Shield Machines: Main Players in Underground Tunnel Boring
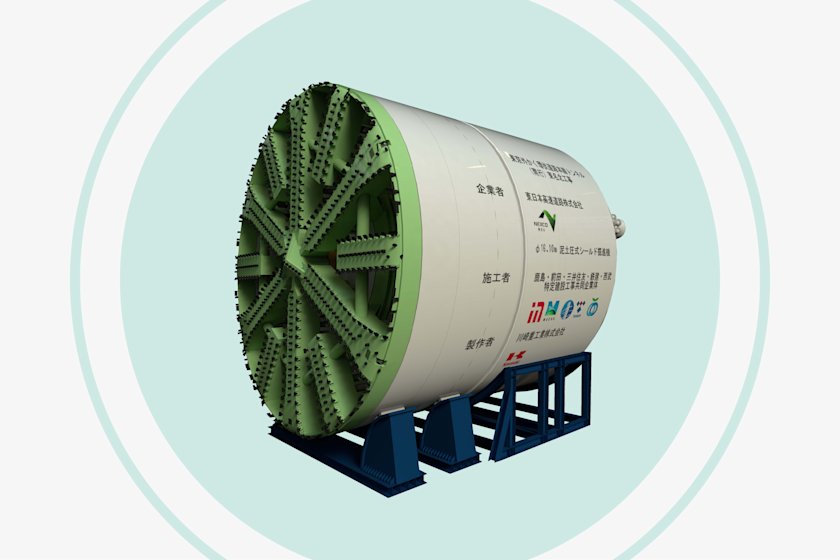
In the past several decades, shield machines have undergone many improvements, reflecting technological advancements in this sector. Even today, they are still the most common boring apparatus for tunneling projects. Kawasaki delivered its first tunnel boring roof shield for a post-war subway construction project in Japan. This marked the beginning of the company’s evolution into a technological leader in mechanizing, upsizing, and automating shield machines.
There are two main construction methods for underground tunnels: 1) the cut-and-cover tunneling method, in which the ground is excavated from the surface down, and 2) the shield tunneling method, in which a vertical shaft is excavated first (without further excavation from the surface) and then lateral excavation is performed from the vertical shaft.
The latter method uses a shield machine, which is an excavator guarded by an outer frame (shield) strong enough to withstand the pressure from earth and water during construction. The machine excavates the ground with a rotating cutter in the front. In this method, the tunnel walls are built to the rear of the shield machine as it moves forward.Thanks to these features, the shield tunneling method is less susceptible to effects caused by groundwater, both during and after construction. Various types of shield machines are used, depending on the properties of the soil: a basic shield machine is used for soft ground, a Tunnel Boring Machine(TBM) for hard rock, and a full-shield TBM when both soft and hard soil are present.
Roof shield (φ 11.6 m) delivered
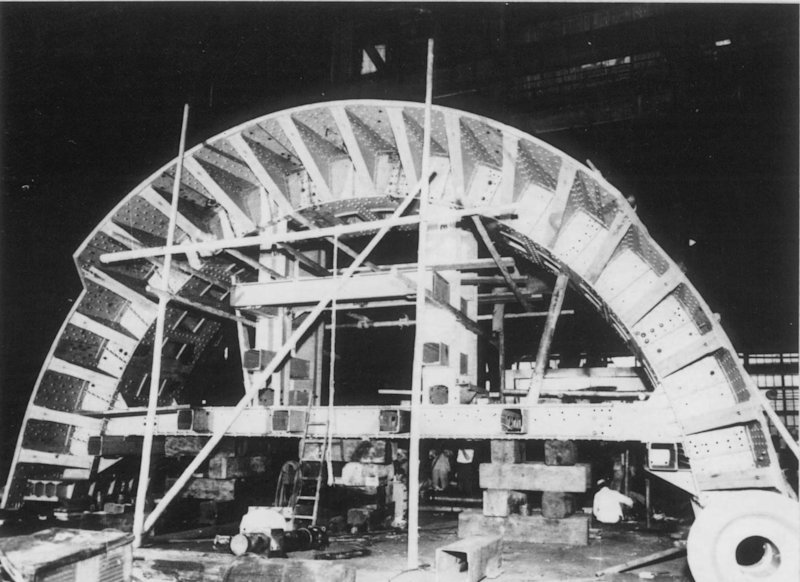
Development of this piece of equipment led Kawasaki to become a leading shield machine developer/manufacturer. It was used for boring a 231-m long tunnel, launched from Kokkai-gijidomae Station on the Marunouchi Subway Line and driving toward Shinjuku. It was the first application of the roof shield tunneling method to a subway tunnel project in Japan.
