The Power of Heat: Behind-the-Scenes Stars Supporting the Comforts of Everyday Life
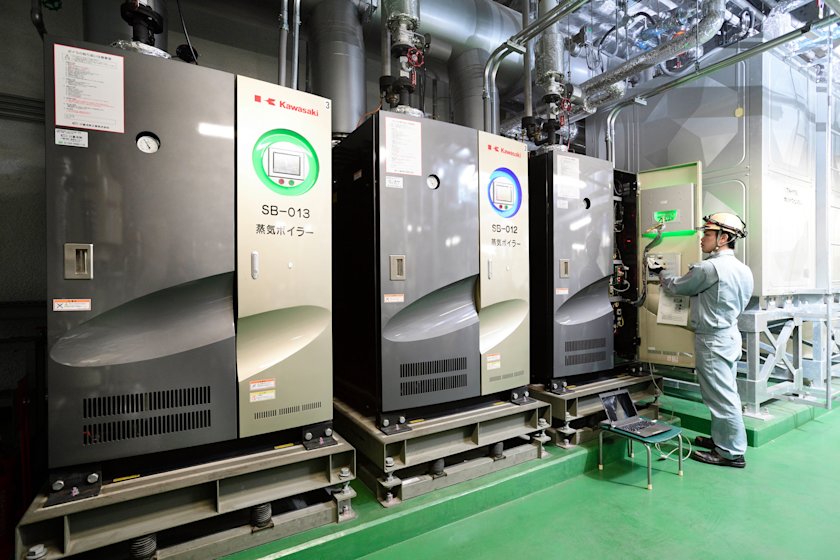
Kawasaki Thermal Engineering Co., Ltd. (KTE) is a pioneer in the manufacturing of boilers and absorption chiller-heaters which support the comforts of our daily lives. This issue of Special Feature focuses on how the “power of heat” is demonstrated in thermal products manufactured by KTE-a heat technology specialist celebrating its 120th anniversary in the boiler business in 2019.
Boilers and Absorption Chiller-Heaters at the Frontline of Life-Saving Work
Osaka Medical College Hospital is located adjacent to Takatsuki-shi Station on the Hankyu Railway Kyoto Line, and is a five-minute walk from Takatsuki Station on the Japan Railway Line. With 29 clinical departments and 14 specialized centers (such as pathology, laboratories, surgery, radiology, etc.), the 1,800-staff hospital serves about 2,000 outpatients per day and has 882 beds. It is positioned as a core community medical institution in the Hokusetsu district (in the northern part of Osaka Prefecture).
In March 2016, a six-story Central Surgery Building was completed at the hospital. One of the largest surgery buildings in western Japan, it has 20 operating rooms, including a robotic surgery room and one for “hybrid” surgeries (a combination of catheter intervention under X-ray guidance and conventional surgical procedures), equipped with coronary and cerebral angiography.
KTE boilers and absorption chiller-heaters are working behind the scenes to support healthcare. Steam generated by the boilers is used in a variety of ways, including sterilization of medical equipment, and the cooling/heating and humidification of the hospital using heat exchangers. Absorption chiller-heaters provide cold and hot water, which are also used for cooling and heating the entire hospital.
Katsuhiko Tsutsumi, head of the Facility Section of the General Administrative Department at Osaka Medical College, which manages all facilities of Osaka Medical College and its hospital, comments, “Boilers and absorption chiller-heaters are energy sources that drive all medical activities at the hospital and are a lifeline for its 24-7 operations. That is why high stability and reliability are expected of them.”
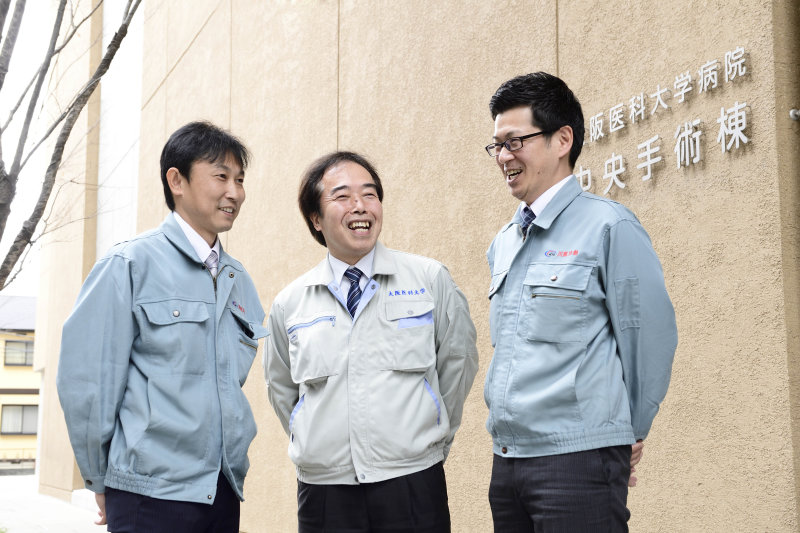
Three units of the KF-A multi-tube once-through boilers are in operation at the hospital. This compact boiler, measuring 110 cm wide, 210 cm high, and 170 cm deep, generates a ton of steam per hour. Also in operation are two Efficio absorption chiller-heater units, each capable of 180-ton refrigeration (equivalent to 265 units of household air-conditioners capable of cooling/heating a room with a floor space of 10 m2).
