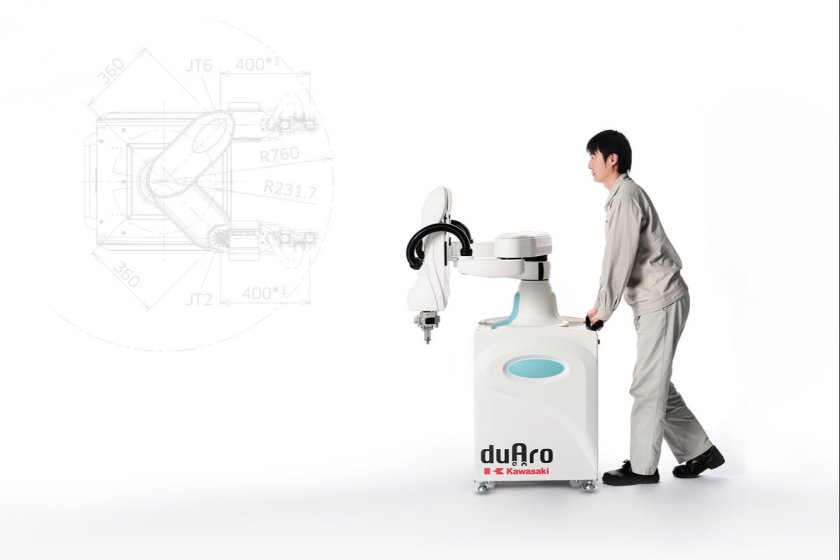
In June 2015, Kawasaki launched a new industrial robot called “duAro.” The dual-armed horizontal articulated robot has the flexibility to be applied to production lines with a short product life cycle and frequent changes. With a small footprint and low price tag, it offers possibilities of robot applications to small and midsize companies as well. Witness the dawn of a new robot revolution in which humans and robots coexist and cooperate to take manufacturing to new heights.
Heralding an Era of New Robot Applications
People who see the duAro for the first time are taken aback by the softness of its appearance. It features a body painted in white with patches of light blue and sleek lines that give off a sense of softness and approachability. These are characteristics that are not normally associated with the traditional image of an industrial robot as being rugged.
The duAro is an articulated robot with two arms that move in horizontal directions. It is the first ever dual-armed horizontal articulated robot to be operated on a single axis. The arms are integrated with a controller, and the entire structure weighs 145 kg and occupies a space of only 62 cm by 60 cm. It comes with a set of wheels for easy relocation, and a surprisingly small price tag. The smallness of its size and affordable pricing came as a welcome shock to manufacturers that were hesitating to introduce robots to their production lines.
Ever since the duAro was released in June 2015, Kawasaki has been receiving a deluge of inquiries about the product. Apparently the possibilities it offers were obvious to everyone.
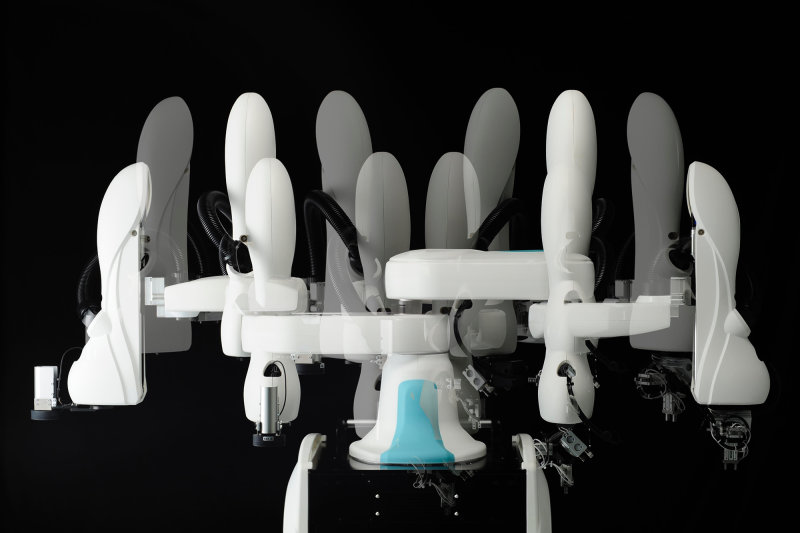
The duAro is a robot that coexits and cooperates with human workers, and is easy to install and operate.
