Waste-to-Energy Power Generation: Common Sense of the New Era Overview of Japanese High-Tech Waste Treatment Facilities
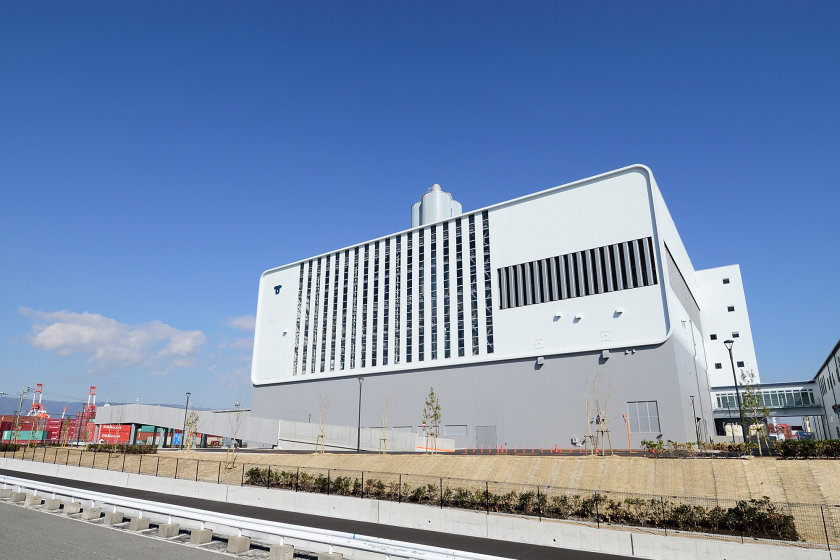
Port Island, located in Kobe City in Hyogo Prefecture, was constructed in 1981 as Japan’s first artificial island with urban functions. This waterfront city between Osaka Bay offers abundant gifts and a traditional aesthetic port town with a gigantic white building with a look of perfect cleanliness. What is this mysterious construction surrounded by rich greenery and two parks? Is it the office building of a leading tech company accommodating talented engineers or a development base for next-generation medical care? Actually, this is a must-visit waste treatment facility that has attracted national attention from an energy-creation point of view.
Energy Supplier in the Event of a Disaster
As alchemy tried to transmute lead into gold, the efforts to transform waste into energy can be called the “eco-alchemy” of the 21st century. In the waste-to-energy process, the heat generated from burning waste produces the steam that rotates turbines, and the rotating turbines produce electricity just as in thermal and hydroelectric power generation facilities. With this technology, refuse is not something to be disposed of but serves as a resource.
Incineration plants equal to energy producers. The Minatojima Clean Center on the southeast side of Port Island materialized this idea on April 1, 2017. The design of the façade of the white building is a lattice pattern created by the outer walls and the inner skeletal structure, which looks like a laptop in landscape orientation––a design suitably called a techno-display. The three installed incinerators are capable of processing 600 tons of waste per day, and the heat from burning the waste generates up to 15,200 kW of electricity. This volume of electricity is sufficient to power 50,000 typical homes in Nagata Ward of Kobe. The energy obtained from burning the waste is used by the Center itself, and the excess is sold to electricity operators. Moreover, the Center was designed as a resilient construction equipped with a gas turbine power generation facility for emergency use to serve as an energy source in the event of a disaster.
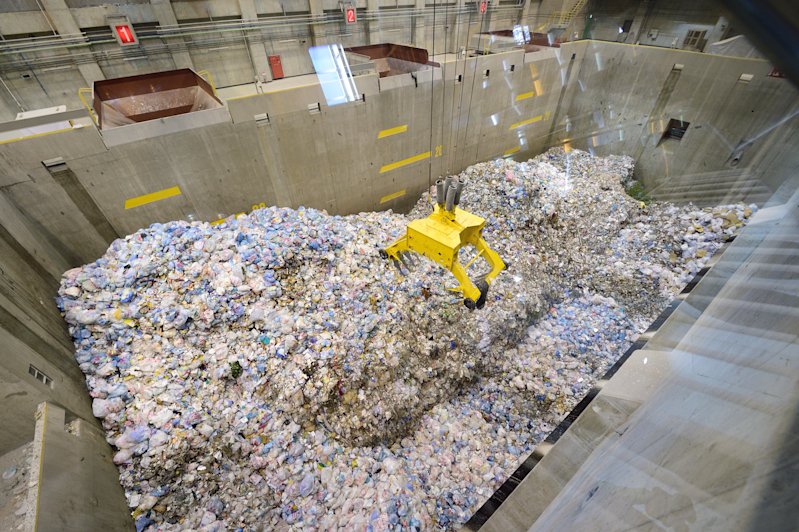
There are many examples of using excess heat from the thermal energy of waste incineration furnaces to warm facilities, as well as swimming pools and tropical greenhouse gardens in the neighborhood. In contrast, the Minatojima Clean Center uses the steam created during incineration to rotate a turbine to produce electricity the same as thermal power generation. This is an evolved form of thermal recycling since household waste is used in its own right as recycling fuel to obtain electricity.
