Flying High in Achieving a Medical Revolution: The hinotori Robotic-Assisted Surgery System
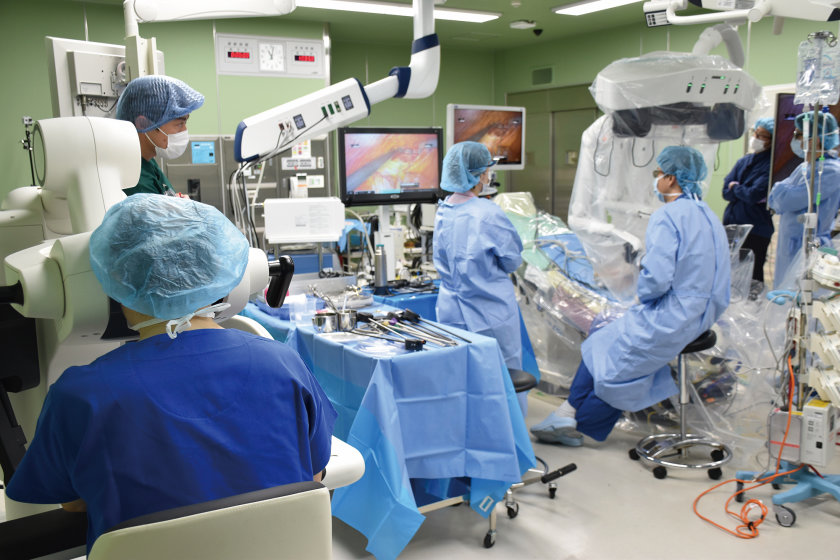
A long time ago, long before humankind knew of the production of iron, primitive medical devices already existed, and such devices were characterized by the use of bronze. Mesopotamia had already invented surgical knives around 2000 BC(*1). In the following 4000 years, including the scientific century, technologies developed exponentially. There has been a remarkable revolution in medicine thanks to advanced expertise in laser, ultrasonic, and nano technologies. Now in 2021, the rise of medical robots is attracting attention.
Vocation to Support Humans
On any given day, modern hospitals have robots working in many ways, such as delivery robots carrying pharmaceuticals and samples, wearable robots helping with rehabilitation, and assistive robots help to feed people. While the mission of most robots is to provide the labor done by people, the hinotori was developed not to replace humans but to provide support.
The surgical support robot allows teleoperation by a surgeon who observes camera images to manipulate robotic arms equipped with an endoscope or forceps. The concept of remote surgery emerged in the early 1970s and was originally devised by NASA to treat astronauts in space.*2
In the late 1980s, surgeons used monitor screens and other devices to initiate laparoscopic surgery to treat the affected areas. Because it is not open surgery and only involves the insertion of cylindrical surgical instruments through multiple incisions (ports) in a patient’s body, this now popular procedure is minimally invasive and reduces the physical impact on patients. However, the movement of conventional laparoscope forceps was linear and lacked flexibility, and only two-dimensional images with limited viewing angles were available.*3
On the other hand, the surgical support robot with its multi-joint arms offers a high degree of freedom of movement, provides three-dimensional (3D) images, facilitates the sense of depth, and allows the surgeon to operate the movable arms and hands with vision close to those of humans. Currently, the da Vinci Surgical System, manufactured by Intuitive Surgical, Inc., of the United States, dominates the surgical robot market. The system was released in 1999 and approved by the US Food and Drug Administration (FDA) in 2000. Since then, about 5,500 units have been in operation worldwide and now carry out more than 1.2 million procedures a year.*4
*1 : Jo Marchant, “Scalpels and skulls point to Bronze Age brain surgery”, New Scientist
*2 : J.Kenneth Salisbury Jr., Ph.D., “Robotic technology in surgery: Past, present, and future” , American Journal of surgery
*3 : Grzegorz S. Litynski, “Mouret, Dubois, and Perissat: The Laparoscopic Breakthrough in Europe (1987-1988)” , Jornal of The Society of Laparoscopic & Robotic Surgeons
*4 : Press release of Intuitive Surgical on January 13, 2021
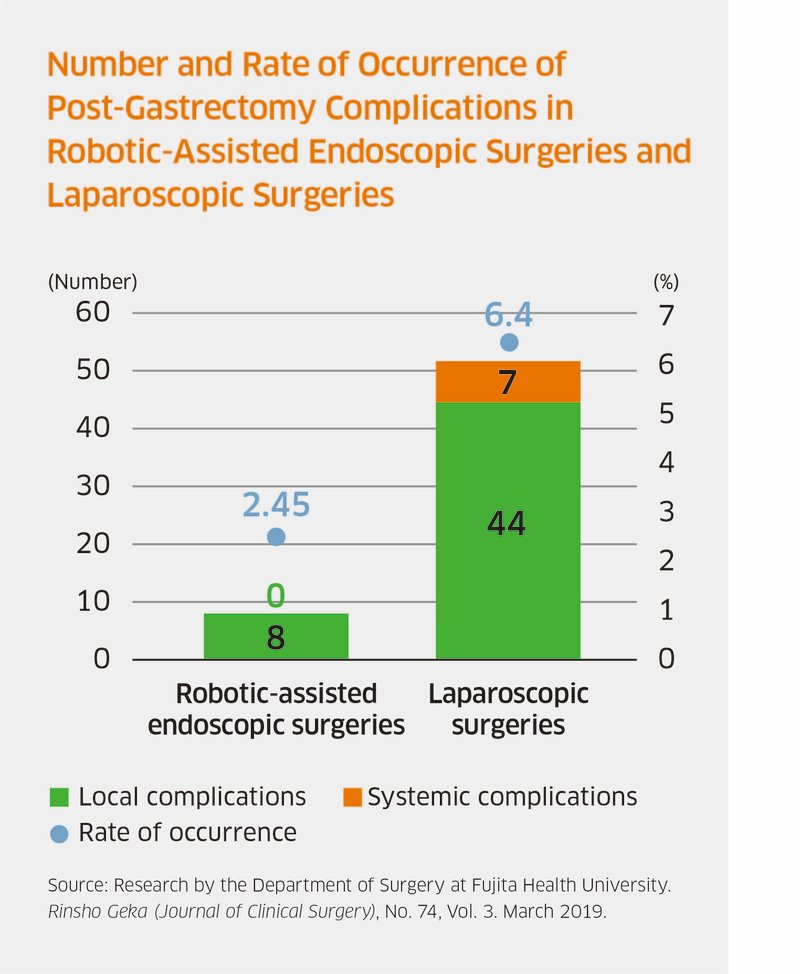
For Healthcare Professionals Saving Lives
The hinotori by Medicaroid, which was formed as a joint venture by Kawasaki and Sysmex Corporation, endeavors to enter the market monopolized by the mighty da Vinci. The partnership between Kawasaki, a leader in the world of industrial robots, and Sysmex, with its abundant expertise and networks in the field of advanced medicine, released the first made-in-Japan robotic-assisted surgery system in 2020.
