Air-Supported Belt Conveyor Kawasaki Flow Dynamics Conveyor (FDC)
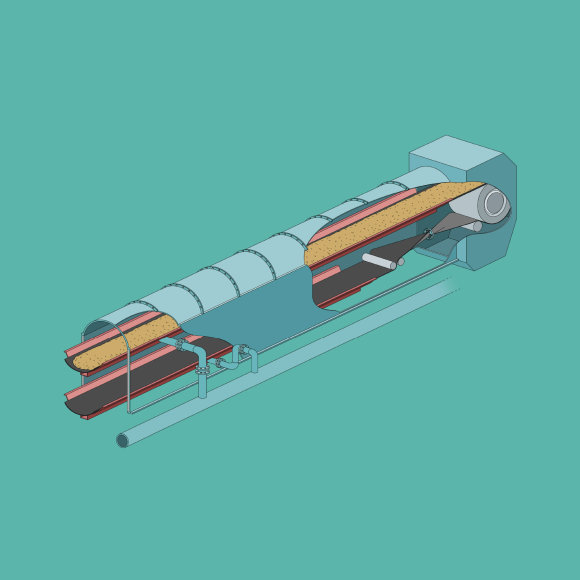
Since the first unit was delivered in 1994, the Kawasaki Flow Dynamics Conveyor (FDC), an idler-less belt conveyor, has been an excellent component for power plants and steelworks in Japan and abroad. Since the belt in the FDC is supported by a cushion of air, there is less maintenance required, lower vibrations and noise, and higher-speed conveyance compared to conventional conveyors with many idlers rotating beneath the belt. The key is the technology and devices to levitate the materials for transport like an air hockey table.
Belt Conveyor Utilizes Air to Transport Materials
The most common image of a belt conveyor used for transporting coal, iron ore, fly ash, and other bulk materials is one with many idlers rotating beneath the belt. However, Kawasaki’s Flow Dynamics Conveyor (FDC) is a very different type in which the belt is supported by a cushion of air.
A number of advantages are brought about by supporting the belt with air. The carrier and return sections are idlerless and fully enclosed to achieve low-noise, low-vibration, and high-speed conveyance, as well as drastically reduced maintenance. The casing contributes to precluding dust spillages, making it an eco-friendly system as well.
Kawasaki began developing the FDC in 1992 and launched its first commercial unit two years later. Thanks to ongoing improvements, to date, the company has delivered 287 units to power plants, steelworks, and other sites in Japan and abroad.
Some FDCs are equipped with a 2m-wide belt stretching over 1 km, moving 6,600 t of coal per hour. It is amazing that air can perform such heavy-duty tasks.
The principle behind the FDC is basically the same as that of an air hockey table. The means by which the belt is levitated is key to making this system work. The belt is floated by a small amount of air introduced into the plenum between the belt and the semicircular trough beneath, with the amount and pressure of air adjusted according to the type of material being transported.
On top of Kawasaki’s proprietary know-how, advancements in the technology for producing and machining troughs have contributed greatly to improving the FDC. A marriage of hydrodynamic theory and manufacturing expertise has resulted in a remarkable evolution in this material handling system.
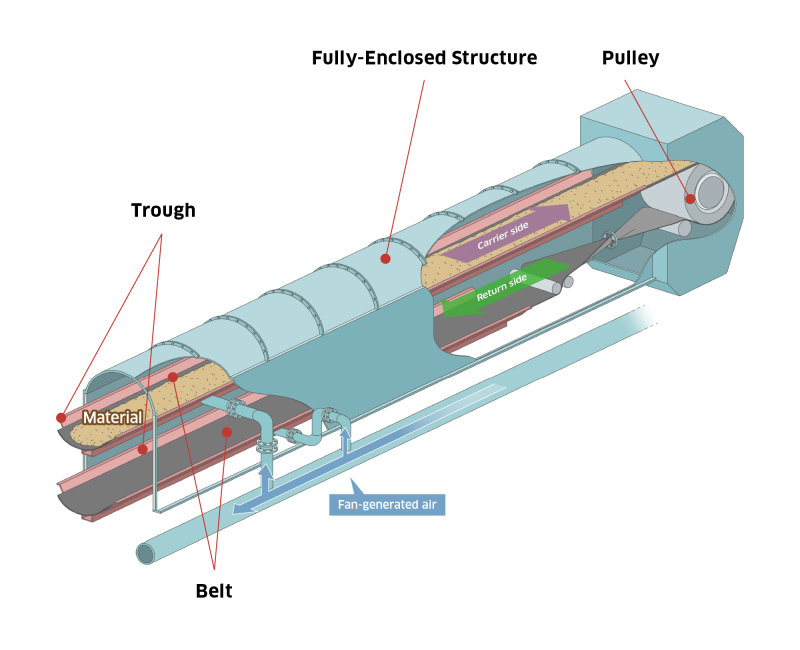
What is the Principle behind the FDC?