The Center’s power generation efficiency stands at 20.8%, which is significantly higher than the national average of 13.74% for waste-to-energy power plants. This performance is at the industry's top tier and is backed by the Kawasaki Advanced Stoker System created by Kawasaki. This state-of-the-art waste incineration system was developed by a gigantic multidisciplinary engineering company through the integration of its prime technologies.
Highly Efficient, Clean, and Tough
Let’s review the mechanism of waste incinerators. There are three major incineration systems: stoker, fluidized bed, and gasification. The most traditional and mainstream of the three is the stoker system, and technological innovations have been encouraged because of the large number of applications.
The stoker refers to the stage for the mixing and transfer of waste and has a lattice pattern so that air is fed from the bottom to burn the waste. Stoker grates are placed stepwise and convey the waste to three zones resulting in the final fine ash product: (1) drying to evaporate water, (2) incinerating with intense fire, and (3) after-burning for complete combustion.
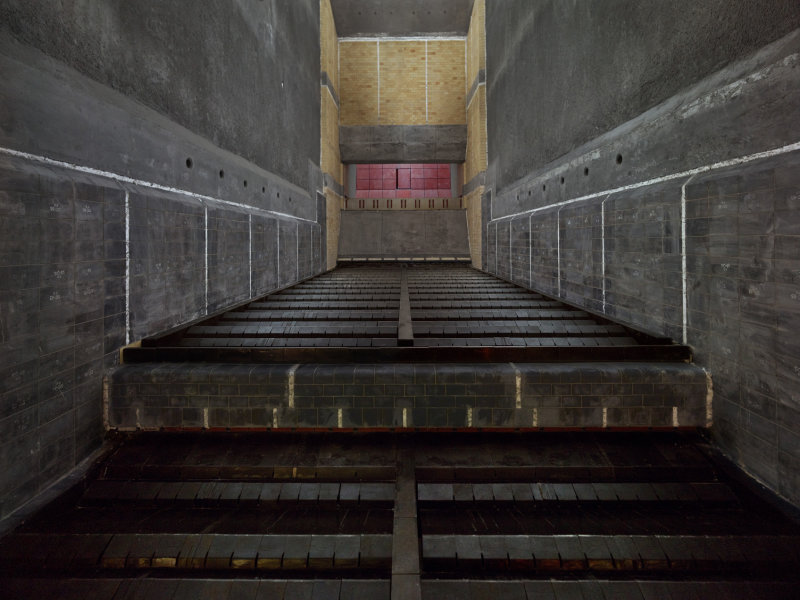
As the “advanced” term suggests, Kawasaki developed a system one-step forward from conventional stoker-type incinerators. The tough mechanism is configured for complete combustion with a smaller volume of air, cleaner incineration ash and exhaust gas from the high-temperature burn, improved heat recovery rate, and stable operation with minimized combustion fluctuations.
Complete Waste Combustion with Less Air
Examine the series of steps to alter waste to energy along with the operation flow of the Kawasaki Advanced Stoker System. First, waste is fed through the inlet into the furnace and goes through the drying, incinerating, and after-burning processes on the stoker grates that move back and forth to convey the waste forward. Three hours later, the ash from the burned waste is collected in a box with a chute. The thermal energy resulting from this combustion is converted into high-temperature, high-pressure steam in a boiler and rotates a power-generating turbine.