The new system was named after the masterpiece manga series, Hi no Tori (Phoenix), created by Osamu Tezuka. The name represents the will to support medical professionals who constantly deal in matters of life and death, just as Osamu Tezuka illustrated the value of life along with the phoenix.
Kawasaki’s specialties are in the art of producing robots with excellent maneuverability as exemplified by arms capable of fine operation (manipulators) and its sophisticated sensors. Since the introduction of the first industrial robot in Japan in 1969, the company has always been a leader for more than 50 years. Kawasaki has also handled many robots for semiconductor manufacturing and pharmaceutical processes that must be absolutely clean, which guarantees a solid background.
Thus, the hinotori development started in 2015. The elite engineers who had created Kawasaki’s robots worked on this long-awaited project, and it did not take long until the robot reached the level of dexterity to peel a grape. However, they were perplexed by comments from surgeons in the actual fields of medicine. Raizo Yamaguchi, vice director of the International Clinical Cancer Research Center (ICCRC) of Kobe University Hospital, who is a urologist with extensive expertise in robotic-assisted surgeries, recalls, “What was challenging was getting the engineers to understand what surgeons felt and experienced during surgery.”
Yamaguchi related a parable of a helicopter and a sports car to explain what was expected of a surgical support robot. “If an industrial robot fails, we can simply deactivate it, but can we do the same with a helicopter in flight? When faced with problems, a pilot must be able to maintain control of the aircraft as long as possible. The same goes for the robotic-assisted surgery system.” He continues, “Engineers tend to be conservative, thinking it’s dangerous if a knife is too sharp, but surgeons are confident in their ability to control sharp knives. We want a robot to be like a luxurious, high-performance, highly responsive sports car, but with redundant safeguards that permit the driver to use as many driving techniques as possible.” This parable specifically identified the technological challenges to be resolved by the engineers.
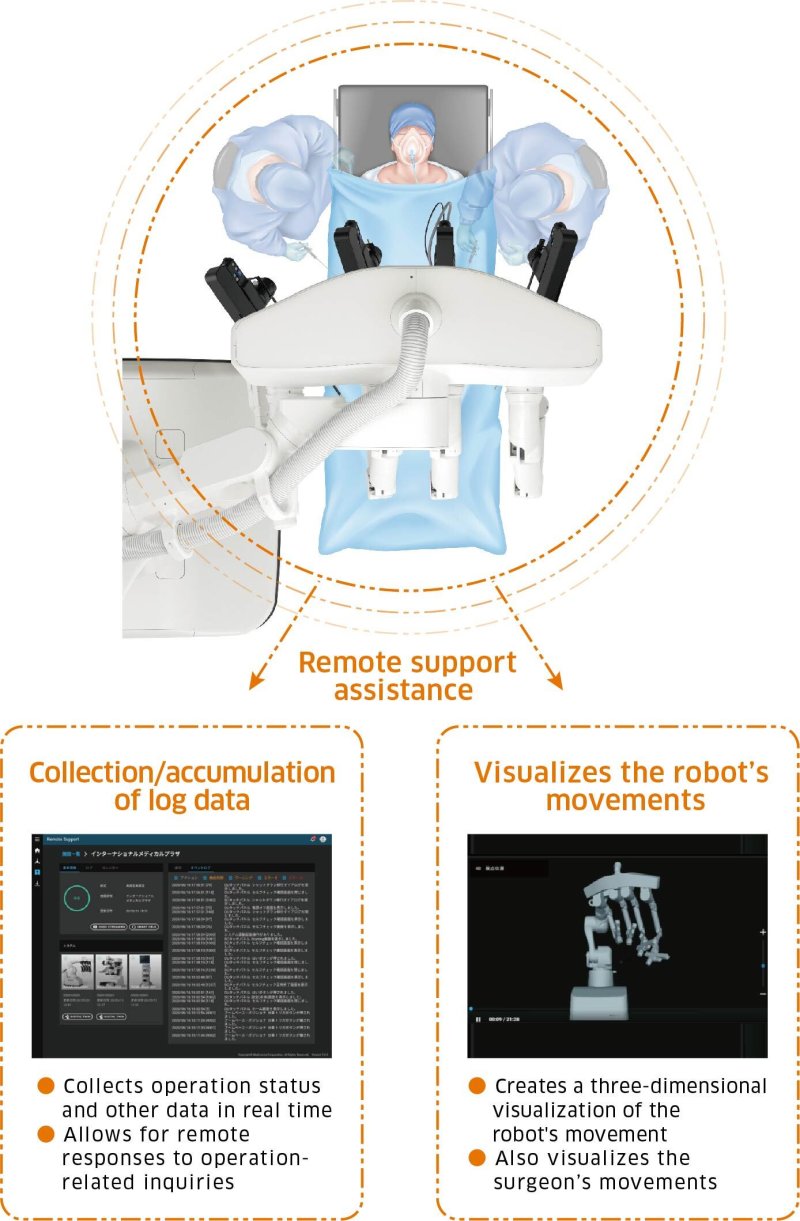
What is Medicaroid?
