Kawasaki’s Robotics: Five Decades of Pursuits that Transformed the World’s Manufacturing Scene
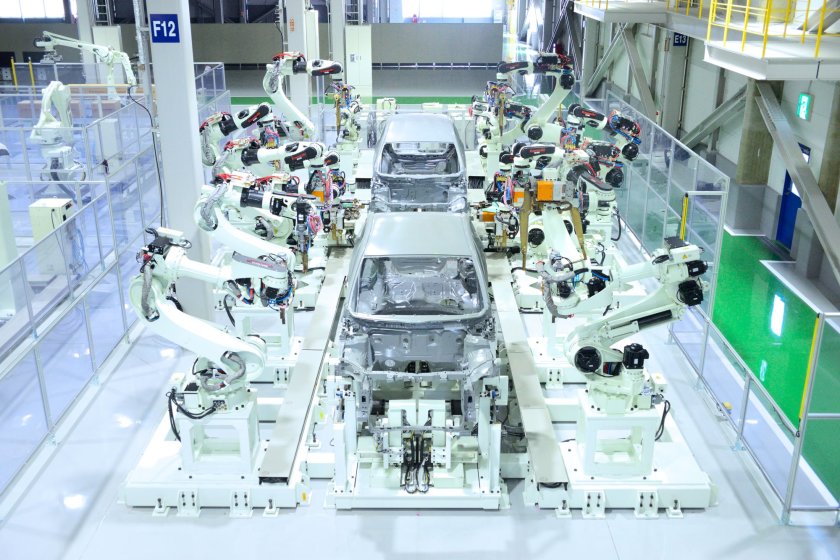
2018 marks the 50th anniversary of the launch of Kawasaki’s industrial robot business. Its half-a-century-long journey represents the chronology not only of Japan’s industrial utilization of robots but also that of the world, demonstrating that Kawasaki has always been a global leader in this sector. Today, the company is presenting to the world a new frontier in robotics applications.
Founder- and Leader- of Industrial Robot Technology for Half a Century
In 1966, an American scientist was invited to Japan as a lecturer on industrial robots. The scientist was Dr. Joseph Engelberger, who is regarded as “the Father of Robotics,” and the host was Kawasaki Heavy Industries (then Kawasaki Aircraft).
Dr. Engelberger was a founder of Unimation, the world’s first industrial robot manufacturer, which had earlier launched an industrial robot, "Unimate." Despite his expectation that only about 10 people would turn up at the lecture, based on his experiences in the United States, more than 200 leaders of Japanese companies crowded the venue. As further evidence of their enthusiasm, a Q&A session which followed the lecture is said to have lasted for two hours.
As labor unions in the United States are basically formed around a single profession, the unions’ perception of industrial robots as a threat to the labor market in the 1960s had been hampering the growth of robotics applications. In Japan, however, interest in automated and unmanned manufacturing operations was heightening, as the economy was booming and the country was experiencing a severe shortage of young laborers. As a backdrop, the popular animated TV series, “Astro Boy,” which depicted robots as helpers of humans, combined with other positive images of robots, are also said to have worked favorably in familiarizing people with robots.
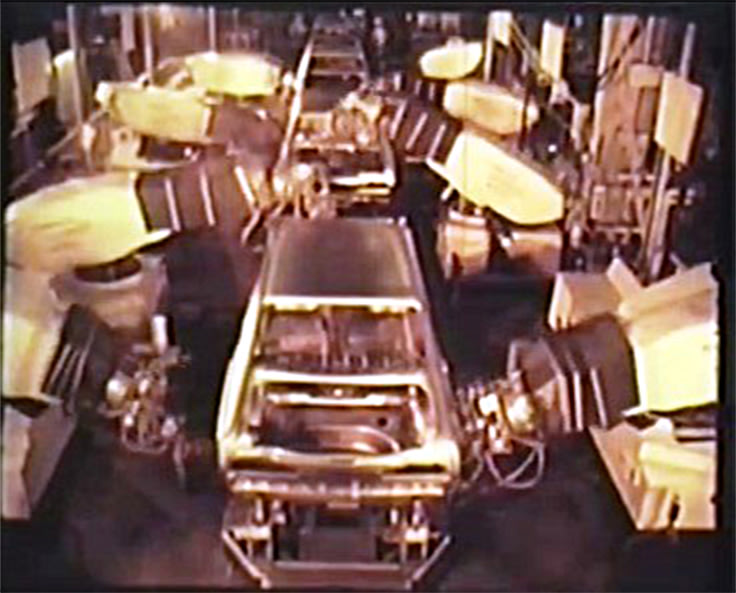
In 1968, Kawasaki entered a technological agreement with Unimation to develop domestically-produced industrial robots. This was the inception of Japan’s industrial robot business. This history, reaching its 50th year in 2018, is indeed the history of how the world has utilized robots for manufacturing.
