Material Handling Systems Stacker-Reclaimer
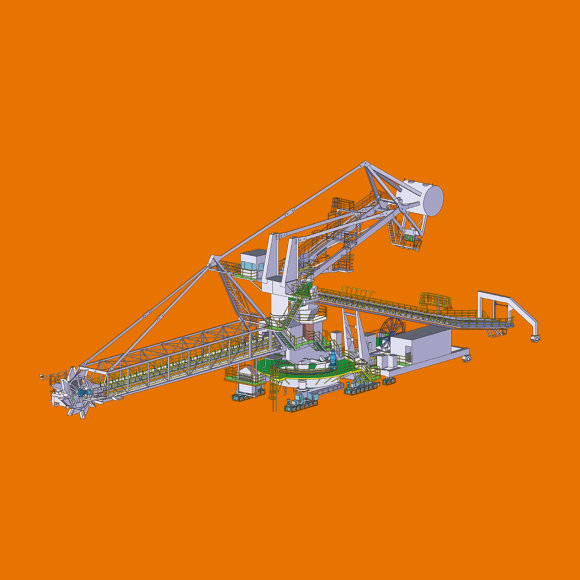
The material handling system stacks coal, iron ore, fertilizer, and other bulk materials into piles or reclaims and moves them to another location. A stacker-reclaimer is a system equipped with both stacking and reclaiming functions. Let’s learn some pieces of trivia about the many Kawasaki skills involved in this field.
System for Stacking and Reclaiming Bulk Materials
One mission of a material handling system is to stack coal, iron ore, fertilizer, and other bulk materials in piles, or to reclaim and move them from storage to another location. The operation of building a pile is called “stacking,” and removing and relocating operations are called “reclaiming.” Stackers and reclaimers are specialized for their respective operations, but a stacker-reclaimer is capable of handling both.
This system is indispensable at ironworks, power plants, ports, and mines. Kawasaki has been developing stackers, reclaimers, as well as stacker-reclaimers, based on its technologies for gantry cranes which load containers to ships and for ship loaders that load bulk materials onto ships.
A system of the size shown upper right is capable of stacking 2,000 tons of materials per hour, but there are also models with a 5,000 tons per hour capacity.
