High-Precision High-Speed Hydraulic Press for Carbon Fiber Reinforced Plastics (CFRP)
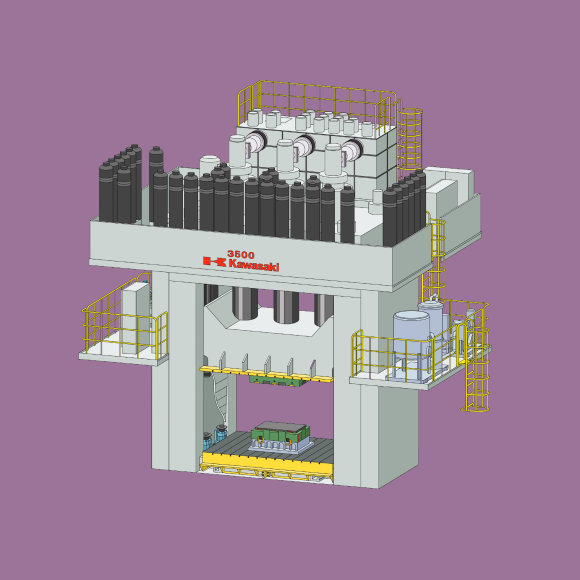
Carbon fiber reinforced plastics (CFRP) are ten times stronger and four times lighter than steel. While the material is used in a variety of products, including sports equipment, industrial machines, and even automobiles and aircraft, sophisticated techniques are required for processing. This article elucidates the expertise in the CFRP hydraulic presses of Kawasaki Hydromechanics Corporation, a press manufacturer with the largest market share of hydraulic press production and sales in Japan.
A Hydraulic Press Packed with the Industry Leader’s Expertise
Press machines mold metal or resin material into desired shapes by applying high pressure. They come in two types, with different mechanisms for applying pressure - mechanical or hydraulic.
Kawasaki Hydromechanics Corporation (hereafter, “KHM”), one of Kawasaki’s Group companies, is a press manufacturer with the largest market share in the Japanese hydraulic press market. To date, KHM has delivered 3,000 units, including 500 for customers outside Japan. The presses are used at various manufacturing sites, improving the quality of parts molding and achieving higher work efficiency.
KHM has been leading the industry with notable achievements, such as commercialization of Japan’s first numerical control system and a high-precision leveling system for hydraulic presses (see Kawasaki’s Superior Technology on the right page). It has also developed a press with an output of 150,000 kilonewtons (kN), which is the highest in the world.
Recently, a high-precision, high-speed hydraulic press for molding carbon fiber reinforced plastic (CFRP) was delivered to Nagoya University’s National Composite Center, which specializes in research for new-generation composite materials. Packed with the seasoned expertise of KHM, the machine is a “dual-purpose” press, capable of molding two different types of CFRP ― thermoset (cured into a solid form when heat is applied) and thermoplastic (cured into a solid form when cooled) ― by applying 35,000 kN of force.