A year later, in 1969, Kawasaki successfully launched Japan’s first hydraulic-powered robot, the “Kawasaki-Unimate 2000.” However, it was in 1973 that the robot business took a significant leap forward: Toyota Motor Corporation and Nissan Motor Corporation decided to use Kawasaki-Unimate for auto body spot welding. This decision by two prominent auto makers opened the floodgates for robotics applications in the Japanese auto industry.
And now, Kawasaki is disclosing a new vision regarding its robotics business for the next 50 years.
Technology Fusion Advanced by Japan’s Extensive Industrial Base
Five decades’ worth of industrial robot business has been a journey of continually pushing forward technological advancements. These innovations include the introduction of a servomotor (replacing the hydraulic or pneumatic motor) which achieves highly accurate control of the motor’s rotation angle and speed, based on positional reference input; a function which widens the robots’ working range and makes trajectory control more precise; a mechanism which achieves movement that is closer to the flexibility of humans; and a more sophisticated microprocessor which increases computation speed, thereby improving the movement of other mechanisms.
Robotics is indeed a synonym for “technology fusion.” What significantly helped the flourishing of robotics innovation in Japan was an industrial base where the needed mechanical, electronic, and sensor technologies were readily available for this fusion.
Tomonori Sanada of the Robot Division gives an example of the fruit of such fusion: “In an auto body welding line, a total of 12 robots-six on the left side and six on the right-work on one car at once and finish the task in one minute. Such high-speed operations are precisely controlled so that the robots neither collide nor interfere with each other.”
Kawasaki has also been a leader of robotics applications in the semiconductor manufacturing sector. The company’s “Clean Robots” handle wafers in clean rooms where microdust must be kept out, improving the yield of semiconductor manufacturing.
Kawasaki has a greater than 50% market share worldwide in this robotics application, and the same clean-robot technology is now being applied to sectors outside of semiconductors, such as food and pharmaceutical manufacturing, which also require ultraclean environments.
Kawasaki’s original high-speed pick-and-place robots were launched in 2009. Using their grippers, our new parallel-link pick-and-place robots can re-align parts and other products, and pack them into boxes. The debut of this new robot opened the door for applications in previously unsuitable sectors, such as food, pharmaceuticals, and cosmetics. Best practices in these industries led to the robots’ usage in yet more sectors requiring assembly, alignment, and other tasks involving electric, electronic, and mechanical components.
In regard to Kawasaki’s leading position in technological innovations, Sanada says, “There are two factors that have made Kawasaki’s innovation possible. First, we have always been in close communication with our customers and have jointly developed solutions to their challenges. Secondly, we have gained a great deal of expertise in robotics applications as a result of selling systematized robots, in addition to stand-alone robots. This has encouraged our pursuit of robotics applications in other fields.”
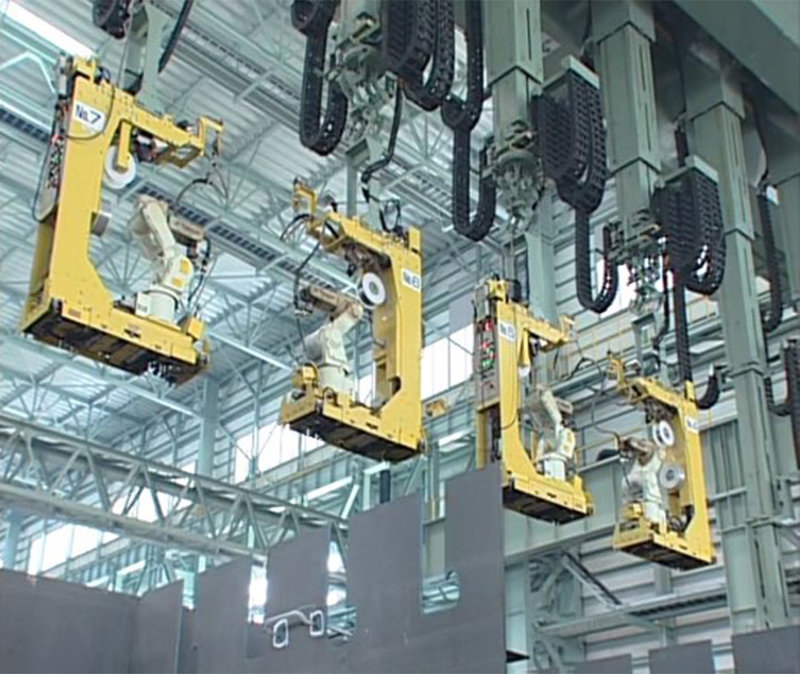
he fact that Kawasaki is a comprehensive manufacturer producing a vast array of products is the single most important factor behind its solution development capability, as such development requires precise identification of robots’ tasks and analysis of procedures, guided by a clear roadmap for solving the problems in question. Sanada adds, “Because of its extensive experience in numerous industries, including aircraft, shipping, and motorcycle, Kawasaki has all-around insights into how robots can be used to bring a customer’s manufacturing to a more sophisticated level and to improve the quality of their products.”