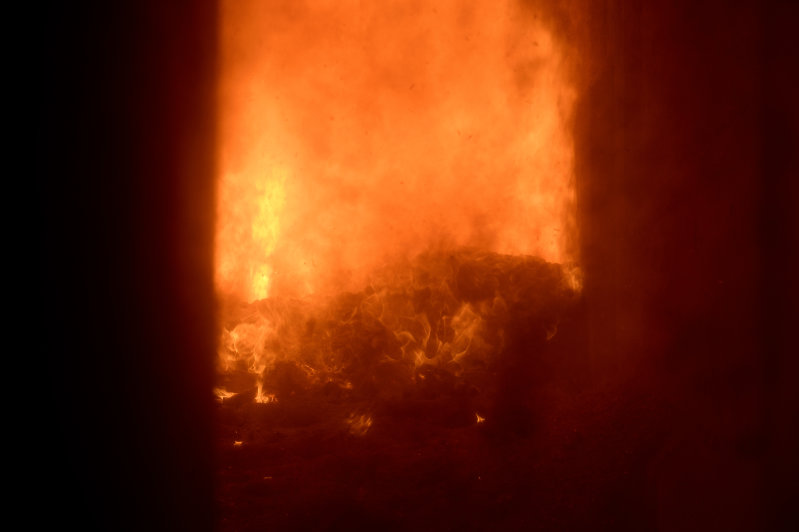
The key point is to burn the waste stably and completely with the smallest amount of air. If the volume of injected air is increased, combustion becomes intense but results in more exhaust gas and a loss of energy at the same time. Therefore, Kawasaki devised the parallel-flow incinerator method. While many stoker incinerators have an opening in the stack right above the stoker grates for the straight discharge of combustion heat and exhaust gas, the Kawasaki style is different. A partition is installed in the ceiling parallel to the downward stoker steps so that combustion gas is diverted to the after-burning area and then forcibly inverted to the secondary combustion area above the partition (re-burning zone) before being fed into the boiler.
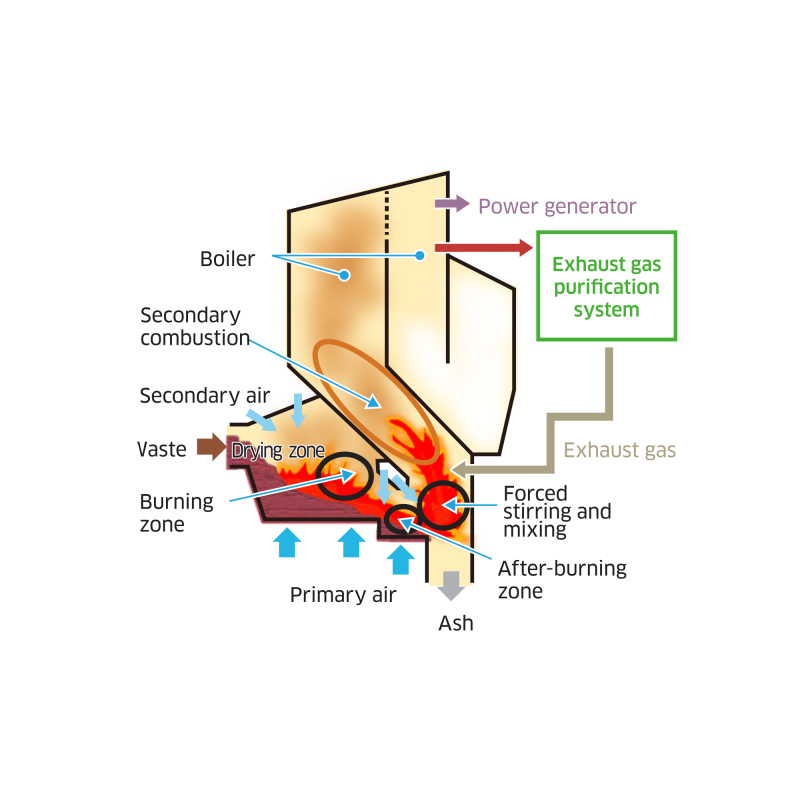
The combustion gas flows side by side with the waste for complete burning, and the inversion turbulently mixes air and exhaust gas, maintaining the high temperature and thoroughly combusting unburned matter in the exhaust gas. Consequently, the generation of dioxin and carbon monoxide, which is always a challenge in the incineration of waste, is reduced. The tiny amount of exhaust gas that remains is treated in a compact exhaust gas cleaner, where part of it is returned to the furnace to maintain the high temperature for recycling and reuse.
Control Technology as the Epitome of Waste Incineration Expertise
You might associate the use of the English term “stoker,” which means a person who shovels coal into a steam engine, with Europe. Yes, this system was first developed in Europe and later introduced to Japan. However, the properties of waste are different between Europe and Japan: here it is humid, and waste contains more moisture, which makes it hard to burn. Japanese engineers invented the parallel-flow furnace to achieve stable combustion, but Kawasaki additionally intended to ensure the accomplishment with another an important technology called Smart-ACC (Automatic Combustion Control).