Medicaroid Corporation is a medical robot manufacturing and sales company, formed in 2013 as a joint venture between Kawasaki and Sysmex Corporation. The company name was created from the terms Medical and Android with the aim of having robots serve and support humans rather than replace humans. Production and distribution approval was obtained for the hinotori™ Surgical Robot System, Japan's first robotic-assisted surgery system, in August 2020.
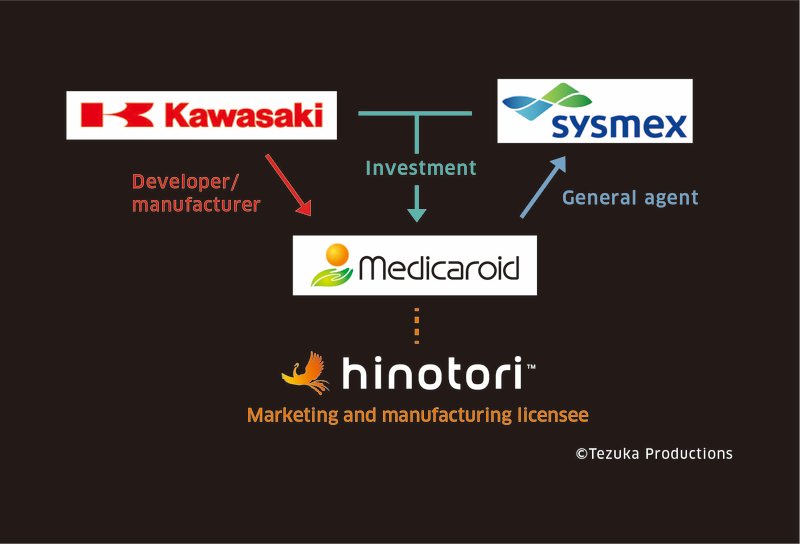
Growing demand for surgical support robots
The use of a robotic-assisted surgery system brings advantages not only to patients, including small incisions for the surgery, slight bleeding, and quick recovery, but also to surgeons in reducing the physical burden. Because they are not forced to maintain a stressful posture for prolonged periods and the high-resolution images help eyesight, the system is expected to extend their professional lives of surgeons. The market research and consulting firm from the United States, MarketsandMarkets, projects that the size of the surgical robot market will grow by 17.6% from 2021 to 2026.
Robotic Arms More Flexible than Human Ones
Three major components comprise the hinotori: (1) the operation unit positioned beside the patient and consisting of a cart and four arms with endoscope, forceps, or various instruments; (2) the surgeon’s cockpit, where the surgeon is seated to operate at a short distance; and (3) the vision unit to provide high-definition 3D images.
Tsuyoshi Tojo, the senior staff officer from Kawasaki who led the development project, finally determined three key concepts in the development of the hinotori: compactness, high-level safety, and maximum maneuverability. The size was reduced to fit the relatively small operating rooms in Japan, and the robotic arms were designed to match the width of the human arm, which had the favorable effect of not overwhelming the patient. However, this compactness was a hurdle to the development project.
Although it is a robot, the hinotori never moves autonomously. The system’s four arms and the instruments at the tips of the arms are tools that act as the surgeon’s eyes and hands to see, explore, grasp, cut, and suture. Each arm provides an eight-axis configuration, which means the degrees of freedom are greater than ordinary industrial robots with six and the human arm with seven. On top, the four-axis motion control of each instrument is added for a total of twelve axes that can achieve smooth, flexible motion.
Meanwhile, when the four compact arms can move freely, the risk of interference increases. A collision of the arms followed by a system stop during surgery may have serious consequences. Therefore, elaborate control of the arms was considered a crucial requirement.