Our comprehensive perspective on feasibility analysis allowed for efficient systematization of our own manufacturing processes, and helped our mechanism designs and control technologies to be applied to various other sectors. It is a shared understanding among companies involved in the robotics business that prominent manufacturers choose Kawasaki as their preferred solutions provider. This testifies to our capability for developing technologicalsolutions and inventing new robotics applications which have helped large corporations resolve their various challenges.
Sanada comments, “Customers place a very high priority on a provider’s track record when making a decision on introducing industrial robots. They’d like to know whether robots that have been incorporated into other companies’ manufacturing systems are functioning properly and achieving expected results. Customers feel safe partnering with Kawasaki in introducing robotic applications, because we have experience in developing prototypes for internal use, as well as being a repository of verification data to substantiate their effectiveness.”
How a Kawasaki Robot Is Made @ Kawasaki’s Akashi Works
Striving to Make Robots More Familiar and User-Friendly
In regard to this new phase in robotics, where applications are being seen in previously-untapped markets, General Manager of the Robot Division, Yasuhiko Hashimoto, commented, “The industrial robot business has finally arrived on the threshold of a full-fledged revolution of robotics."
In the medical sector, for example, in 2013, Kawasaki established a joint venture called Medicaroid Corporation with Sysmex Corporation, a medical equipment manufacturer. The joint venture recently launched the “SOT-100 Vercia,” a robotic operating table capable of a wide range of movements, enabling patients to be positioned in whatever way is required during surgery.
In recent years, more minimally-invasive surgeries are being performed, such as catheter intervention guided by X-ray imaging procedures such as angiography. In addition, “hybrid surgeries” are becoming popular because they are also less invasive and take less time. During a hybrid surgery, a combination of catheter intervention under X-ray guidance and conventional surgical procedures is performed. For these hybrid surgeries to be carried out successfully in operating rooms equipped with angiograms and magnetic resonance tomography (MRT) equipment, patients need to be moved into optimal positions so surgeons can check imaging results while performing operations. The Vercia was developed to achieve these movements smoothly and quickly. Currently, Kawasaki is developing a surgery-assisting robot to be operated by surgeons.
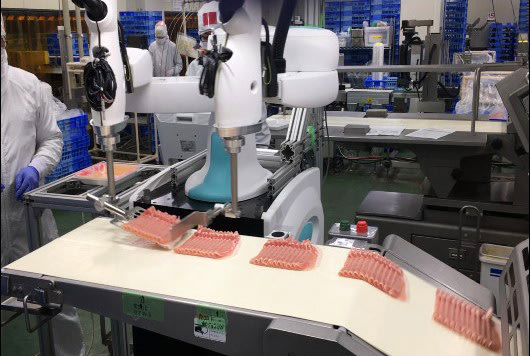
The duAro, a dual-arm SCARA (Selective Compliance Assembly Robot Arm) robot, is another epoch-making product that has been launched in recent years. This two-armed robot can be installed in a space no larger than that required for a single human being, and can be moved freely. Teaching duAro specific tasks can be done easily, using a tablet terminal. The debut of duAro opened up the possibility for manufacturers engaged in multi-variety, small-volume production of short-lived products to incorporate robots in that process.
Because of its low pricing, duAro has been adopted by many small- to medium-sized firms. Finding a duAro in the backroom of a supermarket, chopping and packing meat, for example, is becoming a reality.
Sanada says, “We are offering a service called Robot Haken (robot dispatching service), renting out duAros to increase their usage. In a manufacturing environment where significant production volume fluctuations are seen or where increasing product value is challenging, the duAro can achieve greater efficiency without increasing fixed costs. We also assist manufacturers in designing customized jigs suitable for it.”
We are indeed witnessing the arrival of an age where solutions involvingindustrial robots are available for anyone who seeks them.