Developed independently by Kawasaki, this automatic combustion control technology realizes stable generation of steam to rotate the turbine. Because stable steam generation is the result of steady combustion, the relationship between the waste and the volume of air is the key to a good burn. Smart-ACC is a sophisticated controller that maintains the ideal combustion conditions according to the calorific value and other properties of the waste. Atsushi Hashimoto, senior staff officer in the Equipment Design Section, Environmental Plant Department, Environment Plant Engineering Division, Plant & Infrastructure Company, considers this newest technology for adequate control of combustion and steam generation the epitome of waste incineration expertise.
Epitome of Waste Incineration Expertise―Smart-ACC (Automatic Combustion Control) and AI (Artificial Intelligence)
To comprehend heat generation during waste burning is a way to realize good combustion. The calorific value depends on the properties of waste, which vary dramatically according to the season and the region. For conventional waste treatment facilities, personnel monitor the conditions inside the furnace to maintain optimal combustion. In other words, humans have had to determine precisely how much waste should be fed into the furnace under certain conditions and how much air and exhaust gas should be fed to achieve adequate operation.
Toughness Unique to Kawasaki Products
Kawasaki is proud of its boiler and turbine technologies, which provide a solid foundation for the entire incineration system. A boiler that allows for a high pressure of 4 MPa, which is equivalent to the water pressure at depths of 400 m, and a high temperature of 400°C, is used to rotate the turbine. With the quality steam obtained from stable incineration, the turbine turns steadily. In other words, operators can receive a continual supply of quality electricity.
Kawasaki also emphasizes product durability. Having made heavy-duty industrial products that operate 24/7 under high-intense environment, the Company has the expertise to develop parts that will not be exhausted by extreme use. For example, weld overlay is a unique welding method employed with the boiler super-heater for the combustion furnace to prevent corrosion in the pipes. Overlaying the metal with high corrosion resistance on the pipe surfaces extends the service life from 10 years, when such pipes normally need to be replaced, to more than 30 years. The design of these tough Kawasaki products remarkably lowered maintenance costs by almost 1.5 billion yen.
The Minatojima Clean Center, completed with Kawasaki’s comprehensive technological capabilities, has a site area of 38,900 square meters and a gross floor area of 12,600 square meters. In this vast space, the Kawasaki Advanced Stoker System continues burning waste and producing electricity around the clock. Groups of 10 or more people can visit and observe the latest mechanism (preliminary booking is required). How is our waste turned into electricity? Seeing is believing. How about coming to observe this imposing ecosystem?
Redefining the Role of a Waste Treatment Plant
Waste is the reflection of a society. Clean, speedy, and efficient treatment of waste is vital and directly linked to the landscape, sanitation, and the value of the existence of a municipality, especially in dense urban areas. Kobe City, representative of ports in Japan, initiated the operation of its first waste incineration plant in 1963, which was one of the earliest in Japan. Since then, the city has accumulated substantial experience in waste treatment and knowledge in order to evaluate the technology. The local government, as an expert in waste treatment technology, selected Kawasaki to build a new incineration facility.
The Minatojima Clean Center, which started operation in 2017, is the City’s 11th such construction project. The new waste treatment base is adjacent to an urban area and was expected to be equipped with high process performance and a clean environment, as well as to become a more efficient energy center. As a result of applying Kawasaki’s technology and expertise, the Center has been ranked among the top ten in Japan for its energy recovery rate (power generation per unit amount of waste treatment) since the completion of construction and was ranked in third place in FY 2019.
Kazuhiko Ichie, manager of the Western Region Sales Section, Environmental Plant Sales Department, Marketing & Sales Division, Plant & Infrastructure Company, says, “Thanks to its extensive experience in building a variety of different plants, Kawasaki can offer suggestions on overall waste incineration systems, including improved power generation with a smaller environmental footprint.”
Kawasaki delivered its first waste incineration plant in 1964 to Ichinomiya City in Aichi Prefecture and received another order in 1980 from the city of Kyoto to build a large-scale waste-to-energy plant with a 4,000 kW output, the Toubu Clean Center. Afterwards, the Company pursued the engineering to change the definition of incineration plants from a mere place of disposal to a base for creating energy.