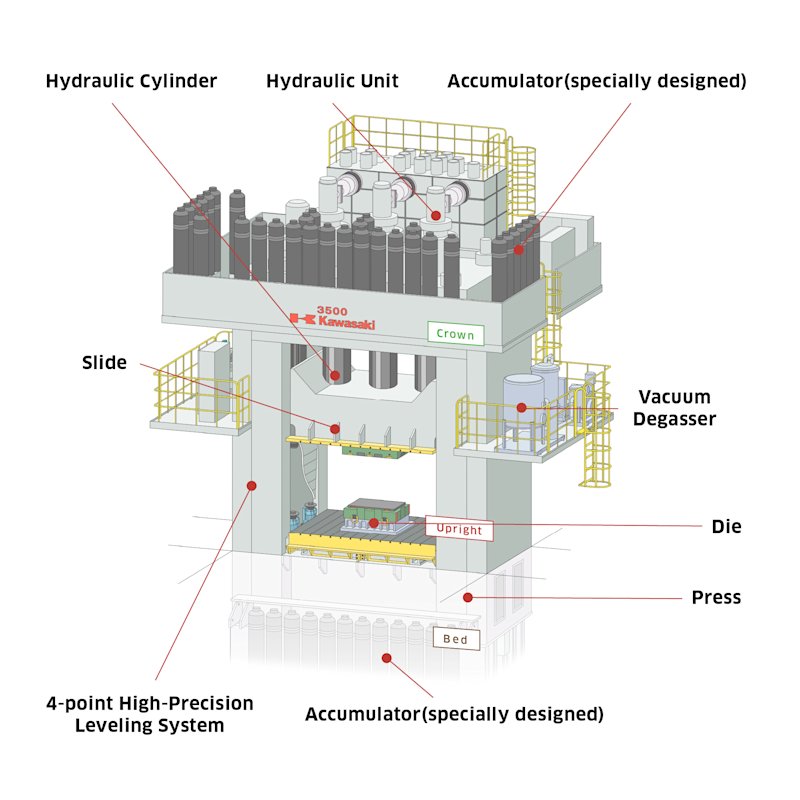
How a Press Machine Works

Accumulator
Balloon-like Components of the Accumulators Control the Press Velocity
When molding CFRP, the two dies must be brought together and pressure quickly applied to the heated blank before it cools down. To achieve this, accumulators (which resemble gas cylinders) installed at the upper section of the press are used to move the press’s cylinders speedily to close the upper die and keep pressing. Inside the accumulator is a rubber balloon filled with nitrogen, which is compressed as oil is injected into the cylinder. When the oil is released, the balloon rapidly expands, resulting in 20 megapascals (MPa) of pressure and discharging a massive volume of oil into the hydraulic circuit to move the cylinders.
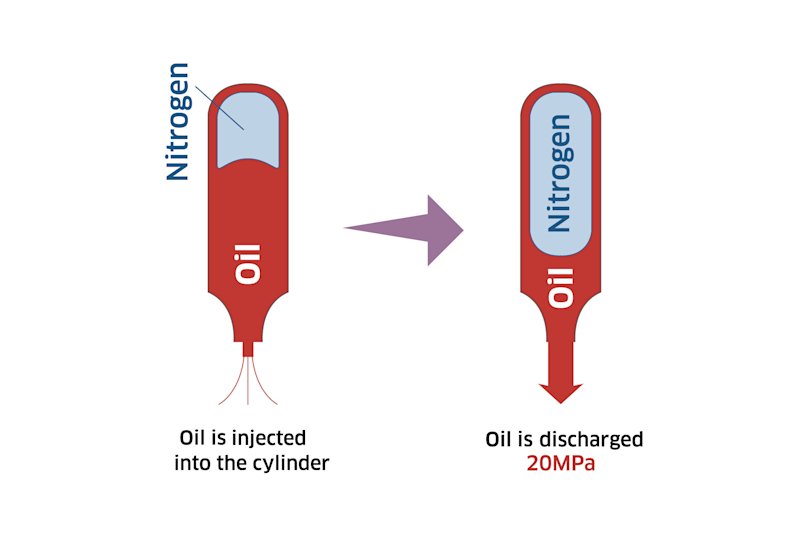
Slide
Perfecting Tasks That Only Hydraulic Presses Can Do
The press’s three cylinders press the die against the blank. These cylinders descend and ascend at a rate of 800 mm/sec, and upon deceleration, exert 35,000 kN of force on the blank in a variety of movements. These various movements and pressure retention features are what distinguish hydraulic from mechanical presses.
