Kawasaki Water-Refrigerant Centrifugal Chiller
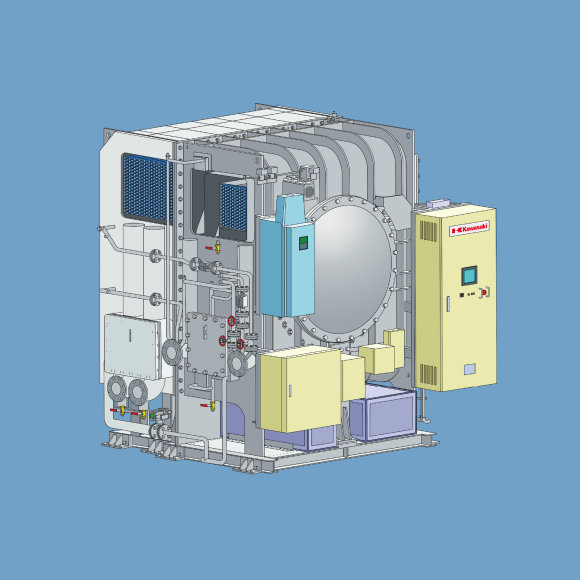
Air conditioners keep rooms cool or warm thanks to the refrigerant that conveys thermal energy. CFCs, which were a common refrigerant, have been implicated in ozone depletion and global warming and were phased out completely as of 2020. Although CFC substitutes (HFCs) are incombustible and easy to handle, they do not easily decompose in the atmosphere and, therefore, remain a source of global warming. Kawasaki developed Japan's first centrifugal chiller using water as the refrigerant, which does not heat the planet, deplete the ozone layer, or present the risk of combustion or toxicity.
Using Water, the Ultimate Refrigerant
Air conditioners can keep a room cool or warm thanks to the work of a refrigerant, which conveys thermal energy. CFCs, which used to be a common refrigerant, have been implicated as a cause of ozone depletion and global warming, and they will be phased out completely by 2020.
Today, CFC substitutes (HFCs) are mainly used as a refrigerant. While HFCs are incombustible and easy to handle, they are not easily decomposed in the atmosphere and therefore still become a source of global warming.
So, is there an ultimate refrigerant that does not heat the planet, deplete the ozone layer, or present the risk of combustion or toxicity? The answer is yes — water. Kawasaki developed Japan’s first centrifugal chiller that uses water as a refrigerant.
Unlike HFCs, which exist in the form of gas under atmospheric conditions, water is a liquid, and its pressure needs to be reduced in order to change phases in the evaporator and condenser, and a high pressure ratio between the evaporator and condenser needs to be achieved for the refrigerant cycle.
In addition, using water as a refrigerant multiplies the volumetric flow rate 100-fold, necessitating the use of a large compressor, which inevitably makes the chiller larger. The footprint of a chiller is a significant issue, affecting the productivity of offices and plants.
To address this issue, Kawasaki developed a compressor that effectively increases pressure, drawing from its fluid analysis technology cultivated through the development of gas turbines and steam compressors. Kawasaki also developed a new high-speed motor to drive the compres- sor. Moreover, the components inside the chiller were also rearranged to achieve both a refrigerating capacity and a footprint on a par with existing chillers.
Kawasaki’s water-refrigerant chiller features a capacity of 100 USRt of refrigeration (352 kW) and a coefficient of performance (COP) of 5.1. This is the same level of performance as HFC chillers, and, of course, water-cooled chillers emit no HFCs.
Assuming a service life of 15 years, they will each keep 575 tons of CO2 out of the atmosphere. Using water as a refrigerant has the added benefit of significant savings in maintenance costs.
A test unit has been in operation at Kawasaki’s Kobe Works since 2013, and so far everything has been running smoothly. This demonstration test has allowed Kawasaki to amass considerable know-how regarding system installation, operation, and after-sales services.
The world’s eyes are increasingly turning to the green and cost-efficient water-refrigerant centrifugal chiller.