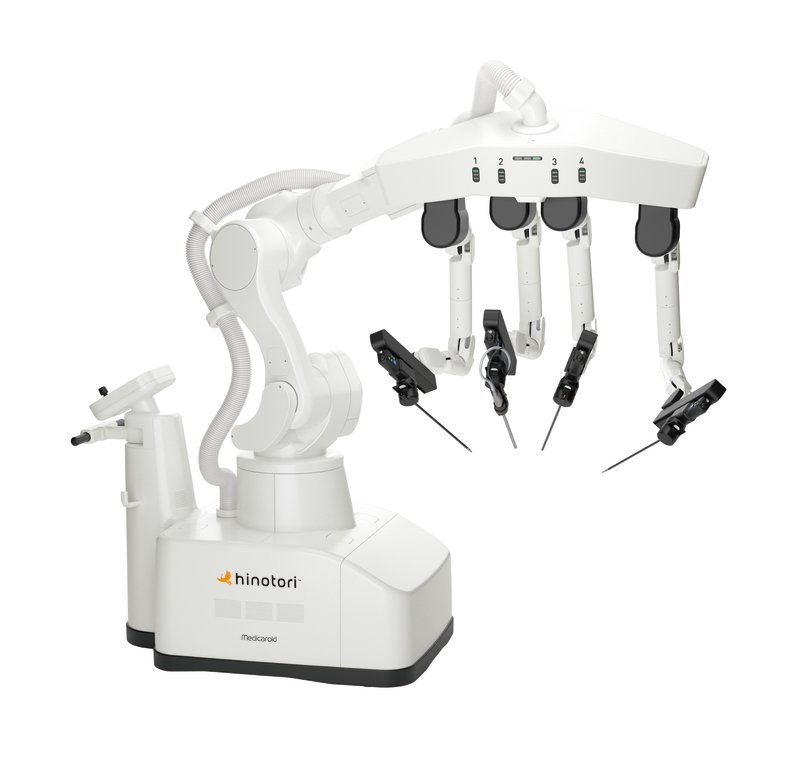
This unit is comprised of cart (the base underrneath the robot's body), the positioner (middle section), the arm base (upper section), and four operation arms. The cart contains the Central Control Unit, which coordinates with the four controllers of the arms. The four arms are comprised of an endoscope, two forceps for securing organs or lifting them up and out of the way.
ⓒTezuka Production
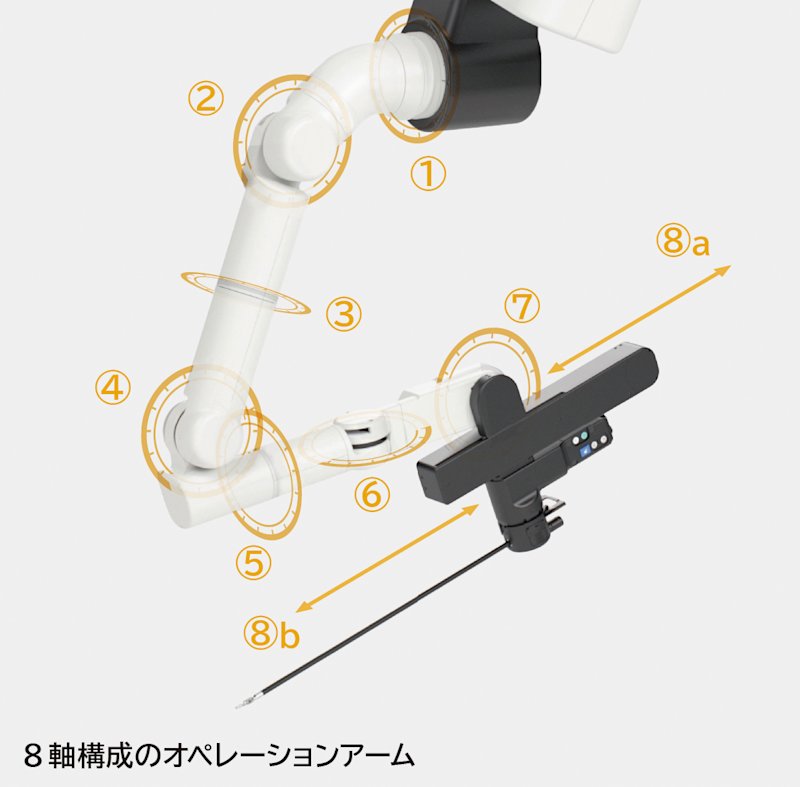
These eight-axis arms of the hinotori are capable of various movements on a par with those of human arms. At the ends of the arms, instruments(e.g., anendoscope and forceps) are attached, which are themselves capable of four-axis movements.
