L30A Highly Efficient Gas Turbine L30A Featuring Hydrogen Combustion Technology
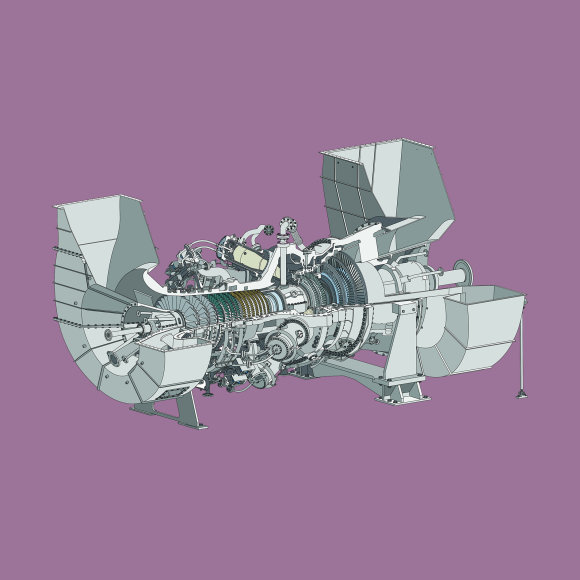
A gas turbine engine burns natural gas or utility gas to produce motive power. The L30A, a 30 MW (megawatt) class industrial gas turbine developed by Kawasaki in 2012, has achieved electrical efficiency that exceeds 40%, which is the world’s highest level in its class. Kawasaki’s long-cultivated expertise in small- and medium-size industrial gas turbines and its highly advanced elemental technologies for aircraft jet engines are combined to realize such performance.
World’s Highest Level 30 MW Class Gas Turbine
A gas turbine is a type of engine that burns natural gas or utility gas to produce motive power. First it draws in a large volume of air and compresses the air with a compressor. Inside the combustor, injected fuel is burned with the compressed air, and the resulting high-pressure, high-temperature gas drives the turbine. The rotating force of the turbine is harnessed to generate electricity, and recovered exhaust heat is utilized to produce steam.
The L30A, a 30 MW class gas turbine developed by Kawasaki in 2012, has achieved a class-leading electrical efficiency exceeding 40%. When incorporated into a cogeneration system, it can achieve a total thermal efficiency over 83%.
The proprietary combustor keeps nitrogen oxide (NOx) emissions at 15 ppm or less—the world’s highest level—and enables mixed combustion with hydrogen fuel, a technology that is attracting wide attention these days. For reference, 30 MW of electricity meets the power needs of 15,000 households.
The three key points in boosting electrical efficiency are air compression ratio, the temperature of gas at the turbine inlet, and component efficiency. Combining Kawasaki’s long-cultivated expertise in small- and medium-size industrial gas turbines and its highly sophisticated aircraft engine technology, the L30A delivers specifications that lead the world in its class.
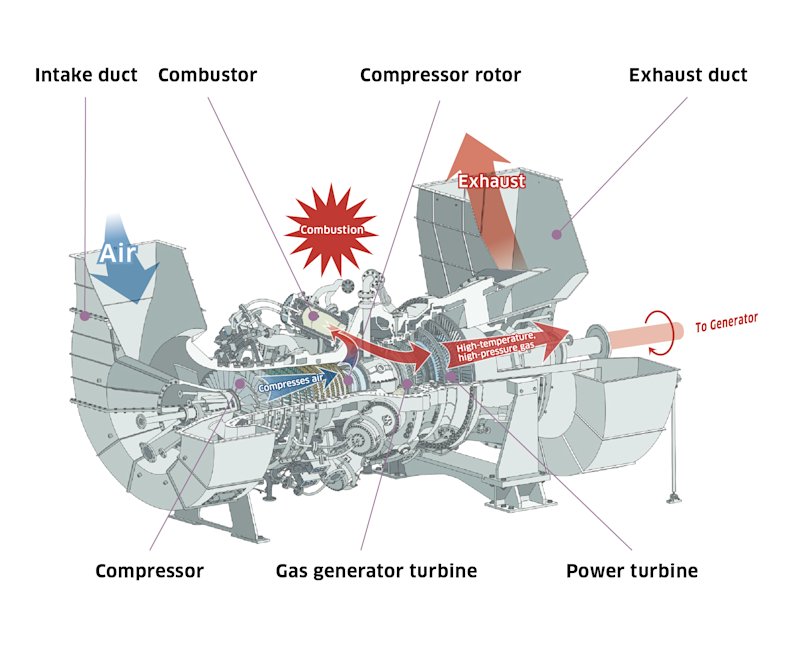
Electrical Efficiency of 40.1% No.1 Performance in the Popular 30 MW Class
The beginnings of Kawasaki’s industrial gas turbines go back to 1972. With proprietary technology, Kawasaki went on to create hit products such as the M7, which became Japan’s first cogeneration gas turbine in the 6-8 MW class to top a total production of 100 units. As Kawasaki got ready to enter the 30 MW class—the most competitive segment—with the L30A, its internal development departments and others worked together to achieve high efficiency leveraging the state-of-the-art design technology. Kawasaki’s L30A also boasts high overall efficiency in cogeneration, and draws attention from around the world with its superior performance.