It easily fits in to a space occupied by a human with no need to make any changes to the existing lines. It handles the same working range as a human, and there is no need to install a safety fence to prevent accidents. It is easy to install, easy to operate, and easy to upgrade. In other words, it allows you to instantly replace any work that you would want a robot to perform.
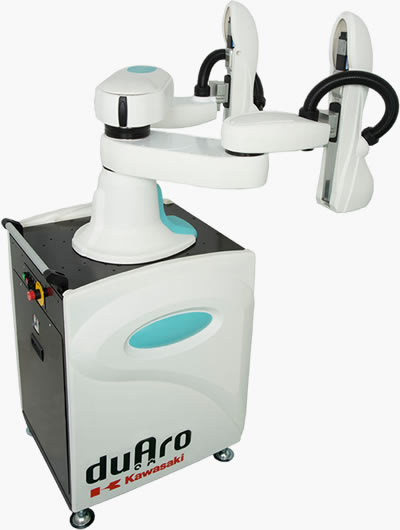
This concept opened a new horizon for the application of robots. Japan leads the world in both annual shipments of industrial robots and the number of robots in operation. Emerging countries are also incorporating robots into production lines at an accelerating pace to streamline operations. There are many factories, however, for which this is not an option.
For example, companies in the electrical and electronics industry normally have a product life cycle of only three to six months. This calls for a quick change of operations, making it difficult to introduce robots due to limited preparation period and cost-effectiveness. The short product life cycle has hitherto prevented these companies from taking advantage of the power of robots, which handle fixed operations with precision.
Small and midsize companies, on the other hand, previously had to give up using robots due to limited factory space and investment capital.
In 1969, Kawasaki manufactured the first industrial robot in Japan, laying the foundation for Japan to become a major power in the field of robots. In addition to welding robots for automobiles, Kawasaki has developed robots for various applications including assembly, material handling, painting, palletizing, and cleanroom automation for semiconductor manufacturing. Taking a market-oriented approach of providing solutions to issues faced by customers, Kawasaki has accumulated a wide range of robot technologies. Kawasaki is a global leader in semiconductor wafer handling robots, boasting a share of roughly 50%.
It has set the annual sales target for the duAro at over 5,000 units. Armed with this new product, Kawasaki is ready to take on the challenge of creating a new market for industrial robots.
A Dual-armed Horizontal Articulated Robot that Fits in to the Space of a Human
A robot that fits in to the space of a human worker without requiring line modifications, works side by side with humans, and is easy to install and manage to realize this concept, Kawasaki’s development engineers experimented with bold combinations of their accumulated robot technologies and new ideas.
First, they worked on reducing the footprint. The duAro succeeded in minimizing installation space by incorporating technologies used by semiconductor wafer handling robots, and integrating a set of two arms with a controller on a single axis. The single-axis, dual-armed structure minimized arm interference, which was more likely to be a problem if two conventional horizontal articulated robots were to be installed side by side. The duAro is also capable of coordinated movements.
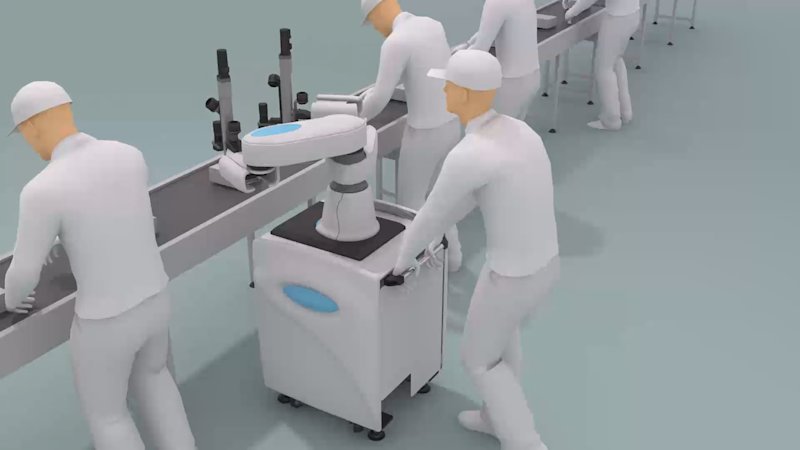
Junichi Murakami, the assistant manager in charge of the duAro’s design, says, “Our aim was to create a robot that can work alongside humans. So we made the arm length roughly equal to the arms of humans. The idea for a dual-armed structure came from the observation that humans rarely work with only one hand.” The duAro, in other words, is a humanoid robot based on a new concept.
