GM Blower (Kawasaki MGM Steam Compressor)
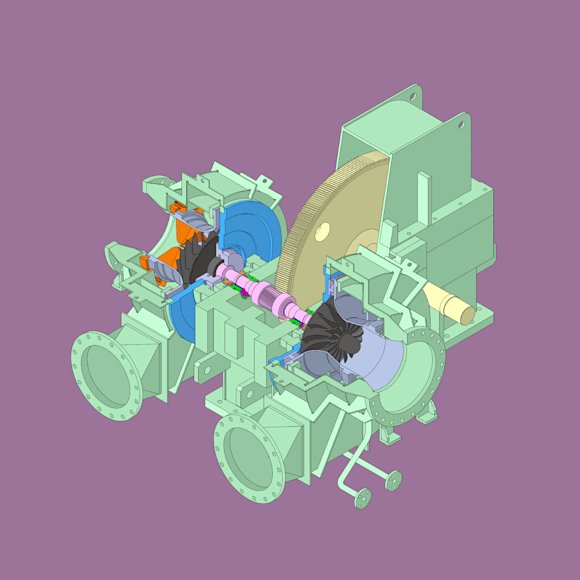
A blower is a mechanical component that supplies air, steam, and gas by applying pressure. Its applications include an air source for chemical reactions, oil refining, and iron making equipment, suction and transportation of gases, treatment of effluent and drainage, and the aeration process at municipal sewage treatment plants. Kawasaki developed a mixed flow-type impeller for higher efficiency and has now supplied more than 1,300 blowers. Lately, the Company placed the MGM Steam Compressor on the mature market of blowers and has successfully realized far more efficient units.
New Innovation in Steam Blowers
A blower is a mechanical component that supplies pressurized air, steam, and gas. It is used in various fields by applying the principle of discharging fluid through the transfer of rotational energy. Applications include performing aeration for biological reaction tanks at municipal sewage treatment plants, supplying air for the ventilation and combustion process of rotary kilns, suction and transportation of various gases, and treatment of wastewater and drainage.
The more compact and efficient a blower is — meaning that it has a smaller footprint and larger discharge pressure — the easier it is to install. Reduced size and increased efficiency also have the added benefit of low vibration and noise. Half a century ago, Kawasaki made a major technological innovation by developing a mixed flow-type impeller, which enabled the development of smaller and more efficient blowers. Since then, Kawasaki has produced over 1,300 blowers, some of which have been in operation for more than 40 years, which attests to the outstanding reliability of Kawasaki’s products.
While blowers have mainly been used to supply air, such as in the aeration of municipal sewage, in recent years they have increasingly been used for industrial applications to pressurize steam and gases.In particular, blowers have been used as steam compressors, with applications including the concentration of dairy products and juice in food production, concentration of plating wastewater in the chemical industry, and the recovery of waste heat from distillation columns in the petroleum industry. For this type of blower as well, Kawasaki offers a product that delivers maximum energy savings, called the Multi-Stage Gear-Increased Mixed-Flow (MGM) Steam Compressor.
The key feature of the MGM Steam Compressor is its multi-stage compression system. Steam that has been compressed in the first stage is further pressurized in the second stage. The MGM Steam Compressor also features a compact size, small inertial moment, low vibration, and low noise, thanks to the development of the mixed flow-type impeller.
One issue that is commonly associated with steam is corrosion. When steam, which is a gas, turns into water, the impeller and other components are subjected to considerable stress. Accordingly, the MGM Steam Compressor uses materials that are highly rigid and resistant to corrosion.