Key considerations in gas turbine technology
There are three things to consider in the evolution of gas turbine technology.
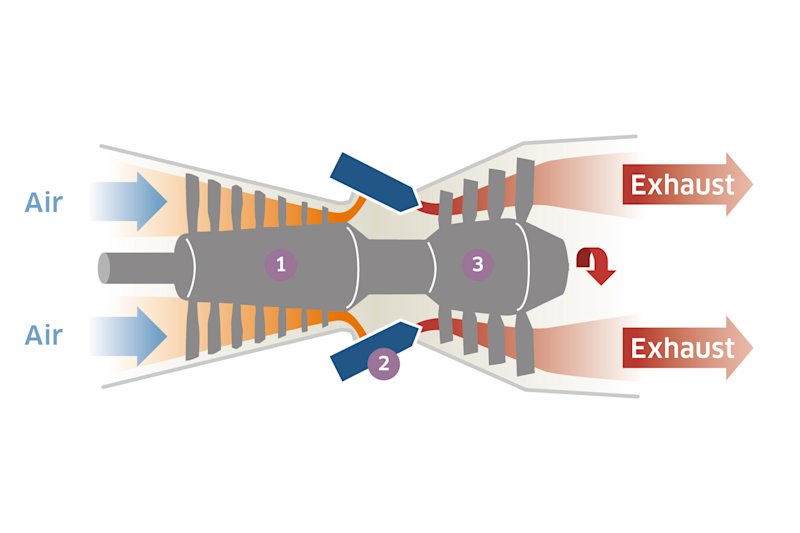
Designing the blade (cascade) geometry for efficiently compressing air
02 Combustor
Development of a mechanism and geometry that facilitate the mixture and uniform combustion of compressed air and fuel
03 Turbine
Development of materials and cooling technologies that can withstand high-temperature, high-pressure gas
Reduces CO2 by burning fuel mixed with hydrogen!
The L30A can use hydrogen, which produces no CO2, as supplementary fuel. It uses a supplementary firing combustion system called the dry low emissions (DLE) system featuring four supplemental firing burners provided for each combustor. This system achieves a mixed combustion ratio of up to 60% hydrogen (in volume), and achieves combustion in a manner that is tailored to the unique properties of hydrogen, namely, its high flame speed and high flame temperature.
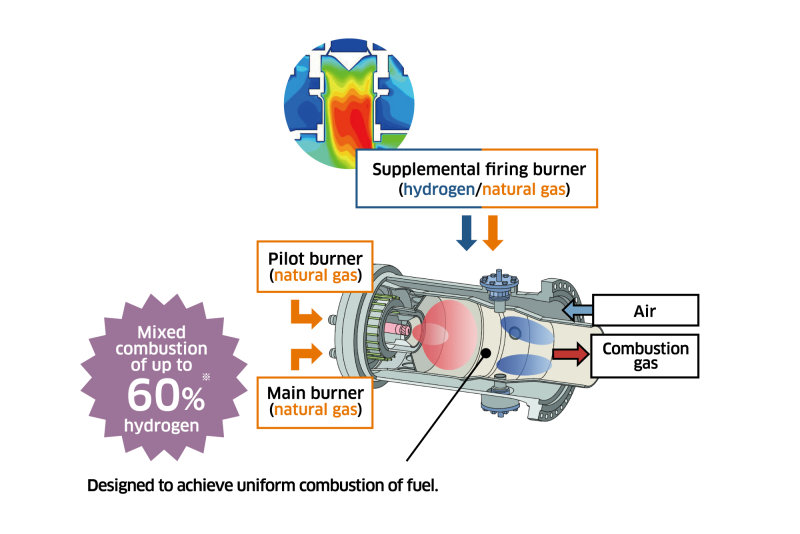
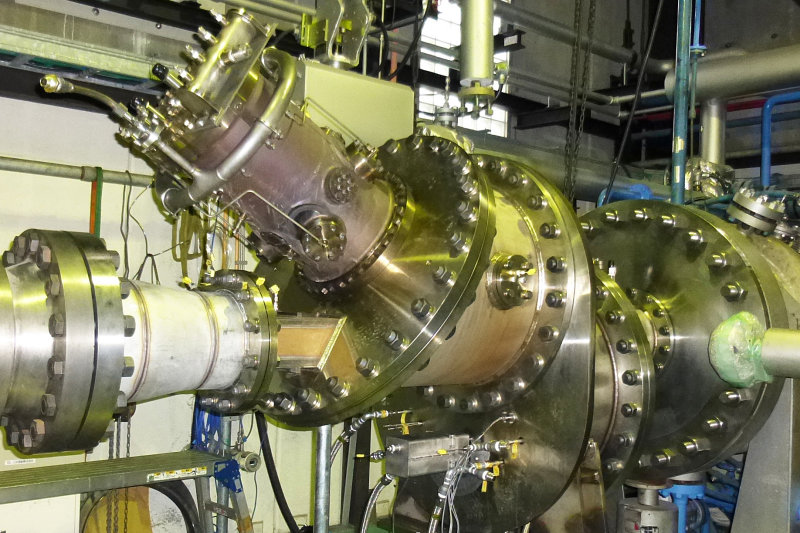
Intake duct
Draws in air from outside.