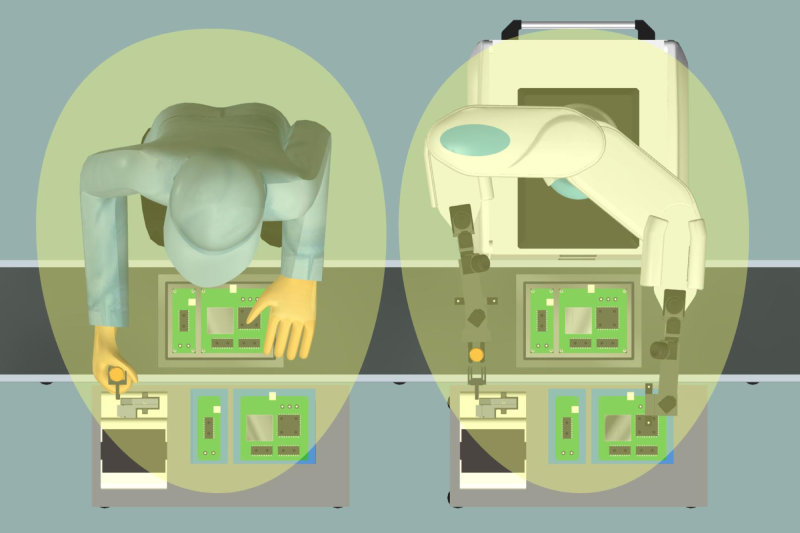
The dual-armed structure was intended to achieve another benefit: simplifying the effectors attached to the arm end. When machining a workpiece with only one arm, some kind of a jig would be necessary to hold the workpiece firmly in place. With a dual-armed robot, it is possible to hold the workpiece with one arm, and perform machining operations with the other. This structure offers the advantage of being able to accommodate a wide range of tasks using simple effectors.
Murakami says, “When introducing industrial robots, you have to consider the costs of effectors, jigs, and other peripheral equipment in addition to the robot itself. These costs can be quite substantial, and the total amount paid can end up being two to three times the price of the robot. But with dual-armed duAro, the cost of operating the robot is relatively small.”
The controller is housed inside a wheeled platform to allow the robot to be easily moved to the desired place. It can be placed at any position along the production line to replace human labor.
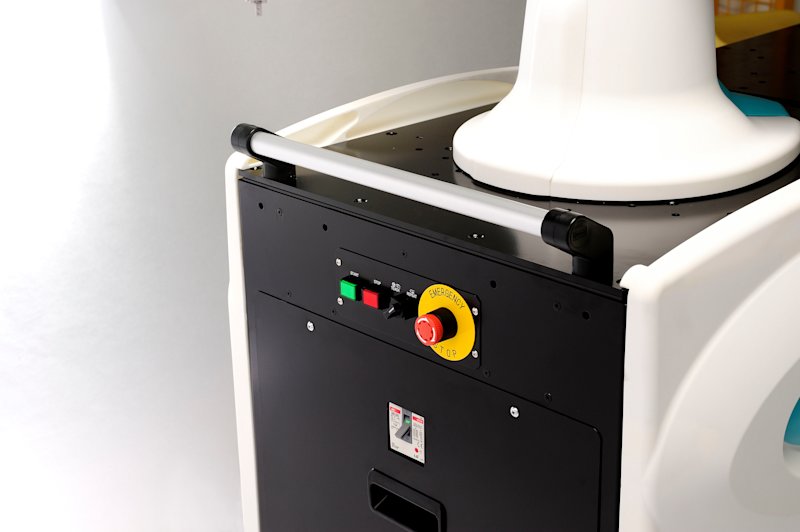
For this to work, however, there needs to be a mechanism that enables the robot to easily learn new tasks and flflexibly accommodate any changes in operation.