Full-shield TBM(φ 8.78 m) use began
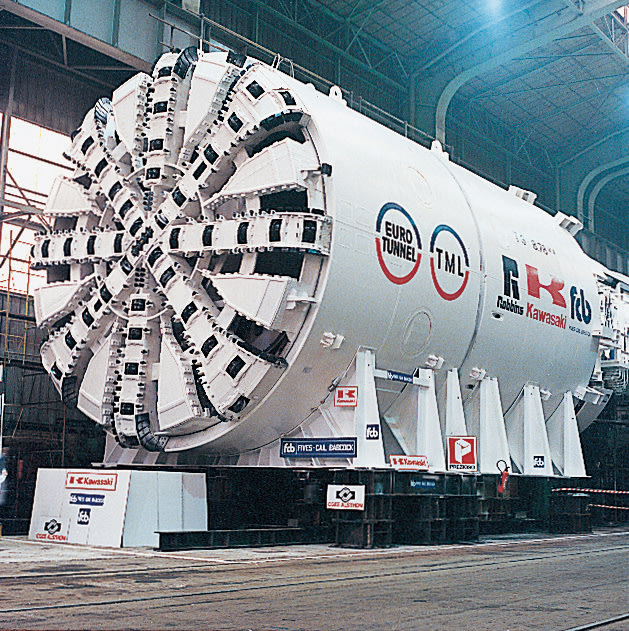
Capable of boring through both soft soil and hard rock, this machine was used for constructing the Channel Tunnel beneath the Strait of Dover. Kawasaki completed boring of its initial target of 16 km eight months ahead of schedule, an achievement that garnered a contract for an additional 4 km. The project was originally conceived of and attempted by Napoleon Bonaparte 200 years ago, with twenty-six subsequent attempts also failing, but the 27th was a success, to which Kawasaki’s shield machine contributed greatly.
Slurry shield machine (φ 14.14 m) delivered
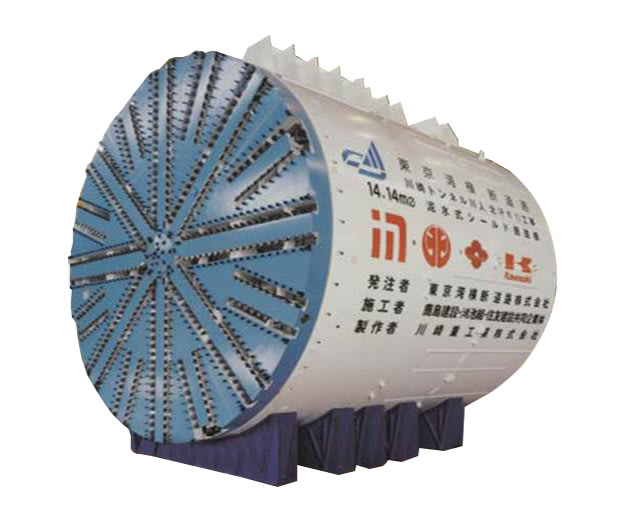
This machine, the diameter of which was the world’s largest at that time, was used in boring the undersea tunnel for the Trans-Tokyo Bay Expressway (a.k.a. Tokyo Aqua-Line Highway). Because the project involved boring two 10-km-long tunnels, eight shield machines were used, of which three were manufactured by Kawasaki. (Because the excavated earth is discharged with water mixed in, it is called a “slurry shield machine.”)