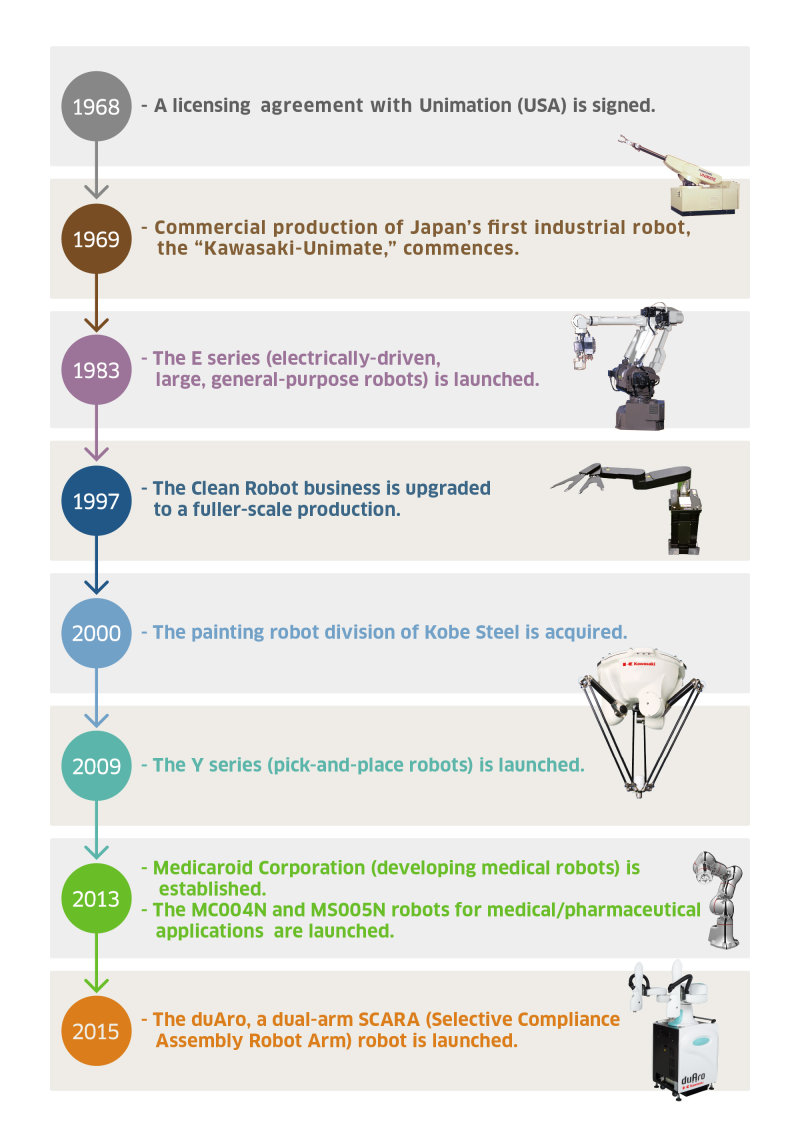

Robot Division Precision Machinery Company
Kawasaki Heavy Industries, Ltd.
*As of January 2018
Human-Robot Coexistence and Collaboration Can Solve Three Social Challenges
For the last five decades, industrial robots have been a vital part of manufacturing in the auto, electric, and electronic parts sectors. With the development of digitized signal processing and more sophisticated robotic mechanisms, they are now capable of performing more complicated tasks at a much faster speed, while their size has been reduced.
Today, the manufacturing of high-quality competitively- priced products is not possible without robots. Manufacturing sectors in fast-growing China and other parts of Asia, as well as in the U.S. and Europe, where much resistance to robotics applications was initially seen, are quickly adopting robots, showing that – worldwide – manufacturing without robots is no longer feasible.
Envisioning the next 50 years, future missions to be fulfilled by robots in industrialized nations are very clear: 1. Accommodate labor shortages arising from aging workforces, 2. Produce value-added products to support economic growth by leveraging passed-down expertise and skills, and 3. Address challenges associated not only with aging populations but also with overall healthcare and welfare.
To achieve these imperatives, the functions and features expected of future robots will be very different than those of today. First, they must address shrinking workforces. Japan is the world’s largest producer of robots, and until recently, it was also the largest user. However, according to statistics, only 300 units per 10,000 workers in the manufacturing industry were in operation, which came to a 3% utilization rate, while in Korea, it was as high as 6%*1. Since 2015, the Japanese workforce has been losing an average of 640,000 people annually, and this trend is expected to continue through 2060*2. If robots could take the place of half of the workers being lost each year, Japanese industry could sustain itself.