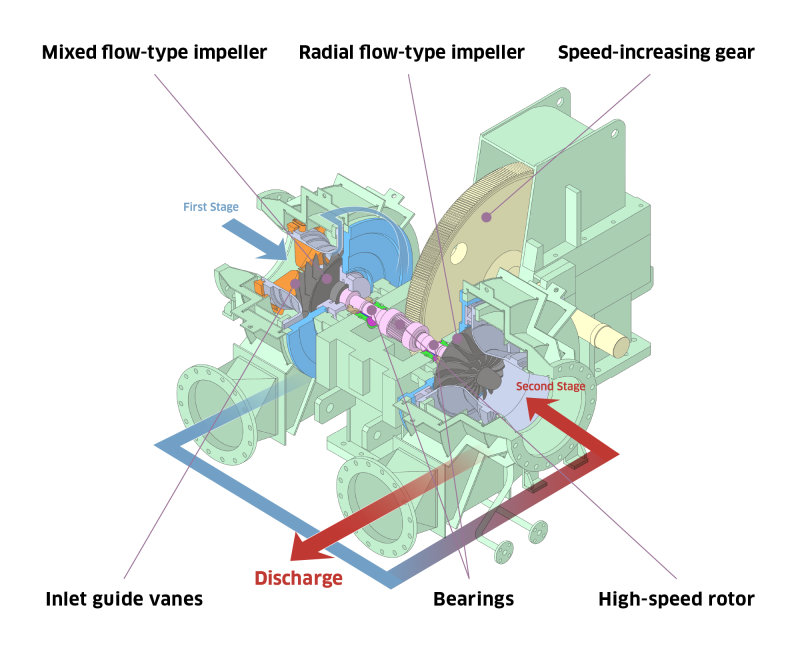
MVR System with a Steam Compressor Offers an Innovative Approach to Energy Saving
A mechanical vapor recompression (MVR) evaporator system, as shown in the illustration, uses a unique energy recovery process to provide heat for condensing products. While many systems use a boiler as a heat source, an MVR system uses a steam compressor to adiabatically compress low-pressure steam discharged from a concentrating column, then reuses the heated and compressed vapor as a heat source.
Since the energy needed by a steam compressor to compress steam is considerably less than the energy used by a boiler to generate steam, an MVR system consumes far less energy than a boiler-type system. An MVR evaporator system takes an innovative approach to conserving energy by employing a steam compressor to pressurize and raise the temperature of the vaporization heat of low-pressure steam, which used to be released into the atmosphere in conventional systems, then reusing it for its own process.
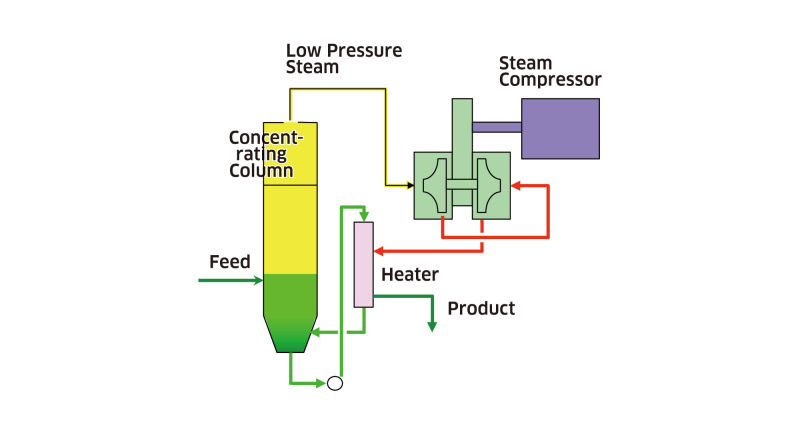
Inlet guide vanes
A number of variable vanes are arranged radially in front of the first-stage impeller for controlling flow with greater efficiency at partial load.
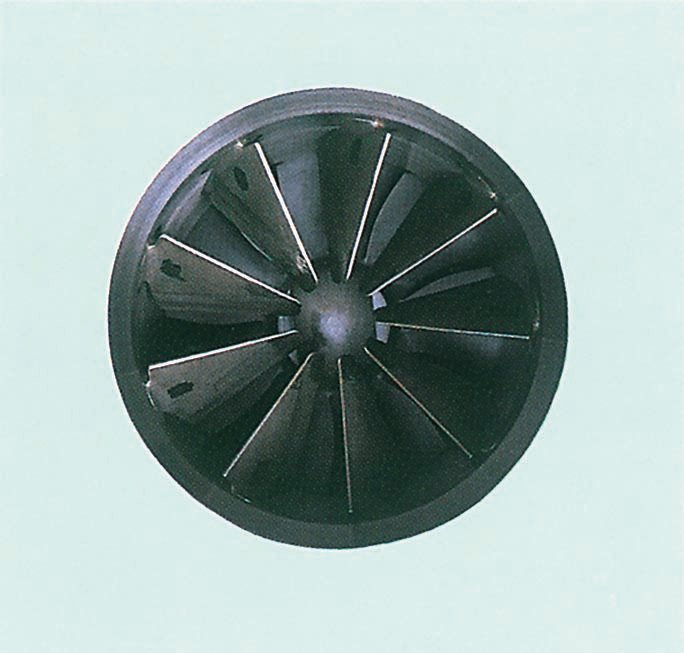
Impellers
A mixed flow-type impeller is used for the first stage, and radial flow-type impellers for the second to fourth stages and later stages, to achieve efficient flow control. The optimal shape is selected based on computational fluid dynamics (CFD) simulations to further increase efficiency. The impellers are made of stainless steel or titanium alloy, according to the application.