Compressor
Intake air is compressed as it passes through 14 stages of cascading turbine blades—a combination of rotor blade rows that rotate to increase pressure through kinetic energy, and stator blade rows that remain stationary to streamline the direction of air flow. State-of-the-art design technology enables air to be efficiently compressed to 24 atmospheric pressure.

Compressor rotor
Air becomes hotter as it gets compressed further. For this reason, the compressor rotor (rotation axis) is subjected to higher temperature toward the rear. To ensure sufficient strength under high temperature, the front half of the rotor is made of ferrous alloy, and the rear half heat-resistant nickel alloy. Kawasaki uses electron beam welding, a technology used to manufacture aircraft jet engines, to join two different types of metal into a single part.
Combustor
Generates high-temperature gas by injecting natural gas or other fuel into compressed air and burning the mixture. Features a proprietary lean premix combustion technology using eight combustors and three types of burners to keep low NOx emissions.
Gas generator turbine
Drives the compressor with rotating force generated by converting high-temperature, high-pressure gas generated in the combustor using a two-stage turbine. The gas temperature at the inlet reaches approximately 1,300°C, and Kawasaki uses its world-leading technology to develop turbine blades that can withstand this temperature.
Power turbine
Drives the power generator and other devices with rotating force generated by converting gas passed through the gas generator turbine using a three-stage turbine. Equipped with a tip shroud at the upper end of each turbine blade to facilitate the generation of rotating force.
Exhaust duct
The exhaust reaches a temperature of around 500°C. By harnessing this heat in a cogeneration system, an efficient use of energy is achieved.
Ease of maintenance

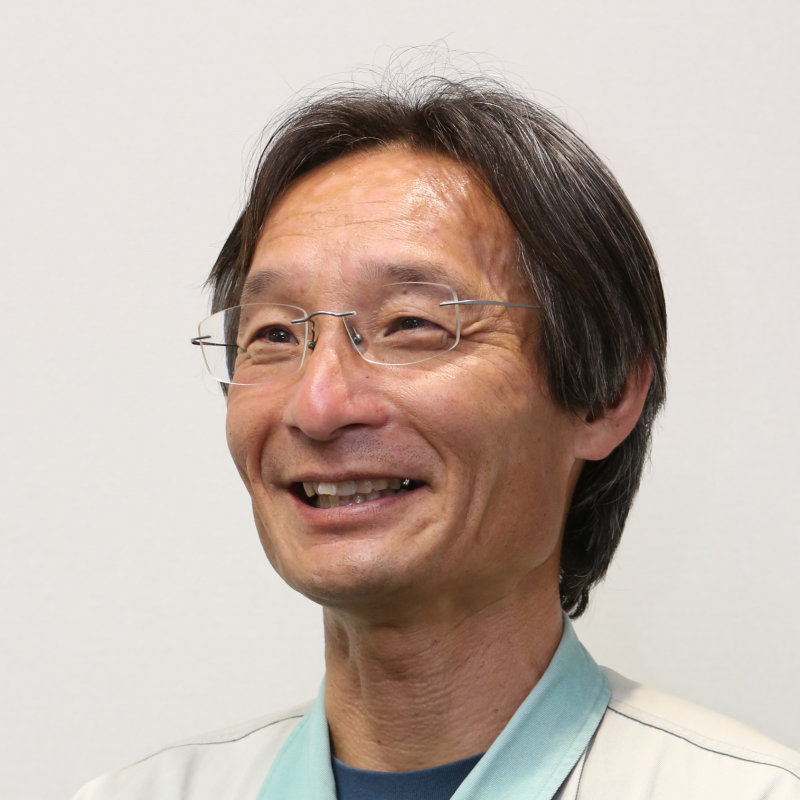
Planning Section
Gas Turbine Development Dept.