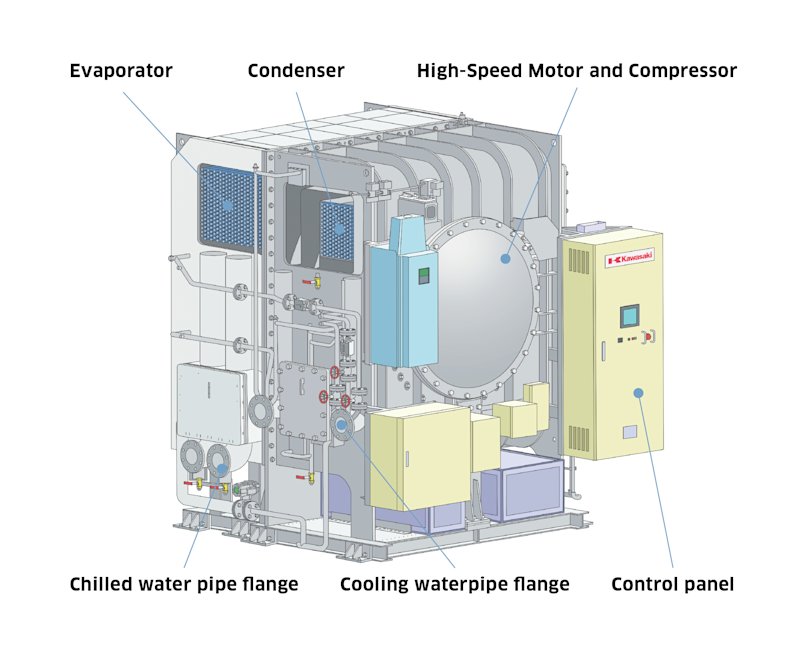
Mechanism of a Water-Refrigerant Centrifugal Chiller
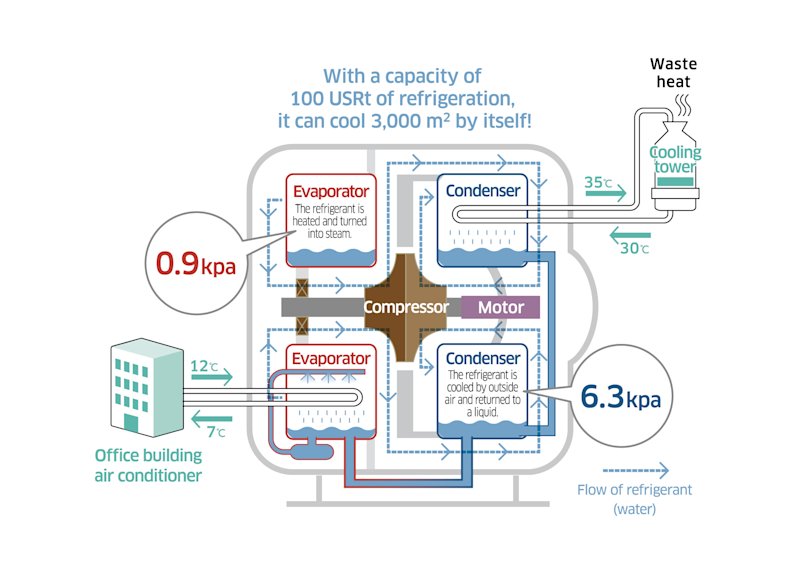
Water reaches its boiling point at lower temperatures under low pressure, which is why it boils quickly on top of a high mountain. Kawasaki’s water-refrigerant centrifugal chiller vaporizes water, the refrigerant, at 6°C under a low pressure of 0.9 kPa (approximately a hundredth of atmospheric pressure) inside the evaporator. Water that returns to the evaporator through a pipe at 12°C is cooled by this vapor to 7°C. The resulting chilled water is used to generate cool air that keeps offices comfortable.
On the other hand, the low-temperature, low-pressure steam flowing from the evaporator is pressurized by a turbo compressor to 6.3 kPa. This steam is cooled inside the condenser and returned to a liquid, which is then sent back to the evaporator. Kawasaki’s water-refrigerant chiller employs two-stage compression to achieve a seven-fold pressure ratio.
Two-Stage Compressor
The pressure of the evaporator is only approximately a hundredth of atmospheric pressure. Moreover, because water, the refrigerant, has a large volume, the compressor must be large as well.
To increase the performance of the compressor under these conditions, Kawasaki adjusted the number and shape of the impellerblades. Kawasaki also introduced further technologies, such as two-stage compression, and an intermediate cooler placed in the middle of the two-stage compression process to keep the temperature low inside the compressor.
These enhancements enabled the creation of a compact, high-performance chiller.
Newly Developed High-Speed Motor and Compressor
A proprietary motor that achieves high-speed rotation. The rotational speed is increased through fine control of magnetic force. The motor is integrated with the compressor and is placed in the refrigerant atmosphere. Therefore, the motor’s coil is coated with resin for insulation and to make it waterproof. Because the motor is connected directly with the compressor, there is no need for a speed-increasing gear and oil.