These 5,000-ton models require conveyor belts that are nearly two meters wide. Since installation sites for these systems differ in size, and have varied workload and speed requirements, they are all made-to-order.
There are only a few companies in Japan that are capable of manufacturing such devices, including Kawasaki, and therefore our material handling business carries a socially important responsibility. This also suggests that manufacturers which failed to meet the daunting requirements of customers have already dropped out of the competition. Because this system should last for at least 30 years, manufacturers must have sophisticated design and development expertise, including selection of the correct parts and accessories.
This is a system that operates behind the scenes, but is packed with technologies that only a comprehensive manufacturer like Kawasaki can offer.
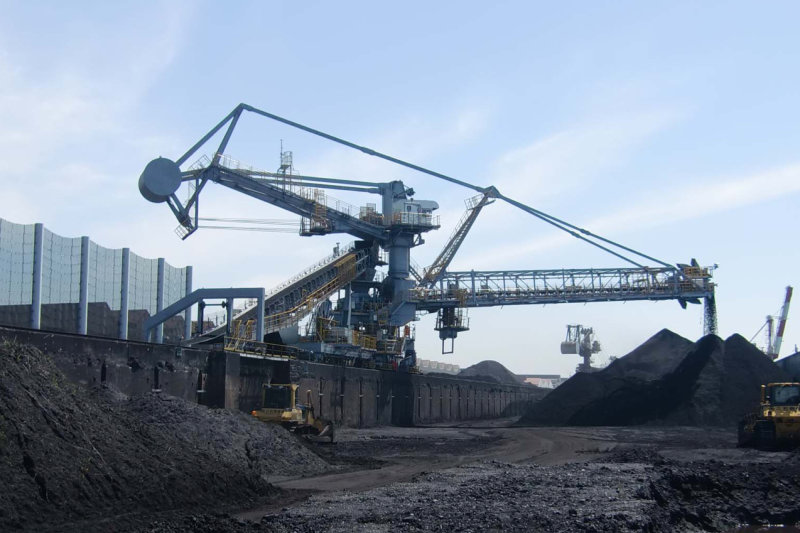
Reclaiming capacity: 700 tons per hour Stacking capacity: 2,000 tons per hour Length: 70 m (of which the boom accounts for 40 m)
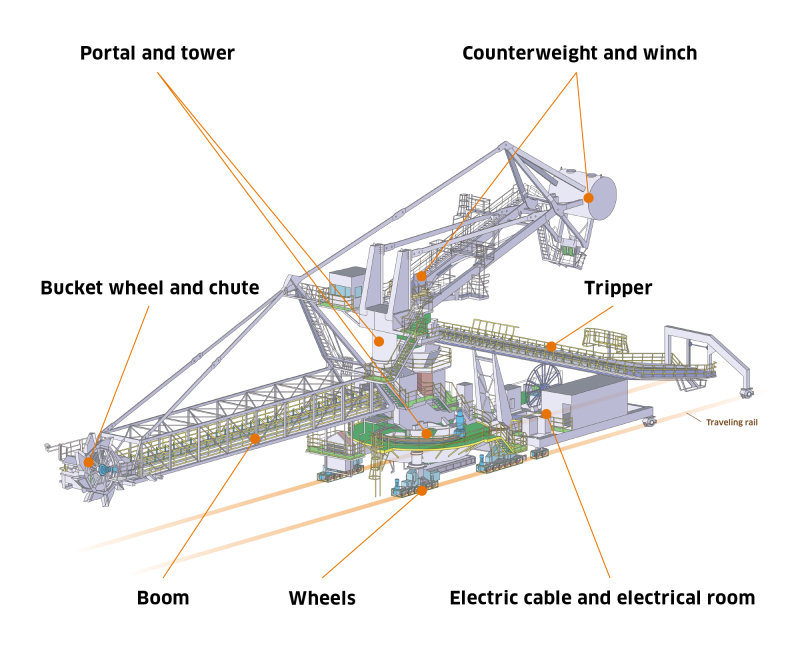
Meeting Diverse Customer Needs with Conveyance Systems Underpinned by Outstanding Developmental Capabilities
Fully made-to- order to accommodate any need