As for the reason why multi-tube, once-through boilers were originally adopted at the hospital, Tsutsumi says, decisively, “Because of KTE’s high standard of manufacturing and a maintenance system that allows expeditious servicing.” He adds, “Boilers can last longer than 20 years if maintained properly. I support KTE’s approach to product development, which is based on its conviction that products should serve the users for a long time and should never be designed as disposable equipment.”
The speed with which service personnel can respond to equipment malfunctions can affect and sometimes jeopardize the mission of a hospital. On KTE’s quickness, Tsutsumi comments, “Absorption chiller-heaters have been the main products we have had business with at KTE, and their responses to malfunctions have been extremely swift. The company also doesn’t change service personnel frequently, and the same staff are assigned each time, so that we can work as a team with the shared goal of protecting hospital operations. KTE has a sense of mission in supporting the frontline of life-saving interventions. This is the biggest reason why our business relationship has lasted for half a century.”
A History Lasting 120 Years, and the Industry’s Longest Warranty Provided with Confidence
Kisha Seizo Co., Ltd., the predecessor of KTE, was the first private company to manufacture a locomotive in Japan. It then launched a smoke tube boiler in 1899, which means that KTE will be celebrating the 120th anniversary of its boiler business in 2019. Boilers evolved as a family of steam-driven types of equipment which led the Industrial Revolution. Presently, once-through boilers account for 90% of the steam boiler market in Japan.
A once-through boiler has a cylindrical body consisting of many heat-transfer tubes connected together by steel plates called “fins,” which are welded in between the tubes. A burner at the top of the cylindrical body burns the gas to heat the water in the tubes, supplied from the bottom section (water circulates continuously), and the heated water rises upward as steam.
Because the volume of water in the tubes is small and therefore the energy stored in the water is also small, this type of boiler is less likely to explode due to pressure and therefore safer. This type is also characterized by a short steam-start-up time after the boiler is activated. In terms of implementation, it is not mandatory in Japan for entities adopting compact boilers to employ a licensed boiler engineer. In recent years, many entities have chosen to adopt compact once-through boilers instead of one large system, in order to obtain the amount of steam needed.
Because of its simple structure, technologies associated with once-through boilers are considered to be already mature. However, Takahide Yanagida, Senior Manager of KTE’s Boiler Engineering Department, says, “We are pursuing further advancement of these technologies in four areas: firing, heat-exchange, control, and welding.”
For example, by reusing exhaust gas and using fins with high heat-transfer performance, boiler efficiency (the ratio of the energy absorbed by the water and steam in the boiler against total energy input) as high as 98% can be attained. Efficient boiler operations are also attributable to KTE’s control technology, which stabilizes fluctuations in the load and in steam pressure.
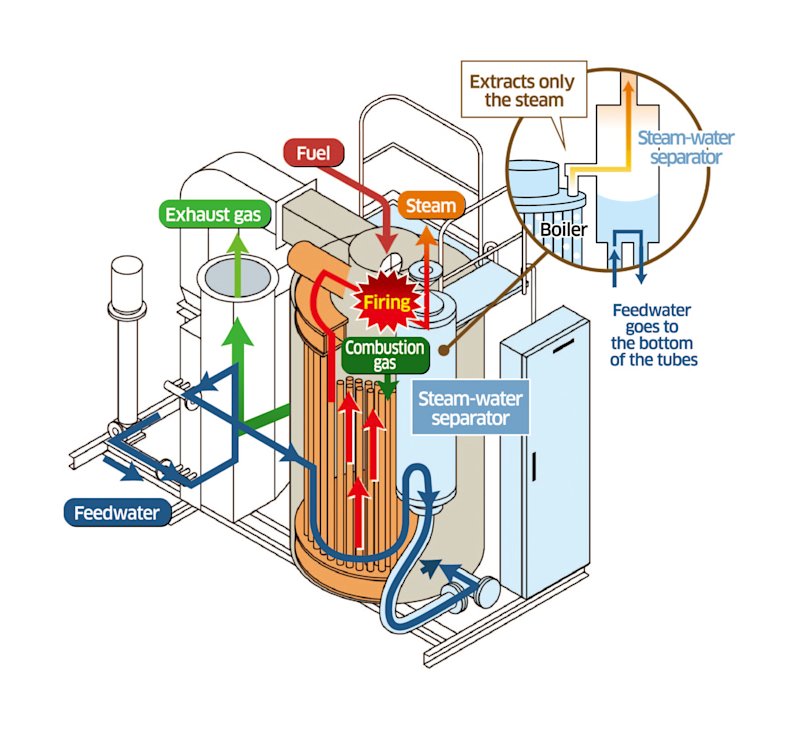
Another component that demonstrates the technological prowess of KTE is a steam-water separator. Once-through boilers manufactured by other companies are designed such that the feedwater is supplied directly to the heat-transfer tubes. KTE’s model, however, heats the feedwater first, using waste heat from the boiler, and then guides the water through the steam-water separator before it is supplied to the tubes.