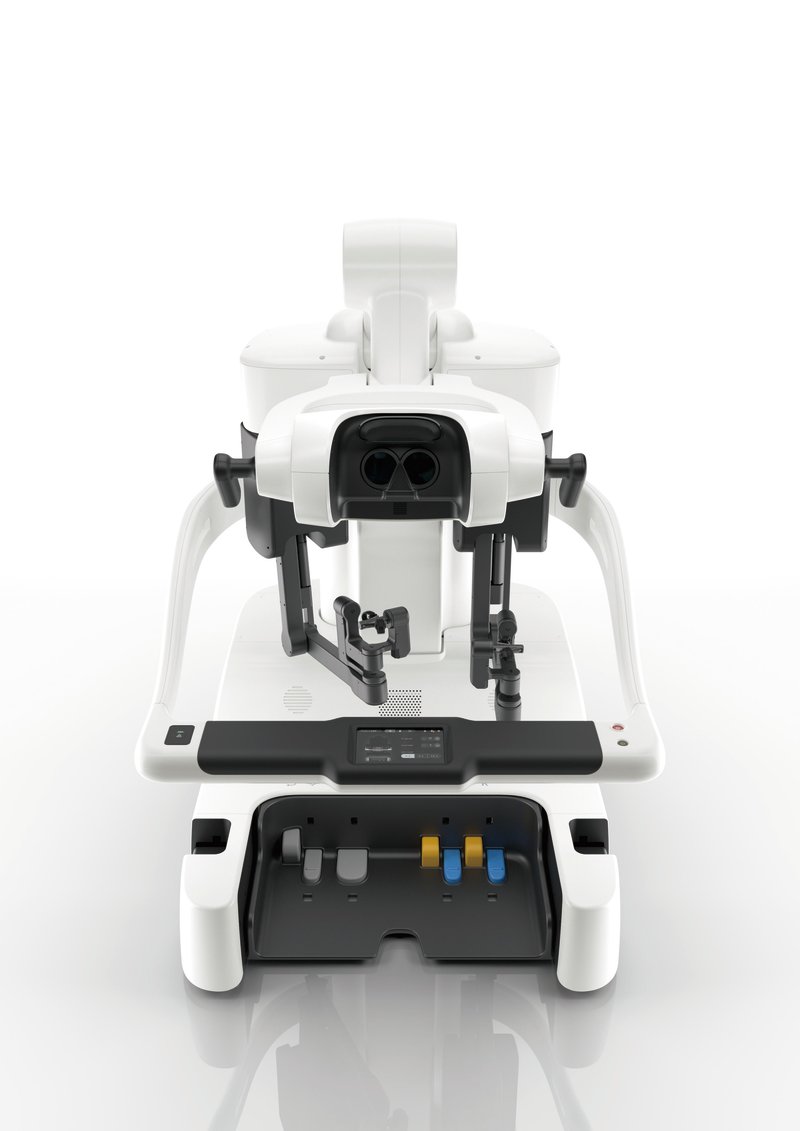
This is a cnsole where the surgeon operates the robot, using two hand controls and a foot switch, with the 3D endoscopic image displayed on a monitor. The cock pit can adjust its position according to the posture the surgeon takes.
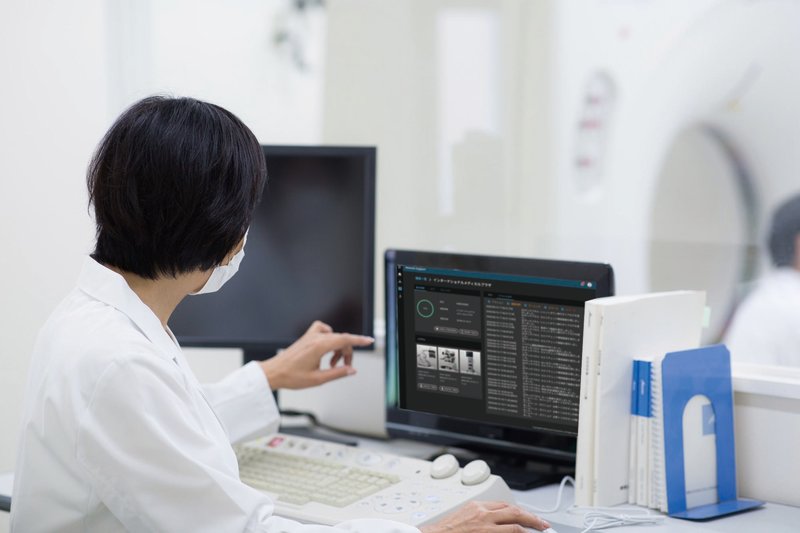
Special chair for the hinotori developed by Okamura, the renowned manufacturer
Okamura, a leading manufacturer of office furniture in Japan, developed a dedicated chair for the hinotori named the kumpel. In collaboration with Medicaroid and Kobe University, they observed the posture of surgeons during operations and designed the chair to support the good posture of the operator without a pelvic tilt in order to reduce the fatigue from long surgeries. The seat inclines by up to five degrees forward and has a V-tip shape with a short depth in consideration of the use of foot pedal switches. The chair back also has a special profile so that the surgeon can rotate the shoulders during breaks.
*3: About kumpel
18 Trillion Simulations Conducted
Hirofumi Yamamori, who was in charge of developing the controls, comments, “Because each arm has to reach the target area through an incision that cannot be relocated, the arms must have a large operating range. Even when attempting to move an arm straight forward, the control process is still very complex because of the positions of the other arms and the angles of the joints.” The most favorable movement of an arm is not always the best option for the four as a whole. While visiting operating rooms to observe how surgeons move their arms and hands, and receiving their feedback, the developers repeated the trial-and-error process in steps to formulate a control method that would achieve the smooth operation of each arm without colliding with one another. They also conducted computerized simulations totaling 18 trillion sessions to identify the optimal control algorithms.
Size reduction also posed challenges to the mechanical design. The senior staff officer at Kawasaki, Wataru Doi, recalls, “If we make the arm thin to keep the device compact, the arm’s instrument becomes unsteady. If we try to use a long, thin part to make the operating range greater, the thinness means the arm cannot support its own weight. It took repeated efforts to find the optimal balance between the mechanical aspects of the system and software controls.” What served to resolve the problem was the combination of a high-output motor and a new reduction gear developed by Kawasaki together with a parts manufacturer. Tojo mentions the outcome, “The compact design optimizes the lines of movement around the operating table and provides ample space for the surgeon’s hands. We were able to generate advantages that benefit not only the surgeons but also the entire operating team.”
The Feel of Manipulation Depends on the Yoke
The surgeon cockpit has hand controls with finger operation, which is equivalent to a vehicle steering wheel and an aircraft yoke, and is the very component directly related to the capability to manipulate the system at will. Surgeons requested that the hand controls give the tactile sensation of being as light as air. It was a challenge, and Doi did not know how to fulfill such a request from an engineering perspective.