Via supply holes, air is introduced from underneath the semicircular trough, levitating the belt, which is moved by rotating pulleys installed at both ends of the system. Small holes are lined up at the bottom of the trough for controlling the amount and pressure of air according to the type and volume of material. It is the combination of these features which makes the belt float properly.
Two troughs are used in the FDC — one under the carrier side of the belt and the other under the return side of the belt, configured on top of each other.
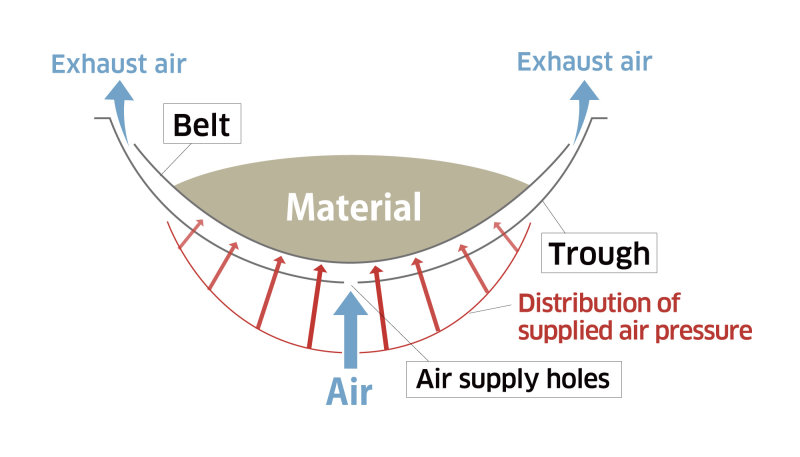
“Belt Turn-Over Technique” Keeps Trough Clean
To prevent the carrier side of the belt from contaminating the trough after it begins the return passage and is face down, a device is used to flip the belt after it completes its pass through the upper trough but before entering the lower trough. Just by flipping the belt 180 degrees, cleaning of the long conveyor becomes unnecessary and maintenance cost is reduced.
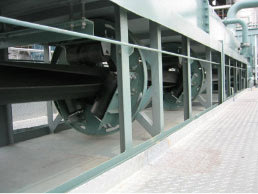
Factory-Assembled Frames Are Installed on Site
Troughs, casings, and auxiliary equipment are pre-assembled at the factory before being shipped to the site where they are joined together and installed. This modular method significantly reduces construction time.
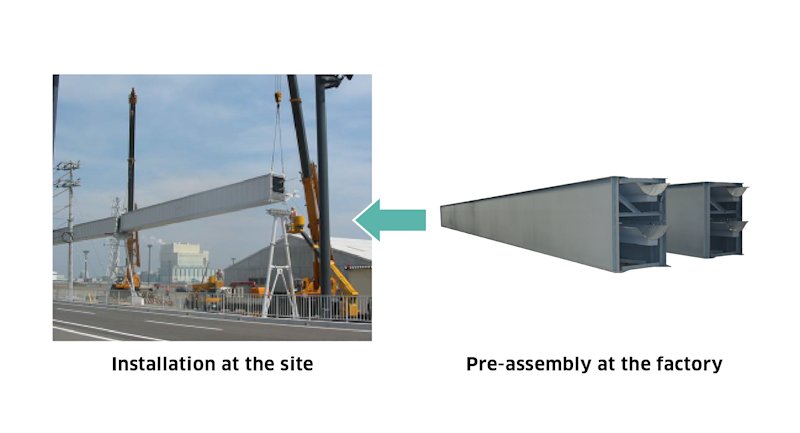
Enormous Eco-Friendly Structure
The photo shows a power plant in Taiwan equipped with two lines of FDCs, parallel to each other. The longer FDC stretches 1 km, moving 4,400 t of coal every hour on a 1.6-m wide belt at a speed of 300 m per minute. Because they are installed offshore, the FDCs are fully enclosed to minimize the environmental footprint.
Trough
The trough is a semicircular structure indispensable for air-supported belt conveyors - the "main player" in this system.
Belt
The width of the belt, which ranges from 0.4 m to 2.0 m, is determined by the type and volume of the material to be conveyed.
Fully-Enclosed Structure
The FDC is an idlerless, fully-enclosed conveyor that achieves reduced noise and vibration. The lack of idlers makes inspection windows for idler replacements unnecessary, thus keeping the entire structure simple.
