Kawasaki UVF Boiler U-KACC
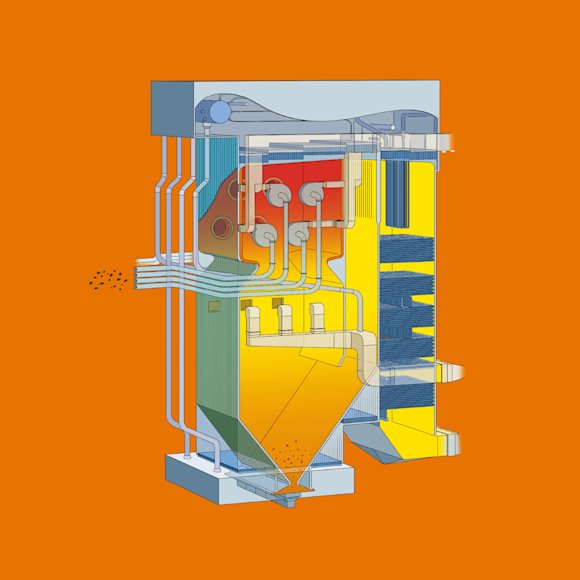
Generating steam by heating water or other media means that boilers are essential in many industries. Exactly for this reason, the effect of improvements in performance on the environment and on advances in manufacturing is immeasurable. Kawasaki has been involved in boiler production since 1880, and the engineers have accomplished the long-awaited development of the large Kawasaki UVF boiler (U-KACC) for oil refineries. Here is the introduction of an excellent idea that runs counter to previous formulas and enables twice the environmental performance of conventional boilers.
U-KACC features for achieving ultra-low-NOx, low-dust combustion
Boilers generate steam by heating water or other heat media. The steam they produce is used as process steam in a factory or as an energy source for generators and so on. The size of a boiler is measured in terms of the evaporation of high-temperature, high-pressure steam, which can reach as high as 3,000 tons per hour with a large boiler.
The history of Kawasaki’s boiler production dates back to 1880. To date, Kawasaki has supplied approximately 1,000 fuel-fired industrial boilers, mainly in the small to medium-size range. Kawasaki’s boilers boast outstanding stability, which is achieved through a mechanism that can absorb fluctuations in steam pressure caused by equipment that consumes steam. Kawasaki’s coal-fired boilers are remarkable for their versatility as well - they can accommodate any differences in the characteristics of coal mined in different regions. These features, combined with the boilers’ low malfunction rates, have led to their track record of safe and stable operation as well as the excellent reputation they enjoy.
Currently, Kawasaki’s engineers are working on the manufacture of the Kawasaki UVF boiler (U-KACC), which is scheduled for delivery in 2017 to an oil refinery, where it will be used to generate steam and electricity.
The U-KACC, the fourth boiler of the Kawasaki Advanced Clean Combustion (KACC) series, produces 295 tons of evaporation per hour. The latest boiler comes loaded with innovative technologies that are based on an idea that runs counter to the previous boilers in the series. Instead of using heavy oil as a fuel, it uses asphalt pitch, which is a difficult-to-burn residue that remains at the very end of the oil refining process. The U-KACC is a state-of-the-art boiler that makes full use of fossil fuels without producing any waste, and it is inexpensive to run thanks to low fuel costs.
The KACC series cut NOx emissions by 30-50%, and dust by as much as 60% compared to conventional low-NOx boilers. In addition to this excellent environmental performance, the U-KACC boiler incorporates numerous technologies to prevent various types of corrosion, ensuring safe operation and a long service life.