Yanagida comments, “If the feedwater is supplied directly to the heat transfer tubes, warm and cold waters are mixed abruptly inside the tube, causing thermal shock and releasing dissolved oxygen into the water, which results in increased corrosion of the tubes. However, by having the feedwater pass through the steam-water separator in order to keep the water level at consistent level, thermal shock can be avoided, minimizing corrosion of the tubes and fluctuations in steam pressure. This may not appear to be an eye-opening design, but many such ingenuities are packed into the boilers to prolong their lives.”
KTE provides a 15-year warranty with its boilers ― the longest in the Japanese market. (Certain conditions apply, such as establishing an annual maintenance contract with KTE.) Yanagida says, “Offering the longest warranty (in the market) reflects our confidence in our products.”
How a KTE Boiler Is Made
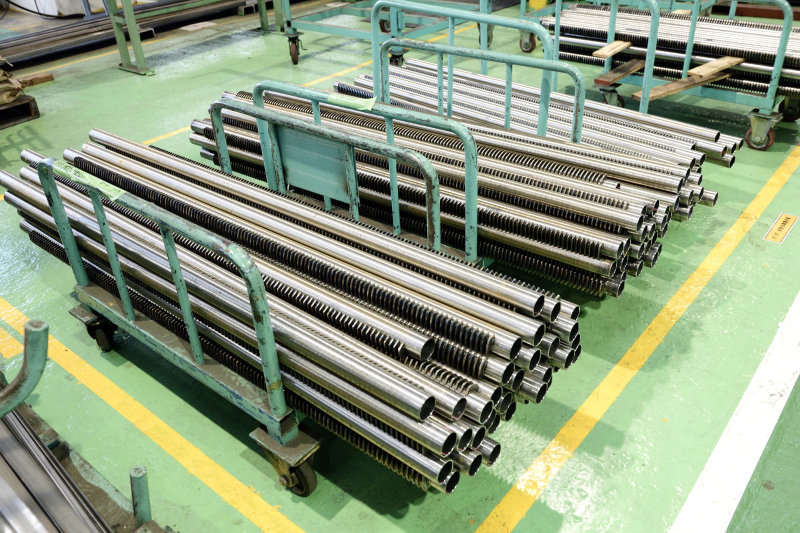
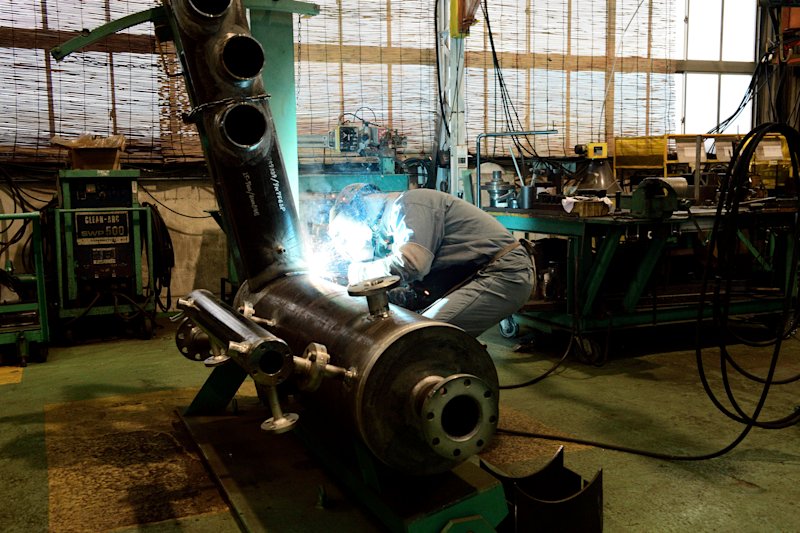
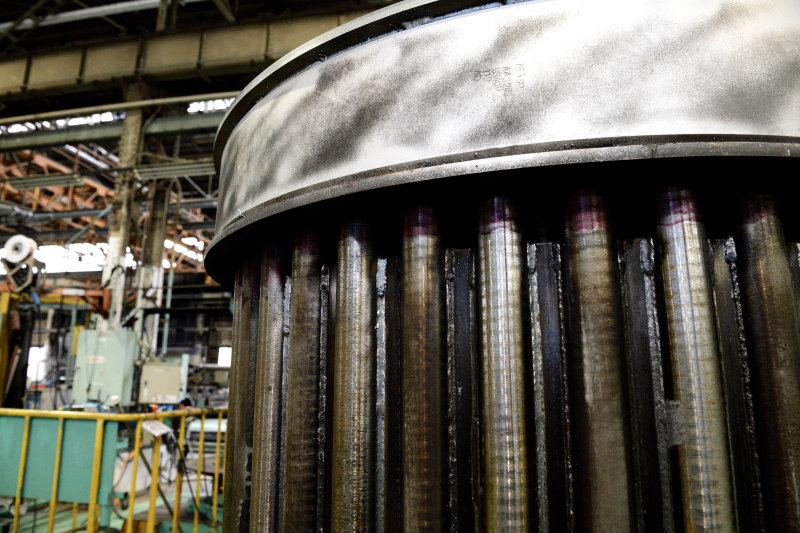
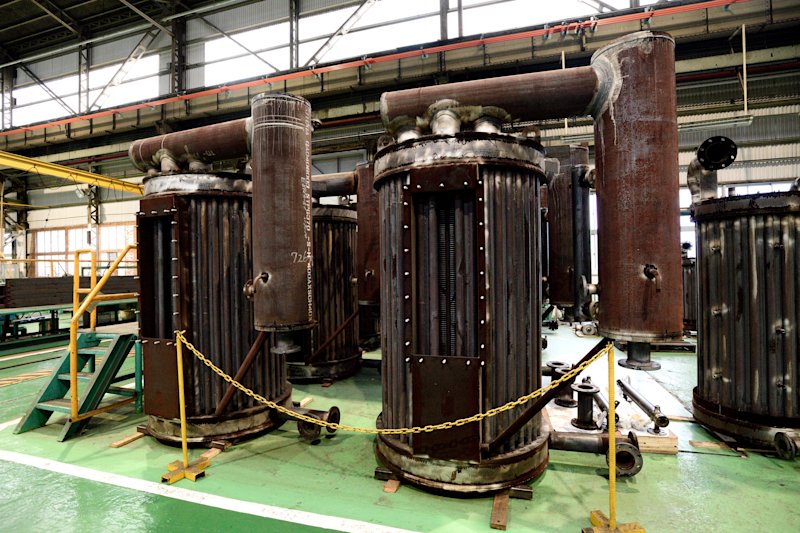
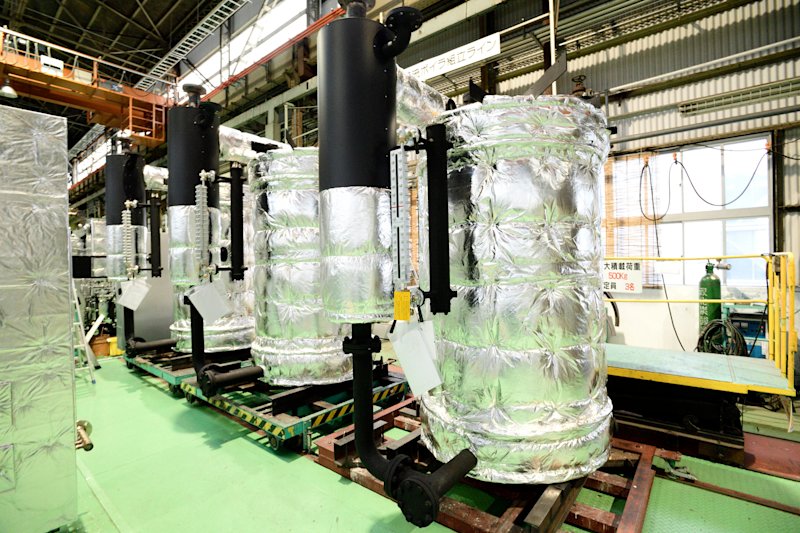
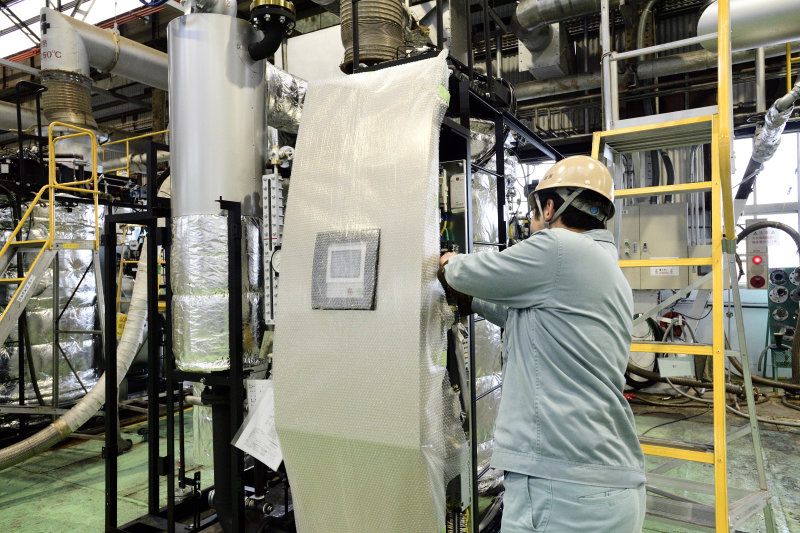
Developer of a Number of World’s Firsts; One of the Largest Market Share Holders for Absorption Chiller-Heaters in Japan
In recent years, more compact and highly efficient absorption chiller-heaters have been developed. An absorption chiller-heater is a piece of equipment used to cool or heat, using the principle of heat extraction through water evaporation―the same mechanism as uchimizu, the Japanese custom of sprinkling water in streets and gardens to cool the surrounding area. Water is used in this system instead of fluorocarbons with high global warming potential, or chlorofluorocarbon substitutes, so as to achieve a large, centralized, eco-friendly heating and cooling system. KTE successfully commercialized the double-effect direct-fired absorption chiller-heater in 1968, and the triple-effect direct-fired absorption chiller-heater in 2005―both of which were first in the world of their kind.
Regarding the features of this equipment, Koichi Someya, Senior Manager of KTE’s Research & Development Department, explains, “The triple-effect absorption chiller-heater achieves a COP*1 of 1.74. Compared to the double-effect models, it achieves 35% fewer carbon dioxide emissions and reduces annual running cost by about 3.5 million yen. For its high-temperature regenerator, the same cylindrical body design as the once-through boiler was adopted, which was achievable by KTE alone because we are in possession of both boiler and absorption technologies.”