The key to resolving this issue was the gear reduction ratio. Because the hand control transmits a sense of heaviness when the friction increases between the motor and the reduction gear, the developers lowered the gear reduction ratio to decrease the friction. They added software sensory compensation to establish the best feel through integration of both the mechanical design and software control.
A dual monitoring system was employed for the other concept of development, for reasons of safety. The robot remains deactivated unless the sensor in the 3D viewer detects the surgeon’s gaze. In addition, an alarm is activated if the arms interfere with each other. However, according to Yamamori, the system allows a skillful surgeon to continue the procedure by careful manipulation even if the arms are about to collide or if an arm reaches the limit of its operating range.
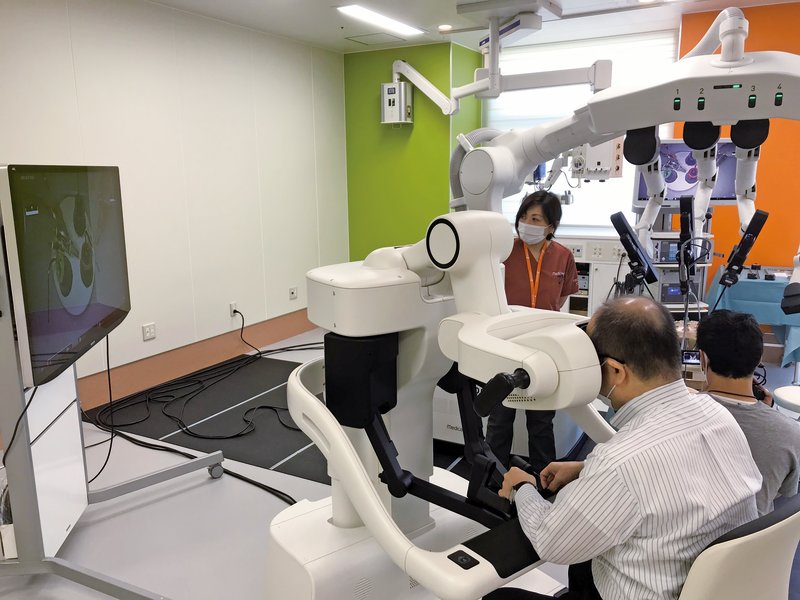
5G and 6G Networks will Expand the Possibility of the hinotori
On December 14, 2020, a press conference was held at ICCRC on the success of the initial surgery using the first domestically produced robotic-assisted surgery system, the hinotori. Dr. Masato Fujisawa, dean of the Kobe University Graduate School of Medicine (present-day president of Kobe University), who had been an advisor in the development of the hinotori system, operated the system for a total prostatectomy.
Subsequent to the more than four hours of surgery, Dr. Fujisawa commented to the press, “I’d score the manipulation perfect,” and said that he was extremely moved by the fact that they had achieved societal implementation of a new medical device.
The system also enjoyed success at a second facility, Wakayama Medical University, and a third, Tokushima University Hospital as well in April 2021. Where in the world is the hinotori going to fly for more records of accomplishment? Tojo foresees future possibilities, “We still have many issues to resolve, including virtual pre-operation simulations incorporating CT-scan images, the automation of simple suturing, and the inheritance of experienced surgical skills.”
Regarding the prospective evolution of surgical robots, Yamaguchi of the ICCRC reports that three navigational features will be subject to critical improvements: “One will be to enhance the level of procedural precision using accurately visualized images of the surgical field obtained by injecting fluorescent dye. Another will be to accumulate and analyze data from robotic surgeries performed by expert surgeons so that their expertise can be leveraged as best-practice examples. Finally, the advancement of telesurgery using 5G and 6G (5th- and 6th-generation) communication systems is also vital.” Some parties now positively encourage verification tests for real-time transmission of 8K images with the 5G communication system. Once the next-generation high-speed communication networks are popularized more broadly, telesurgery would be possible between remote locations without a time lag.
As the first step in proving this idea, on April 16, 2021, Medicaroid announced the initiation of the first demonstration experiment in the world to remotely control the made-in-Japan robotic-assisted surgery system via commercial 5G networks. The idea is that high-definition 3D surgical images and robot control signals are transmitted in real-time by means of NTT Docomo’s commercial 5G and cloud services, and the first target is to realize telesurgery support through this system, in other words, the doctor on-site uses the surgical support robot to carry out a procedure with the assistance of a skillful surgeon in the robot cockpit from a remote location.
The 5G technology and the hinotori system intend to create a society where everyone can receive equal quality healthcare services. Widespread, societal implementation of surgical support robots will bring advanced surgical practices to towns without specialists and borderlands isolated by the ocean. If trips to the Moon are common in the future, a travel agency brochure might contain an exciting copy: Take it easy! Doctors on Earth will take care of you if you get sick on the Moon.
Robotic automation of PCR testing that would affect staff in a healthcare setting
Kawasaki, together with Sysmex and Medicaroid, quickly developed a fully automated robotic PCR testing system for COVID-19, which can handle up to 2,500 samples a day. The testing system significantly reduces the burden on healthcare professionals and features rapid testing in about 80 minutes. The space-saving design means the system can be dispatched in a 40-foot container to event venues in different places as a traveling test site.