Shield machine with APORO Cutter (All Potential Rotary Cutter) system delivered
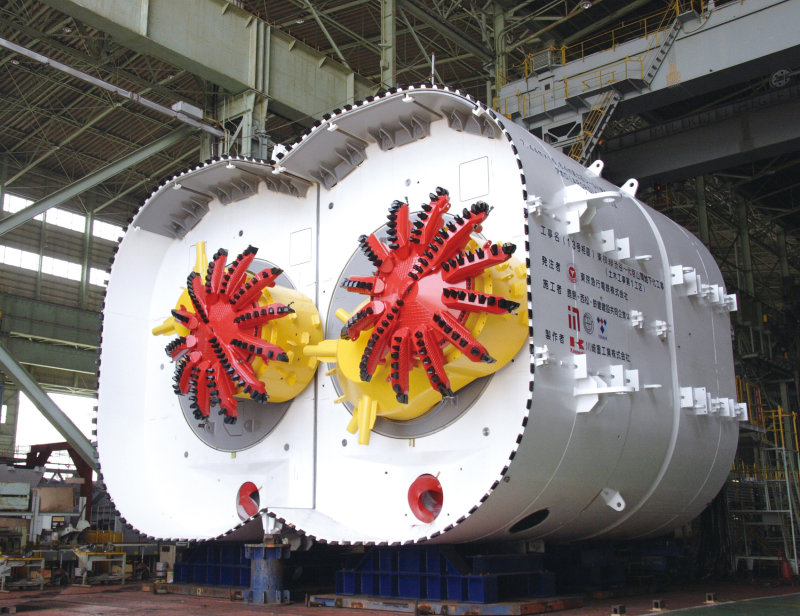
This shield machine was used for the underground section in between Shibuya and Daikanyama Stations on the Tokyu Toyoko Line. A non-circular shield had to be developed in conjunction with Kajima Corporation in order to achieve an effective excavation cross section for the double-track railway line while keeping a safe distance from sewage pipes, the pilings of buildings, and other obstructions under the ground.
In this double-headed machine, both cutters rotate as the drums revolve.
Earth Pressure Balanced shield machine (φ 16.1 m) launched
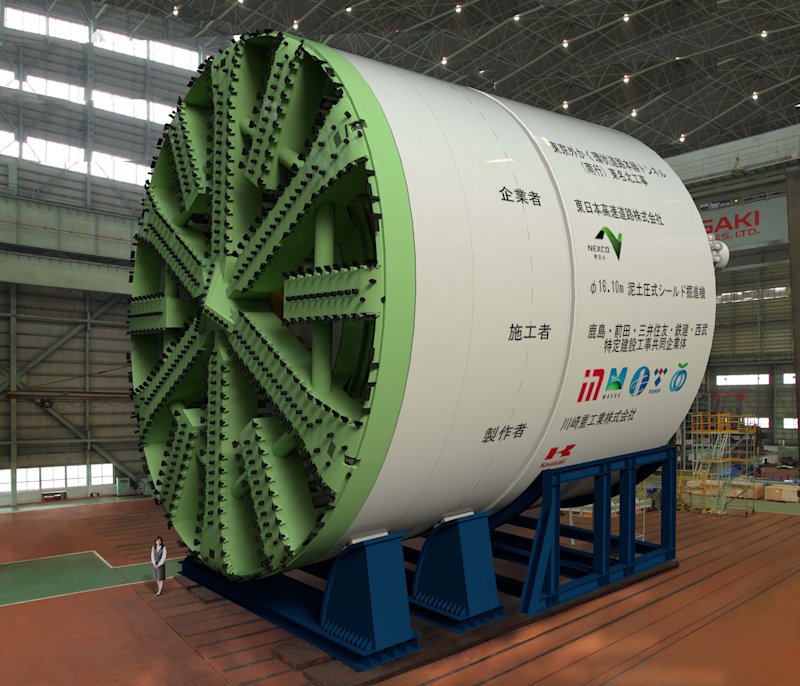
This latest Earth Pressure Balanced(EPB) shield machine is being used for boring the 16-km-long underground tunnel for the Tokyo Outer Ring Road, which connects the Tomei Expressway and the Kan-Etsu Expressway. The 3-lane tunnel, for southbound traffic, is being excavated from the Tomei end by a Kawasaki machine. With another team excavating from the Kan-Etsu end, the tunnel hole-through is expected to take place beneath Inokashira-dori Avenue. Kawasaki’s shield machine is responsible for a 9-km-portion of the 16-km tunnel, which is one of the longest distances bored for a tunnel in Japan. The diameter of this machine is 16.1 m, which is the largest in Japan.
Kawasaki first entered the tunnel boring market in 1957, when it delivered a roof shield to Teito Rapid Transit Authority (present-day Tokyo Metro Co., Ltd.) for its project to construct the Marunouchi Subway Line. The roof shield was originally designed for manual boring.As mechanization of the boring process was progressing at that time, Kawasaki developed a mechanized shield machine, using its heavy-industry expertise. Since then, the company has been leading the industry by developing innovative boring equipment to respond to emerging needs. These requirements included larger bores, automation, optimization of the excavation cross section, reduction of vertical shafts, and accommodation for significantly deeper construction sites and excavations covering longer distances.
These behind-the-scenes machines are actually the main players in tunnel boring. To date, Kawasaki has delivered 1,400 units for both domestic and international tunnel projects.