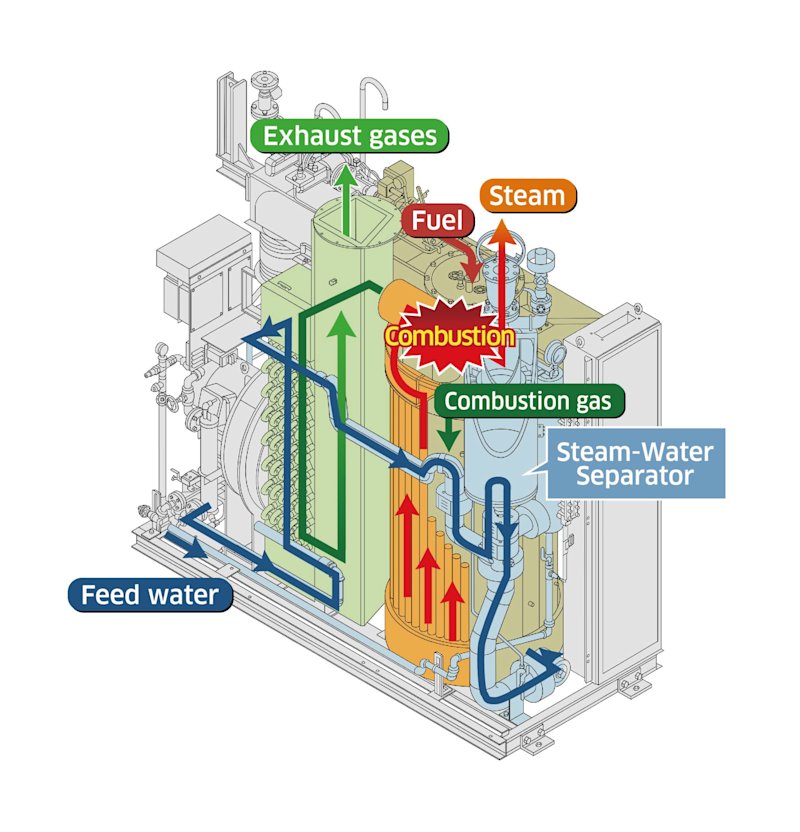
Steam-Water Separator
A steam dryness - the proportion of steam in “wet steam,” a mixture of steam and water - of greater than 99.5% is achieved by KTE’s proprietary Steam-Water Separator. The fins, which are turning inside the Steam-Water Separator, accelerate the centrifugal speed of the steam generated in the boiler, and the steam becomes drier after unvaporized hot water is removed by the inversion separator.
Also, because the water used for the boiler is preheated in the lower part of the separator, thermal shock - the result of cold water coming into contact with hot water inside the water tubes — can be avoided.
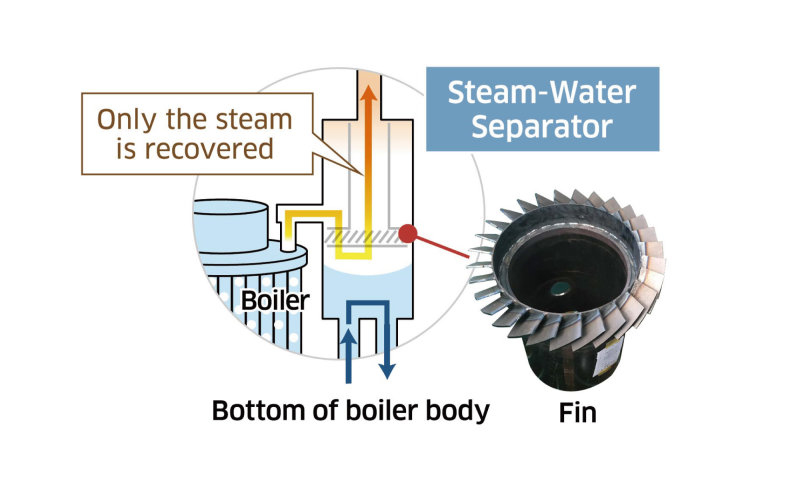
Boiler Combustion Control and Water Tube Fins
The boiler converts into steam the feed water fed from the lower section of the boiler, using the heat generated through combustion in the burner installed in the upper section of the boiler. During this process, PID control is at play, ensuring that the burner’s flames are distributed properly so that no particular area is at an excessively high temperature and NOx emissions can be avoided as much as possible. PID control also optimizes the degree of heating during periods when less steam is required (i.e., when reduced amounts of water are fed into the system), which is KTE’s unique tuning method for optimizing the “chemistry” between the burner and the boiler (furnace). The water tubes are equipped with fins of different shapes, optimized according to the location of each individual water tube, thereby facilitating the tuning.

Economizer
The economizer is the main player in achieving 99% boiler efficiency, effectively recovering waste heat by creating a heat exchange between the feed water and the boiler’s exhaust gas. A great deal of heat can be recovered if the area occupied by heat-transfer tubes (through which the feed water flows) is large. However, this approach increases the size of the boiler system, resulting in exhaust gas flowing in a larger area, slowing down flow speed and lowering thermal conductivity. To resolve this dilemma and achieve the best results, KTE has optimized the layout of the heat-transfer tubes and added fins to them. The rounded, protruding parts in the illustration are the heat-transfer tubes.