Engineering Center
Gas Turbine Division
Gas Turbine & Machinery Company
Kawasaki Heavy Industries, Ltd.
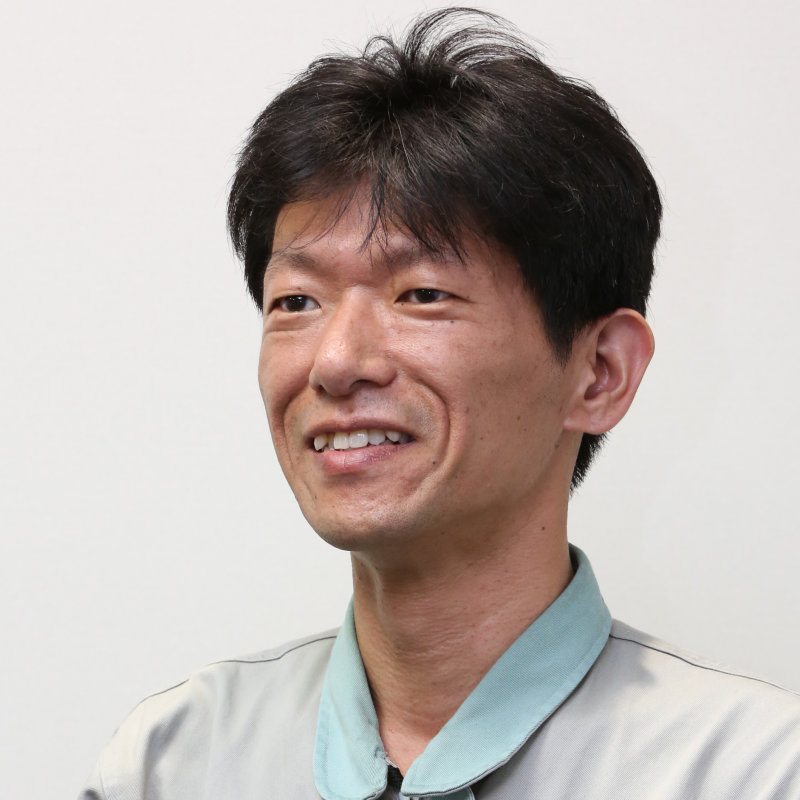
Combustor Section
Technology Dept.
Engineering Center
Gas Turbine Division
Gas Turbine & Machinery Company
Kawasaki Heavy Industries, Ltd.
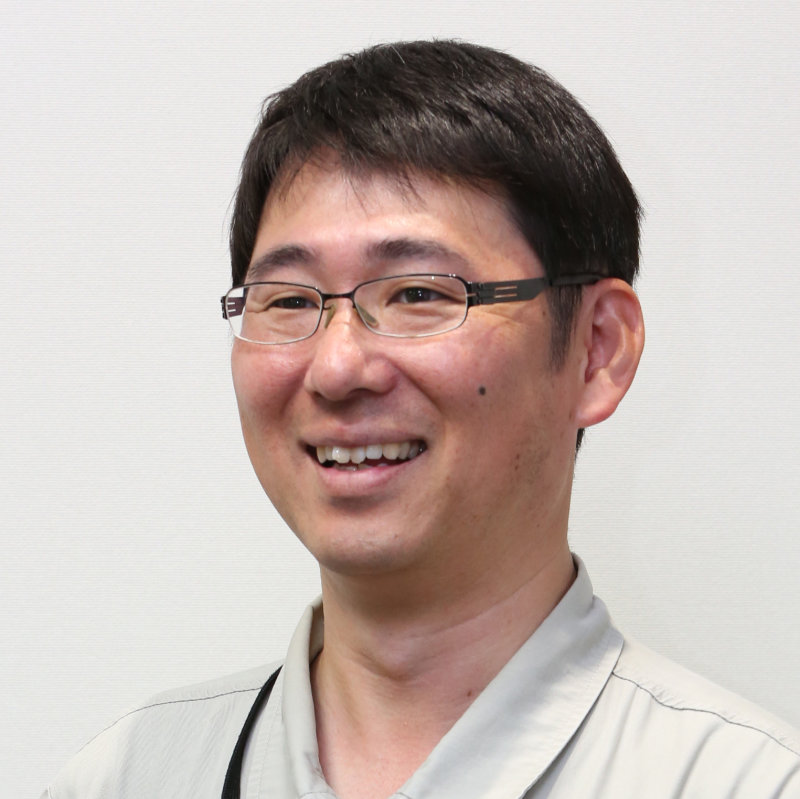
Development Section 1
Gas Turbine Development Dept.
Engineering Center
Gas Turbine Division
Gas Turbine & Machinery Company
Kawasaki Heavy Industries, Ltd.