Another feature contributing to the advantages of absorption chiller-heater is the versatility that allows the use of diverse heat sources for its regeneration process, including gas, oil, waste heat from the co-generation system, cooling water heated by the large engines of the same system, etc. Moreover, KTE’s Efficio absorption chiller-heater series includes a model which uses gas or oil interchangeably as an energy source, making it a preferred model of medical institutions and other entities in need of such versatility. On the significance of this feature, Someya comments, “Operations at a hospital designated as a ‘Disaster Relief Core Hospital,’ which serves as a medical hub in the event of large-scale disasters, will not be interrupted if it has the option of switching to oil if the gas supply is shut down. This means that this model could be positioned as a critical component of business continuity planning.”
*1 “Coefficient of performance” (COP) denotes the energy consumption efficiency of refrigerating equipment such as a freezer. It is the ratio of the cooling or heating capacity of the system divided by the fuel consumption. The higher the ratio, the more efficient the energy consumption under the rated conditions.
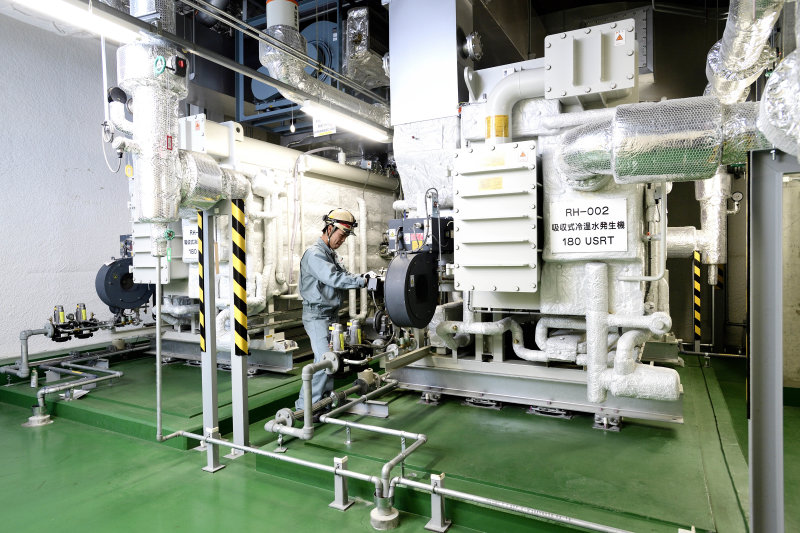
Kawasaki holds a 25% market share in Japan (in terms of equipment capacity), making it one of the largest market share holders in the country’s absorption chiller-heater market. This is attributable to KTE’s capabilities for developing a number of the world’s first technologies, and to its maintenance system and other services accommodating users’ diverse needs.
The WILLHEAT Compact Once-Through Boiler Was Launched to Meet Diverse Customer Needs
In 2000, KTE launched the Ifrit series (large once-through boilers), and 16 years later, the WILLHEAT series made its debut to better accommodate diverse customer needs.
In April 2018, the Boiler Development Division ― dedicated to developing next-generation once-through boilers ― was established to strengthen KTE’s product offerings geared toward Southeast Asian markets and other regions where growth in boiler demand is seen. The division is focused especially on selling boilers with maintenance contracts and supplies of corrosion-prevention chemicals. Presently, the division is based in Malaysia, at Kawasaki Gas Turbine Asia Sdn. Bhd. (KGA). In addition, KTE plans to establish a subsidiary in Thailand in the future to bolster its marketing capabilities. Yanagida adds, “We are hoping to develop compact boilers with a maximum steam output that is 1.5 times greater than current models. We will be exploring improved water flow, flow rate, circulation, and other functions to improve overall efficiency.”