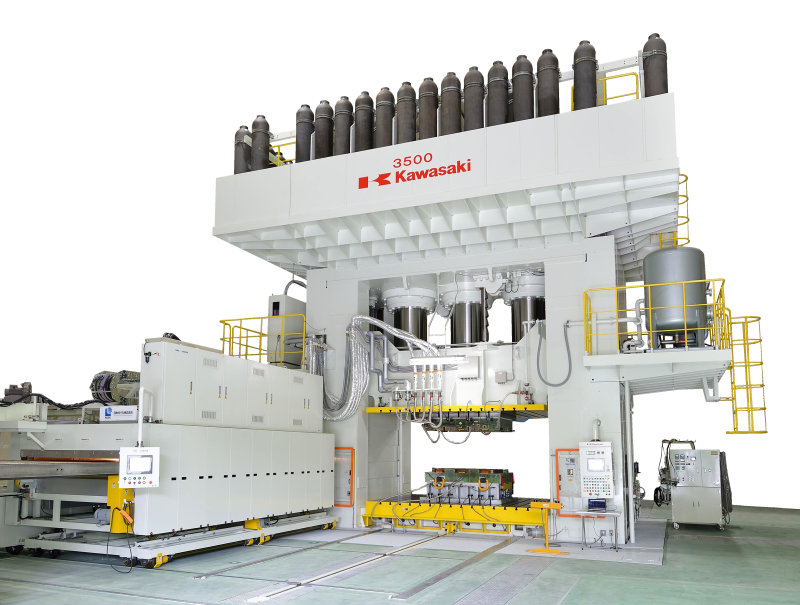
4-point High-Precision Leveling System
Achieves Precision Level of 5/100 mm
When molding resins, pressure must be applied uniformly across the surface or the thickness of the product will be uneven. To prevent this, the upper and lower dies must be leveled and the movement of the press controlled according to the resin’s expansion and contraction. A four-point high-precision leveling system makes this possible, achieving horizontal leveling accuracy of 5 mm per 100 mm. The system controls the hydraulic valve’s movement according to various data sent from the sensors installed close to the four pillars that support the press.
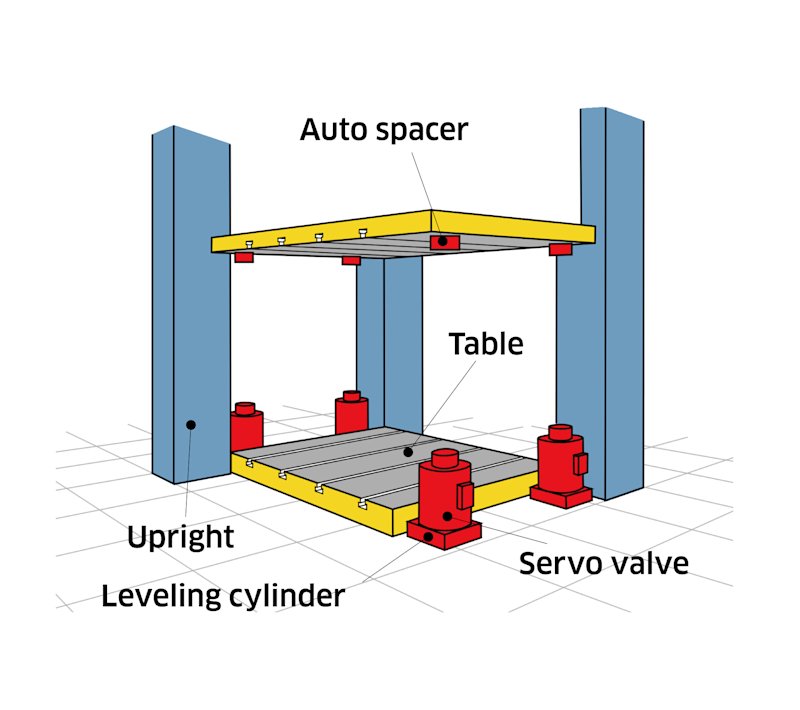
Molded Products Are Used Everywhere
Hydraulic presses produce products that are found in our everyday lives, such as the rear doors, chassis, and bodies of eco-friendly cars; kitchen sinks; and modular bathrooms. The main pillars of the Tokyo Skytree (a broadcasting tower with an observation deck) are made of slabs molded by a press into cylindrical shapes.