Kawasaki has been developing a vast array of conveyance equipment in addition to stackers, reclaimers, and stacker-reclaimers that offer features of both. There is also a scraper-reclaimer which reclaims material from a pile using scrapers mounted on a circulating conveyor, and a twin-boom type which works even more efficiently by having two booms with scrapers. Kawasaki’s product portfolio also includes a ship loader (right photo) that loads bulk materials via conveyor onto a carrier ship, and a spreader (lower left photo) which reclaims vast areas by spreading sand.
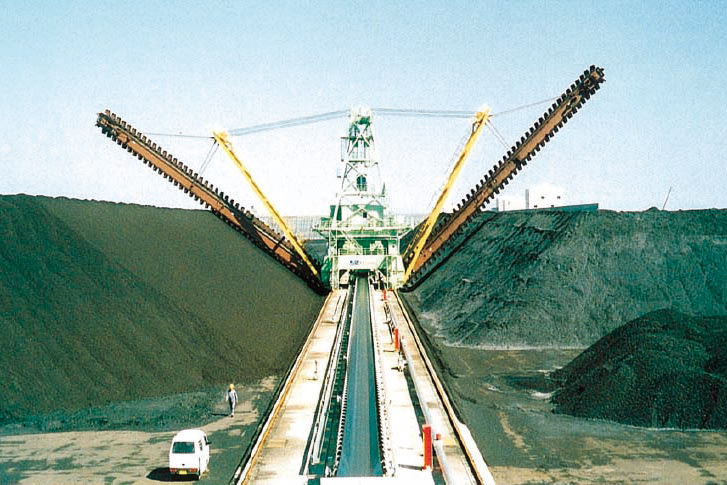
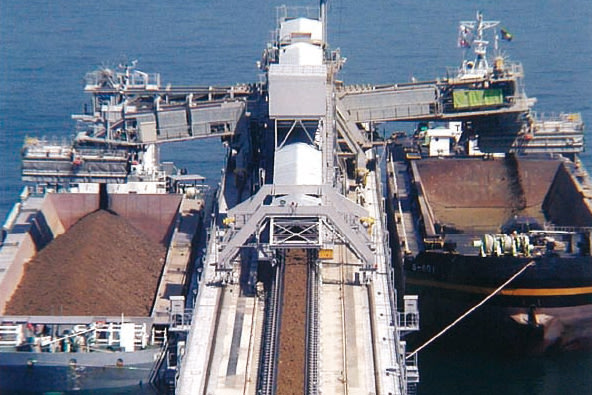
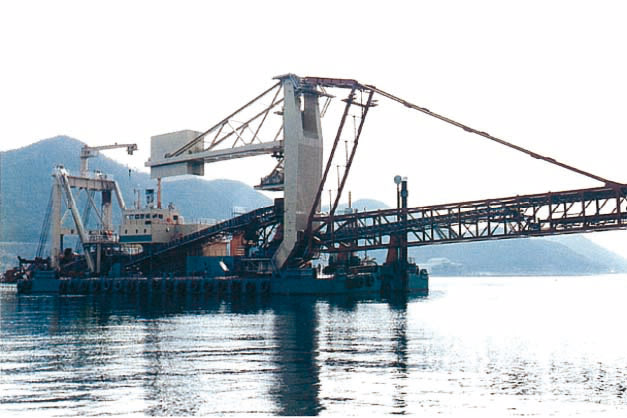
Manpower-Saving Automated Equipment
Kawasaki has realized automated operations to save manpower involved in stacking and reclaiming. Accurate detection of pile edges during reclaiming operations to enable the equipment to operate in response to its changes is key technology for automating operations. Using ultrasonic sensors, Kawasaki developed a technology for detecting pile edges, and moreover, for determining the location where reclaiming should begin.
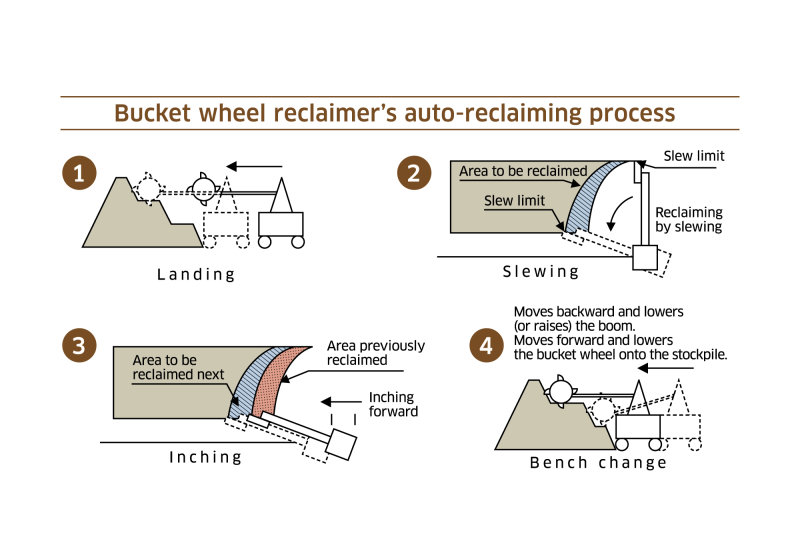
Wheels
The equipment rests on 24 motorized wheels (two sets of six wheels on both sides). Some larger models have 108 wheels.