Ichie comments: “Waste incineration plants are beginning to play pivotal roles in the formation of community energy networks, such that today, large municipalities are trying to be suppliers of stable sources of electricity by running multiple incineration facilities. To accommodate this trend, plant business operators must have the acumen to make specific proposals.” In 1996, one of the largest facilities of this kind in Japan was completed at the Nanyo Incineration Plant in Nagoya City, with an incineration capacity of 1,500 tons of waste per day and power generation of 27,000 kW. This large-scale facility is the embodiment of more than 30 years of research and development.
Smart-ACC assists in the monitoring and adjustment tasks. This advanced device administers different jobs to reduce fluctuations in the volume of steam with regard to the stoker grates with the original oscillating movement to loosen waste for steady contact with combustion air, the sensor that measures the waste volume in the incineration furnace, and the exhaust gas sensor for burn conditions in order to supply optimum combustion air. This makes it easier to regulate electricity output per hour, which enables power generation according to electricity demand. Moreover, as the novel combination between the inventive waste crane control and AI realizes more precise control and prediction, Smart-ACC continues making progress each day even now.
What is the Concept of the Minatojima Clean Center?
On starting the grand project to build a modern waste treatment plant on Port Island, Kawasaki first formulated three concepts. First, the facility should contribute to local communities and be open to the public. Second, it should be eco-friendly, safe, and reliable. And third, it should achieve high economic efficiency and the capacity to treat waste in a stable and continuous manner. The urban waste treatment plant located adjacent to the center of Kobe, which is also known as a tourist destination, thus appeared as a high-tech, clean energy station. These are the reasons that leafy parks are next to the facility, and plant tours are welcome.
Technology Serving to Build a Healthier Nest
Now that the volume of waste generation in Japan is decreasing each year, the concept of incineration plants has reached a turning point. Ichie adds, “With the recycling and reusing of resources becoming so popular, the volume of waste has decreased, and this is precisely why municipalities are avid advocates of converting these plants into profit centers rather than cost centers. Addressing these needs is extremely meaningful in terms of societal benefits.”
The facilities’ role is changing from extinction to generation. As the proverb goes, “It's an ill bird that fouls its own nest.” The technology for the Kawasaki Advanced Stoker System not only removes dirt from the nest but also works to make a better nest as a substructure in support of the 21st century’s society.
Kawasaki has been constructing incineration plants for large-scale facilities in different places that are capable of burning more than 300 tons of daily waste. The total volume of waste treated by the 78 facilities built by Kawasaki is as high as 18,400 tons per day, and power generation capacity has reached 500 megawatts. Kawasaki’s incineration plants are helping to solve environmental and financial issues for municipalities.
Moreover, the company established a joint venture with a Chinese company and has already received orders for 10 stoker-type waste-to-energy facilities. Malaysia, Singapore, Thailand, and Indonesia are promising markets for the construction of waste incineration plants, which are estimated to increase in the future. Japan has the largest number of waste incineration facilities in the world and spreading its excellent technology throughout the world should lead to progress in widening the shrinking Earth into a spacious, plentiful planet again.
Decreasing Amount of Waste in Japan Year after Year
Because the demand for greenhouse gas reduction is now worldwide, the eco-consciousness of companies and the public varies significantly. The amount of waste generation in Japan has been decreasing since the mid-2000s. According to data from 2019 published by the Ministry of the Environment, per-capita generation of waste per day decreased to 918 grams, which had often exceeded 1 kilogram in the past. While older waste incinerators are therefore disappearing, facilities with a power-generation function are increasing and now account for 35% of the overall number. The waste incineration plants generate 9,553 gigawatts of electricity in total, which corresponds to the energy consumed by 3.21 million households per year. Diverse sectors actively seek and promote recovery not only as materials but also as energy for waste recycling.
Historically, human beings have always been bothered by the disposal of waste. The issues of waste are unavoidable themes in the daily lives of people’s, and the solution to this issue is a clue to a better future. In the 21st century, innovations have finally allowed us to reach the idea of waste = energy where the negative thinking of ridding waste from our lives through landfilling or moving is transformed into a positive attitude of regarding waste as an energy resource. Kawasaki materialized this change in attitude with the high-efficiency Kawasaki Advanced Stoker System. The world-class waste-to-energy technology of Japan is opening new horizons in an era of global environmental issues.