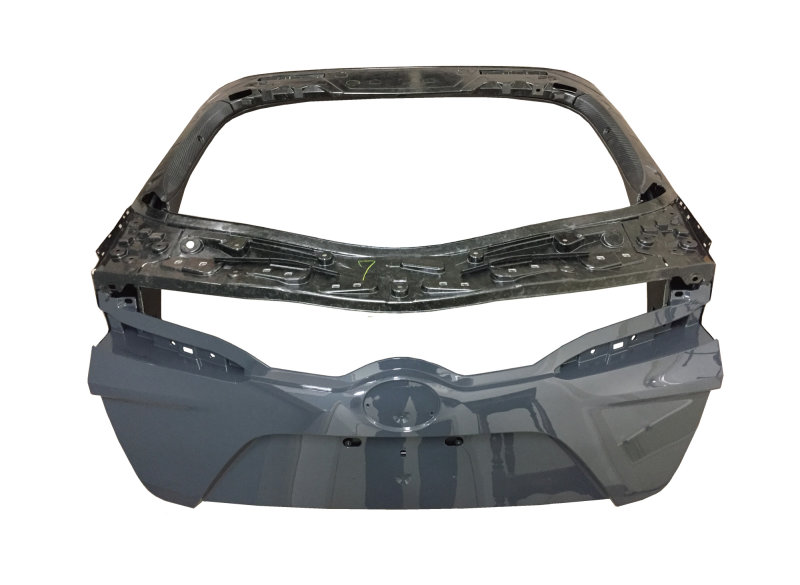
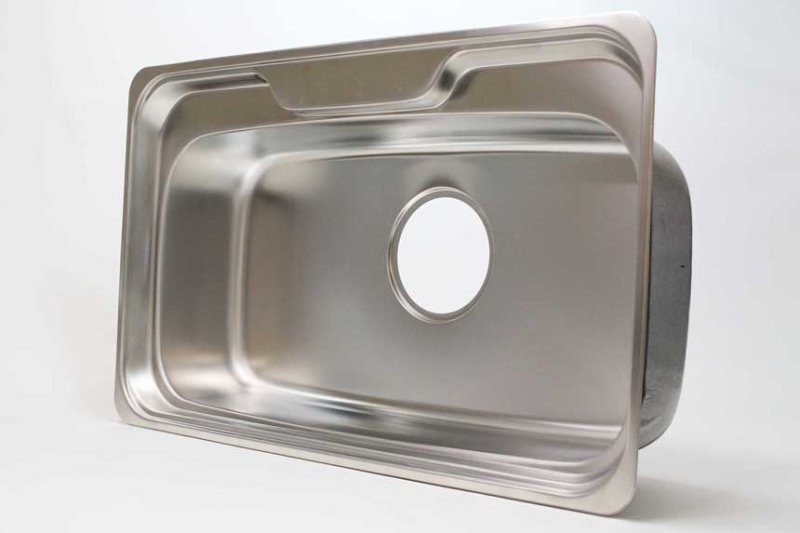
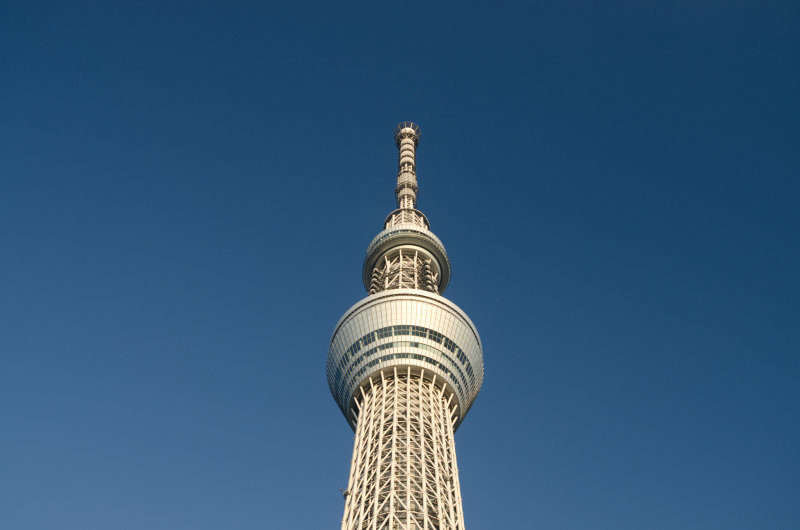
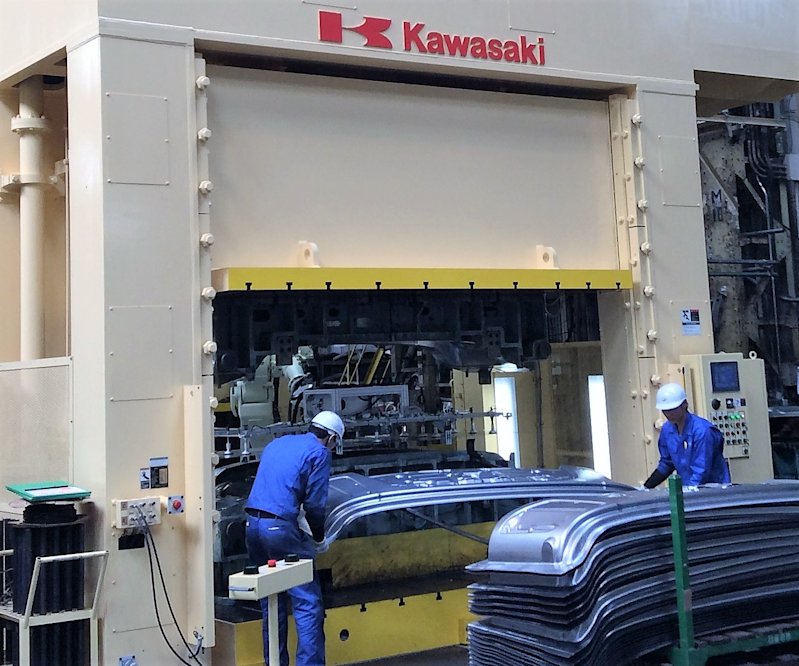
Triple-layered Composition of the Press
The press is triple-layered, with a top (crown), a middle (upright), and a base (bed) which is underground. Each of the four pillars supporting the press has a gigantic 11-meter-long bar that is 250 mm in diameter, joining the three layers to prevent the press from deforming under the strong forces involved.
Hydraulic Unit
The unit’s high-response servo valve precisely controls the oil.
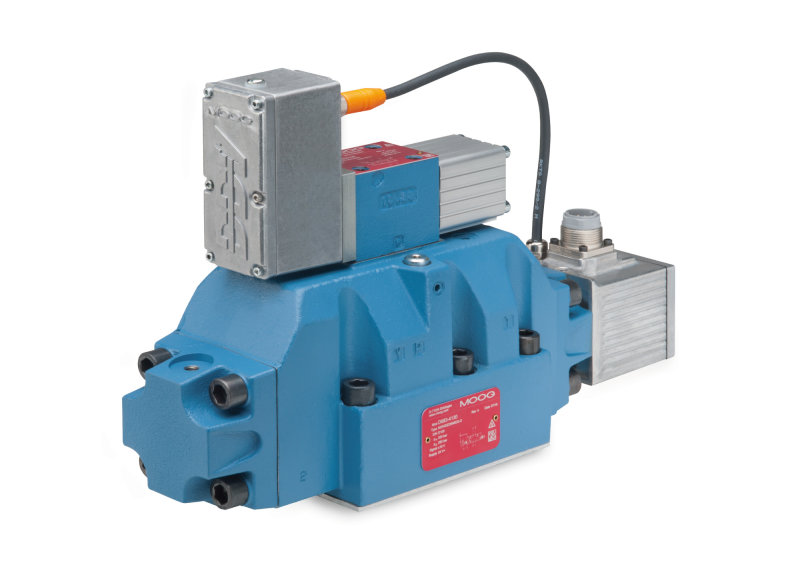
Vacuum Degassed
To improve the texture and prevent burning, any air or gas remaining in the dies is removed through holes in the dies by a vacuum degasser.
Die
The die can be detached from the body of the press.
Next Generation Model
At KHM, development of a “next-generation hybrid hydraulic press,” which offers the benefits of both hydraulic and mechanical presses, is nearing its final phase. When complete, it is expected to lighten the load of oil changes and other maintenance. The company already has an established technology for an electro-hydraulic hybrid system which utilizes both electric motors and hydraulic systems. A prototype is scheduled to be installed at KHM to be used in customer trials.