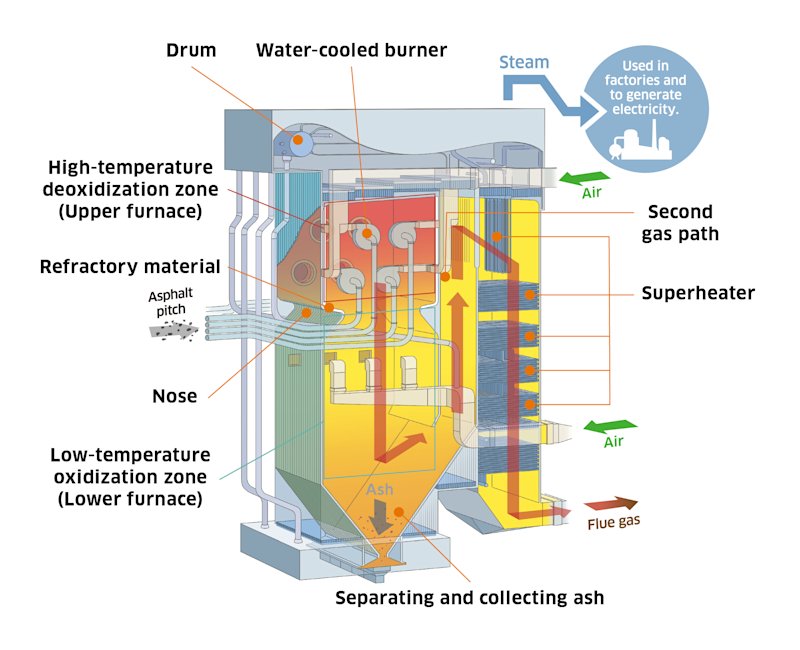
The "U" in U-KACC has three meanings: U-type flow, upside-down, and upgrade.
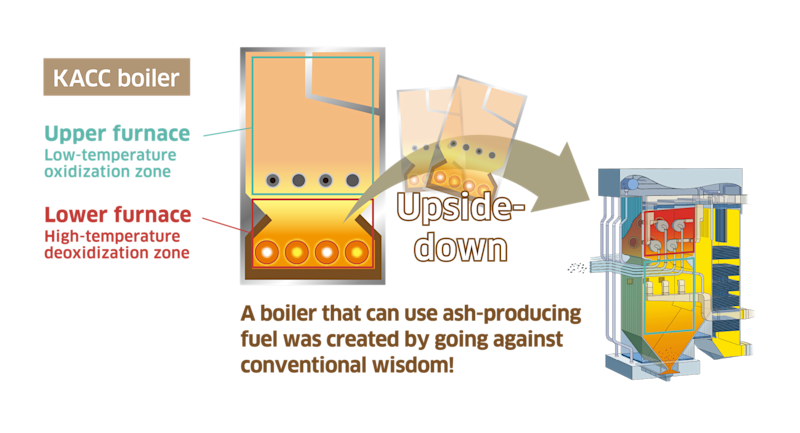
Use of composite tubes
The U-KACC boiler adopts composite tubes for the water wall tubes to reduce sulfurization deoxidization corrosion in the high-temperature deoxidization zone. These tubes use high-strength carbon steel for the inner layer and corrosion-resistant stainless steel for the outer layer to prevent corrosion.
As welding for composite tubes requires high skills, water wall of composite tube are manufactured at Kawasaki’s Harima Works.
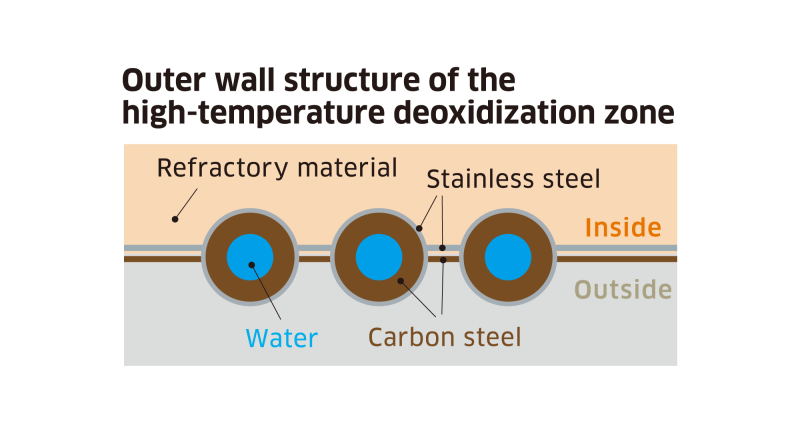
High-temperature deoxidization zone (Upper furnace)
Air (oxygen) needed for combustion is injected into the furnace in reduced amounts.
The nitrogen contained in the fuel is turned into nitrogen intermediates (e.g., NO, HCN). Subsequently, NO is deoxidized by the other intermediates and becomes N2, which reduces the generation of NOx.
Carbon contained in the fuel is gasified due to the high temperature.