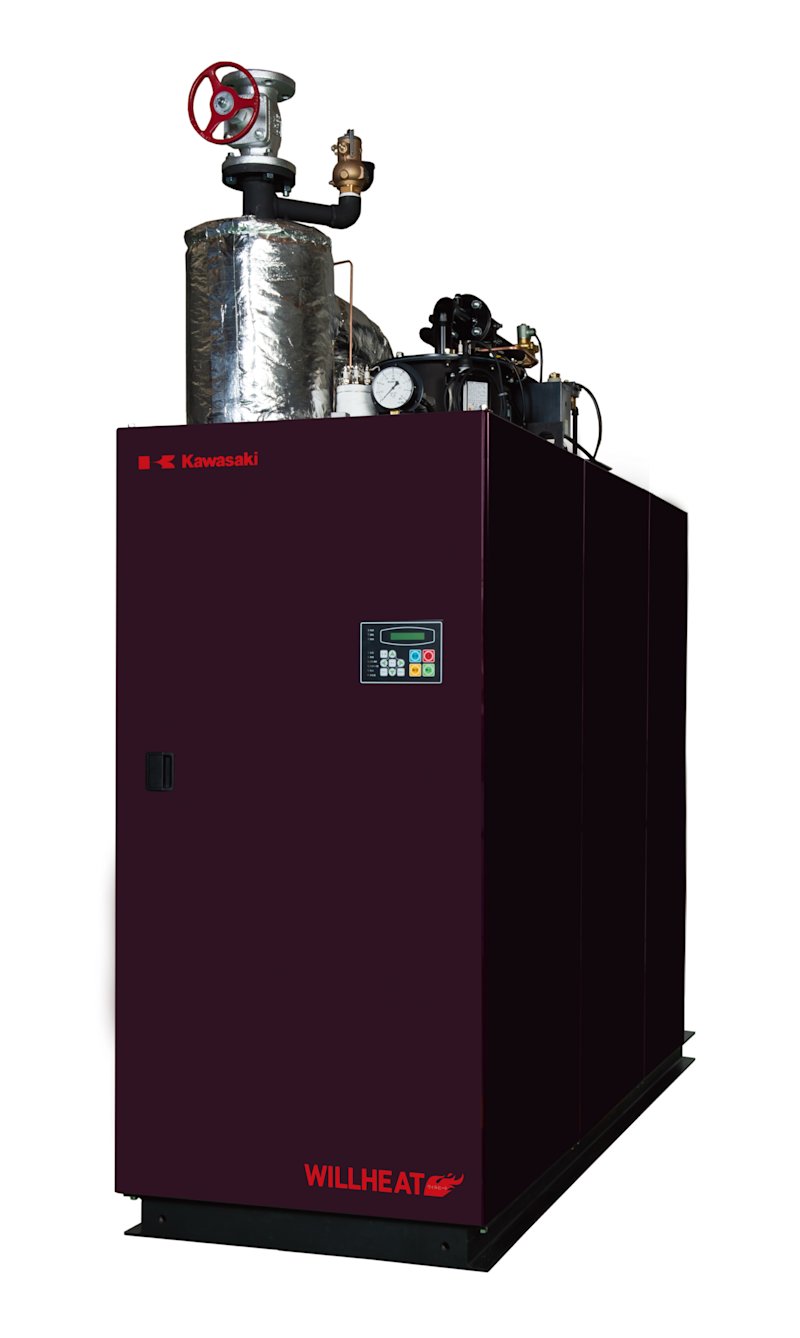
Absorption chiller-heaters are also the subject of KTE’s improvement efforts. These include enhancement of operating procedures and compatibility with various heat sources. Expounding on KTE’s approach, Someya explains, “Our technological enhancements are focused on how we can flexibly accommodate customer needs, such as the leveling of running loads that change seasonally, which is essentially an improvement on so-called ‘seasonal efficiency,’ or the development of a technology to utilize low-temperature waste heat of 60 degrees Celsius or lower.”
Maximizing the potential of the power of heat in order to realize a more comfortable present and an optimal future―that is what KTE is pursuing. Its products may not be in the foreground of attention, but they certainly support our lives behind the scenes.
Verification Testing for Hydrogen-Fired Once-Through Boilers Begins
In March 2018, KTE commenced verification testing for once-through boilers which utilize hydrogen as fuel. Although hydrogen-based energy is expected to play a critical role in realizing an energy-efficient society, there are many challenges to resolve. Ironworks and chemical plants, for example, have been challenged to utilize effectively the hydrogen byproduct which is generated in the production process. Verifying the functioning of the hydrogen-fired once-through boiler is KTE’s endeavor to achieve effective use of eco-friendly hydrogen resources, and thereby resolve various pressing environmental issues.
Because the flame temperature of hydrogen is high, burning it results in high emissions of nitrogen oxide (NOx). In the past, reduction of NOx emissions during hydrogen burning required the use of water or steam. For the verification test, however, KTE developed a technology to achieve NOx emission cuts not involving water or steam, using a newly-developed dry-type burner. This testing is an opportunity to verify the viability of the technology, which KTE plans to apply to the boiler and commercialize it in 2019, in cooperation with the Corporate Technology Division of Kawasaki Heavy Industries.