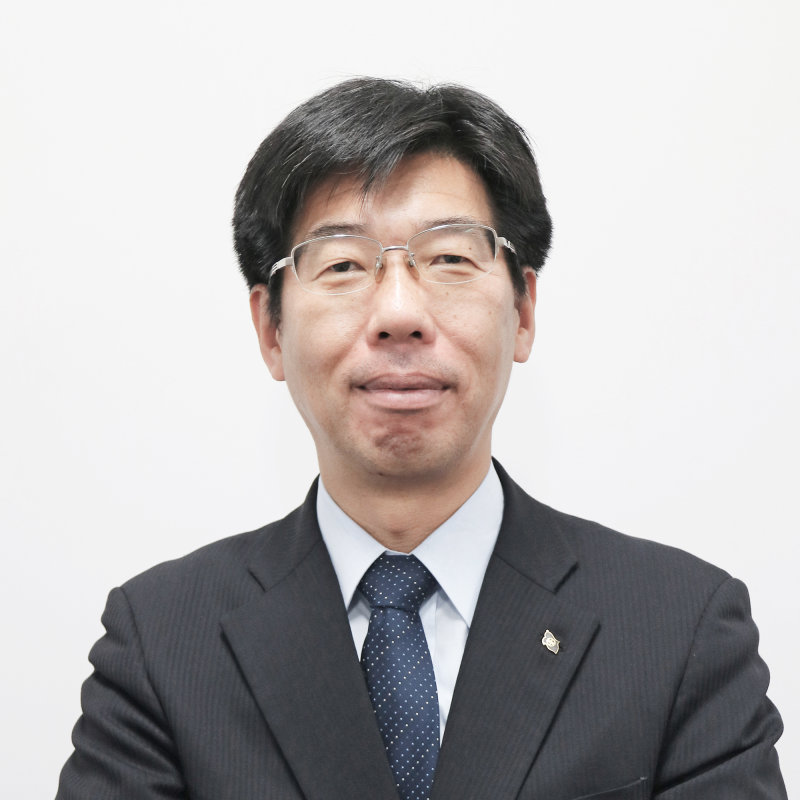
Environmental Plant Engineering Division
Plant & Infrastructure Company
Kawasaki Heavy Industries, Ltd.
Addressing a Global Agenda using Japan’s Advanced Technologies
Since the beginning of the 1960s, when rapid economic growth was beginning to take place in Japan, waste incineration facilities have grown in number and have needed replacing about every 30 years. The combined incineration capacity of the facilities constructed in Japan on an annual basis is about 4,000 tons, and most of those are for renewal projects for facilities built in the early 1990s. Environmental issues promoted the “waste-to-energy” concept, which has become the standard today. For new construction of waste incinerators, technological solutions for achieving both stable incineration and high economic efficiency are proving effective in reducing the financial burden on municipalities.Since its first delivery in 1964, Kawasaki has constructed 178 waste incineration plants in Japan and overseas, of which 78 are currently in operation in Japan.
Since the 1980s, the company has been striving to establish incineration facilities as energy stations, resulting in the development of parallel-flow furnaces, structural components with longer lives, and other proprietary technologies for which Kawasaki has won high acclaim. Kawasaki’s track record, particularly for the construction of large furnaces and large-scale incineration facilities with large power generation systems, is overwhelmingly higher than that of its competitors. Because they are large-scale, a good balance of safety, stability, and economic efficiency was immensely important, and Kawasaki tackled the challenge with its comprehensive technological expertise.
It is said that waste “treatment” usually takes the form of landfills in the beginning, and it is not until the gross domestic product (GDP) exceeds 5,000 US$ per capita that countries can afford to pay for waste treatment, and start building waste incineration plants. China, Malaysia, and Singapore are currently at this stage, soon to be followed by Thailand and Indonesia.
Kawasaki formed a joint venture with a Chinese company, and has already received orders for 10 stoker-type waste-to-energy facilities. In China, the ash remaining after gasification of waste is used as cement material-a system called the CONCH Kawasaki Kiln (CKK) System. We are committed to pro-actively addressing global environmental challenges, by applying the superior technology of waste incineration in Japan. I believe that this is an extremely meaningful business that leads to resolving issues which are considered to be a global agenda.