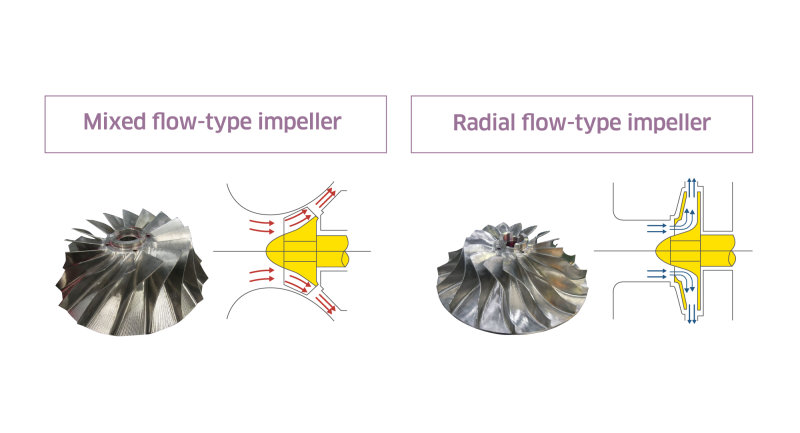
High-speed rotor
The high-speed rotor forms a one-piece shaft with the pinion of the speed-increasing gear, and the impellers are fitted on both its ends. The rotor is made of chrome molybdenum steel, which is heat-treated for strength. It is dynamically balanced by a special balancing machine to ensure stable rotation with minimal vibration.
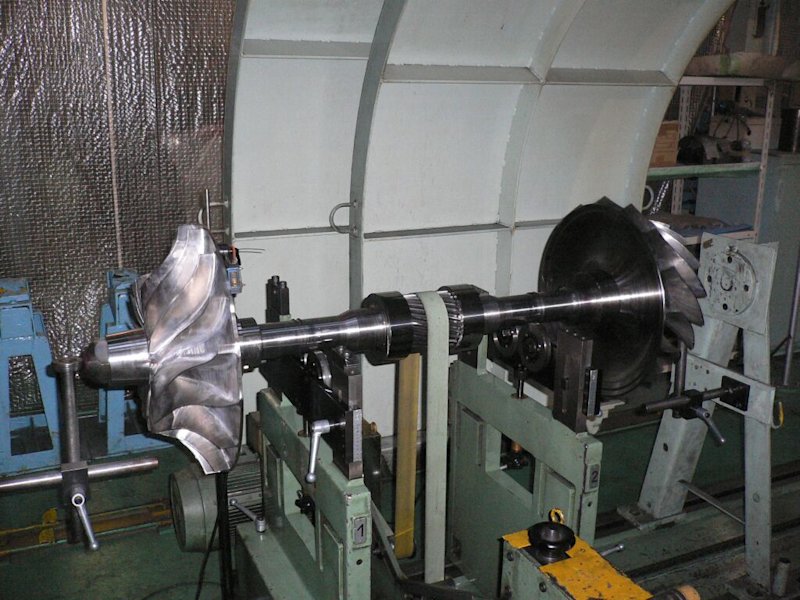
Speed-increasing gear
A helical gear is used, which brings the motor speed up to the impeller rotation speed in a single stage. The gear teeth are ground to high precision and then surface hardened, ensuring low vibration and noise and a long service life.
Bearings
Aluminum lining is used on carbon steel for the bearings. A tilting pad developed by Kawasaki over many years is used to ensure excellent stability during high-speed rotation.