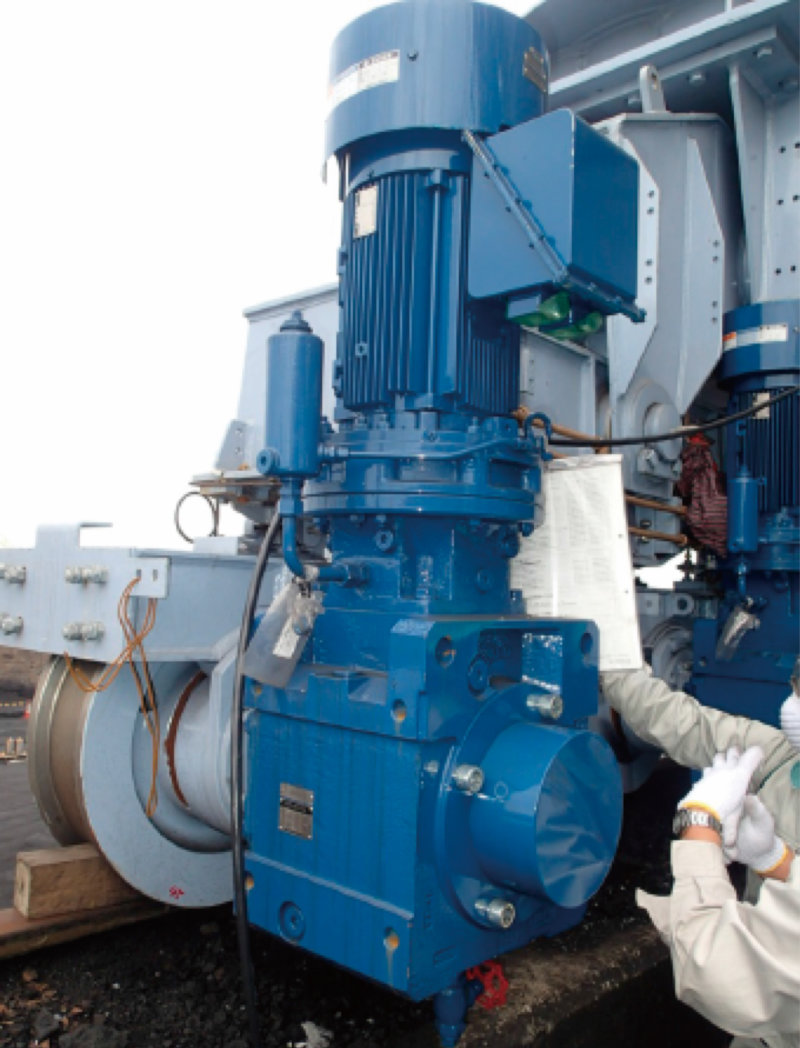
Ellectric cable and electrical room
This system is electrically-powered. The power source is centrally located in between the two rails on which the equipment travels. When it moves forward or backward, the electric cable alternately stretches out or rolls up. An electrical room is in place to control the motors for moving and slewing operations, and to control the winch.
Bucket wheel and chute
In reclaiming operations, the bucket disposed at the boom end digs up material and drops it onto a slanted board (“chute”) designed for material to slide down to the conveyor. In this system, eight buckets are attached to a wheel six meters in diameter. In a single rotation, the bucket wheel is estimated to dig up two tons of material.
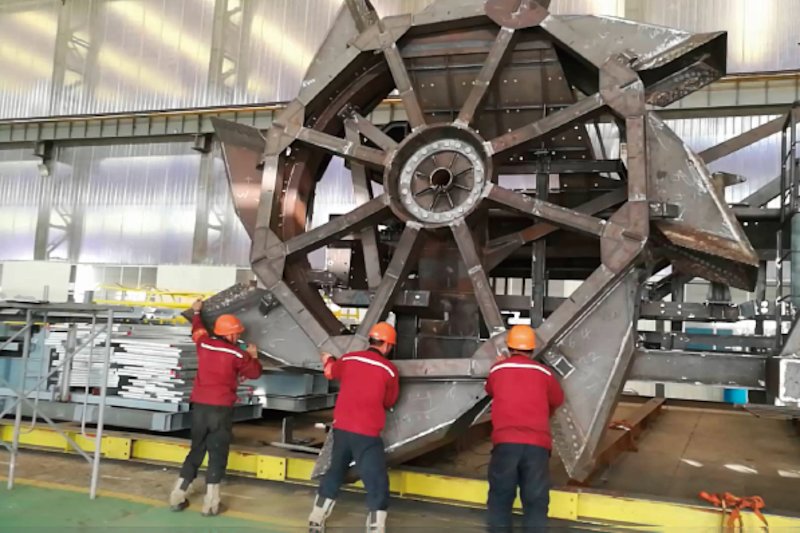
Boom
Material flows by way of the boom - the “main street” of the system - for stacking and reclaiming. The conveyor inside the square framework travels in a loop in order to transport material. For reclaiming, the system drops material from the center of the portal onto the conveyor that runs on the ground between two rails.