Inverter-Equipped
Using an inverter, the system continuously controls the forced draft fan that feeds into the furnace the air for combustion, while changing its rpm according to the combustion load as well as controlling the water pump that adjusts the amount of feed water.
Use of New Boiler Fuel: Hydrogen
In March 2018, KTE launched a demonstration of a once-through boiler fired by hydrogen - the next-generation energy source. Tests on each element of the boiler have been completed successfully and experiments focused on commercialization are now being conducted. To resolve the challenge of NOx emissions resulting from hydrogen with a high flame temperature, KTE has changed the shape of the burner and taken other measures to improve prospects for commercialization.
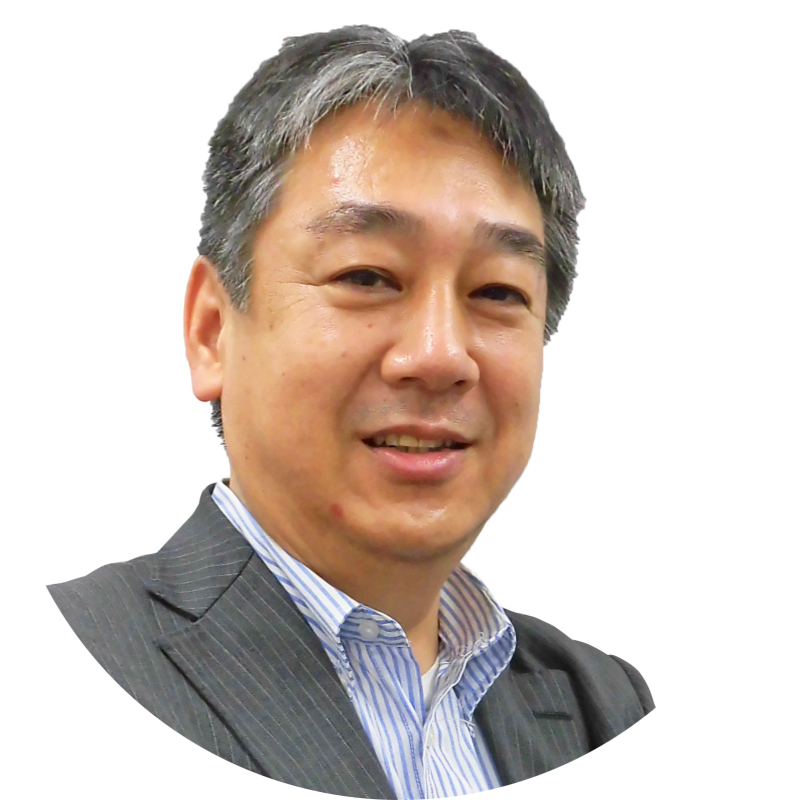
Sales & Service Control Office
Kawasaki Thermal Engineering Co., Ltd.
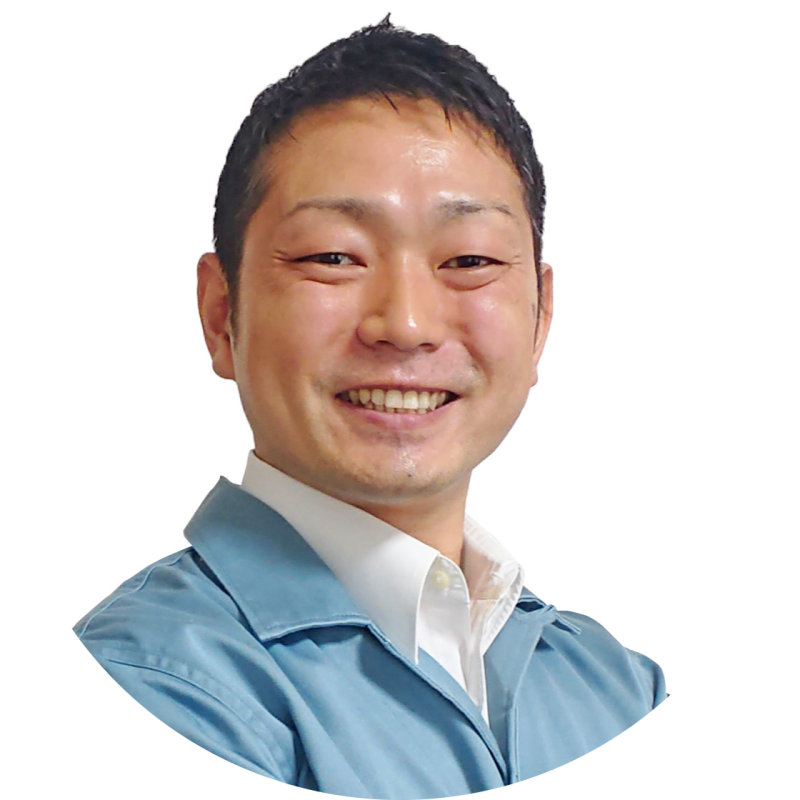
Engineering Office
Research & Development Department
Kawasaki Thermal Engineering Co., Ltd.