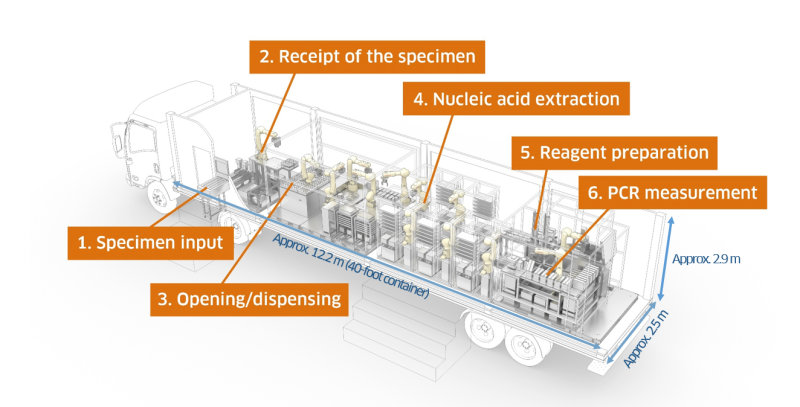
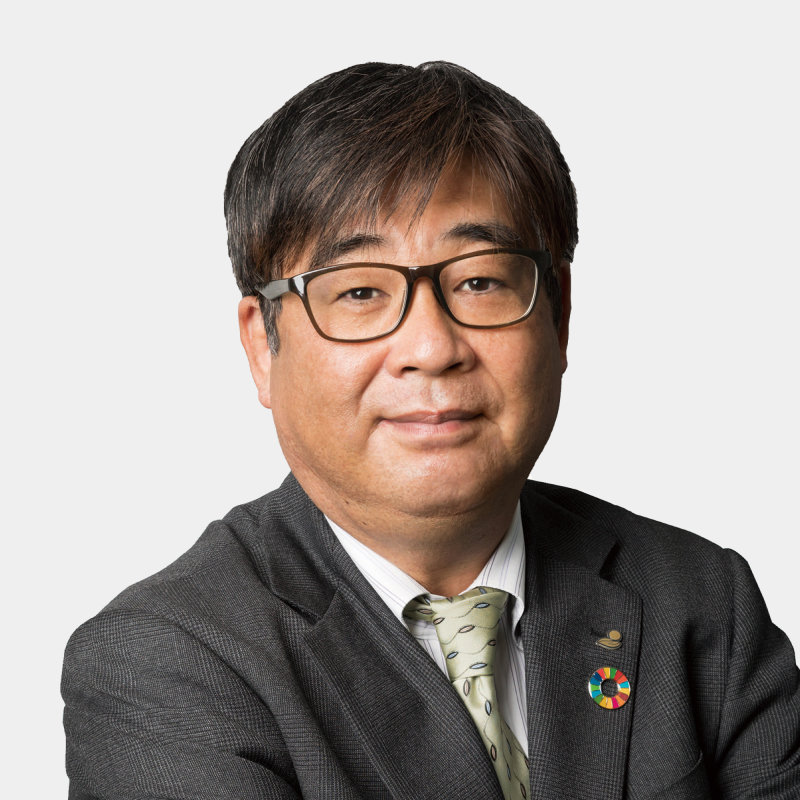
Medicaroid Corporation
Striving to Realize the Ideal Embodied in hinotori’s Name
The development of the hinotori resulted from the collective passion of Kawasaki President Yasuhiko Hashimoto, Sysmex CEO Hisashi Ietsugu, and many others. We had long been frustrated that world-class industrial robot technologies had not yet been applied in the healthcare industry. In fact, the industry was eager for domestically produced medical robots as was evidenced from business feasibility studies in which many physicians expressed support, making such comments as “Existing robots are too costly and make procedures unprofitable,” and, “Producing robots in Japan will allow us to work with manufacturers to continue upgrading them.” The steady advancement in minimally invasive surgeries—as seen in the transition from open surgery to laparoscopic surgery to robotic surgery—also propelled us to initiate development.
Once the decision was made, the engineers at Kawasaki, Sysmex, and Medicaroid worked very hard, day and night. Another driver was Kobe City’s plan to build its Biochemical Industrial Cluster, in which Medicaroid was a partnering firm. This facilitated our collaboration with medical institutions and the manufacturers of medical equipment parts located on Kobe’s Port Island along with Medicaroid. A marketing and manufacturing license from the Ministry of Health, Labour and Welfare was granted in August 2020, which was followed by the first successful surgery in December. Putting us at the forefront of this medical revolution, 2020 therefore turned out to be a year of great excitement.
There remain many challenges to overcome in order for the hinotori to be implemented widely and to achieve further technological advancements. We must devise flexible programs to encourage adoption of the system by mid-sized and small hospitals, such as leasing programs and pay-per-use systems. We also need to have more training centers to teach proctors (physicians who act as instructors). Formation of a users’ club to collect enhancement ideas is also needed so that we can upgrade the hinotori to an even more physician-friendly system and make more robotic procedures subject to insurance coverage. An initiative using AI-based systems to reproduce the expert skills of surgeons and another realizing telesurgeries using high-speed communication lines are underway, as are preparations to obtain approval from the US FDA.
In addition to surgical robots, we are now strengthening our applied robotics business, whereby industrial robots are used for medical applications without major alterations to the basic structure. One such example would be a robotic polymerase chain reaction (PCR) testing system. Medicaroid, Kawasaki, and Sysmex are committed to working together with healthcare professionals to enhance the dignity of life, the ideal embodied in the name hinotori.