Pulley
A rotating body that moves the belt. A drive pulley moves the belt while several other pulleys support the belt.
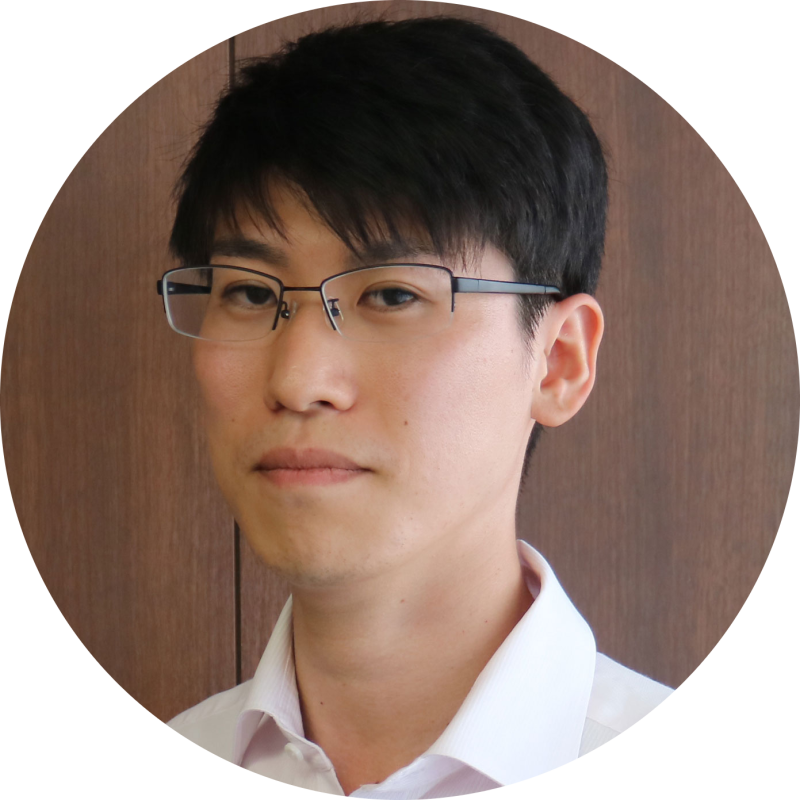
Industrial Plant Engineering Division
Energy System & Plant Engineering Company
Kawasaki Heavy Industries, Ltd.
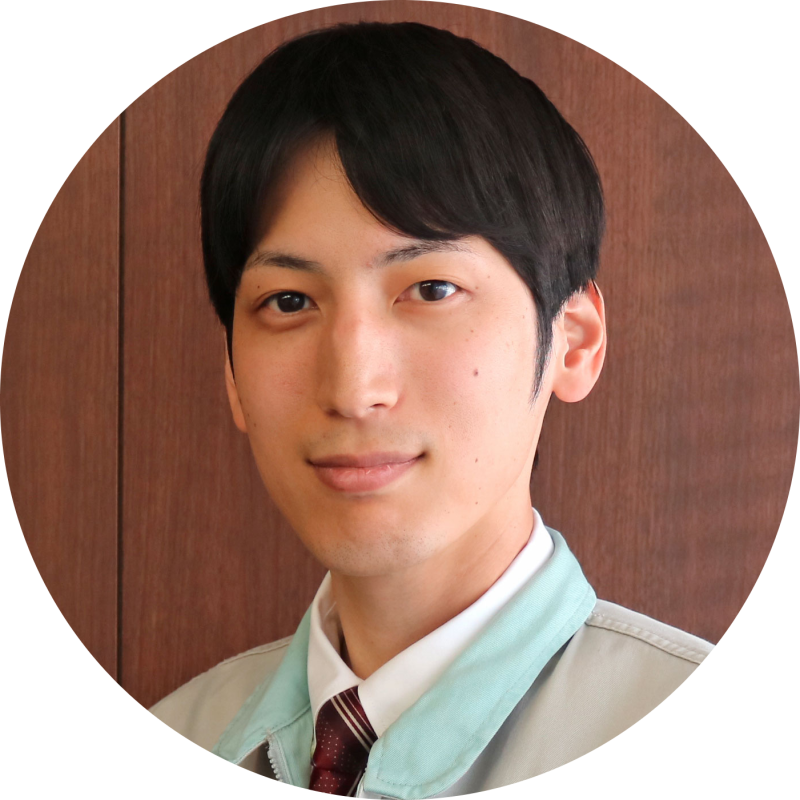
Industrial Plant Engineering Division
Energy System & Plant Engineering Company
Kawasaki Heavy Industries, Ltd.