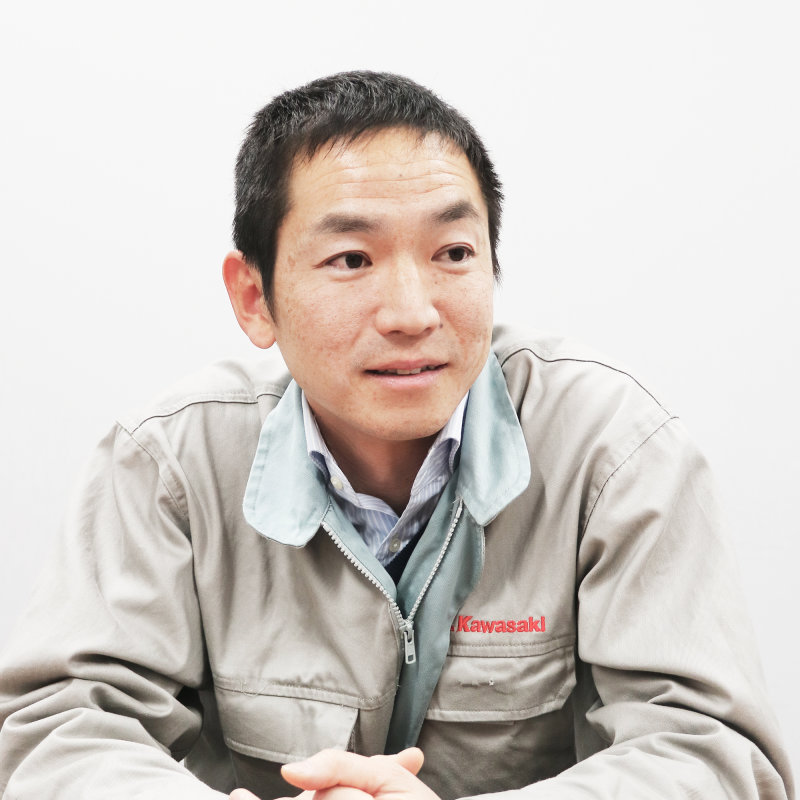
Equipment Design Section
Environmental Plant Department
Environment Plant Engineering Division
Plant & Infrastructure Company
Kawasaki Heavy Industries, Ltd.
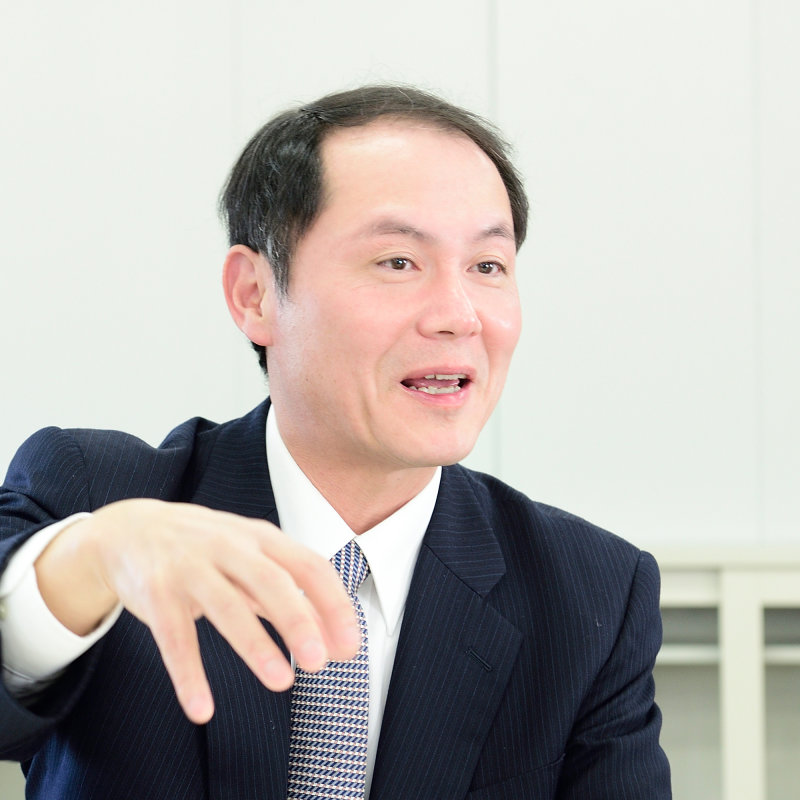
Western Region Sales Section
Environmental Plant Sales Department
Marketing & Sales Division
Plant & Infrastructure Company,
Kawasaki Heavy Industries, Ltd.
Note: The numerical values and job titles stated herein are based on information as of May 2017.