Low-temperature oxidization zone (Lower furnace)
A sufficient amount of air (oxygen) is injected to facilitate combustion.
Secondary combustion air is introduced to cause low-temperature oxidization combus- tion. NOx generation can be reduced due to low-temperature combustion.
Gasified carbon is completely combusted to reduce the generation of unburned carbon, which becomes a cause of dust emission.
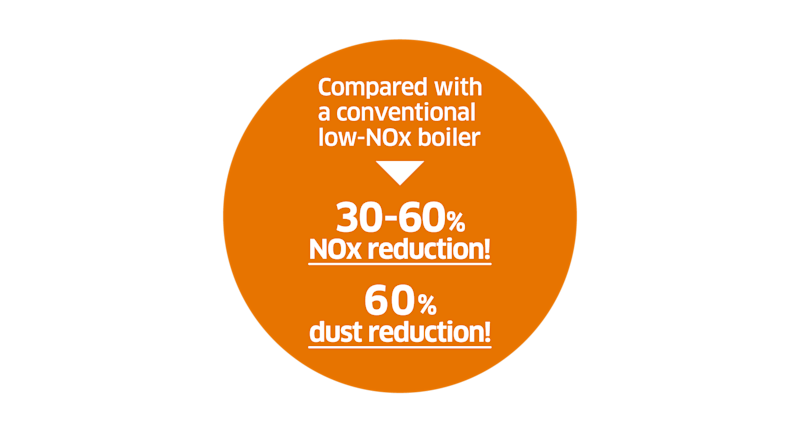
Refractory material
Affixed to the inner water wall of the high-temperature deoxidization zone.
Nose
A constriction that separates the furnace into a high-temperature deoxidization zone and a low-temperature oxidization zone by limiting the free flow of flue gas.
Drum
Separates saturated water and steam.
Water-cooled burner
Prevents the adhesion of asphalt pitch.
Separating and collecting ash
The ash separated from flue gas by the U-type flow in the low-temperature oxidization zone falls down to the discharge outlet.
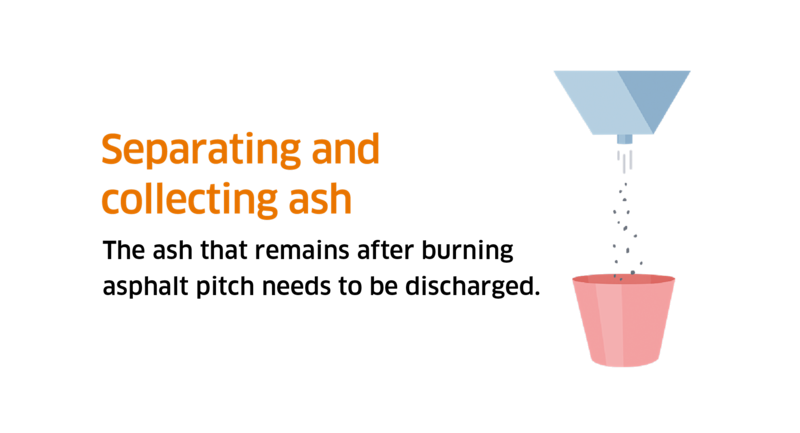
Second gas path
The empty gas path is another distinct feature of the U-KACC boiler. Flue gas leaving the furnace makes a U-type flow, separates ash, and then moves up this path, lowering the gas temperature to a suitable level during the process. This design prevents high-temperature corrosion in the superheater.
Superheater
The superheater superheats saturated steam in three stages. Spray water type steam temperature controlling devices (desuperheaters) are installed between superheaters to keep the steam temperature constant at the boiler outlet.
A Battle Against Collosion
Boilers burn fuel at high temperatures and use the hot flue gas to heat water and generate steam. Sulfur and corrosive heavy metal contained in fuel cause sulfurization deoxidization corrosion, high temperature corrosion due to vanadium ash, and other corrosion phenomena and ash adhesion inside the boiler. Effectively controlling these phenomena is key to the safe and stable operation of boilers.
The U-KACC boiler features numerous ideas and designs to prevent corrosion and ash adhesion.
