Japan’s Largest Liquid Hydrogen Storage Tank. The Intricacies of Keeping Hydrogen at -253°C

At the Tanegashima Space Center and its liquid hydrogen (LH2) storage facilities, the LH2 rocket fuel is stored until a few hours before launch time. Retaining the LH2 in its liquid state over an extended storage period without evaporation is an extremely difficult task because the fuel has to be kept at the extremely low temperatures of -253°C. The editorial team interviewed Hiroto Sato, an engineer in Cryogenic Storage System Engineering Division, Plant & Infrastructure Company, about Kawasaki’s technology to support rocket launches.
A Liquid Hydrogen Storage Tank for Rocket Fuel
The Tanegashima Space Center, with its Liquid Hydrogen Storage (LHS) facilities for the storage and supply of the liquid hydrogen (LH2) that powers rockets into space, is home to Japan’s largest liquid hydrogen storage tank. A few weeks before a rocket launch, liquid hydrogen is loaded into a tank truck and transported over land and sea routes to the Tanegashima Space Center. Until a few hours before the rocket is fueled, the liquid hydrogen is held in the Center’s huge tank. However, maintaining hydrogen in its liquid state over an extended storage period without evaporation is an extremely difficult task. The techniques used for reducing evaporation from the vast quantity of liquid hydrogen needed for a space rocket launch are built on some of Kawasaki Heavy Industries’ unrivaled technological strengths.

Techniques for Storing a Mass of Liquid Hydrogen at -253°C
Sato: “At Kawasaki Heavy Industries, we are charged with operating the Vehicle Assembly Building (VAB) and an array of different types of facilities at the Tanegashima Space Center. I think this is unusual, even for Kawasaki, that we are involved in the operation of facilities after developing them. Of all the facilities and equipment in our charge, this liquid hydrogen tank with its operational aspects tested the limits of our technological capabilities and know-how from the design stage. In order to keep the hydrogen in its liquid state, we needed a method to ensure a storage temperature of -253°C, which is extremely low. Given the large mass of liquid hydrogen, permanent cooling was not an option because of the huge running costs involved. This is why we designed a cooling structure similar to a colossal thermos, so to speak. This structure suppresses any temperature rise right from the moment the liquid hydrogen is loaded into the vessel. Technically, this design was made possible and successful thanks to the superior thermal insulation cold-storage technology used at Kawasaki for cryogenic storage applications.

Cold Insulation Performance that Successfully Reduces the Rate of Evaporation
The liquid hydrogen storage tank at the LHS facility is especially noteworthy for its cold insulation performance. In order to keep hydrogen in a liquid state, it must be kept at -253°C, an extremely low temperature. However, when liquid hydrogen is put into a conventional tank, rapid evaporation occurs. The only way of preventing the resulting pressure surge inside the tank is to release the gaseous hydrogen into the atmosphere. This means a loss of hydrogen, and keeping that loss to a minimum was the original motivation for designing this specialized tank. Although not apparent from the outside, the tank is double-hull, with a vacuum being created between the inner and outer walls. This vacuum is then filled with perlite, a thermal insulation material. Together, these two walls make for a design that permits almost no heat transfer from the outside to the inner vessel. This double-hull tank, however, must be constructed so that the outer vessel supports the inner one, and the needed support structure acts as a heat conduit. Should a significant amount of heat be conducted thereby, it would actually increase the rate of evaporation. To work around this dilemma, engineers designed the shape and determined the position of the support structure with special attention to minimizing the surface area where thermal transfer could occur. Through the confluence of these techniques, Kawasaki engineers achieved an evaporation rate even lower than the target rate of the original design.

No Sign of Deterioration after 30 Years
Sato: “This liquid hydrogen tank was built in 1987 and has been in operation ever since. To date, we have found no sign of deterioration in its cold insulation performance. Considering that 30 years have gone by, it is extraordinary that the tank’s performance is completely undiminished. I can’t help feeling immense gratitude and respect for the engineers we had back then. Designing this liquid hydrogen tank to suppress heat transmission and conduction from the exterior required welding and other manufacturing techniques of the highest caliber to maintain the vacuum in the interspace over such a very long period. In fact, the evaporation rate has not changed since the first day, and there is nothing to suggest that this tank will not continue to deliver a faultless performance. To have a tank this large delivering this level of performance decade after decade without a hiccup is a technical achievement on a global level. It is my goal to generate new technologies based on the high-level technical expertise passed down by preceding engineers and to keep on creating products that are appreciated by our customers.”

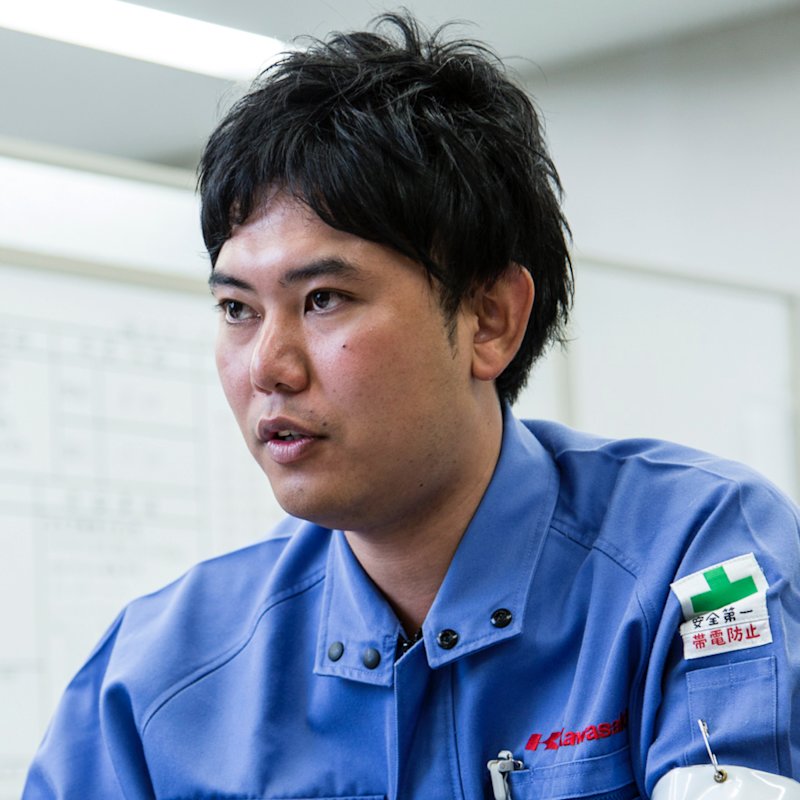
Cryogenic Storage System Department
Cryogenic Storage System Engineering Division
Plant & Infrastructure Company
Kawasaki Heavy Industries, Ltd.