Japan is an industrial robot power. However, when it comes to medical robots, inspection and diagnostic systems are mainly addressed, and we were one step behind in the field of surgical support robots. The hinotori system changed the dynamics. Kawasaki has been cultivating industrial robot technologies for more than a half century, and the first made-in-Japan robotic-assisted surgery system, the hinotori, was born on such a foundation. Marvelously inheriting the DNA of Kawasaki robots, the compact surgical robot with superior manipulability offers excellent support for healthcare professionals at the forefront of medical practice to achieve quality in medicine between patients all over the world.
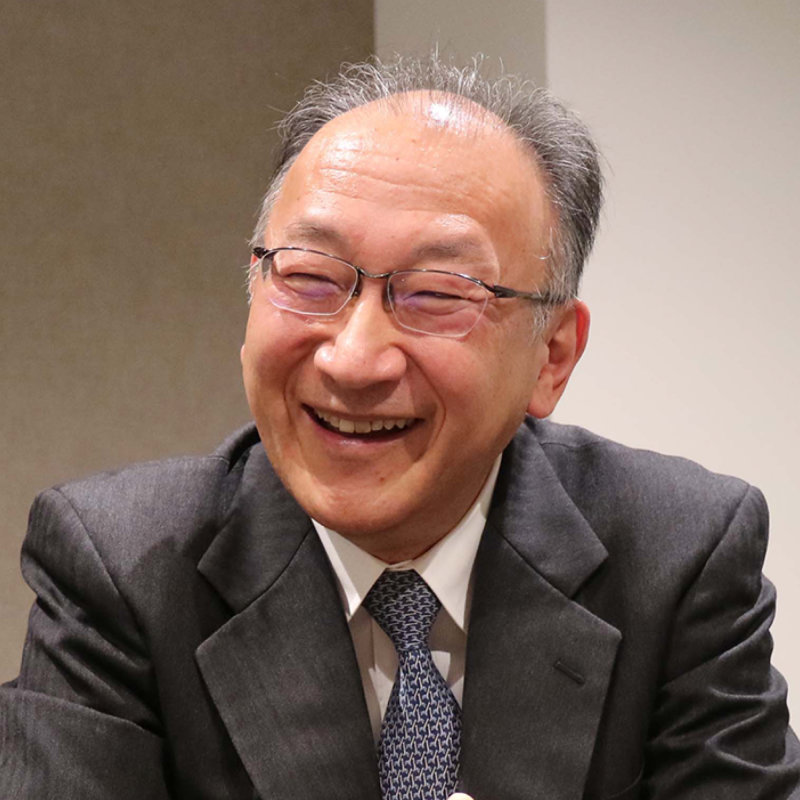
Hospital International Clinical Cancer Reserch Center
Kobe University
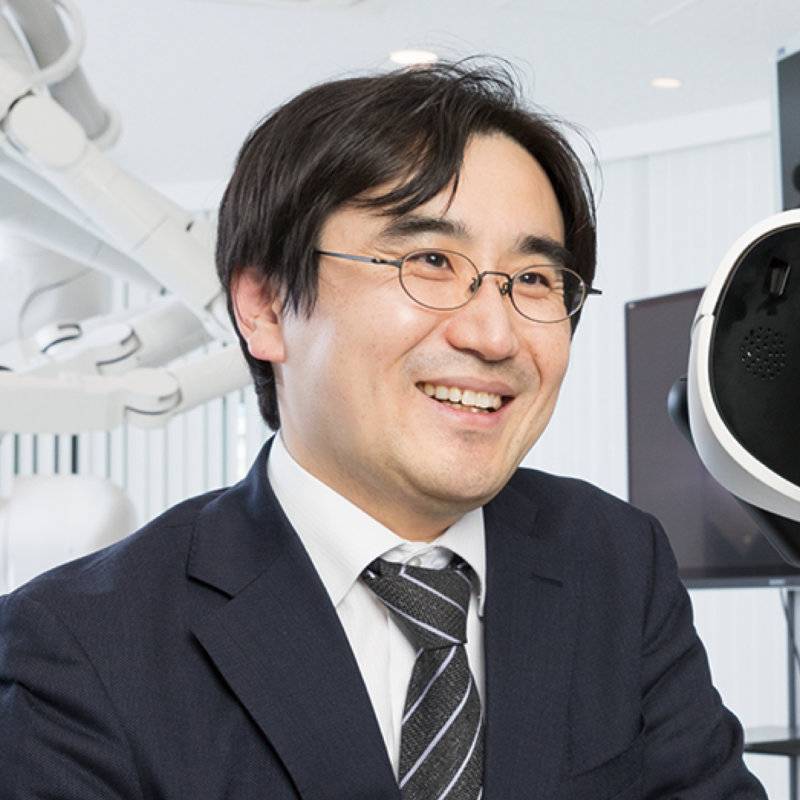
Medical Robot Section 2
Medical Robot Department
Medical Robot Group
Robot Business Division
Precision Machinely & Robot Company
Kawasaki Heavy Industries, Ltd.

Medical Robot Section 2
Medical Robot Department
Medical Robot Group
Robot Business Division
Precision Machinely & Robot Company
Kawasaki Heavy Industries, Ltd.

Medical Robot Section 1
Medical Robot Department
Medical Robot Group
Robot Business Division
Precision Machinely & Robot Company
Kawasaki Heavy Industries, Ltd.