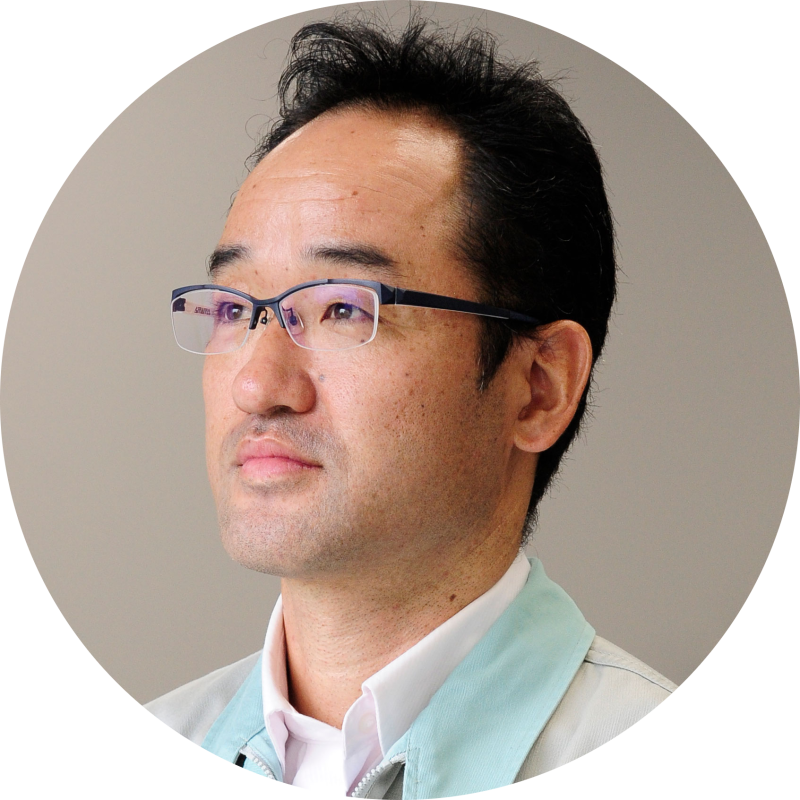
Boiler Design Department Section 1, Energy Plant Engineering Division Plant & Infrastructure Company,Kawasaki Heavy Industries, Ltd.
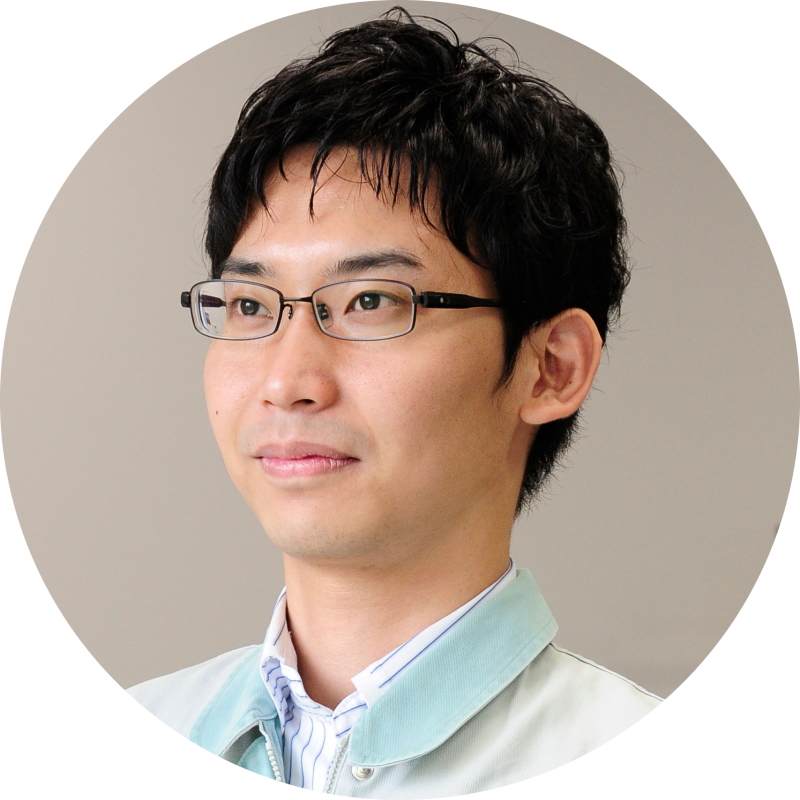