Normally, it takes at least two weeks to robotize a process, given the need to create a program that strictly defines every step that a robot will perform, based on the position the robot will occupy. In an industry where a new product life cycle begins every three months, it is not practical to spend two weeks on teaching alone. With the duAro, however, this can be done in just three days thanks to its direct teaching function and user- friendly tablet terminal.
Easy Operation and Teaching Realized with Kawasaki Technology
Masayoshi Kanbara, the assistant manager responsible for the duAro’s software development, says, “A robot that is easy to operate is a robot that can be used without a manual.” He explains how the duAro embodies this ideal through its direct teaching function: “It’s like teaching children how to do things by taking their hands and guiding them through each process step by step.”
Teaching the duAro how to perform a new task is done basically in the same way. All you need to do is to hold its arms and trace the movement you want it to follow. Then it will automatically determine how to connect each movement in the optimal manner.
It is also possible to program movements through a tablet terminal. Simply open the tablet menu, and enter numerical values indicating the direction and distance of each movement.
“The control panel functions were all moved to a dedicated tablet running an Android OS for enhanced usability,” Kanbara explains. “It won’t take more than a day to learn how to operate the terminal, and you don’t need any knowledge of formulas or programming skills.”
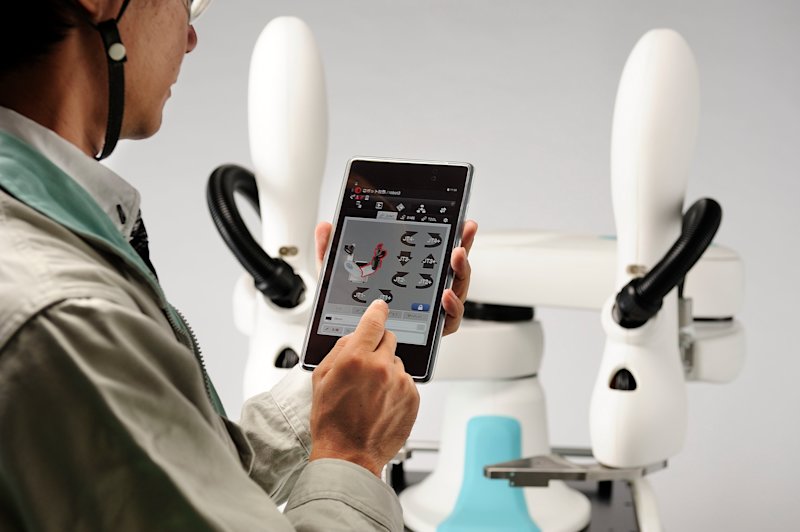
There is one more important issue that needs to be addressed. Since the duAro will be operating alongside humans, it must ensure the safety of human workers in the event of a collision. The duAro is designed with full attention paid in this regard as well. It can be configured to slow down the operating speed when the arms extended sideways enter a set range.

The arms are covered with urethane foam, and impact detection sensors feature a clever control mechanism. Kanbara says, “Impact detection is processed by software to determine if the operation needs to be stopped. We have considerable technological know-how on analyzing arm movements and recognizing impacts that call for stopping the operation. We used this as a foundation with further upgrades added for enhanced capabilities.”