The boom swings in a left/right arc of ±145°, with an upward/downward range of ±15°.
Counterweight and winch
There are two ways to keep the boom in place and to raise/lower it: one is to suspend the boom with a rope and move it using an electric winch; and another is to install a luffing cylinder at the base of the boom. To control the boom’s movement, a huge counterweight is installed. The counterweight (a concrete-filled can) weighs 100 tons.
Portal and tower
A cylinder located at the lower part of the equipment is called the “portal.” It holds the entire unit and serves as the “pivot.” The portal has two motors that allow it to swing the boom in an arc of ±145°. The tower on top of the portal serves as an axis to maintain balance among the components of the system. The winch and the operation room are on the tower.
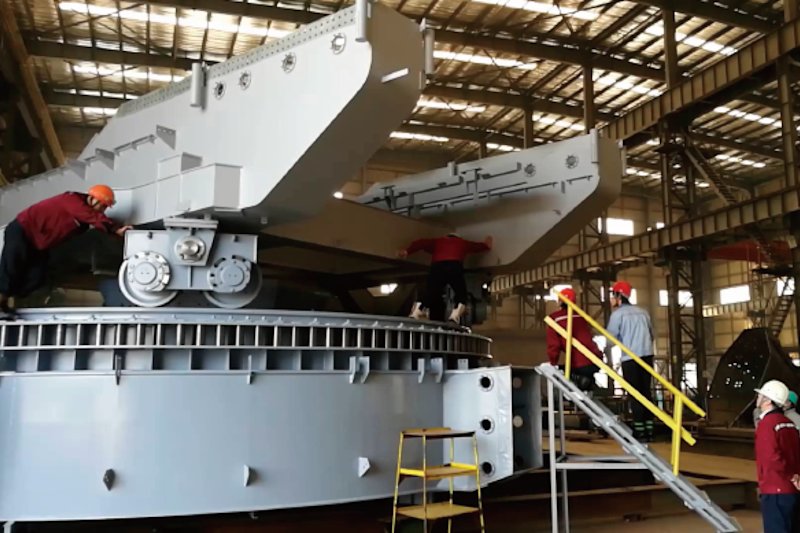
Tripper
The tripper conveys materials brought from another location up to the boom for stacking. Some trippers are equipped with derricks to raise/lower them.
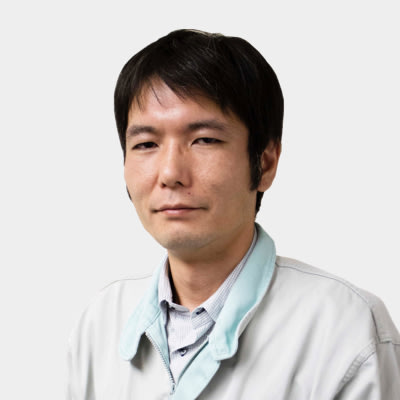
Section 1
Materials Handling Department
Industrial Plant Engineering Division
Plant & Infrastructure Company
Kawasaki Heavy Industries, Ltd.
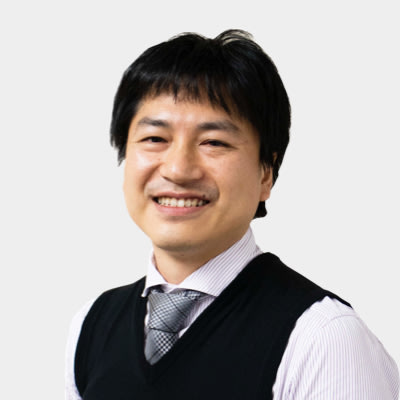
Section 1
Materials Handling Department
Industrial Plant Engineering Division
Plant & Infrastructure Company
Kawasaki Heavy Industries, Ltd.