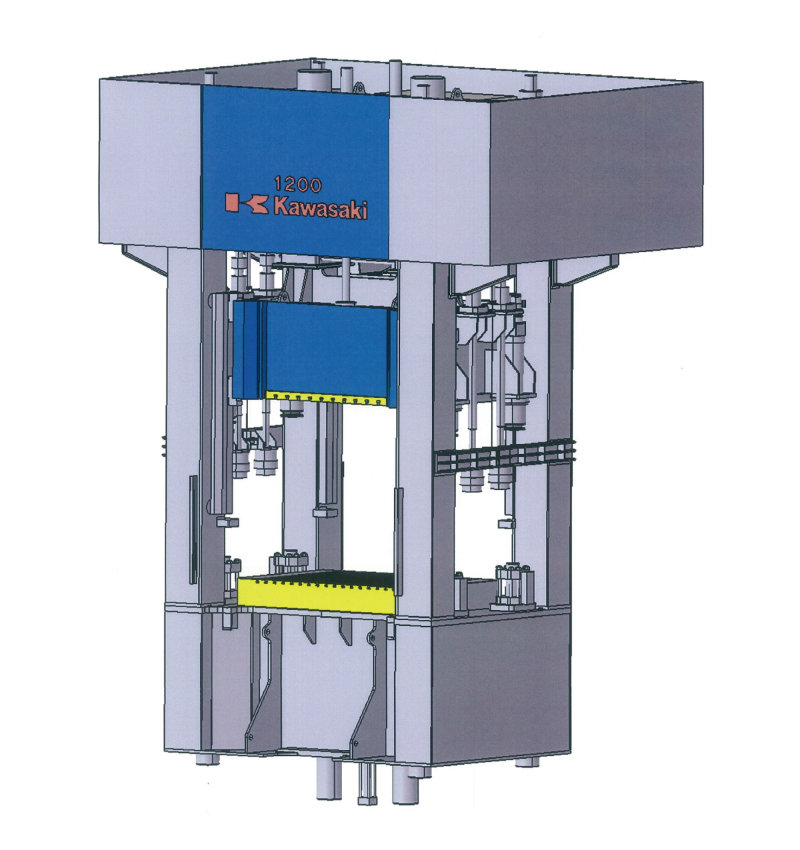

Customer Service Development Division
Engineering Service Department
Kawasaki Hydromechanics Corporation
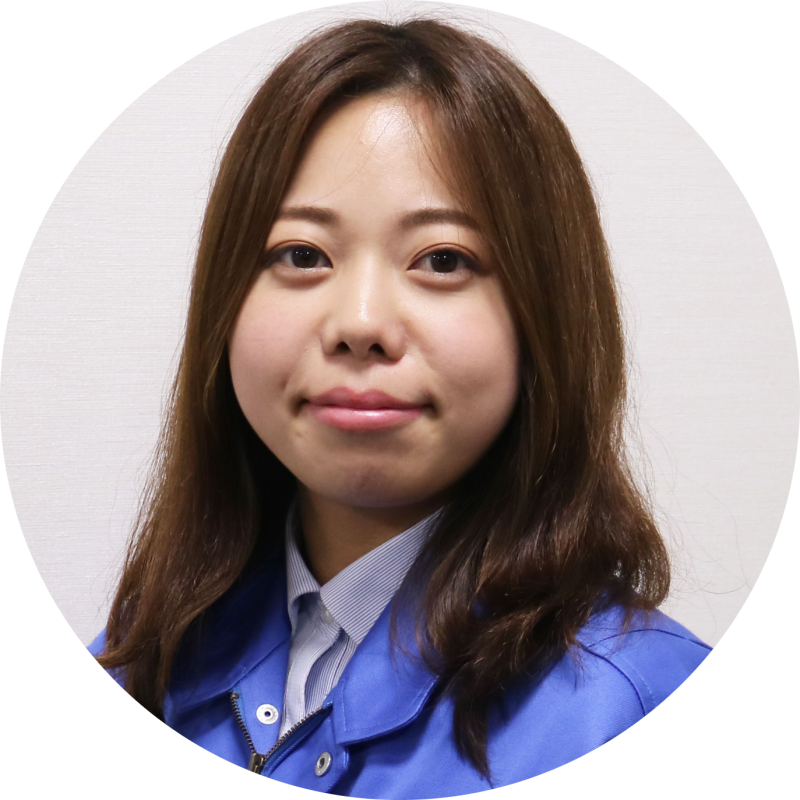
Sales Department
Kawasaki Hydromechanics Corporation