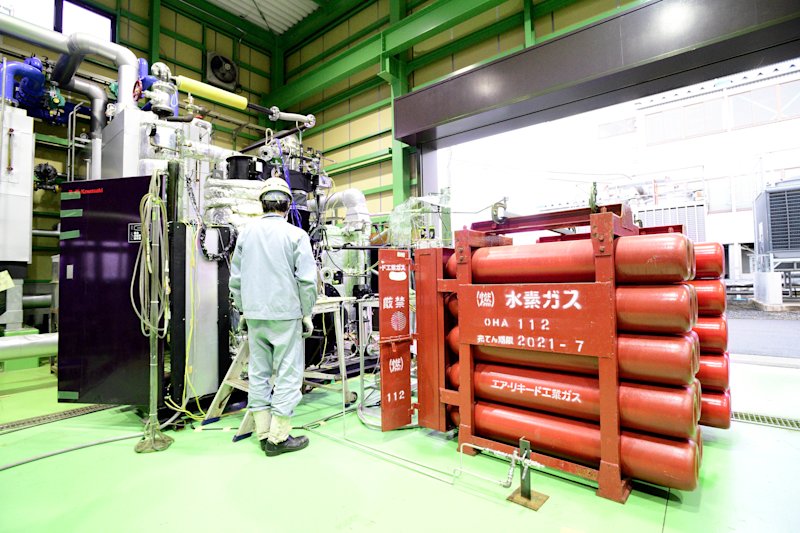
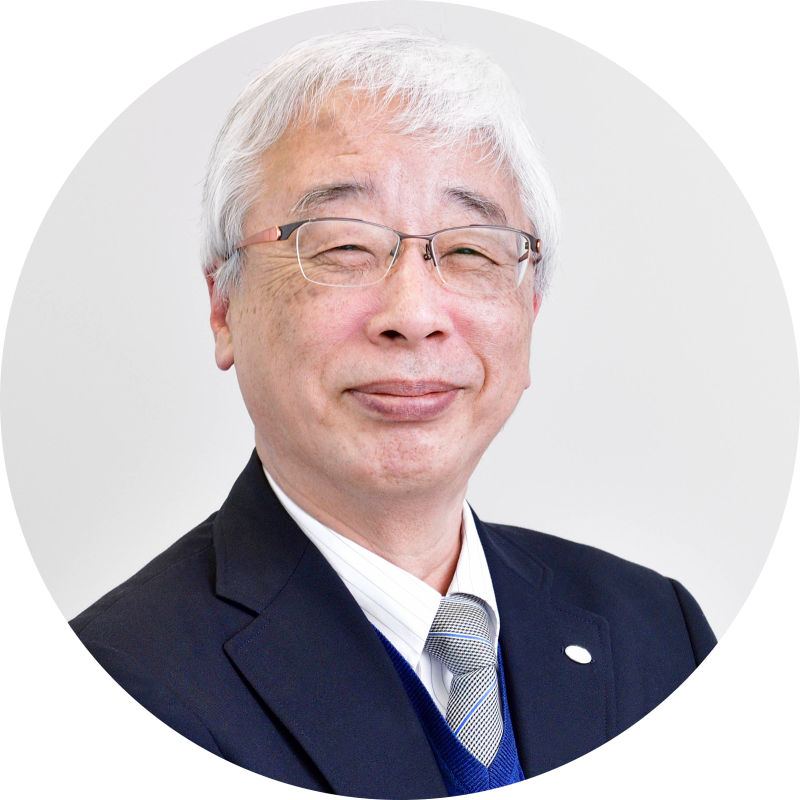
Kawasaki Thermal Engineering, Co., Ltd.
Our Ever-Evolving Endeavor as “Heat Specialists”
In 2019, KTE will be marking 120 years in the boiler business, during which time we also developed the world’s first double-effect and triple-effect absorption chiller-heaters. In both sectors, KTE has been serving as a “heat specialist,” providing superior thermal technology.
In a network of three offices and 13 branches dedicated to product maintenance, one-third of the 500-member KTE team is working hard to ensure uninterrupted operation of their products at customer sites. We are also upgrading our remote monitoring system called “Tele-Mente-Advance,” through which our monitoring center collects operating data and evaluates equipment status in order to support optimal operations. The next version of this system currently being developed is compatible with the IoT (Internet of Things) platform being developed by Kawasaki Heavy Industries (KHI).
With respect to boilers, after we launched the WILLHEAT compact once-through boiler in 2016, we received a great deal of feedback from our customers, expressing high expectations for our compact products. However, we acknowledge that there are many markets we have not been able to tap into which could benefit from equipment like WILLHEAT. For the Japanese market, we offer the industry’s longest 15-year warranty, in a package deal including the equipment, a maintenance contract, and supplies of anti-corrosion chemicals, so as to ensure that our products operate safely for a long time.
KTE is also bolstering its efforts to market waste heat boilers to be used in co-generation systems, utilizing the waste heat from gas turbines and gas engines manufactured by KHI, in order to capitalize further on synergy between the two companies.
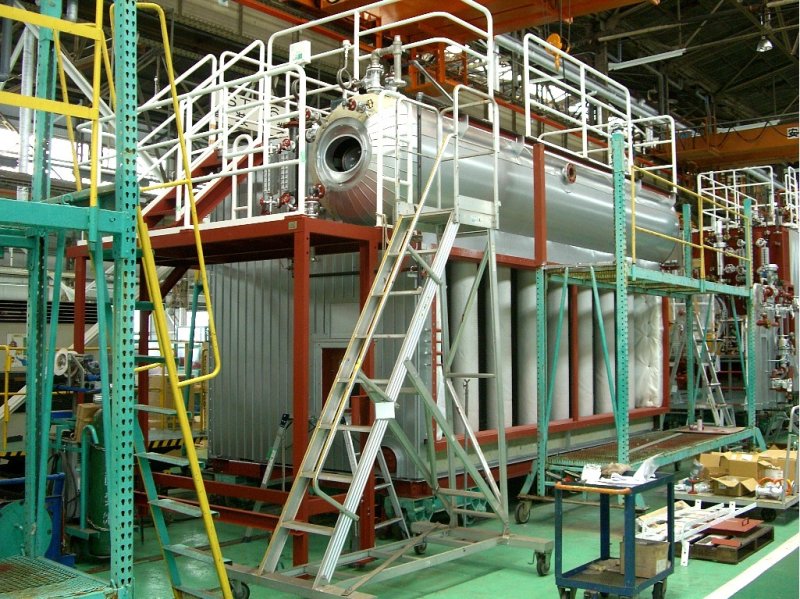
Regarding absorption chiller-heaters, we will be exploring the application of underutilized waste heat in order to improve the products’ versatility in accommodating diverse heat sources. Equipment which can be driven by multiple heat sources is an essential component of business continuity in the event of major disasters, and offers benefits that are not achievable by electricity-driven heating/cooling systems.