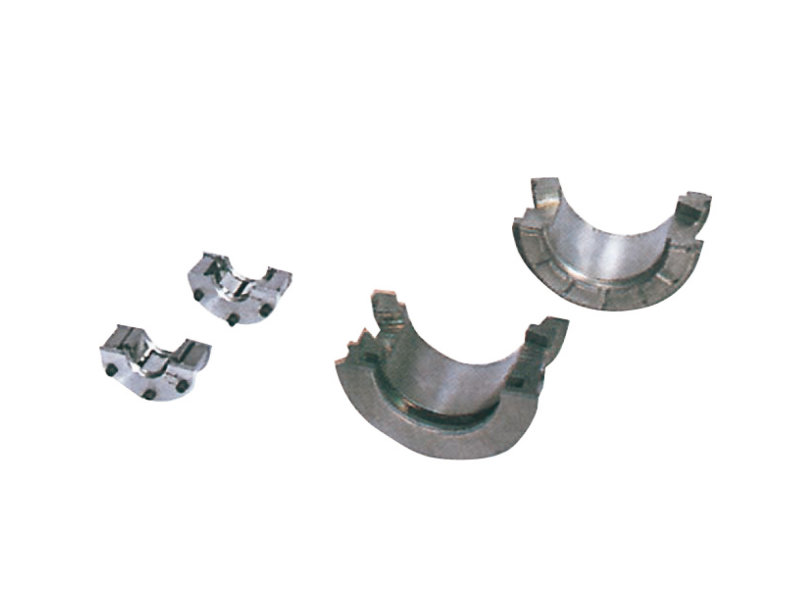
The motor that powers the MGM Steam Compressor can be coupled with a steam turbine to create a mechanism that effectively utilizes steam to drive the motor.
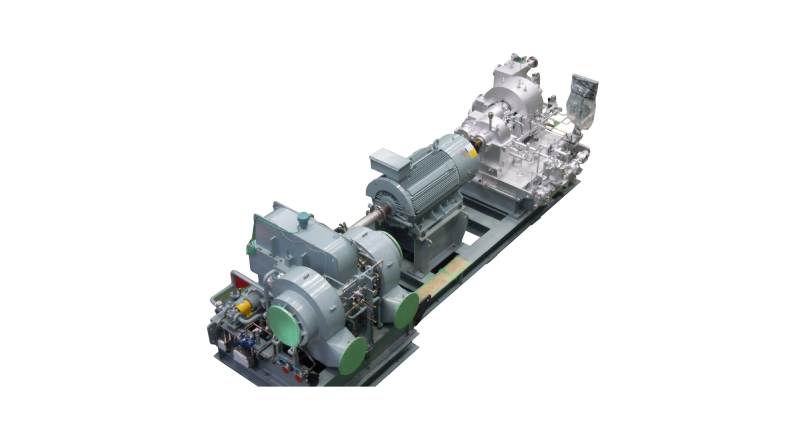
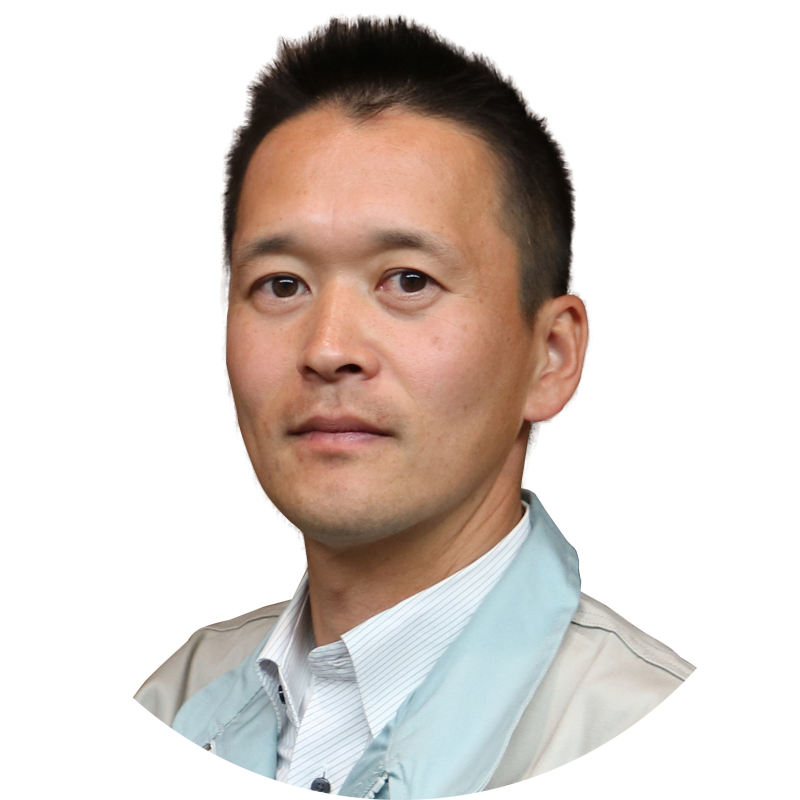
Blower Engineering Section
Aero-Dynamic Machinery Department
Machinery Division Kawasaki Heavy Industries, Ltd.