To that end, we must seriously expand robotics applications. The duAro, a dual-arm SCARA robot, is a highly-versatile, compact robot which can perform a variety of tasks. It can work alongside humans (“co-exist”), as it is equipped with collision-detection safety features. Its low initial cost encourages manufacturers to adopt it for short-lived products. The duAro was Kawasaki’s first countermeasure to the diminishing workforce.
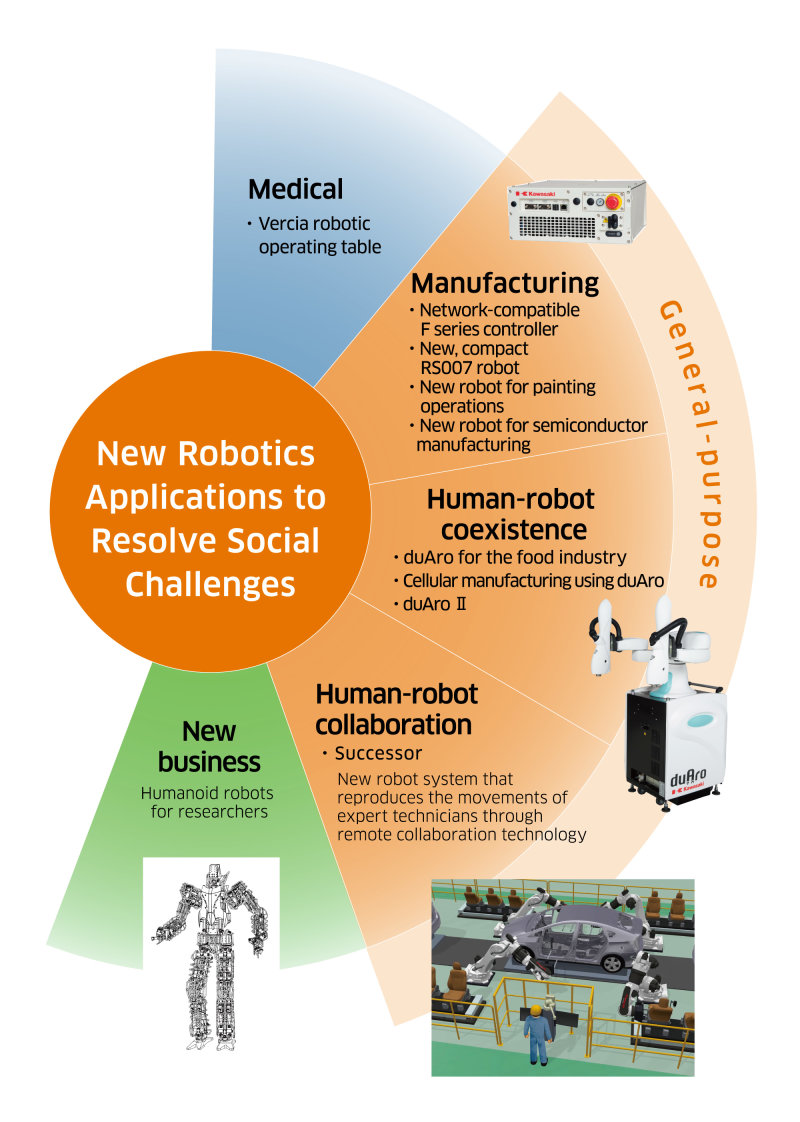
The second invention to fulfill the robots’ mission for the future is the “Successor” series. This innovation was developed based on remote collaboration technology and artificial intelligence to analyze the techniques of skilled technicians and teach those skills to robots and untrained personnel, thereby preserving and passing on specialized expertise to future generations.
Our third focus is medical applications. Expectations for robotics applications in the medical sector are high. They can be applied to areas geared at reducing the risks of medical procedures, such as robot-assisted surgeries and surgical training, and can also be used for patient support, such as robotic beds which move patients automatically, preventing bedsores and other adverse conditions.
Robotics has evolved continuously, improving the efficiency of manufacturing, and it will continue to do so, achieving greater coexistence and collaboration with humans. In such an age, Kawasaki is committed to driving forward new concepts focused on improving the coexistence and collaboration of robots with humans, as represented by the duAro, which works closely with us and can be easily adopted, as well as the Successor, which supports the continuity of superior expertise. Fifty years since its inception, the industrial robot business has finally arrived on the threshold of a full-fledged robotics revolution.
*1 World Robotics 2017, International Federation of Robotics
*2 National Institute of Population and Social Security Research

Marketing and Business Planning Department
Robot Division
Kawasaki Heavy Industries, Ltd.