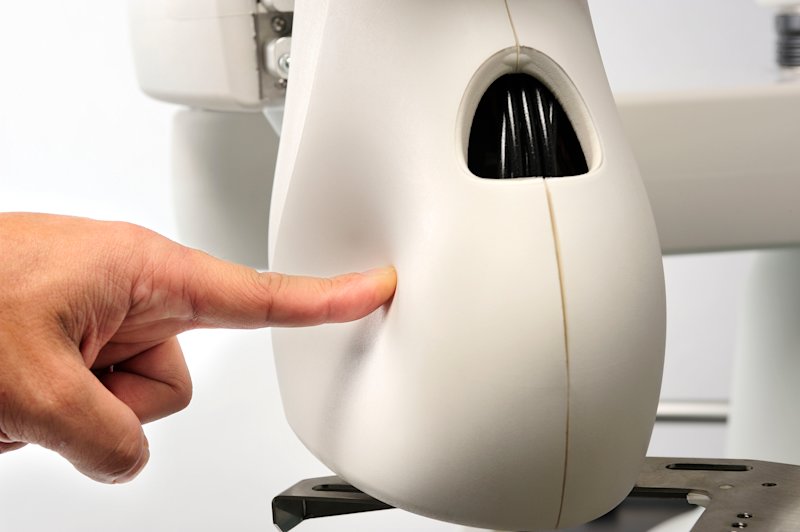
Ability to Propose Improvement is Key to a Successful Application
No matter how smart a machine or robot is, it must be tailored to each application in order to function effectively in a production setting. Satoshi Hibino, the assistant manager, is responsible for ensuring the duAro is integrated seamlessly into a production line. “The toughest part of my job is the process until the duAro is integrated with the system,” he says with laughter, as he mulls over some issues faced at a client, and how to best apply the duAro to help solve them.
“The duAro features options designed to accommodate applications other than in the electrical and electronics industry. However, in order to maximize its full potential, it is necessary to gain an appropriate understanding of the issues faced onsite by the customer, and to offer a suitable proposal to enhance productivity based on this understanding. Providing appropriate training to our sales reps and marketing efforts to convert customers into Kawasaki fans are also important.”
It is expected that the duAro will play a huge role in advancing and automating the manufacturing operations of small and midsize companies, which make up the foundation of industry. The duAro requires minimal costs for peripheral equipment, and minimal effort to respond to process changes. The benefits of its introduction and cost savings add up year after year. “I believe that providing robot-centered solutions is one of our major missions as a manufacturer,” Hibino says.
Manufacturing based on coexistence and cooperation with robots is about to enter a new century.
The project to develop the duAro was started with the aim of finding applications for robots in the electrical and electronics industry. On the other hand, it was also an effort to offer a solution to problems faced by small and midsize companies, which form the foundation of manufacturing. The duAro is small enough to be installed in a factory with limited space, it is easy to operate, and it comes with a relatively small price tag. It offers tremendous benefits as a new addition to the production line. Traditionally, industrial robots have been thought of as something reserved only for large-scale manufacturers. The duAro, however, aims to change that, and start a new era of coexistence and cooperation with robots.
“Easy” is the keyword that defines the duAro, but this does not mean that the level of technologies used to create it is low. Rather, the opposite is true---it takes highly advanced, complex technologies to create something that is as easy to use as the duAro. And this ease of use has had the effect of allowing more customers to make requests for improvement, and offer suggestions for new applications. This in turn allows us to further evolve the product. I believe the greatest significance of having launched the duAro is that it allows us to create a cycle of cooperation and co-creation with the customers toward resolving their issues.
Humans and robots both have their own strengths, and there is sufficient room for enhancing competitiveness by enabling seamless collaboration between humans and robots. For example, it would be possible to establish a production system in which humans and robots work side by side during the day, and only robots work during the night. Robots can also be used to help people with physical impairments to play a more active role in society.
Robots support humans at our side as our best partners. We at Kawasaki hope to enable more customers to reap the benefits of the duAro, as we work to provide a total solution that seeks to optimize the production system as well as the way we work.
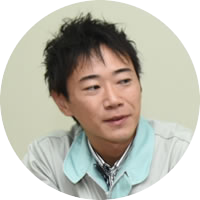
FA and Clean Group
Robot Division
Kawasaki Heavy Industries, Ltd.
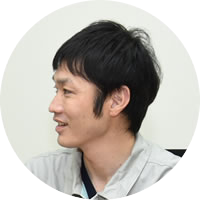
FA and Clean Group
Robot Division
Kawasaki Heavy Industries, Ltd.
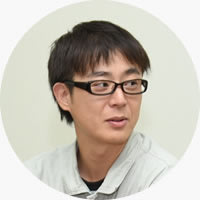
FA and Clean Group
Robot Division
Kawasaki Heavy Industries, Ltd.