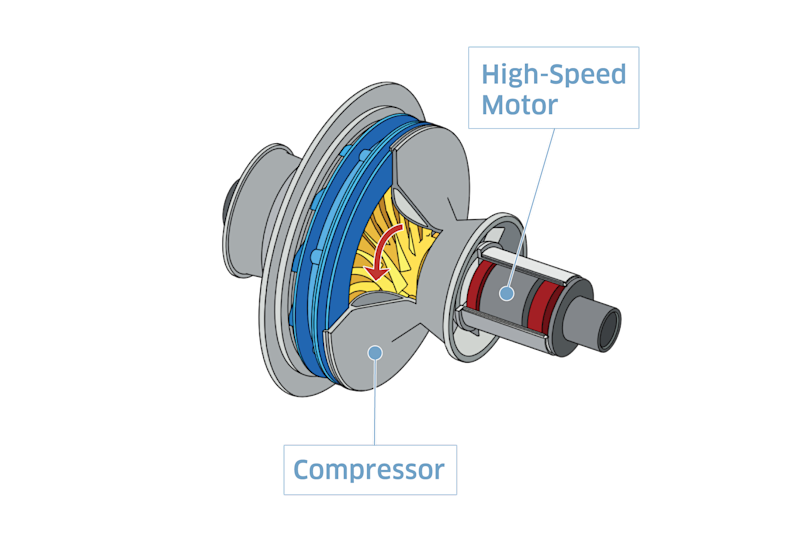
Condenser
The compressed refrigerant is pressurized to 6.3 kPa (one-sixteenth of atmospheric pressure) and rises in temperature, but then it returns to a liquid upon coming into contact with the 30°C pipe inside the condenser and is sent back to the evaporator.
Evaporator
The pressure inside the evaporator is maintained at 0.9 kPa (approximately a hundredth of atmospheric pressure). Here, the refrigerant (water) is vaporized at 6°C, and waterinside the pipe is cooled to 7°C and sent to the building air conditioner.
Vacuum inside the system
The amount of outside air leaking into the system is minimized by enclosing the motor inside the system and connecting it directly with the compressor. The evaporator, condenser, compressor, motor, and other primary components are packaged inside a vacuum container.
Control panel
The control panel features a color touch panel for enhanced visibility.
Cooling waterpipe flange
The inlet/outlet for water flowing inside the condenser. The water enters at 30°C and returns at 35°C, then it is sent to the cooling tower.
Chilled water pipe flange
The outlet for chilled water used by the building air conditioner, and the inlet for returning water.
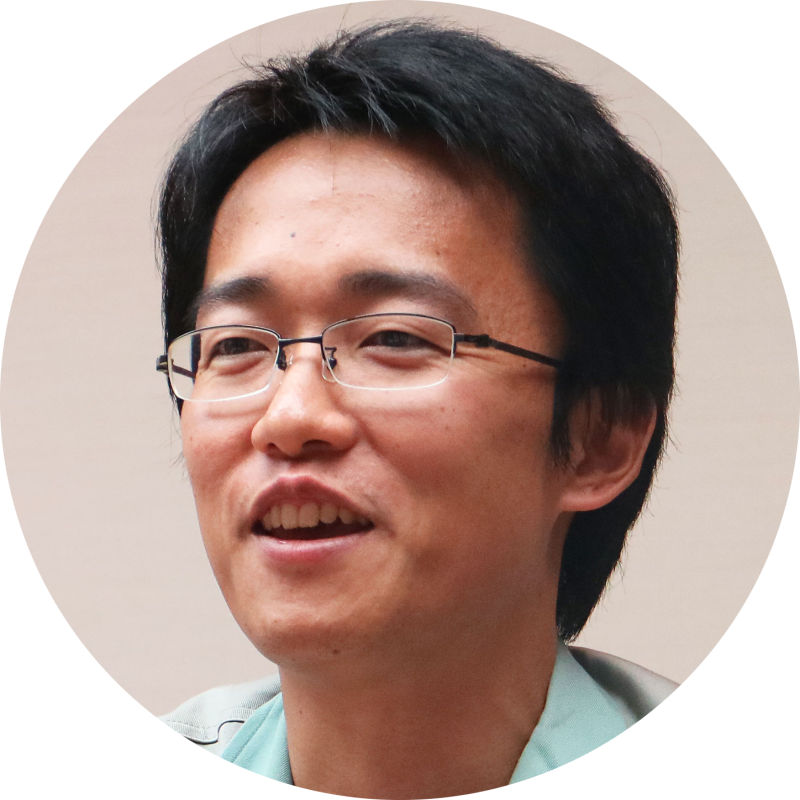
Blower Engineering Section
Aero-Dynamic Machinery Department
Machinery Division
Kawasaki Heavy Industries, Ltd.