KTE plans to focus more on overseas markets, especially the Southeast Asian markets, where package deals inclusive of a maintenance contract are widely accepted. By collaborating with KHI and Kawasaki Gas Turbine Asia, we plan to implement aggressive marketing for both the once-through boilers and waste heat boilers.
Although the technologies for boilers and absorption chiller-heaters are considered to be in the mature stage, we at KTE, as heat specialists, are committed to advancing these technologies further, based on our long-standing expertise and the confidence our customers have placed in our products as “equipment that lasts for a long time.”
* On June 28, 2018, Mr. Noumi's position changed. He is now adviser to KTE
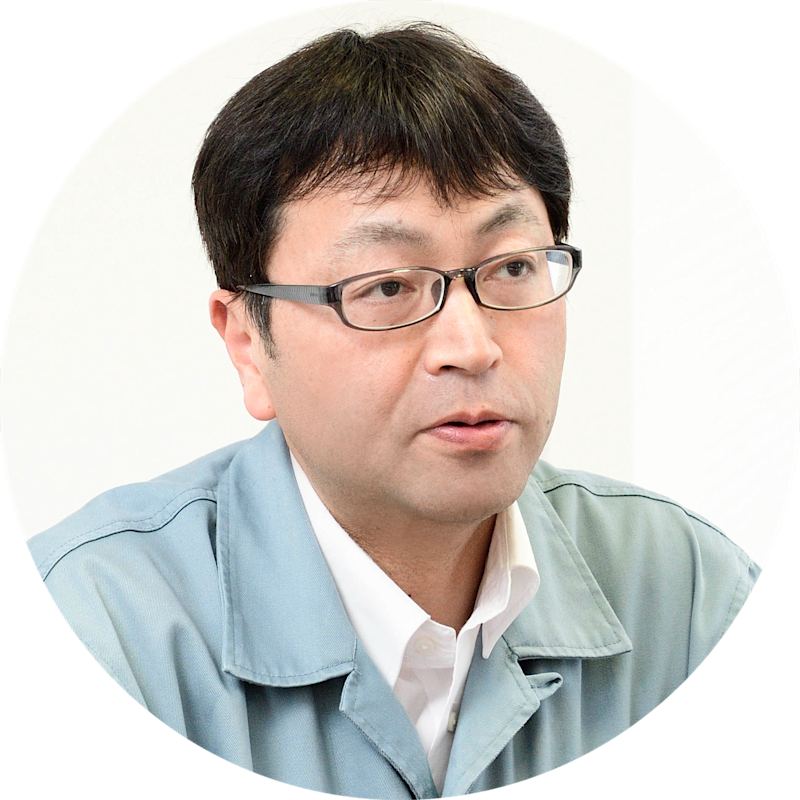
Boiler Engineering Department Engineering Office
Kawasaki Thermal Engineering Co., Ltd.
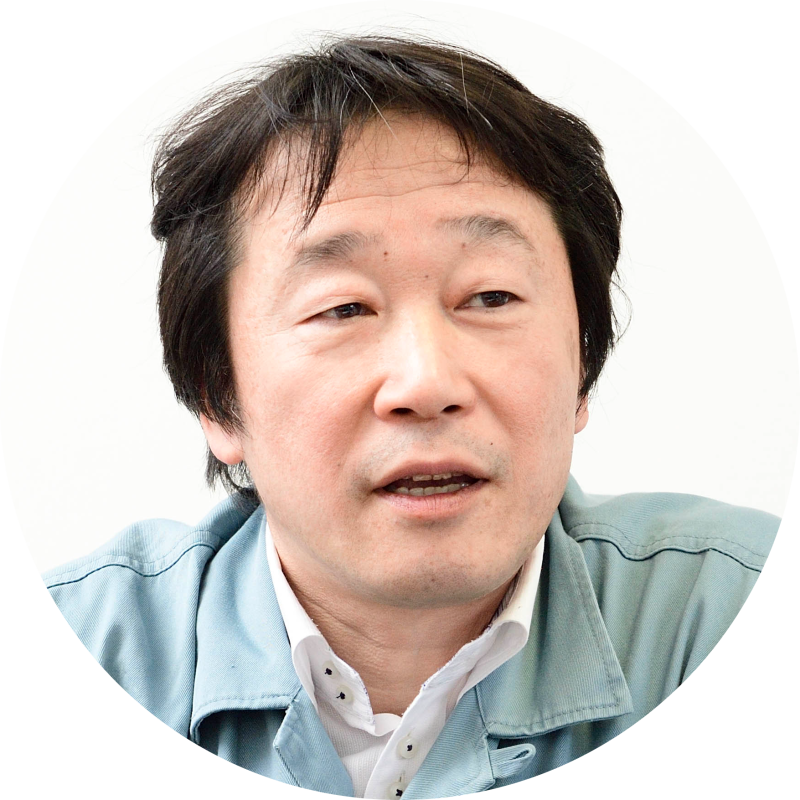
Research & Development Department
Kawasaki Thermal Engineering Co., Ltd.